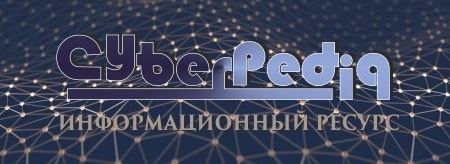
Общие условия выбора системы дренажа: Система дренажа выбирается в зависимости от характера защищаемого...
Адаптации растений и животных к жизни в горах: Большое значение для жизни организмов в горах имеют степень расчленения, крутизна и экспозиционные различия склонов...
Топ:
Определение места расположения распределительного центра: Фирма реализует продукцию на рынках сбыта и имеет постоянных поставщиков в разных регионах. Увеличение объема продаж...
Оснащения врачебно-сестринской бригады.
Характеристика АТП и сварочно-жестяницкого участка: Транспорт в настоящее время является одной из важнейших отраслей народного...
Интересное:
Искусственное повышение поверхности территории: Варианты искусственного повышения поверхности территории необходимо выбирать на основе анализа следующих характеристик защищаемой территории...
Инженерная защита территорий, зданий и сооружений от опасных геологических процессов: Изучение оползневых явлений, оценка устойчивости склонов и проектирование противооползневых сооружений — актуальнейшие задачи, стоящие перед отечественными...
Распространение рака на другие отдаленные от желудка органы: Характерных симптомов рака желудка не существует. Выраженные симптомы появляются, когда опухоль...
Дисциплины:
![]() |
![]() |
5.00
из
|
Заказать работу |
|
|
Под средствами механизации и автоматизации сборки понимают оборудование и технологическую оснастку, предназначенные для выполнения всех операций производственного процесса сборки. По типу выполняемых операций сборочное оборудование подразделяют на основное и вспомогательное. Основное оборудование выполняет процессы соединения деталей и их фиксацию в сборочной единице в соответствии с требованиями конструкции изделия, вспомогательное — обслуживает процессы сборки: удаление готовых изделий, перемещение объектов сборки между операциями, ориентацию деталей, контроль процессов сборки.
Для выполнения операции сборки двух деталей необходимо переместить детали в зону сборки, соориентировать их, расположить сопрягаемые поверхности одну относительно другой, соединить их и зафиксировать положение.
Перемещение деталей и сборочных единиц между операциями осуществляют конвейерами, поворотными столами, манипуляторами или роботами. При ручной сборке деталей в массовом и серийном производстве применяют напольные конвейеры. Тип конвейера выбирают по конструктивным и организационным признакам.
В зависимости от расположения рабочих мест конвейеры бывают распределительные и рабочие. У распределительного конвейера рабочее место расположено рядом с ним, и для осуществления сборки объект снимают с него вручную, манипулятором или сталкиванием на ответвление конвейера. Распределительные конвейеры применяют для сборки небольших изделий. В отличие от распределительных рабочие конвейеры используют непосредственно в качестве рабочих мест сборки. Для этого на несущем органе могут быть установлены приспособления.
|
Поворотные столы используют при ручной и автоматизированной сборке изделий массой до 50 кг. Как правило, поворотные столы совершают циклическое движение. Их конструкции унифицированы, и имеется нормализованный ряд габаритных размеров с соответствующим числом рабочих мест.
Передача деталей с помощью манипуляторов в процессах ручной сборки применяется при использовании распределительных конвейеров или поворотных столов. Манипуляторы имеют строго заданную траекторию перемещения, осуществляемого, как правило, от пневмопривода. Регулировка перемещения возможна только по каждой из координат, смена траектории перемещения не предусмотрена. Для съема изделия манипуляторы снабжают захватными органами различной конструкции. Манипуляторы, имеющие одно линейное или круговое движение, называют шиберными механизмами. Их относят к технологической оснастке и проектируют индивидуально. Выпускаемые типовые конструкции манипуляторов имеют грузоподъемность до 20 кг.
Роботы являются наиболее универсальным технологическим оборудованием для сборочных процессов. Они могут осуществлять как основные, так и вспомогательные операции. Область применения роботов — автоматизированная сборка для групповых ТП.
К типовым механизмам, осуществляющим ориентацию деталей и фиксацию их в зоне сборки, относят бункерные устройства, лотки, накопители, кассеты.
Наибольшим разнообразием характеризуется основное сборочное оборудование. Его конструкция и технические характеристики зависят от вида сборочного соединения, конструктивных особенностей соединяемых деталей, требований к качеству соединения и других факторов. Проектирование типовых механизированных и автоматических устройств, выполняющих соединение деталей, основано на принципах типизации ТП сборки и агрегатирования сборочного оборудования на основе применения унифицированных узлов. Наиболее полно эти принципы нашли применение в приборостроении, автомобильной и тракторной промышленности.
|
Для создания типовых сборочных механизмов проводят типизацию ТП. Например, для сборки резьбовых соединений применяют типовую схему базирования резьбовой детали в исполнительном механизме. Применяемые в конструкциях изделий приборостроения винты от М2 до М5 с различными типами головок базируют в винтоверте по резьбовой поверхности и торцу головки. Такая схема позволила создать серию сменных насадок на винтоверт, обладающих возможностью автоматической подачи винтов под отвертку (рис. 6.19).
В процессе ручной сборки винтоверт используют в компоновке с вибробункером 1 (рис. 6.20) или без него. Отвертка винтоверта вращается от электродвигателя 2 через гибкий или карданный вал 3. Винтоверт 4 либо перемещается по направляющей 5, либо подвешен свободно и перемещается рабочим. Возможна многошпиндельная компоновка механизма. Такая конструкция позволяет завинчивать различные винты от М2 до М5 двумя типами винтовертов со сменными насадками и электродвигателями различной мощности.
Рис. 6.19. Сменные насадки на механизированные (а, б) и автоматические (в) винтоверты
Рис. 6.20. Компоновка механизмов на рабочем месте сборщика
В условиях серийного производства эффективно применение типовых полуавтоматов. На рис. 6.21 показана схема полуавтомата для сборки резьбовых соединений, сконструированного из типовых исполнительных механизмов. Механизм завинчивания, состоящий из винтоверта 1, муфты контроля момента 2, карданной передачи 3, редуктора 4 и двигателя 5, расположен на колонне 8 и может перемещаться по ней.
Рис. 6.21. Схема полуавтомата для установки винтов
Рабочее движение винтоверта с муфтой вдоль оси сборки осуществляется с помощью пневмоцилиндра 6 через рычажную передачу. Положение механизма завинчивания на колонне относительно стола регулируют винтом 7. Винты ориентируются в вибробункере 10 и подаются в винтоверт по лотку 9. Загрузка изделия на полуавтомат может быть ручной или механизированной. Переналадку полуавтомата на другой размер винтов осуществляют путем замены лотков и винтоверта. Если размер винта меняется незначительно, например с М2 на М3, то заменяют только насадку винтоверта.
Дальнейшее развитие типовые сборочные механизмы получили при создании автоматического переналаживаемого сборочного оборудования для условий серийного производства. Сборочные автоматы для серийного производства должны иметь возможность быстрой переналадки при смене объекта сборки. Переналадку сборочных автоматов осуществляют тремя способами: заменой исполнительных механизмов, регулировкой исполнительных механизмов с помощью специальных звеньев конструкции или перепрограммированием оборудования с ЧПУ (в основном в роботизированном производстве). Во всех трех случаях, как правило, меняется технологическая оснастка. Наиболее быстро осуществляется переналадка на программируемом оборудовании. Однако роботизированная сборка имеет меньшую производительность по сравнению с традиционными автоматами и поэтому не всегда эффективна.
|
Эффективность использования переналаживаемых сборочных автоматов возрастает при правильном проектировании процессов сборки на них. Минимального времени переналадки и максимальной универсальности оборудования добиваются тщательным подбором объектов сборки по конфигурации и размерам. Для этого проводят анализ типов соединений и схем базирования деталей на сборочной позиции, группируют изделия по количеству и типу соединений.
Рассмотрим в качестве примера сборку четырех узлов, приведенных на рис. 6.22. Последовательность сборки каждого из них и типы соединений приведены в табл. 6.1.
Из таблицы следует, что групповые ТП сборки сборочных единиц II и III имеют одинаковое число переходов: установку базовой детали, установку присоединяемой детали и закрепление детали. Однако методы их закрепления требуют различных механизмов. Следовательно, групповой ТП может быть осуществлен на переналаживаемом автомате, имеющем четыре позиции: установка базовой детали (деталей), установка присоединяемой детали, закрепление деталей и снятие сборочной единицы. На автомате при смене сборочной единицы необходима переналадка: на поворотном столе — смена приспособлений, на позиции за крепления — смена механизмов и на всех позициях — смена захватных устройств на механизмах перемещения.
|
Рис. 6.22. Сборочные единицы (I — IV) для автоматической сборки на переналаживаемом оборудовании: 1 — базовая деталь; 2 — присоединяемая деталь; 3 — шайба
Групповой ТП сборки сборочных единиц I и IV, имеющих одинаковое число переходов, можно осуществить на переналаживаемом автомате, имеющем пять позиций: установка базовой детали, установка присоединяемой детали, установка шайбы, закрепление деталей и снятие собранного изделия.
Сравнивая структуры автоматов для сборки сборочных единиц II, III и I, IV, можно спроектировать групповой ТП сборки всех сборочных единиц на переналаживаемом пятипозиционном автомате, у которого третья позиция будет загружена на 50 %, что допустимо при серийном выпуске изделий.
Сборочные переналаживаемые автоматы компонуют на базе унифицированных поворотных столов с расположением механизмов вокруг них на штифтах или по направляющим для обеспечения требуемой точности их положения.
На поворотных столах устанавливают приспособления. Компоновка механизмов на сборочных позициях аналогична компоновке полуавтомата для установки винтов, приведенного на рис. 6.21.
При проектировании ТП роботизированной сборки необходимо провести аналогичный анализ. Технолог также должен решить задачу рациональной концентрации позиций сборки на одном рабочем месте. Переналадка роботизированного сборочного оборудования связана со сменой схватов роботов и приспособлений.
Типовые конструкции схватов и приспособлений для роботизированной сборки разрабатывают по тем же принципам, которые характерны для автоматов и полуавтоматов.
Таблица 6.1
|
|
Своеобразие русской архитектуры: Основной материал – дерево – быстрота постройки, но недолговечность и необходимость деления...
Семя – орган полового размножения и расселения растений: наружи у семян имеется плотный покров – кожура...
История развития хранилищ для нефти: Первые склады нефти появились в XVII веке. Они представляли собой землянные ямы-амбара глубиной 4…5 м...
Индивидуальные и групповые автопоилки: для животных. Схемы и конструкции...
© cyberpedia.su 2017-2024 - Не является автором материалов. Исключительное право сохранено за автором текста.
Если вы не хотите, чтобы данный материал был у нас на сайте, перейдите по ссылке: Нарушение авторских прав. Мы поможем в написании вашей работы!