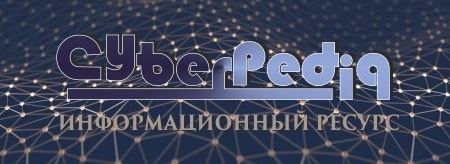
Наброски и зарисовки растений, плодов, цветов: Освоить конструктивное построение структуры дерева через зарисовки отдельных деревьев, группы деревьев...
Папиллярные узоры пальцев рук - маркер спортивных способностей: дерматоглифические признаки формируются на 3-5 месяце беременности, не изменяются в течение жизни...
Топ:
Оценка эффективности инструментов коммуникационной политики: Внешние коммуникации - обмен информацией между организацией и её внешней средой...
Особенности труда и отдыха в условиях низких температур: К работам при низких температурах на открытом воздухе и в не отапливаемых помещениях допускаются лица не моложе 18 лет, прошедшие...
Генеалогическое древо Султанов Османской империи: Османские правители, вначале, будучи еще бейлербеями Анатолии, женились на дочерях византийских императоров...
Интересное:
Как мы говорим и как мы слушаем: общение можно сравнить с огромным зонтиком, под которым скрыто все...
Национальное богатство страны и его составляющие: для оценки элементов национального богатства используются...
Принципы управления денежными потоками: одним из методов контроля за состоянием денежной наличности является...
Дисциплины:
![]() |
![]() |
5.00
из
|
Заказать работу |
Для энергомашиностроения и судостроения с учетом массогабаритных параметров заготовок и технических требований к металлопродукции в производстве проката все большее внимание инженеры и технологи уделяют операциям термомеханической обработки (ТМО), которая среди методов обработки металлов давлением признается как перспективная технология термопластической обработки сталей и сплавов разных систем легирования.
С учетом температурного фактора различают горячую, холодную и тёплую прокатку.
Основная часть проката (заготовка, сортовой и листовой металл, трубы, шары и т.д.) производится горячей прокаткой при начальных температурах: для стали 1000—1300°С, для титана и его сплавов 950—1100°С, для меди 750—850 °С, для латуни 600—800 °С, для алюминия и его сплавов 350—400 °С.
Холодная прокатка применяется главным образом для производства листов и ленты толщиной менее 1,5—6 мм, прецизионных сортовых профилей и труб. Кроме того, холодной прокатке подвергают горячекатаный металл для получения более гладкой поверхности и лучших механических свойств.
Теплая прокатка, в отличие от холодной, происходит при несколько повышенной температуре с целью снижения упрочнения (наклёпа) металла при его деформации (характеризуется протеканием возврата и отсутствием рекристаллизации).
По распространенному определению [3] технология ТМО рассматривается в форме «совокупности операций деформации, нагрева и охлаждения в различной последовательности, в результате которых формирование окончательной структуры металлического сплава, а, следовательно, и его свойств, происходит в условиях повышенной плотности и соответствующего распределения несовершенств строения, созданных пластической деформацией».
В развитие этого определения к настоящему времени при производстве листового проката применяется несколько вариантов технологий. В зависимости от последовательности применения операций нагрева и деформации, а также их абсолютных значений, определяют следующие виды процессов:
- Высокотемпературная термомеханическая обработка (ВТМО) сплавов с полиморфными превращениями (сталей) представляет собой деформацию стабильного аустенита (ГЦК) в температурной области выше порога рекристаллизации и после последнего прохода с немедленной закалкой на мартенсит (ОЦК). В итоге формируется структура с унаследованным строением деформированного аустенита (рис.9), которая в дальнейшем подвергается низкотемпературному отпуску (в мартенсите сталей) или старению (в аустенитных сплавах).
![]() | | |
Рис.9 Схема ВТМО сталей с полиморфными превращениями (слева) и аустенитных сплавов без полиморфных превращений (справа). | ||
| ![]() | |
Рис.10 Схема НТМО сталей с полиморфными превращениями (слева) и стареющих сплавов без полиморфных превращений (справа). | ||
- Низкотемпературная термомеханическая обработка (НТМО) заключается в деформировании аустенита (рис.10) при температурах, меньших температуры рекристаллизации, с последующей закалкой. Производственная проблема с применением НТМО заключается в том, что при температурах, когда нет рекристаллизации, накопление дефектов кристаллической решетки происходит интенсивнее, чем в случае ВТМО, поэтому для деформации аустенита необходимо более мощное цеховое оборудование.
В обоих случаях после закалки следует низкотемпера-турный отпуск (100 — 300°С).
- Контролируемая (нормализационная) прокатка - технологический процесс, используемый для замены нормализации, при котором заключительная стадия процесса проводится в области температур нормализации (чуть выше критической точки А3, для большинства низколегированных сталей Т»820-870°С). При этом по сравнению с нормализованным металлом повышаются прочностные свойства и хладостойкость [4]. Цель процесса - максимально измельчить зерно за счет обжатий и последующих процессов рекристаллизации при пониженных температурах.
Технология ТМО широко применяется как для сталей, так и для цветных сплавов. Метод позволяет получить достаточно высокую прочность (σв = 2200—3000МПа) при хорошей пластичности и вязкости (δ = 6—8%, ψ = 50—60%). Для сравнения: после обычной закалки и низкого отпуска σв = 2000—2200 МПа, δ = 3—4%.
Помимо названных схем ТМО, ставших классическими, используют процессы, обусловленные распадом деформированного аустенита в перлитной области (ВТМизо) или в бейнитной (НТМизо) области, во время перлитного превращения (изоформинг), с деформацией мартенсита (ДМО), с предварительной холодной деформацией перед термообработкой (ПТМО) и другие:
ВТМПО — высокотемпературная термомеханическая поверхностная обработка;
ВНТМО — высоко-низкотемпературная термомеханическая обработка;
НВТМО — низко-высокотемпературная термомеханическая обработка;
МТО — деформация немартенситных структур на площадке текучести при разных температурах со старением.
Термомеханическая обработка низколегированной стали в комплексе с микролегированием обеспечивает формирование микроструктуры с мелким зерном и дисперсными образованиями феррито-бейнито-мартенситных составляющих. Это позволяет получить высокий уровень вязкости при низких температурах испытания, а также обеспечить заданный уровень прочности при снижении углерода и минимизации легирования. Эффективность конкретного способа термомеханического упрочнения металла оценивается по комплексу механических свойств по критериям механики разрушения с определением энергоемкости процесса развития трещины и др. Для низколегированных сталей разработка нового режима ТМО или оптимизация действующего цикла предусматривает выбор:
- температурного интервала рекристаллизации и степени деформации аустенита,
- оптимальной температуры конца прокатки с целью предотвращения образования доэвтектоидного феррита и его последующей деформации,
- оптимальной скорости охлаждения после прокатки, обеспечивающей реализацию фазового g®a превращения в заданном интервале.
При использовании ускоренного охлаждения улучшение комплекса свойств микролегированной стали обусловлено измельчением зерен и образованием дисперсных продуктов промежуточного превращения аустенита.
К настоящему времени широко освоены различные схемы ВТМО и НТМО, в первую очередь при изготовлении таких изделий, как лист и сортовой прокат (круг, квадрат, полоса).
В разработке новых высокопрочных материалов технология термомеханической обработки рассматривается как основная, прецизионная и энергосберегающая. Достигнутый уровень знаний позволяет говорить о том, что, используя различные приемы ТМО, имеется реальная возможность создавать экономно легированные хладостойкие стали и сплавы с фрагментированной и наноразмерной структурой, которая в листовом прокате толщиной до 70 мм обеспечивает высокий уровень в комплексе эксплуатационных свойств. Можно с уверенностью говорить о том, что термопластическая обработка в технологии ТМО для металлических полуфабрикатов может рассматриваться как критическая, активно развивающаяся и востребованная.
Архитектура электронного правительства: Единая архитектура – это методологический подход при создании системы управления государства, который строится...
Индивидуальные и групповые автопоилки: для животных. Схемы и конструкции...
Археология об основании Рима: Новые раскопки проясняют и такой острый дискуссионный вопрос, как дата самого возникновения Рима...
Организация стока поверхностных вод: Наибольшее количество влаги на земном шаре испаряется с поверхности морей и океанов (88‰)...
© cyberpedia.su 2017-2024 - Не является автором материалов. Исключительное право сохранено за автором текста.
Если вы не хотите, чтобы данный материал был у нас на сайте, перейдите по ссылке: Нарушение авторских прав. Мы поможем в написании вашей работы!