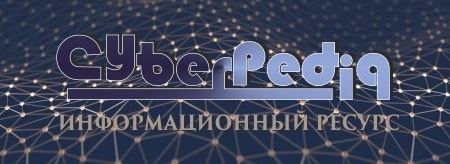
Общие условия выбора системы дренажа: Система дренажа выбирается в зависимости от характера защищаемого...
Биохимия спиртового брожения: Основу технологии получения пива составляет спиртовое брожение, - при котором сахар превращается...
Топ:
Оценка эффективности инструментов коммуникационной политики: Внешние коммуникации - обмен информацией между организацией и её внешней средой...
Методика измерений сопротивления растеканию тока анодного заземления: Анодный заземлитель (анод) – проводник, погруженный в электролитическую среду (грунт, раствор электролита) и подключенный к положительному...
Интересное:
Распространение рака на другие отдаленные от желудка органы: Характерных симптомов рака желудка не существует. Выраженные симптомы появляются, когда опухоль...
Как мы говорим и как мы слушаем: общение можно сравнить с огромным зонтиком, под которым скрыто все...
Финансовый рынок и его значение в управлении денежными потоками на современном этапе: любому предприятию для расширения производства и увеличения прибыли нужны...
Дисциплины:
![]() |
![]() |
5.00
из
|
Заказать работу |
|
|
На АЛ и АС обработку основных отверстий заготовок корпусных деталей диаметром от 15 до 400 мм выполняют преимущественно растачиванием однолезвийным инструментом. При этом обеспечивается точность диаметральных размеров, соответствующая 1T6...IT12; отклонения формы отверстий в поперечном и продольном сечениях в пределах 0,2...0,5 от допуска на диаметральный размер; отклонения от соосности осей, обрабатываемых относительно осей крайних отверстий, в интервале 0,015...0,05 мм на длине до 500 мм; отклонения межосевого расстояния осей отверстий ±(0,02...0,10) мм; отклонения от параллельности осей отверстий 0,02...0,08 мм на длине 300 мм; отклонения от перпендикулярности осей основных отверстий 0,03...0,10 мм на длине 300 мм; отклонения осей основных отверстий от параллельности или перпендикулярности базовой плоскости 0,03...0,1 мм на длине 300 мм; шероховатость поверхности отверстий Ra = 0,63...2,5 мкм.
По некоторым параметрам точности обработки основных отверстий заготовок корпусных деталей, например по отклонениям от соосности осей отверстий или отклонениям от перпендикулярности осей отверстий и их торцев, обработка на расточных и расточно-подрезных АС не имеет конкурентов. Схемы обработки на них отверстий и сопряженных поверхностей заимствуют для других видов металлорежущего оборудования.
Отверстия на расточных АС обрабатывают борштангами, применяя два способа соединения со шпинделями: жесткое, с базированием борштанги поверхностью вращения (выступ — шейка хвостовика или отверстия) и плоскостью фланца с закреплением через фланец (рис. 5.28), и плавающее (рис. 5.29). В последнем случае хвостовик борштанги 3 устанавливают в плавающий патрон 2, а патрон — хвостовиком в шпиндель 1 с базированием борштанги специальными узлами направления. Плавающий патрон допускает возможность смещения оси борштанги на 0,5...2,0 мм и поворот ее оси на угол до 5°. Плавающий патрон передает крутящий момент от шпинделя борштанге и обеспечивает ее осевую фиксацию.
|
На расточных АС и в позициях AJI используют четыре способа направления борштанги:
1) заднее — дополнительная опора (направляющая втулка) находится за обрабатываемой заготовкой (см. рис. 5.28, б);
2)переднее — дополнительная опора (втулка) установлена перед заготовкой относительно направления подачи инструмента (см. рис. 5.29);
3)переднее и заднее (двухопорная схема направления) — дополнительные опоры находятся перед заготовкой и за нею;
4)многоопорное — кроме передней и задней опор имеются одна или несколько промежуточных.
Первый способ применяют только для жесткого соединения борштанги со шпинделем станка, остальные три — для борштанг с плавающим соединением инструмента со шпинделем.
Рис. 5.28. Схемы инструментальных наладок для растачивания при жестком соединении инструмента со шпинделем: а — без направления; б — с задним направлением
Борштанги конструктивно могут быть выполнены цельными — тело вращения представляет собой монолит; сборными с механизмом автоматического подвода и отвода резцов в поперечном направлении для обработки отверстий диаметром более 70 мм и сборными — типа «скользящая втулка». Растачивание отверстий жестко закрепленной на шпинделе станка борштангой обычно выполняют по консольной схеме без применения дополнительной опоры (см. рис. 5.28, а). Для этой схемы характерен относительно большой вылет l x борштанги от торца шпинделя до режущего лезвия резца, который назовем вылетом режущего инструмента. Он зависит от расстояния L от места крепления резца до переднего подшипника шпинделя (см. рис. 5.28, а) и диаметра шпинделя D шп в передней опоре. Устойчивая работа консольно закрепленной борштанги и точность растачиваемых отверстий обеспечиваются при отношении l x / D шп ≤ 3...4 и D бш ≤ D шп, где D бш — диаметр борштанги в зоне резания. Меньшее значение относится к растачиванию отверстий в заготовках из стали и серого чугуна, большее — к растачиванию отверстий в заготовках из легких сплавов цветных металлов.
|
При обработке отверстий на AЛ и АС диаметр борштанги в зоне резания определяют по формуле
D бш = kD – 2 ɀ i max
где k — коэффициент, учитывающий материал обрабатываемой заготовки и вид обработки (черновая, получистовая, чистовая), k = 0,82...0,92; D — диаметр растачиваемого отверстия; ɀ i max — максимальный припуск на радиус отверстия, равный 3...10 мм для черновой обработки, 1...2 мм — для получистовой и ≤ 0,5 мм — для чистовой обработки.
При необходимости иметь больший вылет инструмента, т. е. при l x > (3...4) D бш, рекомендуют растачивание жестко закрепленной борштангой, имеющей дополнительное направление во втулке (см. рис. 5.28, б). Для такой схемы инструментальной наладки предъявляют весьма высокие требования к соосности осей шпинделя и направляющей втулки. Предельно допустимое расстояние l max от торца шпинделя до торца направляющей втулки (см. рис. 5.28, б) составляет (7... 12,5) D бш для чистового растачивания заготовок из чугуна; (8,6...15,0) D бш — для растачивания заготовок из стали и (10...17,5) D бш — для растачивания заготовок из алюминиевых сплавов. При растачивании двумя или тремя резцами l max умножают на коэффициент 0,8, а при растачивании четырьмя—шестью резцами — на 0,7.
При еще больших вылетах инструмента схема, приведенная на рис. 5.28, б, не обеспечивает необходимой жесткости технологической системы, а в случае многошпиндельной обработки возникают проблемы с обеспечением соосности осей жестко закрепленных борштанг и направляющих втулок.
Рис. 5.29. Схемы инструментальных наладок для растачивания при плавающем соединении инструмента со шпинделем:
а, б — одноопорное (переднее) направление борштанги по вращающейся втулке при D вт > D и Dвт < D соответственно;
1 — шпиндель; 2 — плавающий патрон; 3 — борштанга; 4 — направляющая втулка; 5, 8 — шпонки; 6 — люнет; 7 — паз для прохода резца
Тогда прибегают к плавающему соединению борштанга — шпиндель и использованию специальных узлов направления инструмента. На позициях AJI по обработке отверстий, имеющих плавающее соединение борштанга — шпиндель, можно применять нормализованные многошпиндельные коробки и бабки с одним шпинделем. На таких позициях точность расположения осей обрабатываемых отверстий не зависит от геометрических погрешностей станка, его тепловых деформаций и износа. При направлении инструмента по втулкам устраняется схватывание поверхностей в сопряжении втулка — инструмент при скоростях резания свыше 20…25 м/мин вследствие разделения поверхностей, воспринимающих вращательное движение инструмента и его поступательное перемещение (подачу). Такого разделения поверхностей достигают использованием вращающейся направляющей втулки либо конструкцией вспомогательного инструмента (борштанга типа «скользящая втулка»).
|
При одноопорной схеме с передней направляющей инструмента (см. рис. 5.29, а) имеется одна направляющая втулка 4, которая установлена в корпусе приспособления на подшипниках качения и может вращаться. Вспомогательный инструмент — борштанга 3 — соединен со шпинделем 1 станка плавающим патроном 2. Такое соединение исключает появление деформаций инструмента и узла направления при значительных отклонениях (до 0,2 мм) от соосности шпинделя и направляющей втулки. Для исключения влияния радиального биения внутренней поверхности вращающейся втулки 4 на точность обработки на борштанге установлена подпружиненная шпонка 5, а во втулке имеется шпоночный паз. Люнет 6 необходим для вывода борштанги из направляющей втулки при смене резца и других работах. Такую схему применяют при D < DВТ.
Для обработки отверстий с малыми межосевыми расстояниями между отверстиями в одной стенке заготовки используют схему, показанную на рис. 5.29, б. Здесь во вращающейся втулке 4 имеется паз 7 для прохождения резца, а в борштанге — паз для шпонки 8, установленной во втулке.
Рассмотренные одноопорные схемы направления инструмента во вращающихся втулках применяют для обработки отверстий диаметром D = 18... 120 мм и длиной не более 2 D при вылете инструмента l ин < 2,3D. Такие схемы обеспечивают точность обработки диаметральных отверстий, соответствующую IT6...IT12, позиционные отклонения ∆поз = 25... 120 мкм и отклонения меж- осевых размеров ∆м.р = 25... 150 мкм.
|
Для обработки соосных отверстий в нескольких стенках заготовки, растачивания отверстий в стенках заготовки, находящихся на расстоянии l x > 2,3D, растачивания глубоких отверстий l отв > 3D, а также отверстий с большой неравномерностью припуска применяют двухопорную схему направления по двум вращающимся втулкам (рис. 5.30). В схеме, показанной на рис. 5.30, б, диаметр отверстия передней втулки меньше диаметра растачиваемого отверстия (D BT1 < D), поэтому в передней направляющей втулке предусмотрен сквозной паз для прохождения резцов и в борштанге на всей длине ее направляемой части выполнен паз с ловителем шпонок у переднего торца. Точность обработки диаметральных отверстий соответствует IT6...IT12, отклонение от соосности осей отверстий относително общей оси 20...80 мкм, отклонение межосевого расстояния отверстий 30... 120 мкм.
Рис. 5.30. Схемы инструментальных наладок при плавающем соединении и двухопорном направлении борштанги:
а, б — по двум вращающимся втулкам при D BT1 ≥ D 1 и D BT1 < D соответственно; в — по двум вращающимся втулкам, одна из которых многопазовая; 1 — шпонка, закрепленная на борштанге;
2 — то же, на вращающейся втулке
Обработку ряда соосных отверстий (трех и более) с малыми отклонениями расположения, формы и размеров (например, отверстий под коленчатый и распределительный валы и в заготовках блоков цилиндров автомобильных двигателей, отверстий под рабочий вал в заготовках корпусов многоступенчатых центробежных насосов и других) ведут с использованием трех и более опор типа «вращающаяся втулка» (рис. 5.31). Чтобы обеспечить одновременную параллельную обработку системы отверстий, борштангу вводят в заготовку без вращения в определенном угловом положении для прохода резцов через пазы направляющих втулок и отверстия заготовки. Заготовку для этого сдвигают в поперечном направлении (показано стрелкой на рис. 5.31), перпендикулярном оси борштанги, на расстояние, достаточное для прохода резцов 1 и 2 через отверстия, а затем возвращают в исходное положение и закрепляют. По окончании обработки борштангу вновь фиксируют в определенном угловом положении для вывода, а заготовку сдвигают в поперечном направлении для исключения образования продольных рисок на обработанных поверхностях при быстром обратном ходе инструмента с резцами.
При использовании таких схем обработки отклонение от соосности промежуточных опор относительно крайних должно быть очень мало. В противном случае применение промежуточных опор (узлов направления) может привести к увеличению отклонений от соосности обрабатываемых отверстий из-за деформаций борштанги.
|
Рис. 5.31. Схема инструментальной наладки при плавающем соединении и многоопорном направлении борштанги:
1 — чистовой резец; 2 — черновой резец; 3 — ловитель шпонок;
4 — шпонка во вращающейся втулке
Часто в одной позиции AJI предусматривают предварительное и окончательное растачивание системы соосных отверстий. В таких случаях необходимо обеспечить условие l ин > l 1 (l 2) для разделения различных этапов обработки и обеспечения точности диаметров, а также условие l 1 = l 2 = l 3 =... = l n (см. рис. 5.31). Точность обработки диаметральных размеров системы соосных отверстий при такой схеме направления борштанги соответствует IT6...IT10, а отклонения от соосности осей отверстий относительно общей оси составляют 0,015...0,05 мм на длине до 600 мм.
Крепежные отверстия — это группа отверстий корпусной детали (гладких или резьбовых), используемых для присоединения и связанных координатами положения их центров внутри группы. Диаметры отверстий в группе чаще одинаковые, но могут и различаться (от 6 до 50 мм), глубина отверстий преимущественно одинаковая. При изготовлении корпусных деталей на AЛ и поточных линиях из АС технологические переходы обработки крепежных отверстий составляют до 70 % от общего числа переходов. Поэтому наиболее распространенными инструментами на AЛ являются сверла. Обработка крепежных отверстий на AЛ имеет следующие особенности:
1) метод обработки и режимы резания зависят от такта выпуска т линии;
2) работа в автоматическом режиме может быть нарушена вследствие плохого отвода стружки из обрабатываемых отверстий, особенно при вертикальном и наклонном расположении осей глухих отверстий;
3) несвоевременный выход из строя инструментов (их поломка, катастрофический износ и т. п.) требует оснащения AЛ специальными автоматами, сигнализирующими о наличии отверстий в обрабатываемой заготовке, т. е. возникает необходимость дополнительных позиций в AЛ;
4) инструментальные наладки часто имеют режущий и вспомогательный инструмент специфической конструкции.
К крепежным отверстиям предъявляют ряд требований по их технологичности:
1) межосевое расстояние между отверстиями должно быть не менее минимально допустимого, т. е. А ≥ A min (для заготовок из чугунов A min = (2,78...4,75) d, из сталей A min = (4,8...6,9) d, а из алюминиевых сплавов А min = (4,8...6,2) d, где d — диаметр отверстия);
2) длина отверстий l должна быть минимально возможной (для заготовок из стали l ≤ 3d, а для заготовок из чугуна и алюминиевых сплавов l ≤ 5 d);
3) отклонения от перпендикулярности торцев отверстия на входе и выходе относительно оси инструмента должны быть не более 10°;
4) обязательна унификация отверстий по диаметрам, фаскам и другим элементам, так как это сокращает номенклатуру режущего и вспомогательного инструмента, приспособлений для настройки и смены инструмента, причем предпочтение следует отдать сквозным отверстиям.
Рис. 5.32. Инструментальная наладка сверлильной позиции AЛ или АС
В большинстве случаев на AЛ и АС сверление отверстий выполняют с направлением сверл по кондукторным втулкам. Спиральное сверло 8 (рис. 5.32) с коническим хвостовиком устанавливают в удлинитель 9, который помещают в отверстие шпинделя 10 и крепят двумя винтами 1 с упором в наклонный скос. Сверло направляется сменной втулкой 5, установленной в постоянной втулке 6 кондукторной плиты 7. Крутящий момент от шпинделя передается удлинителю шпонкой 11. Гайка 2 предназначена для регулировки (наладки) вылета l нал сверла (после его перетачивания) относительно торца шпинделя. Ее контрят гайкой 4 через замковую шайбу 3, выступ которой входит в продольный паз хвостовика удлинителя. Основные схемы инструментальных наладок при сверлении представлены на рис. 5.33.
Рис. 5.33. Схемы инструментальных наладок при сверлении
Схему с закреплением сверла в удлинителе 1 (см. рис. 5.33, а) применяют для регулировки вылета сверла и уменьшения жесткости инструментальной наладки. Схема с закреплением сверла в короткой переходной втулке 2 (см. рис. 5.33, б) имеет большую жесткость по сравнению с предыдущей. Ее применяют как отдельно, так и в сочетании со схемой а при различных расстояниях от торца шпиндельной коробки до поверхности заготовки. Схема, приведенная на рис. 5.33, в, содержит быстросменный патрон 3, позволяющий сократить время установки инструмента на шпиндель. Схему, представленную на рис. 5.33, г, применяют при сверлении глубоких отверстий. Сверло дополнительно закрепляют в оправке с помощью зажимной гайки 4 и разрезного кольца во избежание его выпадения при быстром обратном ходе. Наконец, на рис. 5.33, d и e даны схемы, которые можно рекомендовать при сверлении предварительно зацентрованных отверстий, рассверливании предварительно просверленного отверстия, сверлении одиночного отверстия диаметром более 40 мм, а также в случае, когда применение кондукторной втулки затруднено. При этом для обработки предпочтительна наладка, в которой сверло устанавливают в специальный патрон 5 и зажимают непосредственно по ленточкам, обеспечивая тем самым повышенную жесткость системы шпиндель — патрон — сверло (схема е).
|
|
Таксономические единицы (категории) растений: Каждая система классификации состоит из определённых соподчиненных друг другу...
Организация стока поверхностных вод: Наибольшее количество влаги на земном шаре испаряется с поверхности морей и океанов (88‰)...
Типы оградительных сооружений в морском порту: По расположению оградительных сооружений в плане различают волноломы, обе оконечности...
Кормораздатчик мобильный электрифицированный: схема и процесс работы устройства...
© cyberpedia.su 2017-2024 - Не является автором материалов. Исключительное право сохранено за автором текста.
Если вы не хотите, чтобы данный материал был у нас на сайте, перейдите по ссылке: Нарушение авторских прав. Мы поможем в написании вашей работы!