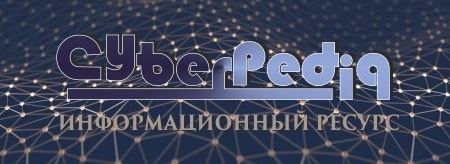
Индивидуальные очистные сооружения: К классу индивидуальных очистных сооружений относят сооружения, пропускная способность которых...
Таксономические единицы (категории) растений: Каждая система классификации состоит из определённых соподчиненных друг другу...
Топ:
Организация стока поверхностных вод: Наибольшее количество влаги на земном шаре испаряется с поверхности морей и океанов...
Техника безопасности при работе на пароконвектомате: К обслуживанию пароконвектомата допускаются лица, прошедшие технический минимум по эксплуатации оборудования...
Теоретическая значимость работы: Описание теоретической значимости (ценности) результатов исследования должно присутствовать во введении...
Интересное:
Что нужно делать при лейкемии: Прежде всего, необходимо выяснить, не страдаете ли вы каким-либо душевным недугом...
Отражение на счетах бухгалтерского учета процесса приобретения: Процесс заготовления представляет систему экономических событий, включающих приобретение организацией у поставщиков сырья...
Искусственное повышение поверхности территории: Варианты искусственного повышения поверхности территории необходимо выбирать на основе анализа следующих характеристик защищаемой территории...
Дисциплины:
![]() |
![]() |
5.00
из
|
Заказать работу |
|
|
Этапы ЧМ:
1) Агломерация — получение шихты (агломерата, поступающего в домну).
2) Производство чугуна.
3) Выплавка и разлив стали.
4) Прокатка.
*** Евраз, НЛМК, Северсталь — комбинаты, то есть имеют собственное производство кокса; г. Старый Оскол — завод работает на ж/р окатышах + теперь на брикетированном железе (технология запатентована в РФ)
Сырьевая база: руда, флюс, топливо, огнеупорный материал.
Производство чугуна. Есть 3 вида: передельный (C в виде химического соединения с Fe; на сталеплавление), литейный (свободный графит; для производства сложных конструкторских элементов типа труб), специальный (переплавка, но на специальные виды стали). Суть процесса: восстановление [принимает электроны] оксидов железа, входящих в состав руды, оксидом углерода CO, водородом Н2 и твердым С, выделяющимися при сгорании топлива в доменной печи. Домна — это вертикальная шахтная печь, выплавляющая чугун и ферросплавы из железорудного сырья и шихты. На 20 тыс. т шихты в сутки производят 12 тыс. т чугуна.
Горение кокса: C + O2 = CO2 +402 кДж
CO2 + C = 2CO – 160 кДж
Восстановление железа: 3Fe2+3O3 + C+2O —> 2Fe3O4 + CO2 +Q
2Fe3O4 + CO —> 3Fe+2O + CO2 – Q
FeO + CO = Fe + CO2 + Q
Твердый C восстанавливает Mn, Si, P, S
Образуются шлаки: CaCO3 (флюс) —> CaO + CO2 – Q
CaO + SiO2 —> CaSiO3
***Фурма — отверстие, через которое подаётся газ. Кокс используют для создания высокой температуры: кокс соединяется с воздухом и сгорает, выделяя CO, H2, C, которые восстанавливают железо из шихты. Домна работает только при непрерывном поступлении воздуха, нагретого до 700°C. Чугунная лётка и шлаковая лётка — то, куда сливаются готовые продукты. Шлаки отправляют на охлаждение и затем грануляцию, впоследствии они идут либо в стройматериалы, либо на подсыпку в горнорудное производство.
|
Сталеплавление. Суть процесса — снизить содержание углерода и других примесей путём их ОКИСЛЕНИЯ и удаления в шлак. 3 способа:
§ Кислородно-конверторный
Залитый в конвертер (плавильный агрегат) чугун продувают снизу воздухом: иногда помимо чугуна также грузят лом (удешевляет производство), далее внутрь опускается кислородная фурма и начинается продувка. Кислород воздуха окисляет примеси чугуна, в результате чего он превращается в сталь. Тепло, выделяющееся при окислении, обеспечивает разогрев стали до 1600°C — главное отличие от остальных способов в том, что не требуется дополнительный подвод тепла. **Конвертор плавит порцию стали в 30–60 мин, может крутится на шарнире, наклоняется. Его ёмкость 100–250 т. № типа конверторов: бессемеровский (кислая футеровка с исп. чугуна с низким содержанием P), томасовский (основная, с высоким Р) и кислородно-конверторный.
§ Электрометаллургия
Здесь основной агрегат — это дуговая печь. Внутрь может загружаться и лом, но основным сырьём являются железорудные окатыши. В чём преимущество? В конверторе после загрузки материала тяжело поменять его состав, а в электродуговой печи можно добавлять что-то в течение самого процесса, поэтому в итоге получают сталь различного состава.
Суть: при опускании электродов в шихту возникает электродуга (электрическая энергия переходит в тепловую), шихта нагревается и начинает плавиться, далее через сливной желоб (в рабочее окно уходят шлаки) отводится готовая сталь: либо по изложницам — чугунным формам, в которых в отдельном помещении происходит охлаждение стали (обдувом холодным воздухом) перед пробой — либо через МНЛЗ: жидкая сталь непрерывно подается в водоохлаждаемую изложницу без дна — кристаллизатор, из нижней части которого вытягивают затвердевший по периферии слиток с жидкой сердцевиной.
Блюминг — крупный обжимной стан, предназначенный для проката из слитков весом от 2,5 т до 20 т заготовок — блюмов, используемых в качестве исходного материала для сортовых станов или как заготовки под ковку и штамповку.
|
Слябинг — тоже крупный обжимной стан, но предназначенный для проката из слитков весом от 8 т до 32 т заготовок — слябов толщиной 60–300 мм и шириной 600–1800 мм.
Блюмы — это заготовки квадратного сечения размером от 150×150 мм до 450×450 мм, для дальнейшей прокатки на заготовочных и сортовых станах.
Слябы — это заготовки плоского сечения толщиной от 50–350 мм и шириной до 2000 мм, для дальнейшей прокатки на листовых станах.
Цветная металлургия
Цветные металлы – группа металлов, отличающихся от железа рядом свойств: антикоррозийностью, способностью образовывать кислотостойкие соединения (преимущественно оксиды), высокой ковкостью.
Производство алюминия
Алюминий – цветной металл, парамагнетик, серебристо белый, легко подвергающийся пластическим дефомациям. Производство отличается трудоемкостью и энергоемкостью. Свойства:
· Оксидная устойчивая пленка
· Низкая плотность
· Стабильность состояния при изменениях температуры.
Качество определяется следующими показателями:
1. Кремниевый модуль (отношение содержания оксидов алюминия к оксидам кремния). Чем выше, тем лучше.
2. Содержание железа в пересчете на оксид железа (II).
3. Содержание серы
4. Содержание карбонатов в пересчете на карбонат-ионы.
Метод получения металлического алюминия — электролиз криолитоглиноземного расплава, то есть электролитическое разложение глинозема (Al2O3), растворенного в электролите (расплавленный криолит (Na3AlF6)). Технологический процесс осуществляется при 950–965°C в электролизных ваннах (электролизерах). В целом процесс разложения глинозема в электролизерах можно представить в виде формул:
Al2O3 + 1,5C ↔ 2Al + 1,5CO2
Al2O3+ 3C ↔ 2Al + 3CO.
Суммарную реакцию можно записать в виде
Al2O3 + x C = 2Al + (3− x)CO2 + (2 x −3)CO
При электролизе на катоде выделяется алюминий, а на аноде — кислород. Алюминий, обладающий большей плотностью, чем исходный расплав, собирается на дне электролизера, откуда его периодически извлекают.
Боксит – алюминиевая руда с содержанием глинозема от 40 до 60 %, используемая также как флюс в черной металлургии. На 4 т боксита приходится 2 т глинозема
Глинозем – результат прокаливания боксита. 2 т глинозема дают 1 т чистового алюминия.
|
Как производят глинозём Al2 O3?
Обычно глинозём — это продукт прокаливания гидроксида алюминия при 1000–1200°C. А вообще существует 2 способа его производства: гидрохимический (выщелачивание по способу Байера: из созданного раствора вытаскиваем полезный компонент) и пирометаллургический (спекание).
***Способы производства глинозема из различных видов сырья (минералов), содержащего алюминий, основаны на получении алюминатных растворов и их свойстве самопроизвольно разлагаться при снижении температуры и концентрации на гидроксид алюминия и щелочь. Прокаливая гидроксид алюминия при температуре 1000 °C — 1200 °C, получают глинозем.
Способ Байера. Этим способом обрабатывают только высокосортные бокситы с малым содержанием кремнезёма (кремниевый модуль = Al2O3/SiO2 >6). Этапы производства глинозёма:
§ Подготовка шихты (дробление и измельчение боксита, мокрый размол, выдержка сырой пульпы, получаем хорошую шихту)
§ Процесс выщелачивания, то есть обработки щелочно-алюминатным раствором, в результате чего из боксита извлекаются оксиды алюминия Al2O3, переходящий в раствор с концентрацией 250–300 г/л.
При этом в осадок выпадают нерастворимые соединения — красный шлам. **Последующие процессы производства связаны с отделением и очисткой алюминатного раствора от красного шлама и промывкой последнего для более полного извлечения алюминатного раствора.
§ Сгущение и промывка красного шлама (для полного извлечения алюминатного раствора) и выделение Al(OH)3 (не выделившийся остаток раствора — оборотный раствор возвращается на стадию создания пульпы)
§ Шлам — в отвалы, а Al(OH)3 подвергается кальцинации — нагреванию до высоких температур (1000–1200°C) с целью удаления летучих примесей или для окисления и придания хрупкости => получаем глинозём
Способ спекания (+ существует комбинированный). Этим способом обрабатываются бокситы с кремниевым модулем <6 и другие виды высококремнистого сырья (нефелины, алуниты, каолины). Суть процесса: за счёт термической обработки смеси алюмосиликатной руды с известняком происходит переход всего оксида алюминия из сырья в растворимую форму в спеке — алюминат натрия, связывание оксида кремния в нерастворимое соединение — двукальциевый силикат. Проще говоря, мы хотим связать Si в малорастворимые соединения путём спекания, чтобы на стадии выщелачивания вывести его из процесса.
|
Метод Байера – щелочно-гидрохимический способ получения глинозема. Шихта из боксита, извести и воды выщелачивается, а затем кальцинируется. Отходы: пыль на этапе создания шихты, шлаки после выщелачивания, красный шлам
Электролиз – физико-химический процесс выделения на электродах составных частей растворов или расплавов. Ключевой способ получения чистового алюминия из глинозема. Энергозатраты в целом на производство алюминия:
Производство первичного алюминия. Первичный алюминий получают в результате электролитического восстановления глинозёма, растворённого в расплавленном электролите (криолите Na3AlF6), при 950–960°C. Электролизёр — это ванна с расплавленным криолитом, дно которой является углеродным катодом, изолированным по внутренней поверхности огнеупорными кирпичами. Углеродные аноды, прикреплены к электропроводящей анодной балке, погружаемой в раствор.
Электролизеры соединены последовательно и образуют серию электролизеров. Постоянный ток подается с анодов через электролит и слой металла на катод, а затем — по комплекту проводников, известных как «ошиновка», на следующий электролизер. Жидкий алюминий оседает на катоде электролизера. Расплавленный металл периодически извлекается из электролизеров специальными ковшами и передается в литейное отделение для получения товарной продукции. В процессе электролиза кислород O2 из глинозема реагирует с углеродным анодом и образует CO2 и CO. Таким образом, в ходе этого процесса происходит непрерывный расход углеродных анодов. Глинозём в электролизёр добавляют сверху постепенно и постоянно.
Расход на 1 кг алюминия:
o 2 кг глинозёма
o 0,5 кг угля
o 15 кВт*ч электроэнергии
**Фторирование глинозёма — отработанный после «сухой очистки» электролизных газов глинозём возвращается в электролиз в качестве сырьевого компонента.
Сырьевая база: глинозём, криолит, углеродные аноды.
Производство меди
Медь – цветной металл, применяемый как в чистом виде, так и в сплавах для создания ювелирной продукции, проводов, кабелей и иной продукции. Часто металл сопровождается примесями в т. ч. других ценных металлов, поэтому распространено комбинирование с аффинажными производствами золота.
Уникальные свойства: высокие тепло- и электропроводность, ковкость, хорошие литейные качества, большого сопротивления на разрыв. Около 40 % всей меди идёт на изготовление проводов и кабелей. Медь широко используют в таких отраслях, как тяжелое машиностроение, электротехника, ювелирка.
|
Латунь – до 45 % Zn, а также в специальные латуни добавляют Fe, Al, Sn, что повышает их коррозионную стойкость и обусловливает применение в судостроении, для художественной ковки, втулок, сепараторов.
Томпак – сплав меди и цинка с повышенным содержанием меди (до 75 %). Применяется в ювелирной промышленности.
Медно-никелевые сплавы: мельхиор (20–35 % Ni, а также Fe и Mn), нейзильбер (5–35 % Ni и 13–45 % Zn) — конструкционные материалы в энергетике и судостроении. Константан (40 % Ni и 1,5% Mn) и манганин (3 % Ni и 12 % Mn) — низкий температурный коэффициент электрического сопротивления.
Штейн –сплавы сульфидов гл. обр. Cu2S и FeS — суммарная концентрация меди, железа и серы достигает 90 %, остальное — сульфиды Zn, Pb, Ni, а также оксиды железа, кремния, алюминия и кальция, увлеченные из шлака и растворенные в штейне. Максимальная концентрация меди в штейне — 79,9 % (чистый Cu2S), в среднем 30–40 %. Самые богатые штейны в Чили (65 % Cu), в России 35–45 %.
Файнштейн – промежуточный продукт пирометаллургической фазы получения меди, результат конвертирования штейнов. Отход производства – хвосты (красные ожелезненные). [по сути, дважды обогащенная медь]
Хвост – пустая порода, отход обогащения, включающий легкие части руды, уносимые при промывке водой.
Анодная медь – результат огневого рафинирования конвертированного штейна или файнштейна. Содержит до 0,16 % фосфора.
Катодная медь – результат электролитического рафинирования анодной меди, выпускаемый в виде листов из меди повышенной чистоты. Отходы производства: электролит (комбинирование с производством кислот), шлаки.
Производство меди включает в себя 4 стадии:
1) Первичное обогащение (флотация) —> на выходе концентрат и хвосты (естественно, содержащие Cu, но в небольших долях)
*** обжигом можно заранее удалить часть Fe и S (за счет окисления)
2) Плавка на штейн (900–1300°C): Cu2O + FeS = Cu2S + FeO
2FeO + SiO2 (флюс для ускорения реакции) = Fe2SiO4 переходит в шлак
Штейн и шлак — полупродукты пирометаллургии меди.
Шлак — это отвальный или побочный продукт, связанный по большей части с содержанием оксидов железа, кремния, малого содержания меди.
Покупают хорошие кварцевые флюсы, чтоб продать шлаки на извлечение
3) Конвертирование — продувка горячим воздухом => на выходе черновая медь.
Cu2S + O2 = Cu2O + SO2
Cu2S + 2Cu2O = 6Cu + SO2 (газ отводится на производство серной кислоты)
4) Рафинирование — получение чистого продукта (медь анодная — огневым рафинированием и медь катодная — электролитическим + электролит идёт на производство медного купороса + шламы на извлечение Au, Ag, Se, Te)
Огневое рафинирование. Примеси окисляются воздухом, продуваемым через ванну: сначала окисляет медь, затем оксид меди окисляет растворенные в ванне примеси:
4Cu + O2 = 2Cu2O
Me + Cu2O = MeO +2Cu
Me + 0,5O2 = MeO
Электролитическое рафинирование. Суммарная концентрация примесей в анодной меди достигает 0,5 %. В процессе электролиза анодная медь растворяется по схеме:
Cu0 – 2e = Cu2+
Cu 2+ + 2e = Cu0
Из электролитной меди производят вайербасы — заготовки с заостренными краями (из очищенной электролитной меди), катанку — это заготовка, получаемая в результате непрерывного литья расплавленной меди и последующей прокатки.
Схема производства меди
|
|
Своеобразие русской архитектуры: Основной материал – дерево – быстрота постройки, но недолговечность и необходимость деления...
Двойное оплодотворение у цветковых растений: Оплодотворение - это процесс слияния мужской и женской половых клеток с образованием зиготы...
Автоматическое растормаживание колес: Тормозные устройства колес предназначены для уменьшения длины пробега и улучшения маневрирования ВС при...
Таксономические единицы (категории) растений: Каждая система классификации состоит из определённых соподчиненных друг другу...
© cyberpedia.su 2017-2024 - Не является автором материалов. Исключительное право сохранено за автором текста.
Если вы не хотите, чтобы данный материал был у нас на сайте, перейдите по ссылке: Нарушение авторских прав. Мы поможем в написании вашей работы!