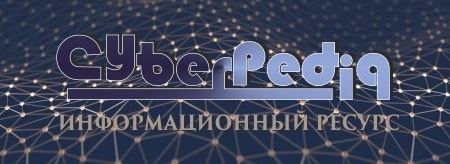
Механическое удерживание земляных масс: Механическое удерживание земляных масс на склоне обеспечивают контрфорсными сооружениями различных конструкций...
Опора деревянной одностоечной и способы укрепление угловых опор: Опоры ВЛ - конструкции, предназначенные для поддерживания проводов на необходимой высоте над землей, водой...
Топ:
Проблема типологии научных революций: Глобальные научные революции и типы научной рациональности...
Техника безопасности при работе на пароконвектомате: К обслуживанию пароконвектомата допускаются лица, прошедшие технический минимум по эксплуатации оборудования...
Эволюция кровеносной системы позвоночных животных: Биологическая эволюция – необратимый процесс исторического развития живой природы...
Интересное:
Уполаживание и террасирование склонов: Если глубина оврага более 5 м необходимо устройство берм. Варианты использования оврагов для градостроительных целей...
Распространение рака на другие отдаленные от желудка органы: Характерных симптомов рака желудка не существует. Выраженные симптомы появляются, когда опухоль...
Влияние предпринимательской среды на эффективное функционирование предприятия: Предпринимательская среда – это совокупность внешних и внутренних факторов, оказывающих влияние на функционирование фирмы...
Дисциплины:
![]() |
![]() |
5.00
из
|
Заказать работу |
|
|
Во многих случаях полученные в результате первичной механической обработки чистовые заготовки используют для изготовления мебельных и столярных плит и щитов. Для того чтобы обеспечить прочность материала, заготовки склеивают между собой.
Основные положения принципа соединения деталей способом склеивания приведены в параграфе 4.2. В данном параграфе рассматриваются особенности технологических процессов формирования плитных материалов с применением клеевых соединений.
Технологический процесс склеивания. Клеевые соединения древесины, как описывалось выше, делят на угловые соединения, соединения по ширине (сплачивание) и соединения по длине (сращивание). Перечисленные соединения выполняют путем соединения боковых либо торцовых поверхностей деталей.
Клеевые соединения должны максимально обеспечивать прочность и качество изделия в процессе эксплуатации. Торцовые клеевые соединения обеспечивают прочность до 80% от прочности цельной древесины. Боковые клеевые соединения имеют прочность склеиваемой древесины (а иногда и превышают ее).
При соединении частиц измельченной древесины получают сочетание торцового и бокового склеивания. Форма, размеры и ориентация частиц в материале обеспечивают преобладание того или иного типа склеивания, что влияет на прочность получаемого материала.
Технологический процесс склеивания во всех случаях состоит из определенной последовательности операций, среди которых:
1) подготовка поверхностей к склеиванию;
2) подготовка клея;
3) нанесение клея на склеиваемые поверхности;
4) сжатие склеиваемых поверхностей;
5) выдержка склеенных заготовок.
Подготовка поверхности к склеиванию. Проведение этой операции зависит от нескольких факторов: вида соединяемых материалов, размера и формы заготовок, типа используемого клея, условий склеивания. Склеиваемые поверхности очищают от масла, смолы, грунта, сажи и других загрязнений. На поверхностях не должно быть опилок, стружки, пыли. Влажность древесины должна быть не более 10%. Покоробленность заготовок не должна превышать 2 мм на 1 м длины для обеспечения плотности прилегания соединяемых поверхностей.
|
При формировании наружного шва поверхности зачищают до показателя шероховатости Rz не более 60 мкм. Поверхности, образующие внутренние швы, должны иметь показатель шероховатости Rz не более 200 мкм. Сопрягаемые поверхности шиповых соединений деталей должны быть выполнены с соблюдением требуемых допусков и посадок.
Подготовка клея. Выбор клея зависит от назначения и типа склеивания, соединяемых материалов, условий эксплуатации изделия и условий проведения процесса склеивания. Виды применяемых при склеивании клеев описаны в параграфе 4.2.
После выбора клеевого состава необходимо приготовить рабочий раствор клея. Для каждого вида клея существует определенный технологический режим подготовки раствора, который регламентирует следующие параметры:
• технические требования. Предъявляются к материалам, применяемому оборудованию (указывается марка оборудования), приготовлению клея (указывается состав компонентов и время хранения), приготовлению компонентов;
• содержание технологического режима. Указываются температура и срок хранения, относительная влажность воздуха, показатель pH, вязкость;
• методы контроля параметров режима и рабочего раствора (указываются стандарты);
• требования безопасности и производственной санитарии. Указываются допустимые концентрации паров состава в воздухе, меры предосторожности, условия нанесения и т.п.
Нанесение клея на склеиваемые поверхности. Промежуток времени с момента, как клеевой раствор был подготовлен в соответствии с технологическим режимом, и до момента начала отвердения называется жизнеспособностью клея. В течение периода жизнеспособности клеевой состав пригоден для нанесения на склеиваемые поверхности и склеивания их с получением соединения требуемого качества. Для каждого типа и вида клея этот период индивидуален, и важно соблюдать технические условия нанесения клеевого состава для обеспечения качественного соединения.
|
После нанесения клея на склеиваемые поверхности процесс отвердения ускоряется вследствие интенсивного испарения и впитывания жидкой фазы. Период от момента нанесения клеевого раствора на поверхность до момента полной потери им клеящей способности называют рабочей жизнеспособностью клея. Необходимо нанести клей на соединяемые поверхности и провести склеивание до истечения срока рабочей жизнеспособности клея. Длительность рабочей жизнеспособности клеящего состава зависит от свойств клея, свойств склеиваемых материалов и от условий склеивания. При повышении температуры рабочая жизнеспособность клея снижается.
При нанесении клея важно соблюдать условие равномерности толщины клеевого слоя по всей обрабатываемой поверхности. Промежуток времени между нанесением клея на поверхность и соединением склеиваемых поверхностей называют открытой выдержкой.
Период с момента соединения склеиваемых поверхностей и до сжатия их под давлением (прессования) называют закрытой выдержкой. Длительность выдержек зависит от свойств и состава клея. Длительность периода открытой и закрытой выдержек не должна превышать срок рабочей жизнеспособности клея для обеспечения надежности склеивания.
Сжатие склеиваемых поверхностей. После нанесения клея и соединения склеиваемых поверхностей необходимо обеспечить адгезию клеевого слоя со склеиваемыми поверхностями по всей площади склеивания. Для этого по истечении требуемого срока закрытой выдержки к склеиваемым материалам прилагают равномерное по всей площади склеивания усилие сжатия и выдерживают определенное время под давлением всю конструкцию. Этот процесс выдержки называют прессованием. Прессование осуществляют в различных пневматических, механических или гидравлических устройствах, обеспечивающих силовое воздействие.
|
Для склеивания деталей из древесины усилие прессования составляет от 0,1 до 1,2 МПа в зависимости от технологических особенностей процесса. Определение оптимального усилия прессования влияет на качество и прочность клеевого соединения. Избыточное давление приводит к истончению клеевого слоя и повышает внутренние напряжения в соединяемых деталях, что снижает прочность склеивания. Недостаточное давление не обеспечивает условий для возникновения адгезии между поверхностями.
Выдержка склеенных заготовок. В сжатом состоянии склеиваемые детали находятся в течении времени, необходимого для полного отверждения клеевого слоя. Прочность отвердевшего клеевого слоя должна обеспечивать жесткость соединения деталей после снятия усилия прессования.
Применяют два способа выдержки в процессе склеивания: холодный и горячий. Склеивание холодным способом проводят без нагрева склеиваемых материалов. Этот способ требует более длительного периода времени для схватывания клея, но позволяет получать хорошее качество склеивания при малых внутренних напряжениях в клеевом шве. Горячий способ склеивания предполагает нагрев склеиваемых деталей или клеевого шва. Этот способ более производителен, чем холодный, поскольку нагрев увеличивает скорость отвердения клея.
После снятия давления склеенные заготовки выдерживают в течение срока технологической выдержки, обеспечивающей достижение прочности клеевого соединения требуемых норм.
Склеивание плит, щитов и брусьев. Мебельные щиты, столярные плиты и клееные брусья являются наиболее распространенными древесными материалами при производстве многих видов строительных, столярных и бытовых изделий, а также объектов искусства.
При изготовлении щитов и плит применяют сплачивание — клеевое соединение кромок заготовок. При изготовлении брусьев используют как сплачивание по толщине и ширине, так и сращивание в длину (в зависимости от размеров заготовок и требуемых форматов готового материала).
Заготовки, используемые для склеивания щитов, плит и брусьев, должны соответствовать определенным требованиям к эстетическим и физикомеханическим свойствам, влажности, точности обработки, количеству и типу допустимых пороков, шероховатости поверхности.
|
Эстетические свойства заготовок являются важным показателем при производстве мебельных щитов, не подлежащих дальнейшему облицовыванию шпоном или текстурированными пленками. Такие клееные конструкции подлежат покрытию прозрачными лакокрасочными материалами, следовательно, заготовки должны обладать выраженной текстурой и естественным цветом.
Технологический процесс изготовления столярных плит и мебельных щитов состоит из следующих стадий:
1) подготовка заготовок к склеиванию (продольное фрезерование кромок и, по необходимости, нластей);
2) сплачивание — склеивание заготовок по ширине (см. параграф 4.2);
3) фрезерование щита (плиты) в размер по толщине;
4) облицовывание плиты (по необходимости);
5) обработка щита (плиты) по периметру;
6) облицовывание кромок (приклеивание обкладок).
Технологический процесс изготовления клееных конструкций состоит из двух различных операций: сращивания — склеивания но длине; и сплачивания — склеивания по толщине и, реже, но ширине.
При склеивании заготовок по длине используют соединения «впритык», «на ус» и «зубчатое соединение» (см. параграф 4.2). Наиболее широко для изготовления клееных конструкций используются зубчатые клеевые соединения (ГОСТ 19414—90).
В зависимости от ориентации зубцов относительно нласти зубчатые клеевые соединения бывают вертикальные, горизонтальные и диагональные (рис. 5.7).
Рис. 5.7. Виды зубчатых соединений но длине:
а — вертикальное; б — горизонтальное; в — диагональное2
Облицовывание заготовок
Одну или обе поверхности древесных и плитных материалов часто оклеивают тонкими текстурированными пленками или слоем строганого шпона из ценных пород древесины. Этот процесс называют облицовыванием. Облицовывание используют при изготовлении недорогой мебели и столярных изделий, имеющих красивый внешний вид. Облицовывание позволяет получить крупные форматы заготовок с яркой текстурой и насыщенным цветом, но без значительного расхода ценных пород древесины. Облицованный материал представляет собой прочную многослойную клееную конструкцию.
Для облицовывания используют основной материал, клей и облицовочный слой.
Основными материалами, которые чаще всего облицовывают, являются пиломатериалы пород древесины с маловыразительной текстурой, ДСП, ДВП, МДФ, столярные щиты и плиты, а также гнутоклееные заготовки. Клей для облицовывания поверхностей выбирают, исходя из свойств основного материала и слоя покрытия, но чаще всего это клеи на основе карбами- доформальдегидных смол, столярные клеи, 11ВА, пленочные клеи и др. В качестве облицовочного слоя используют строганый шпон, полимерные пленки и пропитанную полимерными составами бумагу. Также применяют различные ткани, искусственную кожу, металлическую фольгу и другие слои материалов, которые можно наклеить па поверхность древесины.
|
Одностороннее облицовывание применяют к плитным материалам и заготовкам, имеющим толщину свыше 10 мм. Тонкие материалы облицовывают с двух сторон во избежание коробления листа, поскольку в процессе облицовывания в материале возникают внутренние напряжения. Двусторонняя обработка позволяет компенсировать напряжения, и материал не деформируется.
Облицовывание может быть однослойным и двухслойным. При двухслойном облицовывании используют два слоя облицовки — подслой и лицевой слой. Слои могут быть различными как по составу, так и по толщине. В качестве подслоя используют недорогие материалы, накладываемые на основу для выравнивания поверхности: лущеный шпон, ткань, бумагу и др. Лицевой слой, более тонкий и дорогой, накладывают на подслой.
Технологическая стадия облицовывания состоит из следующих операций: подготовка основы; подготовка покрытия; подготовка клея; наклеивание.
В зависимости от конструкции изделия, формы заготовок и общего технологического процесса производства стадия облицовывания производится либо до раскроя материала, либо облицовывают уже полученные заготовки. Облицовывать можно также сборочные единицы. Заготовки из пиломатериалов облицовывают после стадии обработки в размер.
Плитные материалы сначала калибруют по толщине, а затем облицовывают. Детали сложного профиля, получаемые поэтапной механической обработкой, облицовывают после фрезерования по форме, после чего выполняют операции формирования шипов и проушин, высверливания отверстий и др.
Гнутоклееные детали облицовывают в процессе формирования общего профиля, одновременно с процессом склеивания. Для этого применяют пресс-формы с эластичными элементами. Процесс склеивания при облицовывании криволинейных поверхностей ускоряют при использовании различных нагревательных систем (ТВЧ, инфракрасное излучение и т.п.).
Облицовывать заготовки, как и склеивать, можно как холодным, так и горячим способом.
Подготовка основного материала. Поверхность заготовки, подлежащей облицовыванию, выравнивают с помощью абразивных материалов, устраняя неровности и дефекты, способные снизить прочность склеивания. При необходимости крупные дефекты, такие как сколы, выпавшие сучки, трещины, заполняют шпатлевкой или высверливают, закрывая отверстие вклеиваемой вставкой. Шероховатость поверхности доводят до того уровня, который позволяет провести качественное склеивание, не отображаясь на лицевом слое. Этот уровень, прежде всего, зависит от типа лицевого слоя. Толщина слоя облицовки в 2—3 раза должна превышать высоту неровностей профиля поверхности основы. Если уровень шероховатости не позволяет нанести слой облицовки без заметных искажений последнего, то используют подслой.
С поверхности удаляют различные загрязнения и просушивают ее. Влажность основного материала должна быть ниже равновесной влажности на 1—2%, поскольку при нанесении клея будет происходить неизбежное увлажнение поверхности.
Подготовка слоя облицовки зависит от состава и качества наносимого материала. Слой должен быть однородным по толщине, без отверстий и разрывов. Не допускаются крупные инородные включения, загрязнения и следы увлажнения на поверхности наносимых материалов. Степень влажности для облицовки зависит от тина наносимого материала. Для шпона она должна составлять 8—10%.
Для облицовывания часто используют пленку на основе поливинилхлорида (ПВХ), ее закупают на предприятии-изготовителе в виде рулона. Пленки имеют толщину от 0,15 до 0,4 мм.
Распространенным материалом для облицовывания являются пленки на основе бумаги плотностью от 90 до 130 г/м3, пропитанной термореактивными меламиноформальдегидными, карбамидными или полиэфирными смолами. Толщина бумажных термореактивных пленок — от 0,14 до 0,21 мм, причем до 80% состава их приходится на полимерные смолы.
Пленки, как бумажные, так и полимерные, могут иметь облагороженную или необлагороженную поверхность. Облагороженная поверхность не требует дальнейшей отделки, так как имеет защитный слой. Необлагорожен- ная пленка подлежит дальнейшей отделке. Для повышения декоративных свойств изделий на пленки наносят рисунок с тиснением, имитирующий текстуру ценных пород древесины.
Пленки могут быть однослойные или многослойные. В мебельном производстве чаще всего применяют двухслойные пленки.
Пленки должны быть эластичными и иметь способность скрывать повышенную шероховатость основного материала (особенно это важно для облицовывания ДСП).
Подготовка клея выполняется так же, как и при склеивании заготовок (см. параграф 5.4).
Наклеивание шпона на поверхность основы проводится но технологии, аналогичной склеиванию (см. параграф 5.4).
Пленки на поверхность заготовок с предварительно нанесенным клеем наносят методом кэширования — непрерывного накатывания в вальцовых прессах. Для кэширования используют клеи на основе карбамидных смол, поливинилацетата и эластомеров.
Кэширование может быть холодным, теплым и горячим. При холодном кэшировании облицовка прикатывается к основе при комнатной температуре, без подвода тепла к соединяемым материалам. При теплом кэшировании поверхность основного материала нагревают до нанесения клея. Горячее кэширование предполагает как предварительный нагрев поверхности заготовки, так и нагрев валиков пресса до 200°С в процессе накатки. Горячее кэширование применяют в том случае, если клеевой состав изготовлен без использования влаги (клеи-расплавы, клеящие пленки).
Технологический процесс кэширования состоит из следующих стадий:
• укладка основы;
• очистка поверхности от поверхностных загрязнений (пыли, стружки);
• нанесение клея;
• термообработка поверхности (при теплом и горячем кэшировании);
• формирование пакета;
• прикатывание облицовок;
• выдержка.
Если кэшированием наносят пленку с декоративным тиснением, давление валов ослабляют во избежание повреждения рельефа изображения.
При кэшировании в первоначальный момент времени в процессе прикатывания происходит схватывание клея, а окончательное отверждение клеевого слоя происходит в процессе последующей выдержки облицованного материала[3].
|
|
Двойное оплодотворение у цветковых растений: Оплодотворение - это процесс слияния мужской и женской половых клеток с образованием зиготы...
Организация стока поверхностных вод: Наибольшее количество влаги на земном шаре испаряется с поверхности морей и океанов (88‰)...
Индивидуальные и групповые автопоилки: для животных. Схемы и конструкции...
Адаптации растений и животных к жизни в горах: Большое значение для жизни организмов в горах имеют степень расчленения, крутизна и экспозиционные различия склонов...
© cyberpedia.su 2017-2024 - Не является автором материалов. Исключительное право сохранено за автором текста.
Если вы не хотите, чтобы данный материал был у нас на сайте, перейдите по ссылке: Нарушение авторских прав. Мы поможем в написании вашей работы!