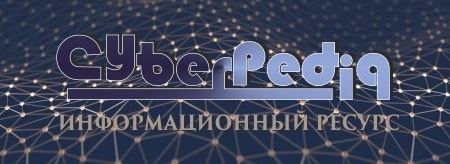
История развития пистолетов-пулеметов: Предпосылкой для возникновения пистолетов-пулеметов послужила давняя тенденция тяготения винтовок...
Археология об основании Рима: Новые раскопки проясняют и такой острый дискуссионный вопрос, как дата самого возникновения Рима...
Топ:
Генеалогическое древо Султанов Османской империи: Османские правители, вначале, будучи еще бейлербеями Анатолии, женились на дочерях византийских императоров...
Марксистская теория происхождения государства: По мнению Маркса и Энгельса, в основе развития общества, происходящих в нем изменений лежит...
Характеристика АТП и сварочно-жестяницкого участка: Транспорт в настоящее время является одной из важнейших отраслей народного...
Интересное:
Распространение рака на другие отдаленные от желудка органы: Характерных симптомов рака желудка не существует. Выраженные симптомы появляются, когда опухоль...
Лечение прогрессирующих форм рака: Одним из наиболее важных достижений экспериментальной химиотерапии опухолей, начатой в 60-х и реализованной в 70-х годах, является...
Отражение на счетах бухгалтерского учета процесса приобретения: Процесс заготовления представляет систему экономических событий, включающих приобретение организацией у поставщиков сырья...
Дисциплины:
![]() |
![]() |
5.00
из
|
Заказать работу |
|
|
Единые технические условия на изготовление отдельных деталей прокатных станов пока не разработаны. На заводах и в конструкторских бюро их назначают, исходя из опыта своей работы или опыта работы на других предприятиях.
Технологию изготовления корпусных деталей рассмотрим на примере станин рабочих клетей прокатных станов. Они бывают открытого и закрытого типа (рис. 4.11). Станины закрытого типа выполняют цельнолитыми, сварно-литыми или сборными в зависимости от оснащенности производства, габаритных размеров и массы. Их конструкция имеет вид замкнутой рамы. Станины открытого типа имеют две вертикальные стойки, отлитые совместно с основанием. Стойки соединены общей крышкой, закрепленной с помощью болтов и шпилек.
Основными обрабатываемыми поверхностями станин закрытого типа (см. рис. 4.11) являются направляющие К и Л проема под подушки прокатных валков; поверхности Б, В, М, Н лап с отверстиями П; плоскости Е, Ж, 3, И разъема; отверстие Д горловины; верхняя плоскость Г; выточки Р для центрирования корпуса нажимного устройства; шпоночные пазы С. Аналогичные поверхности имеют и станины открытого типа.
Наиболее важные технические условия, предъявляемые к механической обработке станин и влияющие в значительной степени на эксплуатационные качества станов, следующие:
несовпадение плоскостей лап станин ≤ 0,1 мм;
отклонение профиля лап и размера между рабочими боковыми поверхностями лап парных станин ≤ 0,1 мм;
отклонение от перпендикулярности боковых поверхностей окон под подушки к основанию лап ≤ 0,1 мм на длине 1000 мм;
отклонение от параллельности боковых поверхностей окон под подушки, рабочих боковых поверхностей лап и оси отверстия под гайку нажимного винта ≤ 0,1 мм на 1000 мм длины;
|
расположение оси отверстия под гайку нажимного винта симметрично боковым поверхностям окон;
отклонение от симметричности рабочих боковых поверхностей лап и боковых поверхностей окон ≤ 0,2 мм при его расположении в одну сторону у обеих парных станин;
отклонение от перпендикулярности стыковых поверхностей станин под траверсы к основанию лап ≤0,1 мм на длине 1 000 мм;
Рис. 4.11. Станина рабочей клети прокатного стана закрытого типа
отклонение от перпендикулярности основания окна под подушки к боковым направляющим ≤ 0,1 мм на длине 1000 мм.
В зависимости от конструкции рабочей клети и назначения прокатного стана технические условия на механическую обработку могут изменяться или дополняться требованиями, характерными для данной рабочей клети. Так, если установочный механизм верхнего валка имеет механический привод, отклонение от параллельности верхней плоскости станины и опорных поверхностей лап допускается ≤0,1 мм на 1000 мм. Кроме того, необходимо выдержать одновысотностъ обеих парных станин, т. е. одинаковый размер от опорных поверхностей лап до верхней плоскости станины. Отклонение размера должно быть выдержано в пределах ±0,2 мм на длине 5...6 м. Когда опорой для нижней подушки является нижняя поверхность окна, она должна быть параллельна опорным поверхностям лап; допустима не- параллельность ≤ 0,15 мм на длине 1 000 мм. Смещение окон под подушки двух парных станин относительно правильно установленных лап допускается ≤ 0,1...0,2 мм для станов, валки которых расположены в подшипниках качения или жидкостного трения, и ≤ 1...2 мм для станов, валки которых установлены в подшипниках скольжения (на подушках с текстолитовыми вкладышами) и т. д.
Анализ технических требований на изготовление деталей прокатного производства показывает широкий диапазон точности и шероховатости обрабатываемых поверхностей.
|
К проектированию ТП станин рабочих клетей необходим индивидуальный подход, так как велико разнообразие их конструкций. Например, для станин закрытого типа высотой до 5 000 мм типовой маршрут обработки следующий.
1. Размечают основные поверхности станины на разметочной плите.
2. Устанавливают на стол строгального станка комплект парных станин и обрабатывают одновременно плоскости лап и верхние плоскости станин, а также технологические базы. Заготовки кладут на бок на коробчатые подставки и крепят болтами к пазам стола. Для создания необходимой устойчивости заготовок при обработке применяют дополнительные распорки.
3. Обрабатывают боковые направляющие и основание проема станины на строгальном или расточном станке.
4. Размечают отверстия.
5. Сверлят на расточном станке все отверстия в лапах, на верхней части и на наружных сторонах стоек.
6. Сверлят на сверлильном станке все оставшиеся отверстия на плоскостях разъема лап и стоек.
7. Размечают все основные поверхности за два установа станины на разметочной плите.
8. Обрабатывают на строгальном или расточном станке боковые направляющие и основание проема станины по размерам, указанным в рабочем чертеже (рис. 4.12, а). На расточном станке фрезеруют плоскости и пазы проема угловой поворотной головкой (рис. 4.12, б).
Рис. 4.12. Эскизы основных операций механической обработки станины закрытого типа: а — общий вид станины;
б — обработка направляющих проема; в — обработка площадок и отверстий под станинные ролики; г — растачивание отверстий и фрезерование площадок верха станины; д — фрезерование торцев лап и сверление отверстий под уравновешивающее устройство
9. Устанавливают станину на ребро В лапы на стол рабочего станка и поверхностью А на призму отверстиями диаметром 520 мм к шпинделю станка и растачивают отверстия под распорки и два отверстия диаметром 520 мм (рис. 4.12, в). Фрезеруют площадки и пазы, расположенные вблизи шпинделя. Посредством перемещения шпиндельной бабки по колонне фрезеруют концевой фрезой базовые плоскости на верхних торцах лап. Перемещают колонну на размер Н и фрезеруют полоску на верхней плоскости станины. Фиксируют размер Н и переносят его на парную станину. Переустанавливают станину противоположной стороной к шпинделю станка. Растачивают конусные отверстия диаметром 660 мм согласно чертежу и фрезеруют площадки с противоположной стороны станины.
|
10. Устанавливают станину отфрезерованными площадками на поворотный стол расточного станка, а торцами лап — на призмы в направлении шпинделя станка. Фрезеруют торцы лап, выдерживая размер h (см. рис. 4.12, а) от фрезерованных баз на лапах с точностью до 0,1 мм. Сверлят и торцуют отверстия на лапах.
Поворачивают стол на 90° и фрезеруют плоскости паза на наружных плоскостях стоек под корпус подшипника станинных роликов с одной стороны. Угловые плоскости паза фрезеруют концевыми фрезами с разворотом стола на заданный угол. Поворачивают стол на 90° и фрезеруют верхнюю плоскость станины (рис. 4.12, г). При чистовом проходе фрезу устанавливают по фрезерованной базе, выдерживая размер Н ( см. рис. 4.12, а). Подрезают и растачивают выточку для центрирования корпуса нажимного устройства, растачивают отверстие горловины с подрезкой торцев. Размечают и сверлят отверстие на верхней плоскости станины. Поворачивают стол на 90° и фрезеруют паз под корпус подшипника станинных роликов с противоположной стороны.
11. Устанавливают станину торцами лап к шпинделю расточного станка. Размечают отверстия под уравновешивающие устройства (рис. 4.12, д) и сверлят специальными головками методом глубокого сверления.
12. Устанавливают две парные станины на ребро В и поверхностью А на призму, расположенную на плитном настиле расточного станка, верхними плоскостями к шпинделю. Совмещают между собой плоскости торцев лап по контрольным линейкам и проверяют совпадение верхних плоскостей станин и направляющих проема с помощью щупа толщиной 0,1 мм. Данная операция является контрольной. Обнаруженные отклонения от технических условий исправляют путем фрезерования верхних плоскостей станин на расточном станке до отправки в сборочный цех.
На предприятиях тяжелого машиностроения станки с ЧПУ получили широкое распространение на всех механообрабатывающих операциях по изготовлению корпусных деталей. В ряде случаев окончательный контроль деталей ведут на контрольноизмерительных машинах с фиксацией измеряемых параметров на записывающем устройстве.
|
При разработке ТП для станин других конструкций необходимо обращать внимание на такие основные операции, как обработка поверхностей разъемов, направляющих проема под подушки, торцев лап, верхней плоскости станины и отверстия горловины. От качества и точности обработки этих поверхностей зависит собираемость станин рабочих клетей.
Рассмотрим некоторые из этих операций.
Поверхности разъема обрабатывают на продольно-строгальных, продольно-фрезерных или расточных станках в зависимости от габаритных размеров станины и имеющегося станочного оборудования. Станину выверяют по осевым и разметочным рискам с использованием домкратов и распорок, крепят болтами и планками в местах расположения опор.
При черновых переходах поверхности разъемов обрабатывают одновременно двумя вертикальными суппортами. Чистовой проход осуществляют с одного хода резца или фрезы одним и тем же суппортом для обеспечения высоких требований, предъявляемых к плоскостности этих поверхностей.
Для фиксации парных станин между собой при сборке на плоскостях разъема каждой станины предусматривают шпоночные пазы, расположенные вдоль продольной оси станины. Как правило, эти пазы обрабатывают за один установ. При парной обработке шпоночных пазов вдоль стола устанавливают одновременно правую и левую станины (рис. 4.13, а). Поэтому нет необходимости в выдерживании с высокой точностью размеров между осями шпоночных пазов, так как при таком способе обработки их совпадение будет обеспечено.
Обрабатывая поверхности разъемов фланцевых приливов на продольно-строгальном станке (рис. 4.13, б), фактические размеры А, Б, В замеряют штихмасом от направляющей боковой стойки станка до режущей кромки резца и выдерживают их одинаковыми у парных станин.
Рис. 4.13. Эскизы установки парных станин (а) и их одновременной обработки на продольнострогальном (б) и продольнофрезерном (в) станках
На продольно-фрезерном станке подобные размеры выдерживают аналогичным способом либо путем непосредственного измерения размера Г. С этой целью к станине приваривают бобышку (на рис. 4.13, в она зачернена) и фрезеруют одновременно паз на торце фланца горловины и в технологической бобышке. Измерения ведут от паза в бобышке до пазов, расположенных на поверхности разъема лап. После этого выдерживают размер Д.
На расточных станках размеры между шпоночными пазами выдерживают одним из описанных выше способов либо путем непосредственного измерения расстояния между пазами по от- счетному устройству станка при касании концевой фрезой одной из сторон паза. Одновременно с плоскостями разъема и шпоночными пазами проводят обработку остальных поверхностей, доступных для выполнения с одного установа.
|
Направляющие проема станин под подушки имеют прямоугольную или ступенчатую конфигурацию. Наиболее часто их обрабатывают строганием на поперечно-строгальных станках, фрезерованием на расточных станках, строганием на продольно-строгальных станках.
Поперечно-строгальный станок используют, когда проем имеет много ступеней и пазов, расположенных в поперечном направлении на боковых направляющих и на основании станины. Станину устанавливают в горизонтальном положении на ребро, а обработанными боковыми площадками — на призмы. Выверку ведут по обработанным плоскостям разъемов с точностью до 0,1...0,15 мм на длине 1000 мм. Если боковые площадки не обработаны, станину устанавливают на ребро и горловиной на призму с выверкой по осевым рискам и по разметке (рис. 4.14).
Последовательность строгания такова, что по разметке осуществляют грубую обработку окна, а при чистовой обработке сначала строгают сторону направляющей проема той стойки, на которой созданы боковые базы В выдерживая размеры l 7 и l 11 от базы В с заданной по технологии точностью. В данном случае точность выполнения размеров зависит от допустимого смещения проемов у парных станин. С помощью размеров l 4 и l 5 при строгании выдерживают размер от торцев лап и базы Г до основания проема. При этом предусматривают необходимый припуск, если торцы лап не обработаны. С этого же установа строгают другую боковую направляющую с допусками, указанными на рабочем чертеже, что позволяет достаточно просто добиться параллельности направляющих между собой.
Установку и выверку парных станин при фрезеровании направляющих проемов на расточном станке ведут способом, аналогичным используемому для поперечно-строгального станка. Черновую обработку направляющих проема осуществляют цилиндрическими сборными фрезами, чистовую — цельными или насадными концевыми фрезами. За один установ заготовки обрабатывают все поверхности с наружной стороны станины. Данный способ обработки особенно эффективен, когда вдоль направляющих парной станины имеется большое число продольных пазов, а объем их обработки значителен. Способ позволяет повысить производительность обработки на 20...30 % по сравнению со строганием на поперечно-строгальном станке, однако шероховатость фрезерованной поверхности при этом несколько хуже. Вследствие большого вылета шпинделя и отжима фрезы непараллельность направляющей достигает 0,2...0,3 мм на ширине проема.
Рис. 4.14. Схема расположения измерительных баз для обеспечения точности размеров обрабатываемых поверхностей проема станины
Если направляющие проемов парных станин не имеют переходов и уступов, их можно обрабатывать на продольно-строгальных станках. Станины устанавливают обработанными плоскостями разъемов горловины и лап на стол станка, выверку осуществляют по базовым площадкам индикатором с точностью до 0,1 мм на длине 3000 мм. В местах опор заготовку крепят болтами и планками и расклинивают с четырех сторон. Обработку ведут вертикальными суппортами в закрытом контуре парной станины. Торцы лап и верхние плоскости парных станин обрабатывают совместно или раздельно. При совместной обработке за один установ строгают на продольно-строгальных или фрезеруют на расточных станках плоскости лап и верхние плоскости парных станин. Станины соединяют между собой промежуточными поперечинами. Это обеспечивает плоскостность торцев лап и верхних плоскостей станин.
Парное строгание ведут боковыми суппортами при одновременной обработке торцев лап и верхних плоскостей станин (см. рис. 4.14). Лапы и верхние плоскости станин строгают за два обдирочных, получистовой и чистовой проходы. Одновременно создают базы для выдерживания соосности проема окна с осью лап. Для этого наружную боковую плоскость Б лапы и боковую плоскость В стойки обрабатывают до Rz = 40 мкм. Для удобства применения контрольно-измерительных средств строгают базы А и Г. Размеры l 1 l 3, l 9, l 12 измеряют штихмасом от направляющих боковой стойки и от траверсы станка до баз Б, В, Г и основания лап; размеры маркируют на базах В и Г. Если габаритные размеры станины не позволяют применить продольно-строгальный станок, то аналогичную совместную обработку ведут на расточных станках.
Для сокращения цикла все большее распространение находят раздельные способы обработки парных станин. При этом способ настройки фрез по мерным штихмасам применяют редко из-за его невысокой точности. Выдерживая одинаковые размеры парных станин от торцев лап до плоскости горловины при нониус- ном способе, возможен вариант установки станин боковой стороной к шпинделю расточного станка. В целях обеспечения од- новысотности парных станин фрезеруют боковые площадки А и Б на основании лап и верхних плоскостях станин (рис. 4.15, а).
Иногда после обработки плоскостей разъема фрезеруют базы с обратной стороны торцев лап, перемещают шпиндель на технологический размер Н и фрезеруют верхние плоскости станин. Обрабатывая парные станины, размер Н выдерживают с точностью до 0,1 мм от фактического размера.
После создания баз по одному из описанных вариантов станины устанавливают торцами лап к шпинделю расточного станка и фрезеруют плоскости лап согласно размерам, приведенным на чертеже. Чистовой проход проводят заподлицо с ранее обработанными базовыми плоскостями. Затем заготовку переустанавливают верхней плоскостью к шпинделю и фрезеруют торцевые поверхности, примыкающие к верхним плоскостям станин. При чистовом проходе фреза должна касаться базовой площадки А.
Обеспечивая одновысотность парных станин способом раздельной обработки от постоянных баз по разметке, плоскости лап фрезеруют согласно размерам на чертеже отдельно у каждой станины на расточном станке. После этого станины устанавливают верхними плоскостями к шпинделю.
За первой станиной, напротив обработанных лап, устанавливают две контрольные призмы, которые тщательно выверяют (рис. 4.15, б). Фактические размеры l 1 и l 2 от призм до лап измеряют штихмасом и записывают в технологическую карту. Далее фрезеруют верхнюю плоскость этой станины по разметке с выдерживанием требуемой по чертежу высоты. От направляющей колонны расточного станка до отфрезерованной плоскости замеряют размер l 3 штихмасом и записывают его в технологическую карту. Призмы, закрепленные на плитном настиле, оставляют в том же положении и к ним устанавливают вторую станину, выдерживая размеры l 1 и l 2 с точностью до 0,1 мм.
Рис. 4.15. Схемы обеспечения одновысотности парных станин при раздельной обработке по нониус - ной линейке (а) и от постоянных баз плитного настила и станка (б)
Фрезеруют верхнюю плоскость станины, выдерживая с точностью до 0,1 мм размер l 3, полученный при обработке первой парной станины.
Используя постоянные базы в виде двух призм, закрепленных на плитном настиле, и направляющую колонну станка, обеспечивают одновысотность парных станин с точность до 0,2...0,3 мм.
Горловину любой станины выполняют в виде утолщения верхней ее части с двух- или многоступенчатым отверстием под гайку нажимного винта (см. рис. 4.12, а). Обработку горловины совмещают с операцией фрезерования верхней плоскости станины. При растачивании способом вылета шпинделя первоначально обрабатывают отверстие горловины, расположенное ближе к станку, по IT9. В него устанавливают люнетную втулку для опоры шпинделя, после чего растачивают остальную часть отверстия резцовой головкой, расположенной на оправке. Протачивание серповидных канавок в большом отверстии ведут с применением специального люнета с двумя отверстиями, межцентровое расстояние которых зависит от глубины канавок. Люнет устанавливают в большое отверстие и расклинивают.
Длительность цикла обработки сложных станин иногда составляет 30...60 сут, поэтому его сокращение является актуальной задачей. Можно предложить следующие пути ее решения:
обработка крупных станин одновременно на нескольких станках;
обработка станин на поворотных столах большой грузоподъемности;
применение специальных установочных стендов;
организация специализированных участков по изготовлению станин;
применение вместо универсальных агрегатных, специальных и специализированных станков, а также станков с ЧПУ;
отработка конструкции детали на технологичность.
|
|
Типы оградительных сооружений в морском порту: По расположению оградительных сооружений в плане различают волноломы, обе оконечности...
Историки об Елизавете Петровне: Елизавета попала между двумя встречными культурными течениями, воспитывалась среди новых европейских веяний и преданий...
Общие условия выбора системы дренажа: Система дренажа выбирается в зависимости от характера защищаемого...
Состав сооружений: решетки и песколовки: Решетки – это первое устройство в схеме очистных сооружений. Они представляют...
© cyberpedia.su 2017-2024 - Не является автором материалов. Исключительное право сохранено за автором текста.
Если вы не хотите, чтобы данный материал был у нас на сайте, перейдите по ссылке: Нарушение авторских прав. Мы поможем в написании вашей работы!