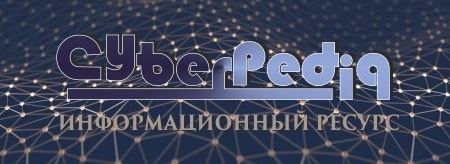
Семя – орган полового размножения и расселения растений: наружи у семян имеется плотный покров – кожура...
История развития пистолетов-пулеметов: Предпосылкой для возникновения пистолетов-пулеметов послужила давняя тенденция тяготения винтовок...
Топ:
Устройство и оснащение процедурного кабинета: Решающая роль в обеспечении правильного лечения пациентов отводится процедурной медсестре...
Оснащения врачебно-сестринской бригады.
Выпускная квалификационная работа: Основная часть ВКР, как правило, состоит из двух-трех глав, каждая из которых, в свою очередь...
Интересное:
Подходы к решению темы фильма: Существует три основных типа исторического фильма, имеющих между собой много общего...
Как мы говорим и как мы слушаем: общение можно сравнить с огромным зонтиком, под которым скрыто все...
Мероприятия для защиты от морозного пучения грунтов: Инженерная защита от морозного (криогенного) пучения грунтов необходима для легких малоэтажных зданий и других сооружений...
Дисциплины:
![]() |
![]() |
5.00
из
|
Заказать работу |
|
|
6.7.1 Необходимо перевести режим разливки с автоматического (AUTOMATIC MODE) в ручной режим («MANUAL»).
6.7.2 Когда будет достигнут заданный уровень старта соответствующего ручья (таблица 6.1), старший разливщик должен дать команду на открытие данного ручья.
6.7.3 Переместить стопор при помощи ручного пульта управления в положение от 15 до
18 мм (по показанию электронного индикатора положения стопора или по визуальному индикатору).
6.7.4 Спустя 3-5 секунд переместить в положение 10-14 мм. Спустя 3-5 секунд переместить стопор в положение от 8 до 10 мм и продолжать наполнение кристаллизатора.
6.7.5 В момент появления уровня стали от 10 до 20 % на цифровом индикаторе пульта разливщик прикрывает стопор полностью.
6.7.6 Нажать кнопку “Автоматический режим” и плавно начать открывать стопор с помощью ручного пульта управления стопором.
6.7.7 Когда уровень металла в кристаллизаторе достигнет 20% стопор переключиться в «Автоматический» режим управления.
6.7.8 При достижении уровня стали в кристаллизаторе 20 % система управления запустит привод тянущей клети и переключит систему управления уровнем металла в кристаллизаторе в автоматический режим. Параллельно с ТПМ производится запуск механизма качания кристаллизатора и системы роликового вторичного охлаждения.
6.7.9 В случае необходимости открытия ручья при массе металла в промежуточном ковше больше 25 т - производить запуск только в ручном режиме управления стопором. Время наполнения кристаллизатора при этом должно составлять не менее 15 с.
6.7.10 Когда уровень металла в кристаллизаторе достигнет 60 % (нижнего торца погружного стакана) добавить в кристаллизатор шлакообразующую смесь.
6.7.11 Назначение марки ШОС в зависимости от содержания углерода, разливаемой марки стали приведены в приложении А.
|
6.7.12 Присадку ШОС и ведение шлакового режима производится вручную.
6.7.12.1 Разливщики на ручьях устанавливают открытые расходные коробки с ШОС непосредственно у ручьев перед началом разливки.
6.7.12.2 Коробки должны быть маркированы (марка ШОС) для исключения смешивания и перепутывания разных ШОС.
6.7.12.3 Не допускается попадание влаги в коробки с ШОС.
6.7.12.4 ШОС подают в кристаллизаторы специальными совками.
6.7.12.5 Первую порцию ШОС подают при наполнении кристаллизатора после заглубления погружного стакана под уровень стали.
6.7.12.6 Далее ШОС подают периодически порциями, равномерно распределяя ее в кристаллизаторе кислородной трубкой.
6.7.12.7 Количество ШОС, присаживаемой за одну порцию, и частота присадки порций зависят от сечения заготовки и скорости литья и должны обеспечивать постоянный ровный слой ШОС в кристаллизатор темного цвета толщиной от 25 до 35 мм без искрения, проблесков расплавленного шлака и стали. Толщина расплавленного шлака 5-10 мм.
6.7.13 Контроль толщины слоя шлака осуществляется при помощи проволоки и трубки диаметром 6 мм (см. рисунок 6.3).
6.7.14 Проволока должна быть надежно зафиксирована в трубке, трубка опускается в кристаллизатор до контакта среза трубки с поверхностью ШОС. Спустя 15 секунд трубку с проволокой необходимо вынуть из кристаллизатора и с помощью линейки измерить расстояние от среза трубки до металла на проволоке.
Рисунок 6.3 – Схема измерения толщины слоя ШОС в кристаллизаторе
6.7.15 Периодически, через 10-20 мин, либо в случаях затягиваний, промывок стаканов, при колебаниях уровня стали разливщики проверяют наличие гарнисажа по периметру кристаллизатора.
6.7.16 При проверке гарнисажа слой ШОС перемешивают кислородной трубкой по периметру и в углах кристаллизатора, не допуская скопления смеси и шлака в одном месте и на одной грани.
6.7.17 Образующийся гарнисаж удаляют кислородной трубкой.
|
6.7.18 Запрещается перемешивать слой ШОС со сталью, погружать кислородную трубку в сталь и утапливать гарнисаж в мениск стали.
6.7.19 Сменные мастера МНЛЗ и старший разливщик контролируют присадку ШОС, состояние шлакового покрова в кристаллизаторах.
6.7.20 Разливку производить при крайнем нижнем положении ТПК (контроль по HMI), положения гидроцилиндров ТПК должны отличаться не более 5 мм (контроль визуальный). Погружные стаканы должны быть заглублены под уровень металла в кристаллизаторе на глубину не менее 100 мм (контроль визуальный).
6.7.21 В журнале МНЛЗ на каждой плавке отмечать режим подачи ШОС по каждому ручью и Ф.И.О. разливщика, контролирующего подачу ШОС.
6.7.22 После запуска всех ручьев проверить центровку погружных стаканов по центру кристаллизаторов. Допускаемое отклонение осей погружных стаканов от осей кристаллизаторов не более 5 мм.
6.7.23 При нестабильной разливке, затягивании ПС неметаллическими включениями, повышенных колебаниях уровня металла в кристаллизаторе, разрешается временно, до стабилизации процесса, снижать скорость литья, но не ниже минимальной.
6.7.24 Признаки начала затягивания стаканов – повышение позиции стопоров и увеличение амплитуды их движения при постоянной скорости литья, сопровождающиеся повышенными колебаниями уровня стали в кристаллизаторе.
6.7.25 При невозможности дальнейшего литья на ручье из-за затягивания стакана производят:
- цикл очистки;
- замену погружного стакана с очисткой канала стакан-дозатора кислородом;
- останавливают разливку на ручье.
6.7.26 Для отчистки стакан-дозатора от неметаллических включений методом «цикла очистки» необходимо нажать кнопку «Цикл отчистки» («CLEANING CYCLE»).
6.7.27 При этом стопор закрывается примерно на 0,5 с, а затем открывается так чтобы достичь заданный уровень стали в кристаллизаторе.
6.7.28 Погружной стакан заменяется в случае его износа или зарастания стакан-дозатора неметаллическими включениями.
6.7.28.1 При необходимости замены погружного стакана необходимо нажать кнопку «Закрыть стопор».
6.7.28.2 При этом уровень стали опуститься ниже значений 20% и двигатели ТМП автоматически остановятся.
6.7.28.3 Затем нажать кнопку «Ручной режим» («MANUAL»).
6.7.28.4 Если погружной стакан заменяется по причине зарастания стакан-дозатора неметаллическими включениями, то при помощи кислородного держака с установленной трубкой диаметром 6 мм аккуратно по внутреннему периметру прочистить канал стакан-дозатора от неметаллических включений кислородом.
|
6.7.28.5 Подачу кислорода в канал стакан-дозатора производить порциями от 3 до 4 с, при этом клавишу подачи кислорода полностью не выжимать.
6.7.28.6 Перед промывкой стакан-дозатора накрыть кристаллизатор асбестовым листом.
6.7.28.7 Операцию очистки стакан-дозатора должен выполнять старший разливщик стали, при этом соблюдая осторожность, чтобы не повредить тело стакан-дозатора и кончик стопора.
6.7.28.8 Признаком горения огнеупорного материала является выделяющийся коричневый дым из стакан-дозатора промежуточного ковша.
6.7.28.9 Затем установить новый погружной стакан с уплотнительной вставкой и произвести его центровку относительно оси кристаллизатора.
6.7.28.10 Затем нажать кнопку «Автоматический режим» («AUTOMATIC»), при этом управление стопора переключиться в автоматическое управление.
6.7.28.11 Потом при помощи ручного пульта управления стопором открыть поворотом селектора стопор от 10 до 15 мм на 2-3 с, при это следить за поступлением стали в кристаллизатор.
6.7.28.12 Признаками поступления стали являются вылетающие искры металла из кристаллизатора.
6.7.28.13 Затем обратным поворотом селектора закрыть стопор, выждать 7-10 секунд и снова начать наполнение кристаллизатора.
6.7.28.14 После набора металла в кристаллизаторе до уровня 20% стопор перейдет в режим автоматического режима работы для набора заданного уровня стали, запустятся двигатели ТПМ, механизм качания, охлаждение зоны вторичного охлаждения и ЭМП кристаллизатора.
6.7.29 Общее время остановки ручья допускается не более 2 мин.
6.8 Разливщики в процессе разливки должны контролировать:
- уровень металла в промежуточном ковше;
- покрытие «зеркала» металла в промежуточном ковше утепляющей смесью;
- температуру металла в промежуточном ковше;
- уровень металла в кристаллизаторе (по индикатору уровня металла на локальном пульте);
- отсутствие искрения металла в кристаллизаторе при разливке закрытой струей;
|
- скорость разливки в зависимости от температуры металла в промежуточном ковше;
- при разливке открытой струей состояние мениска металла в кристаллизаторе, наличие и характер смазки стенок гильзы кристаллизатора (горение масла), организованность струи из стакана- дозатора в кристаллизатор;
- наличие шлака в кристаллизаторе;
- работу механизма качания;
- работу стопорного механизма;
- положение стопора.
6.9 Операторы МНЛЗ в процессе разливки должны контролировать:
- расход, давление и перепад температуры воды, подаваемой на охлаждение кристаллизатора;
- скорость разливки в зависимости от температуры металла в промежуточном ковше;
- колебания уровня металла в кристаллизаторе;
- режим качания кристаллизатора;
- режим электромагнитного перемешивания металла в кристаллизаторе;
- режим работы стопорных механизмов;
- расход и давление воды, подаваемой на вторичное охлаждение;
- режим работы тянуще-правильного агрегата (давление и усилие прижатия роликов);
- расцепление и парковку затравок;
- работу основного гидравлического оборудования;
- режим работы контура охлаждения оборудования;
- режим работы машины газовой резки;
- качество выпускаемой продукции;
- режим работы транспортного и разгрузочного рольгангов;
- режим работы рольгангов горячего всада;
- режим работы маркировочной машины;
- режим работы шлеппера, холодильника с шагающими балками;
- дефекты непрерывно литой заготовки (приложение Л).
6.10 О нарушениях работы оборудования сменный персонал должен сообщить сменному мастеру МНЛЗ и старшему оператору.
Отделение затравки
6.11.1 Режимы работы ТПМ при запуске и разливке ручья приведены в таблице 6.3
Таблица 6.3 Режим работы ТПМ
Режим работы | Кв.150 мм | КВ.180 мм |
Давление ролика вытягивания затравки (бар) | 50 | 50 |
Давление тянущей клети при вытягивании горячей заготовки (бар) | 28 | 33 |
Давление правильной клети (бар) | 17 | 21 |
Давление прижимного ролика при отделении затравки (бар) | 180 | 180 |
6.11.2 Отсоединение затравки от заготовки происходит под воздействием прижимного ролика при поступлении заготовки в отделяющий модуль ТПМ. Ролик деформирует заготовку, происходит смещение заготовки относительно головки затравки и обламывание штифта (рисунок 6.4).
Рисунок 6.4 - Отсоединение заготовки от затравки
6.11.3 Если отделения затравки не произошло, то необходимо отрезать головную часть заготовки с помощью ручного газокислородного резака и переместить затравку в позицию парковки.
6.11.4 После ТПМ через промежуточный рольганг заготовки поступают на МГР.
6.11.5 Передний конец заготовки отрезается на МГР в автоматическом режиме, при этом длина «головной» обрези для сечения 150х150 мм и 180х180 мм не менее 500 мм на ручей.
|
6.11.6 Мерная длина заготовок и общая длина отлитого слитка на ручьях от начала разливки измеряется автоматически с помощью кодового датчика ТПА1 и ТПА3.
6.11.7 Порезка заготовок на машинах газовой резки (МГР) производится в автоматическом режиме в соответствии с заданием ПО.
6.11.8 Допускается порезка заготовок ручным аварийным резаком при условии, если МГР вышла из строя в процессе разливки.
6.11.9 Длина отрезаемых заготовок рассчитывается Уровнем 2 по заранее заданной заказной длине с учетом коэффициента термической усадки непрерывнолитой заготовки.
6.11.10 При недорезах, отказах в работе МГР порезку заготовок на мерные длины ведут вручную газокислородными резаками с переходной площадки.
6.11.11 Все порезанные заготовки на мерные длины на разгрузочном рольганге 1 ускоряются и перемещаются на разгрузочный рольганг 2 для взвешивания.
6.11.12 После взвешивания заготовки перемещаются на разгрузочный рольганг 3 для подъема гидравлическим передаточным устройством на опорную раму верхнего уровня. Отсюда заготовки перемещаются поперечным шлеппером к толкателю заготовок в зону напротив передаточного рольганга 1.
6.11.13 Заготовки взвешиваются отдельно на каждом ручье.
6.11.14 На разгрузочном рольганге предусмотрен убирающийся упор, позволяющий осуществлять параллельное складирование заготовок (длиной 6 м) перед их подъемом на 2-й уровень.
6.11.15 В случае «горячего посада» передаточные рольганги (TRT 1 и 2) транспортируют пакет заготовок до конечного упора, собранный поперечным шлеппером и перемещенный толкателем заготовок, к конвейеру-столу для укладки заготовок.
6.11.16 После обнаружения датчиками конвейерного-стола пакета заготовок, конвейер принимает весь пакет с передаточного рольганга и поднимает заготовки одна за другой на следующий уровень, где дополнительный рольганг перемещает горячие заготовки к прокатному стану. Заготовки транспортируются непосредственно на загрузочную решетку нагревательной печи стана 9511.
6.11.17 Для передачи заготовок на склад, собранный поперечным шлеппером пакет заготовок снимается подвижными рейками холодильника с передаточного рольганга, при этом поперечное перемещение заготовок к холодильнику поперек рольганга осуществляется при помощи толкателя. Толкатель работает в режимах одиночного или параллельного складирования.
6.11.18 Подача следующего пакета заготовок возможна только, если передаточный рольганг не загружен.
6.11.19 Для автоматизации процесса МНЛЗ оборудована устройствами обнаружения заготовок (датчиками) для запуска следующего узла машины:
- устройство обнаружения №1 расположено напротив убирающегося упора разгрузочного рольганга 2 – для запуска процесса взвешивания заготовки;
- устройство обнаружения №2 расположено между убирающимися упорами 1 и 2 в начале разгрузочного рольганга 3 – для работы параллельного складирования заготовок (запуск передаточного устройства) подъем 2 заготовок с каждого ручья;
- устройство обнаружения №3 расположено перед конечным упором разгрузочного рольганга 3 – в режиме параллельного складирования для задействования убирающегося упора 2 следующая заготовка остановится здесь;
- устройства обнаружения №4 и №5 расположены на передаточном рольганге 1 (между конечным упором 2 и убирающимся упором 3) – для обнаружения пакета заготовок на передаточном рольганге 1. Далее заготовки либо толкателем передаются по одной на кантующий холодильник или пакет заготовок по передаточным рольгангам передается на прокатный стан 9511;
- устройство обнаружения №6 расположено перед конечным упором 3 передаточного рольганга 2 – для подъема конвейером пакета заготовок на уровень рольганга, ведущего к прокатному стану.
6.11.20 Кран непрерывно снимает пакеты заготовок с накопителя при их расположении в зоне «Захвата». Если выгрузка пакетов невозможна, то оставшаяся часть заготовок данной плавки будет выгружена поперечным шлеппером на передаточный рольганг. В противном случае процесс разливки будет прерван.
Маркировка заготовок
6.12.1 Маркировка заготовок осуществляется на двух маркировочных машинах заготовок (ММЗ) оборудованных маркировочным молотом и штамповочной головкой револьверного типа.
6.12.2 ММЗ расположена по обеим сторонам кантующего холодильника.
6.12.3 Высота/ширина/шаг символа: 8/5/9,5 мм.
6.12.4 Возможные символы: (0 – 9) и (A – F) – всего возможно 14 цифр, штампы можно сменить вручную на любые другие символы.
6.12.5 Глубина нанесения символов ~ 1,5 мм (зависит от марки стали и температуры заготовки).
6.12.6 Маркировка выполняется в один ряд и состоит из 12 знаков: первые 8 знаков – номер плавки (1 цифра – номер конвертера, 2 цифры - год и 5 цифр – собственно номер плавки по порядку выплавки), 9-я – номер МНЛЗ, 10-я – номер ручья, с 11 и по 12-ю – порядковый номер НЛЗ. В конце добавляется 2 дополнительных символа для улучшения распознавания OPR.
6.12.7 Маркировка должна быть четко различимой.
6.12.8 При сбое работы ММЗ номера ручьев и заготовок оператор МГР наносит вручную при помощи несмывающейся резины, мелков и т.п. на верхнюю грань и торец заготовки.
6.12.9 В случае нечеткой маркировки после разливки проверяют исправность ММЗ, при необходимости заменяют клейма, проводят ремонт.
6.12.10 Проведение операций по перемещению заготовки и описание продукции, складированной на складе осуществляется посредством системы управления складским двором (СУСД), которая управляется Уровнем 2 МНЛЗ.
6.12.11 Во время разливки СУСД получает данные о разлитой продукции от системы Уровня 2 МНЛЗ.
6.12.12 По мере выхода продукции по ручьям МНЛЗ на холодильник информация в СУСД постоянно обновляется о местонахождении продукции. Информация, хранящаяся в СУСД:
- маркировочный код;
- информация о физическом местонахождении продукции, которая хранится на складском дворе;
- марка стали;
- номер плавки;
- длина продукции;
- идентификационный номер сечения продукции;
- качество.
6.12.13 СУСД постоянно обменивается данными с Уровнем 2 прокатного стана с целью определения местонахождения продукции, отвечающей соответствующим требованиям (тип профиля, марка стали, длина), определенной в программе прокатки.
6.12.14 Для равномерного охлаждения заготовки по мере прохождения по холодильнику проворачиваются вокруг своей оси за счет конструктивных особенностей реек холодильника.
6.12.15 В конце холодильника, заготовки выталкиваются на накопитель заготовок во время поступательного движения подвижной рейки.
6.12.16 В автоматическом режиме кантующий холодильник начинает работу если на его входе обнаружена заготовка и будет работать до тех пора пока последняя заготовка не окажется на накопителе заготовок.
6.12.17 Схема загрузки заготовок на холодильнике сечением 150 мм – на каждый зубец, сечением 180 мм – каждый 2-й зубец.
6.12.18 После шагающего холодильника, на накопителе заготовок при помощи гидравлического толкателя формируются пакеты заготовок (8 заготовок сечением 150 мм или 6 сечением 180 мм), размещается на накопителе не более 3-х пакетов.
6.12.19 Последний пакет по ходу движения с накопителя удаляется краном при помощи электромагнитов в штабеля.
6.12.20 Кран непрерывно снимает пакеты заготовок с накопителя.
|
|
Поперечные профили набережных и береговой полосы: На городских территориях берегоукрепление проектируют с учетом технических и экономических требований, но особое значение придают эстетическим...
Механическое удерживание земляных масс: Механическое удерживание земляных масс на склоне обеспечивают контрфорсными сооружениями различных конструкций...
История создания датчика движения: Первый прибор для обнаружения движения был изобретен немецким физиком Генрихом Герцем...
Типы сооружений для обработки осадков: Септиками называются сооружения, в которых одновременно происходят осветление сточной жидкости...
© cyberpedia.su 2017-2024 - Не является автором материалов. Исключительное право сохранено за автором текста.
Если вы не хотите, чтобы данный материал был у нас на сайте, перейдите по ссылке: Нарушение авторских прав. Мы поможем в написании вашей работы!