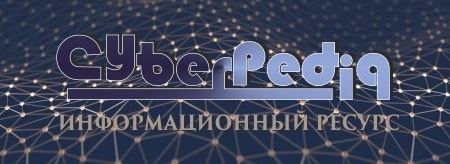
Своеобразие русской архитектуры: Основной материал – дерево – быстрота постройки, но недолговечность и необходимость деления...
История создания датчика движения: Первый прибор для обнаружения движения был изобретен немецким физиком Генрихом Герцем...
Топ:
Техника безопасности при работе на пароконвектомате: К обслуживанию пароконвектомата допускаются лица, прошедшие технический минимум по эксплуатации оборудования...
Процедура выполнения команд. Рабочий цикл процессора: Функционирование процессора в основном состоит из повторяющихся рабочих циклов, каждый из которых соответствует...
Особенности труда и отдыха в условиях низких температур: К работам при низких температурах на открытом воздухе и в не отапливаемых помещениях допускаются лица не моложе 18 лет, прошедшие...
Интересное:
Финансовый рынок и его значение в управлении денежными потоками на современном этапе: любому предприятию для расширения производства и увеличения прибыли нужны...
Мероприятия для защиты от морозного пучения грунтов: Инженерная защита от морозного (криогенного) пучения грунтов необходима для легких малоэтажных зданий и других сооружений...
Искусственное повышение поверхности территории: Варианты искусственного повышения поверхности территории необходимо выбирать на основе анализа следующих характеристик защищаемой территории...
Дисциплины:
![]() |
![]() |
5.00
из
|
Заказать работу |
|
|
Типового химического состава
Из распространенных коррозионностойких аустенитных сталей, которые применяются в изделиях энергетического машиностроения, для модельных испытаний была выбрана сталь марки 08Х18Н10Т, химический состав которой соответствовал (ГОСТ 5632). Для экспериментов с вариацией термопластического воздействия были изготовлены образцы из полуфабрикатов двух видов: катаного прутка Ø30 мм и крупногабаритной поковки.
Предварительная оценка металлургического качества стали показала, что в испытуемых прутках и поковке металл характеризуется одинаковым содержанием недеформируемых силикатов, количество которых оценено 2 баллом по шкалам ГОСТ 1778 (рис. 28), и сложных карбидов типа Ме23С6 - (Fe,Cr)23C6 и карбида титана TiC.
![]() | ![]() |
Рис.28 Неметаллические включения (карбонитриды и недеформируемые силикаты) в прутке и поковке стали 08Х18Н10Т. |
До имитации операций ТМО в недеформированном состоянии частицы Ме23С6в форме крупных сфероидов располагались внутри и по границам зерен, формируя микроликвационные строчки. Частицы TiC округлого вида и меньших размеров залегали внутри зерен на дислокациях и субграницах. Их объемная доля была ниже, чем у выделений Ме23С6.
![]() | ![]() |
Рис.29 Структура зерен в прутке (слева) и в поковке (справа) из стали 08Х18Н10Т. |
В образцах, изготовленных из прутков и поковки, размер зерен существенно различался. Например (рис. 29), в прутках величина зерна характеризовалась 9 баллом по шкалам ГОСТ 5639, что типично для однородного мелкозернистого и высокопрочного состояния металла. В поковке в пределах поля зрения микроскопа величина зерен менялась от 50 до 500 мкм, свидетельствуя о неоднородном структурно-механическом состоянии металла уже до имитационного моделирования.
|
Поэтому результаты экспериментов с горячей деформацией образцов разнозернистых сталей представляли не только научный, но и практический интерес.
Механические испытания – основная
Информационная база совершенствования
Термопластической обработки
В науке о материалах давно утвердилось осознание положения, что внутреннее строение твердого тела определяет его многие свойства, в том числе и механические. Поэтому разработка любого технологического процесса, связанного с изменением размеров и формы исходного материала, будет успешной, если известны или установлены структурно-механические параметры материала, а также природа и механизмы структурных изменений. Надежную и адекватную информацию о свойствах конструкционных сталей и сплавов различных систем легирования можно получить путем целевых механических испытаний с вариацией условий воздействия с последующим изучением произошедших структурных превращений.
Введение в действие Федерального закона о техническом регулировании утвердило повышение роли механических испытаний в поисковых, прикладных и других работах, касающихся разработки и применения материалов. Результаты исполнения законодательных актов уже видны в технических регламентах, стандартах, руководствах и других нормативных документах.
С целью получения информации о наилучших режимах горячей пластической обработки сталей и сплавов проведено большое количество исследований с определением структурно-механического состояния при разных температурно-скоростных условиях нагружения. Установлено, что при прокатке, ковке, производстве труб поперечно-винтовой прокаткой или прошивкой и т.д. горячая деформация оказывает существенное влияние на характер напряженно-деформированного состояния и структурные изменения в металле, и, как следствие, на сопротивление деформации. В общем случае при различных процессах горячей пластической деформации структурно-механическое состояние материала является очень сложным, и лабораторные эксперименты лишь упрощенно отражают реальную картину происходящего в реальном производстве. Однако можно и удается найти приемлемую корреляцию между промышленными условиями и лабораторными опытами, если регистрация параметров напряженно-деформиро-ванного состояния и модель поведения материала выбраны обоснованно. Поэтому для объективной оценки структурно-механического состояния сталей и сплавов в условиях горячей пластической деформации основное внимание уделено получению и обработке данных механических испытаний как полной и достоверной информации отклика материала на оказываемое воздействие.
|
Известно [8], что в металлоконструкциях напряженно-деформированное состояние материала контролируется природой прикладываемого напряжения и геометрией зоны деформации. Применительно к технологии термомеханической обработки распространенными вариантами напряженных состояний являются: одноосное сжатие, двухосное сжатие и трехосное сжатие (рис. 30).
Первый случай соответствует свободной ковке и прокатке узких заготовок в гладких валках, когда сжатие заготовок осуществляется одновременно со смазкой торцовых поверхностей.
![]() | ![]() | ![]() |
Линейное одноосное сжатие, S3< 0 | Плоское одноименное двухосное сжатие, S2< 0; S3< 0 | Объемное трехосное сжатие, S1< 0; S2< 0; S3< 0 |
Рис. 30 Типы напряженных состояний и диагональные компоненты тензора напряжений Ŝ при сжатии заготовок в технологиях ТМО. |
Второй вариант встречается при прокатке в ручьевых валках или ковке в штампах, закрытых с двух сторон.
Трехосное сжатие реализуется при прессовании под гидростатическим давлением и ковке в закрытых штампах. В общем случае действие механических сил характеризуется объемным трехосным напряженным состоянием в форме тензора напряжений второго ранга Ŝ, в котором из девяти компонент три независимых определяют касательные напряжения и способность к пластической деформации, и три также независимых компоненты нормальных напряжений выражают условия сплошности (неразрывности) материала. Подобно тензору напряжений, тензор деформаций ê в общем случае также характеризуется шестью компонентами – тремя удлинениями и тремя сдвигами. В разных видах обработки компоненты напряжений и деформаций различны, но в большинстве случаев поддаются расчету и позволяют совершенствовать оснастку, инструмент и технологический цикл металлообработки.
|
В зависимости от способа нагружения материала могут изменяться направление, величина и распределение усилий, максимальных нормальных и касательных напряжений, а также структура, сопротивление и степень локализации деформации.
Недостатком горячей деформации растяжением является сосредоточенное (локализованное) микропластическое течение, возникающее даже при небольших относительных деформациях.
В отличие от растяжения при сжатии деформация в большей степени однородна, и возможны очень большие деформации.
Испытание на сжатие не входит в число стандартных, обязательных для характеристики материала, поскольку оно мало добавляет к сведениям относительно вязких материалов, получаемых при испытаниях на растяжение. Учитывая особенности нагружения при «теплых» или «горячих» температурах, для оценки структурно-механического состояния металлов и сплавов в технологиях ТМО эксперименты производят в условиях сжатия.
Объективную, хотя и усредненную по объему образца, информацию о структурно-механическом состоянии материала и происходящих в нем изменениях содержат диаграммы нагружения (рис.31), построенные в координатах «истинные» напряжения (S) – логарифмическая деформация (e). В общем случае кривые деформирования состоят из чередующихся линейных, параболических и переходных стадий. Вид кривой пластического течения и величины, характеризующие отдельные ее стадии, от размера образца существенно не зависят.
С целью получения корректных данных о механических свойствах испытываемого материала, а также систематизации и обобщения результатов экспериментов на основе измерений размеров (длины и сечения) образцов в процессе деформирования, диаграммы нагружения следует строить в «истинных» значениях напряжений S и логарифмических деформаций e [8]. Для этого назначается непрерывная или дискретная через малые интервалы времени запись значений S (t) и e (t) с последующим построением зависимости S (e), где S - истинное напряжение, e — логарифмическая деформация, t – время.
|
![]() |
Рис.31 Пример диаграмм деформации технического алюминия по данным [7], полученным при растяжении (1) и сжатии (2). Экспериментальные точки легли на одну кривую S (e), которая описывается степенной функцией «истинные» напряжения (S) – логарифмическая деформация (e). |
В исследовании реакции испытуемого материала на оказываемое воздействие такой способ регистрации данных позволяет обнаружить изменения в кинетике структурно-механического состояния образца по силовым и деформационным параметрам.
Современные испытательные машины, оснащенные необходимыми датчиками и программными средствами, позволяют из зависимостей «нагрузка – перемещение» в каждый момент времени вычислить «истинные» координаты по стандартным уравнениям:
S = P / A0 (1 – ε) e = - ln(h0 / h),
где P – нагрузка, A0 – исходная площадь поперечного сечения образца и h0 – его исходная высота, h– «мгновенная» высота образца в режиме реального времени и ε – относительная текущая деформация образца, определяемая как ε = [(h0 – h)/h0]. При малых деформациях различие между истинными и условными (относительными техническими) характеристиками мало и e ~ε. Но при больших деформациях необходимо введение поправки, например:
при ε = 25% e = ln 1,25 = 22%;
при ε = 50% e = ln 1,5 = 40,5%;
при ε = 100% e = ln 2 = 69%.
Главной отличительной особенностью способа определения истинного напряжения и истинной деформации является признание взаимозависимости между размерами (длиной и диаметром) образца в процессе пластического деформирования при условии сохранения объема тела. Вследствие этого кривые напряжение – деформация, построенные по данным испытаний в относительных и истинных координатах, отличаются друг от друга (рис. 32). Например, кривая, построенная для относительных значенийε, достигает максимума при наибольшей нагрузке, а затем понижается до момента разрушения образца. В истинных координатах S (e) кривая, построенная по тем же экспериментальны данным, монотонно возрастает до момента разрушения. Отмеченное различие связано с возникновением локализованного пластического течения (в шейке образца) и способом определения относительного напряжения σ при условии неизменности объема тела. Для условий горячей пластической деформации установлены типичные виды кривых деформирования (рис. 33) [8].
|
В зависимости от типа кристаллической решетки на кривых можно обнаружить характерные стадии. Например, при деформациях ε<0,1 материал интенсивно «упрочняется», как правило, с постоянным показателем деформационного упрочнения. В наибольшей степени деформационное упрочнение характерно доля аустенитных сталей и сплавов титана, меди. Слабое упрочнение наблюдается в алюминии и его сплавах, α-железе.
![]() | ![]() |
Рис.32 Диаграммы деформации образца, построенные в относительных координатах σ(ε) –а) и истинных координатах S (e) –б). Предел текучести – σ0,2 или σт, точки «А – Е» представляют определенные уровни напряжений по мере деформации образца, S k – сопротивление разрушению в момент образования шейки, e k = (S k – σт)/D – пластичность, а величина D – сопротивление пластическому деформированию. |
При завершении стадии параболического упрочнения и достижении σmax активизируются процессы разупрочнения с последующей стабилизаций структурно-механи-ческого состояния и выходом зависимости σ(ε) на площадку «насыщения». На установившейся стадии температурно-скоростные условия пластической деформации определяют субструктуру материала.
Известны различные варианты построения диаграмм деформирования, но, независимо от выбранного способа, диаграммы деформации S (e) дают наглядное представление о поведении материалов и их механических свойствах и удовлетворительно аппроксимируются функцией вида:
S = R e n,
где R – это коэффициент деформационного упрочнения, определяемый как истинное напряжение при значении истинной деформации, равной 1; параметр n — показатель деформационного упрочнения, принимающий значения от 1 при идеально упругом поведении материала, до 0 в случае идеально пластичного поведения.
![]() |
Рис.33 Модельные кривые деформирования σ(ε) металлов и сплавов в условиях горячей пластической деформации [8]: 1 – упрочнение на фоне активного динамического возврата, характерное для металлов и сплавов с высокой энергией дефектов упаковки (ЭДУ), 2 – кривая с максимумом, наличие которого определяется типом кристаллической решетки. Участки: заштрихованный (А) – единичное скольжение дислокаций при ε<0,03; (Б) – множественное скольжение при ε<0,1; (В) – параболическое упрочнение при ε до 0,3; (Г) – начало динамического разупрочнения. |
Опираясь на проверенный многолетний опыт определения структурно-механического состояния сталей и сплавов, в исследованиях технологий ТМО, основным источником информации о поведении деформируемого материала используются кривые деформирования σ(ε), полученные в условиях реального времени. В процессах горячего сжатия при деформации ε<30% значения ε и e близки. Поэтому при температурах T>0,5Tплавл и скоростях деформации от 10-3 до 10 с-1 зависимости σ(ε) и S (e) адекватны условиям испытаний и, тем самым, предоставляют возможность моделирования технологических операций ТМО.
|
|
Эмиссия газов от очистных сооружений канализации: В последние годы внимание мирового сообщества сосредоточено на экологических проблемах...
История развития пистолетов-пулеметов: Предпосылкой для возникновения пистолетов-пулеметов послужила давняя тенденция тяготения винтовок...
Общие условия выбора системы дренажа: Система дренажа выбирается в зависимости от характера защищаемого...
История развития хранилищ для нефти: Первые склады нефти появились в XVII веке. Они представляли собой землянные ямы-амбара глубиной 4…5 м...
© cyberpedia.su 2017-2024 - Не является автором материалов. Исключительное право сохранено за автором текста.
Если вы не хотите, чтобы данный материал был у нас на сайте, перейдите по ссылке: Нарушение авторских прав. Мы поможем в написании вашей работы!