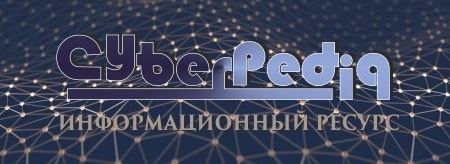
Таксономические единицы (категории) растений: Каждая система классификации состоит из определённых соподчиненных друг другу...
Поперечные профили набережных и береговой полосы: На городских территориях берегоукрепление проектируют с учетом технических и экономических требований, но особое значение придают эстетическим...
Топ:
Оснащения врачебно-сестринской бригады.
Основы обеспечения единства измерений: Обеспечение единства измерений - деятельность метрологических служб, направленная на достижение...
Организация стока поверхностных вод: Наибольшее количество влаги на земном шаре испаряется с поверхности морей и океанов...
Интересное:
Мероприятия для защиты от морозного пучения грунтов: Инженерная защита от морозного (криогенного) пучения грунтов необходима для легких малоэтажных зданий и других сооружений...
Искусственное повышение поверхности территории: Варианты искусственного повышения поверхности территории необходимо выбирать на основе анализа следующих характеристик защищаемой территории...
Инженерная защита территорий, зданий и сооружений от опасных геологических процессов: Изучение оползневых явлений, оценка устойчивости склонов и проектирование противооползневых сооружений — актуальнейшие задачи, стоящие перед отечественными...
Дисциплины:
![]() |
![]() |
5.00
из
|
Заказать работу |
|
|
Опишите контроль за качеством продукции на АБЗ, а также основы проектирования асфальтобетонных заводов
Для контроля качества на асфальтобетонных заводах (АБЗ) используют лаборатории к АБЗ.
Во время изготовления асфальтобетонной смеси, необходимо постоянно контролировать качество асфальта, в соответствии с технологическим регламентом производства.
На стадии входного контроля определяется соответствие основных показателей каждой партии сырьевых материалов требованиям действующих стандартов.
Операционный контроль основных показателей сырьевых материалов проводят не реже одного раза в десять смен в лаборатории к АБЗ.
Битум испытывают путем отбора проб из каждого рабочего котла не реже одного раза в смену. Для контроля температурного режима определяют температуру нагрева исходных материалов готовой смеси, получая показания с приборов прямым измерением либо с помощью термометров.
Для приемочного контроля, температуру смеси измеряют прямо в кузове автомобильного транспорта. Качество смеси контролируется путем отбора одной пробы от каждой выпущенной партии. Отгрузочной партией считается - количество смеси одного состава, выпущенное на одной установке в течение смены, но количеством, не превышающим 600 тонн. Отбор начинают не ранее тридцати минут после выпуска смеси. Для этого составляют одну объединенную пробу из трех-четырех точечных проб, взятых с интервалом двадцать-тридцать минут, в зависимости от производительности смесителя.
Перечень необходимого лабораторного оборудования:
• пресс гидравлический с нагрузкой до 100тс;
• устройство выпрессовочное с электроприводом, для извлечения асфальтобетонных образцов из стандартных цилиндрических форм;
|
• формы для изготовления образцов;
• пресс механический с нагрузкой до10тс с обжимным устройством;
• сушильный шкаф;
• весы лабораторные;
• установка вакуумная с вакуумным насосом;
• печь муфельная с автоматическим регулированием температуры;
• набор сит для грохота;
• комплект форм для испытания щебня;
• прибор для определения пылевидных и глинистых частиц;
• пенетрометр;
• дуктилометр;
• вискозиметр;
• устройство для встряхивания жидкостей в сосудах;
• прибор для определения глубины вдавливания штампа при испытании литых асфальтобетонных смесей;
• стеклянная лабораторная посуда.
Проектирование любого АБЗ делают исходя из следующего плана:
Исходные данные АБЗ;
Тип и характер АБЗ;
Выбор оборудования;
Генеральный план;
Технологический процесс АБЗ;
Монтаж и демонтаж оборудования;
Охрана труда и окружающей среды на АБЗ.
Дайте краткое описание экскаваторов, применяемых при разработке вскрышных пород, напишите формулу производительности экскаватора, опишите цикл экскавации, а также формулу, определяющую ширину заходки экскаватора при разработке грунта с одной стоянки
Вскрышные экскаваторы выпускают с ковшами емкостью от 4 до 35 м3, на гусеничном ходу, с электрическим приводом и рабочим оборудованием прямой механической лопаты. Они отличаются удлиненной стрелой и рукоятью, что позволяет применять их для верхней погрузки и перемещения горной массы в отвал. К вскрышным относятся экскаваторы ЭВГ-4, ЭВГ-6--в основном для верхней погрузки в транспортные сосуды; ЭВГ-15 и ЭВГ-35/65--для перемещения горной массы в выработанное пространство карьера.
Шагающие драглайны имеют ковши емкостью от 4 до 100 м3 и стрелы длиной до 100 м. Они предназначены главным образом для перемещения вскрышных пород в отвалы. Малые модели драглайнов с ковшами емкостью 4-6 м3 используются также для погрузки в транспортные сосуды, для проходки траншей, рытья котлованов, насыпки дамб и т. п. В настоящее время на карьерах применяют шагающие драглайны ЭШ-5/45, ЭШ-10/70, ЭШ-14/75, ЭШ-15/90, ЭШ-20/65, ЭШ-25/100, а также работает драглайн ЭШ-80/100 с ковшом емкостью 80-100 м3.
|
К основным технологическим параметрам одноковшовых экскаваторов относятся емкость ковша, рабочие параметры, масса, габариты, преодолеваемый уклон, удельное давление на грунт.
Таблица 3 - Технические характеристики одноковшовых гидравлических экскаваторов
Наименование показателей | ЭО-2621В-3 | ЭО-3323A | эо- 3122А | эо- 3221А | 30-4322 | эо- 4124Б | эо- 4125А | ЭО-5124 | ЭО-6123 (ЭО-6123-1) |
Эксплуатационная масса с оборудованием «обратная лопата», т | 6,1 | 13.8 | 14.3 | 14,2 | 20,4 | 25,0 | 25,6 | 39 | 67,5 (62) |
Вместимость, н?основного ковша обратной лопаты сменных ковшей | 0,25 0,15-0,5 | 0,63 0,25-1,2 | 0,63 0,25-1,2 | 0,63 0,25-0,8 | 1 0,5-1,25 | 1 0,3-2 | 1,25 0,3-2 | 1.6 1-3 | 2,5 1,6-5 |
Двигатель | Д65 | Д-240 Д-243 Д-245 | СМД17Н | А-01М, А-01МС | ЯМЗ-2381 | 4А2806У | |||
Мощность двигателя, кВт | 44 | 55-73 | 73,6 | 95,6 | 95,6 | 125 | 2x75 | ||
Частота вращения двигателя, мин-1 | 1750 | 2200 | 1800 | 1800 | 1700 | 1700 | 1700 | ||
Среднее давление на грунт, КПа | 37-59 | 18-34 | 62-67 | 63-68 | 81-98 | 101-103 | |||
Скорость передвижения, наибольшая, км/ч | 19 | 19,4 | 3 | 3 | 20 | 2.5 | 2,5 | 2,2 | 1.5 |
Частота вращения поворотной платформы, мин"1 | До 7,4 | До 7,4 | До 8,75 | До 6,9 | До 5,6 | До 6 | До 5,6 | До 4,9 | |
Наибольший угол подъема, град | 13 | 22 | 22 | 20 | |||||
Управление основными механизмами | Гидравлическое | Гидравлическое | |||||||
Радиус А, описываемый хвостовой частью, мм | 2450 | 2450 | 3060 | 2840 | 3150 | 3280 | 3150 | 3800 | |
Ширина Б платформы, мм | 2100 | 2500 | 2490 | 2500 | 2600 | 3000 | 3000 | 3000 | 3180 |
Габаритная высота В, мм | 2160 | 3300 | 3665 | 3500 | 3250 | 3060 | 3290 | 3172 | 3860 |
Просвет Г под поворотной платформой, мм |
| 1160 | 1045 | 1405 | 990 | 1085 | 1084 | 1500 |
Годовая производительность экскаватора (комплекса машин) непрерывного действия определяется по следующим формулам:
на вскрышных работах
Пгод = Qсут x Kвр(т) x Kпер x Кх.х x Kо.к x Nраб, куб. м;
где:сут - среднегодовое значение суточной производительности, куб. м/сут.;вр(т) - коэффициент врезки (доработки торцов);пер - коэффициент передвижки;х.х - коэффициент холостого хода;о.к - коэффициент обеспечения качества продукции;раб - расчетное число рабочих дней экскаватора (комплекса) в году;
гамма - плотность угля, т/куб. м.
Суточная производительность экскаватора равна
сут = Qсм x nсм, куб. м,
|
где:см - сменная производительность экскаватора, куб. м;см - количество рабочих смен в сутки.
Сменная среднегодовая производительность экскаватора (комплекса машин) определяется по формуле
см = Qт x Kз x Kупр x Kп x Kтр x Kг.к x Kис x Kкл x Tсм, куб. м,
где:т - техническая производительность экскаватора, куб. м/ч;з - коэффициент состояния забоя;упр - коэффициент качества управления экскаватором;п - коэффициент потерь (просыпей) экскавируемого материала;тр - коэффициент обеспеченности забоя транспортом;г.к - коэффициент готовности комплекса машин. Для роторных экскаваторов с ленточными конвейерами Kг.к = 0,90;ис - коэффициент использования времени смены;к.л - коэффициент влияния климата;см - продолжительность рабочей смены, ч.
Техническая производительность экскаватора определяется по формуле
т = Q x - x эта р, куб. м/ч,
где:- теоретическая производительность экскаватора, куб. м/ч;р - коэффициент разрыхления экскавируемой породы в ковше экскаватора;
эта р - коэффициент влияния крепости пород на экскавацию.
Ширина заходки экскаватора при разработке грунта с одной стоянки.
где Rч.у - радиус черпания на уровне стояния выемочного оборудования, м.
Опешите приготовление битума из гидрола, вспененных битумов и эмульсий
Производство нефтяных битумов является одним из термических процессов нефтепереработки. Основные параметры термических процессов, влияющие на ассортимент, материальный баланс и качество получаемых продуктов, - качество сырья, давление, температура и продолжительность термолиза (термического процесса).
Основным сырьём для производства битума в нашей стране являются остаточные продукты нефтепереработки: гудроны, асфальты деасфальтизации, экстракты селективной очистки масляных фракций и др.
Различают три основных способа получения нефтяных битумов.
. Концентрированием нефтяных остатков путём перегонки их в вакууме получают остаточные битумы. Для получения остаточных битумов может быть использовано только сырьё с большим содержанием асфальтосмолистых веществ, которые в достаточном количестве присутствуют в тяжёлых высокосмолистых сернистых нефтях. В процессах вакуумной перегонки и деасфальтизации получают остаточные и осаждённые битумы. Главное назначение этих процессов - извлечение дистиллятных фракций для выработки моторных топлив - в случае первого, подготовка сырья для производства базовых масел (начальный этап) - в случае второго. В то же время побочные продукты этих процессов - гудрон перегонки и асфальт деасфальтизации - соответствуют требованиям по сырью в производстве битумов или их используют в качестве сырья в производстве окисленных битумов.
|
. Окислением кислородом воздуха различных нефтяных остатков и их композиций при температуре 180 - 300 0С (окисленные битумы). Окисление воздухом позволяет существенно увеличить содержание асфальтосмолистых веществ, наиболее желательного компонента в составе битумов. Для производства окисленных битумов БашНИИНП предложено классифицировать нефти по содержанию (%, мас.) в них асфальтенов (А), смол (С) и твёрдых парафинов (П). Нефть считается пригодной для производства окисленных битумов, если выполняется условие:
Основным процессом производства битумов является окисление - продувка гудронов воздухом. Окисленные битумы получают в аппаратах периодического и непрерывного действия. Последние более экономичные и простые в обслуживании. Принцип получения окисленных битумов основан на реакциях уплотнения при повышенных температурах в присутствии воздуха, приводящих к увеличению концентрации асфальтенов, способствующих повышению температуры размягчения битумов, и смол, улучшающих адгезионные и эластичные свойства товарного продукта. Аппараты, используемые в производстве битумов - трубчатые реактора или окислительные колонны. При получении строительных битумов предпочтительны первые, дорожных - вторые.
Смешением различных окисленных и остаточных битумов, а также нефтяных остатков и дистиллятов между собой получают компаундированные битумы.
Остаточные битумы - мягкие легкоплавкие продукты, окисленные - эластичные и термостабильные. Битумы, получаемые окислением крекинг-остатков, содержат большое количество карбенов и карбоидов, которые нарушают однородность битумов и ухудшают их цементирующие свойства.
Технология
Остаточные битумы вырабатывают из мазутов с высокой концентрацией асфальтосмолистых веществ вакуумной перегонкой как остаток этой перегонки. Напомним, что мазут является остатком от атмосферной перегонки нефти. Более подробно остановимся на окислении гудронов или остаточных битумов кислородом воздуха. Основными параметрами процесса являются температура, расход воздуха и давление. Чем выше температура, тем быстрее протекает процесс окисления, но при слишком высокой температуре ускоряется образование карбенов и карбоидов, которые предают битумам нежелательную повышенную хрупкость. Обычно температуру поддерживают на уровне 250 - 280 0С. Чем больше расход воздуха, тем меньше требуется времени на окисление. При чрезмерно большом расходе воздуха температура в окислительной колонне может возрасти выше допустимой. Поэтому расход воздуха является основным регулирующим параметром для поддержания нужной температуры. Общий расход воздуха зависит от химического состава сырья и качества получаемого битума и составляет от 50 до 400 м3 / т битума. Давление в зоне реакции при его повышении интенсифицирует процесс, и качество окисленного битума улучшается. В частности, повышается пенетрация битума при неизменной температуре размягчения. Обычно давление колеблется от 0,3 до 0,8 МПа. Принципиальная схема получения окисленного битума показана на рисунке ниже.
|
Рисунок 1 - Принципиальная схема установки получения окисленных битумов: 1 - окислительная колонна; 2 - отпарная колонна (промежуточный сепаратор); 3 - сборник соляра (сепаратор); 4 - скруббер; 5 - печь; 6 - теплообменник; 7 - насосы; потоки: I - гудрон, II - лёгкие продукты окисления с отработанным воздухом, III - битум на отпарку, IV - готовый битум, V - пары стабилизации битума, VI - отработанный воздух, VII - очищенный отработанный воздух, VIII - свежий воздух, IX - соляр, X - вода, XI - загрязнённая нефтепродуктом вода, XII - водяной пар, XIII - рециркулят. Основным аппаратом является окислительная колонна диаметром 3400 мм и высотой 21 500 мм.
Технологический режим процесса следующий: температура, 0С: сырья на выходе из печи 180 - 250 в окислительной колонне, не выше 290 битума на выходе из холодильника 170 - 200 налива битума в цистерны 170 - 180 давление в окислительной колонне, МПа 0,3 - 08 расход воздуха, м3 / т битума. 50-400 тепловой эффект процесса, кДж / кг битума 168 - 502 содержание кислорода в газообразных продуктах окисления, % 3 -11 отношение рециркулят: сырьё 6:1
Наконец, третий способ получения битумов - это компаундирование. Способ этот является завершающей стадией получения битумов и использует в качестве компонентов как битумы, полученные в виде остатков вакуумной перегонки, так и окисленные битумы. Кроме того, одними из важных компонентов компаундов являются экстракты селективной очистки дистиллятных масел и деасфальтизаты, так как, являясь концентратом полициклической многокольчатой ароматики, они придают битуму эластичность и хорошую растяжимость.
Технологический режим такой установки: температура, 0С: сырья на входе в установку 100 - 120 окисления в реакторах 260 битума после холодильников. 170 давление, МПа: воздуха на входе в смесители. 0,9 смеси на входе в реактора 0,8 расход воздуха, м3 / м3 продукта 100-150 отношение рециркулят: сырьё 6:1.
Мощность установок производства битума - от 120 до 500 тыс. т / год.
Таблица 1 - Материальный баланс установки переработки смешанного сырья
Показатели | % |
Взято: | |
гудрон | 23,7 |
асфальт деасфальтизации гудрона | 39,7 |
экстракт селективной очистки масел | 32,9 |
поверхностно - активные вещества | 3,7 |
Итого: | 100,0 |
Получено: | |
битумы дорожные, в т.ч.: | 73,5 |
БНД 200 / 300, БНД 130 / 200 | 15,0 |
БНД 90 / 130 | 15,0 |
БНД 60 / 90 | 28,5 |
БНД 40 / 60 | 15,0 |
битумы строительные, в т.ч.: | 22,4 |
БН - IV | 11,2 |
БН - V | 11,2 |
отгон | 1,3 |
газы окисления | 2,8 |
Итого: | 100,0 |
Дайте описание поперечного и продольного способов проходки траншей в горных породах. Их достоинства и недостатки, условия применения каждого из указанных способов.
Разработка поперечными проходками
При значительных в плане размерах выемки целесообразно разрабатывать ее поперечными проходками вдоль меньшей стороны, рисунок 2.
Рисунок 2 - Схема проходок
Такой способ разработки обеспечивает минимальную длину пионерной траншеи и позволяет организовать наиболее производительное кольцевое движение транспорта.
Выемки, глубина которых превосходит максимальную высоту забоя для данного типа экскаватора, разрабатывают в несколько ярусов, рисунок 3.
Рисунок 3 - Ярусная последовательность разработки грунтов
При этом нижний ярус разрабатывают аналогично верхнему, а автомобили подают к экскаватору так, чтобы ковш наводился на кузов сзади.
Трасса движения автомобиля в этом случае должна быть параллельной оси проходки экскаватора, но направлена в противоположную сторону.
При работе с обратной лопатой также применяют торцовый или боковой забой. При разработке грунта торцовым забоем экскаватором с обратной лопатой Кна себя экскаватор движется по оси отрываемой им траншеи или котлована и попеременно разрабатывает то одну, то другую его сторону в зависимости от того, с какой стороны подходит очередной автомобиль. В торцовом забое средний угол поворота машины 70 90. Траншею можно расширять параллельными боковыми забоями, рисунок 4.
Рисунок 4 - Схема проходок с дополнительными параллелями
Боковой забой образуется при разработке грунта по одну сторону от оси движения экскаватора. Если при разработке траншеи грунт складывают в отвал по одну сторону от траншеи, ось проходки смещается в сторону отвала, а ширина разработки уменьшается по сравнению с максимально возможной при торцовой проходке. При разработке в отвал и на транспорт автомобили подходят к экскаватору со стороны, противоположной отвалу, а ось проходки смещается относительно оси траншеи в ту сторону, в которую отгружается большая часть грунта. При боковом и торцовом забоях автосамосвалы подходят по трассе, параллельной оси движения экскаватора, но навстречу ему, а при торцовом забое их устанавливают под загрузку под углом 15 25 к оси движения экскаватора.
Наиболее целесообразно применять экскаватор с обратной лопатой для отрывки траншей глубиной до 6 м и небольших котлованов глубиной до 4 м (например, под фундаменты отдельных колонн).
Разработка продольными проходками
Продольный способ состоит в разработке выемки проходками, направление которых выбирается по наибольшей стороне выемки.
Грунт разрабатывается по ходу экскаватора и отсыпается в отвалы на одну или две стороны от канала.
Рисунок 5 - Формы элементов забоя при продольной разработке канала экскаватором драглайн: а - поперечное сечение забоя; б - план забоя; в - продольное сечение забоя
При продольном способе разработки грунта используют экскаватор драглайн, который выбирают, исходя из следующих условий: радиус выгрузки Rв должен быть равен расстоянию А от оси канала до внешней бровки кавальера или несколько больше него:
где b - ширина канала по дну; т - заложение откоса канала; H - глубина канала; С - ширина бермы; mк - заложение внутреннего откоса кавальера; Нк - высота кавальера; ак- ширина кавальера поверху; глубина разработки Нр должна быть равна глубине канала Н или больше нее:
высота выгрузки Нв должна быть больше высоты кавальера Нкили равна ей:
ширина ковша bк должна быть меньше ширины канала
по дну b:
Размеры и размещение кавальеров назначают с учетом следующего:
площадь поперечного сечения одного кавальера следует определять с учетом коэффициента разрыхления грунта Кр:
где
- площадь поперечного сечения канала;
заложение откосов кавальеров назначают равным углу внутреннего трения грунта ; ширину бермы С принимают из условия устойчивости откоса выемки от обрушения и из условия работы машин вдоль канала в период строительства и в период эксплуатации. Величина С должна быть не менее 2 м. Кавальер следует размещать за пределами призмы обрушения грунта на откосе канала. При продольном способе разработки грунта ось движения экскаватора совпадает с продольной осью канала. Место второй и последующих стоянок экскаватора определяется шагом экскаватора
где а и h- координаты пяты стрелы;
- угол внутреннего откоса забоя;
Н - глубина канала.
Во избежание недоборов на откосах канала шаг экскаватора рекомендуется принимать не более половины длины стрелы. Чтобы не было лишних стоянок, а следовательно, и лишних затрат времени на передвижение экскаватора, нужно заранее определить шаг экскаватора.
|
|
Наброски и зарисовки растений, плодов, цветов: Освоить конструктивное построение структуры дерева через зарисовки отдельных деревьев, группы деревьев...
Особенности сооружения опор в сложных условиях: Сооружение ВЛ в районах с суровыми климатическими и тяжелыми геологическими условиями...
Двойное оплодотворение у цветковых растений: Оплодотворение - это процесс слияния мужской и женской половых клеток с образованием зиготы...
Типы сооружений для обработки осадков: Септиками называются сооружения, в которых одновременно происходят осветление сточной жидкости...
© cyberpedia.su 2017-2024 - Не является автором материалов. Исключительное право сохранено за автором текста.
Если вы не хотите, чтобы данный материал был у нас на сайте, перейдите по ссылке: Нарушение авторских прав. Мы поможем в написании вашей работы!