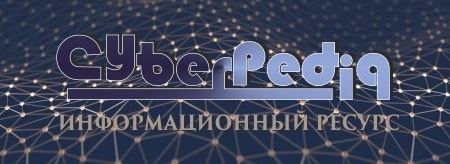
Типы оградительных сооружений в морском порту: По расположению оградительных сооружений в плане различают волноломы, обе оконечности...
Кормораздатчик мобильный электрифицированный: схема и процесс работы устройства...
Топ:
Интересное:
Влияние предпринимательской среды на эффективное функционирование предприятия: Предпринимательская среда – это совокупность внешних и внутренних факторов, оказывающих влияние на функционирование фирмы...
Как мы говорим и как мы слушаем: общение можно сравнить с огромным зонтиком, под которым скрыто все...
Подходы к решению темы фильма: Существует три основных типа исторического фильма, имеющих между собой много общего...
Дисциплины:
![]() |
![]() |
5.00
из
|
Заказать работу |
|
|
По каким признакам осуществляется классификация металлорежущих станков общего назначения? Как подразделяются станки по классу точности?
Классификация металлорежущих станков общего назначения осуществляется:
- по назначению:
1. Токарные
2. Сверлильные и расточные
3. Шлифовальные и доводочные
4. Комбинированные (электрофизические)
5. Зубо- и резьбообрабатывающие
6. Фрезерные
7. Строгальные, долбёжные, протяжные
8. Разрезные
9. Разные (делительные машины для испытания инструмента)
- по степени автоматизации: ЧПУ, автоматические линии
- по точности в соответствии с ГОСТ 8– 82: Н – нормальная; П – повышенная;
В – высокая; А – особо высокая; С – особо точные станки.
Импортные станки по ISO230-2:
Н – повышенной; Р – прецизионные; SP – суперпрезиционные; UP – ультрапрецизионные.
- по оснащенности (есть или нет приспособления).
- по массе: – легкие (до 1 т), средние (до 10 т), тяжелые (от 10 т до 30 т), особо тяжелые (свыше 30т), уникальные (вес более 100Т).
- по универсальности: универсальные, позволяют обработать детали широкой номенклатуры; специализированные, используются только для обработки деталей определенной номенклатуры; специальные станки, применяются для обработки деталей одного типа, используются в крупносерийном и массовом производстве.
по размерам (линейные размеры):
малые 1800х800 мм
средние 4000х2000 мм
крупные 8000х4000 мм
особо крупные 15000х6000 мм
Показатели оценки качества МРС (мировые показатели): а) надежность; б) точность (геометрическая, технологическая, параметрическая); в) производительность; г) безопасность; д) удобство обслуживания
Перечислите основные показатели, характеризующие качество станочного оборудования и используемые для сравнительной оценки технического уровня металлорежущих станков.
|
Показатели оценки качества МРС:
Надёжность станка – свойство станка обеспечивать бесперебойный выпуск продукции в заданном количестве в течение определённого срока службы в условиях применения технологического обслуживания, ремонтов, хранения и транспортирования.
Точность (геометрическая, технологическая, параметрическая). Для потребителя точность МРС выражается в их способности обеспечить готовые изделия: точность размеров, точность формы и взаимного положения плоскостей обрабатываемых, их волнистость, шероховатость а так же стабильность этих показателей в заданных пределах.
Производительность определяется его стабильностью обеспечивать обработку определённого числа деталей в единицу времени
Безопасность
Удобство обслуживания
Жёсткость
Приведите классификацию металлорежущих станков общего назначения.
Классификация металлорежущих станков общего назначения осуществляется:
- по назначению:
1. Токарные
2. Сверлильные и расточные
3. Шлифовальные и доводочные
4. Комбинированные (электрофизические)
5. Зубо- и резьбообрабатывающие
6. Фрезерные
7. Строгальные, долбёжные, протяжные
8. Разрезные
9. Разные (делительные машины для испытания инструмента)
- по степени автоматизации: ЧПУ, автоматические линии
- по точности в соответствии с ГОСТ 8– 82: Н – нормальная; П – повышенная;
В – высокая; А – особо высокая; С – особо точные станки.
Импортные станки по ISO230-2:
Н – повышенной; Р – прецизионные; SP – суперпрезиционные; UP – ультрапрецизионные.
- по оснащенности (есть или нет приспособления).
- по массе: – легкие (до 1 т), средние (до 10 т), тяжелые (от 10 т до 30 т), особо тяжелые (свыше 30т), уникальные (вес более 100Т).
- по универсальности: универсальные, позволяют обработать детали широкой номенклатуры; специализированные, используются только для обработки деталей определенной номенклатуры; специальные станки, применяются для обработки деталей одного типа, используются в крупносерийном и массовом производстве.
|
по размерам (линейные размеры):
малые 1800х800 мм
средние 4000х2000 мм
крупные 8000х4000 мм
особо крупные 15000х6000 мм
Показатели оценки качества МРС (мировые показатели): а) надежность; б) точность (геометрическая, технологическая, параметрическая); в) производительность; г) безопасность; д) удобство обслуживания
Производительность АЛ.
Любая АЛ в пределах планового фонда может находиться в состояниях:
1) Линия работает, выполняется заданный ТП обработки, контроля, сборки и т.д. tр
2) Линия работает, выполняет вспомогательные операции, обеспечивающих реализацию ТП, tx
3) Линия работает, но выдаваемая продукция не соответствует техническим условиям, брак
4) Линия простаивает из-за отказа механизмов и инструментов
а) Номинальная производительность: , Р- количество изделий выполненных в одно время
б) Цикловая производительность: (0,7-0,95),tр+tx=T(10-240 с)
в) Техническая производительность:
Простой АЛ и раб. машин делят:
1) Простой по инструменту (неработоспособность по инструменту)
2) Простой по оборудованию (неработоспособность механизмов и устройств по причине поломки, отказов, уборки стружки и т.д.)
3) Простой по организационным причинам (АЛ работоспособна, однако отсутствуют заготовки, нет Е и другие)
4) Простои из-за брака
5) Простои по переналадке линии на обработку новых деталей
Фактическая производительность: (0,5-0,95).
Исходные данные для проектирования АЛ:
1) Принятые методы и маршруты обработки
2)Требуемая производительность
Комбинированные
По количеству управляемых координат: однокоординатные, многокоординатные
По обратной связи: разомкнутые, замкнутые
МЕТРОЛОГИЯ,СТАНДАРТИЗАЦИЯ
Что такое шероховатость поверхности? Укажите основные параметры, которые используются для оценки шероховатости поверхности. Расшифруйте обозначение параметров шероховатости, представленное на рисунке.
Шероховатость и волнистость являются характеристиками качества поверхности, оказывающими большое влияние на многие эксплуатационные свойства деталей машин. Шероховатость поверхности представляет собой совокупность неровностей, образующих рельеф реальных поверхностей с относительно малыми шагами.
|
Рассматриваемые микронеровности образуются в процессе механической обработки путем копирования формы режущих инструментов, пластической деформации поверхностного слоя деталей под воздействием обрабатывающего инструмента, трения его о деталь, вибраций и т.д.
Шероховатость поверхностей деталей оказывает существенное влияние на износостойкость, усталостную прочность, герметичность и другие эксплуатационные свойства.
Для отделения шероховатости поверхности от других неровностей с относительно большими шагами (отклонения формы и волнистости) ее рассматривают в пределах ограниченного участка, длина которого называется базовой длиной I. Базовая длина / нормируется в зависимости от параметров шероховатости в пределах ряда: 0,01; 0,03; 0,08; 0,25; 0,8; 2,5; 8; 25, т.е. чем больше микронеровности, тем больше базовая длина.
Линия, на которой выделяется совокупность поверхностных неровностей, называется базовой линией.
Базовая линия - это линия заданной геометрической формы, проведенная определенным образом относительно профиля и служащая для оценки геометрических параметров поверхностных неровностей. Вид этой линии зависит от вида поверхности элемента детали. Таким образом, базовая линия поверхности элемента детали имеет форму линии номинального профиля и расположена эквидистантно этому профилю.
В качестве базовой линии при оценке поверхностных неровностей используется средняя линия, которая является базой для отсчета отклонения профиля.
Такая система отсчета в международной практике носит название системы "М".
Средняя линия профиля т - это базовая линия, имеющая форму номинального профиля и проведенная так, что в пределах базовой длины среднее квадратическое отклонение профиля от этой линии минимально.
Рассмотрим кратко эти нормируемые параметры.
Среднее арифметическое отклонение профиля Ra — среднее арифметическое абсолютных значений отклонений профиля от средней линии в пределах базовой длины.
Числовые значения параметров Ra, Rz, Rmax, Sm, S определены стандартом ГОСТ 2789-73, причем для всех трех высотных параметров выделены предпочтительные значения, которыми и следует в первую очередь пользоваться. Эти числовые значения параметров шероховатости проставляют на чертежах.
|
Значения уровня сечения профиля р отсчитывают от линии выступов и выбирают из ряда: 5; 10; 15; 20; 25; 30; 40; 50; 60; 70; 80; 90 % Rmax.
Числовые значения t выбирают из ряда: 10; 15; 20; 25; 30; 40; 50; 60; 70; 80; 90 %.
Требования к шероховатости поверхности деталей и выбор параметров для ее оценки устанавливаются исходя из функционального назначения поверхности для обеспечения заданного качества поверхности.
Для неответственных деталей можно не указывать параметры шероховатости, в таком случае она не подлежит контролю.
Некоторые специальные технологические методы окончательной обработки позволяют получить на поверхностях регулярный заранее заданный микрорельеф из канавок или лунок определенной формы. ГОСТ 24773-81 устанавливает характеристики таких параметров.
На рисунке схематично показаны параметры шероховатости, где: — базовая длина;
— средняя линия профиля;
— средний шаг неровностей профиля;
— средний шаг местных выступов профиля;
— отклонение пяти наибольших максимумов профиля;
— отклонение пяти наибольших минимумов профиля;
— расстояние от высших точек пяти наибольших максимумов до линии параллельной средней и не пересекающей профиль;
— расстояние от низших точек пяти наибольших минимумов до линии параллельной средней и не пересекающей профиль;
— наибольшая высота профиля;
— отклонения профиля от линии
;
— уровень сечения профиля;
— длина отрезков, отсекаемых на уровне
.
Высотные параметры:
Ra — среднее арифметическое отклонение профиля;
или
Rz — высота неровностей профиля по десяти точкам;
Rmax — наибольшая высота профиля;
Шаговые параметры:
Sm — средний шаг неровностей;
S — средний шаг местных выступов профиля;
tp — относительная опорная длина профиля, где p — значения уровня сечений профиля из ряда 10; 15; 20; 30; 40; 50; 60; 70; 80; 90%.
Ra, Rz и Rmax определяются на базовой длине l которая может принимать значения из ряда 0,01; 0,03; 0,08; 0,25; 0,80; 2,5; 8; 25мм.
Параметр Ra является предпочтительным.
Какие основные параметры шероховатости поверхности высотные и шаговые Вы знаете? Какой высотный параметр является предпочтительным? Приведите профиль шероховатости и укажите его характеристики и параметры.
ТЕХНОЛОГИЧЕСКАЯ ОСНАСТКА
1. В системе отверстия или в системе вала выполняется отверстие в кондукторной втулке? Определить допуск и отклонения размера отверстия кондукторной втулки под сверло Æ8(-0,12) мм (Æ5(-0,12) мм). Выявить наибольший начальный зазор между сверлом и отверстием втулки Smax. Какое следует назначить расстояние от нижнего торца кондукторной втулки до поверхности детали, если производится сверление отверстия в детали из стали 10Х18Н9Т (серый чугун)?
|
Допуск на диаметр отверстия в кондукторных втулках для прохода сверл и зенкеров устанавливают по посадке F8(+10+28) в системе вала. При точности отверстия по 6 – 7 квалитету и выше допуски на диаметр отверстия для прохода сверл назначают по Н7(0+12).
Наибольший начальный зазор между сверлом и отверстием втулки Smax = 40 мкм.
Расстояние от нижнего торца втулки до поверхности заготовки выбирают равным
е = (1/3 – 1) d диаметра отверстия. Меньшее расстояние выбирают при обработке чугуна, большее – при обработке стали. Для заданных условий е = 1,5…2,5 мм.
Определить погрешность базирования втулки при её установке на жесткой оправке с зазором и упором в торец. Обработке подвергается наружная цилиндрическая поверхность. Заданы размеры цилиндрической оправки и базового отверстия.
3. Определить необходимую силу зажима (Q) заготовки, развиваемую одним кулачком 3-х кулачкового самоцентрирующегося патрона, в котором установлена заготовка ØD при растачивании отверстия под резьбу. Заданы крутящий момент от сил резания, коэффициент трения между кулачками и заготовкой f, диаметр заготовки и коэффициент запаса надежности при закреплении.
При данной схеме установки величина погрешности базирования будет определяться как величина наибольшего зазора в соединении оправка-втулка, т.е.
мм
Здесь е - эксцентриситет наружного диаметра и диаметра базового отверстия заготовки. Величина отклонения от соосности при обработке может составить:
мм = 31,5 мкм
4. Определить необходимую силу (Q) закрепления заготовки в тисках, если сила резания PZ = 350Н направлена параллельно рабочим поверхностям губок тисков, т.е. перпендикулярно направлению силы Q. Заданы значения коэффициентов трения между поверхностями заготовки и губками тисков f, между установочными элементами и заготовкой f=0,35, коэффициент запаса надежности К=2,5.
Сдвигу заготовки под действием силы резания PZ при фрезеровании паза с закреплением заготовки в тисках препятствуют силы трения, возникающие в местах контакта заготовки с опорами и с губками тисков.
При этом должно соблюдаться условие: FТР. = К · PZ, где FТР = Q · (fоп. + fзм..),
где fоп. = 0,15 - коэффициент трения между установочными элементами и поверхностью заготовки. Тогда потребное усилие закрепления заготовки в тисках будет равно:
1750 Н.
5. Элемент приспособления нагружен силой Р и моментом М (см. рис.). Построить эпюры поперечной силы Q и изгибающего момента М. Определить координату опасного сечения.
Показать теоретическую схему базирования и охарактеризовать базы по лишаемым степеням свободы и по характеру проявления для случая базирования заготовки по плоскости и двум отверстиям. Определить ожидаемую погрешность базирования, связанную с углом поворота заготовки, при заданном межцентровом расстоянии, диаметрах базовых отверстий и размерах установочных пальцев.
1,2,3 – установочная база; 4,5 – двойная опорная; 6 – опорная.
Для схемы установки детали по плоскости и двум базовым отверстиям характерны два вида погрешностей:
Погрешность размера, вызванная смещением заготовки на пальцах в одну сторону.
баз = Smax = Dотвmax – Dопрmin
Поворот заготовки на пальцах.
баз = tg
; tg
= (Smax1-Smax2)/2L
Показать теоретическую схему базирования и охарактеризовать базы по лишаемым степеням свободы и характеру проявления для случая установки цилиндрической заготовки в трех кулачковом самоцентрирующемся патроне. Составить размерную цепь и определить ожидаемую погрешность базирования при подрезке торцов заготовки, согласно приведенной схемы.
10. Укажите базы при установке цилиндрической заготовки в призму с упором в торец. Определить погрешность базирования (eб) цилиндрической заготовки при фрезеровании лыски за один рабочий ход на вертикально-фрезерном станке.
Рассмотрим схему установки вала диаметром d в призме при фрезеровании паза, размер которого задан от различных конструкторских баз.
Во всех случаях вал устанавливают по вспомогательной базе и, таким образом, погрешность базирования неизбежна и зависит от допуска на диаметр вала d и угла призмы .
Для расчета погрешностей базирования предположим, что на призме установлен вал с наибольшим предельным диаметром d max и наименьшим предельным диаметром d min; тогда величина h1, h2; h3 из геометрических построений будет характеризовать величину погрешности базирования для каждой схемы соответственно.
К - коэф. зависящий от угла призмы
11. Приведите зависимость jст = ¦(Х) для определения жесткости токарного станка при обработке заготовки в центрах, если известны жесткости основных узлов станка jсуп, jзб, jпб, а также длина заготовки L, координата Х и составляющая силы резания Py.
ТЕХНОЛОГИЯ МАШИНОСТРОЕНИЯ
Показать теоретическую схему базирования и охарактеризовать базы по лишаемым степеням свободы и по характеру проявления для случая базирования заготовки по плоскости и двум отверстиям. Определить ожидаемую погрешность базирования, связанную с углом поворота заготовки, при заданном межцентровом расстоянии, диаметрах базовых отверстий и размерах установочных пальцев.
1,2,3 – установочная база; 4,5 – двойная опорная; 6 – опорная.
Для схемы установки детали по плоскости и двум базовым отверстиям характерны два вида погрешностей:
· Погрешность размера, вызванная смещением заготовки на пальцах в одну сторону.
баз = Smax = Dотвmax – Dопрmin
· Поворот заготовки на пальцах.
баз = tg
; tg
= (Smax1-Smax2)/2L
Установочных пальцев.
Эти схемы базирования, можно разделить на три группы:
1. По торцу и отверстию;
2. По плоскости, торцу и отверстию с осью, параллельной плоскости;
3. По плоскости и двум перпендикулярным к ней отверстиям.
При базировании деталей по торцу и отверстию, возможны два случая:
· Основной базирующей поверхностью является отверстие;
· Основной базирующей поверхностью является торец.
Рисунок 4. Схема базирования по плоскости и двум перпендикулярным к ней отверстиям.
Погрешности базирования в приспособлениях.
Суммарная погрешность при выполнении любой операции механической обработки состоит из:
1. Погрешности установки заготовки;
2. Погрешности настройки станка;
3. Погрешности обработки, возникающей в процессе изготовления детали.
Погрешность установки , возникает при установке обрабатываемой заготовки в приспособлении и складывается из погрешности базирования
, погрешности закрепления
, и погрешности положения заготовки
, зависящей от неточности приспособления и определяемой ошибками изготовления и сборки его установочных элементов и их износа при работе.
При установке деталей по плоскости и двум отверстиям необходимо выполнить расчеты, связанные с установкой на пальцы.
Рисунок 5. Расчетная схема для случая установки детали на два цилиндрических пальца.
Введем обозначения:
,
- расстояние между центрами базовых отверстий и установочных пальцев (номинальный размер);
- допуск на межцентровое расстояние базовых отверстий;
- допуск межцентрового расстояния установочных пальцев;
-минимальный зазор в сопряжении первого отверстия с пальцем;
-- минимальный зазор в сопряжении второго отверстия с пальцем;
( =1/5…1/2
)
Показать теоретическую схему базирования и охарактеризовать базы по лишаемым степеням свободы и характеру проявления для случая установки цилиндрической заготовки в трех кулачковом самоцентрирующемся патроне. Составить размерную цепь и определить ожидаемую погрешность базирования при подрезке торцов заготовки, согласно приведенной схемы.
10. Укажите базы при установке цилиндрической заготовки в призму с упором в торец. Определить погрешность базирования (eб) цилиндрической заготовки при фрезеровании лыски за один рабочий ход на вертикально-фрезерном станке.
Рассмотрим схему установки вала диаметром d в призме при фрезеровании паза, размер которого задан от различных конструкторских баз.
Во всех случаях вал устанавливают по вспомогательной базе и, таким образом, погрешность базирования неизбежна и зависит от допуска на диаметр вала d и угла призмы .
Для расчета погрешностей базирования предположим, что на призме установлен вал с наибольшим предельным диаметром d max и наименьшим предельным диаметром d min; тогда величина h1, h2; h3 из геометрических построений будет характеризовать величину погрешности базирования для каждой схемы соответственно.
, К - коэф. зависящий от угла призмы
11. Приведите зависимость jст = ¦(Х) для определения жесткости токарного станка при обработке заготовки в центрах, если известны жесткости основных узлов станка jсуп, jзб, jпб, а также длина заготовки L, координата Х и составляющая силы резания Py.
Жесткость упругой системы СПИД выражается отношением радиальной составляющей силы резания, направленной по нормали к обрабатываемой поверхности, к смещению режущей кромки инструмента относительно детали, отсчитываемому в том же направлении, при действии всех составляющих сил резания.
где - жесткость системы;
- радиальная составляющая силы резания;
У - смещение режущей кромки инструмента (деформация упругой системы).
Аналогично выражается жесткость отдельных элементов технологической упругой системы - для суппорта (), передней бабки (
), задней бабки (
), обрабатываемой детали (
) и т.д.
Существует несколько методов определения жесткости металлорежущих
станков или их отдельных узлов:
6. статический (испытания на неработающем станке);
7. производственный (испытания при обработке заготовки).
Статический метод заключается в постепенном нагружении узлов станка силами, воспринимающими действие силы резания с одновременным измерением возникающих при этом деформаций.
Перемещения узлов станка измеряются в направлении действия силы PY, нормальной к обрабатываемой детали, т.к. эти перемещения имеют основное значение, хотя на деформацию системы в этом направлении оказывают некоторое влияние и составляющие PX и PZ.
Определенный при этом коэффициент жесткости может приближенно характеризовать упругие свойства системы СПИД, но не отражает действительных условий работы станка.
При определении жесткости системы СПИД в производственных условиях узлы станка нагружают ступенчато с постоянно возрастающей нагрузкой с одновременным измерением величины перемещения узлов станка в направлении, нормальном к обрабатываемой поверхности. При производственном методе испытания жесткости заготовка обрабатывается с переменной глубиной резания, для этого удобно использовать заготовку с наличием эксцентриситета. Глубина резания за половину оборота заготовки изменяется при этом от. tmin до tmax.
ТЕХНОЛОГИЯ МАШИНОСТРОЕНИЯ
1. Методика назначения режимов резания. Определите мощность резания при черновом наружном точении поверхности вала из стали 40Х ÆD (мм) резцами с пластинами из твердого сплава при глубине резания - t (мм) и скорости подачи - S (мм/об.)
2. Дайте определение понятий «норма времени» и «трудоемкость». Приведите зависимость для определения общей трудоемкости при изготовлении партии деталей. Укажите основные составляющие трудоемкости.
Норма времени – это регламентированное время, выполнения некоторого объема работ в определенных производственных условиях одним или несколькими исполнителями соответствующей квалификации.
За единицу объема работ – операция.
Трудоемкость — затраты труда, рабочего времени на производство единицы продукции (физических единиц времени на один рубль выпускаемой продукции). Трудоемкость обратно пропорциональна производительности труда, выработке продукции на одного работника.
Величина обратная нормы времени – есть техническая норма выработки, выражает количество изделий выпускаемых в единицу времени, смену.
Для нормирования используют 3 метода назначения норм:
1. Нормы времени устанавливаются на основе изучения затрат рабочего времени, наблюдение.
2. Назначаются по нормативам.
3. Назначаются методом сравнения и расчет по типовым нормам.
Методы наблюдения:
1. Фотография рабочего дня.
2. Самофотография.
3. Хронометраж.
Тшт=t0+tв+tабс+tпер, tабс=tто+tорг, Тшт-к=Тшт+Тпз/n, где n количество деталей в партии.
Тшт – штучное время выполнения операции, которое состоит:
tо – основное время, связанное с обработкой на данной операции.
tв – вспомогательное время, которое учитывает время с установкой, закреплением, раскреплением и управление станком, предварительный замер.
tто – время технического обслуживания, связанное со сменой инструмента, его правкой. Учитывает регулирование и поднастройку станка и др. действия связанные с уходом за рабочим местом при выполнении заданной работы.
tорг – включает затраты за уходом за станком в течении смены, смазка механизмов, уборка инструмента, уборка рабочего места.
tпер – время на личные потребности, отдых.
Тшт-к – время выполнения операций для партии деталей.
Тпз – подготовительно-заключительное время, учитывающее время на подготовку исполнительных средств технологического оснащения к выполнению технологической операции и приведением в порядок после выполнения.
3. Назовите основные типы производств, существующих в машиностроении. Какие показатели используются для определения типа производства?
Тип производства – это классификация категорий производства, выделяемая по признакам широты номенклатуры, регулярности и объема выпуска изделий, стабильности.
Одной из характеристик является коэффициент закрепления операций, представляющий собой число всех технологических операций, выполняемых, или подлежащих выполнению к числу рабочих мест.
– суммарное число различных операций.
- явочное число рабочих подразделений выполняемых различные операции.
Кв – коэффициент выполнения норм (1,18-1,3).
Ф – месячный фонд времени рабочего при работе в одну смену.
– суммарная трудоемкость прогр. выпуска детали за месяц.
Ni – прог. выпуска I позиции номенклатуры.
Согласно ГОСТ 3.11.21-84 признаны следующие значения , которые характеризуют типы производства:
– массовое
– крупносерийное
– среднесерийное
– мелкосерийное
– единичное
Где - такт выпуска.
(мин/шт)
Где - нормативный коэффициент загрузки (
)
4. Укажите основные параметры, которые следует учитывать при выборе оборудования для разрабатываемого варианта технологического процесса.
1. размеры рабочей зоны станка, которые должны соответствовать габаритам обрабатываемой детали.
2. возможность достижения при обработке требуемой точности и шероховатости поверхности (особое значение данный фактор имеет при чистовой или окончательной обработке).
3. соответствие мощности, жесткости и кинематических данных оборудования и более рациональных режимов обработки.
4. обеспечение необходимой прог. произвести с заданной программой выпуска.
5. соответствие оборудования при выпуске данного тех процесса требования к безопасности и программы санитарии.
6. соответствие оборудования заданной программе по критерию себестоимости.
Наиболее экономный ип оборудования выбирают с учетом наименьшего срока окупаемости, наивысшего коэффициента сравнительной экономичной эффективности, наименьшие суммы приведенных годовых затрат и наибольшего годового экономического эффекта.
Ток=(К2-К1)/(С1-С2), Е=(С1-С2)/(К2-К1)=1/Ток, где К1 и К2 – капитальные вложения по базовым и внедренным вариантам. С1 и С2 – себестоимость ГП по по этим же вариантам.
Косилова т2 245 еще
Косилова
Спиральные сверла имеют наибольшее распространение. Это сверло (рис. 309) состоит из рабочей части, включающей режущую часть, шейки, конического (рис. 309, а) или цилиндрического (рис. 309, б) хвостовика для крепления сверла в шпинделе станка, лапки, служащей упором для выбивания сверла из гнезда шпинделя. Режущая часть (рис. 309, в) состоит из двух зубьев, образованных двумя канавками для отвода стружки; сердцевины— срединной части сверла, соединяющей оба зубца; двух передних поверхностей, по которым сбегает стружка и которые воспринимают силу резания; двух ленточек — узких полосок по наружному диаметру сверла, служащих для его направления и центрирования в отверстии; двух главных режущих лезвий, образованных пересечением передних и задних поверхностей и выполняющих основную работу резания; поперечного лезвия или перемычки, образованной пересечением обеих задних поверхностей.
Спиральное сверло содержит пять лезвий: два главных, два вспомогательных (вдоль ленточек) и поперечное, которое не режет, а сминает, выдавливает металл. Поперечное лезвие у сверла есть основной его дефект. Геометрические параметры сверла рассматриваются на его режущей части.
Задний угол α рассматривается в плоскости АА, параллельной оси сверла (рис. 309, г), для текущей точки х (см. сечение АА); он изменяется от αmin на периферийной точке сверла до αmах, у перемычки сверла.
Передний угол γ берется в плоскости ББ, перпендикулярной режущему лезвию сверла (рис. 309, г), для текущей точки х; этот угол изменяется от γmin у перемычки сверла до γmах на периферийной точке сверла. Угол при вершине сверла 2φ находится между главными режущими лезвиями: 2φ = 116 ÷ 118° при обработке стали, чугуна, твердой бронзы; 2φ = 140° при обработке алюминия и легких сплавов; 2φ = 80 ÷ 90° при обработке эбонита, целлулоида, мрамора.
Угол наклона поперечного лезвия ψ равен 55º.
Заточкой придают сверлу (рис. 309, г) следующие значения углов: αmin ≈ 7º, αmax ≈ 26º, γmin ≈ 3º, γmax ≈ 30º.
Критерием правильной заточки является соблюдение углов 2φ, ψ и αmin.
Кроме этого, нужно, чтобы ось сверла проходила через середину перемычки и делила угол при вершине 2φ на две равные части и чтобы главные режущие лезвия были равны.Во избежание защемления сверла на сверле дают обратный конус в сторону хвостовика на величину примерно 0,05 мм на 100 мм длины.
На рис. 309, д дана одинарная заточка сверла; на рис. 309, е — двойная заточка сверла; на рис. 309, ж — одинарная заточка с подточкой поперечного лезвия; на рис. 309, з — одинарная заточка сверла с подточкой ленточек. Двойн
|
|
Организация стока поверхностных вод: Наибольшее количество влаги на земном шаре испаряется с поверхности морей и океанов (88‰)...
Кормораздатчик мобильный электрифицированный: схема и процесс работы устройства...
Двойное оплодотворение у цветковых растений: Оплодотворение - это процесс слияния мужской и женской половых клеток с образованием зиготы...
Своеобразие русской архитектуры: Основной материал – дерево – быстрота постройки, но недолговечность и необходимость деления...
© cyberpedia.su 2017-2024 - Не является автором материалов. Исключительное право сохранено за автором текста.
Если вы не хотите, чтобы данный материал был у нас на сайте, перейдите по ссылке: Нарушение авторских прав. Мы поможем в написании вашей работы!