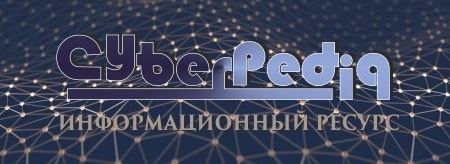
Папиллярные узоры пальцев рук - маркер спортивных способностей: дерматоглифические признаки формируются на 3-5 месяце беременности, не изменяются в течение жизни...
Своеобразие русской архитектуры: Основной материал – дерево – быстрота постройки, но недолговечность и необходимость деления...
Топ:
Марксистская теория происхождения государства: По мнению Маркса и Энгельса, в основе развития общества, происходящих в нем изменений лежит...
Установка замедленного коксования: Чем выше температура и ниже давление, тем место разрыва углеродной цепи всё больше смещается к её концу и значительно возрастает...
Теоретическая значимость работы: Описание теоретической значимости (ценности) результатов исследования должно присутствовать во введении...
Интересное:
Подходы к решению темы фильма: Существует три основных типа исторического фильма, имеющих между собой много общего...
Финансовый рынок и его значение в управлении денежными потоками на современном этапе: любому предприятию для расширения производства и увеличения прибыли нужны...
Лечение прогрессирующих форм рака: Одним из наиболее важных достижений экспериментальной химиотерапии опухолей, начатой в 60-х и реализованной в 70-х годах, является...
Дисциплины:
![]() |
![]() |
5.00
из
|
Заказать работу |
Содержание книги
Поиск на нашем сайте
|
|
Наиболее эффективный расширяющий компонент – трехсульфатный гидросульфоалюминат кальция. Состав цемента дает возможность регулировать количество и скорость образования кристаллов гидросульфоалюмината кальция и избежать появления вредных напряжений, вызывающих растрескивание затвердевшего цементного камня.
Водонепроницаемый р. ц. (ВРЦ) – является быстросхватывающимся и быстротвердеющим гидравлическим вяжущим. Получается путем смешивания глиноземистого цемента (70%), гипса (20%) и молотого высокоосновного гидроалюмината кальция (10%).
Гипсоглиноземистый р. ц. - быстротвердеющее гидравлическое вяжущее, получаемое совместным тонким измельчением высокоглиноземистых клинкера или шлака и природного двуводного гипса. Обладает свойством расширения при твердении в воде; при твердении на воздухе проявляет безусадочные свойства.
Расширяющийся портландцемент (РПЦ) – гидравлическое вяжущее вещество, получаемое совместным тонким измельчением портландцементного клинкера – 58-63, глиноземистого шлака или клинкера – 5-7, гипса – 7-10, активной минеральной добавки – 23-28. РПЦ отличается быстрым твердение в условиях кратковременного пропаривания, высокой плотностью и водонепроницаемостью цементного камня и способностью расширяться в водных условиях при постоянном увлажнении в течение первых 3 суток.
Напрягающий цемент – состоит из 65-75% портландцемента, 13-20% глиноземистого цемента и 6-10% гипса; затворенный водой сначала твердеет и набирает прочность, затем расширяется и напрягает железобетон.
49. Методика определения истинной плотности материала.
Истинной плотностью называется масса единицы объема материала в абсолютно плотном состоянии, т.е. без учета пор и пустот.
Истинная плотность определяется по формуле: ρ=m/V, [г/см3],
где m - масса образца, г; V - объем образца в абсолютно плотном состоянии, см3.
Материалы для определения истинной плотности дробят, размалывают до тонкого порошка и высушивают при температуре 105-1100С до постоянной массы. Истинную плотность можно определить при помощи объемомера Ле-Шателье (рис. 1), руководствуясь ГОСТ в соответствии с методиками.
Рис.1. Приборы для определения истинной плотности: Ле-Шателье.
Объемомер заполняют до нулевой риски жидкостью, инертной к исследуемому материалу, причем уровень жидкости устанавливают по касательной к вогнутому мениску. Горловину прибора тщательно просушивают бумагой. Для испытания берут навеску порошка 70 - 90 г. Навеску порошка взвешивают в чаше на технических весах с точностью до 0,01 г, после чего постепенно всыпают в объемомер небольшими порциями, чтобы не произошло образования пробок. Порошок прекращают всыпать после того, как уровень жидкости поднимается до черты с делением 20 мл (см3) или выше, в пределах градуированный части прибора. Оставшуюся часть порошка взвешивают и по разности масс определяют массу порошка, всыпанного в обьемомер. Вычисление плотности с точностью до 0,01 г/см3 производится по формуле
|
, [г/см3], где m1– масса порошка с чашкой, в которой взвешивался порошок, г;m2 - масса остатка порошка с чашкой, г; V - объем жидкости, вытесненной всыпанным порошком, см3.
Для получения достоверного результата проводится не менее трех испытаний и за окончательный результат принимается среднее арифметическое значение.
50. Методика определения средней плотности материала.
Средней плотностью называют массу единицы объема материала в естественном состоянии, т.е. вместе с порами и пустотами. Средняя плотность определяется по формуле: р0 , [г/см3],
где m - масса образца, г; V - объем образца в естественном состоянии, см3.
Для вычисления средней плотности материала определяют массу образца и его объем в естественном состояния. Одно и то же количество материала в естественном состояние занимает больший объем, чем в плотном. Поэтому средняя плотность каменных материалов всегда меньше истинной плотности.
В практике определения средней плотности твердого материала возможны два случая:
а)образец материала имеет правильную форму;
б)образец имеет неправильную форму.
1(а) Определение средней плотности образцов правильной формы
Образцы правильной геометрической формы должны иметь наименьшее измерение не менее 10 см, если материал пористый, и не менее 4 см, если материал плотный. Испытания проводят на 5-ти образцах кубической или цилиндрической формы. Образцы взвешивают на технических весах с точностью до 0,1 г, (если масса образца менее 500 г). Перед взвешиванием образцы должны быть высушены до постоянной массы.
|
Для определения объема образцы измеряют с помощью штангенциркуля с точностью до 0,1 мм.
Для обеспечения точности результатов среднюю плотность вычисляют как среднее арифметическое пяти определений.
2(б). Определение средней плотности образцов неправильной формы
При работе с образцами неправильной формы, сложность представляет измерение объема. В этом случае определение производят методом гидростатического взвешивания или с помощью объемомера.
Точность такого определения в значительной степени зависит от пористости материалов, так как образец, погружаемый в воду, не только вытесняет, но и частично впитывает ее в свои поры, а это приводит к искажению результатов.
51. Методика определения насыпной плотности материала.
Насыпная плотность - отношение массы зернистых материалов в виде порошка или гранул ко всему занимаемому ими объему, включая и пространства между частицами.
Ход работы:
Песок высушивают до постоянной массы и просеивают через сито с диаметром отверстия 5 мм, затем засыпают в стандартную воронку, имеющую в нижней части затвор.
Под воронку устанавливают сосуд, имеющий емкость I л и заранее взвешенный. Открывают затвор воронки, медленно заполняют сосуд с высоты 10 см до образования пирамидки над сосудом. Не передвигая сосуд, излишки песка снимают вровень с краями металлической линейкой, после чего сосуд с песком взвешивают.
Насыпную плотность (m) определяют в г/см3 или в кг/м3 как среднее арифметическое результатов трех измерений.
52 (53). Методика определения водопоглощения по массе (по объему) материала.
Испытание производят на образцах в виде куба с ребром 40 - 50 мм или в виде цилиндра, имеющего одинаковые диаметр и высоту. Допускается определение водопоглощения материала на образцах, имеющих неправильную геометрическую форму и массу не менее 200 г.
Образцы в количестве 5 шт. перед испытанием предварительно высушивают при температуре плюс (110±5)°С до постоянной массы.
Взвешивание образцов производят после их остывания на воздухе. Подлежащие испытанию образцы укладывают в сосуд с водой температурой 15-20°Св один ряд на решетку так, чтобы уровень воды в нем был выше верха образцов на 2 - 10 см. Образцы средней плотностью менее 1000 кг/м3пригружают, чтобы они не всплывали. Их выдерживают в воде в течение 48 ч, затем вынимают из сосуда, обтирают влажной тканью и немедленно взвешивают. Массу воды, вытекшей из образца на чашку весов, включают в массу насыщенного водой образца. Водопоглощение по массе и объему вычисляют по формулам: W=(m1-m)/V, где m - масса сухого образца, г; m1 – масса насыщенного водой образца, г; Vo-объем образца, м3. с точностью до 0,1%. За окончательный результат принимают среднее арифметическое пяти определений для образцов горных пород.
|
Для ускоренного определения водопоглощения каменных материалов применяют способ кипячения. Высушенные до постоянной массы образцы погружают в сосуд с водой и нагревают до температуры кипения. Кипятят образцы в течение 4 ч, после чего их охлаждают до температуры 20 - 30°С путем доливания в сосуд холодной воды. Образцы поочередно вынимают, обтирают влажной тканью, взвешивают и вычисляют водопоглощение.
54. Методика определения прочности при сжатии горной породы.
Образец изолируют от жидкости, передающей гидростатическое давление, либо вместе с приложенными к его торцам стальными плитами (при изоляции боковых поверхностей образца и плит трубчатой резиной), либо отдельно от них сплошным покрытием образца двух-трехкратным слоем клея.
Изолированный образец устанавливают в рабочую полость камеры объемного сжатия в сборе с плитами или прокладывая их между торцами образца и опорными торцами нагрузочных элементов камеры.
Поддерживая заданное значение бокового давления с погрешностью ± 5 %, нагружают образец вдоль оси до разрушения равномерно со скоростью нагружения 1-5 МПа/с. Момент разрушения фиксируют по максимальному значению осевой нагрузки.
Предел прочности при объемном сжатии () в мегапаскалях при заданном значении бокового давления для каждого образца вычисляют по формуле
где Р - разрушающая сила, приложенная к торцам образца, кН;
S - площадь поперечного сечения образца, см2.
Обработку результатов испытаний n образцов производят в следующем порядке.
Вычисляют среднее арифметическое значение предела прочности по пробе, среднее квадратическое отклонение и коэффициент вариации V:
Вычисления производят:
площади поперечного сечения образца, частных и среднего арифметического значений, а также среднего квадратического отклонения предела прочности - до третьей значащей цифры; коэффициента вариации - до целого числа.
Результаты испытаний представляют средними значениями предела прочности , бокового давления p и коэффициента вариации V.
55. Методика определения открытой пористости материала.
Пористость П – степень заполнения объема материала порами. П=(1-ρ0/ρ)*100; где ρ0 - средняя плотность материала, ρ0= m/V, ρ – истинная плотность, ρ= (m-m1)/V, m–масса измельченного материала, m1–остаток после всыпания в прибор, V–объемом вытесненной жидкости.
Для определения О.П. строительных материалов их высушивают до постоянной массы, насыщают жидкостью, чаще всего водой, и взвешивают. Разность масс сухого и водонасыщенного материала дает массу воды, заполнившей поры материала. Так как масса 1м3 воды составляет 1000кг, то величину массы воды, заполнившей поры, принимают за оюъем открытых пор. Пот=((mнас-mсух)/Vест)*100
56. Методика определения закрытой пористости материала.
|
З.П.-один из показателей свойств огнеупорных изделий и кусковых материалов. З.П. определяют как отношение объемов закрытых пор материала, выраженное в процентах.
Закрытая пористость характеризуется наличием в теле материала замкнутых пор и воздушных включений, не сообщающихся между собой. Закрытую пористость вычисляют как разность между общей и открытой пористостью.
57. Методика определения истираемости горных пород.
Перед испытанием образцы взвешивают и измеряют площадь истираемой грани. Образцы устанавливают в специальные гнезда круга истирания. После установки проверяют возможность свободного перемещения образцов в гнездах в вертикальной плоскости. К каждому образцу (по центру) прикладывают сосредоточенную вертикальную нагрузку величиной (300±5) Н, что соответствует давлению (60±1) кПа. На истирающий диск равномерным слоем насыпают первую порцию (20±1) г шлифзерна 16 (на первые 30 м пути истирания каждого образца). После установки образца (образцов) и нанесения на истирающий диск абразива включают привод круга и производят истирание. Через каждые 30 м пути истирания, пройденного образцами, истирающий диск останавливают. С него удаляют остатки абразивного материала и истертого в порошок бетона и насыпают на него новую порцию абразива и снова включают привод истирающего круга. Указанную операцию повторяют 5 раз, что составляет 1 цикл испытаний (150 м пути испытания). После каждого цикла испытаний образец (образцы) вынимают из гнезда, поворачивают на 90° в горизонтальной плоскости и проводят следующие циклы испытаний. Всего проводят 4 цикла испытаний для каждого образца (общий путь истирания равен 600 м). После 4 циклов испытания образцы вынимают из гнезд. Воздушно-сухие образцы обтирают сухой тканью и взвешивают. Водонасыщенные образцы помещают на 30 мин в воду, затем протирают влажной тканью и взвешивают. Истираемость бетона на круге истирания G1 в г/см2, характеризуемую потерей массы образца, определяют с погрешностью до 0,1 г/см2 для отдельного образца по формуле
где т 1 - масса образца до испытания, г; т 2 - масса образца после 4 циклов испытания, г; F - площадь истираемой грани образца, см2.
58. Методика определения водопоглощения керамического кирпича.
Средства испытания:
Сосуд с решеткой; электрошкаф сушильный с автоматической регулировкой температуры в пределах 100-110 °С.; весы.
Подготовка к испытанию:
Водопоглощение определяют не менее чем на трех образцах.
Образцы керамических изделий предварительно высушивают до постоянной массы.
Проведение испытания:
Образцы укладывают в один ряд по высоте с зазорами между ними не менее 2 см на решетку в сосуд с водой, нагревают и доводят до кипения (приблизительно 1 ч), кипятят ч и оставляют на 16-19 ч остывать до температуры помещения
|
Образцы выдерживают в воде 48ч
Насыщенные водой образцы вынимают из воды, обтирают влажной тканью и взвешивают. Массу воды, вытекшей из образца на чашку весов, включают в массу образца, насыщенного водой. Взвешивание каждого образца должно быть закончено не позднее 2 мин после его удаления из воды. После взвешивания образцы силикатных изделий высушивают до постоянной массы
Водопоглощение (W) образцов по массе в процентах вычисляют по формуле
где m1 - масса образца, насыщенного водой, г;
m - масса образца, высушенного до постоянной массы, г.
За значение водопоглощения изделий принимают среднее арифметическое результатов определения водопоглощения всех образцов, рассчитанное с точностью до 1%.
59. Методика определения марки кирпича по прочности.
Марку кирпича определяют испытанием специально подготовленных образцов из кирпича на сжатие и изгиб.
Кирпич распиливают пополам и склеивают между собой быстротвердеющим раствором марки 100 кгс/см2, верхнюю и нижнюю грани образца выравнивают этим же раствором, используя стеклянные пластины и смоченные листы бумаги. Грани, образовавшиеся при распиливании кирпича, должны быть обращены в противоположные стороны. Толщина слоя раствора 3 - 5мм. Выравнивание поверхностей образца, соприкасающихся с прессом при испытании, обеспечит равномерную передачу нагрузки на образец. После затвердевания раствора образец устанавливают под пресс, нагрузку на образец подают плавно и фиксируют разрушающую нагрузку Рразр (кН). Предел прочности при сжатии Rсж (Мпа) определяют по формуле:
Rсж=10 Рразр / F (МПа),
Прочность при сжатии кирпича вычисляют как среднее арифметическое результатов испытаний 5 или 3 образцов.
Предел прочности при изгибе определяют путем испытания целого кирпича на гидравлическом прессе с максимальным усилием 25-50 кН. Образец устанавливают на 2 шаровые опоры, нагрузка передается так же через шаровую опору, расположенную в середине кирпича. Для равномерного распределения нагрузки во время испытания образцов на них предварительно наносят три выравнивающие полоски шириной 20..30 мм под опоры. Расстояние между опорами 200 мм, диаметры шарнирных опор 20..30 мм. Предел прочности образца при изгибе Rн, МПа, вычисляют по формуле: Rн=30Pразрl/2bh2,
Предел прочности кирпича при изгибе определяют как среднее арифметическое результатов испытаний 5 или 3 образцов. По результатам испытаний устанавливают марку кирпича.
60. Методика определения нормальной густоты гипсового теста.
Определение нормальной густоты гипсового теста сводится к установлению количества воды (в см3 на 100 г гипса), необходимого для придания гипсовому тесту определенной пластичности.
Определение нормальной густоты гипсового теста производится с помощью вискозиметра Суттарда, который состоит из медного или латунного цилиндра, имеющего внутренний диаметр 5 см и высоту 10 см, и квадратного листового стекла со сторонами 20 см.
На стекле нанесен ряд концентрических окружностей метром 6—20 см, причем окружности диаметром до 15-20 см расположены через каждый 1 см, а от17 до 19 - через 0,5 см. Перед испытанием цилиндр и стекло увлажняют мягкой тканью, смоченной в чистой воде. Стеклянная пластинка кладется строго горизонтально, цилиндр ставится в центр концентрических окружностей.
При определении густоты гипсового теста готовится смесь гипса с водой в количестве, достаточном для заполнения цилиндра. Для этого отвешивают 300 г гипса и, добавляя его постепенно к воде, быстро размешивают в течение 30 с до получения однородного теста. Затем, сделав два резких перемешивания, быстро выливают массу в цилиндр, поставленный на стекло, и ножом сравнивают поверхность гипса с краями цилиндра (на это затрачивается не более 15 с). Резким вертикальным движением поднимают цилиндр, тесто разливается на стекло в конусообразную лепешку, величина которой обуславливается консистенцией теста. Требуемой густотой обладает тесто, которое дает лепешку диаметром около 1 см. Если тесто расплывается в лепешку диаметром менее 18 см, испытание повторяют, увеличивая количество воды затворения; если диаметр лепешки более 18 см количество воды затворения уменьшают.
Нормальная густота гипсового теста выражается числом кубических сантиметров воды, приходящейся на 100 г гипса.
61. Методика определения сроков схватывания гипсового вяжущего.
Сроки схватывания гипсового вяжущего зависят от нескольких факторов, наиболее важные из которых: вид вяжущего вещества, водогипсовое отношение, тонкость помола и др. Сроки схватывания гипсового вяжущего определяются на приборе Вика.
Всыпать гипс надо по возможности равномерно в течение 30 сек. После этого массу немедленно выливают в форму (усеченный конус) прибора Вика, избыток срезают ножом и выравнивают поверхность. Для удаления вовлеченного воздуха гипсовое тесто в форме встряхивается 4-5 раз.
Форма помещается под иглу прибора Вика, затем игла прибора доводится до соприкосновения с поверхностью гипсового теста в форме и закрепляется винтом подвижного стержня. Испытания проводятся через каждые 30 сек - игла опускается в гипсовое тесто каждый раз в новое место. После погружения игла тщательно вытирается.
При этом отмечаются два момента: первый, когда игла не доходит до дна формы, и второй, когда игла опускается в тесто не более чем на 1 мм. За начало схватывания гипсового теста принимается период времени от момента затворения гипсового вяжущего водой до момента, когда свободно опущенная игла после погружения в тесто первый раз не дойдет до поверхности стеклянной пластинки (до дна формы). За конец схватывания гипсового теста принимается период времени с момента затворения гипсового вяжущего водой до момента, когда свободно опущенная игла погружается в тесто на глубину не более 1 мм от поверхности.
Сроки схватывания гипсового вяжущего выражают в минутах.
62. Методика определения водостойкости гипсового камня.
Степень водостойкости искусственного камня на основе гипсовых вяжущих веществ оценивают по коэффициенту размягчения. Чтобы узнать коэффициент водостойкости испытывают с определением прочностных показателей три образца из гипса, высушенных до постоянной массы при температуре не выше 60 °С, и три идентичных образца – в водонасыщенном состоянии. Насыщают образцы гипса, выдерживая их в воде в течение 2 ч, предварительно высушив до пост. массы при температуре не выше 60 °С.
Коэффициент размягчения вычисляют как частное от деления предела прочности при сжатии водонасыщенных образцов на предел прочности при сжатии образцов в сухом состоянии с погрешностью 0,01.
Rнасыщ. - предел прочности при сжатии насыщенных образцов, МПа;
Rсух. - предел прочности при сжатии образцов, высушенных до постоянной массы, МПа.
63. Методика определения тонкости помола гипсового вяжущего и портландцемента.
50 г гипса, предварительно высушенного в сушильном шкафу в течение 1 часа при температуре 50—55° С, просеивают сквозь сито с сеткой № 02. Просеивание гипса считается законченным, если в течение 1 мин сквозь сито проходит не более 0,05 г гипса. Контрольное просеивание производят на бумагу при снятом с сита донышке. Тонкость помола гипса (Т) определяется с точностью до 0,1% и вычисляется как остаток гипса на сите с сеткой № 02 в процентах от массы просеиваемой пробы по формуле
T=(g·100)/G
где g - масса остатка гипса на сите с сеткой № 02, г;
G - масса первоначальной навески гипса, г.
Для определения тонкости помола применяется сито с сеткой № 008, прибор для механического или пневматического просеивания цемента. Пробу цемента высушивают в сушильном шкафу при температуре 105–110 °С в течение 2 ч и охлаждают в эксикаторе. Затем отвешивают 50 г цемента с точностью до 0,01 г и высыпают его на сито. Закрыв сито крышкой, устанавливают его в прибор для механического просеивания. Через 5–7 мин от начала просеивания останавливают прибор, осторожно снимают донышко и высыпают из него прошедший через сито цемент. Сетку прочищают с нижней стороны мягкой кистью, вставляют донышко и продолжают просеивание. Просеивание считается законченным, если при контрольном просеивании сквозь сито проходит не более 0,05 г цемента. Контрольное просеивание выполняют вручную при снятом донышке на бумагу в течение 1 мин. Тонкость помола цемента должна быть такой, чтобы при просеивании через сито № 008 проходило не менее 85 % от массы пробы (ГОСТ 10178–85).
64. Методика определения марки по прочности гипсового вяжущего.
Сущность испытания заключается в определении пределов прочности стандартного образца-балочки размером 40 х 40 х 160 мм, которую испытывают на изгиб, а образовавшиеся половинки балочки — на сжатие.
Образцы формуют из теста стандартной консистенции. Для этого берут 1200 г гипса и количество воды, необходимое для получения теста нормальной густоты. Гипс всыпают в воду и интенсивно перемешивают в течение 60 с. Образцы формуют в трехгнездных формах, которые предварительно очищают и смазывают машинным маслом. Все три гнезда формы заполняют одновременно, для чего чашку с гипсовым тестом равномерно продвигают над формой. Для удаления воздуха заполненную форму встряхивают 5...6 раз.
После наступления начала схватывания излишки гипсового теста срезают линейкой. Через (15 ±5) мин после конца схватывания образцы извлекают из формы.
Испытания начинают через 2 ч после начала перемешивания.
Балочки устанавливают на опоры таким образом, чтобы те грани, которые были горизонтальными при изготовлении, при испытании находились бы в вертикальном положении. Предел прочности при изгибе испытываемого портландцемента вычисляют как среднее арифметическое из двух наибольших результатов испытаний трех образцов.
Предел прочности при сжатии определяется испытанием половинок образцов-балочек, получившихся после испытаний на изгиб (шесть штук). Для того чтобы результаты испытаний половинок балочек были сопоставимы, несмотря на разный размер, используют металлические накладки. Площадь поверхности накладок, соприкасающейся с образцом, равна 25 см2.
Образец с пластинками центрируют на опорной плите 5 пресса. Средняя скорость нарастания нагрузки на образец при испытании должна составлять (5 ± 1,25) кН/с. Предел прочности при сжатии Д.ж (МПа) каждого образца вычисляют по формуле
где F— разрушающая нагрузка, кН; А — площадь металлических пластинок, см.
Предел прочности при сжатии гипсовых образцов вычисляют по результатам испытаний как среднее арифметическое из четырех результатов.
Марку по прочности гипсового вяжущего устанавливают в соответствии с требованиями стандарта по наименьшему значению предела прочности при сжатии или изгибе.
65. Методика определения активности воздушной извести.
Навеску негашеной комовой или молотой извести массой 4–5 г предварительно растирают в течение 5 мин в фарфоровой ступке. Навеску растертой извести массой 1 г помещают в коническую колбу вместимостью 250 мл, добавляют 100–150 мл дистиллированной воды, кладут 3–5 стеклянных бус или оплавленных стеклянных палочек длиной 5– 7 мм, закрывают стеклянной воронкой или часовым стеклом и нагревают 5–7 мин до температуры кипения. Раствор охлаждают до температуры 20–30º С, промывают стенки колбы и стеклянную воронку (или часовое стекло) кипяченой дистиллированной водой, добавляют 2–3 капли 1 %-ного спиртового раствора фенолфталеина и титруют при постоянном взбалтывании 1н раствором соляной кислоты HCl до полного обесцвечивания раствора. Титрование считают законченным, если в течении 8 минут при периодическом взбалтывании раствор остается бесцветным.
Содержание CaO и MgO в процентах по массе (активность) А определяют по формуле:
А = V· 2,804∙ K/ G,
где V – количество 1 н раствора соляной кислоты, пошедшее на титрование, мл; K – поправка к титру 1н раствора соляной кислоты; 2,804 – количество оксида кальция, соответствующе 1 мл 1 н раствора соляной кислоты, умноженное на 100; G – навеска извести, взятая для титрования, г.
66. Методика определения содержания в извести непогасившихся зерен.
В металлический сосуд цилиндрической формы вместимостью 2—3 л наливают 1—1,5 л нагретой до температуры 85—90° С воды и всыпают 0,2 кг извести, непрерывно перемешивая содержимое до окончания интенсивного выделения пара (кипения). Полученное тесто закрывают крышкой и выдерживают два часа, затем разбавляют холодной водой до консистенции известкового молока и промывают на сите с сеткой № 063 слабой непрерывной струей, слегка растирая мягкие кусочки стеклянной палочкой с резиновым наконечником. Остаток на сите высушивают при температуре 140—150° С до постоянной массы. Содержание непогасившихся зерен в процентах вычисляют по формуле
НЗ=(m/М) 100%
где m — остаток на сите после высушивания, г
М – масса пробы, г
67. Методика определения нормальной густоты цементного теста.
Нормальной густотой цементного теста считают такую консистенцию его, при которой пестик прибора Вика, погруженный в форму, заполненную тестом, не доходит на 5-7 мм до пластинки, на которой установлена форма. Нормальную густоту цементного теста характеризуют количеством воды затворения, выраженным в процентах от массы цемента. Для ручного приготовления цементного теста отвешивают 400 г цемента, высыпают в чашу, предварительно протертую влажной тканью. Затем делают в цементе углубление, в которое вливают в один прием воду в количестве, необходимом (ориентировочно) для получения цементного теста нормальной густоты. Углубление засыпают цементом и через 30 с после прилипания воды сначала осторожно перемешивают, а затем энергично растирают тесто лопаткой. Продолжительность перемешивания и растирания составляет 5 мин с момента приливания воды. После окончания перемешивания форму быстро наполняют в один прием цементным тестом и 5-6 раз встряхивают его, постукивая пластинку о твердое основание. Поверхность теста выравнивают с краями формы, срезая избыток теста ножом, протертым влажной тканью. Немедленно после этого приводят пестик прибора в соприкосновение с поверхностью теста в центре кольца и закрепляют стержень стопорным устройством, затем быстро освобождают его и предоставляют пестику свободно погружаться в тесто. Через 30 с с момента освобождения стержня производят отсчет погружения по шкале. Форма с тестом при отсчете не должна подвергаться толчкам. При несоответствующей консистенции цементного теста изменяют количество воды и вновь затворяют тесто, добиваясь погружения пестика на глубину 5-7 мм до пластинки. Количество добавляемой воды для получения теста нормальной густоты определяют с точностью до 0,25 %.
68. Методика определения сроков схватывания портландцемента.
Иглу прибора Вика доводят до соприкосновения с поверхностью цементного теста нормальной густоты, приготовленного и уложенного в форму. В этом положении закрепляют стержень стопором, затем освобождают стержень, давая игле свободно погружаться в тесто. В начале испытания, пока тесто находится в пластичном состоянии, во избежание сильного удара иглы о пластинку допускается слегка ее задерживать при погружении в тесто. Как только тесто загустеет настолько, что опасность повреждения, иглы будет исключена, игле дают свободно опускаться. Момент начала схватывания определяют при свободном опускании иглы. Иглу погружают в тесто через каждые 10 мин, передвигая кольцо после каждого погружения для того, чтобы игла не попадала в прежнее место. После каждого погружения иглу вытирают. Началом схватывания цементного теста считают время, прошедшее от начала затворения (момента прилипания воды) до того момента, когда игла не доходит до пластинки на 2-4 мм. Концом схватывания цементного теста считают время от начала затворения до момента, когда игла опускается в тесто не более чем на 1-2 мм.
|
|
Особенности сооружения опор в сложных условиях: Сооружение ВЛ в районах с суровыми климатическими и тяжелыми геологическими условиями...
Организация стока поверхностных вод: Наибольшее количество влаги на земном шаре испаряется с поверхности морей и океанов (88‰)...
Папиллярные узоры пальцев рук - маркер спортивных способностей: дерматоглифические признаки формируются на 3-5 месяце беременности, не изменяются в течение жизни...
Индивидуальные очистные сооружения: К классу индивидуальных очистных сооружений относят сооружения, пропускная способность которых...
© cyberpedia.su 2017-2024 - Не является автором материалов. Исключительное право сохранено за автором текста.
Если вы не хотите, чтобы данный материал был у нас на сайте, перейдите по ссылке: Нарушение авторских прав. Мы поможем в написании вашей работы!