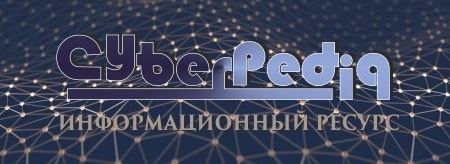
Автоматическое растормаживание колес: Тормозные устройства колес предназначены для уменьшения длины пробега и улучшения маневрирования ВС при...
Общие условия выбора системы дренажа: Система дренажа выбирается в зависимости от характера защищаемого...
Топ:
Методика измерений сопротивления растеканию тока анодного заземления: Анодный заземлитель (анод) – проводник, погруженный в электролитическую среду (грунт, раствор электролита) и подключенный к положительному...
Процедура выполнения команд. Рабочий цикл процессора: Функционирование процессора в основном состоит из повторяющихся рабочих циклов, каждый из которых соответствует...
Отражение на счетах бухгалтерского учета процесса приобретения: Процесс заготовления представляет систему экономических событий, включающих приобретение организацией у поставщиков сырья...
Интересное:
Наиболее распространенные виды рака: Раковая опухоль — это самостоятельное новообразование, которое может возникнуть и от повышенного давления...
Влияние предпринимательской среды на эффективное функционирование предприятия: Предпринимательская среда – это совокупность внешних и внутренних факторов, оказывающих влияние на функционирование фирмы...
Принципы управления денежными потоками: одним из методов контроля за состоянием денежной наличности является...
Дисциплины:
![]() |
![]() |
5.00
из
|
Заказать работу |
|
|
РЕКОМЕНДАЦИИ ПО ПРОЕКТИРОВАНИЮ ПРОЦЕССА ПРЕССОВАНИЯ ПОРОШКОВЫХ МАТЕРИАЛОВ В ЖЕСТКИХ ПРЕСС-ФОРМАХ И РАЗРАБОТКИ КОНСТРУКЦИЙ ИНСТРУМЕНТА.
Усадка при спекании.
Полученное в результате прессования изделие проходит операцию спекания. Вследствие объемных деформаций материала при спекании происходит усадка или рост объема, в зависимости от химического состава порошка. Следует иметь в виду, что величина объемных деформаций и их распределение в изделии зависит от распределения плотности после прессования и схемы прессования. Неравномерность плотности является одной из основных причин коробления изделий после спекания.
1.5 Выбор припусков под механическую обработку и калибровку.
Наличие упругого последействия и усадки при спекании приводит к изменению размеров изделий в процессе их изготовления. Требования по точности и шероховатости поверхности к готовым изделиям в большинстве случаев более жесткие чем разброс этих параметров у спеченных изделий. В этом случае для их доработки используются дополнительные операции механической обработки некоторых поверхностей или калибровки. В том и другом случае должен быть предусмотрен специальный припуск на обработку (слой материала, добавляемый на обрабатываемую поверхность). Для обработки резанием оставляется припуск 0,3- 0,5 мм на сторону для чистового точения за один проход. На калибровку - припуск 0,1 -0,2 мм на сторону. Во многих случаях припуск приходится оставлять из-за несоответствия шероховатости поверхности изделий из порошков после спекания, которая составляет Rz 20, а после калибровки Ra 2,5. Применение дополнительных операций обработки повышает трудоемкость изготовления изделий, в то же время в результате расширения поля допусков на размеры изделия после прессования и спекания снижается стоимость конструкции и изготовления инструмента.
|
1.6 Разработка чертежа заготовки изделия.
Чем сложнее геометрия изделия, тем сложнее должна быть пресс-форма для его прессования. В зависимости от конкретных условий производства и серийности выпуска изделия технолог должен принять решение: либо получить максимально точную заготовку с минимальными припусками (или без них), но при этом значительно усложнить конструкцию пресс-формы и трудоемкость процесса прессования, либо упростить конфигурацию прессуемого изделия за счет назначения технологических напусков и припусков и упростить конструкцию пресс-формы. В этом случае речь идет о получении заготовки, из которой в последствии после дополнительной обработки будет получено готовое изделие.
Разработка чертежа заготовки изделия и проектирование технологии состоит из нескольких этапов:
- выбор порошкового материала и способа его подготовки для прессования;
- выбор способа и схемы прессования изделия с учетом необходимых дополнительных формообразующих операций, определение энергосиловых параметров процесса прессования, выбор оборудования;
- исходя из технологических возможностей выбранного способа и схемы прессования, назначить необходимые технологические напуски (упрощения формы заготовки вследствие технологических ограничений процесса прессования), припуски для механической обработки и калибровки (геометрия заготовки после спекания и после калибровки);
- определить упругое последействие заготовки в результате прессования (номинальные размеры полости пресс-формы);
- по объему заготовки после прессования и плотности материала определить необходимый объем порошка;
- на основании полученных результатов разработать чертеж заготовки с указанием припусков, размеров заготовки с допусками и размеров готовой детали (указываются в скобках), в некоторых случаях выполняются также чертежи заготовок после спекания и после прессования для контроля качества после этих операций.
|
Таблица 1.Осноные технологические схемы получения порошковых изделий конструкционного назначения
Условия | Класс | Группа |
Малосерийное производство |
Пример проектирования технологии прессования детали типа фланца. Технология и схема прессования детали. В качестве технологии изготовления детали выбираем следующую, в соответствии с таблицей технологических процессов А + М = (холодное прессование + спекание) + (механическая обработка)
Выбираем схему прессования два независимых пуансона с низу и один сверху.
Расчет напусков на выступ на фланце по условию разноплотности. Схема расчёта разноплотности для определения напуска представлена на рис. 5: Рис. 5 Схема расчета разноплотности выступа на фланце. Заданная разноплотность между элементами фланца составляет 15%.
Разница плотностей составила 21% (>15%), пересчитаем высоту засыпки и разноплотность с напуском 2 мм. Тогда новая плотность В данном случае разноплотность составляет 14,8% (<15%).
Усадка при спекании Полученное в результате прессования изделие проходит операцию спекания. Вследствие объемных деформаций материала при спекании происходит усадка или рост объема, в зависимости от химического состава порошка. Следует иметь в виду, что величина объемных деформаций и их распределение в изделии зависит от распределения плотности после прессования и схемы прессования. Неравномерность плотности является одной из основных причин коробления изделий после спекания. В нашем случае усадка в горизонтальном и вертикальном направлении различна. KВ= 1,008; Kг =1,016
H10: 12,2 *1,008= 12,3 мм H15: 15,7 *1,008 = 15,8 мм H45: 45,4*1,008 = 45,8 мм
Расчет высоты засыпки. Расчет засыпки порошка производится исходя из его массы. На рис. 6 представлены размера заготовки перед спеканием и размеры объема засыпки порошка в пресс-форму. Рис.6 Размера заготовки перед спеканием и размеры объема засыпки порошка в пресс-форму. Р = 800 МПа ρ0 = 3 V = 714423,1 m = 3*414,42 = 2143 г.
Прочностной и жесткостной расчет пресс-формы Расчет матриц на прочность. При расчете прочности матриц рассматриваются два случая: - давление на внешнюю матрицу; - давление на внешний нижний пуансон со стороны втулки (1). σэкв = σэкв = 441 – (- 320) = 761 МПа < [ σ ] σ экв1 = σэкв1 = 563 – (- 320) = 883 МПа < [ σ ] 4.2. Расчет пуансонов на сжатие и изгиб Расчет пуансонов на потерю устойчивости. Критическая сила изгиба пуансона определяется по следующей формуле. Pk = (2*p2*E* Jmin)/ l2 где
Таким образом, расчет необходим лишь для пуансона длина, которого равна 238-15=223 мм.
Геометрия пресс-форм На рис. 7 и 8 представлены чертежи пресс-форм для прессования внешних и внутренних фланцев Рис.7 Пресс-форма для прессования внешних фланцев. Рис.8 Пресс-форма для прессования внутренних фланцев.
Циклограмма работы пресс-формы На рис.9 представлена циклограмма работы пресс-формы. Рис. 9 Циклограмма работы пресс-формы.
Таблица 3. Зависимости плотности порошков от давления прессования
РЕКОМЕНДАЦИИ ПО ПРОЕКТИРОВАНИЮ ПРОЦЕССА ПРЕССОВАНИЯ ПОРОШКОВЫХ МАТЕРИАЛОВ В ЖЕСТКИХ ПРЕСС-ФОРМАХ И РАЗРАБОТКИ КОНСТРУКЦИЙ ИНСТРУМЕНТА. Проектирование геометрии прессованной заготовки. 1.1 Определение потребного давления прессования. Формование представляет собой процесс получения из порошковых материалов изделий (прессовок), обладающих такой прочностью, при которой полученное изделие можно извлечь из формующего инструмента и подвергнуть дальнейшей обработке. Процесс формования в жестких пресс-формах характеризуется давлением и временем прессования. В отличии от компактных материалов порошковые материалы могут деформироваться как вследствие деформации отдельных частиц, так и вследствие их смещения относительно друг друга. Таким образом изменяется не только форма, но и объем порошка. При формовании может происходить одновременно упругая, хрупкая и пластическая деформация частиц. Процесс формования складывается из 3-х основных стадий (рис. 1). 1. Увеличение плотности за счет перемещения частиц порошка относительно друг друга (заполнение пустот, разрушения образовавшихся связей между частицами и т.д.). 2. Деформация частиц порошка с увеличением металлического контакта между ними (за счет разрушения пленки окислов на поверхности частиц), резче проявляются силы трения порошка о стенки формующей полости матрицы. 3. Деформация отдельных зон внутри частиц; их упрочнение, что требует больших усилий для дальнейшего формования и резко затрудняет процесс уплотнения. Обычно при формовании высота заготовки по отношению к высоте насыпанного порошка уменьшается в 2,5- 3 раза и больше.
Одной из главных задач при формовании наряду с получением заданной формы, точности размеров и достаточной механической прочности является получение заданной плотности изделия. От плотности зависят как эксплуатационные характеристики готового изделия, так и ряд специальных свойств, например, антифрикционные. Это обусловлено тем, что во время дальнейшего спекания происходит дополнительное уплотнение изделия, что в свою очередь приводит к усадке, приводящей к короблению изделий. Теоретически можно получить изделие со 100% плотностью, соответствующей компактному материалу. Но как видно по кривой уплотнения (рис. 1) на последних стадиях уплотнения при прессовании удельные усилия прессования резко возрастают без значительного изменения величины плотности. Удельные усилия могут достигать при этом 1500 МПа и более. Такие значения удельных усилий близки к пределу текучести материалов, используемых для изготовления инструмента для пресс-форм.
Таким образом при выборе давлений прессования необходимо исходить из условий достижения максимальной плотности изделий с учетом реальной стойкости пресс-форм. Исходя из практического опыта, давление прессования составляет для порошков [1].:
Для каждого конкретного материала порошка может быть получена опытным путем своя кривая уплотнения, позволяющая наиболее точно определить необходимое давление прессования. 1.2 Упругое последействие. Упругая деформация частиц порошка, возникающая в процессе его прессования, является нежелательной, но к сожалению неотъемлемой составной частью процесса формования. После приложения нагрузки к формуемому порошку и последующей кратковременной выдержки формообразования изделия на этом этапе заканчивается. Внешнее давление, приложенное к пресс-форме, снимается и упругая деформация пресс-формы и заготовки после этого создает новое взаимодействие между ними. Так как деформации имеют противоположные знаки, полученная заготовка очень прочно удерживается в полости пресс-формы. Это явление называется упругим последействием. Упругое последействие является основной причиной затрудненного извлечения из пресс-формы изделия, возникновения на его поверхности сколов и трещин, а также заклинивания отдельных частей пресс-формы при их разборке. Величина упругого последействия может быть определена по формуле
где d - упругое последействие, %; ak - конечный размер изделия после распрессовки, мм; ao - размер изделия до распрессовки (в пресс-форме), мм. Увеличение размеров в направлении прессования в результате упругого последействия может достигать у высокоплотных прессовок и в два и более раз превышать поперечное последействие. В результате этого явления при извлечении изделия из пресс-формы в результате действия сил трения на боковой поверхности необходимо приложить усилие равное 0,3 - 0.4 (0,2 -0,35) от усилия прессования. 1.3 Боковое давление. При прессовании порошковых материалов в жестких пресс-формах на первом этапе наблюдается относительно равномерное уплотнение материала. Затем, в результате возникновения связей между отдельными частицами порошка и их трением о внутреннюю поверхность пресс-формы осевое давление начинает превышать давления на боковые стенки. Величина бокового давления распределяется неравномерно по высоте пресс-формы. Вследствие действия сил трения в направлении противоположном направлению прессования, усилие прессования расходуется на их преодоление, поэтому происходит уменьшение осевого давления по высоте изделия, а следовательно и бокового давления на стенки. В общем случае потери на трение зависят от материала порошка, шероховатости поверхности матрицы, коэффициента трения, геометрии полости пресс-формы. Потери на преодоление сил трения могут достигать до 60% от усилия прессования, а боковое давление составляет примерно 40% от давления прессования непосредственно у поверхности пунсона и 15-20 % на наибольшем удалении от него (при одностороннем прессовании - в нижней части, при двухстороннем - посередине). Наличие бокового давления и сил трения вызывает неравномерное распределение плотности по высоте готового изделия. Плотность в общем случае снижается в направлении прессования. Зона максимальной плотности находится на некотором удалении от прессующего (подвижного относительно матрицы) пуансона, так как возникают силы трения на торцевой поверхности пуансона. Для повышения однородности получаемых изделий по плотности используют различные технологические приемы и схемы прессования, применяются различные смазки, используют схемы двухстороннего прессования или схему с “плавающей матрицей”. При прессовании полых изделий для более эффективного “перемешивания” порошка во время рабочего хода применяется относительное движения стержня и матрицы и др. Особенно большое внимание уделяется этому вопросу при прессовании изделий сложной формы (фланцев, ступенчатых втулок и т.д.). В этом случае используются специальные пресс-формы, имеющие до 5 подвижных элементов. Усадка при спекании. Полученное в результате прессования изделие проходит операцию спекания. Вследствие объемных деформаций материала при спекании происходит усадка или рост объема, в зависимости от химического состава порошка. Следует иметь в виду, что величина объемных деформаций и их распределение в изделии зависит от распределения плотности после прессования и схемы прессования. Неравномерность плотности является одной из основных причин коробления изделий после спекания. 1.5 Выбор припусков под механическую обработку и калибровку. Наличие упругого последействия и усадки при спекании приводит к изменению размеров изделий в процессе их изготовления. Требования по точности и шероховатости поверхности к готовым изделиям в большинстве случаев более жесткие чем разброс этих параметров у спеченных изделий. В этом случае для их доработки используются дополнительные операции механической обработки некоторых поверхностей или калибровки. В том и другом случае должен быть предусмотрен специальный припуск на обработку (слой материала, добавляемый на обрабатываемую поверхность). Для обработки резанием оставляется припуск 0,3- 0,5 мм на сторону для чистового точения за один проход. На калибровку - припуск 0,1 -0,2 мм на сторону. Во многих случаях припуск приходится оставлять из-за несоответствия шероховатости поверхности изделий из порошков после спекания, которая составляет Rz 20, а после калибровки Ra 2,5. Применение дополнительных операций обработки повышает трудоемкость изготовления изделий, в то же время в результате расширения поля допусков на размеры изделия после прессования и спекания снижается стоимость конструкции и изготовления инструмента. 1.6 Разработка чертежа заготовки изделия. Чем сложнее геометрия изделия, тем сложнее должна быть пресс-форма для его прессования. В зависимости от конкретных условий производства и серийности выпуска изделия технолог должен принять решение: либо получить максимально точную заготовку с минимальными припусками (или без них), но при этом значительно усложнить конструкцию пресс-формы и трудоемкость процесса прессования, либо упростить конфигурацию прессуемого изделия за счет назначения технологических напусков и припусков и упростить конструкцию пресс-формы. В этом случае речь идет о получении заготовки, из которой в последствии после дополнительной обработки будет получено готовое изделие. Разработка чертежа заготовки изделия и проектирование технологии состоит из нескольких этапов: - выбор порошкового материала и способа его подготовки для прессования; - выбор способа и схемы прессования изделия с учетом необходимых дополнительных формообразующих операций, определение энергосиловых параметров процесса прессования, выбор оборудования; - исходя из технологических возможностей выбранного способа и схемы прессования, назначить необходимые технологические напуски (упрощения формы заготовки вследствие технологических ограничений процесса прессования), припуски для механической обработки и калибровки (геометрия заготовки после спекания и после калибровки); - определить упругое последействие заготовки в результате прессования (номинальные размеры полости пресс-формы); - по объему заготовки после прессования и плотности материала определить необходимый объем порошка; - на основании полученных результатов разработать чертеж заготовки с указанием припусков, размеров заготовки с допусками и размеров готовой детали (указываются в скобках), в некоторых случаях выполняются также чертежи заготовок после спекания и после прессования для контроля качества после этих операций.
Таблица 1.Осноные технологические схемы получения порошковых изделий конструкционного назначения
|
|
|
Общие условия выбора системы дренажа: Система дренажа выбирается в зависимости от характера защищаемого...
Биохимия спиртового брожения: Основу технологии получения пива составляет спиртовое брожение, - при котором сахар превращается...
Индивидуальные и групповые автопоилки: для животных. Схемы и конструкции...
Типы сооружений для обработки осадков: Септиками называются сооружения, в которых одновременно происходят осветление сточной жидкости...
© cyberpedia.su 2017-2024 - Не является автором материалов. Исключительное право сохранено за автором текста.
Если вы не хотите, чтобы данный материал был у нас на сайте, перейдите по ссылке: Нарушение авторских прав. Мы поможем в написании вашей работы!