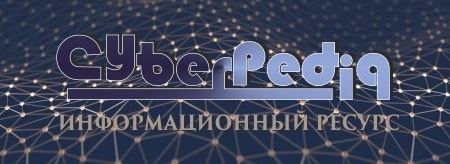
Поперечные профили набережных и береговой полосы: На городских территориях берегоукрепление проектируют с учетом технических и экономических требований, но особое значение придают эстетическим...
История развития хранилищ для нефти: Первые склады нефти появились в XVII веке. Они представляли собой землянные ямы-амбара глубиной 4…5 м...
Топ:
Методика измерений сопротивления растеканию тока анодного заземления: Анодный заземлитель (анод) – проводник, погруженный в электролитическую среду (грунт, раствор электролита) и подключенный к положительному...
Марксистская теория происхождения государства: По мнению Маркса и Энгельса, в основе развития общества, происходящих в нем изменений лежит...
Интересное:
Финансовый рынок и его значение в управлении денежными потоками на современном этапе: любому предприятию для расширения производства и увеличения прибыли нужны...
Аура как энергетическое поле: многослойную ауру человека можно представить себе подобным...
Наиболее распространенные виды рака: Раковая опухоль — это самостоятельное новообразование, которое может возникнуть и от повышенного давления...
Дисциплины:
![]() |
![]() |
5.00
из
|
Заказать работу |
|
|
Станок может настраиваться двумя способами:
1) по пробным деталям (более трудоемкая); *) по эталонам (менее трудоемкая).
В некоторых случаях необходимо отводить инструмент от обра- батываемой заготовки и затем вновь ставить его в прежнее положе- ние, что производиться при помощи жестких или индикаторных упо- ров. Для обычных условий погрешность установки по жесткому упо- ру составляет 20¼50 мкм. При малой жесткости упора и низкой ква- лификации рабочего погрешность установки может возрасти до 100¼130 мкм. Погрешность установки по индикаторным упорам зна- чительно меньше и лежит в пределах 10¼20 мкм.
Выводы:
Настройка по пробным деталям обеспечивает высокую точ-
ность, но трудоемка. В условиях массового производства при обра- ботке на автоматах и многоинструментных станках на настройку за- трачивается до 20% общего фонда времени. Недостаток - брак дета- лей, что неприемлемо для крупных и дорогих изделий. Метод на- стройки по пробным деталям находит применение для станков с от- носительно простой наладкой и при небольших размерах обрабаты- ваемых деталей.
Настройка по эталонам менее трудоемка, что обеспечивает бо- лее полное использование оборудования во времени. Она дает надеж- ные и стабильные результаты в отношении точности и исключает расход пробных деталей. Особенно целесообразна для операций об- работки с многоинструментым оснащением, т.к. настройка по эталону не связана с использованием наладчиков высокой квалификации и может производиться вне станка при наличии сменных инструмен- тальных блоков, суппортов и револьверных головок.
Износ инструмента
В процессе работы инструмент изнашивается, как по передней,
|
так и по задней граням.
Износ протекает следующим образом. По передней поверхности износ в основном связан со стойкостью инструмента, а по задней и с точностью обработки. Резец, изношенный по задней грани на 0,1 мм продолжает работать, хотя получаемые размеры существенно отли- чаются от заданного. При обработке детали значительного размера, износ инструмента сказывается и на точности формы. Наибольшее влияние на величину размерного износа инструмента оказывает ско- рость резания, подача, глубина резания и задний угол. Величина из-
носа, влияющая на точность обработки, определяется по формуле
* L l доп Uo
1**0
где L - длина пути резания, в м; Lдоп - дополнительный путь в м (для
доведенного инструмента 500 м.; для заточенного инструмента 1500
м.; если работа идет на участке нормального износа режущего инст-
румента (*b) (рис. 5.33) то Lдоп =*); U* - величина относительного
(удельного) износа.
При обработке детали методом пробных проходов и промеров размерный износ инструмента не оказывает влияния на точность раз- меров.
2 Повышение доводки его режущих кромок для сокращения
величины первоначального износа (участок * -a).
3 Стабилизация сил резания.
4 Сокращение вибрации в системе СПИД, если это не виброре-
зание.
5 Выбор наиболее экономичных режимов обработки.
6 Своевременная смена инструмента для его переточки. * Правильный подбор применяемой СОЖ.
8 Своевременная компенсация размерного износа инструмента
путем поднастройки размерных цепей системы СПИД.
9 Правильная установка и закрепление инструмента с учетом изменения его геометрии при возникновении силы резания и упругих перемещений.
Несколько иные условия возникают при работе абразивным ин- струментом, т.к. в этом случае износ может быть как положительным, так и отрицательным явлением и, следовательно, износ должен учи- тываться, как один из основных технологических факторов.
Износ инструмента оказывает на точность и косвенное влияние
|
т.к. по мере увеличения износа увеличивается сила Рv, следовательно,
возрастают деформации технологической системы СПИД. В процессе
работы температурный режим системы СПИД меняется, происходит нагрев станка, режущего инструмента, обрабатываемой детали, на- грев связанный с измерениями.
Температурные деформации
В процессе работы температурный режим системы СПИД меня-
ется. Нагревание станка вызвано в основном действиям трения в подшипниках и направляющих, а также теплотой, идущей от встро- енных электродвигателей, от охлаждающей жидкости и гидросисте- мы. Нагревание станины, корпусных деталей и других частей станка происходит неравномерно. Так, разность температур отдельных эле-
ментов станицы может быть до 10С, в различных точках корпуса бабки - от 10 до 50С, температура валов и шпинделей на 3*-40%
выше средней температуры корпусных деталей, в которых они смон- тированы.
Относительно сильный нагрев шпиндельных бабок влечет за со- бой изменение положения оси шпинделя. Большое влияние на точ- ность обработки оказывают тепловые деформации винтов подач. Поэтому винты делают по возможности меньшей длины (для перемеще-
ния бабки шлифовальных станков).
Нагревание режущего инструмента, при резании в некоторых случаях может иметь существенное значение. При обработке крупной заготовки тепловые деформации резца могут вызвать погрешность формы обрабатываемой поверхности. Тепловые деформации влияют на точность размеров при обработке на предварительно настроенных станках по методу автоматического получения размеров, но могут быть учтены рабочим при обработке методом пробных проходов и промеров.
Внутренние напряжения
Внутренние напряжения оказывают наибольшее влияние на
точность обработки нежестких тонкостенных заготовок, а также крупных точных деталей (рамы, станины). Внутренними остаточными называют напряжения, которые существуют в заготовке или готовой детали при отсутствии внешних нагрузок. Остаточные напряжения полностью уравновешиваются и их действие на деталь с внешней стороны ничем не проявляется. По причине образования остаточные
напряжения делятся на две группы:
1 Конструкционные - вызываются процессами, происходящи-
ми в конструкции.
2 Технологические - возникающие в процессе изготовления.
В зависимости от применяемого технологического метода оста-
точные напряжения бывают:
1 литейные - возникающие при остывании отливок;
2 ковочные - образуются в поковках и горячих штамповках;
3 термические;
4 сварочные;
5 от наклепа, возникающие при прокатке, холодной штампов-
ке, чеканке и т.д.
|
|
Архитектура электронного правительства: Единая архитектура – это методологический подход при создании системы управления государства, который строится...
Типы сооружений для обработки осадков: Септиками называются сооружения, в которых одновременно происходят осветление сточной жидкости...
Двойное оплодотворение у цветковых растений: Оплодотворение - это процесс слияния мужской и женской половых клеток с образованием зиготы...
Наброски и зарисовки растений, плодов, цветов: Освоить конструктивное построение структуры дерева через зарисовки отдельных деревьев, группы деревьев...
© cyberpedia.su 2017-2024 - Не является автором материалов. Исключительное право сохранено за автором текста.
Если вы не хотите, чтобы данный материал был у нас на сайте, перейдите по ссылке: Нарушение авторских прав. Мы поможем в написании вашей работы!