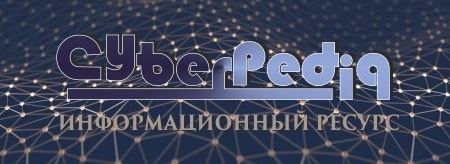
История развития пистолетов-пулеметов: Предпосылкой для возникновения пистолетов-пулеметов послужила давняя тенденция тяготения винтовок...
История развития хранилищ для нефти: Первые склады нефти появились в XVII веке. Они представляли собой землянные ямы-амбара глубиной 4…5 м...
Топ:
Генеалогическое древо Султанов Османской империи: Османские правители, вначале, будучи еще бейлербеями Анатолии, женились на дочерях византийских императоров...
Характеристика АТП и сварочно-жестяницкого участка: Транспорт в настоящее время является одной из важнейших отраслей народного хозяйства...
Техника безопасности при работе на пароконвектомате: К обслуживанию пароконвектомата допускаются лица, прошедшие технический минимум по эксплуатации оборудования...
Интересное:
Искусственное повышение поверхности территории: Варианты искусственного повышения поверхности территории необходимо выбирать на основе анализа следующих характеристик защищаемой территории...
Инженерная защита территорий, зданий и сооружений от опасных геологических процессов: Изучение оползневых явлений, оценка устойчивости склонов и проектирование противооползневых сооружений — актуальнейшие задачи, стоящие перед отечественными...
Финансовый рынок и его значение в управлении денежными потоками на современном этапе: любому предприятию для расширения производства и увеличения прибыли нужны...
Дисциплины:
![]() |
![]() |
5.00
из
|
Заказать работу |
|
|
При производстве деталей встречаются три различных метода
получения и измерения размеров и угловых величин: цепной, коорди- натный и комбинированный.
Сущность цепного метода заключается в том, что каждый по- следующий размер (или угловая величина) получаются или измеря- ются вслед за ранее полученными или измеренными. Причем для это- го в качестве одной из технологических или измерительных баз ис- пользуется связывающая их общая поверхность. Таким образом, при получении каждого последующего звена происходит переход к новой технологической базе и тем самым исключается влияние погрешно- стей предшествующих звеньев на погрешность вновь получаемого звена. Следовательно, погрешность, образующаяся на каждом цепном звене, зависит только от особенностей той технологической операции, в результате которой образуется (получается) данное звено. Поэтому, основным преимуществом цепного метода получения размеров дета- лей, является независимость точности изготовления каждого из звеньев цепи от погрешностей остальных звеньев.
Сущность координатного метода заключается в том, что все размеры детали получаются и измеряются от одной и той же выбран- ной базы, независимо один от другого. Вследствие этого, погреш- ность, получаемая на каждом из координатных звеньев, является следствием особенностей той технологической операции, в результа- те выполнения которой образуется данное координатное звено. Таким образом, погрешность каждого из координатных звеньев не зависит от погрешностей других координатных звеньев - это первое преиму- щество данного метода.
Из рис. 7.6 видно, что при цепном методе получение линейных
|
размеров А1, А2, А3, А* ступенчатого валика каждый его координат- ный размер Б1, Б*, Б3, определяющий положение торцевых поверх- ностей 1, 2, 3 относительно единой измерительной базы, представляет собой замыкающее звено размерной цепи, составляющими звеньями которой являются соответствующие цепные размеры. Например, ко- ординатный размер Б3 является замыкающим звеном размерной цепи - Б3=А*+А2+А3.
В соответствии с этим, погрешности, получаемые на каждом ко- ординатном размере при цепном методе получения размеров, будут равны: ∆Б3=∆А1+∆А2+∆А3.
Эти погрешности координатных размеров при прочих равных
условиях возрастают по мере увеличения количества цепных звеньев, составляющих этот координатный размер.
Погрешности же, измеряемые на каждом цепном звене при ис- пользовании координатного метода получения размеров, зависят от погрешностей только двух координатных звеньев, образующих дан- ное цепное звено это второе преимущество координатного метода. Например, цепные размеры А2 и А4 представляют собой замыкаю-
щие звенья размерной цепи
А2=Б2-Б1, А*=Б4-Б3.
В соответствии с этим погрешности цепных звеньев определя-
ются по формулам
∆А*=∆Б2+∆Б1, ∆А4=∆Б*+∆Б3.
Сопоставление обоих рассмотренных методов получения разме-
ров показывает, что использование при обработке деталей координат- ного метода, в силу присущих ему особенностей, позволяет получать, как правило, более высокую точность. К этому добавляется еще одно преимущество координатного метода, заключающееся в том, что при нем погрешность установки детали остается постоянной при получе- нии всех координатных звеньев.
Вследствие этих преимуществ координатный метод получил широкое использование в технологической практике.
Сущность комбинированного метода заключается в том, что при изготовлении детали для получения одних звеньев используется координатный метод, а для других - цепной метод. При этом для по- лучения звеньев, определяющих относительные повороты поверхно- стей (параллельные, перпендикулярные и другие угловые величины относительного расположения поверхностей) и большую часть разме- ров, преимущественно используют координатный метод.
|
Цепной метод используется, главным образом в тех случаях, ко- гда на отдельных размерах требуется обеспечить очень высокую точ- ность или когда погрешность установки, связанная со сменой техно- логических баз, относительно невелика, или когда использование ко- ординатного метода дает на надлежащем цепном звене погрешность, больше установленного допуска.
Способы простановки основных размеров на рабочих чертежах
деталей.
В большинстве случаев при конструировании стремятся обеспе- чить наиболее точные сопряжения и взаимные расположения деталей относительно друг друга в механизмах машины. С этой точки зрения предпочтительнее является простановка размеров на рабочих черте- жах деталей и на операционных эскизах от одной базы, т.к. при этом обеспечивается наибольшая точность взаимного расположения по- верхностей при экономически обоснованных допусках. Однако в ряде случаев приходится отступать от этого правила. Например, если важ- нее определенности координации какой-либо поверхности оказывает- ся определенность ее размеров, то прибегают к цепной простановке размеров.
28. Принципы совмещения баз, постоянства баз и смены баз
Принцип совмещения баз. Известно, что точность размера обраба-
тываемой поверхности, ее форма, шероховатость в основном зависят от метода обработки, тогда как точность расположения этой поверхности, т.е. точность размера, координирующего поверхность, зависит, прежде всего, от положения, которое занимает заготовка детали на станке. От- сюда следует, что выбор комплекта баз заготовки непосредственно свя- зан с задачей обеспечения заданной точности взаимного расположения поверхностей детали. В связи с этим при выборе баз следует придержи- ваться следующего правила.
При разработке операций технологического процесса в качестве технологических баз следует принимать те поверхности детали, относи- тельно которых на рабочем чертеже координировано положение обра- батываемой поверхности, т.е. поверхности, которые одновременно яв- ляются конструкторскими и (или) измерительными базами. Это правило известно под названием «принципа совмещения технологической базы с конструкторской (измерительной)».
|
Отступление от этого принципа приводит к тому, что точность расположения обработанной поверхности относительно конструктор- ской базы становится зависимой не только от точности установки, но и от точности расположения конструкторской базы относительно поверх- ности, принятой в качестве технологической базы. Возникает дополни- тельная погрешность - погрешность от не совмещения баз, которая не имеет отношения ни к методу обработки, ни к точности приспособления и вызывается только нарушением рассматриваемого принципа выбора
баз.
Принцип единства (постоянства) баз. Переход от одной техноло- гической базы к другой всегда вносит дополнительную ошибку во вза- имное расположение поверхностей, обработанных от разных баз. Размер этой ошибки зависит от величины погрешности во взаимном располо- жении обеих баз. Поэтому без серьезных оснований менять базы не сле- дует, т.е. предпочтительнее производить обработку основных поверхно- стей от одной и той же технологичной базы. Это правило получило на- звание «принципа постоянства баз». Постоянство базы весьма упроща- ет установление всех зависимостей во взаимном расположении обрабо- танных поверхностей, расчет операционных припусков и размеров и т.п.
Большей частью в качестве постоянной базы используются окон- чательно обработанные поверхности - установочные технологические базы, стремясь выдерживать и принцип совмещения баз.
Принцип смены баз. Анализ чертежа детали показывает, что не всегда возможно использовать принцип совмещения баз. В таких случаях приходится выполнять смену баз, т.е. в качестве технологи- ческих баз использовать не конструкторские, а операционные базы. Причем, под операционной базой будем понимать такую технологи- ческую базу, по отношению к которой непосредственно не координи- руется исходя из чертежа детали обрабатываемая поверхность.
Использование операционных баз, как правило, требует ужесто- чения (уменьшения) допусков, определяющих точность положения операционной базы относительно технологической базы, для которой соблюдается принцип совмещения баз (т.е. совмещение технологиче- ской и конструкторской баз).
Избежать чрезмерного ужесточения допусков можно двумя метода-
ми:
- использованием в качестве операционных баз поверхностей за- готовки детали, которые позволяют получить меньшую величину по-
грешности от не совмещения баз;
- созданием у заготовки детали искусственных технологических баз.
Характерными примерами искусственных технологических баз являются: центровые отверстия валов; два цилиндрических отверстия у корпусных деталей при установке заготовки на плоскость и два пальца и т.п.
|
|
Историки об Елизавете Петровне: Елизавета попала между двумя встречными культурными течениями, воспитывалась среди новых европейских веяний и преданий...
Архитектура электронного правительства: Единая архитектура – это методологический подход при создании системы управления государства, который строится...
Индивидуальные очистные сооружения: К классу индивидуальных очистных сооружений относят сооружения, пропускная способность которых...
Автоматическое растормаживание колес: Тормозные устройства колес предназначены для уменьшения длины пробега и улучшения маневрирования ВС при...
© cyberpedia.su 2017-2024 - Не является автором материалов. Исключительное право сохранено за автором текста.
Если вы не хотите, чтобы данный материал был у нас на сайте, перейдите по ссылке: Нарушение авторских прав. Мы поможем в написании вашей работы!