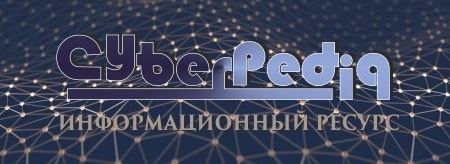
Наброски и зарисовки растений, плодов, цветов: Освоить конструктивное построение структуры дерева через зарисовки отдельных деревьев, группы деревьев...
Историки об Елизавете Петровне: Елизавета попала между двумя встречными культурными течениями, воспитывалась среди новых европейских веяний и преданий...
Топ:
Техника безопасности при работе на пароконвектомате: К обслуживанию пароконвектомата допускаются лица, прошедшие технический минимум по эксплуатации оборудования...
Основы обеспечения единства измерений: Обеспечение единства измерений - деятельность метрологических служб, направленная на достижение...
Марксистская теория происхождения государства: По мнению Маркса и Энгельса, в основе развития общества, происходящих в нем изменений лежит...
Интересное:
Как мы говорим и как мы слушаем: общение можно сравнить с огромным зонтиком, под которым скрыто все...
Что нужно делать при лейкемии: Прежде всего, необходимо выяснить, не страдаете ли вы каким-либо душевным недугом...
Искусственное повышение поверхности территории: Варианты искусственного повышения поверхности территории необходимо выбирать на основе анализа следующих характеристик защищаемой территории...
Дисциплины:
![]() |
![]() |
5.00
из
|
Заказать работу |
|
|
Материальный поток на пути от первичного источника сырья до конечного потребителя проходит ряд производственных звеньев. Управление материальным потоком на этом этапе имеет свою специфику и называется производственной логистикой.
Актуальность рассмотрения производственной логистики как отдельной функциональной подсистемы состоит в том, что в последние годы отмечена тенденция к сокращению сферы массового и крупносерийного производства. Расширяется применение универсального оборудования, гибких переналаживаемых производственных систем. Производители получают все больше заказов на производство небольших партий и даже единичных изделий. При этом со стороны покупателей все чаще выдвигается требование удовлетворить потребность за минимально короткий срок (сутки, час) с высокой степенью гарантий. Другим аспектом актуальности производственной логистики является организация производства в рамках кооперации по выпуску сложных изделий.
Производственная логистика должна заниматься оперативным планированием и управлением материальными потоками в производстве интегрировано и в сочетании с процессами снабжения и дистрибуции. Современное понимание логистики не только как методологии управления материальными и сопутствующими потоками, но и как концепции системной рационализации управления потоковыми процессами предполагает постепенное развитие и формирование интегрированных систем управления, построенных на принципах синхронизации, оптимизации и интеграции всех процессов, происходящих в организации. Сущность применения производственной логистики в интегрированном управлении предприятием заключается в создании условий для оптимального, эффективного и результативного протекания производственного процесса в пространстве и во времени.
|
В производственной логистике для определения норм времени и нормативов трудоемкости выполнения логистических операций используются проверенные практикой стандартные инструменты хронометрирования и фотографии рабочего дня. На выполнение каждой логистической операции должны быть установлены нормы затрат времени, финансовых ресурсов и трудоемкости, что позволяет эффективно контролировать операционную деятельность и показатели логистического плана. Правильно установленные прогрессивные нормы и нормативы позволяют не только контролировать расходование ресурсов, приходящихся на логистическую операцию, но и определить резервы роста производительности логистической инфраструктуры и персонала службы логистики компании.
Когда речь заходит об оптимизации логистических затрат в производственных компаниях, вспоминают о транспорте и складе, а в последнее время также об анализе ассортимента и управлении запасами. На возможности оптимизации затрат в производстве мало кто обращает внимание. Однако, основная часть добавленной стоимости у большинства предприятий создается именно на производстве. Большинство компаний может существенно повысить эффективность производства без значительных затрат, лишь за счет небольших точечных инвестиций.
Как известно, объектами внимания производственной логистики являются:
-валовое планирование производства на период в соответствии с поступившими заявками или прогнозами продаж;
-разработка планов и производственных заданий цехам и сменам;
-установление и контроль нормативов расходования сырья и материалов;
-оперативное управление производством и организация выполнения производственных заданий.
При этом многим предприятиям приходится сталкиваться со следующими основными проблемами в производственной логистике:
|
-не налажен учет материалов и полуфабрикатов в производстве, возможны их хищения;
-перерасход материалов, завышенное время производства изделий;
-в производственных помещениях «мало места», материальные потоки сырья, полуфабрикатов и готовой продукции не налажены (нерациональные внутрипроизводственные перемещения, неэффективное планирование производства);
-при недостатке готовой продукции для продаж производственные мощности загружены менее чем на 70%;
-простои оборудования, частые производственные сбои;
-несогласованность производства с другими бизнес-процессами предприятия (снабжением, дистрибуцией, транспортировкой).
И рано или поздно собственник бизнеса (собственником может быть и государство) ставит задачу максимально повысить эффективность имеющегося производственного оборудования и площадей. Вот как обычно выглядит типичный перечень действий для решения этой задачи:
-посещение производства, получение цифровой информации о загрузке оборудования и площадей;
-выявление и составление перечня проблем;
-получение цифровой информации в ракурсе каждой из проблем;
-оцифровка потоков на каждом из участков, изучение технологических параметров всего оборудования;
-выявление причин проблем и проектирование изменений;
-создание плана-графика мероприятий;
-в случае необходимости инвестиций – создание бизнес-плана проекта с расчетом сроков окупаемости;
-сопровождение реализации изменений руководителем проекта.
Решение задачи повышения эффективности имеющегося производственного оборудования и площадей предполагает:
-проектирование оптимального размещения имеющегося оборудования на имеющихся площадях, расчет грузопотоков на единицу времени;
-проектирование буферов, позволяющих избежать избытков и недостатков сырья, полуфабрикатов и комплектующих на рабочих местах;
-предложения по инвестициям в дополнительное (не производственное) оборудование, позволяющее повысить эффективность использования имеющегося;
-повышение эффективности использования оборудования и площадей до практического максимума;
-полное описание процессов под имеющиеся (либо проектируемые) задачи и оборудование;
-налаживание планирования и графиков производства с учетом минимально допустимых и максимально возможных партий, спроса, сроков годности выпускаемой продукции и ее доставки до потребителей.
|
Пример проекта размещения оборудования с учетом существующих грузопотоков приведен на рис. 2.4.
Рис. 2.4. Пример проекта размещения оборудования
Немаловажными направлениями при оптимизации производственных систем является:
-согласование производства с другими бизнес-процессами, прежде всего со снабжением и дистрибуцией;
-обеспечение высокой точности планирования производства;
-оптимизация норм расходов материалов на единицу продукции;
-постоянный контроль качества продукции на всех этапах производственного цикла.
К примеру, в одной из компаний-производителей косметической продукции долгое время работа велась по следующей схеме: минимальная варка в 200 кг (по параметрам существующих котлов), затем чистка котла с утилизацией остатков, потом варка другого крема, снова чистка – и возвращение к первому крему. Такая организация производства была удобна для отдела продаж, который стремился отпускать клиентам только свежайшую продукцию небольшими партиями. С целью оптимизации использования имеющегося оборудования и мощностей логисты разработали концепцию составления нормальных графиков производства с минимумом лишних чисток и утилизаций остатков, и только за счет этого удалось сэкономить 8% затрат на сырье.
Еще один пример, компания производит различные виды сухих строительных смесей. У них есть некие общие компоненты и есть различные. При этом в ассортименте есть дорогие смеси с высокими требованиями к производству и сырью, а есть продукты попроще и подешевле. Скажем, есть смесь А – дорогая и технологичная, а смесь Б – дешевая и с минимальными требованиями.
Производятся они на одной линии. При переходе со смеси А на смесь Б для очистки оборудования достаточно 30 минут, и потери сырья небольшие. А вот при переходе от смеси Б к смеси А требуется 2-3 часа для тщательной очистки и пробного прогона линии, да и потери при этом существенно увеличиваются.
Понятно, что при этом производство нескольких партий в цикле А-А-А-Б-Б-Б будет явно более быстрым и дешевым, чем А-А-Б-Б-Б-А. Но такое планирование производства невозможно без должного планирования сбыта и складских остатков.
|
После того, как будет составлен подробный и качественный план сбыта товаров собственного производства, следует составить план работы этого самого производства. Естественно, план производства уникален для каждого предприятия, однако в целом рекомендуется укрупнять партии с тем, чтобы уменьшать количество переходов между разными видами товара на одной линии – скажем, сначала сделать товар А, потом товар Б, а не 70% товара А, потом 25% товара Б, потом 30% товара А и оставшиеся 75% товара Б.
При наличии возможности неплохо бы подвозить в зону производства сырье и тару для всего цикла либо наладить их подвоз по мере расходования таким образом, чтобы не допускать остановок производственного процесса из-за того, что кладовщик еще не отпустил то или иное сырье либо упаковку. Да и в целом сырье и упаковка должны храниться максимально близко к производственным линиям для уменьшения пробега погрузчиков.
Но порой часть продукции оседает на складе и из-за того, что она производится большими партиями «про запас» во избежание дополнительных переналадок оборудования, которые отнимают много времени. В таких случаях необходимо сокращать время переналадки. Здесь кроются огромные резервы.
Например, компания-производитель чая с помощью ряда организационных и технических мер сумела за полгода ускорить переналадку линии фасовки в 6 раз. Если раньше они могли делать 3-4 партии за сутки, то теперь – 20-22 партии, причем общее время переналадок не увеличилось. А объем партий, соответственно, сократился. И компания смогла иметь на складе не 3-4 вида продукции в больших количествах, а понемногу всего. Это важное преимущество, учитывая, насколько важна в этом бизнесе широта ассортимента. Уровень логистического червиса в данном случае вырос с 65% до 97% при том, что клиенты не заказывают товар заранее, а приобретают непосредственно со склада.
Еще в одной компании, проблема заключалась в отсутствии учета полуфабрикатов и незавершенного производства.Т.е. сырье, поступающее в производство, и готовая продукция на выходе учитывались, а все, что внутри – «незавершенка», полуфабрикаты, сырье в технологических остатках – никак. Был проведен аудит, и оказалось, что почти все рецептуры, технические условия и технологические карты были несколько изменены по количеству необходимого сырья и нормам «усушки», «уварки» и «утруски». В результате реальная себестоимость выпускаемой продукции была завышена примерно на 5%. И нормальный учет материалов в производстве позволил избежать этих потерь.
Исходные условия в третьей компании, очевидно, знакомы многим: пространства в зоне производства постоянно не хватает, все проходы между станками завалены сырьем, полуфабрикатами и готовой продукцией. Перемещения товарно-материальных ценностей хаотичны, хотя примерно соответствуют неким «сложившимся годами» правилам. В этом случае пришлось анализировать потоки, проводить расчет пропускной способности и необходимой емкости зон у каждого станка. Затем была проведена небольшая реорганизация рабочего пространства, созданы буферы (при необходимости со стеллажами), на отдельных участках движение товарно-материальных ценностей было автоматизировано (с помощью рольганговых конвейеров). В результате при сравнительно небольших инвестициях эффективность производства была увеличена почти на 20%.
|
Излишние движения, перемещения людей и материалов, не добавляющие ценности продукту – это тоже потери, и нередко весьма значительные. Например, руководство одного из машиностроительных заводов все жаловалось на острую нехватку квалифицированных рабочих. А в цехах в это время можно было наблюдать следующую картину: станочник VI разряда, закончив обработку партии деталей, взваливает ящик с ними на плечи и несет в отдел контроля качества. Там все проверяют, ставят штампы, и только после этого работа считается выполненной, можно приступать к следующей. Разве в отделе контроля качества нет переносного оборудования, чтобы контролеры прямо в цехе все проверяли и ставили необходимые отметки? Конечно же есть. Но почему тогда квалифицированные сотрудники, которых так не хватает, тратят время на то, чтобы туда-сюда носить тяжести? Да так, исторически так сложилось, они всегда носили.
Для наших предприятий, особенно имеющих постсоветские традиции, это практически стандартная ситуация: рабочие сами ходят в отдел контроля качества, за инструментом, за нарядами и т.д., и т.п. Стоило бы оценить потери компании из-за этих хождений, т.е. из-за нецелевого использования рабочего времени, и задуматься о более рациональной организации рабочих мест. Многое изменить к лучшему помогает простая житейская логика, но добиться оптимальных результатов можно лишь при системном подходе. В Lean Production есть для этого система 5S – пять последовательных шагов по улучшению организации рабочего пространства (сортировка, порядок, чистота, стандартизация, дисциплина).
Источником лишних движений и перемещений на многих предприятиях оказывается и центральный склад. Скажем, материалы и комплектующие завозятся на него, ставятся на учет, размещаются на хранение, а потом по мере необходимости отгружаются и доставляются в цеха. Сколько лишних движений, перемещений, упаковки/переупаковки, оформления документов и т.п. Исключить их можно, если все необходимое сразу доставлять к местам будущего использования – где материал нужен, там он и лежит. Для этого, скорее всего, придется внести изменения в информационную систему. Но некоторые компании, подсчитав свои непродуктивные затраты, готовы идти и на более радикальные меры ради их сокращения.
Например, при внедрении MRP-системы на одном из заводов Caterpillar (один из ведущих производителей крупнейшей спецтехники в мире) специалисты пришли к выводу, что росту эффективности проекта мешает сама организация цехового пространства. Анализ материальных потоков показал, что перемещения на склад и со склада не только отнимают много времени, но и не поддаются точному планированию по времени. Это ставило под угрозу качество управления в целом. Поэтому было принято решение, и за два выходных дня склад просто физически перенесли на новое место, более удобное при существующей схеме движения потоков.
Второй пример касался российского завода. В его составе было два механических цеха. В ходе ERP-проекта проанализировали потоки движения деталей и увидели, что часто они многократно перемещаются из цеха в цех. И каждый раз при перемещена оформляются документы сдачи/приемки. Этож масса лишних трансакций и, соответственно, потерянного времени. Чтобы исключить их, пришлось принять нестандартное решение, признав, что цех – это не помещение, а зона ответственности. Два здания, расстояние между которыми составляет около 10 м, были объединены в один цех. Сначала документально и организационно, чтобы избавиться от необходимости выполнять многочисленные трансакции приема/передачи, а со временем и физически – при замене и обновлении оборудования его расположение проектировали таким образом, чтобы вся обработка выполнялась по замкнутому циклу в пределах одного цеха, детали не нужно было никуда переносить.
Впрочем, излишние перемещения материалов могут быть и следствием проблем внутренней логистики предприятия: что-то не по тому маршруту повезли, что-то – не в том количестве и т.п. Потом возвраты, дополнительная доставка – т.е. опять непродуктивные расходы. Рецепт избавления от них – совершенствование планирования перемещения материалов в соответствии с логикой производственного процесса, анализ и синхронизация потоков создания ценности и материальных потоков. И применение в управлении этими потоками, там, где это рационально, техники Канбан для оптимизации их обслуживания, упрощения отчетности, снятия излишней нагрузки с управляющего аппарата.
Немаловажным направлением оптимизации производственных систем является внедрение системы мотивации производственного персонала. Последний сюрприз преподнесла версия ISO 9000-2015. В ней дается 3 года на изменения («Переходные условия»), содержатся такие интересные разделы, как 7.1.4 «Среда функционирования процессов», 7.3 «Осведомленность», и введено положение об экспертной оценке с помощью опроса. Теперь, проводя аттестацию по ISO, аудиторы опросят не менее 30-40 любых сотрудников предприятия. Если ранее мотивация была великим достижением отдельных компаний, то теперь будет обязательным условием для всех, кто хочет получить сертификат ISO 9000 по новой системе. При этом в ISO впервые введены не только социальные (отсутствие дискриминации и конфронтации, спокойствие), но и психологические показатели – такие, как снижение стресса, предотвращение истощения, защита от эмоций.
Сотрудники не просто должны быть осведомлены, как они участвуют в производственном процессе, но еще и должны каждый на своем рабочем месте объяснить свой вклад в результативность системы менеджмента качества. Попробуйте пройтись у себя по цехам и поспрашивать об этом рабочих. В одну из белорусских компаний на сертификацию приехали поляки и говорят: «Не можем подтвердить сертификацию – у вас нет мотивации». Наши сразу предоставляют кипу документов: «Мы же платим!» Поляки: «Ну и что? У вас оплата есть – мотивации нет».
Например, СООО «Белвест» премирует сотрудников за некурение (ни на работе, ни дома). Не куришь – получи сверх своей зарплаты 50 рублей. Дополнительно платит «Белвест» и за постоянство выходов на работу. Заболел, не работал – зарплата согласно законодательству. Но если человек регулярно выходил на работу, не допуская пропусков даже по уважительной причине, то получит премию дополнительно.
Таким образом, в производственной логистике есть масса «узких» мест, где возможна оптимизация. Это, конечно, не так бросается в глаза, как оптимизация транспортных или складских затрат, но суммы экономии в результате обычно также очень существенны.
И в заключении хотелось бы отметить, – «Никогда не говорите, что мы никогда не будем заниматься производством». Некоторые компании, наладившие эффективные цепи поставок, построившие крупные торговые сети, вынуждены обратить внимание на производство, купить действующее производство, провести там техперевооружение или организовать производство с нуля. Ведь требование о наличии товаров белорусского производства в торговых сетях никто не отменял. Например, у ООО «Мегатоп» (сеть обувных магазинов) в Витебске есть своя фабрика ООО «Тувия» (торговая марка «Happy Family»). Пока там шьют только женскую обувь. Учитывая требования Министерства торговли Республики Беларусь по наличию белорусского товара в розничных сетях, «Мегатоп» планирует расширить производственные мощности своей фабрики и наладить выпуск мужской и детской обуви.
Владельцы сети «Ziko» (COOO «Зико»), 80-ти магазинов по продаже импортных ювелирных изделий и часов в Беларуси, став крупными ритейлерами, также задумались о собственном производстве. Открытие нового производственного корпуса площадью более 15 тыс. м2 состоялось в конце 2014 г. Теперь в группу компаний «Ziko» входят завод «Zorka» и одноименная розничная сеть. На предприятии производится широкий ассортимент ювелирных изделий: от обручальных колец без вставок до эксклюзивных украшений из золота 14 и 9 карат со вставками из драгоценных камней. Теперь в обороте магазинов «Ziko» продажа часов занимает 20%, а ювелирных изделий – 80%. Примерно половину от реализуемых ювелирных изделий составляет продукция «Zorka».
Однако вывод один, заниматься производством намного «затратнее», чем просто дистрибуцией товаров импортного производства в Беларуси.
Оценка эффективности производственной системы предприятия проводится с помощью следующих ключевых показателей эффективности (KPI):
1. Производительность труда по выручке от реализации рассчитывается путем деления выручки от реализации продукции, товаров, работ (услуг) на численность промышленно-производственного персонала:
, (2.9)
где В – выручка от реализации продукции, товаров, работ (услуг) за отчетный период, руб.; Чпп – численность промышленно-производственного персонала, чел.
Производительность труда рассчитывается как за отчетный период, так и базовый период. Например, в организации численность промышленно-производственного персонала в 2015 г. составила 125 чел., в 2014 г. – 140 чел. Выручка от реализации составила в 2015 г. 7 590 тыс. руб., в 2014 году – 8 050 тыс. руб. Производительность труда по выручке от реализации в отчетном периоде составила 60,72 тыс. руб. (7 590/125), в базовом – 57,5 тыс. руб. (8 050/140).
При необходимости из полученной выручки от реализации продукции, товаров, работ (услуг) вычитаются налоги и сборы, а также материальные и прочие затраты, производится расчет производительности труда по добавленной стоимости.
2. Производительность труда по добавленной стоимости рассчитывается путем деления выручки от реализации продукции, товаров, работ (услуг) (за вычетом начисленных налогов и сборов из выручки, материальных и прочих затрат) на численность промышленно-производственного персонала:
, (2.10)
где Вдоб – выручка от реализации продукции, товаров, работ (услуг) (за вычетом начисленных налогов и сборов из выручки, материальных и прочих затрат) за отчетный период, руб.; Чпп – численность промышленно-производственного персонала, чел.
Под добавленной стоимостьюпонимается часть общей стоимости продукции, товара, услуги, на которую увеличивается стоимость потребленных в процессе обработки материальных ресурсов (услуг) к моменту продажи потребителю. Добавленная стоимость широко используется как показатель оценки объема производства, поскольку не содержит повторного счета стоимости приобретенных сырья, материалов, услуг. Положительная динамика производительности труда по добавленной стоимости характеризует качественный уровень экономического развития организации.
Все чаще в качестве показателя для расчета производительности труда делается выбор в пользу именно добавленной стоимости, которая нивелирует влияние фактора материальных затрат на объем производства и в большей мере отражает эффективность производственной системы предприятия.
Например, объем производства в фактических отпускных ценах (за вычетом начисленных налогов и сборов из выручки) составил в 2015 году 5 490 тыс. руб., материальные затраты – 2 530 тыс. руб. и прочие затраты – 120 тыс. руб.; в 2014 году объем производства составил 5 450 тыс. руб., материальные затраты – 2 460 тыс. руб. и прочие затраты – 108 тыс. руб. Численность промышленно-производственного персонала в 2015 г. составила 135 чел., в 2014 г. – 140 чел. Производительность труда по добавленной стоимости в отчетном периоде составила 21,0 4 тыс. руб. ((5 490 – 2 530 – 120)/135), в базовом периоде – 20,59 тыс. руб. ((5 450 – 2 460 – 108)/140).
3. Темп роста производительности труда рассчитывается как отношение производительности труда в отчетном периоде к производительности труда в базовом периоде:
, (2.11)
где ПТотч – производительность труда в отчетном периоде, руб.; ПТбаз – производительность труда в базовом периоде, руб.
Для расчета темпа роста можно использовать как производительность труда по выручке от реализации, так и по добавленной стоимости. Производительность труда может увеличиваться за счет сокращения численности работников в отчетном по сравнению с базовым периодом, а также при увеличении выручки от реализации продукции, товаров, работ (услуг).
Например, производительность труда в отчетном периоде составила 60,72 тыс. руб., в базовом – 57,5 тыс. руб. Темп роста производительности труда составил 105,6% (60,72/57, 5×100).
4. Доля производственных заданий, выполненных в срок:
, (2.12)
где Звып.пр.зад – количество производственных заданий с датой завершения/отгрузки в отчетном периоде (месяц, квартал, полугодие, год), которые не имеют отклонения по срокам завершения производства, количеству единиц, указанных в производственном задании, ед.; Зприн.пр.зад – количество всех производственных заданий с датой завершения/отгрузки в отчетном периоде, ед.
Низкая дисциплина выполнения производственных заказов отражается на репутации и имидже компании, на отношениях с заказчиками, что в итоге приводит к снижению объемов заказов. В тоже время высокая точность выполнения производственных заказов позволяет сокращать складские запасы, ускорять оборачиваемость и снижать финансовую нагрузку на компанию. Пример лучших производственных компаний – точность выполнения производственных заказов 99%.
5. Темп роста производственной себестоимости:
, (2.13)
где Cфакт – фактическая производственная себестоимость выпущенной продукции в отчетном периоде, руб.; Cплан – плановая производственная себестоимость выпущенной продукции в отчетном периоде, руб.
Кроме того, что фактическая себестоимость не должна превышать плановую (за допущением единичных случаев), лучше поставить задачу на снижению данного KPI. Для этого есть масса инструментов: пересмотр и модернизация технологии, увеличение выхода годного, снижение доли брака, работа с поставщиками сырья и материалов, снижение трудоемкости выполняемых операций.
6. Доля рекламаций от клиентов в количестве отгруженных заказов:
, (2.14)
где Зрекл – количество заказов, по которым получены рекламации в отчетном периоде, ед.; Звып – количество выполненных заказов в отчетном периоде, ед.
Каждая внешняя рекламация требует тщательного анализа. Кроме выявления реальной причины возникновения сбоя и точечного устранения проблемы, необходимо системно подойти и предпринять превентивные действия, чтобы в будущем данная ошибка не возникла снова. Данный показатель важен в динамике, его снижение говорит о качественной работе с рекламациями.
На основе указанных ключевых показателей эффективности (KPI), разрабатываются основные направления повышения эффективности производственной системы предприятия.
В зависимости от характера, масштаба и особенностей производственных структур для автоматизации процессов управления производством применяются различные модули и программные решения: MES, APS, EAM-системы.
Система управления производством (Manufacturing Execution System, MES) – специализированное прикладное программное обеспечение, предназначенное для решения задач синхронизации, координации, анализа и оптимизации выпуска продукции в рамках какого-либо производства.
Автоматизированная система управления производством (MES) позволяет связать в единую структуру все производственные бизнес-процессы. Сегодня автоматизация производства лежит в основе развития современной промышленной отрасли. Благодаря автоматизации производственных процессов, в значительной степени повышается эффективность труда, заметно улучшается качество производимой продукции. Автоматизация производства делает процесс изготовления продукции более безопасным и комфортным для всех работников предприятия на каждом из его этапов.
MES-система предназначена для предприятий, у которых возникает необходимость точно измерять издержки производства, эффективность работы оборудования и персонала. Путем систематической регистрации точных данных о производственных процессах, система позволяет внедрить концепцию «бережливого производства», т.е. устранять расточительность, и вместе с тем, сводить до минимума производственные издержки. MES-Система постоянно накапливает информацию о производственных процессах, делая ее доступной для дальнейшей аналитики, согласно заранее установленным служебным правам, упрощает при этом руководящим кадрам процесс принятия решений, а работникам производства обеспечивает чувство безопасности, путем чёткой персонализации при выполнении отдельных операций.
Система управления производством (MES) предполагает следующую функциональность:
-управление рецептурами;
-прослеживаемость (генеалогия) продукции;
-управление бизнес-процессами в производстве;
-управление производственными заявками;
-составление и автоматическое обновление графика производства;
-количественная информация о продукции в процессе производства;
-оперативный и архивный реестр работы оборудования и персонала;
-реестр производственных событий;
-управление партиями и серийными номерами продуктов;
-поддержка процессов контроля качества;
-интеграция с внешними системами.
С помощью MES-системы компании имеют возможность, в режиме реального времени, осуществлять планирование, оптимизацию, контроль и документирование всех процессов от начала формирования заказа, до выпуска готовой продукции. Система автоматизации производства позволяет быстро и эффективно моделировать производственные бизнес-процессы, а также регистрировать ход их выполнения. Возможность интеграции с другими модулями и ERP-системами позволяет прослеживать продукцию, компоненты и сырье на каждом отдельном этапе их пребывания на производстве. Использование предопределяемых отчетов в MES-системе, позволяет отражать полную картину производственного процесса на всех уровнях – начиная с мастера смены и заканчивая директором завода.
Преимущества автоматизации производства при помощи MES системы:
-увеличение производительности труда;
-поддержка «бережливого производства;
-сокращение производственных расходов;
-оперативный мониторинг производственных процессов;
-возможность быстрого выявления критических ситуаций;
-ликвидация бумажного документооборота;
-упорядочение процессов и ресурсов;
-интеграция с внешними системами;
-возможность простого и быстрого моделирования бизнес-процессов.
Процесс внедрения системы управления производством (MES) – это серьезный процесс, который требует детального и обдуманного подхода. На практике внедрение систем MES-класса на небольших предприятиях и в начинающих компаниях не доставляет особых сложностей. Отсутствие истории, требующей конвертации в новый программный продукт, и опыта работы с применением автоматизированных систем не дает возможности оценить эффективность их использования на производстве. На крупных предприятиях ситуация противоположная: перенос необходимых данных и параллельное сопровождение внедряемого программного обеспечения требуют значительных временных и финансовых затрат. Для эффективного внедрения MES-системы следует использовать следующий алгоритм действий:
1. Провести тщательный анализ производства и оценить возможную выгоду от внедрения MES-системы. При этом необходимо ставить конкретные цели: снижение времени простоя производственного оборудования в цехах; экономия ресурсов; сокращение издержек; повышение качества выпускаемой продукции; увеличение производительности труда. Система управления производством может дать значимый эффект только при проведении грамотного анализа и расчете возможной выгоды.
2. Создать рабочую группы, члены которой будут непосредственно заниматься внедрением системы на производстве. Рациональным решением будет включение в состав группы только тех сотрудников, которые имеют опыт работы в сфере информационных технологий и интересуются инновациями. Такими сотрудниками могут быть как менеджеры производственного предприятия, так и мастера производственных цехов, на которых будет внедряться MES-система. Члены рабочей группы должны быть заинтересованы в рациональном использовании оборудования и ресурсов, а также в повышении производительности труда.
3. Определить конкретные сроки внедрения MES-системы. Желательно сначала на существующем производстве установить систему на небольшое количество станков (не более 10). Это позволит на практике проанализировать эффективность использования и внести коррективы в реализацию проекта в большом масштабе.
4. Подготовить аргументацию внедрения системы для руководства предприятия и рассчитать калькуляцию возврата вложенных средств, затраченных на реализацию проекта. Внедрение системы управления должно окупить себя и приносить прибыль.
Например, в целях повышения эффективности работы НПЗ ОАО АНК «Башнефть» было принято решение о внедрения MES-системы. В рамках проекта было проведено детальное обследование технологических объектов и потоков НПЗ, создана математическая модель производства. MES-система была интегрирована с ERP-системой предприятия на базе платформы SAP.
Одно из главных достижений в том, что благодаря переходу на MES стали более эффективными бизнес-процессы на производстве. Например, если раньше технические параметры с неавтоматизированных установок передавались по телефону, то теперь каждый оператор вводит данные в специальный «легкий» интерфейс. В результате применения новых методологий оптимизированы процессы получения сводной (консолидированной) производственной отчетности. Благодаря проекту удалось обеспечить технические и экономические службы производственных предприятий своевременными, достоверными и структурированными данными о перерабатывающих процессах. Они могут быть использованы не только для принятия оперативных решений, но и для анализа и оптимизации процессов на производстве. Внедрение MES-системы позволило сократить сроки подготовки производственной отчетности, повысить уровень ее достоверности. Внедрение MES-системы проходило в несколько этапов. Сначала решение было запущено на одном перерабатывающем заводе компании и потом успешно тиражировано на других НПЗ.
Кроме того, появились информационные системы, реализующие исключенные функциональные возможности: усовершенствованное планирование производства (Advanced Planning & Scheduling, APS) – решает задачи составления производственных расписаний в рамках всего предприятия; управление основными фондами предприятия (Enterprise Asset Management, EAM) – отвечает за управление физическими активами и режимами их работы, рисками и расходами на протяжении всего жизненного цикла для достижения и выполнения стратегических планов организации.
Синхронное планирование производства (Advanced Planning & Scheduling, APS) – специализированное прикладное программное обеспечение, предназначенное для расширенного календарного и оперативного планирования производства.
APS-система предназначена в первую очередь, для производственных компаний и направ
|
|
Таксономические единицы (категории) растений: Каждая система классификации состоит из определённых соподчиненных друг другу...
Автоматическое растормаживание колес: Тормозные устройства колес предназначены для уменьшения длины пробега и улучшения маневрирования ВС при...
Индивидуальные и групповые автопоилки: для животных. Схемы и конструкции...
Организация стока поверхностных вод: Наибольшее количество влаги на земном шаре испаряется с поверхности морей и океанов (88‰)...
© cyberpedia.su 2017-2024 - Не является автором материалов. Исключительное право сохранено за автором текста.
Если вы не хотите, чтобы данный материал был у нас на сайте, перейдите по ссылке: Нарушение авторских прав. Мы поможем в написании вашей работы!