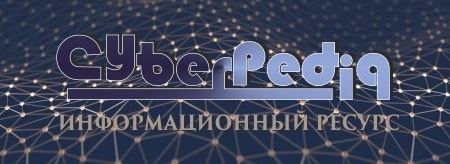
Папиллярные узоры пальцев рук - маркер спортивных способностей: дерматоглифические признаки формируются на 3-5 месяце беременности, не изменяются в течение жизни...
Биохимия спиртового брожения: Основу технологии получения пива составляет спиртовое брожение, - при котором сахар превращается...
Топ:
Техника безопасности при работе на пароконвектомате: К обслуживанию пароконвектомата допускаются лица, прошедшие технический минимум по эксплуатации оборудования...
Проблема типологии научных революций: Глобальные научные революции и типы научной рациональности...
Интересное:
Мероприятия для защиты от морозного пучения грунтов: Инженерная защита от морозного (криогенного) пучения грунтов необходима для легких малоэтажных зданий и других сооружений...
Берегоукрепление оползневых склонов: На прибрежных склонах основной причиной развития оползневых процессов является подмыв водами рек естественных склонов...
Наиболее распространенные виды рака: Раковая опухоль — это самостоятельное новообразование, которое может возникнуть и от повышенного давления...
Дисциплины:
![]() |
![]() |
5.00
из
|
Заказать работу |
|
|
Ступенчатые валы
Валы предназначены для передачи крутящих моментов и монтажа на них различных деталей и механизмов. Конструктивно ступенчатые валы подразделяют на гладкие, фланцевые и валы- шестерни. В общем случае они представляют собой сочетание гладких посадочных и непосадочных, шлицевых, шпоночных, резьбовых и переходных поверхностей. Для уменьшения массы валов их часто выполняют пустотелыми. Если отношение длины вала к среднему диаметру L / D ≤ 12, вал считают жестким, при L / D > 12 — нежестким.
Технические требования, предъявляемые к валам, характеризуются следующими данными.
Диаметральные размеры посадочных шеек выполняют по IT7, 1Т6, реже по IT5, других шеек — по IT 10, IT 11; допуски на длину ступеней вала назначают в пределах 0,1...0,4 мм.
Допуски формы (отклонения от круглости, цилиндричности и прямолинейности) обычно составляют часть допуска Т i, на выполняемый диаметральный размер (для тел вращения, например, до 0,ЗТ i). Допуски расположения — отклонения от параллельности шпоночных канавок или шлицевых поверхностей относительно оси не более 0,1 мкм на 1 мм длины; отклонения от перпендикулярности для опорных заплечиков под подшипники и привалочных фланцевых поверхностей валов не более 0,1 мкм; соосность поверхностей в пределах 0,01...0,03 мм.
Неравномерность шага шлицевых поверхностей, их смещение относительно оси должно быть не более 0,02 мм. Допускаемые биения посадочных шеек относительно базовых поверхностей не должны превышать 0,01...0,03 мм, а непосадочных 0,05...0,10 мм. Шероховатость поверхности посадочных шеек Ra = 0,8...0,2 мкм, непосадочных шеек Ra = 3,2...6,3 мкм.
Валы, работающие с высокой частотой вращения, подвергают динамической балансировке, их дисбаланс не должен превышать 12...40 г мм. Ступенчатые валы изготовляют из стали марок 25, 35, 40, 45, 35Х, 40Х, 40ХН, 45ХНМ, 38Х2ЮА, 38Х2МЮА и других, подвергаемой для повышения износостойкости и физико-механических свойств материала различным видам термической обработки. Валы из малоуглеродистых сталей цементируют на глубину 0,7... 1,2 мм, обеспечивая твердость после закалки и отпуска в пределах 55...58 HRC; из среднеуглеродистых сталей подвергают улучшению, нормализации или поверхностной закалке, а валы из высоколегированных сталей (38Х2ЮА, 38Х2МЮА и др.), работающие при высоких скоростях скольжения, азотируют на глубину 0,3...0,4 мм, обеспечивая твердость до 1000 HV.
|
Заготовки для ступенчатых валов в серийном производстве при небольших перепадах диаметров ступеней получают резкой из горячекатаного проката. При значительных перепадах диаметров ступеней заготовки валов изготовляют ковкой на молотах или прессах. В крупносерийном и массовом производстве заготовки ступенчатых валов получают штамповкой из проката, высадкой на горизонтально-ковочных и обжатием на радиально-ковочных машинах, поперечно-клиновой прокаткой. Эти методы (кроме последнего) обеспечивают коэффициент использования материала К и.м ≈ 0,7. При поперечно-клиновой прокатке K и.м ≥ 0,85. Типовой ТП изготовления заготовок состоит из следующих операций: отрезания заготовки из проката, ее нагреве до температуры ковки, непосредственного формоизменения, удаления заусенцев или облоя, термической обработки и правки. После пластического деформирования заготовку подвергают термической обработке в целях снятия остаточных напряжений и обеспечения необходимой структуры металла.
Основными факторами, определяющими технологию изготовления и применяемое оборудование, являются конструкция вала, его размеры и жесткость, технические требования, программа выпуска.
При обработке заготовок валов в качестве технологических баз используют центровые отверстия, которые позволяют обрабатывать почти все наружные поверхности вала на единых базах с установкой в центрах. Жесткие требования на линейные размеры обеспечиваются применением плавающего переднего центра и базированием заготовки по торцу, от которого выдерживают размеры при токарной обработке и шлифовании заплечиков. Это исключает влияние погрешности зацентровки вала на точность линейных размеров.
|
Маршрут обработки заготовок в центрах включает обычно следующие операции: создание базовых поверхностей, черновое и чистовое обтачивания, черновое шлифование шеек, фрезерование шпоночных пазов, сверление отверстий, нарезание резьб, термическую обработку, зачистку центров, шлифование шлицев, окончательное шлифование шеек, микрофиниширование шеек, контроль размеров вала. Для обеспечения заданной точности в маршруте необходимо соблюдать принцип постоянства баз при обработке практически всех ответственных поверхностей: посадочных шеек, торцевых заплечиков, боковых поверхностей шпоночных пазов и шлицев, а также обеспечивать соосность шеек и внутренних поверхностей. Точность обработки после каждого перехода повышается, число переходов для каждой элементарной поверхности зависит от точности исходной заготовки и технических требований на деталь.
Обработку заготовок нежестких валов ведут с использованием в схеме установки дополнительных опор: неподвижных и подвижных люнетов. Для применения неподвижного люнета в маршрут изготовления вала включают дополнительные операции обработки шейки под люнет (а в ряде случаев и контрольных поясков, используемых при выверке заготовки на станке). Такую шейку выполняют на середине заготовки, а неподвижный люнет устанавливают на станине станка. Подвижный люнет располагают на суппорте токарного станка, осуществляющем подачу: при этом опорные ролики люнета контактируют с обрабатываемой поверхностью. Кроме того, если допускают технические требования, маршрут изготовления нежестких валов дополняют операциями правки. На стадии выполнения операций обработки стараются уменьшить силы резания, снижая глубину резания и подачу инструмента, а также изменяя у резцов главный угол в плане.
Ступенчатые валы изготовляют различными сериями, используя для этого разные структурные схемы операций и оборудование, однако общая последовательность операций остается одинаковой для любого типа производства.
|
В серийном производстве при отсутствии специального оборудования базовые поверхности валов обрабатывают на токарном станке за два установа. Заготовку закрепляют в патроне, подрезают торец, центровым сверлом обрабатывают отверстия. После перезакрепления переход повторяют. Смена баз и перезакрепление заготовки приводят к возникновению погрешности расположения осей центровых отверстий относительно оси, вследствие которой в процессе обработки заготовка будет базироваться по кромкам конических поверхностей, вызывая их смятие и погрешности формы. Создание базовых поверхностей таким способом характерно для заготовок валов, осей, торсионов и требует для повышения точности обработки введения в процесс дополнительных операций правки и восстановления базовых поверхностей. Центровые отверстия по большому диаметру D конуса (рис. 5.14, а—в) обрабатывают с допуском Т D = 0,2...0,5 мм, что вызывает изменение глубины центрового отверстия на ∆ l = 0,5 Т D / tg 30° = 0,17...0,43 мм. Такое изменение при отсутствии опорной торцевой базы приведет к погрешности линейных размеров.
Рис. 5.34. Виды центровых отверстий (а—в) и торцеподрезной инструмент для обработки центрового отверстия (г)
В крупносерийном и массовом производстве для обработки базовых поверхностей применяют фрезерно-центровальные полуавтоматы МР-71,..., МР-74 и автоматы А981, А982. Для обработки заготовку устанавливают в призмы и в осевом положении базируют по торцевой поверхности, расположенной предпочтительно посредине вала для равномерного распределения припуска по торцам. На первой позиции торцевой фрезой обрабатывают торцы, на второй — центровые отверстия. Для обеспечения шероховатости конической поверхности с параметром Ra = 1,6 мкм подача центрового сверла должна быть 0,05...0,06 мм/об. Соосность осей самоцентрируюгцих призм и шпинделей станка обеспечивает минимальную погрешность зацентровки.
В последнее время в крупносерийном и массовом производстве применяют однопозиционные станки, оснащенные торцеподрезным инструментом (рис. 5.34, г), конструкция которого обеспечивает идентичность глубины центровых отверстий (размер l) и соответственно стабильность точности обработки линейных размеров. Инструмент работает со скоростью резания около 70 м/мин для пластин и около 20 м/мин для сверл.
|
Токарную обработку валов в серийном производстве выполняют на станках с ЧПУ моделей 16К20ФЗ, 16К.20Т1.02, 1716ПФ30 и других, работающих по полуавтоматическому циклу. Оснащенные 6- и 8-позиционными инструментальными головками с горизонтальной осью поворота или магазином эти станки применяют для обработки заготовок со сложным ступенчатым и криволинейным профилем, включая нарезание резьб. Наличие в головке нескольких инструментов позволяет вести многопереходную обработку поверхностей, устойчиво обеспечивая квали- тет точности IT 10 и выше. Схема обтачивания вала на станке с ЧПУ приведена на рис. 5.35.
Рис. 5.35. Схема обтачивания вала на станке с ЧПУ:
а — чистовой проход; б — нарезание резьбы
Время обработки на станках с ЧПУ по сравнению со станками с ручным управлением сокращается в 1,5—2 раза за счет сокращения вспомогательного времени и интенсификации режимов резания.
В крупносерийном производстве обработку валов ведут на многорезцовых или гидрокопировальных полуавтоматах. Точность обработки на многорезцовом полуавтомате в значительной степени зависит от положения резцов в наладке. Неодновременное начало и окончание их работы вызывает изменение отжатий технологической системы, что приводит к возникновению погрешности формы обрабатываемых поверхностей. В общем случае точность обработки соответствует IT10, IT 11, а точность линейных размеров и их стабильность выше, чем на обычных станках. Многорезцовые полуавтоматы более эффективны при тонком обтачивании (точность обработки соответствует IT9). Время наладки и подналадки гидрокопировальных станков в 2—3 раза меньше времени наладки многорезцовых станков и составляет в среднем 30 мин. Точность обработки на гидрокопировальных станках соответствует IT 10.
В последнее время в целях расширения технологических возможностей гидрокопировальных полуавтоматов их выпускают с многоинструментальными головками и устанавливают дополнительные каретки (рис. 5.36). Заготовку устанавливают на центры, используя плавающий передний центр; координацию линейных размеров ведут от упора в левую торцевую поверхность.
Поверхности вала обрабатывают резцом 1, им же обтачивают хвостовик. Резцом 2 обтачивают поверхность под шлицы, резцом 4 подрезают торец, а резцом 3 — канавку под стопорное кольцо. Иногда для подрезки торцев используют несколько резцов, расположенных в разных плоскостях.
|
Рис. 5.36. Схема обработки ступенчатого вала на гидрокопировальном полуавтомате
В массовом производстве обработку валов ведут на AЛ, скомпонованных из фрезерно-центровального и нескольких гидрокопировальных станков с автоматической загрузкой и транспортировкой заготовок роботами портальной конструкции.
Точность обработки обеспечивают проведением при проектировании операции необходимых точностных расчетов, назначением на их основе режимов резания, а также использованием адаптивных систем управления. На станках с ЧПУ точность формы повышают путем предыскажения траектории движения инструмента.
Обработку шлицевых поверхностей валов ведут на шлицефрезерных станках червячными шлицевыми фрезами при установке заготовок в центрах. Если шлицевая поверхность предусматривает центрирование по наружнему диаметру, то обработку выполняют фрезами, имеющими у основания зубьев фланк для обработки фасок на вершинах шлицев. При центрировании вала по внутреннему диаметру шлицы обрабатывают фрезами с усиками для одновременного прорезания канавок во впадинах, чтобы облегчить процесс шлифования шлицев. Если центрирование соединения ведут по внутреннему диаметру и боковым поверхностям одновременно, то профиль зубьев фрезы имеет более сложную форму. Канавки во впадинах иногда обрабатывают дисковыми фрезами отдельно. Припуск на шлифование шлицев после термической обработки предусматривают до 0,1 мм на сторону. Шероховатость после фрезерования составляет по боковой поверхности Ra = 10 мкм, по дну впадины Ra = 5 мкм; точность обработки соответствует IT9, IT10. Шлифованием шлицевых поверхностей точность обработки повышают до IT8, IT9; погрешность шага уменьшают до 0,01 мм, а шероховатость поверхности — до Ra = 0,4 по дну и Ra = = 1,8 мкм по боковой поверхности.
Шлицевые поверхности с эвольвентным профилем нарезают фрезами с прямолинейным профилем зуба. Фрезерование открытых шпоночных пазов выполняют дисковыми срезами на шпоночно-фрезерных станках. Закрытые шпоночные пазы (рис.5.37) обрабатывают шпоночными, концевыми или сверлопазовыми фрезами. Для облегчения работы шпоночных и концевых фрез вначале сверлят отверстие на полную глубину паза сверлом меньшего диаметра, чем ширина паза, а затем осевой подачей вводят фрезу и обрабатывают паз.
В серийном производстве обработку таких пазов ведут методом «маятниковой подачи», используя шпоночные фрезы (см. рис. 5.37). В результате на боковых поверхностях пазов появляются продольные риски. Для обеспечения натяга в соединении паз калибруют зачистным проходом, который выполняют с применением патрона, регулирующего эксцентриситет фрезы. Точность обработки ширины паза соответствует IT8, IT9 при шероховатости боковой поверхности Ra = 5 мкм. Смазочные отверстия различного назначения в зависимости от конструкции вала обрабатывают на сверлильных станках с вертикальной или горизонтальной осью расположения шпинделя.
Резьбы на валах в массовом производстве нарезают твердосплавным инструментом на автоматах и станках с ЧПУ, работающих по автоматическому циклу. Точность обработки резьбы соответствует полю допуска 6h. Перед резьбонарезанием шейки валов шлифуют с точностью до IT7. Менее ответственные резьбы на валах получают резьбофрезерованием. В серийном производстве резьбы нарезают на токарно-винторезных станках обычным способом, а также на станках с ЧПУ.
Посадочные шейки валов шлифуют дважды (предварительно и окончательно) методом продольного или врезного шлифования при установке заготовок в центрах.
Рис. 5.37. Схема обработки закрытого шпоночного паза
Предварительным шлифованием обеспечивают квалитет точности IT8, IT9 и шероховатость поверхности Ra = 0,4...0,8 мкм, окончательным, которое выполняют после термической обработки, — IT6, IT7 и Ra = 0,2...0,4 мкм.
В большинстве случаев валы шлифуют методом продольного шлифования, для которого характерно равномерное изнашивание круга в процессе работы, его самозатачивание, минимальное тепловыделение и высокое качество поверхности.
Для совмещенного шлифования характерна одновременная обработка нескольких поверхностей широким кругом (рис. 5.38). В этом случае возможна и обработка торцевых заплечиков. Обработка вала совмещенным шлифованием ведется по автоматическому циклу, обеспечивая высокую производительность.
Точность формы шлифованных поверхностей определяется в значительной степени состоянием базовых поверхностей, поэтому перед окончательным шлифованием их исправляют конусными абразивными кругами на специальных станках.
В отдельных случаях при обработке высокоточных валов применяют тонкое шлифование, когда речь идет о шероховатости поверхности Ra = 0,025...0,1 мкм; при этом снимаемый слой металла составляет 0,05...0,1 мм. Эту операцию выполняют на высокоточных станках с предварительной подготовкой круга и применением охлаждающей жидкости.
Шейки валов шлифуют и на бесцентрово-шлифовальных станках методом проходного или врезного шлифования. Обрабатываемую заготовку 1 устанавливают на опорный нож 3 между шлифовальным 4 и ведущим 2 кругами (рис. 5.39). Вращение заготовки происходит под действием силы трения, возникающей в контакте с ведущим кругом, а продольная подача достигается поворотом оси ведущего круга на определенный угол.
Рис. 5.38. Схема обработки ступенчатого вала широким шлифовальным кругом
Рис. 5.39. Схема бесцентрового круглого шлифования вала
Жесткость технологической системы бесцентрово-шлифовальных станков в 1,5—2 раза выше жесткости круглошлифовальных станков. Это позволяет вести обработку со скоростью резания до 60 м/с с точностью, соответствующей IT5, IT6. Бесцентровым шлифованием обрабатывают гладкие валы или валы, имеющие небольшие перепады ступеней.
После шлифования острые кромки на поверхностях валов притупляют, переходные поверхности подвергают доработке, а посадочные поверхности — суперфинишированию. В крупносерийном и массовом производстве валы обрабатывают на АЛ, которые компонуют из специальных станков, соединенных транспортными системами с роботами для установки и снятия заготовок, а также со средствами активного контроля и централизованным управлением.
Технический контроль валов предусматривает контроль всех ответственных размеров и параметров. С этой целью применяют многомерные контрольные стенды и приспособления, оснащенные различными приборами.
Коленчатые валы
Коленчатые валы подразделяют на цельные, составные и сборные. Цельные изготовляют длиной до 5000 мм, составные — из двух секций для крупных судовых двигателей, сборные — для двигателей небольшой мощности (например, мотоциклетных). Наиболее массовыми в производстве считаются коленчатые валы автотракторных двигателей. Их длина изменяется от 400 до 1000 мм. Являясь конструктивно и технологически сложной деталью, коленчатый вал считается одной из самых ответственных деталей двигателя. Все это обусловливает высокие требования к точности изготовления коленчатых валов: квалитет точности диаметральных размеров коренных и шатунных шеек IT5 (реже IT6), допуски формы коренных и шатунных шеек ≤ 0,3 от допуска на диаметр этих шеек, отклонения от соосности расположения коренных шеек ≤ 0,02 мм, отклонения от параллельности осей коренных и шатунных шеек ≤ 0,015 мм на длине шейки, угол разворота колен
± 30', биение коренных шеек относительно оси центровых отверстий 0,01...0,03 мм, шероховатость поверхности коренных шатунных шеек Ra = 0,08...0,2 мкм, дисбаланс коленчатых валов 15...40 г мм, твердость коренных и шатунных шеек 58...62 HRC при глубине 3...5 мм.
Коленчатые валы бензиновых двигателей изготавливают из углеродистой стали марок 45, 45А, 40Х, 45Г2, 50Г и др. Для дизелей применяют легированные стали 18ХНМА, 40ХНМА, 42ХМФА, 18Х2Н4ВА и др. Хромоникелевольфрамовая сталь 18Х2Н4ВА отличается особенно высокой прочностью (321...381 НВ) и ударной вязкостью. Поверхностную твердость и износостойкость углеродистых сталей повышают термической обработкой с нагревом токами высокой частоты (ТВЧ). Твердость и усталостную прочность поверхностного слоя валов из высоколегированных сталей 40ХМА, 18Х2Н4ВА обеспечивают азотированием.
В качестве материала для коленчатых валов используют и высокопрочный чугун с шаровидной формой графита. Такие чугуны содержат, % (масс.): 0,2...0,25 Сг, 1,15...1,4 Мn, < 0,002...0,14 S, а также незначительное количество церия и других легирующих элементов. Механические свойства таких чугунов близки к свойствам высококремнистой стали. Материал имеет высокие эксплуатационные качества и хорошо обрабатывается режущим инструментом. Применяют также серые чугуны, модифицированные сплавом ферроцерия с магнием.
В качестве заготовок коленчатых валов автотракторных двигателей используют штамповки, изготовленные на AЛ. Так, заготовку для двигателей КамАЗов получают из горячекатаной труднообрабатываемой стали 42ХМФА, легированной ванадием. На AЛ проводят индукционный нагрев, предварительное формоизменение заготовки вальцеванием, ее штамповку на кривошипном горячештамповочном прессе, обрезание облоя и выкрутку колен на гидравлическом прессе, правку заготовки, термическую обработку с контролем твердости поковок, удаление окалины. Применяемые на заводах ТП изготовления заготовок обеспечивают их высокие точностные параметры. Более крупные заготовки, например для тепловозных двигателей, получают методом гибки с высадкой, сущность которого заключается в следующем. Слиток нагревают в газопламенной печи и на мощном прессе подвергают протяжке, в результате которой получают длинную круглую заготовку. Эту заготовку обтачивают по наружному диаметру в механическом цехе в целях удаления дефектов поверхности после ковки. Для последующего формоизменения участок заготовки под одно колено нагревают токами промышленной частоты и подают под пресс, где в штампе сначала высадкой, а затем гибкой формообразуют колено. Таким же образом последовательно обрабатывают каждое колено. Это позволяет, используя менее мощное оборудование, получить качественную заготовку со значительно меньшими припусками и благоприятным расположением волокон. Заготовки крупных судовых двигателей в серийном производстве изготовляют методом свободной ковки универсальными инструментами. В этом случае К и.м составляет 0,2...0,25.
Заготовки литых валов получают литьем в песчаные или оболочковые формы. Литье в оболочковые формы обеспечивает ква- литет точности IT12...IT14 с припусками на обработку 1,5...3 мм. Это позволяет отдельные поверхности оставлять черными и начинать обработку шеек шлифованием. В связи с высокой износоустойчивостью чугуна шейки валов иногда не подвергают термической обработке.
Коленчатые валы автомобильных и тракторных двигателей в крупносерийном и массовом производстве получают на поточных или автоматических линиях по типовым ТП. В качестве баз для обработки коренных шеек и других поверхностей принимают центровые отверстия, на которых выполняют черновую, чистовую и отделочную обработки, сохраняя принцип постоянства баз. Соответственно шатунные шейки обрабатывают при базировании по коренным шейкам, что обеспечивает их параллельность и точность радиуса кривошипа. Угловыми базами служат обработанные площадки на противовесах или поверхностях кривошипов. В качестве базы по длине используют поверхности щек средней коренной шейки. В серийном производстве при изготовлении коленчатых валов специальных ответственных двигателей ТП отрабатывают особенно тщательно. Они состоят из 40, 60 и более операций. Отдельные поверхности подвергают трех- или четырехкратному шлифованию.
Рассмотрим особенности обработки заготовки коленчатого вала для V-образного 12-цилиндрового двигателя, имеющего 6 шатунных и 7 коренных опор. В качестве заготовки использована штамповка, изготовленная на кривошипном горячештамповочном прессе. Материал заготовки 18ХНВА. Укрупненно процесс можно разделить на четыре этапа.
1. Черновая обработка, которая заключается в удалении больших объемов материала (обработка концов вала, центровых отверстий, обтачивание коренных шеек за два установа, шлифование четвертой коренной шейки под люнет, обтачивание шатунных шеек), шлифовании коренных шеек, обработке центрального отверстия в коренных и отверстий в шатунных шейках; закалка и высокий отпуск.
2. Восстановление баз — центровых фасок, шлифование пятой коренной шейки под люнет, обработка концов вала, коренных и шатунных шеек, шлифование шеек, обработка контуров щек, их скосов, шлифование торцев щек, окончательная обработка центрального отверстия и отверстий в шатунных шейках, обработка смазочных отверстий и старение.
3. Восстановление баз, шлифование коренных и шатунных шеек, азотирование.
4. Восстановление баз, полирование торцев щек их контуров, двухкратное шлифование коренных и однократное шлифование шатунных шеек, полирование центрального отверстия и отверстий в шатунных шейках, балансировка детали.
После изготовления деталей выполняют контроль их размеров.
При обработке заготовок коленчатых валов структура построения операций и применяемое оборудование зависят от объема выпуска. При этом в любом процессе особое внимание уделяется состоянию базовых поверхностей и выполнению отделочных операций для формирования высокой точности обработки.
Для снижения деформаций при обработке заготовок нежестких коленчатых, распределительных и других валов кроме люнетов применяют специальные станки с центральным или двухсторонним приводом.
В массовом и крупносерийном производстве обработку базовых поверхностей заготовок коленчатых валов выполняют специальным инструментом (см. рис. 5.34, г) на торцеподрезных центровальных станках. В основу конструкции станка положен торцеподрезной полуавтомат и балансировочная машина. Обработку ведут после нахождения оси, относительно которой заготовка наиболее уравновешена. Базирование заготовки осуществляют по крайним коренным шейкам.
Коренные шейки обрабатывают на специальных многорезцовых станках с центральным или двухсторонним приводом в центрах. Обработку шатунных шеек ведут на специальных токарных станках, основное кинематическое движение в которых задается с помощью двух эталонных коленчатых валов (рис. 5.40). Заготовка 1 вращается синхронно с эталонами 3 относительно коренных шеек. Кулисы суппорта 2 с инструментами 4, совершая плоскопараллельное движение, перемещаются вместе с обрабатываемыми шейками, благодаря чему кинематика резания сохраняется неизменной.
Рис. 5.40. Схема обтачивания шатунных шеек коленчатого вала
(I — траектория движения центра обрабатываемой шейки;
II — траектория движения режущей кромки резца)
При обработке заготовок более крупных валов, например для тепловозных двигателей, такие станки не применяют в связи с большими вращающимися массами. Обработку шатунных шеек в этом случае ведут на токарно-дисковых станках последовательно, одну за другой (рис. 5.41). В конструкции станка имеется вращающийся суппорт 4, который приводится во вращение зубчатым венцом 5 от червячного привода и осуществляет главное рабочее движение инструмента 6. Радиальное перемещение суппорт совершает по призматическим направляющим 3.
Рис. 5.41. Схема обработки коленчатого вала на токарно-дисковом станке
Перед обработкой заготовку крайними коренными шейками устанавливают в призмы 1, выверяя по разметке горизонталь. Ось обрабатываемой коренной шейки совмещают с осью вращающегося суппорта поворотом заготовки вала вокруг его оси и поперечным перемещением корпуса 7. Заготовку по коренным шейкам закрепляют элементами 2. На таких станках обрабатывают и контуры щек. Точность при чистовой обработке может соответствовать IT8, IT9 при шероховатости Ra = 0,8...1,6 мкм.
Термическая обработка шеек коленчатых валов обычно заключается в закалке и низком отпуске до твердости 55...58 HRC. В условиях крупносерийного и массового производства закалку ведут с нагревом ТВЧ. Заготовки устанавливают вертикально шейками в индукторы 1 (рис. 5.42, а), нагрев ТВЧ продолжается определенное время, а затем из этих же индукторов подается вода и происходит закалка поверхностного слоя. Длительностью охлаждения регулируют температуру отпуска и соответственно твердость закаливаемой поверхности.
Если переходные поверхности валов — галтели — подвергают поверхностному пластическому деформированию, то в процессе термической обработки их защищают керамическими полукольцами 2 (рис. 5.42, б) или обмазывают специальным составом, а затем (после термической обработки) обкатывают роликами.
Для повышения общей усталостной прочности и износостойкости поверхностей шеек коленчатых валов применяют азотирование. Для этого вал устанавливают на выдвижную платформу электрической тоннельной печи, укладывают коренными шейками на графитовые подшипники и сообщают ему медленное вращение для исключения деформирования в процессе азотирования. Азотирование проводят в печи при температуре 520...530 °С перед последней отделочной операцией. Твердость поверхности на глубине 0,30...0,40 мм достигает 1000 HV и выше.
Рис. 5.42. Схема термической обработки коленчатого вала с нагревом ТВЧ(а) и защитные керамические полукольца (б)
(q — направление теплового потока при отпуске)
Для ответственных двигателей в качестве отделочной операции применяют микрошлифование подпружиненными шлифовальными брусками, совершающими дополнительно осциллирующее движение в осевом направлении относительно коренных и шатунных шеек, а также наружное хонингование брусками с алмазным наполнителем.
Контроль коленчатых валов ведут на многоинструментных контрольных приспособлениях или машинах, позволяющих сразу определить несколько размеров и параметров.
Рычаги в шатуны
К деталям этого класса относятся собственно рычаги разной формы, тяги, серьги, поводки, коромысла, балансиры, вилки, прихваты и шатуны (рис. 5.43).
Рычаги являются звеньями кинематических цепей машин, которые выполняют требуемые перемещения деталей с необходимой скоростью или фиксируют их положение относительно других деталей.
Рис. 5.43. Конструктивные разновидности рычагов: а — рычаги;
б — вилки
Они имеют два или большее количество основных отверстий, оси которых расположены параллельно или под различными углами. Тело рычагов представляет собой стержень, как правило, некруглого сечения. Кроме основных отверстий в них могут быть шпоночные и шлицевые канавки, крепежные отверстия и прорези в бобышках.
Технические условия на изготовление деталей этого класса следующие: квалитет точности диаметров основных отверстий рычагов IT7...IT9, шатунов — IT6...IT8; отклонения межосевого расстояния основных отверстий 0,05...0,2 мм; квалитет точности размера между торцами бобышек IT 10, ITU, а ширины шпоночных пазов IT9, IT 10; отклонение от параллельности осей основных отверстий 0,05...0,25 мм на 100 мм длины; отклонение от перпендикулярности торцевых поверхностей бобышек, головок шатунов относительно оси основных отверстий 0,05...0,3 мм на 100 мм радиуса, а торцевых поверхностей лапок вилок относительно оси основных отверстий 0,1...0,3 мм на 100 мм длины; отклонение от соосности наружных поверхностей головок нагруженных рычагов, тяг, серег относительно оси отверстий 0,5...1мм (из условий прочности); шероховатость поверхностей основных отверстий Ra = 0,32...2,5 мкм, торцев головок Ra = 1,25...3,2 мкм.
Рычаги и шатуны изготовляют из конструкционных и легированных сталей 20, 35, 45, 35Х, 40Х, 18ХНМА, 18ГН4ВА, а также серого и ковкого чугуна СЧ10, СЧ15, КЧ37-12 и др. В зависимости от объема выпуска, типа производства и применяемого материала заготовки получают ковкой, штамповкой или литьем. При изготовлении рычагов ковкой желательны простые формы, образованные плоскими и цилиндрическими поверхностями. При получении заготовок штамповкой выбранная поверхность разъема должна обеспечить легкую выемку ее из штампа. Предпочтительна симметричная форма заготовки относительно поверхности разъема и разъем по плоской поверхности (а не по криволинейной). Это облегчает и упрощает изготовление штампов.
Для штамповки используют паровоздушные штамповочные молоты. Чем больше объем выпуска, тем больше оснований использовать высокопроизводительное оборудование: кривошипные прессы, горизонтально-ковочные машины, метод поперечно-винтовой прокатки. Плоские рычаги (типа серег) штампуют из листа соответствующей толщины. Для снятия остаточных напряжений после штамповки и улучшения обрабатываемости после кузнечных операций заготовки рычагов подвергают нормализации. Стальные рычаги и вилки из среднеуглеродистых сталей, работающие при значительных нагрузках, для повышения прочности подвергают закалке и отпуску. Перспективным для изготовления рычагов, вилок является использование метода горячего прессования порошковых материалов, позволяющего получить заготовки практически без пор, с мелкозернистой структурой, что обеспечивает требуемые прочностные свойства изделий. Данный метод почти полностью исключает последующую механическую обработку, а при автоматизации производства — и ручной труд.
При получении заготовок литьем предпочтительнее прямолинейная форма рычага вместо криволинейной. Это упрощает изготовление модели и формы, так как допускает разъем в одной плоскости. Заготовки рычагов получают литьем в песчаные формы. Для образования основных отверстий применяют стержни. Заготовки стальных рычагов сложной формы и небольших размеров получают литьем в керамические формы по выплавляемым моделям. Для устранения возможного искривления рычаги из стали и ковкого чугуна подвергают правке до и в процессе обработки.
Для повышения точности заготовок применяют плоскостную или объемную калибровку. Плоскостная калибровка (чеканка) обеспечивает необходимую точность вертикальных размеров на отдельных участках поковок. Ее проводят в холодном состоянии на чеканочных кривошипно-коленных прессах. Поверхности, подвергнутые чеканке, в дальнейшем не обрабатывают вовсе или только шлифуют. Объемная калибровка обеспечивает точность размеров поковки в разных направлениях. Для мелких рычагов калибровку выполняют в холодном состоянии, для крупных — в горячем с нагревом заготовки до определенной температуры. Маршрут обработки заготовок рычагов резанием следующий:
1) последовательная или параллельная обработка торцевых поверхностей основных отверстий (у заготовок, подвергнутых чеканке или полученных точным литьем, эту обработку часто не проводят);
2) обработка основных отверстий;
3) обработка шпоночных пазов или шлицевых поверхностей в основных отверстиях;
4) обработка поверхностей стержня рычага, прорезей, пазов;
5) обработка вспомогательных отверстий, нарезание резьбы.
Применяют варианты маршрута, в которых первую и вторую
операции меняют местами или объединяют в одну. Например, при обработке на фрезерно-сверлильно-расточном станке в одной операции объединяют несколько видов обработки.
На разных этапах ТП используют различные технологические базы. При обработке торцевых поверхностей основных отверстий за базу принимают торцы и наружные поверхности бобышек (рис. 5.44, а). Для обеспечения равностенности головок (рис. 5.44, б) при обработке основных отверстий за базу берут обработанные торцы и наружные необработанные поверхности головок. Для обработки шпоночных и шлицевых канавок рычаги базируют по обработанной поверхности одного из основных отверстий и торцев (рис. 5.44, в). Для угловой ориентации используют либо второе отверстие, либо необработанную поверхность стержня, либо вторую бобышку рычага. При обработке пазов, уступов, технологических лысок, фасонных исполнительных поверхностей рычагов применяют схемы базирования, показанные на рис. 5.44, г, д. При обработке отверстий в большой и малой головках шатуна в качестве базы используют обработанные торцы, две технологические лыски на малой головке и одну лыску на большой головке рычага (рис. 5.44, е). При построении маршрута обработки рычагов должен быть выдержан принцип постоянств
|
|
Особенности сооружения опор в сложных условиях: Сооружение ВЛ в районах с суровыми климатическими и тяжелыми геологическими условиями...
Семя – орган полового размножения и расселения растений: наружи у семян имеется плотный покров – кожура...
Поперечные профили набережных и береговой полосы: На городских территориях берегоукрепление проектируют с учетом технических и экономических требований, но особое значение придают эстетическим...
Таксономические единицы (категории) растений: Каждая система классификации состоит из определённых соподчиненных друг другу...
© cyberpedia.su 2017-2024 - Не является автором материалов. Исключительное право сохранено за автором текста.
Если вы не хотите, чтобы данный материал был у нас на сайте, перейдите по ссылке: Нарушение авторских прав. Мы поможем в написании вашей работы!