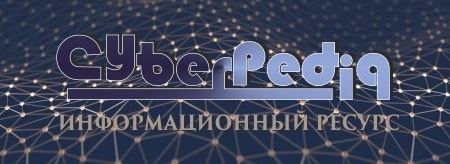
История создания датчика движения: Первый прибор для обнаружения движения был изобретен немецким физиком Генрихом Герцем...
Таксономические единицы (категории) растений: Каждая система классификации состоит из определённых соподчиненных друг другу...
Топ:
Генеалогическое древо Султанов Османской империи: Османские правители, вначале, будучи еще бейлербеями Анатолии, женились на дочерях византийских императоров...
Отражение на счетах бухгалтерского учета процесса приобретения: Процесс заготовления представляет систему экономических событий, включающих приобретение организацией у поставщиков сырья...
Марксистская теория происхождения государства: По мнению Маркса и Энгельса, в основе развития общества, происходящих в нем изменений лежит...
Интересное:
Наиболее распространенные виды рака: Раковая опухоль — это самостоятельное новообразование, которое может возникнуть и от повышенного давления...
Отражение на счетах бухгалтерского учета процесса приобретения: Процесс заготовления представляет систему экономических событий, включающих приобретение организацией у поставщиков сырья...
Мероприятия для защиты от морозного пучения грунтов: Инженерная защита от морозного (криогенного) пучения грунтов необходима для легких малоэтажных зданий и других сооружений...
Дисциплины:
![]() |
![]() |
5.00
из
|
Заказать работу |
|
|
Уплотнение формовочной смеси прессованием (рис. 8, а) осуществляют при подаче сжатого воздуха при давлении 0,5—0,8 МПа в нижнюю часть цилиндра /, в результате чего прессовый поршень 2, стол 3 с прикрепленной к нему модельной плитой 4 поднимаются. При этом колодка 7,. закрепленная на траверсе 8, входит внутрь наполнительной рамки 6 и уплотняет формовочную смесь в опоке 5. Плотность формовочной смеси уменьшается по мере удаления от прессовой колодки из-за трения формовочной смеси о стенки опоки. Неравномерность плотности формовочной смеси тем больше, чем выше опока и модели. Прессование используют для уплотнения формовочной смеси в опоках высотой 200— 250 мм
Для достижения равномерной плотности формовочной смеси в опоках используют многоплунжерные прессовые колодки (рис. 8, б). При прессовании стол 4 машины движется в сторону многоплунжер
ной прессовой колодки 1. Вследствие различной степени сопротивления формовочной смеси в форме плунжеры 3 под действием давления масла на поршень 2 прессуют находящиеся под ним участки формы
независимо от соседних.
Уплотнение формовочной смеси встряхиванием (рис. 8, в) осуществляют при подаче сжатого воздуха при давлении 0,5—0,8 МПа в нижнюю часть цилиндра 1, в результате чего встряхивающий поршень 2 поднимается на высоту 25—80 мм. При этом впускное отверстие 10 перекроется боковой поверхностью поршня, а нижняя его кромка откроет выхлопные окна 7, в результате чего воздух выйдет в атмосферу. Давление под поршнем снизится, и стол 3 с укрепленной на нем модельной плитой 4 упадет на торец цилиндра 8. Скорость стола, а следовательно, и скорость модельной плиты падает до нуля, в то время как формовочная смесь в опоке 5 и наполнительной рамке 6, продолжая двигаться вниз по инерции, уплотняется. В момент, когда канал 9 встряхивающего поршня окажется против отверстия 10 встряхивающего цилиндра, сжатый воздух снова войдет в полость встряхивающего цилиндра. Это повлечет за собой новый подъем встряхивающего стола и новый
|
удар его о торец и т. д.
Встряхивающий стол обычно совершает 120—200 ударов в минуту. В результате повторных ударов происходит уплотнение формовочной смеси в опоке. При этом слои формовочной смеси, лежащие у модельной плиты, будут иметь большую плотность, чем слои, лежащие в верхней части формы. Встряхиванием уплотняют формы высотой до 800 мм. Для уплотнения верхних слоев формы встряхивание совмещают с прессованием. Это обеспечивает высокую и равномерную плотность форм.
Уплотнение формовочной смеси пескометом (рис. 8, г), осуществляют рабочим органом пескомета — метательной головкой, выбрасывающей пакеты смеси на рабочую поверхность модельной плиты. В стальном кожухе 4 метательной головки вращается закрепленный на валу 6 электродвигателя ротор 5 с ковшом 2. Формовочная смесь подается в головку 1 непрерывно ленточным конвейером 3 через окно в задней стенке кожуха. При вращении ковша (1000—1200 об/мин) формовочная смесь собирается в пакеты 8 и центробежной силой выбрасывается через выходное отверстие 7 в опоку 9. Попадая на модель 10 и модельную плиту П, смесь уплотняется за счет кинетической энергии равномерно по высоте опоки. Метательную головку равномерно перемещают над опокой. Пескометы применяют
для уплотнения крупных форм.
Пленочно-вакуумную формовку (рис. 8, д) осуществляют в следующей последовательности: модельную плиту / с моделью 2 накрывают разогретой полимерной пленкой толщиной не более 0,1 мм. Вакуумным насосом в воздушной коробке 7 создают вакуум 2,6—5,2 МПа. Пленка 6 плотно прижимается к модели и модельной плите. На модельную плиту устанавливают опоку 3, которую заполняют сухим кварцевым песком 5, уплотняют его с помощью вибрации и выравнивают открытую верхнюю поверхность опоки. На верхнюю поверхность накладывают разогретую полимерную пленку 4, которая за счет разрежения в 4—6 МПа плотно прилегает к опоке, что способствует уплотнению песка и устойчивости формы. После этого полуформу снимают с модели.
|
Изготовляют как верхнюю, так и нижнюю полуформу, затем форму собирают. Вакуумирование продолжается не только при изготовлении полуформ, но и при их сборке, заливке и затвердевании залитого металла. При заливке металла в форму пленка сгорает. Продукты сгорания выполняют роль противопригарного покрытия. Этим способом изготовляют формы для отливок массой 0,1—10 т на автоматических формовочных линиях.
ИЗГОТОВЛЕНИЕ СТЕРЖНЕЙ
Процесс изготовления стержней включает следующие операции: формовку сырого стержня, сушку, отделку и окраску сухого стержня. Если стержень состоит из двух или нескольких частей, то после сушки их склеивают.
При изготовлении стержней вручную в разъемном стержневом ящике (рис. 9, а) раздельно набивают половины стержневого ящика (поз. 1). Поверхности разъема смазывают клеем и обе половины ящиков соединяют друг с другом и металлической иглой делают вентиляционный канал (поз. 2). Затем стержень удаляют из стержневого ящика, устанавливают на сушильную плиту (поз, 3) и отправляют в сушильную печь. На поз. 4 показан стержень, подготовленный к сборке.
При изготовлении стержней на пескодувных машинах (рис. 9, б) стержневая смесь из бункера 12 периодически поступает.в пескодувный резервуар 1. Сжатый воздух из ресивера 9 через быстродействующий клапан 10 заполняет резервуар 1 и через отверстия 2, 11 поступает в гильзу 3, в которой резко повышается давление и стержневая смесь выталкивается через сопло 5 в полость стержневого ящика 6. Для выпуска воздуха в надувной плите 4 и стержневом ящике 6 предусмотрены венты 7, 8. Эти машины обеспечивают высокое качество стержней и обладают высокой производительностью.
Изготовление стержней в нагреваемой оснастке (рис. 9, в) состоит в следующем. На позиции 1 нагретые до температуры 200—300 °С половинки стержневого ящика 2 и опустошитель 3. собирают. Из пескодувного резервуара 1 стержневая смесь с синтетической смолой вдувается в стержневой ящик. Связующее при нагреве отверждается, обеспечивая прочность стержню 4. После непродолжительной выдержки (15—120с) опустошитель 3 извлекают и пневматическим цилиндром 5 отводят одну из половин ящика (поз. 2). После этого вторая половина ящика поворачивается на 90°, и выталкивателями 6 стержень 4 удаляется из стержневого ящика (поз. 3). Стержни, полученные этим способом, имеют высокую прочность, точность размеров, газопроницаемость. Этим способом стержни изготовляют на высокопроизводительных автоматических машинах.
|
Рис. 9. Схемы процессов изготовления стержней:
|
|
История развития пистолетов-пулеметов: Предпосылкой для возникновения пистолетов-пулеметов послужила давняя тенденция тяготения винтовок...
Семя – орган полового размножения и расселения растений: наружи у семян имеется плотный покров – кожура...
Таксономические единицы (категории) растений: Каждая система классификации состоит из определённых соподчиненных друг другу...
Кормораздатчик мобильный электрифицированный: схема и процесс работы устройства...
© cyberpedia.su 2017-2024 - Не является автором материалов. Исключительное право сохранено за автором текста.
Если вы не хотите, чтобы данный материал был у нас на сайте, перейдите по ссылке: Нарушение авторских прав. Мы поможем в написании вашей работы!