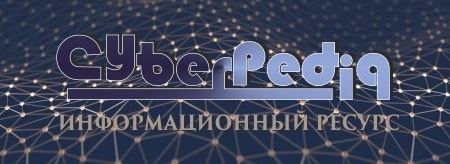
Двойное оплодотворение у цветковых растений: Оплодотворение - это процесс слияния мужской и женской половых клеток с образованием зиготы...
Механическое удерживание земляных масс: Механическое удерживание земляных масс на склоне обеспечивают контрфорсными сооружениями различных конструкций...
Топ:
Организация стока поверхностных вод: Наибольшее количество влаги на земном шаре испаряется с поверхности морей и океанов...
Выпускная квалификационная работа: Основная часть ВКР, как правило, состоит из двух-трех глав, каждая из которых, в свою очередь...
Особенности труда и отдыха в условиях низких температур: К работам при низких температурах на открытом воздухе и в не отапливаемых помещениях допускаются лица не моложе 18 лет, прошедшие...
Интересное:
Лечение прогрессирующих форм рака: Одним из наиболее важных достижений экспериментальной химиотерапии опухолей, начатой в 60-х и реализованной в 70-х годах, является...
Наиболее распространенные виды рака: Раковая опухоль — это самостоятельное новообразование, которое может возникнуть и от повышенного давления...
Аура как энергетическое поле: многослойную ауру человека можно представить себе подобным...
Дисциплины:
![]() |
![]() |
5.00
из
|
Заказать работу |
|
|
Назначение и принцип действия.
Нагнетатель предназначен для сжатия (компремирования) природного газа, транспортируемого по магистральному газопроводу при температуре газа до –15о, и воздуха = -50о.
При вращении рабочего колеса на входе его создаётся разряжение. Поступающий в межлопаточное пространство газ под действием центробежных сил движется плавно изогнутых каналов рабочего колеса.
На выходе из рабочего колеса по направлению движения газа расположен кольцевой диффузор, который преобразует кинетическую энергию движущего газа после Р.К., в потенциальную и уменьшает закрутку потока в направлении вращения.
Основные элементы проточной части нагнетателя.
1. Всасывающая камера – служит для плавной и равномерной подачи газа в осевом направлении на вход Р.К. В ней происходит повышение скорости и понижение давления газа (канал имеет конфузорное сечение).
2. Рабочее колесо – является основным элементом проточной части, в котором механическая энергия привода передаётся потоку газа. За счёт этого в Р.К. происходит увеличение скорости и давления газа. Межлопаточный канал – диффузорный.
3. Лопаточный диффузор – закреплен в пакете на выходе Р.К. Служит для увеличения давления за счёт торможения потока. Лопаточному диффузору предшествует укороченный безлопаточный, который служит для выравнивания скоростей газа после Р.К.
4. Обратный направляющий аппарат – расположен в пакете между первой и второй ступенью. Служит для поворота газа и его плавной подачи в осевом направлении к второму Р.К. Параметры газа существенно не меняются.
5. Сборная нагнетательная камера (улитка) – служит для сбора газа и его плавного отвода в нагнетательный патрубок, а также для окончательного повышения давления за счёт снижения скорости потока.
|
СТУПЕНЬ НАГНЕТАТЕЛЯ.
СОСТОИТ: из рабочего колеса и лопаточного диффузора. При работе нагнетателя газ захватывается вращающимся Р.К. и продвигается в центробежном направлении по межлопаточным каналам. За счёт вращения ротора, механическая энергия движущимися лопатками передаётся потоку газа и его абсолютная скорость увеличивается. Повышение давления в Р.К. происходит за счёт диффузорности межлопаточного канала и уменьшения относительной скорости, а также за счёт действия на частицы газа центробежных сил.
Увеличение давления за счёт центробежных сил объясняется тем, что к выходу из Р.К. окружная скорость вращения потока увеличивается, а следовательно увеличиваются центробежные силы, под действием которых происходит сжатие газа. В лопаточном диффузоре происходит дальнейшее повышение давления и температуры, за счёт уменьшения абсолютной скорости потока. Таким образом в Р.К. механическая энергия переходит в кинетическую и потенциальную, а в диффузоре кинетическая – в потенциальную.
ОСЕВОЕ УСИЛИЕ НА РОТОР НАГНЕТАТЕЛЯ.
РАЗГРУЗКА ОТ ОСЕВЫХ УСИЛИЙ.
При работе нагнетателя осевые нагрузки на ротор возникают в основном за счёт разницы давлений на входной и выходной поверхности Р.К. Усилие от давления газа на Р.К. в районе покрывного диска снаружи и изнутри уравновешиваются и не оказывают влияние на осевой сдвиг ротора. Ниже покрывного диска на входную поверхность действует давление входа + усилие скоростного напора. На обратную поверхность основного диска действует давление выхода из рабочего колеса. Кроме того площадь на входной поверхности больше на величину гайки обтекателя. Направление осевого усилия на упорные колодки будет зависеть от режима работы нагнетателя.
На пусковых режимах при открытии крана №6 (6р), когда степень сжатия небольшая ∆ Р на Р.К. тоже небольшой. При этом за счёт большого расхода газа, усилия скоростного напора на входную поверхность будет больше усилия от ∆Р. Следовательно будут нагружены упорные колодки со стороны турбины, чтобы снизить нагрузки на подшипник при пуске и останове. Осевые нагрузки частично снижаются подачей масла на специальный разгрузочный диск и возникает осевое усилие противоположное усилию на Р.К.
|
На рабочих режимах с высокой степенью сжатия ∆ Р на основном диске Р.К. может пересилить воздействие скоростного напора и суммарное осевое усилие будет направлено от турбин.
ПОМПАЖ НАГНЕТАТЕЛЯ.
Представляет собой автоколебания потока газа в проточной части, которые вызываются периодическими срывами потока с рабочих лопаток на нерасчётных режимах или из за снижения расхода газа.
Процессы протекающие в проточной части.
Если при работе нагнетателя по какой либо причине произойдёт снижение расхода газа по сравнению с расчётным, то направление потока газа на Р.Л. отклоняется от безударного. В следствии этого, обтекание лопаток будет происходить с ударом по контуру и срывом потока со стенки лопатки, что приведет к образованию завихрений газа в межлопаточном канале. До определённого момента снижения расхода и увеличения степени сжатия не нарушает устойчивую работу нагнетателя, а только уменьшает его КПД за счёт увеличения трения. При достижении критической степени сжатия и расхода, срыв потока увеличивается на столько, что вихревая зона быстро расширяется и мгновенно заполняет каналы Р.К. При этом давление создаваемое нагнетателем резко уменьшается. Однако в первой момент давление в нагнетательном патрубке и трубопроводе остаётся высоким, в следствии чего часть газа с выхода сбрасывается на вход. При движении обратного потока газа, давление в выходном трубопроводе уменьшается. Уменьшается меньше той величины, которую обеспечивает в данный момент нагнетатель. Так как сопротивление на выходе нагнетателя резко уменьшается, то нагнетатель подаёт весь газ в расчётном направлении, причём расход газа резко увеличивается до нормального значения. Обтекание лопаток становится безударным, вихревые зоны вымываются из межлопаточных каналов и нагнетатель кратковременно возвращается к нормальному режиму с высокой степенью сжатия. Однако по мере увеличения давления в выходном трубопроводе, сопротивление на выходе растёт, что приводит к снижению расхода газа через нагнетатель. Когда давление на выходе газа снизится на столько, что вихрь мгновенно вновь заполняет межлопаточные каналы и цикл помпажных колебаний повторяется.
|
ПРИЧИНЫ:
1. Самопроизвольное закрытие кранов №1; 2; 7; 8, охранных линейных.
2. Разрыв входного коллектора.
3. Образование гидратных пробок.
4. Помпаж осевого компрессора.
5. Аварийный останов одного из т/а.
6. Неправильная загрузка т/а (с низкими оборотами).
МЕРЫ ПРЕДОТВРАЩЕНИЯ
1. Для пунктов №1;2;3 – предупреждается выход т/а на «кольцо», через краны №6, или №36.
2. Изменение режима работы г/провода, которое приводит к снижению или отбора газа и степени сжатия. Определить это можно по снижению входного и выходного давления. В данном случае возникает несоответствие между снизившейся подачей газа и не изменившимися оборотами нагнетателя. Режим работы нагнетателя становится завышенным по сравнению с новым режимом газопровода. В данном случае необходимо снизить обороты до стабилизации входного и выходного давления, наблюдая за соответствием оборотов и степенью сжатия. В момент начала помпажа, как кратковременная мера, может быть использована повышение оборотов на время открытия крана №36.
ВНЕШНИЕ ПРИЗНАКИ И ВОЗМОЖНЫЕ ПОСЛЕДСТВИЯ.
Приближение к зоне помпажа можно определить по повышенной степени сжатия до критического значения. Кроме того может наблюдаться некоторое повышение температуры газа за нагнетателем, а также изменение тона работы нагнетателя. При наступлении помпажа резко усиливается вибрация в проточной части, слышны сильные гидроудары, наблюдается резкое изменение оборотов СТ, давления газа на входе и выходе, осевых сдвигов ротора нагнетателя, перепада м/г, быстро растёт температура газа за нагнетателем.
Работа в помпажном режиме может привести к разрушению лопаток и дисков рабочих колёс, подшипников, уплотнений, зубчатой муфты, промвала, а также к разрыву трубопровода крановой обвязки. Поэтому при помпаже нагнетателя должна срабатывать автоматическая аварийная защита, а при несрабатывании защиты и невозможности вывода нагнетателя из помпажа т/а необходимо остановить от кнопки.
|
РЕЖИМ «НУЛЕВОЙ» ПРОИЗВОДИТЕЛЬНОСТИ.
При длительной работе т/а в помпажной зоне нагнетатель может самопроизвольно перейти в режим «0» производительности, который характеризуется устойчивой работой нагнетателя без колебаний газового потока, отсутствием сильного шума, гидроударов и вибрации. На данном режиме практически не происходит подачи газа в выходной коллектор и вся мощность привода расходуется на преодоление трения при циркуляции газового потока с выхода на вход рабочего колеса вдоль стенок рабочих лопаток и через уплотнения покрывного диска. Отличить данный режим от нормальной работы нагнетателя довольно трудно, т. к. отсутствует сильный шум и вибрация. Давление за данным нагнетателем не будет значительно от давления на других рабочих т/а, кроме того из-за малой нагрузки на этом т/а самопроизвольно повышаются обороты СТ, что способствует повышению выходного давления. Отличительной особенностью является быстрое увеличение температуры газа на выходе и сильный нагрев корпуса нагнетателя. При длительной работе в таком режиме (более 30 мин.), температура газа может превысить 100оС, что может быть причиной значительных тепловых деформаций узлов нагнетателя. В данном случае необходимо открыть кран №6, произвести «Н.О» и охладить нагнетатель при закрытых дверях отсека и отключенной вентиляции.
«ВЕНТИЛЯТОРНЫЙ» РЕЖИМ.
При работе нагнетателя со степенью сжатия намного ниже расчётной на данные обороты, наступает так называемый «вентиляторный режим». Такой режим может быть в следствии работы в «магистраль» при большом отборе или подачи газа, а также при работе на «кольцо» с высокими оборотами. В «вентиляторном режиме» скорость газа в проточной части может значительно превысить расчётное, что приведёт к возникновению срывов потока и повышенной вибрации лопаток аппарата, особенно в диффузорах, происходит повышенной износ рабочих лопаток. Ротор нагнетателя находится в режиме газо-динамичной неуравновешенности, вследствие чего могут возникнуть непрогнозируемые осевые смещения. КПД нагнетателя на таком режиме очень низкий. При работе ГПА следует избегать работы с низкой степенью сжатия, из-за низкой экономичности данного режима, а также из-за повышенной опасности появления дефектов нагнетателя.
ВОЗМОЖНЫЕ НЕИСПРАВНОСТИ И ПРИМЕРНЫЕ МЕТОДЫ ИХ УСТРАНЕНИЯ.
Неисправность. | Причина, методы их устранения. |
При возникновении неисправности, проверь испр. КИП. I. ТЕМПЕРАТУРА МАСЛА. | |
1. Томасла на вых. с маслоохлад. <35оС. | Оценить работоспособность РТП-65,при необходимости заменить. |
2. То масла на вых. с масоохлад. > 55оС. | а). Проверить кол-во раб. ВМНов, при необход. дополнить. б). Оценить работоспособность РТП-65, при необход. замен. |
3. Превышение tо масла на выходе опор. и опорно-упорного подшипника нагнетателя. | а). Контроль РМ в напор. кол-ре, проверить настр. КР, проверить раб-ть ГНС, контроль ∆Р на фильтрах. б). Пров. зазор ротор-уплотнение масляных колец подшипн. в). Проверить состояние колодок подшипника. г). Проверить зазор в упорном подшипнике. д). Контроль tо масла на выходе МОНов. |
4.Превышение tоМ на входе в двиг., выход с МОДов. | а) Проверить работу ВМОДов (вкл. дополнительно). Проверить работу РТП-32-50. При необходимости заменить. |
II. ТЕМПЕРАТУРА ВОЗДУХА. | |
1. tо в ОД и ОН <15о. | а) Проверить наличие подачи г/в в ОД и ОН. |
2. tо в. в ОД >100оС. | а) Проверить раб. ВВОДов. б) Проверить налич. горячих выбросов и разъёмов двиг. и места соед. СТ и улитки. Открыть эжекторы КЦВ. |
1. Падение Р см Н. | III. ДАВЛЕНИЕ МАСЛА. а) Проверить работу ГНС. б) Проверить настройку работы КР. в) Контроль ∆Р см. фильтров. г) Проверить зазор, вал-уплотнение колец подшипника. д) Проверить величину зазора между упорным гребнем и уплотнительным кольцом. е) Герметичность м/с, отсутствие подсоса воздуха на всасе насосов, наличие дроссельных шайб на вх. в подшипники. |
2.∆ Р М/Г < 0,3 кг/см2. | а) Неисправность ПНУ, ГНУ. б) Исправность РПД-2М и настройку. в) Проверить зазор между валом ротора и кольцом со стороны камеры м/г. г) Проверить состояние резиновых уплот. колец, в случае необходимости заменить. д) Проверить ∆Р на фильтрах высокого давления. |
3.∆Р на Фсм или Ф упл.больше нормы. | а) Проверить положение вентилей. б) Перейти на резервный фильтр. в) Провести регенерацию фильтров. |
4. Падение Рм на входе в двиг. < 2,3 кг/см2. | а) Убедиться в герметичности м/с. б) Проверить положение вентилей на Ф см. двигателя. в) Контроль ∆Рм на фильтрах. |
|
IV. Р ГАЗА. | |
1. Р Т.Г. < 18 кг/см2. | а) Проверить работу БПТПГ. б) Проверить работу стопорного клапана. в) Проверить работу крана №12. г) Проверить чистоту фильтров топливного газа, при необходимости перейти на резервный. |
2. Р Т.Г. > 5 кг/см2. 3. Р Т.Г. < 3 КГ/ см2. | а) Проверить работу БПТГ. а) Проверить работу БПТГ. б) Проверить работу фильтра пускового топлива. |
4. ∆ Р Г на защитной решётке > 0,5 кг/см2. | а) Осмотреть решётку (очистить). |
V. ПРОЧИЕ НЕИСПРАВНОСТИ. | |
1. Уровень м/б ниже нормы. | а) Проверить фактический уровень масла по шкале поплавкового уравномера. Дозаправить. |
2. Вибрация ротора больше нормы. | а) Проверить режим работы ГПА. б) Проанализировать показания КСА-15 с предыдущими. в)Проверить крепление подмоторной рамы к раме турбоблока. г)Провести осмотр шеек вала ротора в месте установки датчиков. д) Проверить наличие зазора между корпусом СТ и улиткой, привести в соответствии с чертежом. е) Проверить центровку двиг. и нагнет. и при необходимости произвести подцентровку. ж) Проверить влияние трубопроводов газовой обвязки на центровку. з) С помощью эндоскопа проверить состояние проточной части нагнетателя. |
3.Переток масла по торс. валу в высокотемпературную зону. | а) Проверить состояние т/п на кожухах подшип. и торс. вала. б) Проверить состояние уплотнит. Колец торс.вала и зазор между ними. |
4. Предпомпажное сост-е нагнетателя. | а) Проверить величину ∆ на защитной решётке. б) Определить точку работы ГПА по газодинамическим хар-кам (изменить режим работы). |
5.Опасная загазовнность ОН, ОД. | а) Проверить раб. РПД –2М, Рм. сис-мы смазки. б) Методом обмыливания определить утечку газа и устранить их. |
6. Осевой сдвиг ротора > нормы. | а) Проанализировать значение tо упор.подшип. по предыдущим замерам. б) Проверить значение установок по сигнализации КСА-15. в) Контроль вибрации ротора нагнетателя. |
7. М/с агрегата не обеспечивает необходимое давление. | а) Проверить герметичность м/с, исключить подсос воздуха. б) Проверить закрытие КР. в) Проверить соответствие эл/дв. паспортным данным насосов. г) Проверить вращение эл/двигателя. д) Произвести ревизию насосов. |
8.Пульсация перекачиваемого масла | а) Проверить герметичность м/системы. б) Отрегулировать предохранительные и заборные кл. м/н. |
9. Повышенная вибрация м/насосов ГПА. | а)Проверить крепл. насосов и двигателя к плите (фундаменту). б) Проверить влияние трубопроводов. в) Проверить центровку с приводом (отцентровать). г) Проверить состояние подшипников. |
10. Течь масла по сальникам м/насоса. | а) Проверить жёсткость пружины сальника. б) Определить кач-во уплотнительных колец. в) Проверить кач-во трущихся поверхностей, дефекты исправить или заменить деталь. |
11. КР-1;2;3 – не поддерживает заданное Р смазки. | а) Произвести ревизию клапанов, кач-во трущихся поверхностей. б) Проверить настройку клапанов. |
12. РПД-2М не поддерживает заданный ∆ Рм/г. | а) Произвести ревизию РПД-2М. Провер. кач-во трущихся поверхностей, целостность мембраны, дефекты устранить. б) Произвести настройку, при необходимости заменить. |
13. Неиспр. м/отводчиков.(раб. контролировать по сливу через смотров. окно. Диаметр струи 5-10 мм, при наличии газа в нагнетателе. | а) Произвести ревизию м/отводчиков, проверить кач-во и исправность клапанов системы, замеченные дефекты устранить. |
14. Повышенная вибрация маслоохладителей (вентиляторов). | а) Проверить крепление вентиляторов. б) Проверить сост-ние сварных швов, кронштейнов вентиляторов. в) Проверить дисбаланс крыльчаток, произвести балансировку (статистическую) крыльчаток. |
СПЕЦТЕХНОЛОГИЯ.
НАЗНАЧЕНИЕ ЗАПОРНОЙ АРМАТУРЫ СИСТЕМЫ ТЕХНОЛОГИЧЕСКОГО ГАЗА.
На КС осуществляются следующие технологические процессы: приём газа, очистка газа, сжатие и охлаждение. Измерение и контроль технологических параметров. Управление режимом ГПА и г/провода.
Узел подключения. Состоит из трубной обвязки, запорной арматуры, камеры приёма и запуска поршня с соответствующей обвязкой.
СОК, ЮОК установлены на подводящем и отводящем шлейфе г/п, предназначены для отсечения и подключения КЦ. При работе КЦ – открыты.
Кран №7
Кран №7 установлен на входе КЦ, обеспечивает подачу газа в технологическую обвязку КЦ. При работе цеха – открыт. Закрывается для предотвращения поступления газа в обвязку цеха. Управление – автоматическое, дистанционное, местное и вручную.
Кран №7/.
Байпас крана №7 – установлен на обводной линии, при работе КЦ закрыт. Служит для заполнения обвязки КЦ газом. Имеет только ручное управление.
Дроссель за краном №7 – служит для ограничения потока газа при заполнении газом обвязки КЦ.
Кран №8.
Установлен на выходном шлейфе КЦ. При работе открыт Закрывается для предотвращения поступления газа со стороны газопровода. Также имеет как и кран №7 четыре вида управления.
Кран №8//.
Установлен на обводной линии кр. №8, при работе цеха закрыт. Служит для заполнения цеха газом, имеет только ручное управление.
Дроссель крана №8.
Служит для ограничения потока газа при заполнении.
Обратные клапаны перед краном №8.
Служат для предотвращения перетока газа со стороны выходного шлейфа в сторону всасывания при переводе цеха на «кольцо».
Краны №17, №18.
Свечные краны. Служат для стравливания газа из обвязки цеха. При работе цеха краны закрыты. Имеют также четыре способа управления.
Кран №36.
Установлен между всасывающим и нагнетательным шлейфом на перемычке. Предназначен для работы ГПА на большое станционное «кольцо» (через АВО газа). При работе цеха закрыт. Открывают при повышении Р на выходе КЦ, помпаже нагнетателя, для прогрева ПУ и ликвидации гидратных пробок. Управляется дистанционно с ГЩУ, местного щита управления и вручную.
Кран №36Д (дроссельный).
Служит для ограничения потока газа при открытия кр.№36. Создаёт необходимое сопротивление для обеспечения требуемой степени сжатия ГПА. Управление – ручное.
Кран №36Р.
Служит для регулирования режима работы КЦ. При работе цеха закрыт. Управляется дистанционно с ГЩУ, с местного узла управления и вручную.
КРАН №20.
Делит г/п на высокую и низкую сторону, при работе цеха закрыт. Открывается когда КЦ не работает, для прохода газа мимо цеха. Управляется с ГЩУ дистанционно, с места, ручным насосом.
Свечные краны у кр. №20 служат для стравливания газа с м/г до и после кр. №20, а также для заполнения участка газом до и после крана.
Краны №19, 21 (северный и южный охранные краны).
Устанавливаются на подводящем и отводящем уч-ке г/п. Служат для отсечения цеха с двух сторон, при работе цеха открыты, закрываются при аварийной ситуации на КЦ (разрыв обвязки цеха, отказ в закрытии кранов №7;8. Управляется дистанционно с ГЩУ, с местного узла управления, вручную.
|
|
Особенности сооружения опор в сложных условиях: Сооружение ВЛ в районах с суровыми климатическими и тяжелыми геологическими условиями...
Адаптации растений и животных к жизни в горах: Большое значение для жизни организмов в горах имеют степень расчленения, крутизна и экспозиционные различия склонов...
Типы оградительных сооружений в морском порту: По расположению оградительных сооружений в плане различают волноломы, обе оконечности...
История развития пистолетов-пулеметов: Предпосылкой для возникновения пистолетов-пулеметов послужила давняя тенденция тяготения винтовок...
© cyberpedia.su 2017-2024 - Не является автором материалов. Исключительное право сохранено за автором текста.
Если вы не хотите, чтобы данный материал был у нас на сайте, перейдите по ссылке: Нарушение авторских прав. Мы поможем в написании вашей работы!