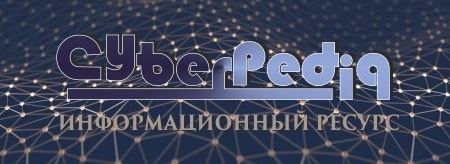
Наброски и зарисовки растений, плодов, цветов: Освоить конструктивное построение структуры дерева через зарисовки отдельных деревьев, группы деревьев...
Поперечные профили набережных и береговой полосы: На городских территориях берегоукрепление проектируют с учетом технических и экономических требований, но особое значение придают эстетическим...
Топ:
Теоретическая значимость работы: Описание теоретической значимости (ценности) результатов исследования должно присутствовать во введении...
Установка замедленного коксования: Чем выше температура и ниже давление, тем место разрыва углеродной цепи всё больше смещается к её концу и значительно возрастает...
Интересное:
Уполаживание и террасирование склонов: Если глубина оврага более 5 м необходимо устройство берм. Варианты использования оврагов для градостроительных целей...
Берегоукрепление оползневых склонов: На прибрежных склонах основной причиной развития оползневых процессов является подмыв водами рек естественных склонов...
Наиболее распространенные виды рака: Раковая опухоль — это самостоятельное новообразование, которое может возникнуть и от повышенного давления...
Дисциплины:
![]() |
![]() |
5.00
из
|
Заказать работу |
|
|
Кафедра механики и инженерной графики
МАТЕРИАЛОВЕДЕНИЕ
И ТЕХНОЛОГИЯ МАТЕРИАЛОВ
Методические указания
для самостоятельной подготовки по дисциплине
«Материаловедение и технология материалов»
для курсантов и студентов, обучающихся
по специальностям 280104.65 — «Пожарная безопасность»,
280103.65 – «Защита в чрезвычайных ситуациях» и по направлению подготовки 280700.62 – «Техносферная безопасность»
Иваново 2011
УДК 621.7
Ш 55
Пучков П.В., Топоров А.В. Материаловедение и технология материалов.Методические указания для самостоятельной подготовки по дисциплине для курсантов и студентов, обучающихся по специальностям 280104.65 — «Пожарная безопасность», 280103.65 – «Защита в чрезвычайных ситуациях» и по направлению подготовки 280700.62 – «Техносферная безопасность». — Иваново: ООНИ ИвИ ГПС МЧС России, 2011. — 57 с.
В методических рекомендациях представлен теоретический материал по курсу «Материаловедение и технология материалов» и список рекомендуемой литературы.
Методические рекомендации предназначены для курсантов и студентов очной формы обучения обучающихся по специальностям 280104.65 — «Пожарная безопасность», 280103.65 – «Защита в чрезвычайных ситуациях» и по направлению подготовки 280700.62 – «Техносферная безопасность».
Методические рекомендации рассмотрены
и рекомендованы к публикации
на заседании кафедры механики и инженерной графики
протокол № ___ от «__» ________ 2011 г.
Печатается по решению Редакционно-издательского совета института
Рецензенты:
© ИвИ ГПС МЧС России, 2011
Содержание
№темы | Наименование темы | Стр. | |
Тема №1 | Введение. Общие сведения о металлах, сплавах и неметаллических материалах. | ||
| Вопрос 1. Несовершенства кристаллического строения.............................. | 4 | |
Вопрос 2. Влияние несовершенств кристаллического строения на механические свойства материалов............................................................... | 6 | ||
Тема №2 | Физико-механические свойства материалов и методы их определения. | ||
| Вопрос 1. Физические свойства материалов................................................ | 6 | |
Вопрос 2. Влияние температуры на изменение механических свойств материалов......................................................................................................... | 9 | ||
Вопрос 3. Неразрушающие методы исследования механических свойств металлов и сплавов........................................................................................... | 9 | ||
Тема №3 | Основы теории сплавов | ||
| Вопрос 1. Компоненты и фазы железоуглеродистых сплавов.................... | 12 | |
Вопрос 2. Процессы при структурообразовании железоуглеродистых сплавов. Структуры железоуглеродистых сплавов....................................... | 14 | ||
Тема №4 | Железоуглеродистые сплавы | ||
| Вопрос 1. Легированные стали, их классификация, маркировка и область применения......................................................................................... |
15
17 | |
Вопрос 2. Способы получения чугунов различных типов и их маркировка. Процесс графитизации. Факторы, способствующие графитизации.................................................................................................... | |||
Тема №5 | Основы технологии термической и химико-термической обработки материалов | ||
| Вопрос 1. Структурно-фазовые превращения в стали в результате термической обработки................................................................................... | 18 | |
Вопрос 2. Диффузионная металлизация как вид ХТО, её виды, режимы и назначение...................................................................................................... | 20 | ||
Вопрос 3. Поверхностная закалка, лазерная термическая и химико-термическая обработка.................................................................................... | 21 | ||
Тема №6 | Цветные металлы и их сплавы. Неметаллические материалы | ||
| Вопрос 1. Композиционные материалы......................................................... | 24 | |
Вопрос 2. Пластмассы, их общая характеристика, классификация, и назначение......................................................................................................... | 25 | ||
Вопрос 3. Резины, их общая характеристика, классификация и назначение.......................................................................................................... | 29 | ||
Тема №7 | Поведение материалов в особых условиях. Коррозия металлических материалов и её виды. Защита металлов и сплавов от коррозии. | ||
Вопрос 1. Поведение материалов в особых условиях................................. Вопрос 2. Стали и сплавы с особыми физико-механическими свойствами......................................................................................................... | 30 33 | ||
Тема №8 | Основы технологии литейного производства и обработки материалов давлением. | ||
| Вопрос 1. Технология изготовления отливок в песчано-глинистых формах................................................................................................................ | 35 | |
Вопрос 2. Производство чугуна....................................................................... | 39 | ||
Вопрос 3. Производство стали......................................................................... | 40 | ||
Вопрос 4. Производство меди.......................................................................... | 46 | ||
Вопрос 5. Основы порошковой металлургии................................................. | 47 | ||
Тема №9 | Основы технологии получения неразъёмных соединений. | ||
| Вопрос 1. Пайка металлов, её общая характеристика и физическая сущность............................................................................................................. | 49 | |
Вопрос 2. Газокислородная резка металлов, её общая характеристика, физическая сущность........................................................................................ | 50 | ||
Вопрос 3. Процесс обработки материалов резанием: общая характеристика, виды, область применения................................................... | 52 | ||
Литература......................................................................................................... | 57 |
Тема №1 Введение. Общие сведения о металлах, сплавах и неметаллических материалах
По геометрическим признакам различают следующие структурные несовершенства (дефекты) кристаллического строения:
1) точечные — малые во всех трёх измерениях;
2) линейные — малые в двух измерениях и сколь угодно протяжённые
в третьем;
3) поверхностные — малые в одном измерении.
Точечные дефекты
Точечные дефекты являются одними из наиболее распространённых несовершенств кристаллического строения металлов. К точечным дефектам относятся: вакансии, межузельные (дислоцированные) атомы, наличие в узлах кристаллической решётки атомов примесей (рис. 1).
|
Вакансия — это отсутствие атомов в узлах кристаллической решётки, «дырки» (незанятые атомами места в ячейках кристаллической решётки) (рис. 1а).
Образуются вакансии при переходе атомов с поверхности в окружающую среду или из узлов решётки на поверхность (границы зёрен, пустоты, трещины и т. д.), в результате пластической деформации, при бомбардировке тела атомами или частицами высоких энергий (облучение в циклотроне или нейтронное облучение в ядерном реакторе). Число вакансий увеличивается с повышением температуры, при обработке давлением, облучении и других видах воздействия. Скопление многих вакансий может привести к образованию пор и пустот.
Рис. 1. Точечные дефекты.
Атомы примесей (примесные атомы) всегда присутствуют в металле, так как практически невозможно выплавить химически чистый металл. Они располагаются в узлах решётки или междоузлиях и могут иметь размеры больше или меньше размеров основных атомов (рис. 1 б, 1 в).
Дислоцированный (межузельный) атом — это атом, вышедший из узла решётки и занявший место в междоузлие (рис. 1 в). Межузельные дефекты образуются в результате перехода атома из узла в межузлие кристаллической решётки.
Точечные дефекты вызывают внутренние напряжения и незначительные искажения кристаллической решётки, что приводит к изменению физико-механических свойств тела (прочности, электропроводности, магнитных свойств и т. д.).
Линейные дефекты
Основными линейными дефектами являются дислокации.
Дислокации — это линейные дефекты кристаллического строения, представляющие собой линии, вдоль и вблизи которых нарушено характерное для кристалла правильное расположение атомных плоскостей (рис. 2). Для дислокаций характерно наличие лишних атомов, находящихся в междоузлиях.
Различают два вида дислокаций — краевые и винтовые (см. рис. 2).
Краевая дислокация представляет собой местное искажение кристаллической решётки, линию, вдоль которой внутри кристалла обрывается край «лишней» полуплоскости (рис. 2,). Неполная плоскость называется экстраплоскостью (рис. 2 б).
|
![]() | ![]() |
Рис. 2. Дислокации: а- краевая; б- экстраплоскость. | Рис. 3. Механизм образования винтовой дислокации. |
Винтовая дислокация образуется при помощи частичного сдвига кристалла по плоскости Q вокруг линии EF (рис. 3) На поверхности кристалла образуется ступенька, проходящая от точки Е до края кристалла. Такой частичный сдвиг нарушает параллельность атомных слоёв, кристалл превращается в одну атомную плоскость, закрученную по винту в виде полого геликоида вокруг линии EF, которая представляет границу, отделяющую часть плоскости скольжения, где сдвиг уже произошёл, от части, где сдвиг не начинался.
Дислокации образуются при термической и химико-термической обработках, в процессе кристаллизации, пластической деформации и других видах воздействия на структуру металлов и сплавов.
Плотность
Плотность ( ρ = m / V, г/см3) является одной из важнейших характеристик металлов и сплавов, численно равная отношению массы однородного тела к его объёму. По плотности металлы делят на следующие группы:
– лёгкие (плотностью не более 5 г/см3) — Mg, Be, Al, Ti и др.;
– тяжёлые (плотностью от 5 до 10 г/см3) — Fe, Ni, Cu, Zn, Sn и др. (это наиболее обширная группа);
– очень тяжелые (плотностью более 10 г/см3) — Мо, W, Au, Pb и др.
Самый легкий металл — литий Li (ρ = 0,53 г/см3), самый тяжёлый — осмий Os (ρ = 22,6 г/см3).
Важность плотности как физической характеристики материала обусловлена использованием установок в таких отраслях промышленности, как судостроение, транспортное машиностроение и особенно авиационная и ракетно-космическая техника. Для таких объёмов одним их решающих условий применения является минимизация массы технического объекта.
Температура плавления
Температура плавленияТ пл, ºС характеризует переход металла из твёрдого состояния в жидкое.
Температура плавления Т пл и равная ей температура затвердевания — характерный признак конкретного вещества.
Физическая сущность процесса плавления состоит в следующем. При плавлении нарушается порядок в расположении атомов, существующий в твёрдом состоянии, — происходит разрушение пространственной кристаллической решётки. В кристаллическом теле атомы совершают колебательные движения около своих положений равновесия. С повышением температуры амплитуда их колебаний возрастает (происходит повышение внутренней энергии тела) и достигает некоторой критической величины, после чего кристаллическая решётка разрушается. В свою очередь для разрушения кристаллической решётки требуется дополнительная тепловая энергия, поэтому в процессе плавления температура не повышается до тех пор, пока не произойдет разрушения всей кристаллической решётки тела, несмотря на то, что тепло продолжает поступать.
|
Температура плавления Т пл, подобно температуре кипения, зависит от давления. Для веществ, у которых увеличивается объём при плавлении, повышение давления снижает температуру плавления Т пл, и наоборот.
Удельная теплоёмкость
Теплоёмкость — способность материала при нагревании поглощать определённое количество тепла, а при остывании его отдавать.
Удельная теплоёмкостьС р, (Дж/кг·К) или (Дж/кмоль·К) — это количество энергии (теплоты), необходимое для повышения температуры единицы массы тела на один градус
,
где m — масса материала, кг;
Δ t — разность температур материала до и после нагревания, К;
Q — количество теплоты, переданное образцу.
Удельная теплоёмкость С р уменьшается с увеличением порядкового номера элемента в таблице Менделеева.
Удельные теплоёмкости разных металлов различны и, как правило, значительно меньше, чем у других веществ, благодаря хорошей теплопроводности. Например, у алюминия Al С р = 880 Дж/кг·К; у железа Fe С р = 460 Дж/кг·К; у меди Сu С р = 385 Дж/кг·К; свинца Pb С р = 130 Дж/кг·К.
Удельная теплоёмкость С р слабо растёт с повышением температуры и сильно меняется при фазовых превращениях. Известно также, что при высоких температурах теплоёмкость металлов и других кристаллических тел почти не изменяется и близка к постоянному значению. С понижением температуры теплоёмкость начинает быстро падать. Вблизи абсолютного нуля теплоёмкость всех тел стремится к нулю. При криогенных температурах даже малое количество теплоты существенно изменяют температуру материала.
Электропроводность
Электропроводность γ характеризует способность материала проводить электрический ток. Известно, что металлы хорошо проводят электрический ток. Хорошая электропроводность металлов объясняется наличием в них свободных электронов, обладающих большой подвижностью, которые под влиянием даже небольшой разности потенциалов способны перемещаться от отрицательного полюса к положительному.
На электропроводность металлов оказывает влияние температура. С повышением температуры усиливаются колебания ионов и атомов металлов, что затрудняет перемещение электронов по проводнику (металлу) и тем самым приводит к снижению электропроводности. При низких температурах колебательное движение ионов и атомов кристаллической решётки проводника, наоборот, сильно уменьшается и электропроводность резко возрастает. Уже вблизи абсолютного нуля (–273,15ºК) сопротивление металлов практически отсутствует.
Лучшим проводником электрического тока является серебро (Ag), за которым следуют медь (Cu), золото (Au), алюминий (Al), железо (Fe). Наряду с медными изготавливаются и алюминиевые электрические провода (кабели).
Отражательная способность
Отражательная способность — это способность металла отражать световые волны определенной длины, которая воспринимается человеческим глазом как цвет. Цвет металлов: Mg — бело-серый, Al — серовато-белый, Fe — голубовато-белый, Au —жёлтый, Ag — белый и т. д.
Характерный металлический блеск металлов обусловлен взаимодействием электромагнитных световых волн со свободными электронами металлов.
Компоненты пластмасс
Обычно пластмассы представляют собой сложные композиции, состоящие из нескольких веществ. Требуемые эксплуатационные свойства пластмасс получают благодаря подбору отдельных компонентов и их определенным сочетаниям.
В большинстве случаев пластмассы состоят из смолы, наполнителя, пластификатора, красителя и других добавок, улучшающих технологические и эксплуатационные свойства пластика.
Связующее вещество
Основным компонентом всех пластмасс является связующее вещество (высокомолекулярное органическое соединение), которое придаёт пластмассам пластичность и способность формоваться, а затем затвердевать, сохраняя полученную форму. Некоторые пластмассы состоят только из связующего вещества (например, полиметилметакрилат — оргстекло). В качестве связующего вещества в пластмассах применяют главным образом синтетические смолы.
Для повышения механической прочности, теплостойкости, электроизоляционных и других свойств в состав большинства пластмасс вводят другой весьма важный компонент — наполнитель, который после пропитки связующим веществом спрессовывается в однородную массу. Кроме связующих веществ наполнителей в состав пластмасс вводят пластификаторы, пигменты и другие добавки.
Синтетические смолы используют в качестве связующего вещества в пластмассах. Их получают из веществ с низким молекулярным весом, а также из природных или ранее полученных веществ с высокомолекулярным весом. Получение высокомолекулярных синтетических смол может быть осуществлено методами полимеризации или поликонденсации.
Наполнители – это органические и неорганические вещества в виде порошков, волокон, листов.
Наполнители вводят в пластмассы с целью: Улучшения физико-механических свойств, диэлектрических свойств, фрикционных и антифрикционных свойств, повышения теплостойкости, уменьшения теплостойкости, уменьшения усадки, снижения стоимости пластмасс.
Наполнители делятся на: органические и неорганические.
Органические наполнители - это материалы на основе целлюлозы. Они снижают хрупкость смол и сохраняют малый удельный вес, однако увеличивают гигроскопичность и уменьшают термостойкость пластмасс.
Неорганические наполнители - это материалы, которые увеличивают хрупкость пластмасс, но повышают теплостойкость и улучшают электроизоляционные свойства. При формовании у пластмасс с неорганическими (минеральными) наполнителями усадка значительно меньше, чем у пластмасс с органическими наполнителями.
В зависимости от требуемой структуры в пластмассы могут быть введены наполнители следующих видов:
1) порошкообразные (в виде порошкообразной крошки) древесная мука, целлюлоза, слюда, кварцевая мука, сажа, графит, тальк, Ti02 и некоторые другие.
2) волокнистые (в виде различных волокон) хлопковые очёсы, асбестовое волокно, стеклянное волокно, кроме того, могут использоваться отходы тканей, бумаги, картона, древесного шпона и др. Волокнистые наполнители повышают механические свойства пластмасс, однако вследствие меньшей текучести затрудняют процессы формования и возможность изготовления изделий сложной конфигурации;
3) слоистые (в виде цельнолистовых материалов) бумагу, ткани (хлопчатобумажные, стеклянные, асбестовые) и древесный шпон. Использование слоистых (листовых) наполнителей дает возможность получать пластмассы с наиболее высокими механическими свойствами и рядом специальных параметров. Такие пластмассы называют конструкционными.
В некоторых случаях изготовляют пластмассы без наполнителей, представляющие собой или прозрачные (типа органического стекла) или отдельные непрозрачные композиции.
Пластификаторы – это вещества, которые уменьшают межмолекулярное взаимодействие и хорошо совмещаются с полимерами. Пластификаторы вводятся в пластмассы в количестве 10-20% для повышения эластичности, уменьшения хрупкости готового изделия (улучшают морозостойкость) и предотвращения прилипание прессматериала к стенкам пресс-формы. В качестве пластификаторов применяют различные органические вещества: стеарин, касторовое масло, олеиновую кислоту, дибутилфталаты, трикрезилфосфаты и др.
Специальные добавки – это смазочные материалы, красители, добавки для уменьшения статических зарядов и горючести, для защиты от плесени, ускорители и замедлители отверждения и др. Специальные добавки служат для изменения или усиления какого-либо свойства.
Стабилизаторы – это вещества, предотвращающие разложение полимерных материалов во время их переработки и эксплуатации под воздействием атмосферных условий, повышенных температур и других факторов.
В качестве стабилизаторов используют ароматические амины, фенолы, сернистые соединения, газовую сажу.
Красители
В композиции пластмасс для придания определенной окраски вводят соответствующие красящие вещества — пигменты.
Виды красителей:
1) минеральные (мумия, охра, умбра, литопон, крон и др.); 2) органические (нигрозин, родамин).
Для ускорения отверждения термореактивных пластмасс в их состав перед формованием вводят катализаторы (перекиси, кислоты или соли).
При производстве пластмасс с пористым или ячеистым строением в их состав вводят специальные вещества — порообразователи.
Классификация пластмасс
Классификация пластмасс по происхождению: органического происхождения и неорганического происхождения.
Наибольшее применение в машиностроении получили пластмассы органического происхождения.
Классификация пластмасс в зависимости от пластической деформации при нагреве:
1) термопластичные (термопласты) пластмассы;
2) термореактивные (реактопласты) пластмассы.
Классификация пластмасс по диэлектрическим свойствам:
1) неполярные; 2) полярные.
Классификация резин
Классификация резин по твердости:
пористые (губчатые); мягкие (≤ 5%S); особо эластичные; средней твёрдости (10 – 15%S);
твёрдые; высокой твердости; жесткие (Эбониты (≥ 30%S)).
Классификация резин по назначению:
1) универсальные;
2) специальные: а) масло- и топливостойкие; б) химически стойкие; в) светостойкие;
г) морозо- и теплостойкие; д) газонепроницаемые; е) диэлектрические; ж) стойкие к радиации.
Классификация резин по технологии изготовления:
клееные; формованные; штампованные; литые.
Классификация резин по типу и конструкции изделий:
шинные; камерные; рукавные; протекторные; транспортные; амортизационные и др.
Из всех частиц наибольшее влияние на свойства конструкционных материалов оказывают нейтроны, способные из-за отсутствия заряда проникать далеко в глубь кристаллической решётки металла и вызывать в ней следующие существенные изменения:
1) образование «пар Френкеля» вследствие упругого столкновения частиц с ядрами атомов металла;
2) нарушение электронной структуры (ионизационные эффекты) в результате столкновения частиц с орбитальными электронами;
3) местное повышение температуры (термический пик), связанное с упругими колебаниями решётки на пути прохождения частиц;
4) образование атомов новых элементов в процессе ядерного распада, а также при захвате ядром частиц;
5) радиационная эрозия в результате отрыва атомов с поверхности под влиянием ударов высокоскоростных пылевидных частиц окружающей среды.
Соударения частиц с атомами в узлах кристаллической решётки смещают и возбуждают другие атомы. Вследствие упругого соударения частицы с атомами она теряет часть своей кинетической энергии, зависящую от целого ряда факторов этого взаимодействия. Если при этом соударении атом приобретает дополнительную энергию и она становится больше энергии, необходимой для его смещения, то атом из узла кристаллической решётки перемещается в междоузлие. За счёт такого перемещения атома из узла решётки в междоузлие и наличия вакансии образуется «пара Френкеля».
Возникающие дефекты строения приводят к изменению следующих структурно чувствительных свойств сплавов: снижаются пластичность, вязкость, повышается удельное электросопротивление и прочность, а главным образом сопротивление малой пластической деформации (σ 0,2).
Наиболее опасное явление, наблюдаемое при радиационном облучении, — это охрупчивание материалов. Данное явление наиболее сильно проявляется у металлов с ОЦК решёткой; так, например, критическая температура хрупкости молибдена после нейтронного облучения повышается от –30 до +70ºC.
Вследствие радиационного облучения у металлов и сплавов понижаются вязкость, пластичность, сопротивление отрыву, а прочность и электросопротивление повышаются, т. е. возрастает вероятность хрупких разрушений.
Тугоплавкие материалы
Тугоплавкие материалы. Тугоплавкие металлы и сплавы на их основе применяют для работы при температурах более 1000ºC.
Тугоплавкими называются металлы, имеющие температуру плавления выше, чем у железа. Наибольшее применение в технике находят тугоплавкие металлы, имеющие следующие температуры плавления: хром (Cr) — 1900ºC, ниобий (Nb) — 2415ºC, молибден (Мо) — 2620ºC, тантал (Та) — 3000ºC, вольфрам (W) — 3410ºC.
Расширение производства и применение тугоплавких металлов и сплавов связано с развитием атомной теплоэнергетики и ракетно-космической техники.
Сплавы на основе ниобия (Nb) и молибдена (Mo) имеют наиболее удовлетворительные технологические свойства. Кроме того, они охрупчиваются при сравнительно низких температурах (+100) — (–100)ºC. Вольфрам (W) переходит в хрупкое состояние при температуре 600ºC. Благодаря сравнительно высокой пластичности сплавы ниобия и молибдена имеют более широкое распространение.
Все тугоплавкие металлы имеют низкую жаростойкость. Для защиты их от окисления применяют различные покрытия. Для молибденовых и вольфрамовых сплавов применяют различные термодиффузионные силицидные покрытия.
В качестве материала для вкладышей сопел в реактивных двигателях, работающих на твёрдом топливе, применяют графит, имеющий температуру плавления 3900ºС. Температура пламени в таких двигателях достигает 3500ºC. Недостатком графита является низкая эрозионная стойкость, приводящая к износу сопла из-за твёрдых частиц, содержащихся в отходящих газах.
Формовочные материалы
Материалы, из которых изготовляют литейные формы, исключая металлические, называют формовочными материалами.
Виды формовочных материалов: исходные; формовочные смеси (для изготовления форм); стержневые смеси (для изготовления стержней); материалы окончательной отделки форм и стержней; отработанные — бывшие в употреблении смеси.
Исходными являются материалы, из которых приготовляют формовочные в стержневые смеси, а также материалы окончательной отделки форм и стержней.
Формовочные и стержневые смеси представляют собой предварительно подготовленные, взятые (в зависимости от назначения) в определённой пропорции, равномерно перемешанные между собой исходные материалы. Стержневые смеси подвергаются значительно бóльшим термическим и механическим воздействиям, чем формовочные, так как стержень практически со всех сторон окружён расплавленным металлом. Для улучшения механических, технологических и других свойств в формовочные и стержневые смеси вводят вспомогательные формовочные материалы: связующие (смолы, жидкое стекло), противопригарные (пылевидный кварц, каменноугольная пыль), защитные (борная кислота, фтористая присадка) и др. Перед установкой стержней в формы их обязательно просушивают.
Состав формовочных смесей:
1) Песок формовочный (ГОСТ 2138).
Песок формовочный – это диспергированный горный минерал.
В состав песка входит кремнезём (SiO2), который обладает температурой плавления равной 1713 °С и плотностью 2,5÷2,8 г/см3.
В песке также содержатся вредные примеси, такие как: слюда, полевой шпат, окислы железа и щелочноземельных металлов, которые имеют более низкую температуру плавления и поэтому снижают огнеупорность песка.
Основным показателем качества песка является показатель содержания глины и примесей.
Огнеупорность песков
По огнеупорности пески позволяют отливать в песчаноглинистые смеси все цветные металлы, а также сталь и чугун. Повысить огнеупорность песка можно путем введения в него огнеупорных материалов.
Виды огнеупорных материалов:
Циркон (ZrO2+SiO2); Магнезит (МgCO3); Хромистый железняк (FeOCr2O3).
Материалами для окончательной отделки форм и стержней являются огнеупорные литейные краски, замазки, клеи и т. п. материалы, которые часто называют вспомогательными.
Основные свойствами формовочных и стержневых:
1) прочность на сжатие и разрыв, поверхностная прочность или осыпаемость; 2) газопроницаемость (способность смеси пропускать газы); 3) газотворность (способность нагретой смеси выделять газы); 4) гигроскопичность; 5) формуемость; 6) текучесть;
7) уплотняемость; 8) выбиваемость и др.
Все эти свойства контролируются стандартными методиками на специальных приборах.
Составы и уровни свойств смесей назначают в зависимости от характера технологического процесса, в свою очередь, являющегося функцией большого числа факторов (масштаба производства, материала, массы, степени сложности, тонкостенности отливок и др.).
Исходные материалы для производства чугуна
В поверхностных слоях земной коры железо редко встречается в чистом виде. Благодаря большой склонности железа к окислению, в земной коре оно находится в виде окислов в смеси с окислами других химических элементов.
Железная руда — это горная порода, содержащая железо в таких количествах, при которых её технически возможно и экономически целесообразно перерабатывать. Руда состоит из смеси железосодержащих минералов с пустой породой, в состав которой входят различные соединения, прежде всего кремнезём (SiO2), глинозём (Al2O3), оксид кальция (CaO) и оксид магния (MgO). Реже в состав пустой породы входит магнезит (MgCO3) и доломит (MgCO3∙CaCO3).
Пустой породой руды называется такая её составляющая, которая не вносит существенных технологических осложнений в металлургическую переработку руды и легко отделяется от рудных минералов или в процессе обогащения или переходит в шлаки при плавке.
Пригодность железной руды для доменной плавки зависит от содержания железа (Fe), состава пустой породы и концентрации таких вредных примесей, как сера (S), фосфор (P), мышьяк (As) и др. Вредные примеси осложняют металлургические процессы, и, загрязняя основной металл, снижают его свойства.
В зависимости от количества рудного вещества различают богатые и бедные руды. Железные руды принято называть богатыми, если они содержать более половины железа (Fe); но это понятие меняется со временем. Также важную роль играет восстановимость руды, которая определяется скоростью восстановления из неё железа и зависит от природы оксида железа, плотности и пористости руды. Чем плотнее и менее пориста руда, тем хуже её восстановимость.
К основным рудообразующим минералам, наиболее часто используемым для производства чугуна, относятся следующие железные руды:
1) Магнитный железняк (магнетит). Содержит железо в количестве 40 – 70% в виде оксида Fe3O4 (закись-окись железа) и обладает хорошо выраженными магнитными свойствами.
2) Красный железняк (гематит). Содержит 45 – 65% железа в виде безводного оксида Fe2O3. В качестве пустой породы гематит содержит кремнезём (SiO2).
3) Бурый железняк (лимонит). Содержит железо в виде водных окислов типа n Fe2O3· m H2O с переменным количеством гидратной влаги.
4) Шпатовый железняк (сидерит). Содержит 30 – 40% железа в виде карбоната FeCO3.
Кроме железных руд, для металлургического производства чугуна требуются следующие исходные материалы: марганцевая руда, флюсы, топливо и воздух. Дадим краткую характеристику этим материалам.
Марганцевые руды — горные породы, содержащие марганец (Mn) в виде различных окислов MnO2, Mn3O4, Mn2O3 с общим содержанием марганца в пределах 25 – 40% (мас.). Марганец (Mn) при выплавке чугуна используется в первую очередь как раскислитель.
Флюсы — материалы (вещества) определённого химического состава, способствующие превращению в шлак пустой породы, вредных примесей и золы топлива. Данное определение справедливо только для металлургического производства. Доменные флюсы также вводятся в доменную печь с целью понижения температуры плавления пустой породы железной руды.
Основным видом топлива, используемым при выплавке чугуна в доменных печах и вагранках, является кокс.
Кокс (каменноугольный кокс) — представляет собой твёрдую пористую массу, которую получают сухой перегонкой (прокаливанием) при температуре 1000 – 1200ºC без доступа воздуха некоторых сортов каменных углей, называемых коксующимися. Средняя теплота сгорания кокса составляет 29,3 МДж/кг (7000 ккал/кг).
Подготовка исходных материалов к плавке
Перед плавкой руды проходят специальную подготовку, которая повышает производительность доменных печей и уменьшает расход топлива. Основными операциями подготовки руд к плавке являются: 1) дробление; 2) сортировка; 3) обогащение; 4) обжиг; 5) агломерация (спекание) обогащённой руды.
Производство стали
Сталями называются сплавы на основе железа (Fe) и углерода (C) с содержанием углерода до 2,14% (мас.). Практическое применение нашли стали с содержанием углерода (C) до 1,5% (мас.). Постоянными примесями в сталях являются марганец (Mn), кремний (Si), фосфор (P) и сера (S). Кроме углеродистых сталей, в машиностроении и строительстве широко применяют легированные стали, в состав которых для улучшения физико-механических и эксплуатационных свойств дополнительно введены различные химические элементы (хром (Cr), никель (Ni), молибден (Mo) и др.
В последние годы широко применяются электрометаллургические способы производства стали, позволяющие получать наиболее сложные и высоколегированные стали. Ниже рассмотрим три основных способа производства стали, применяемых в современном металлургическом производстве: в кислородных конверторах; в мартеновских печах, в электрических печах.
Исходными материалами для получения стали служат передельный (белый) чугун, стальной лом и ферросплавы. Чугун по сравнению со сталью содержит бóльшее количество углерода (C) и примесей. Поэтому основная задача передела чугуна в сталь состоит в удалении избытка углерода (C) и примесей с помощью окислительных процессов, протекающих в сталеплавильных агрегатах.
Кислородно-конверторный способ выплавки стали. Разработка данного способа выплавки стали явилось новым важным этапом в совершенствовании сталеплавильного производства. Замена воздушного дутья кислородным поставило конверторный способ производства стали на современный уровень и обеспечило ему повсеместное широкое применение.
Применение технически чистого кислорода (не менее 99,5% О2) для продувки чугуна позволило за счёт снижения содержания азота (N2) улучшить качество кислородно-конвертерной стали. В нашей стране в настоящее время используются кислородные конвертеры ёмкостью 100 – 400 т. Объём выплавляемой кислородно-конвертерной стали в нашей стране составляет около 35% от общего объёма её производства. На большинстве металлургических предприятий для кислородно-конверторного способа выплавки стали используют конверторы с глухим дном (см. рис. 1).
![]() | Рис. 1. Кислородный конвертор на 100 – 130 т: 1 — опорная станина; 2 — опорные подшипники; 3 — корпус конвертора; 4 — |
|
|
Кормораздатчик мобильный электрифицированный: схема и процесс работы устройства...
Таксономические единицы (категории) растений: Каждая система классификации состоит из определённых соподчиненных друг другу...
Общие условия выбора системы дренажа: Система дренажа выбирается в зависимости от характера защищаемого...
Организация стока поверхностных вод: Наибольшее количество влаги на земном шаре испаряется с поверхности морей и океанов (88‰)...
© cyberpedia.su 2017-2024 - Не является автором материалов. Исключительное право сохранено за автором текста.
Если вы не хотите, чтобы данный материал был у нас на сайте, перейдите по ссылке: Нарушение авторских прав. Мы поможем в написании вашей работы!