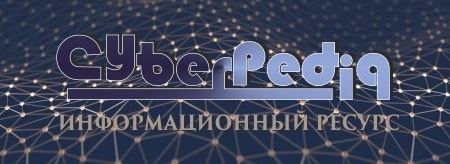
Кормораздатчик мобильный электрифицированный: схема и процесс работы устройства...
Опора деревянной одностоечной и способы укрепление угловых опор: Опоры ВЛ - конструкции, предназначенные для поддерживания проводов на необходимой высоте над землей, водой...
Топ:
Организация стока поверхностных вод: Наибольшее количество влаги на земном шаре испаряется с поверхности морей и океанов...
Методика измерений сопротивления растеканию тока анодного заземления: Анодный заземлитель (анод) – проводник, погруженный в электролитическую среду (грунт, раствор электролита) и подключенный к положительному...
Процедура выполнения команд. Рабочий цикл процессора: Функционирование процессора в основном состоит из повторяющихся рабочих циклов, каждый из которых соответствует...
Интересное:
Уполаживание и террасирование склонов: Если глубина оврага более 5 м необходимо устройство берм. Варианты использования оврагов для градостроительных целей...
Как мы говорим и как мы слушаем: общение можно сравнить с огромным зонтиком, под которым скрыто все...
Влияние предпринимательской среды на эффективное функционирование предприятия: Предпринимательская среда – это совокупность внешних и внутренних факторов, оказывающих влияние на функционирование фирмы...
Дисциплины:
![]() |
![]() |
5.00
из
|
Заказать работу |
|
|
Барахтин Б.К., Лебедева С.Н., Панова Г.А.
Термопластические технологии в машиностроении. Термомеханическая обработка сталей и сплавов для судостроения: учеб. пособие / Б.К.Барахтин, С.Н.Лебедева, Г.А.Панова.- СПб.: Изд-во СПбГМТУ, 2018.- с.
Учебное пособие разработано в соответствии с требованиями общеобразовательных стандартов к содержанию дисциплины «Материаловедение».
В краткой и доступной форме изложены сведения о методах деформирования металлов давлением (ОМД), среди которых для нужд судостроения базовыми являются технологии термопластической обработки. Рассмотрены принципы перспективной термомеханической обработки(ТМО) сталей и сплавов. Описано оборудование для моделирования операций. Приведены методики исследований и примеры нахождения наилучших условий ТМО с помощью карт процесса. Изложение построено на принципах междисциплинарного системного анализа и концепций научной методологии по направлению к созданию конвергентных технологий будущего.
Пособие предназначено для студентов и аспирантов, обучающихся по программам бакалавриата и магистратуры по специальности «Материаловедение в машиностроении». Может быть полезно студентам других специальностей, связанных с материаловедением.
Табл. 8. Ил. 53.Библиогр. назв.
СПбГМТУ,
2018
ОГЛАВЛЕНИЕ
Стр. | |
Введение | 5 |
Часть 1. Термопластические технологии в машиностроении и поведение конструкционных материалов в условиях горячей пластической деформации | 9 |
1.1 Определения и способы термопластической формовки металлических материалов | 10 |
1.2 Классификация методов термопластической обработки сталей и сплавов | 17 |
1.3 Влияние температурного фактора | 22 |
1.4 Структурные изменения в условиях горячей пластической деформации | 26 |
1.5 Фрагментация структуры как эволюционный процесс | 32 |
1.6 Типовые технологические дефекты при термопластической обработке металлов | 35 |
Часть 2. Пути совершенствования термопластической обработки металлических материалов | 39 |
2.1 Использование современных аналитических средств для контроля структурных изменений | 39 |
2.2 Распространенные стали и сплавы, производимые по технологиям термопластического деформирования | 43 |
2.2.1 Особенности структуры судостроительных магналиев | 44 |
2.2.2 Строение сталей на основе железа | 46 |
2.2.3 Строение аустенитных сталей, насыщенных азотом | 53 |
2.2.4 Строение нержавеющей аустенитной стали типового химического состава | 57 |
2.3 Механические испытания – основная информационная база совершенствования термопластической обработки | 59 |
2.4 Диагностика механического состояния материалов в имитационном моделировании ТМО | 67 |
2.5 В условиях горячей пластической деформации поведение твердых тел с позиций реологии | 71 |
2.5.1 Реологическая модель распределения механической энергии | 75 |
2.5.2 Алгоритм расчета коэффициентов эффективности диссипации и построение карты процесса | 82 |
2.5.3Имитационные испытания и применение карты процесса | 87 |
2.5.4 Перспективы совершенствования технологий с термопластической обработкой сталей и сплавов | 100 |
Список литературы | 105 |
|
ВВЕДЕНИЕ
Издревле Человечеству известны методы обработки металлических материалов путем пластической деформации и нагрева. Многовековой практический опыт и накопленные знания привели к созданию разнообразных нагревательных устройств и деформирующих агрегатов, на основе которых возникла и успешно развивается мощная производственная металлургическая отрасль – обработка металлов давлением (ОМД). Сочетание температурного воздействия с пластической деформацией металлических полуфабрикатов общепризнано как наиболее важный этап в жизненном цикле любой металлоконструкции. В условиях термопластической деформации формируется структура материала, которая в дальнейшем определяет его механические и эксплуатационные свойства, технологичность, материалоемкость, надежность и в конечном итоге – стоимость изделия.
|
К настоящему времени разработаны разные способы и методы ОМД. В реальном производстве общепризнанная классификация методов позволяет выбрать наиболее эффективные условия обработки полуфабрикатов. В разрешении проблемы производства металлопродукции с требуемым комплексом свойств технологу предстоит решить ряд задач, в которых ответы должны указать на режимы обработки металла и результаты оказанного воздействия. В задачах первого типа («как сделать»?) ответы важны при выборе оборудования, которое должно обеспечить необходимые температурно-силовые режимы обработки: ковки, прессования, прокатки и др. В задачах второго типа («что в итоге»?) в сравнении с требуемыми параметрами оценивается структурно-механическое состояние обработанного металла.
Для производственных задач некоторые частные решения разной степени сложности известны (рис.1) [1].
![]() |
Тем не менее, в связи с совершенствованием технологического оборудования и постоянно возрастающими требованиями к металлопродукции изыскания новых технических решений не прекращаются. Например, в пресс-релизе регионального правительства об итогах XX Московского международного Салона изобретений и инновационных технологий «Архимед»[1] сообщалось, что в ОАО «Магнитогорский металлургический комбинат» разработана технология ТМО для изготовления толстолистового высокопрочного проката для нужд судостроения.
В современных многоэтапных и высокопроизводительных технологических звеньях производства проследить путь формирования структуры металла, определяющей выходные параметры продукции, чрезвычайно сложно. Одним из методов получения необходимой информации является моделирование операций ТМО путем механических испытаний, имитирующих условия реального производства. Обработка данных имитационных термопластических испытаний дает возможность построить карту процесса, которая после подтверждения структурными исследованиями становится информационной базой для совершенствования технологического процесса. В системе координат «температура – скорость пластической деформации» найденные решения в виде количественных оценок эффективности рассеяния вводимой механической энергии позволяют найти ответ на вопрос «как сделать»? Последующая проверка решений методами структурных исследований отвечает на вопрос «что в итоге»? Суммарное заключение указывает путь совершенствования исследованной технологической операции. Изложение материала построено на основе современных представлений о процессах и явлениях, происходящих в металлических материалах в условиях горячей пластической деформации.
|
Проводившиеся исследования со сталями разных систем легирования и магналиями соответствуют приоритетным научным направлениям: «Новые материалы и химические технологии», «Производственные технологии», а также «Материалы и сплавы со специальными свойствами», которые входят в перечень «Приоритетных направлений развития науки, технологий и техники Российской Федерации» и «Перечень критических технологий Российской Федерации», утвержденных Президентом Российской Федерации.
Целью пособия авторы определили описание перспективной экспериментальной методики имитационного моделирования базовых операций ТМО, позволяющей с помощью построенной карты процесса найти наилучшие условия термопластической обработки сталей и сплавов разных систем легирования. В пособии рассмотрены как методические аспекты, так и концептуальные положения современного материаловедения. Задача пособия состоит в том, чтобы показать применение современных научных положений в практической разработке новых материалов и технологий их производства.
Определения и способы термопластической формовки металлических материалов
Полуфабрикаты (как правило, слитки) сталей и сплавов, которые применяются в энергомашиностроении и судостроении, в настоящее время обрабатываются в разных вариантах термопластической обработки. Например, для получения заготовок, имеющих «приближенные» формы и размеры необходимых деталей и требующих обработку резанием для придания им окончательных размеров с поверхностью заданного качества, основными операциями являются ковка и штамповка. Для получения заготовок постоянного поперечного сечения по длине (прутков, листов, лент, проволоки) используют прессование, прокатку (рис.3).
|
![]() |
Рис.3 Наиболее распространенные способы термопластической обработки сталей и сплавов с помощью давления Р. |
Ко́вка —высокотемпературная обработка, как чистых металлов, так и сплавов на основе железа, меди, титана, алюминия и др., нагретых до ковочной температуры. Для каждого металла существует своя ковочная температура, зависящая от физических и химических свойств (табл.1). Без нагрева ковка не производится. Пластическая деформация без нагрева рассматривается как просто гнутый металл.
Ковка является одним из экономичных способов получения заготовок деталей, вес которых может достигать нескольких десятков тонн. Изделия и полуфабрикаты, получаемые ковкой, называют «поковка».
Штамповка – производственный метод массового изготовления продукции путем пластической деформации заготовки с помощью штампа заданной или требуемой формы.
Прессование – процесс ОМД, в котором разогретая до высокой температуры заготовка, помещенная в замкнутую прочную форму, выдавливается из нее сквозь одно или несколько отверстий. Форма и размеры поперечного сечения выдавленной части заготовки соответствуют форме и размерам отверстий.
Таблица 1
Пластической деформации
Накопленный практический опыт горячей пластической деформации металлов и сплавов позволяет утверждать, что корректно построенная карта структурных состояний является необходимой базой оптимального управления даже в сложном случае многократных деформаций с одного нагрева, как это происходит в многоклетьевых прокатных станах.
В разработанных и многократно проверенных положениях деформационно-термической обработки, подчеркивается, что все структурно-фазовые изменения в материалах должны происходить на фоне высокой концентрации дефектов кристаллической решетки, генерируемых по ходу пластической деформации. В условиях горячей пластической деформации, которая является ключевой, из числа явлений и механизмов, определяющих уровень упрочнения и (или) разупрочнения материала, выделяют:
1) динамический возврат,
2) динамическую рекристаллизацию,
3) сверхпластичность,
4) образование пор и микротрещин,
5) локализацию пластического течения,
6) межзеренное разрушение.
Учитывая исключительную важность перечисленных механизмов, приведем их краткие характеристики.
|
Динамический возврат – релаксационный процесс, который способствует уменьшению коэффициента упрочнения и достижению динамического баланса скоростей генерации, и аннигиляции подвижных дислокаций. Движение дислокаций реализуется путем поперечного скольжения и переползания с формированием малоугловых границ (субграниц) из дислокаций одного знака (рис. 11).
![]() | ![]() ![]() |
Рис. 11 Схема движения дислокаций ρ при полигонизации –а) и варианты образования внутризеренных малоугловых границ в форме упорядоченных скоплений дислокаций одного знака –б). |
Процесс динамического возврата термически активируемый. Металлами, в которых в условиях горячей пластической деформации активно развивается динамический возврат, являются: Al, α-Fe, Mo, W, Zn. Легирование твердого раствора элементами, которые затрудняют динамический возврат, следует указать: Cu, Ni, Co, γ-Fe, Ag, Pb. Явление динамического возврата задерживает начало работы другого механизма структурообразования – динамической рекристаллизации, инициируемой непосредственно в очаге деформации (рис. 12).
Динамическая рекристаллизация – явление зарождения и роста новых (рекристаллизованных) зерен по ходу горячей пластической деформации в определенном интервале напряжений, зависящем от протекания процессов динамического возврата. Динамическая рекристаллизация активируется по мере достижения «критической» (пороговой) степени деформации, при которой скорость образования центров кристаллизации начинает превышать скорость их роста. Процесс динамической рекристаллизации считается благоприятным, поскольку приводит к однородной мелкозернистой структуре с хорошими технологическими свойствами. В зависимости от условий обработки динамическая рекристаллизация может сопутствовать упрочнению за счет измельчения зерна (эффект Пэтча-Холла) и разупрочнению вследствие релаксации структурных напряжений и снижения уровня латентной энергии.
![]() ![]() ![]() ![]() |
Рис. 12 Заключительная стадия проката с возможным переходом от динамического возврата к процессам рекристаллизации. |
Активация динамической рекристаллизации увеличивается с ростом скорости деформации и температуры. Снижение скорости и повышение температуры прокатки инициирует образование крупных зерен рекристаллизации.
Развитие динамической рекристаллизации зависит от наличия мелкодисперсных фаз (карбидов, нитридов, интерметаллидов и др.), которые закрепляют границы исходных зерен.
В условиях динамической рекристаллизации обрабатывают углеродистые и легированные стали в аустенитном состоянии, жаропрочные никелевые сплавы и латуни.
Сверхпластичность — изотермическое состояние материального объекта, при котором возможность его деформирования без разрушения резко возрастает. Интерес к этому явлению обусловлен его большим практическим значением в связи с возможностью существенного ускорения процессов обработки металлов давлением при одновременном улучшении качества изделий и значительной экономии металла и энергоресурсов.
Состояние сверхпластичности характеризуется:
1) повышенной чувствительностью напряжения течения материалов к изменению скорости деформации;
2) большим ресурсом деформационной способности;
3) напряжением пластического течения, значительно меньшим предела текучести.
Для материалов, находящихся в состоянии сверхпластичности, отмечают сильную зависимость напряжения течения σ от скорости деформации έ:
σ = έm,
где m – показатель скоростной чувствительности напряжений.
Для обычных материалов m<0,3, а для тех, которые способны деформироваться на большую величину, 0,5 <m< 0,7, а в некоторых случаях величина m близка к 1. Для описания сверхпластичности скоростную зависимость напряжения преобразуют в соотношение:
m= [d(lg σ)] / [d(lg έ)].
Для развития сверхпластичности необходимо обеспечить такие условия деформации, чтобы значения m превышали 0,3—0,35.
Выделяют несколько видов сверхпластичности:
- структурную, наиболее изученную, характерную для мелкозернистых материалов при отсутствии фазовых превращений в твердом состоянии;
- мартенситную, обусловленную фазовыми превращениями;
- высокотемпературную (немартенситную), которая наблюдается как в изотермических, так и при термоциклических условиях вблизи температур фазового превращения.
Поры и микротрещины – объемные дефекты, которые образуются при пластической деформации с необратимым разрывом межатомных связей. Их морфологические особенности определяются пластической податливостью металла и условиями горячей пластической деформации. Например, при высоких скоростях деформации при низких температурах могут образовываться микропустоты и поры. При медленной пластической деформации и высоких температурах возможно возникновение микротрещин (рис. 13).
![]() |
Рис.13 Варианты встречи дислокационных скоплений у границы зерна А-А, удаленных друг от друга на расстояние δ –а), которая может привести к образованию микротрещины –б) или поры –в). |
Локализация пластического течения – опасное явление в деформируемом материале, которое свидетельствует о неоднородном структурно-механическом состоянии, слабом упрочнении и локальной потере механической устойчивости среды с нарушением сплошности срезом. Как правило, эффект проявляется в виде полос или трещин адиабатического сдвига (ПАС), у которых вдоль границ можно наблюдать следы рекристаллизационных процессов или фазовых превращений (рис.14).
Неустойчивости пластической деформации возникают в пространственно неоднородной структуре вследствие следующих причин:
- локального возрастания скорости деформации и локального упрочнения;
- локальной концентрации напряжений;
- прироста поверхности из-за локализации деформации и локального изменения геометрического фактора.
![]() | ![]() |
Рис.14 Трещины адиабатического сдвига в образцах титанового сплава ВТ1-0 –а) и технического железа –б), деформированных в условиях горячего сжатия. |
Межзеренное разрушение может возникнуть при любых температурах и скоростях пластической деформации на участках границ с ослабленными силами сцепления между соседними объектами поликристаллического материала. Как правило, эффект проявляется в зонах ликвационных неоднородностей, из-за окисления зерен при перегреве металла или при деформации композиционных материалов, полученных спеканием.
Из перечисленных кинетических механизмов формирования структур динамическая рекристаллизация и сверхпластичность являются «безопасными» для операций горячей обработки давлением, а механизм возврата – для теплой пластической деформации.
В произвольных условиях горячей деформации структурные изменения неизбежны. Эволюция структур может сопровождаться образованием пор и трещин в стыках зерен и вдоль плоскостей сдвига, неоднородностью в размерах и распределении зерен, что неблагоприятно как для технологической обработки, так и для выходных (механических) параметров материала. В условиях активной пластической деформации одной из особенностей в преобразовании структур выделяют явление фрагментации, которое присутствует на всех этапах термопластической обработки металлических материалов.
Фрагментация структуры как
Эволюционный процесс
В современном материаловедении фрагментация трактуется как феномен разбиения однородно ориентированных зерен на сильно разориентированные субзерна, которые в процессе пластической деформации уменьшаются до 0,2 мкм, а их взаимные разориентировки θ увеличиваются по линейному закону:
θ = ξ1 (ε – ε0),
где ε – истинная (логарифмическая) макродеформация, ε0 – пороговая деформация, соответствующая началу фрагментации, ξ1 – коэффициент.
Рассматривая структурные изменения с позиций кинетики, можно представить процесс накопления разориентаций с помощью простейшего эволюционного уравнения:
dθ/dt = ξ2 θ,
где ξ2 – коэффициент, определяющий характер или темп развития процесса. Если задано начальное состояние θ(t0), то существует единственное решение уравнения, предсказывающее будущие разориентировки для любых t>t0 и «степень завершенности» фрагментации при отсутствии внешних факторов.
На этапе активного упрочнения аналогичные зависимости можно записать и для деформации:
dε/dt = ξ3 (ε – ε0,02).
Здесь ξ3 – также коэффициент, ε0,02 – пороговая необратимая (микро-) деформация.
Решения приведенных простейших эволюционных уравнений предсказывают, что с течением времени внутреннее строение деформируемого материала, как в терминах разориентаций, так и деформаций, на этапе упрочнения должно достичь некоторого предельного состояния, при достижении которого возникает новое. Например, при активной деформации в нормальных температурных условиях достижение предельного фрагментированного состояния приводит к зарождению микротрещин как нового структурного состояния и механизма релаксации накопленной упругой энергии. В терминах физической мезомеханики это событие равносильно выходу вихря механического поля на свободную поверхность.
В условиях горячей пластической деформации, когда активны механизмы динамической релаксации, в новых динамически рекристаллизованных зернах возможны повторные процессы фрагментации с накоплением латентной энергии и последующим ее рассеянием в других «более новых» структурных состояниях.
Несмотря на существенные отличия в температурах плавления, в кинетическом отклике на термомеханическое воздействие для всех исследованных в данной работе сталей и сплавов общее отмечается в единообразной зависимости ГЦК металлов от гомологической температуры (~0,7 от температуры плавления). Имеющиеся данные о поведении ГЦК металлов в условиях термопластического воздействия позволяют высказать предположение, что одним из механизмов рассеяния вводимой механической энергии является некая приграничная квазиаморфная неустойчивая фаза. Образование этого неустойчивого состояния можно рассматривать с позиций химической кинетики как проявление нестационарного массопереноса вблизи границ раздела зерен.
В стационарных условиях полиморфные реакции с образованием фаз зависят от концентрации реагентов согласно уравнениям массопереноса в виде:
∂2c/∂r2 + 2/r (∂c/∂r) = k cn = k f(c),
где вид уравнения приведен в безразмерных координатах (r), f(c) – произвольная функция, зависящая от концентрации вещества (с) в сплошной фазе, n – порядок химической реакции, k – константа скорости объемной химической реакции. Возможные граничные условия: r = 1, с = 1, r→ ∞, с→ 0.
При n = 1 (реакция первого порядка) можно получить точное аналитическое решение задачи:
C = {exp[ k½ (1 – r)]} /r.
В условиях горячей деформации с нестационарным переносом атомов и микрообъемной реакцией кинетическое уравнение имеет другой вид:
∂c/∂τ = ∂2c/∂x2 – k f(c),
где также в безразмерных переменных: x = X/d (Х – координата, отсчитываемая от границы зерна величиной d, D –коэффициент диффузии, t – время, τ = D t/d2.
В нестационарных условиях структурообразования возрастает роль кинетических процессов. В зависимости от вида функций кинетики распределение концентраций атомов, входящих в ансамбли дефектов кристаллического строения, может различаться на десятки порядков. Поскольку диффузионные процессы способны к переносу материальной среды на расстояния нескольких нанометров, предметом исследований является разрешение проблемы в определении соотношения между реакционной кинетикой и кинетикой массопереноса.
Следовательно, в условиях нагрева и деформации для структуры как физической системы с возможностью структурно-фазовых переходов, необходимо учитывать:
- исходное состояние структуры (размер зерна);
- содержание примесей, определяющих деформационное старение;
- наличие и завершенность фрагментированного состояния, которое определяет нагартованность (сопротивление пластической деформации) металла.
Сформулированные требования представляются важными, поскольку основа любой технологии – ее воспроизводимость, и на всех этапах производства структурно-механическое состояние материала определяет качество производимого металлопроката.
ТЕРМОПЛАСТИЧЕСКОЙ ОБРАБОТКИ
МЕТАЛЛИЧЕСКИХ МАТЕРИАЛОВ
Современное прокатное производство – сложный производственный механизм. Изготовление проката состоит из нескольких последовательных операций, в ходе которых осуществляются нагрев, изотермическая выдержка, пластическая деформация и последующее охлаждение металла.
Процессы и явления, реализуемые на практике, весьма разнообразны, но независимо от способа термосилового воздействия, для получения материалов с необходимым комплексом эксплуатационных свойств требуется изыскание наилучших условий обработки, которые определяются величиной (ε) и скоростью пластической деформации (έ), а также температурой (Т). Эти основополагающие параметры определяют выбор способа деформации по суммарной величине, дробности, разработке проектов размещения и согласования деформирующих агрегатов и термического оборудования. Время (t) не столь явно входит в число определяющих параметров, хотя через скорость пластической деформации оказывает существенное влияние на производительность процесса, а продолжительность операций термического воздействия (нагревы, выдержки и охлаждения) определяет качество продукции. Как видно, анализ и учет кинетики структурных изменений являются одними из возможных путей совершенствования технологии термопластической обработки металлов и сплавов.
Магналиев
Магналии – сплавы системы «алюминий-магний», относятся к группе высокопрочных коррозионностойких свариваемых термически не упрочняемых конструкционных материалов, которые находят широкое применение в изделиях морской, авиационной и космической техники. Сплавы очень технологичны. Путем вариации режимов термопластического воздействия в магналиях возможно формирование ультра мелкозернистого состояния, необходимого, но недостаточного для проявления эффекта сверхпластичности.
Для проведения имитационных экспериментов выбран распространенный магналий Al-Mg (табл.4) с разным содержанием микролегирующих добавок (хрома, титана, циркония и скандия).
Таблица 4
Металлических материалов
Вклад в величину предела текучести | Механизм упрочнения |
Δσ0 = α G c½ | Нульмерными дефектами (вакансиями, межузельными атомами) концентрацией c в твердом растворе |
Δσ1 = β Gb ρ½ | Линейными дефектами (дислокациями) плотностью ρ в скоплениях разного типа (хаотическом, ячеистом, фрагментированном) |
Δσ2 = k d-½ | Планарными дефектами (границами) зерен размером d, известный как закон Холла-Пэтча |
Δσ3 = γ G b l-1 | Объемными объектами разного типа (частицами, фазами) размером l |
Здесь: α, β, γ, k– постоянные, G – модуль сдвига, b – вектор Бюргерса. |
Возникновение такой пластинчатой структуры приводит к неоднородности механических свойств деталей, имеющих большие площади сечения, значительному снижению пластичности и ударной вязкости, а также к ухудшению свариваемости стали.
Устранение отрицательного влияния прерывистого распада на механические свойства стали достигается:
- легированием ванадием, обеспечивающим смену прерывистого распада γ→γ + Cr2N на непрерывный распад γs —> γ + VN (γs — пересыщенный азотом аустенит);
- термопластической обработкой, изменяющей форму и характер распределения частиц Cr2N и формирующей структуру типа «микродуплекс»;
- горячим пластическим деформированием с окончанием обработки при температуре, превышающей температуру начала реакции прерывистого распада, но недостаточной для развития собирательной рекристаллизации аустенита;
![]() | ![]() |
Рис.27 Ультрадисперсные частицы в матрице –а) и дугообразные следы прерывистого распада твердого раствора, декорированные ямками травления –б), в сплаве типа 04Х20Н6 после деформации со скоростью έ = 1 c-1 при температуре 1000 оС. |
- гранульной технологией, обеспечивающей измельчение колоний γ+ Cr2N в гранулах, полученных при быстром охлаждении.
В экспериментах с имитацией ТМО использован аустенитный сплав с содержанием азота (0,4-0,6%) типа 04Х20Н6, который в машиностроении рассматривается как коррозионностойкий свариваемый материал.
Термопластической обработки
В науке о материалах давно утвердилось осознание положения, что внутреннее строение твердого тела определяет его многие свойства, в том числе и механические. Поэтому разработка любого технологического процесса, связанного с изменением размеров и формы исходного материала, будет успешной, если известны или установлены структурно-механические параметры материала, а также природа и механизмы структурных изменений. Надежную и адекватную информацию о свойствах конструкционных сталей и сплавов различных систем легирования можно получить путем целевых механических испытаний с вариацией условий воздействия с последующим изучением произошедших структурных превращений.
Введение в действие Федерального закона о техническом регулировании утвердило повышение роли механических испытаний в поисковых, прикладных и других работах, касающихся разработки и применения материалов. Результаты исполнения законодательных актов уже видны в технических регламентах, стандартах, руководствах и других нормативных документах.
С целью получения информации о наилучших режимах горячей пластической обработки сталей и сплавов проведено большое количество исследований с определением структурно-механического состояния при разных температурно-скоростных условиях нагружения. Установлено, что при прокатке, ковке, производстве труб поперечно-винтовой прокаткой или прошивкой и т.д. горячая деформация оказывает существенное влияние на характер напряженно-деформированного состояния и структурные изменения в металле, и, как следствие, на сопротивление деформации. В общем случае при различных процессах горячей пластической деформации структурно-механическое состояние материала является очень сложным, и лабораторные эксперименты лишь упрощенно отражают реальную картину происходящего в реальном производстве. Однако можно и удается найти приемлемую корреляцию между промышленными условиями и лабораторными опытами, если регистрация параметров напряженно-деформиро-ванного состояния и модель поведения материала выбраны обоснованно. Поэтому для объективной оценки структурно-механического состояния сталей и сплавов в условиях горячей пластической деформации основное внимание уделено получению и обработке данных механических испытаний как полной и достоверной информации отклика материала на оказываемое воздействие.
Известно [8], что в металлоконструкциях напряженно-деформированное состояние материала контролируется природой прикладываемого напряжения и геометрией зоны деформации. Применительно к технологии термомеханической обработки распространенными вариантами напряженных состояний являются: одноосное сжатие, двухосное сжатие и трехосное сжатие (рис. 30).
Первый случай соответствует свободной ковке и прокатке узких заготовок в гладких валках, когда сжатие заготовок осуществляется одновременно со смазкой торцовых поверхностей.
![]() | ![]() | ![]() |
Линейное одноосное сжатие, S3< 0 | Плоское одноименное двухосное сжатие, S2< 0; S3< 0 | Объемное трехосное сжатие, S1< 0; S2< 0; S3< 0 |
Рис. 30 Типы напряженных состояний и диагональные компоненты тензора напряжений Ŝ при сжатии заготовок в технологиях ТМО. |
Второй вариант встречается при прокатке в ручьевых валках или ковке в штампах, закрытых с двух сторон.
Трехосное сжатие реализуется при прессовании под гидростатическим давлением и ковке в закрытых штампах. В общем случае действие механических сил характеризуется объемным трехосным напряженным состоянием в форме тензора напряжений второго ранга Ŝ, в котором из девяти компонент три независимых определяют касательные напряжения и способность к пластической деформации, и три также независимых компоненты нормальных напряжений выражают условия сплошности (неразрывности) материала. Подобно тензору напряжений, тензор деформаций ê в общем случае также характеризуется шестью компонентами – тремя удлинениями и тремя сдвигами. В разных видах обработки компоненты напряжений и деформаций различны, но в большинстве случаев поддаются расчету и позволяют совершенствовать оснастку, инструмент и технологический цикл металлообработки.
В зависимости от способа нагружения материала могут изменяться направление, величина и распределение усилий, максимальных нормальных и касательных напряжений, а также структура, сопротивление и степень локализации деформации.
Недостатком горячей деформации растяжением является сосредоточенное (локализованное) микропластическое течение, возникающее даже при небольших относительных деформациях.
В отличие от растяжения при сжатии деформация в большей степени однородна, и возможны очень большие деформации.
Испытание на сжатие не входит в число стандартных, обязательных для характеристики материала, поскольку оно мало добавляет к сведениям относительно вязких материалов, получаемых при испытаниях на растяжение. Учитывая особенности нагружения при «теплых» или «горячих» температурах, для оценки структурно-механического состояния металлов и сплавов в технологиях ТМО эксперименты производят в условиях сжатия.
Объективную, хотя и усредненную по объему образца, информацию о структурно-механическом состоянии материала и происходящих в нем изменениях содержат диаграммы нагружения (рис.31), построенные в координатах «истинные» напряжения (S) – логарифмическая деформация (e). В общем случае кривые деформирования состоят из чередующихся линейных, параболических и переходных стадий. Вид кривой пластического течения и величины, характеризующие отдельные ее стадии, от размера образца существенно не зависят.
С целью получения корректных данных о механических свойствах испытываемого материала, а также систематизации и обобщения результатов экспериментов на основе измерений размеров (длины и сечения) образцов в процессе деформирования, диаграммы нагружения следует строить в «истинных» значениях напряжений S и логарифмических деформаций e [8]. Для этого назначается непрерывная или дискретная через малые интервалы времени запись значений S (t) и e (t) с последующим построением зависимости S (e), где S - истинное напряжение, e — логарифмическая деформация, t – время.
![]() | ||||
Рис.31 Пример диа
![]() Архитектура электронного правительства: Единая архитектура – это методологический подход при создании системы управления государства, который строится... ![]() Типы сооружений для обработки осадков: Септиками называются сооружения, в которых одновременно происходят осветление сточной жидкости... ![]() Механическое удерживание земляных масс: Механическое удерживание земляных масс на склоне обеспечивают контрфорсными сооружениями различных конструкций... ![]() Особенности сооружения опор в сложных условиях: Сооружение ВЛ в районах с суровыми климатическими и тяжелыми геологическими условиями... © cyberpedia.su 2017-2024 - Не является автором материалов. Исключительное право сохранено за автором текста. |