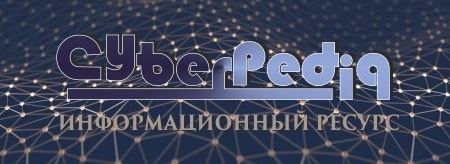
Типы оградительных сооружений в морском порту: По расположению оградительных сооружений в плане различают волноломы, обе оконечности...
Наброски и зарисовки растений, плодов, цветов: Освоить конструктивное построение структуры дерева через зарисовки отдельных деревьев, группы деревьев...
Топ:
Оснащения врачебно-сестринской бригады.
Устройство и оснащение процедурного кабинета: Решающая роль в обеспечении правильного лечения пациентов отводится процедурной медсестре...
Процедура выполнения команд. Рабочий цикл процессора: Функционирование процессора в основном состоит из повторяющихся рабочих циклов, каждый из которых соответствует...
Интересное:
Влияние предпринимательской среды на эффективное функционирование предприятия: Предпринимательская среда – это совокупность внешних и внутренних факторов, оказывающих влияние на функционирование фирмы...
Финансовый рынок и его значение в управлении денежными потоками на современном этапе: любому предприятию для расширения производства и увеличения прибыли нужны...
Берегоукрепление оползневых склонов: На прибрежных склонах основной причиной развития оползневых процессов является подмыв водами рек естественных склонов...
Дисциплины:
![]() |
![]() |
5.00
из
|
Заказать работу |
|
|
Введение
Литейное производство является одним из самых древних видов обработки металлов. Археологические исследования показывают, что уже за 5000 лет и более до нашей эры в древних центрах человеческой культуры литейное ремесло и искусство достигли высокого уровня. Об этом свидетельствуют найденные при раскопках древних городов античные вазы-амфоры, статуи и предметы домашнего обихода. Установлено, что первым литейным материалом была бронза.
В последние годы была найдено много стоянок древнего человека, на которых обнаружили литые наконечники копий и предметы домашней утвари. Это дало основание считать, что уже в последнюю эпоху каменного века предки умели выплавлять металл, владели литейным ремеслом. Археологи установили, что на берегу Исетского озера был металлургический «завод» с законченным циклом производства. Здесь отливали топоры, наконечники стрел, украшения и предметы домашнего обихода. Сейчас на этом месте установили своеобразный памятник древним металлургам.
Наивысшего расцвета литейное дело достигло в конце ХII - начало ХIII веков, когда стали применять двухсторонние формы из твердых пород камня, снабженные разветвленными литниковыми системами. Формовку производили в глине, а плавку металла в тиглях, для контроля жидкотекучести применяли специальные технологические пробы.
Параллельно с развитием технологии литейного производства происходило освоение новых литейных материалов (сплавов) чугуна, стали, ковкого чугуна, алюминиевых, магниевых и других цветных сплавов на основе редких металлов.
При современном уровне развития техники машины являются неотъемлемой частью нового вида производства. Повышая производительность труда и качества выпускаемого вида продукции, машины обеспечивают высокие темпы развития всех отраслей народного хозяйства нашей страны.
|
Процесс создания машины начинается в техническом отделе завода, а затем в цеховых технологических бюро, где технологи разрабатывают наиболее рациональные процессы производства отдельных деталей и сборки машины с учетом имеющихся на данном предприятии производственных условий и создают механическую документацию, определяющую характер и особенности производственных процессов, связанных с выпуском машин.
Заготовки деталей машин и другие металлические изделия можно получить различными способами: ковкой, сваркой, штамповкой. Однако наиболее распространенным и самым дешевым способом их производства следует считать литье, характерной особенностью которого является универсальность, возможность получать самые разнообразные по конфигурации и технологическим свойствам фасонные отливки из чугуна, стали и сплавов известных металлов.
В литейных цехах фасонные отливки получают путем заливки расплавленного расплава в песчано-глинистую форму. Такая форма служит для изготовления одной отливки и называется разовой.
Высокие механические и эксплуатационные свойства отливки обуславливают их широкое применение в различных отраслях промышленности и особенно в станкостроении, где литые детали составляют до 90% массы металлорежущего станка. Учитывая это, литейное производство по праву считают основой машиностроения.
В современных условиях литейные цеха машиностроительных заводов, а также входящие в структуру металлургических, строительных и других предприятий, производят фасонные отливки, масса которых колеблется в широких пределах - от нескольких граммов до 300 тонн. С учетом массы чугунные и стальные отливки принято подразделять на группы: мелкие до 100кг, средние до 1000 кг, крупные до 5000 кг, тяжелые до 15000 кг и особо тяжелые свыше 15000 кг.
|
Литейное производство характеризуется трудоемкостью, серийностью и номенклатурой выпускаемых отливок. Под трудоемкостью понимают время, затрачиваемое для производства отливок, под серийностью - количество ежемесячно выпускаемых одинаковых отливок, а под номенклатурой - их разнообразие.
Различают следующие основные типы литейного производства: единичное, серийное и массовое.
Единичное (индивидуальное) производство характеризуется выпуском в небольших количествах самых разнообразных отливок. При этом производство отдельных отливок может периодически повторяться. Примером единичного производства может служить выпуск отливок для ремонтных целей в литейных мастерских небольшой мощности или очень крупных единичных отливок массой в несколько десятков тонн (детали мощных экскаваторов, корпуса крупных турбин).
Серийное производство характерно периодическим выпуском отливок огромной или широкой номенклатурой, значительными или небольшими партиями. Примером серийного производства является выпуск отливок для различных типов металлорежущих станков в литейных цехах станкостроительных заводов. С учетом объема и номенклатуры выпуска отливок серийное производство принято подразделять на мелкосерийное и крупносерийное.
Массовое производство характеризуется непрерывным выпуском отливок предельной номенклатуры в больших количествах. Примером массового производства служит выпуск отливок литейными цехами автомобильных и тракторных заводов.
Тип производства оказывает большое влияние на выбор методов литья и технологию производства отливок, на характер производственного оборудования и организацию труда в литейном цехе.
Если единичное производство характеризуется применением ручных методов труда, частичной механизацией производственных процессов и незначительным количеством применяемой модельно-литейной технологической оснастки, то в серийном и особенно в массовом производстве рационально применять наиболее технически современное и высокопроизводительное оборудование, большое количество специальных приспособлений и приборов обеспечивающих качественное выполнение операций.
Табл.1 Свойства применяемых литейных сплавов
Сплавы | Физические и технологические свойства
| Механические свойства * | ||||||
плотность, т/м³ | усадка, % | температура плавления, ºС | Пределы прочности, кгс/мм² | Относительное удлинение δ, % | Твердость по Бринеллю НВ | |||
при разрыве δв | при изгибе δизг | |||||||
Серый чугун (обыкновенный) | 7,15 | 1,0 | 1150-1260 | 12-44 | 28-64 | 1,5-3,0 | 143-289 | |
Ковкий чугун | 7,25 | 1,5 | 1150-1350 | 30-63 | - | 2-12 | 163-269 | |
Сталь литая углеродистая | 7,80 | 2,0 | 1420-1520 | 40-60 | - | 10-24 | 109-199 | |
Бронза | 8,60 | 1,5 | 1000-1150 | 6-60 | - | 5-30 | 14-250 | |
Латунь | 8,60 | 1,5 | 900-950 | 20-65 | - | 6-20 | 40-150 | |
Алюминиевые сплавы | 2,55-2,83 | 1,0 | 580-630 | 12-25 | - | 1-9 | 40-100 | |
Магниевые сплавы | 1,8-1,83 | 1,2 | 600-650 | 10-30 | - | 1-6 | 3075 |
* Зависят от вида применяемых форм (песчаная, металлическая), а также метода получения отливок (литье статическое, центробежное, литье под давлением)
Приготовление и нанесение на рабочие поверхности кокилей специальных покрытий. Подготовка кокиля к заливке.
1.При производстве кокильного литья из чугуна применяют теплоизоляционное покрытие кокилей и противопригарную краску.
.Теплоизоляционное покрытие целесообразно наносить в качестве облицовочного слоя на рабочие поверхности кокилей один - два раза в смену.
.Противопригарная краска наносится на рабочую поверхность кокилей перед каждой заливкой металла.
.Теплоизоляционное покрытие и противопригарная краска наносится на рабочую поверхность кокилей инжекционным воздушным распылителем (пульверизатором).
.Приготовление теплоизоляционного покрытия и противопригарной краски, нанесение их на рабочие поверхности кокиля:
.Состав теплоизоляционного покрытия:
пылевидный кварц - 50% (42 кг.);
бентонит - 25% (21кг.);
жидкое стекло (модуль) - 25% (21кг.);
вода (сверх 100%) - до плотности 1,10-1,15 г/см³.
5.2.Залить в смеситель 40-50 литров воды и 21 кг. жидкого стекла, интенсивно перемешать раствор в течение 2-3 минут.
.Продолжая интенсивное перемешивание раствора, ввести в него небольшими порциями предварительно взвешенное количество пылевидного кварца. Раствор интенсивно перемешать в течение не менее 5 минут.
.Залить в смеситель 20-30 литров воды, интенсивно перемешивая раствор ввести в него небольшими порциями расчетное количество бентонита. Раствор перемешивать не менее 5 минут, после чего произвести отбор полученной краски для контроля плотности. Отбор краски из смесителя производить открытием вентиля в нижней части смесителя.
|
.При необходимости довести плотность теплоизоляционного покрытия до требуемых параметров (1,10-1,15 г/см³).
5.6.Теплоизоляционное покрытие должно быть однородным, не содержать сгустков и комков, плотность краски (покрытия) определять с помощью денсиметра.
.Приготовление противопригарной краски:
.Состав противопригарной краски приведен ниже в таблице 4:
Табл.4
Графит черный | -70% | - 120 кг. |
Пылевидный кварц | - 10% | - 17 кг. |
Стекло жидкое | - 10% | - 17 кг. |
Бентонит | - 10% | - 17 кг. |
Вода (всверх100%) до плотности 1,25-1,28 г/см³. |
.Залить в смеситель для противопригарной краски 60-80 литров воды и 17 килограмм жидкого стекла, интенсивно перемешать раствор в течение 2-3 минут.
.Продолжая интенсивное перемешивание раствора, ввести в него небольшими порциями предварительно взвешенное количество пылевидного кварца и бетонита. Перемешать полученный раствор в течение не менее 5 минут.
.Залить в смеситель дополнительно 30-40 литров воды, интенсивно перемешивая раствор загрузить в него мелкими порциями расчетное количество графита черного. После окончания загрузки графита перемешать раствор в течение не менее 15 минут, после чего произвести отбор полученной краски для контроля ее плотности. Отбор краски из смесителя производить открытием вентиля в нижней части смесителя.
.При помощи денсиметра произвести контроль плотности краски, при необходимости довести ее водой до требуемых параметров (1,25-1,28 г/см³.).
6.6.Краска должна быть однородной, не содержать сгустков и комков, плотность краски должна соответствовать требуемым параметрам.
.Краску (покрытие) хранить в закрытой металлической емкости. Время хранения краски практически не ограничено.
.Перед использованием краску (покрытие) следует интенсивно перемешать в течение не менее 15 минут и замерить плотность.
.Нанесаение теплоизоляционного покрытия и противопригарной краски на рабочие поверхности кокилей.
.Рабочие поверхности верхней и нижней половины кокиля очистить металлической щеткой от ржавчины, мусора, остатков предыдущих покрытий. При помощи воздушного инжектора удалить с рабочей поверхности кокилей пылевидные остатки материалов.
.Внимательно осмотреть состояние рабочих поверхностей кокилей. Рабочие поверхности не должны иметь трещин, разгара, поднутрений, заливов металла, наслоений предыдущих слоев краски.
.В течение 1,5-2 часов произвести равномерный газовый нагрев кокилей.
.Температуру нагрева кокиля контролировать контактной термопарой ТХА, закаченной в кокиль. При достижении температуры кокиля 110-150ºС отключить газ и приступить к нанесению красок на рабочие поверхности кокиля (максимально допустимая температура кокиля перед нанесением краски 180-200ºС.
|
.Вначале на разогретый кокиль наносится теплоизоляционное (белое) покрытие. Покрытие наносится на поверхность кокиля вручную инжекционным распылителем, угол наклона оси факела распыла к рабочей поверхности кокиля ~45º. Оптимальное расстояние от головки распылителя до окрашиваемой рабочей поверхности кокиля 180-200мм.
.Толщина слоя покрытия не должна вызвать искажение размеров отливок, слой краски должен быть равномерным, без наплывов и подтеков (ориентировочная толщина слоя - 0,2-0,5 мм.).
.В течение рабочей смены теплоизоляционное покрытие наносится на рабочую поверхность кокилей дважды: в начале смены и в середине.
.При помощи воздушного инжектора нанести на теплоизоляционное покрытие кокиля противопригарную (черную) краску. При этом необходимо соблюдать требования, аналогичные при нанесении теплоизоляционного покрытия - угол наклона оси факела распыла к рабочей поверхности кокиля ~45ºС, расстояние от головки распылителя до окрашиваемой рабочей поверхности кокиля 180-200мм. Слой краски должен быть равномерным, без наплывов и подтеков, ориентировочная толщина слоя - 0,2-0,5 мм.
.При помощи мостового крана и бесконечных цепных чалок грузоподъемностью 2,0-1,5 тонн произвести сборку кокиля.
.На предварительно разогретую до 110-150ºС литейную чашу нанести распылителем теплоизоляционное покрытие и противопригарную краску. Установить литейную чашу в собранный кокиль.
Заливка кокилей.
1.Требуемый химический состав чугуна и его ковшовая обработка (модифицирование) регламентированы данными таблицы 5:
Табл.5
Вид плавильного оборудования | Химический состав, % | Модификатор | ||||||
С | Si | Mn | Cr | P | S | Кол-во (%) | Марка | |
Индукцион-ная печь | 3,5-3,7 | 2,5-2,3 | 0,4-0,7 | до 0,20 | до 0,12 | до 0,10 | 0,4-0,3 | ФС 65 |
Коксовая вогранка | 3,3-3,6 | 2,4-2,2 | 0,5-0,7 | до 0,20 | до 0,20 | до 0,12 | 0,2-0,3 | ФС 65 |
Примечание: 1.в вариантах химического состава чугуна большему содержанию С соответствует меньшее содержание Si и наоборот.
.размер кусков модификатора ФС 65 - 1-8 мм, модификатор вводить под струю металла при заполнении ковша.
.Чугун из ИЧТ-10 и коксовой вогранки выпускать в технически исправные крановые ковши Q=1,8 т., предварительно прогретые газовой горелкой до красного каления футеровки (800-900 ºС). Т чугуна на выпуске из ИЧТ-10 и вагранки - 1420-1450ºС.
.После заполнения барабанного кранового ковша Q=1,8 т. металлом в количестве 150-200кг. при помощи совковой лопаты ввести под струю модификатор ФС 65, предварительно подготовленный по фракционному составу и прогретый газовой горелкой до температуры не менее 100ºС. Расход модификатора - согласно таблице 5.
.Уровень металла в заполненном ковше не должен превышать 7/8 высоты ковша. Оперативно скачать шлак с ковша в шлаковую.
.Залить пробу чугуна «на отбел» и для экспресс-анализа химического состава металла.
.Допустимая величина отбела пробы - не более 1,0-1,5 мм., в случае превышения величины отбела пробы, произвести корректировку химического состава чугуна за счет увеличения содержания С и Si до эвтектического состава чугуна (Сσ +1/3 Si = 4,3%).
7.Подать мостовым краном или передаточной тележкой ковш с металлом в зону заливки кокилей.
.Температура заливки кокилей чугуна 1350-1300ºС (замер температуры производить оптическим пирометром).
.Время разливки модифицированного чугуна не должно превышать 12-15 минут, остаток металла слить с ковша в индукционные печи ИЧТМ-6 (ИЧТ-10) или в изложницы, предварительно подогретые до 100-150ºС и покрашенные кокильными красками.
.Заливку металла в кокиль производить равномерной струей, не прерывая металл на всем протяжении заливки. Высота струи металла должна быть минимальной и не превышать 80-100 мм. С целью предотвращения попадания в отливку неметаллических включений в течение всего периода заливки кокиля литниковую чашу держать наполненной жидким металлом в количестве не менее 2/3 ее высоты. Не допускать заливки металлом верхней поверхности (вентил, каналов) кокилей.
.После окончания заливки кокилей, установить ковш с остатками металла на землю, снять клещами вручную литейную чашу с кокиля.
.при помощи бесконечных чалок и мостового крана снять верхнюю половину кокиля.
.Выдержать отливку в кокиле в течении 1-2 минут, необходимых в соответствии с технологической картой для кристаллизации чугуна конкретного наименования отливки.
.Произвести вручную кантовку кокиля с отливкой на 180ºС, зафиксировать кокиль в этом положении при помощи фиксатора.
.С целью обеспечения и своевременного извлечения отливки из кокиля, производить одновременные синхронные удары двумя стальными кувалдами Q=5кг. по толкателям в кокиле (удары по толкателям производить крест на крест).
.После извлечения отливки из кокиля, необходимо вручную вернуть его в исходное положение (кантовку кокиля производить за цапфу, а не за сам кокиль). Зафиксировать кокиль вручную в рабочем положении при помощи фиксатора.
.Вследствие конструктивных особенностей кокилей некоторых наименований отливок (в частности - «Крышка магистрального люка») изменяется порядок извлечения отливки из кокиля. А именно, после охлаждения (выдержки) отливки в кокиле в течение 1 минуты и удаления клещами вручную литейной чаши при помощи мостового крана и бесконечных цепных чалок, снять за цапфы верхнюю половину кокиля с отливкой.
.Соблюдая меры предосторожности и правила техники безопасности с помощью системы толкателей и стальной кувалды произвести выбивку отливки из кокиля.
.Если в конструкции кокиля не предусмотрена система толкателей или если их применение не обеспечивает извлечение отливки из кокиля аварийную выбивку отливки производить при помощи стального ломика длиной 0,5-1,0м. (в зависимости от конструкции кокиля) и стальной кувалды Q= 3-5кг.
.Перед каждой заливкой кокиля на его рабочие поверхности и литниковую чашу наносить противопригарную (черную) краску.
.После каждой заливки кокиля контролировать визуально качество противопригарного покрытия. В случае неоднородности покрытия, наличия подтеков и наплывов краски произвести очистку старого покрытия кокиля металлической щеткой. После чего нанести на рабочую поверхность теплоизоляционное (белое) покрытие и противопригарную краску.
.В ходе эксплуатации кокилей контролировать их температуру нагрева (контроль производить термопарой ТХА). Рабочая температура кокиля должна находиться в пределах 110-150ºС, для получения тонкостенных отливок из серого чугуна без отбела температуру кокиля следует превысить до 150-220ºС.
.При превышении рекомендуемой температуры кокиля, заливку кокилей металлом временно прекратить, полуформы кокиля раскрыть чтобы ускорить теплоотвод и охлаждение кокилей.
.В середине смены обязательно нанести на очищенную от старой краски поверхность кокиля теплоизоляционное (белое) покрытие, а затем - противопригарную краску.
Требования безопасности
Требования безопасности при производстве кокильного литья.
1.Работники, задействованные в производстве кокильного литья из чугуна (вагранщик, заливщик, плавильщик, кокильщик сборщик) должны быть обеспечены соответствующими средствами индивидуальной защиты (СИЗ).
.Перед началом работы кокильщик сборщик обязан:
а) проверить исправность кокильной оснастки, то есть, прежде всего, убедиться в отсутствии трещин разгара, выбоин на рабочих поверхностях кокиля, а также - отсутствие остатков чугуна «приваренного к кокилю в результате предыдущей заливки»;
б) проверить исправность газовой горелки воздушных инжекторов (распылителей), приводов кокильных машин, инструментов и приспособлений. Они должны быть технически исправны и пригодны к применению. Кроме того, инструменты, непосредственно контактирующие с жидким чугуном в процессе изготовления кокильного литья (ломики, клещи) должна быть предварительно нагретыми до температуры 100-110° и покрашенными кокильными красками.
в) убедиться в исправности освещения рабочего места и приточной вытяжной вентиляционной системой.
г) подготовить рабочее место к работе в частности убедиться в отсутствии влаги, убрать смесь металла, шлак и мусор. Убрать все посторонние предметы с пути транспортировки расплава чугуна.
.Во время работы кокильщик сборщик обязан:
а) во избежании ожогов работать в спецодежде согласно существующих норм и правил, а также с применением СИЗ, в частности в защитных очках или с защитным щитом.
б) не допускать заливку металла в холодный кокиль
в) с целью исключения возможности «приваривания» отливки к кокилю производить своевременную покраску кокиля и не превышать его допустимую температуру нагрева
г) прекратить эксплуатацию кокиля для устранения неисправностей, в случае если металл течет по разъему кокиля или происходит кипение металла в кокиле
д) систематически убирать из-под ног смесь пролитого металла.
.После окончания работы кокильщик сборщик обязан:
а) убрать рабочее место, проверить техническое состояние кокильной оснастки, оборудования, инструмента, приспособлений
б) сдать рабочее место мастеру, сообщив об имевших место в течение смены неисправностях и неполадках
.Заливщик металла перед началом работы обязан:
а) проверить состояние футеровки крановых ковшей используемых для заливки кокилей
б) проверить техническую исправность крановых ковшей, состояние корпуса траверса и механизмы наклона ковша, наличие количества крепежных болтов, исправность защелки фиксатора траверсы, о всех выявленных недостатках проинформировать мастера (старшего мастера). К работе приступить после устранения неполадок.
в) убедиться в отсутствии посторонних предметов на пути транспортировки жидкого металла
г) нагреть до 100-150° кокильные счищения и покрасить противопригарными красками.
Во время работы заливщик обязан:
а) на выпуске металл направлять струю строго по центру ковша
б) заполнять ковш металлом на более 150-250 мм до верха ковша
в) не заливать металл в холодные или не покрашенные кокиля
г) не допускать нахождение посторонних людей в зоне заливки.
По окончанию работы заливщик обязан:
Очистить рабочее место, убрать в специальное место инструмент и приспособления.
Литература
1.Сосненко М.И. Святкин Б.К. Общая технология литейного производства.
.Святкин Б.К. Егорова М.Б. Производство отливок в кокили.
.Технологическая инструкция РУП ГЛЗ «Центролит»
Введение
Литейное производство является одним из самых древних видов обработки металлов. Археологические исследования показывают, что уже за 5000 лет и более до нашей эры в древних центрах человеческой культуры литейное ремесло и искусство достигли высокого уровня. Об этом свидетельствуют найденные при раскопках древних городов античные вазы-амфоры, статуи и предметы домашнего обихода. Установлено, что первым литейным материалом была бронза.
В последние годы была найдено много стоянок древнего человека, на которых обнаружили литые наконечники копий и предметы домашней утвари. Это дало основание считать, что уже в последнюю эпоху каменного века предки умели выплавлять металл, владели литейным ремеслом. Археологи установили, что на берегу Исетского озера был металлургический «завод» с законченным циклом производства. Здесь отливали топоры, наконечники стрел, украшения и предметы домашнего обихода. Сейчас на этом месте установили своеобразный памятник древним металлургам.
Наивысшего расцвета литейное дело достигло в конце ХII - начало ХIII веков, когда стали применять двухсторонние формы из твердых пород камня, снабженные разветвленными литниковыми системами. Формовку производили в глине, а плавку металла в тиглях, для контроля жидкотекучести применяли специальные технологические пробы.
Параллельно с развитием технологии литейного производства происходило освоение новых литейных материалов (сплавов) чугуна, стали, ковкого чугуна, алюминиевых, магниевых и других цветных сплавов на основе редких металлов.
При современном уровне развития техники машины являются неотъемлемой частью нового вида производства. Повышая производительность труда и качества выпускаемого вида продукции, машины обеспечивают высокие темпы развития всех отраслей народного хозяйства нашей страны.
Процесс создания машины начинается в техническом отделе завода, а затем в цеховых технологических бюро, где технологи разрабатывают наиболее рациональные процессы производства отдельных деталей и сборки машины с учетом имеющихся на данном предприятии производственных условий и создают механическую документацию, определяющую характер и особенности производственных процессов, связанных с выпуском машин.
Заготовки деталей машин и другие металлические изделия можно получить различными способами: ковкой, сваркой, штамповкой. Однако наиболее распространенным и самым дешевым способом их производства следует считать литье, характерной особенностью которого является универсальность, возможность получать самые разнообразные по конфигурации и технологическим свойствам фасонные отливки из чугуна, стали и сплавов известных металлов.
В литейных цехах фасонные отливки получают путем заливки расплавленного расплава в песчано-глинистую форму. Такая форма служит для изготовления одной отливки и называется разовой.
Высокие механические и эксплуатационные свойства отливки обуславливают их широкое применение в различных отраслях промышленности и особенно в станкостроении, где литые детали составляют до 90% массы металлорежущего станка. Учитывая это, литейное производство по праву считают основой машиностроения.
В современных условиях литейные цеха машиностроительных заводов, а также входящие в структуру металлургических, строительных и других предприятий, производят фасонные отливки, масса которых колеблется в широких пределах - от нескольких граммов до 300 тонн. С учетом массы чугунные и стальные отливки принято подразделять на группы: мелкие до 100кг, средние до 1000 кг, крупные до 5000 кг, тяжелые до 15000 кг и особо тяжелые свыше 15000 кг.
Литейное производство характеризуется трудоемкостью, серийностью и номенклатурой выпускаемых отливок. Под трудоемкостью понимают время, затрачиваемое для производства отливок, под серийностью - количество ежемесячно выпускаемых одинаковых отливок, а под номенклатурой - их разнообразие.
Различают следующие основные типы литейного производства: единичное, серийное и массовое.
Единичное (индивидуальное) производство характеризуется выпуском в небольших количествах самых разнообразных отливок. При этом производство отдельных отливок может периодически повторяться. Примером единичного производства может служить выпуск отливок для ремонтных целей в литейных мастерских небольшой мощности или очень крупных единичных отливок массой в несколько десятков тонн (детали мощных экскаваторов, корпуса крупных турбин).
Серийное производство характерно периодическим выпуском отливок огромной или широкой номенклатурой, значительными или небольшими партиями. Примером серийного производства является выпуск отливок для различных типов металлорежущих станков в литейных цехах станкостроительных заводов. С учетом объема и номенклатуры выпуска отливок серийное производство принято подразделять на мелкосерийное и крупносерийное.
Массовое производство характеризуется непрерывным выпуском отливок предельной номенклатуры в больших количествах. Примером массового производства служит выпуск отливок литейными цехами автомобильных и тракторных заводов.
Тип производства оказывает большое влияние на выбор методов литья и технологию производства отливок, на характер производственного оборудования и организацию труда в литейном цехе.
Если единичное производство характеризуется применением ручных методов труда, частичной механизацией производственных процессов и незначительным количеством применяемой модельно-литейной технологической оснастки, то в серийном и особенно в массовом производстве рационально применять наиболее технически современное и высокопроизводительное оборудование, большое количество специальных приспособлений и приборов обеспечивающих качественное выполнение операций.
Литейные сплавы и их свойства
Наряду с физическими (плотность, теплопроводимость, температура плавления), механическими (прочность, твердость, пластичность) свойствами литейные сплавы должны также обладать определенными технологическими свойствами, основными из которых являются жидкотекучесть, усадка, склонность к ликвации и поглощению газов.
Жидкотекучесть - способность расплава полностью заполнять любые очертания полости формы. При недостаточной жидкотекучести расплав заполняет форму частично, отливка получается с недоливом и бракуется. Жидкотекучесть, прежде всего, зависти от химического состава сплава, то есть от того, какие и в каком количестве элементы входят в сплав. Известно, что фосфор улучшает, а сера ухудшает жидкотекучесть серого чугуна.
|
|
Опора деревянной одностоечной и способы укрепление угловых опор: Опоры ВЛ - конструкции, предназначенные для поддерживания проводов на необходимой высоте над землей, водой...
Семя – орган полового размножения и расселения растений: наружи у семян имеется плотный покров – кожура...
Кормораздатчик мобильный электрифицированный: схема и процесс работы устройства...
Особенности сооружения опор в сложных условиях: Сооружение ВЛ в районах с суровыми климатическими и тяжелыми геологическими условиями...
© cyberpedia.su 2017-2024 - Не является автором материалов. Исключительное право сохранено за автором текста.
Если вы не хотите, чтобы данный материал был у нас на сайте, перейдите по ссылке: Нарушение авторских прав. Мы поможем в написании вашей работы!