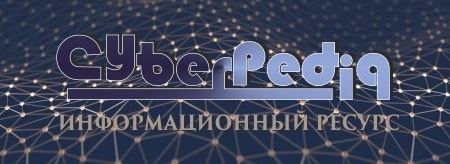
Семя – орган полового размножения и расселения растений: наружи у семян имеется плотный покров – кожура...
Опора деревянной одностоечной и способы укрепление угловых опор: Опоры ВЛ - конструкции, предназначенные для поддерживания проводов на необходимой высоте над землей, водой...
Топ:
Методика измерений сопротивления растеканию тока анодного заземления: Анодный заземлитель (анод) – проводник, погруженный в электролитическую среду (грунт, раствор электролита) и подключенный к положительному...
Основы обеспечения единства измерений: Обеспечение единства измерений - деятельность метрологических служб, направленная на достижение...
Марксистская теория происхождения государства: По мнению Маркса и Энгельса, в основе развития общества, происходящих в нем изменений лежит...
Интересное:
Принципы управления денежными потоками: одним из методов контроля за состоянием денежной наличности является...
Мероприятия для защиты от морозного пучения грунтов: Инженерная защита от морозного (криогенного) пучения грунтов необходима для легких малоэтажных зданий и других сооружений...
Средства для ингаляционного наркоза: Наркоз наступает в результате вдыхания (ингаляции) средств, которое осуществляют или с помощью маски...
Дисциплины:
![]() |
![]() |
5.00
из
|
Заказать работу |
|
|
Заготовки
Выбор метода получения заготовки определяется:
- технологической характеристикой материала детали, т.е. ли-
тейными свойствами и способностью претерпевать пластические де- формации при обработке давлением, а также структурными измене- ниями материала заготовки, получаемыми в результате применения того или иного метода выполнения заготовки (расположение волокон
в поковках, величина зерна в отливках и пр.);
- конструктивными формами и размерами заготовки;
- требуемой точностью выполнения заготовки, шероховатостью
и качеством ее поверхностных слоев;
- величиной объема выпуска и временем, на которое рассчитано выполнение этого задания.
На выбор метода выполнения заготовки оказывает также боль- шое влияние время подготовки технологической оснастки (изготов- ление штампов, моделей, пресс-форм и пр.), наличие соответствую- щего технологического оборудования и желаемая степень автомати- зации процесса. Причем, выбранный метод должен обеспечить наи- меньшую себестоимость изготовления детали, т.к. с повышением точности заготовки объем механообработки снижается. Однако при малом объеме выпуска не все методы могут оказаться рентабельными из-за того, что расходы на оснастку для заготовительных процессов экономически не окупаются.
Зная технологические характеристики заготовительных методов можно отобрать сравнительно небольшое количество методов, удов- летворяющих поставленным условиям. Окончательный выбор метода должен производиться на основе экономических расчетов.
При получении заготовок литьем или пластическим деформиро-
ванием предварительно устанавливают:
- припуски на обработку;
|
- допуски на размеры обрабатываемых и черновых поверхно-
стей;
- базовые поверхности первой операции механообработки и тре-
бования, предъявляемые к этим поверхностям;
- термообработку заготовок (если она нужна) и требования к структуре и твердости материала с точки зрения его обрабатываемо-
сти;
- метод очистки поверхностей заготовки;
- методы предварительной обработки заготовок (обдирка, зачи-
стка, зацентровка и т.д.).
При изготовлении заготовок из сортового материала листа уста- навливают профиль и размеры прутка или толщину листа исходя из необходимых величин припусков на обработку и размеров детали.
Контроль качества заготовок предусматривает: выявления по- роков материала внешним осмотром черновых и предварительно об- работанных поверхностей, проверку размеров заготовок и, в случае необходимости, проверку физических и механических свойств мате- риала и его химического состава.
Выбор баз для изготовления детали имеет целью наметить как сами базы, так и порядок их смены (если необходимо) при выполне- нии технологического процесса механической обработки детали. Ис- ходными данными при выборе баз являются: рабочий чертеж детали, вид заготовки, а также желаемая степень автоматизация процесса. При выборе баз учитываются условия работы детали в механизме. Принятая схема базирования определяет конструктивные схемы при- способлений и влияет на точность размеров и на точность взаимного положения поверхностей деталей. Наилучшие результаты по точно- сти обработки обеспечиваются при выдерживании принципа совме- щения баз. В этом случае погрешности базирования равны нулю. При невозможности выдержать данный принцип за базу принимают дру- гую поверхность, стремясь уменьшить нежелательные последствия от не совмещения баз.
При выборе баз должны быть сформулированы требования по точности и шероховатости их обработки, а также предусмотрена не- обходимость (если требуется) повторной их обработки в целях ликви- дации возможной деформации от действия остаточных напряжений в материале заготовки. Выбор баз связан с первой наметкой плана об- работки детали, который подвергается дальнейшей детализации на последующих этапах проектирования технологического процесса.
|
Выбор маршрута обработки отдельных поверхностей детали производят исходя из требований рабочего чертежа и принятой заго- товки. По заданному квалитету точности и шероховатости поверхностей детали и с учетом ее размера, веса и конфигурации выбирают
один или несколько возможных методов окончательной обработки, а также тип соответствующего оборудования. Зная вид заготовки, та- ким же образом решается вопрос о выборе первого метода обработки (маршрута). Если, например, точность заготовки не высока, то обра- ботку данной поверхности начинают с использования предваритель- ного (черного) метода. При точной заготовке сразу можно начинать чистовую, а в некоторых случаях и отделочную обработку.
Базируясь на завершающем и первом методах маршрута, уста- навливают промежуточные методы. При этом исходят из того, что каждому методу окончательной обработки предполагается один или несколько возможных предшествующих методов. Так, например, чис- товому развертыванию отверстия предшествует предварительное, а предварительному - чистовое зенкерование или сверление. При по- строении маршрута исходят из того, что каждый последующий метод должен быть точнее предыдущего. Технологический допуск на про- межуточный размер и качество поверхности, полученные на преды- дущем методе, должны находиться в тех пределах, при которых воз- можно нормальное использование намечаемого последующего метода обработки. Так, нельзя после чернового растачивания применять чис- товое развертывание, из-за большой глубины резания. Поэтому выбор маршрута обработки поверхности связан с установлением припусков на эту поверхность.
Количество возможных вариантов маршрута обработки данной поверхности может быть довольно большим. Не все они, однако, рав- ноценны по эффективности и рентабельности. Выбор окончательного варианта по этим показателям сложен и трудоемок. Решение данной задачи может быть облегчено разработкой соответствующих норма- тивов для выбора типовых маршрутов.
Количество вариантов часто можно сокращать с учетом ряда практических соображений. К их числу можно отнести необходи- мость обработки данной поверхности на одном станке за несколько последовательных переходов; ограничение возможности применения других методов обработки при недостаточной жесткости детали; не- обходимость обработки данной поверхности совместно с другими по- верхностями и другими требованиями местного характера.
|
7.4.4 Составление маршрута изготовления детали в целом
Составление маршрута представляет сложную задачу с большим
количеством вариантов решения. Его цель - дать общий план обра-
ботки, наметить содержание операций технологического процесса и
выбрать тип оборудования. Для решения этой задачи могут быть да- ны следующие рекомендации.
План технологического процесса изготовления детали делится
на ряд операций, преследующих определенное целевое назначение.
1. Подготовительные операции или подготовительная стадия обработки - это операции, на которых выполняется обработка, на- правленная на подготовку заготовки к правильной установке и вы- полнению основных операций, т.е. ведется обработка чистовых тех- нологических баз.
2. Основные или решающие операции - это операции, в которых осуществляется съем основной массы металла, детали придается ос- новная форма и выявляются дефекты заготовки (раковины, волосови- ны, недоливы металла и т.п.). В основных операциях обрабатываются основные рабочие поверхности, определяющие целевое назначение детали. Это черновая и получистовая обработка поверхностей. Одна- ко в целях своевременного выявления брака помимо черновой обра- ботки иногда делают и сразу чистовую обработку тех поверхностей, на которых дефекты не допустимы. Основные операции характери- зуются большими силами резания, деформациями, повышением тем- пературы, перераспределением внутренних напряжений, и, как след- ствие, невысокой точностью обработки. Поэтому для повышения точности обработки вводятся чистовые операции. Однако перед ними зачастую вводится ряд промежуточных операций.
3. Операции для снятия внутренних напряжений - это термиче- ские или операции старения. Они не всегда являются обязательными и зависят от степени точности, предъявляемой к изготовленной дета- ли и конфигурации последней.
|
4. Промежуточные операции вводятся после основных и назна- чения их - это обработка поверхностей, в большей части не опреде- ляющих целевое назначение обрабатываемой детали. Это сверление и расточка различных отверстий и т.п.
5. Исправление баз. Эти операции вводятся в случае потери точ- ности технологических баз из-за всевозможного деформирования ме- талла, в том числе, и после термообработки (закалки), на базовых по- верхностях.
6. Чистовые операции. В этих операциях производится обработ- ка основных поверхностей обрабатываемых деталей. Если не требует- ся высокой точности и малой шероховатости поверхности, то такие
операции могут быть и заключительными.
7. Доводочные операции или заключительные - это операции направленные на доведение основных поверхностей до заданной точ- ности и, в основном, шероховатости.
При необходимости в термической обработке (закалка), послед- няя вводится между основными и чистовыми операциями. Термооб- работка как бы расчленяет технологический процесс на две части. После нее зачастую требуется не только исправление баз, но и по- вторная обработка отдельных поверхностей для обеспечения задан- ной точности и шероховатости.
Последовательность обработки в определенной степени зависит и от способа простановки размеров. Так, в первую очередь рекомен- дуется обрабатывать ту поверхность, относительно которой на черте- же координировано большее количество других поверхностей детали. Приведенная схема составления маршрута обработки детали является принципиальной и часто возможны отступления, диктуемые какими- либо технологическими причинами. Так, во многих случаях дополни- тельные операции не могут выполняться до чистовых, в других - точ- ная обработка некоторых поверхностей требуется для создания на- дежных баз, которые обрабатываются с высокой точностью и т.п.
7.4.5 Построение операций механической обработки
Для проектирования отдельной операции необходимо знать:
- схему ее базирования и закрепления,
- какие поверхности и с какой точностью нужно обрабатывать,
- какие поверхности и с какой точностью были обработаны на
предшествующих операциях,
- припуск на обработку,
- величину такта выпуска, если операция проектируется для по-
точной линии.
При проектировании операции уточняется ее содержание, уста- навливается последовательность и возможность совмещения перехо- дов во времени, выбирается оборудование, инструменты и приспо- собления (или дается задание на их проектирование), назначаются режимы резания, определяется норма времени на выполнение опера- ции, устанавливаются настроечные размеры, а также составляется схема наладки. Проектируя операцию в любом ее варианте, технолог
|
стремится к уменьшению величины штучного времени Тшт. При по-
точном методе работы Тшт увязывается с тактом выпуска, и оно
должно быть таким, чтобы обеспечивалась заданная производитель-
ность поточной линии.
В общем случае величина штучного времени (Тшт) определяется
из следующей зависимости
Тшт = То + Тв + Торг + Тн = Топ + Тдоп,
где То - основное (машинное) время, Тв - вспомогательное время, Торг - время организационно-технического обслуживания станка, Тн - время на отдых и личные надобности, Топ - оперативное время, равное сумме основного и вспомогательного времени, Тдоп - дополнительное время, равное сумме Торг и Тн.
При этом элементы дополнительного времени определяются
практически во всех нормативах в виде величины процента от опера- тивного времени. Поэтому для уменьшения штучного времени необ- ходимо стремится в первую очередь к уменьшению величин основно- го и вспомогательного времени.
Продолжительность элементов основного времени сокращается в результате применения высокопроизводительных режущих инстру- ментов и режимов резания, сокращения числа проходов и переходов при обработке поверхностей. Величина вспомогательного времени сокращается за счет уменьшения времени холостого хода станка и применения наиболее современных установочных приспособлений с быстродействующими зажимами.
Наряду с уменьшением продолжительности каждого элемента
Топ прибегают к совмещению элементов основного и вспомогательно-
го времени.
В этом случае в состав штучного времени входят лишь наиболее продолжительные элементы времени из числа всех совмещаемых. Возможности такого совмещения зависят от схемы построения ста- ночной операции.
Возможности перекрытия элементов Топ при выполнении ста-
ночных операций зависит от числа устанавливаемых для обработки
заготовок, от числа участвующих в обработке инструментов и от по- рядка обработки поверхностей этими инструментами.
По числу устанавливаемых для обработки заготовок схемы ста- ночных операций разделяются на одноместные и многоместные (вре- мя установки и съема детали может быть перекрыто основным време- нем). По числу используемых инструментов схемы операции могут быть одноинструментными и многоинструментными.
Последовательная или параллельная работа инструментов при обработке поверхностей заготовки, а также последовательное или па-
раллельное расположение нескольких заготовок по отношению к ре-
жущим инструментам дают схемы операций с различными условиями совмещения переходов во времени. В зависимости от этого операции могут быть последовательного, параллельно-последовательного и па- раллельного выполнения. При последовательных схемах невозможно
перекрытие переходов обработки во времени и в Тшт входит сумма
времени всех переходов. Параллельные и параллельно-
последовательные схемы дают такую возможность, и учитываемое в
Тшт основное время равно времени лимитирующего перехода или ли-
митирующих переходов. В результате сочетания названных призна-
ков образуется ряд схем, начиная от наименее производительных од- номестных, одноинструментных, последовательных и кончая наибо- лее производительными многоместными, многоинструментными, па- раллельными и параллельно-последовательными схемами.
Выбрав конкретные схемы по каждой операции, т.е. уточнив со- держание операций, тем самым произведем очередные уточнения ра- нее намеченного маршрута изготовления детали в целом.
Уточненное содержание операции позволяет осуществить выбор станка из имеющегося парка или по каталогу либо заказать специаль- ный станок. Характер операции и принятый метод обработки опреде- ляют тип станка (токарный, фрезерный, сверлильный), а размеры за- готовки и обрабатываемых поверхностей - основные размеры станка. Установленная степень концентрации технологических переходов влияет на выбор модели станка. При высокой степени концентрации выбирают многосуппортные или многошпиндельные станки. Тип ре- жущего инструмента выбирается по произведенному ранее расчету промежуточных размеров заготовки (для зенкеров, разверток, протя- жек и других мерных инструментов), либо в процессе расчета режи-
мов резания (для резцов, расточных скалок и других инструментов).
В заключение производится техническое нормирование каждой операции технологического процесса с определением квалификации работы и оформление на соответствующих бланках (формах) спроек- тированного технологического процесса.
Многоместные схемы могут осуществляться в трех основных
вариантах:
1) Когда заготовки обрабатываются станкопартией, устанавли- ваемой на станке одновременно (например, шлифование партии мел- ких заготовок на магнитном столе плоскошлифовального станка).
2) Когда заготовки (или группа заготовок) устанавливается в своих приспособлениях независимо от других и обрабатываются по- очередно (например, при фрезеровании заготовок с маятниковой по- дачей или в поворотных приспособлениях).
3) Когда обработка выполняется на непрерывно вращающемся
столе или барабане (например, обработка на карусельных станках).
Этапы проектирования многоинструментных наладок.
Проектирование многоинструментной наладки включает сле-
дующие этапы:
*) Составление плана размещения инструментов по переходам и предварительный расчет режимов резания применительно к заданно- му темпу обработки.
2) Составление наладочной карты с размещением инструментов и указанием их шифров, уточнение схемы установки, корректирова- ние режимов резания, подбор сменных колес, копиров и других эле-
ментов наладки, определение Тшт
*) Выдача задания на проектирование рабочих и контрольных
приспособлений и специальных инструментов.
Проектирование станочной операции и многоинструментной наладки станка сопровождается расчетом настроечных размеров, дей- ствующих сил и ожидаемой точности обработки. Причем расчет ре- жимов резания должен обеспечить согласованную работу всех инст- рументов, участвующих в выполнении проектируемой операции.
Условия проектирования операций для многостаночного об- служивания.
При проектировании операций для многостаночного обслужи-
вания должны выполняться следующие условия:
1. Процесс обработки должен быть непрерывным до конца ра- бочего хода суппорта или стола, а при необходимости сопровождать- ся автоматическими переключениями станка.
2. Штучное время для группы станков многостаночного обслу-
живания должно быть равно между собой или кратно наименьшему.
3. Время рабочего хода суппорта должно быть равно или больше
суммы времени, затрачиваемого на снятие и установку заготовок (tус),
и времени, затрачиваемого на переход рабочего (*перех) от станка к
станку, т.е. tр.х ³(tус + tперех).
4. Станки должны иметь механизм автоматического выключе-
ния подачи при окончании рабочего хода суппорта или стола.
Если представляется целесообразным выполнять операцию на специальном станке, то должно быть разработано задание на проек- тирование этого станка. К заданию должны быть приложены чертежи заготовки с указанием веса, размеров с допусками и шероховатостям поверхностей до и после обработки на станке; чертежи специального инструмента, карта технологического процесса обработки заготовки и карта выполняемой на проектируемом станке операции.
7.4.6 Технологическая документация и дисциплина
При подготовке нового производства в качестве исходного до-
кумента необходимо иметь технологический процесс, т.к. без него не- возможно спроектировать и подготовить режущий инструмент, мери- тельный инструмент, приспособления, заказать оборудование и мате- риалы.
А после того, как предприятие приступило к работе по выпол- нению заказа, на первый план выступает требование строжайшего со- блюдения технологической дисциплины. Причем, практика показала, что малейшее отклонение от установленного технологического про- цесса вызывает удорожание обработки, перерасход материалов, уве- личение брака.
И поэтому имеется специальное Постановление Правительств от 08.*7.1940 г. «О соблюдении технологической дисциплины на маши- ностроительных заводах», которое признало обязательным фиксиро- вание проектируемых и действующих технологических процессов на предприятиях. Технологическая документация имеет еще и то пре- имущество, что позволяет накапливать производственный опыт, сис- тематизировать его, распространять передовой опыт и прогрессивную технологию на другие предприятия и организации.
В отечественной практике широкое распространение получили следующие основные формы технологической документации: мар-
шрутные и операционные карты, карты эскизов, контроля и другие.
*.5 Особенности проектирования типовых и групповых
|
|
Двойное оплодотворение у цветковых растений: Оплодотворение - это процесс слияния мужской и женской половых клеток с образованием зиготы...
Организация стока поверхностных вод: Наибольшее количество влаги на земном шаре испаряется с поверхности морей и океанов (88‰)...
Механическое удерживание земляных масс: Механическое удерживание земляных масс на склоне обеспечивают контрфорсными сооружениями различных конструкций...
Эмиссия газов от очистных сооружений канализации: В последние годы внимание мирового сообщества сосредоточено на экологических проблемах...
© cyberpedia.su 2017-2024 - Не является автором материалов. Исключительное право сохранено за автором текста.
Если вы не хотите, чтобы данный материал был у нас на сайте, перейдите по ссылке: Нарушение авторских прав. Мы поможем в написании вашей работы!