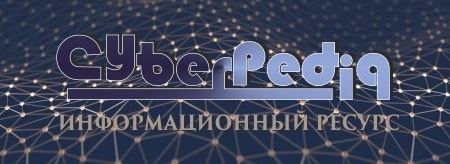
Наброски и зарисовки растений, плодов, цветов: Освоить конструктивное построение структуры дерева через зарисовки отдельных деревьев, группы деревьев...
Папиллярные узоры пальцев рук - маркер спортивных способностей: дерматоглифические признаки формируются на 3-5 месяце беременности, не изменяются в течение жизни...
Топ:
Комплексной системы оценки состояния охраны труда на производственном объекте (КСОТ-П): Цели и задачи Комплексной системы оценки состояния охраны труда и определению факторов рисков по охране труда...
Устройство и оснащение процедурного кабинета: Решающая роль в обеспечении правильного лечения пациентов отводится процедурной медсестре...
Интересное:
Берегоукрепление оползневых склонов: На прибрежных склонах основной причиной развития оползневых процессов является подмыв водами рек естественных склонов...
Искусственное повышение поверхности территории: Варианты искусственного повышения поверхности территории необходимо выбирать на основе анализа следующих характеристик защищаемой территории...
Лечение прогрессирующих форм рака: Одним из наиболее важных достижений экспериментальной химиотерапии опухолей, начатой в 60-х и реализованной в 70-х годах, является...
Дисциплины:
![]() |
![]() |
5.00
из
|
Заказать работу |
|
|
5.2.1. Технологические возможности станков с ЧПУ и требования к конструкции изготавливаемых деталей
Технологические возможности станков с ЧПУ обусловлены их высокой гибкостью, повышенной жесткостью, мощностью и точностью, многоинструментальностью, широким диапазоном частот вращения шпинделя и подач, возможностью коррекции положения режущего инструмента и изменения подачи без корректировки управляющей программы. На таких станках существенно сокращается вспомогательное время вследствие высоких скоростей (до 20...22 м/мин) холостых перемещений и минимизации до 2...3 с вспомогательного времени на смену инструмента. Технологические возможности станков с ЧПУ обеспечиваются их конструкцией и функциональными возможностями устройств ЧПУ.
Станки с замкнутой системой управления, имеющие обратную связь по перемещению исполнительного органа, обеспечивают более высокую точность позиционирования в сравнении с разомкнутыми, у которых такая связь отсутствует. По характеру программирования траектории перемещения инструмента станки бывают с позиционной или контурной системой управления. При позиционной системе управления программируют только координаты заданных точек, а перемещения из одной точки в другую обеспечивают направляющие станка. Применяют такие системы обычно на сверлильных и расточных станках. При контурной системе программируют всю траекторию перемещения инструмента, что обеспечивает возможность обработки криволинейных контуров. Контурные системы используют на токарных, фрезерных и сверлильно-фрезерно-расточных станках.
Токарные станки чаще выпускают с вертикально или наклонно расположенными направляющими станины. Это обеспечивает надежное удаление стружки либо в поддон, либо на транспортер. Наиболее распространены токарные станки с двумя или тремя координатами управления. В последнем случае кроме перемещения суппорта по двум координатам предусмотрено угловое позиционирование шпинделя. Это позволяет автоматизировать процесс установки и снятия несимметричной заготовки, а при наличии револьверной головки с приводом осевого инструмента в некоторых позициях и обработку заготовок корпусных деталей. Все современные станки имеют обратную связь между вращением шпинделя и перемещением суппорта для обработки винтовых поверхностей. На станках некоторых конструкций имеется возможность обработки винтовой поверхности с плавно изменяющимся шагом.
|
Для автоматической смены инструмента в подавляющем большинстве случаев используют револьверные головки, которые в сравнении с магазинными устройствами обеспечивают меньшие затраты времени на смену инструмента и экономически более целесообразны. Однако при размещении в головке длинных консольных инструментов возникают проблемы в связи с невозможностью их совместного размещения в зоне обработки. Поэтому в некоторых моделях токарных станков помимо револьверных головок предусматривают магазины инструментов. В других моделях возможность столкновения неработающего в данный момент инструмента с заготовкой и приспособлением исключается программно-математическим обеспечением системы ЧПУ. При наладке станка данные по вылетам инструмента и его положению в револьверной головке вводят в память устройства, и при проверке управляющей программы, в случае возникновения аварийной ситуации, цикл обработки прерывается.
В зависимости от типа производства используют одно-, двух- или трехсуппортные (рис. 5.1) станки. Независимое управление суппортами обеспечивает возможность последовательной и параллельной односторонней (см. рис. 5.1, а) или многосторонней (см. рис. 5.1, б, в) обработки.
|
В указанных компоновках заготовка обрабатывается в патроне (см. рис. 5.1, а, б) или в цанге (см. рис. 5.1, в). В последнем случае заготовка, обработанная в левом шпинделе, захватывается правым шпинделем, вытаскивается из левой цанги на необходимую длину и после отрезки осуществляется обработка левой стороны заготовки.
Рис. 5.1. Варианты компоновок токарных станков с ЧПУ
При такой компоновке управляемых координат может быть семь или восемь с учетом управляемого поворота по координате С. Помимо независимых перемещений суппортов по двум координатам и углового позиционирования шпинделей предусматривается управление их осевым перемещением.
В конструкциях револьверных головок токарных станков с ЧПУ предусмотрена возможность использования вращающихся
инструментов (сверл, зенкеров, разверток, метчиков, пальцевых фрез). Помимо токарных переходов на этих станках можно обрабатывать радиальные и торцевые отверстия, расположенные не на оси вращения; шпоночные пазы; сложнопрофильные элементы на развертке и торцах цилиндра.
Фрезерные станки с ЧПУ имеют вертикальную, горизонтальную или комбинированную компоновку и как минимум три управляемые координаты.
В современных моделях сверлильно-фрезерно-расточных станков возможна линейная, круговая или винтовая интерполяция, что обеспечивает возможность формообразования не только криволинейных плоских и объемных поверхностей, но и винтовых. На таких станках можно фрезеровать наружные и внутренние резьбовые поверхности, вырезать отверстия в плитах без предварительного сверления отверстия для ввода концевой фрезы, обрабатывать методом обкатывания объемные криволинейные поверхности (например, рабочую часть лопаток газовых турбин). Предусмотрена также сплайновая интерполяция (на базе метода конечных элементов) для соединения заданной последовательности точек в гладкий непрерывный контур с точным прохождением через все точки сплайна при высокоскоростной обработке. Разработчики сверлильно-фрезерно-расточных станков главным образом нацелены на создание системы высокоскоростной высокоточной обработки, обеспечивающей сокращение времени на обработку по сравнению с традиционными технологиями. Максимальная рабочая подача на таком оборудовании составляет 10 000 мм/мин при максимальной частоте вращения шпинделя не менее 20 тыс. об/мин.
|
Режущие инструменты чаше всего размещают либо в револьверных головках, либо в магазинах, что обеспечивает их автоматическую замену при выполнении операции. Помимо фрез в инструментальную наладку могут входить мерные инструменты и расточные оправки для обработки гладких или резьбовых отверстий.
Сверлильно-фрезерно-расточные станки в основном выпускают горизонтальной компоновки с четырьмя координатами управления (три координатных перемещения и вращение стола вокруг оси Y) (рис. 5.2, а). В ряде случаев применяют специальную конструкцию станка, когда дополнительно нужно обеспечить программируемое вращение А вокруг оси X (рис. 5.2, б). Реже применяют станки вертикальной компоновки с программированием трех линейных перемещений. В серийном производстве используют двухшпиндельные станки с вертикальным и горизонтальным шпинделями (рис. 5.2, в), что обеспечивает как последовательную, так и параллельную многостороннюю обработку.
Рис. 5.2. Варианты компоновок сверлильно-фрезернорасточных станков с ЧПУ
Выпускают станки с вертикальным расположением стола, обеспечивающим надежное стружкоудаление (рис. 5.2, г).
У некоторых моделей станков шпиндельная бабка в процессе выполнения операции может изменять угловое положение от вертикального до горизонтального. В сочетании с поворотным столом это позволяет обработать все поверхности, кроме базовой. Из этих же соображений четырехкоординатные станки оснащают угловыми насадками, которые обеспечивают изменениенаправления оси вращения инструмента относительно оси вращения шпинделя. Отдельные станки имеют опрокидывающие столы со сквозными окнами, которые позволяют выполнить обработку со стороны базовой поверхности заготовки.
Сверлильно-фрезерно-расточные станки оснащают инструментальными магазинами, располагающими от 20 до 120 и более инструментами, которые автоматически могут заменяться в процессе выполнения операции.
В серийном производстве для сокращения основного времени обработки стремятся совместить выполнение переходов во времени. Для этого применяют комбинированные инструменты или многошпиндельные головки, у которых предусмотрена возможность изменения межцентровых расстояний вручную. Последние также располагаются в инструментальном магазине.
|
Системами ЧПУ оснащают также плоскошлифовальные и бесцентровые круглошлифовальные станки. При создании шлифовальных станков с ЧПУ возникают технические трудности следующего характера. Процесс шлифования характеризуется, с одной стороны, необходимостью получения высокой точности и качества поверхности при минимальном рассеянии размеров, а с другой — быстрой потерей размерной точности шлифовального круга вследствие его интенсивного изнашивания в процессе работы. Поэтому на шлифовальных станках необходимы механизмы автоматической компенсации изнашивания шлифовального круга. Кроме того, ЧПУ должно компенсировать деформации технологической системы, температурные погрешности, различия припусков на заготовках, погрешности станка при перемещении по координатам и т. д. Измерительные системы должны иметь высокую разрешающую способность, обеспечивающую жесткие допуски на точность позиционирования. Для шлифовальных станков используют устройства ЧПУ с управлением по трем-четырем координатам, но в станках, работающих несколькими кругами, возможно управление по пяти-шести и даже по восьми координатам.
Наибольшее распространение получили круглошлифовальные станки с ЧПУ, дающие максимальный эффект при обработке с одной установки многоступенчатых деталей типа шпинделей, валов электродвигателей, редукторов, турбин и т. д. Высокая производительность обеспечивается в основном в результате снижения вспомогательного времени на установку заготовки и съем готовой детали, на переустановку для обработки следующей шейки вала, на измерение и т. д. Время обработки многоступенчатых валов на круглошлифовальном станке с ЧПУ в 1,5—2 раза меньше, чем на станках с ручным управлением.
Бесцентровые круглошлифовальные станки эффективно применяют при изготовлении деталей малого и большого диаметров без ограничения длины либо тонкостенных деталей, а также деталей, имеющих сложные наружные профили (поршень, кулак и т. д.). В условиях массового производства эти станки характеризуются высокой производительностью и точностью обработки. В мелкосерийном и индивидуальном производстве их применение ограничено в связи с трудоемкостью переналадки.
Применение систем ЧПУ позволило управлять многокоординатным функционированием бесцентровых круглошлифовальных станков. В устройстве ЧПУ используют программные модули, которые рассчитывают траектории инструмента (круга, алмаза), его коррекцию и обеспечивают взаимодействие с оператором. Для обработки деталей с различными геометрическими формами (конус, шар и т. д.) имеется программное обеспечение, содержащее диспетчер режимов, интерполятор и модуль управления приводами. При обработке заготовок и правке круга число сочетаемых управляемых координат может доходить до 19, в том числе по две-три координаты отдельно для правки шлифовального и ведущего кругов. На станке возможна установка любого из четырех вариантов управления:
|
1) одна управляемая координата — поперечная подача шлифовального круга;
2) две управляемые координаты — поперечная подача шлифовального круга и правящего алмаза в целях их синхронизации;
3) три управляемые координаты — поперечная подача шлифовального круга, поперечная и продольная подачи алмаза при его правке;
4) пять управляемых координат — поперечная подача шлифовального круга, а также поперечные и продольные подачи алмазов при правке шлифовального и ведущего кругов.
Наличие многокоординатной системы ЧПУ обеспечивает большую универсальность таких станков, малые подачи кругов, что позволяет эффективно управлять процессами шлифования и правки.
Решающее влияние на технологические возможности станков с ЧПУ оказывают их конструкция и математическое обеспечение устройства ЧПУ. Первые устройства типа NC (Numerical Control) обладали достаточно широкими технологическими возможностями: линейно-круговой интерполяцией, коррекцией положения инструментов, выдачей необходимого числа технологических команд и др. Однако они имели существенные недостатки, в частности, не позволяли хранить и редактировать управляющие программы непосредственно на рабочем месте.
Устройства второго поколения типа SNC (Stary Numerical Control) — системы с расширенной памятью на входе для хранения и редакции управляющих программ — были результатом доработки систем типа NC. Основной недостаток устройств NC и SNC — возможность изменения и расширения их функциональных возможностей.
Устройства ЧПУ третьего поколения — системы типа CNC (Computerized Numerical Control) были построены на базе микро- ЭВМ. Они резко расширили функциональные возможности программного управления: обеспечивают хранение и редактирование программы непосредственно на рабочем месте, имеют развитые системы диагностики и управления качеством обрабатываемых поверхностей с использованием активного контроля, расширенные возможности индикации информации на дисплее, диалоговое общение с оператором, перепрограммирование первоначально заложенных функциональных возможностей устройства при его эксплуатации. Системы CNC позволяют организовать многостаночное обслуживание, эффективно автоматизировать процесс выполнения простейших операций при размерах партии заготовок менее 10 шт. К недостаткам таких систем можно отнести большие затраты времени на ввод и редактирование значительных по объему управляющих программ. Моделями данного ряда являются устройства «Размер-4», «Размер-5», Н55-1, Н55-2, а также и оперативные устройства «Электроника НЦ-31», «Электроника НЦ-80-ОГ», 2Р-22, 2Р-32, 2С-42.
Для устройств ЧПУ четвертого поколения характерно блочное мультипроцессорное исполнение. В качестве их элементной базы используют специальные большие интегральные схемы и микроЭВМ. Программирование технологических функций и диалоговых режимов осуществляется на языках высокого уровня. К моделям данного ряда можно отнести устройства «Электроника МС2101», ЗС100, ЗС200. Ввод программы в них осуществляется как непосредственно с клавиатуры, так и с электронной кассеты или кассеты на цифровых магнитных доменах.
Современные устройства ЧПУ («Маяк», Integral) создают на базе промышленных и персональных компьютеров. Использование PC-совместимой материнской платы и операционных систем Windows, Linux позволяет конструировать устройства ЧПУ на базе широко применяемых во всем мире компьютерных компонентов. В этих устройствах реализуются все современные достижения, свойственные персональным компьютерам: языки программирования высокого уровня, программно-математическое обеспечение, системы ввода, хранения и обмена информации, возможность структурного изменения, возможность выполнения функций самонастройки и адаптации и др. Жесткий диск большой мощности многократно расширяет память управляющих технологических программ. Внешняя связь с устройством ЧПУ обеспечивается с помощью простого последовательного интерфейса или посредством локальной сети. Устройства ЧПУ, основанные на открытой архитектуре, могут интегрировать программное обеспечение пользователя, учитывая специфику требований конкретного применения системы.
В современных устройствах ЧПУ используются решения, обеспечивающие компенсацию возмущающих воздействий процесса обработки, погрешностей кинематики станка и погрешностей, связанных с изменением окружающей среды (температуры, колебания питающего напряжения и т. д.). Адаптивная система управления перемещением по координатам (осям) устраняет резонансные явления, компенсирует ошибку регулирования в реальном масштабе времени.
Технологические возможности станков с ЧПУ обеспечивают менее жесткие ограничения по конструктивным формам деталей в сравнении с обработкой на станках других типов.
Для токарных станков с ЧПУ вполне технологичными являются сочетания цилиндрических, конических и криволинейных поверхностей. Здесь допустимы разные радиусы галтелей, ширина канавок и винтовые поверхности с переменным шагом. Для резьбовых поверхностей не требуются канавки для выхода резца.
Для обработки на фрезерных и сверлильно-фрезерно-расточных станках с контурной системой управления допустимы сочетания криволинейных, плоских и объемных поверхностей с поверхностями простой формы. Здесь возможна обработка канавок и резьбовых поверхностей в отверстиях корпусных деталей методами расфрезерования или планетарного растачивания.
При анализе технологичности деталей, обрабатываемых на станках с ЧПУ, необходимо учитывать требования надежного удаления стружки, максимального упрощения программирования, обеспечения благоприятных условий работы режущего инструмента, а также надежного закрепления заготовки, обеспечивающего обработку максимального числа ее поверхностей и одновременно высокую жесткость системы заготовка — приспособление. При автоматической загрузке заготовок дополнительно следует учитывать возможность их ориентирования и захвата загрузочным устройством.
Конструкция заготовки детали должна быть такой, чтобы для обработки требовалось минимальное количество инструментов. Этому способствует рациональное оформление канавок (рис. 5.3, о) и широкая унификация размеров основных и крепежных отверстий. Для уменьшения объема работ по подготовке управляющей программы следует радиусы r закруглений внутренних контуров выполнять одинаковыми и согласованными с диаметром фрезы: (рис. 5.3, б). Технологичной является симметричная форма детали, когда по одной программе заготовка может быть обработана с двух сторон (рис. 5.3, в).
Криволинейные поверхности целесообразно профилировать участками прямых линий и дуг окружностей, что облегчает
Рис. 5.3. Технологичные для изготовления на станках с ЧПУ конструкции деталей
подготовку программы, так как станки обычно имеют линейно-круговые интерполяторы. На рис. 5.4 показаны две конструкции плоской криволинейной поверхности. В первой (см. рис. 5.4, а) направление строк обхода контура возможно только вдоль оси X, во второй (см. рис. 5.4, б) — как вдоль оси X, так и вдоль оси Y. Учитывая, что объем расчетов по определению координат опорных точек значительно меньше при движении по оси Y, чем по оси X, второй вариант более технологичен.
Рис. 5.4. Цельная (а) и составная (б) конструкции деталей
Радиусы фрезерования в карманах (см. рис. 5.3, б), окнах, занижениях следует по возможности увеличивать, что повышает жесткость инструмента. Из этих же соображений конструкцию корпусной детали, имеющей соосные отверстия в двух стенках, следует проектировать так, чтобы при растачивании отношение длины к диаметру фрезы было не более 6.
При многопереходной обработке целесообразно вместо глухих отверстий и карманов предусматривать сквозные отверстия и окна, что способствует лучшему стружкоудалению. Конструкция должна способствовать исключению или максимальному уменьшению последующей после обработки на станках с ЧПУ станочной или ручной доработки. Для этого нецелесообразно предусматривать резьбовые отверстия менее М6. Точность цилиндрических наружных поверхностей должна быть не выше IT6, а внутренних — IT7; шероховатость — не ниже Ra = 0,8 мкм.
Особое внимание нужно уделять простановке размеров на чертеже детали. Координаты осей отверстий следует проставлять в декартовой, а не в полярной системе координат. В противном случае их приходится пересчитывать при подготовке управляющей программы. В общем случае размеры задают от принятых технологических баз.
Рис. 5.5. Варианты простановки осевых размеров на чертеже ступенчатого вала
Простановка осевых размеров, технологичная при обработке на универсальном токарном станке (рис. 5.5, а), недопустима при обработке на станке с ЧПУ. В последнем случае при выдерживании размеров и
(см. рис. 5.5, а) возникает погрешность базирования, равная допуску на размер L, который обычно превышает допуски на
и
. При обработке на станке с ЧПУ осевые размеры следует проставлять, как показано на рис. 5.5, б.
|
|
Опора деревянной одностоечной и способы укрепление угловых опор: Опоры ВЛ - конструкции, предназначенные для поддерживания проводов на необходимой высоте над землей, водой...
Археология об основании Рима: Новые раскопки проясняют и такой острый дискуссионный вопрос, как дата самого возникновения Рима...
Папиллярные узоры пальцев рук - маркер спортивных способностей: дерматоглифические признаки формируются на 3-5 месяце беременности, не изменяются в течение жизни...
Механическое удерживание земляных масс: Механическое удерживание земляных масс на склоне обеспечивают контрфорсными сооружениями различных конструкций...
© cyberpedia.su 2017-2024 - Не является автором материалов. Исключительное право сохранено за автором текста.
Если вы не хотите, чтобы данный материал был у нас на сайте, перейдите по ссылке: Нарушение авторских прав. Мы поможем в написании вашей работы!