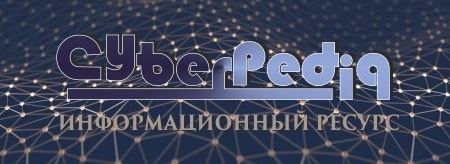
Адаптации растений и животных к жизни в горах: Большое значение для жизни организмов в горах имеют степень расчленения, крутизна и экспозиционные различия склонов...
Организация стока поверхностных вод: Наибольшее количество влаги на земном шаре испаряется с поверхности морей и океанов (88‰)...
Топ:
Установка замедленного коксования: Чем выше температура и ниже давление, тем место разрыва углеродной цепи всё больше смещается к её концу и значительно возрастает...
Организация стока поверхностных вод: Наибольшее количество влаги на земном шаре испаряется с поверхности морей и океанов...
Особенности труда и отдыха в условиях низких температур: К работам при низких температурах на открытом воздухе и в не отапливаемых помещениях допускаются лица не моложе 18 лет, прошедшие...
Интересное:
Отражение на счетах бухгалтерского учета процесса приобретения: Процесс заготовления представляет систему экономических событий, включающих приобретение организацией у поставщиков сырья...
Лечение прогрессирующих форм рака: Одним из наиболее важных достижений экспериментальной химиотерапии опухолей, начатой в 60-х и реализованной в 70-х годах, является...
Искусственное повышение поверхности территории: Варианты искусственного повышения поверхности территории необходимо выбирать на основе анализа следующих характеристик защищаемой территории...
Дисциплины:
![]() |
![]() |
5.00
из
|
Заказать работу |
|
|
Строительная сталь предназначается для изготовления строительных конструкций – мостов, газо- и нефтепроводов, ферм и т.д. Все строительные конструкции, как правило, являются сварными, и свариваемость – одно из основных свойств такой стали. К низколегированным строительным сталям относятся низкоуглеродистые стали, с содержанием углерода до 0,22-0,25%, содержащие легирующие элементы (обычно до 2,5 %) и обладающие повышенной прочностью и пониженной склонностью к хрупким разрушениям по сравнению с углеродистыми сталями. Строительные стали имеют феррито-перлитную зернистую структуру, причем, чем меньше зерно, тем лучше качество.
В качестве легирующих элементов используют марганец (до 1,8 %), кремний (до 1,2 %), хром (до 0,9 %), никель (до 0,8 %), медь (до 0,5 %), ванадий (0,05–0,15 %), ниобий (0,02–0,06 %), азот (до 0,025 %) и др. Легирующие элементы, растворяясь в феррите, упрочняют его (твердорастворное упрочнение). Наиболее существенно влияют кремний и марганец. Для измельчения зерна вводят сильные карбидо– и нитридообразующие элементы (ванадий, ниобий, титан). Это обеспечивает зернограничное и дисперсионное упрочнение за счет дисперсных частиц карбидов (VC,NbC,TiC), нитридов (VN,NbN,TiN), карбонитридов (V(C,N),Nb(C,N),Ti(C,N)). Для получения нитридов и карбонитридов в сталь вводится азот. Примером сталей с карбонитридным упрочнением могут служить стали 14Г2АФБ, 16Г2АФ, 15ГФ и др. Такие элементы, как марганец, хром, кремний, никель, бор, повышают устойчивость переохлажденного аустенита и обеспечивают получение дисперсной феррито-карбидной смеси.
Никель – дорогой и дефицитный легирующий элемент, его вводят в состав сталей для особо ответственных конструкций с целью повышения ударной вязкости и снижения порога хладноломкости. Для повышения коррозионной стойкости во влажной атмосфере сталь легируют медью (до 0,5 %) и фосфором (0,07–0,12 %). В качестве примера можно привести стали 10ХСНД и 10ХСДП.
|
Для повышения обрабатываемости резанием в жидкую сталь вводят кальций или церий. Низколегированные строительные стали подразделяются на стали повышенной прочности и высокопрочные.
Стали повышенной прочности
Как правило, строительные стали повышенной прочности (σТ≤ 400 МПа) поставляют в горячекатаном состоянии с феррито-перлитной структурой. Основными легирующими элементами в этих сталях являются марганец, кремний, хром, ванадий, ниобий, титан, медь, фосфор, иногда азот (в сочетании с ванадием и алюминием).
Упрочнение сталей при легировании в основном достигается вследствие твердорастворного упрочнения феррита растворенными в нем легирующими элементами. Для сталей с содержанием углерода 0,16 – 0,20 % некоторое упрочнение вносит перлитная составляющая структуры и здесь играет роль упрочнение вследствие повышения устойчивости переохлажденного аустенита при легировании и получения более дисперсных продуктов распада аустенита на феррито-карбидную смесь. Повышение содержания углерода приводит к снижению ударной вязкости и повышению порога хладноломкости. В сталях с ванадием и ниобием наблюдается дисперсионное упрочнение вследствие образования дисперсных карбидов и (или) карбонитридов ванадия и ниобия. При этом измельчается зерно (зернограничное упрочнение). Примерами сталей повышенной прочности являются 09Г2, 09Г2С, 10Г2С1, 17ГС, 15ГФ, 10ХНДП, 15ХСНД и др. Стали повышенной прочности поставляют в горячекатаном или нормализованном состоянии. Нормализация приводит к большей стабильности механических свойств, повышению пластичности, ударной вязкости и хладостойкости по сравнению с горячекатаным состоянием. Реже применяют улучшение (закалка с высоким отпуском). После улучшения получается дисперсная сорбитная структура. Стали повышенной прочности имеют предел текучести в 1,3–1,6 раз больше, чем углеродистая сталь ВСт3сп, что обеспечивает снижение массы металлоконструкций на 15–30 %. В отожженном состоянии стали принадлежат к доэвтектоидному классу; в нормализованном – к перлитному.
|
Высокопрочные стали
Высокая прочность (σТ= 400–750 МПа) в этих сталях должна сочетаться с малой склонностью к хрупкому разрушению, т.е. наряду с повышением прочности должна обеспечиваться высокая хладостойкость. Достичь этого довольно сложно. Существует четыре группы высокопрочных строительных сталей: стали с карбонитридным упрочнением, малоперлитные стали, стали бейнитного класса, стали мартенситного класса.
Для несварных конструкций можно использовать кипящую сталь. Для сварных расчетных конструкций – полуспокойную или спокойную сталь. Для ответственных конструкций или конструкций, работающих в условиях низких температур, необходимо использовать сталь в нормализованном состоянии или после термического улучшения. Для этих сталей также можно использовать технологию контролируемой прокатки, в результате получается структура с мелким зерном и дополнительным упрочнением.
Для армирования железобетонных конструкций применяют прутки и проволоку. Эти прутки находятся в сложнонапряженном состоянии, поэтому в таких конструкциях применяют высокопрочные стальные стержни и проволоку. Используют Ст5, 18Г2С, 35ГС, 20ХГ2Ц.
Получение изделий методами порошковой металлургии. Технологическая схема
получения порошковых материалов. Порошковые твердые сплавы: Штамповые стали. Стали для инструментов горячей обработки давлением. Стали для измерительных инструментов. Выбор инструмента
Порошковая металлургия - особый вид металлургического производства, обеспечивающего получение изделий таких видов и из таких материалов, которые практически невозможно изготовить другими методами. Исходным материалом для изделий служат порошки металлов и неметаллических материалов с размером частиц от нескольких МКМ до 0,1 мм.
Метод порошковой металлургии позволяет получать изделия как из обычных металлов и сплавов, так из сложных порошков металлов, сплавов и неметаллических материалов. Методом порошковой металлургии получают:
|
-антифрикционные изделия (подшипники скольжения, втулки), представляющих сложные смеси на основе порошков меди, бронзы, железа с добавками графита, окиси кремния, асбеста и др.);
-фрикционные изделия - накладки в тормозных системах тракторов, автомобилей и т.д.;
-фильтры из порошков меди, бронзы, нержавеющей стали и др.;
-щетки для коллекторных электродвигателей из смесей порошков меди, серебра с W, Мо,Ni- электрические контакты и другие изделия электротехнического и специального назначения;
-нити накаливания в электролампах из W;
-все изделия из так называемых инструментальных твердых сплавов (смеси карбидов W, Тiс Со илиNi) для обработки металлов резанием (пластины для резцов, фрез и др.), обработки давлением; фильеры для волочения проволоки; инструмента для бурения скважин и др.
Изготовление изделий методом порошковой металлургии имеют следующие преимущества перед другими:
-изделия получаются повышенной точности со специальными свойствами в зависимости от состава порошков;
-сокращается или полностью исключается механическая обработка изделий; т.е. снижается расход металла на изделие и общая трудоемкость изготовления; повышается коэффициент использования металла;
-возможно изготовление изделий из смеси металлических и неметаллических материалов;
-увеличивается долговечность и надежность изделий: пористых подшипников и деталей, работающих в агрессивных средах.
Экономически целесообразно применение порошковой металлургии только при больших масштабах производства изделий небольшого габарита (крупносерийное, массовое).
Технологический процесс производства изделий методом порошковой металлургии включает в себя следующие этапы: производство металлических порошков (самостоятельное направление в порошковой металлургии; дозировка и перемешивания порошков - приготовление шихты; формообразование изделий из порошков; спекание; отдельные операции.
1.Применяют следующие способы производства металлических порошков, основанные на механических, металлургических электрохимических и др. способах.
Механическое измельчение материала. Является несовершенным из-за неравномерной величины частиц 10-500 мкм. Дробление производят в шаровых мельницах, а пластичных металлов - в мельницах вихревого размола.
|
Распыление жидкого металла в порошок струей воды, пара или воздуха.
Восстановление металла из их окислов и солей и углеродом, водородом, газообразными углеродистыми или углеводородными соединениями. ПолучениеFе-порошка восстановлением его из железной окалины или руды природным газом дает возможность использовать в качестве сырья большое количество дешевой окалины, образующейся при прокатке и ковке стали.
Электролиз водных растворов и расплавов солей и комплексных соединений. Получают мелкие порошки многих металлов и сплавов: тонкие (массой 05-10 мг и ультратонкие (менее 0,5 мг).
2. Приготовление шихты состоит из очистки порошков от примесей, классификации, их дозировки и перемешивание. Качество подготовки шихты влияет на механические свойства готовых изделий.
3. Этап формообразования изделий из порошков требует применения инструментальной оснастки (штампы, матрицы, пуансоны и др.)
Наиболее широкое применение имеет холодное прессование. Прессование состоит из ряда операций: дозировка и засыпка шихты в пресс-форму, прессование, выпрессовка. В пресс-форму могут загружать брикеты из порошков строго по весу и затем производят прессование под давлением, зависящим от состава порошка и назначения изделия.
Горячее прессование в пресс-форме - изделие не только формуется, но может подвергаться спеканию (операции формообразования и спекания совпадают).
Мундштучное прессование. Заготовку (трубы, полосы, стержня ид р.) получают продавливанием порошка через отверстие соответствующее конфигурации и размерам заготовки, под действием усиления пресса. Форма изделий задается формой матрицы и может быть сколь угодно сложной.
Способ прокатки металлических порошков заключается в подаче в зазор между валками, при вращении которых происходит обжатие и вытяжка порошка в ленту или полосу определенной толщины. Этот метод применяется для производства тонких пластин из твердых сплавов, фрикционных полос и лент, тепловыделяющих элементов атомных реакторов и др. трудно получаемых при обычных способах изготовления изделий. Получают однослойные и многослойные пористые и беспористые ленты, полосы, прутки, проволоку диаметром от 0.25 до несколько миллиметров.
Напылением металлического порошка на соответствующую форму получают тонкие фасонные изделия.
4. Спекание - термическая операция с целью повышения прочности; твердости изделия из прессованного порошка при температурах 0.6-0.9 абсолютной температуры плавления основного компонента сплава. Технология спекания влияет на прочность и твердость изделий - время выдержки и температура процесса должны быть оптимальными. Спекания проводят в вакууме или защитной атмосфере из водорода, окиси азота с водородом (восстановительная атмосфера), в среде аргона, гелия.
5. При необходимости спеченные металлокерамические изделия подвергают отделочным операциям: калиброванию, обработке резанием, термической и химико-термической обработке, повторному прессованию.
|
|
Индивидуальные очистные сооружения: К классу индивидуальных очистных сооружений относят сооружения, пропускная способность которых...
История развития пистолетов-пулеметов: Предпосылкой для возникновения пистолетов-пулеметов послужила давняя тенденция тяготения винтовок...
Типы сооружений для обработки осадков: Септиками называются сооружения, в которых одновременно происходят осветление сточной жидкости...
Опора деревянной одностоечной и способы укрепление угловых опор: Опоры ВЛ - конструкции, предназначенные для поддерживания проводов на необходимой высоте над землей, водой...
© cyberpedia.su 2017-2024 - Не является автором материалов. Исключительное право сохранено за автором текста.
Если вы не хотите, чтобы данный материал был у нас на сайте, перейдите по ссылке: Нарушение авторских прав. Мы поможем в написании вашей работы!