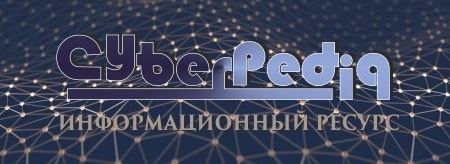
Двойное оплодотворение у цветковых растений: Оплодотворение - это процесс слияния мужской и женской половых клеток с образованием зиготы...
Кормораздатчик мобильный электрифицированный: схема и процесс работы устройства...
Топ:
Определение места расположения распределительного центра: Фирма реализует продукцию на рынках сбыта и имеет постоянных поставщиков в разных регионах. Увеличение объема продаж...
Марксистская теория происхождения государства: По мнению Маркса и Энгельса, в основе развития общества, происходящих в нем изменений лежит...
Теоретическая значимость работы: Описание теоретической значимости (ценности) результатов исследования должно присутствовать во введении...
Интересное:
Средства для ингаляционного наркоза: Наркоз наступает в результате вдыхания (ингаляции) средств, которое осуществляют или с помощью маски...
Финансовый рынок и его значение в управлении денежными потоками на современном этапе: любому предприятию для расширения производства и увеличения прибыли нужны...
Наиболее распространенные виды рака: Раковая опухоль — это самостоятельное новообразование, которое может возникнуть и от повышенного давления...
Дисциплины:
![]() |
![]() |
5.00
из
|
Заказать работу |
|
|
Раскрой плитных и листовых древесных материалов
При производстве изделий широко используют различные материалы на основе древесины (ДВП, ДСП, МДФ, фанера). На предприятиях эти материалы изготавливают в виде листов или плит, форматные характеристики которых регламентируются стандартами. Стандартные форматы листов и плит раскраивают на заготовки.
Раскрой плитных и листовых материалов проводить проще, чем раскрой пиломатериалов, поскольку они имеют заданные стандартом показатели качества и нет необходимости в процессе раскроя отслеживать наличие скрытых дефектов, изменение цвета и формы.
Основными критериями, в соответствии с которыми проводят процесс раскроя плитных и листовых материалов, являются количество и размеры заготовок.
Раскрой плитных и листовых материалов в зависимости от типа производства и по назначению получаемых заготовок делят на три вида: индивидуальный, комбинированный и смешанный. При индивидуальном раскрое каждый формат материала раскраивают на одинаковые но типу и размеру заготовки. При комбинированном раскрое из одного формата можно выкраивать различные заготовки. Смешанный раскрой предполагает комбинацию индивидуального и комбинированного типов раскроя для отдельных случаев.
Эффективность раскроя оценивают показателем выхода заготовок в зависимости от рациональности использования материала. Выход заготовок зависит от технологии раскроя материалов и используемого для раскроя оборудования.
Для рационального раскроя плит и листов на предприятиях разрабатывают карты раскроя. Карта раскроя представляет собой графический эскиз расположения заготовок на стандартном формате раскраиваемого материала. При составлении карт раскроя учитывают размеры заготовок, формат материала, ширину пропилов и технологические возможности применяемого оборудования. На формате раскраиваемого материала располагают все выкраиваемые из него заготовки (чаще всего в масштабе).
|
Раскрой листовых и плитных материалов осуществляют на форматно- раскроечном оборудовании, технологические особенности которого зависят от мощностей предприятия, вида раскроя, сложности карты раскроя. Раскраивают материалы дисковыми пилами диаметром 300—400 мм с твердосплавными пластинами. Скорость резания и подачи зависит от типа раскраиваемого материала.
Облицовывание заготовок
Одну или обе поверхности древесных и плитных материалов часто оклеивают тонкими текстурированными пленками или слоем строганого шпона из ценных пород древесины. Этот процесс называют облицовыванием. Облицовывание используют при изготовлении недорогой мебели и столярных изделий, имеющих красивый внешний вид. Облицовывание позволяет получить крупные форматы заготовок с яркой текстурой и насыщенным цветом, но без значительного расхода ценных пород древесины. Облицованный материал представляет собой прочную многослойную клееную конструкцию.
Для облицовывания используют основной материал, клей и облицовочный слой.
Основными материалами, которые чаще всего облицовывают, являются пиломатериалы пород древесины с маловыразительной текстурой, ДСП, ДВП, МДФ, столярные щиты и плиты, а также гнутоклееные заготовки. Клей для облицовывания поверхностей выбирают, исходя из свойств основного материала и слоя покрытия, но чаще всего это клеи на основе карбами- доформальдегидных смол, столярные клеи, 11ВА, пленочные клеи и др. В качестве облицовочного слоя используют строганый шпон, полимерные пленки и пропитанную полимерными составами бумагу. Также применяют различные ткани, искусственную кожу, металлическую фольгу и другие слои материалов, которые можно наклеить па поверхность древесины.
|
Одностороннее облицовывание применяют к плитным материалам и заготовкам, имеющим толщину свыше 10 мм. Тонкие материалы облицовывают с двух сторон во избежание коробления листа, поскольку в процессе облицовывания в материале возникают внутренние напряжения. Двусторонняя обработка позволяет компенсировать напряжения, и материал не деформируется.
Облицовывание может быть однослойным и двухслойным. При двухслойном облицовывании используют два слоя облицовки — подслой и лицевой слой. Слои могут быть различными как по составу, так и по толщине. В качестве подслоя используют недорогие материалы, накладываемые на основу для выравнивания поверхности: лущеный шпон, ткань, бумагу и др. Лицевой слой, более тонкий и дорогой, накладывают на подслой.
Технологическая стадия облицовывания состоит из следующих операций: подготовка основы; подготовка покрытия; подготовка клея; наклеивание.
В зависимости от конструкции изделия, формы заготовок и общего технологического процесса производства стадия облицовывания производится либо до раскроя материала, либо облицовывают уже полученные заготовки. Облицовывать можно также сборочные единицы. Заготовки из пиломатериалов облицовывают после стадии обработки в размер.
Плитные материалы сначала калибруют по толщине, а затем облицовывают. Детали сложного профиля, получаемые поэтапной механической обработкой, облицовывают после фрезерования по форме, после чего выполняют операции формирования шипов и проушин, высверливания отверстий и др.
Гнутоклееные детали облицовывают в процессе формирования общего профиля, одновременно с процессом склеивания. Для этого применяют пресс-формы с эластичными элементами. Процесс склеивания при облицовывании криволинейных поверхностей ускоряют при использовании различных нагревательных систем (ТВЧ, инфракрасное излучение и т.п.).
Облицовывать заготовки, как и склеивать, можно как холодным, так и горячим способом.
Подготовка основного материала. Поверхность заготовки, подлежащей облицовыванию, выравнивают с помощью абразивных материалов, устраняя неровности и дефекты, способные снизить прочность склеивания. При необходимости крупные дефекты, такие как сколы, выпавшие сучки, трещины, заполняют шпатлевкой или высверливают, закрывая отверстие вклеиваемой вставкой. Шероховатость поверхности доводят до того уровня, который позволяет провести качественное склеивание, не отображаясь на лицевом слое. Этот уровень, прежде всего, зависит от типа лицевого слоя. Толщина слоя облицовки в 2—3 раза должна превышать высоту неровностей профиля поверхности основы. Если уровень шероховатости не позволяет нанести слой облицовки без заметных искажений последнего, то используют подслой.
|
С поверхности удаляют различные загрязнения и просушивают ее. Влажность основного материала должна быть ниже равновесной влажности на 1—2%, поскольку при нанесении клея будет происходить неизбежное увлажнение поверхности.
Подготовка слоя облицовки зависит от состава и качества наносимого материала. Слой должен быть однородным по толщине, без отверстий и разрывов. Не допускаются крупные инородные включения, загрязнения и следы увлажнения на поверхности наносимых материалов. Степень влажности для облицовки зависит от тина наносимого материала. Для шпона она должна составлять 8—10%.
Для облицовывания часто используют пленку на основе поливинилхлорида (ПВХ), ее закупают на предприятии-изготовителе в виде рулона. Пленки имеют толщину от 0,15 до 0,4 мм.
Распространенным материалом для облицовывания являются пленки на основе бумаги плотностью от 90 до 130 г/м3, пропитанной термореактивными меламиноформальдегидными, карбамидными или полиэфирными смолами. Толщина бумажных термореактивных пленок — от 0,14 до 0,21 мм, причем до 80% состава их приходится на полимерные смолы.
Пленки, как бумажные, так и полимерные, могут иметь облагороженную или необлагороженную поверхность. Облагороженная поверхность не требует дальнейшей отделки, так как имеет защитный слой. Необлагорожен- ная пленка подлежит дальнейшей отделке. Для повышения декоративных свойств изделий на пленки наносят рисунок с тиснением, имитирующий текстуру ценных пород древесины.
Пленки могут быть однослойные или многослойные. В мебельном производстве чаще всего применяют двухслойные пленки.
|
Пленки должны быть эластичными и иметь способность скрывать повышенную шероховатость основного материала (особенно это важно для облицовывания ДСП).
Подготовка клея выполняется так же, как и при склеивании заготовок (см. параграф 5.4).
Наклеивание шпона на поверхность основы проводится но технологии, аналогичной склеиванию (см. параграф 5.4).
Пленки на поверхность заготовок с предварительно нанесенным клеем наносят методом кэширования — непрерывного накатывания в вальцовых прессах. Для кэширования используют клеи на основе карбамидных смол, поливинилацетата и эластомеров.
Кэширование может быть холодным, теплым и горячим. При холодном кэшировании облицовка прикатывается к основе при комнатной температуре, без подвода тепла к соединяемым материалам. При теплом кэшировании поверхность основного материала нагревают до нанесения клея. Горячее кэширование предполагает как предварительный нагрев поверхности заготовки, так и нагрев валиков пресса до 200°С в процессе накатки. Горячее кэширование применяют в том случае, если клеевой состав изготовлен без использования влаги (клеи-расплавы, клеящие пленки).
Технологический процесс кэширования состоит из следующих стадий:
• укладка основы;
• очистка поверхности от поверхностных загрязнений (пыли, стружки);
• нанесение клея;
• термообработка поверхности (при теплом и горячем кэшировании);
• формирование пакета;
• прикатывание облицовок;
• выдержка.
Если кэшированием наносят пленку с декоративным тиснением, давление валов ослабляют во избежание повреждения рельефа изображения.
При кэшировании в первоначальный момент времени в процессе прикатывания происходит схватывание клея, а окончательное отверждение клеевого слоя происходит в процессе последующей выдержки облицованного материала[3].
Окончательная обработка
В стадию окончательной механической обработки входят технологические операции, предусматривающие формирование различных конструктивных элементов в зависимости от требуемой конфигурации детали. Это может быть нарезание шипов и выборка проушин, фрезерование контура, профилей и рельефа, высверливание отверстий.
Технологические операции формирования детали следуют друг за другом в том порядке, который обеспечивает наименьшие затраты энергии и труда. Последовательность операций при формировании детали из чистовой заготовки зависит от требуемой формы детали, от наличия, количества и взаимного расположения в ней конструктивных элементов, а также от технических условий предприятия и характера производственного процесса.
Чаще всего на производстве используют следующую последовательность технологических операций. Сначала формируют соединительные шины, поскольку они могут выполнять функцию дополнительных базовых поверхностей. Затем следуют операции фрезерования профилей сечения, контуров по периметру, скругление кромок и т.п. После выбирают пазы, гнезда, сверлят отверстия.
|
Фрезерование
Наиболее универсальной операцией технологического процесса деревообработки является фрезерование. Фрезерованием можно получить любую требуемую форму, сформировать любой конструктивный элемент. Фрезерованием обрабатывают заготовки из пиломатериалов и из плитных материалов, а также уже собранные щитовые и рамные конструкции.
В процессе окончательной обработки заготовок фрезерование используют для получения различных профилей сечения, контура и рельефа заготовки.
Фрезерование осуществляют на фрезерных станках различных конструкций. В качестве инструментов используют фрезы — многолезвийные инструменты разных типов.
Существует две принципиальных схемы фрезерования, которые различаются положением режущей кромки инструмента относительно оси вращения: цилиндрическим и торцовым (рис. 5.12). Сочетанием этих двух схем получают различные типы комбинированного, конического и фасон- но го фрезерования.
Рис. 5.12. Основные схемы фрезерования:
а — цилиндрическое; б — торцовое; 1 — поверхность резания; 2 — обработанная поверхность; 3 — обрабатываемая поверхность; v — направление вращения инструмента; S — направление подачи заготовки1
При цилиндрическом фрезеровании лезвия инструмента параллельны оси вращения и при вращении они описывают цилиндрические поверхности. При торцовом фрезеровании режущие кромки расположены перпендикулярно оси вращения инструмента п при вращении они описывают плоские круговые поверхности.
В зависимости от взаимного направления движения заготовки и инструмента фрезерование может быть попутным и встречным. При встречном фрезеровании движение резца осуществляется навстречу движению подачи заготовки (рис. 5.13, а), а при попутном фрезеровании направление подачи заготовки совпадает с направлением вращения инструмента (рис. 5.13, б).
Рис. 5.13. Схемы фрезерования:
а — встречное; б — попутное; v — направление вращения инструмента;
5 — направление подачи заготовки1
По характеру обрабатываемой поверхности фрезерование можно разделить на три типа:
· 1) фрезерование прямолинейных заготовок по линейке;
· 2) фрезерование криволинейных заготовок с кольцом по шаблону;
· 3) фрезерование поверхности сложной кривизны.
Фрезерование прямолинейных заготовок но направляющей линейке (рис. 5.14) выполняют на вертикально-фрезерных станках с нижним расположением шпинделя. По этой схеме выполняют такие виды работ, как формирование и выверка гладких поверхностей и прямых плоскостей (в том числе кромок); сквозное и несквозное фрезерование профиля, формирование фасонного профиля постоянного сечения на прямолинейных заготовках (плинтуса, молдинги, карнизы и др.) с помощью профильных фрез. Для фрезерования по такой схеме применяют линейку с прорезыо для фрезы.
Рис. 5.14. Фрезерование кромки прямолинейной заготовки по линейке:
1 — фреза; 2 — рабочий стол; 3 — направляющая линейка с прорезью; 4 — заготовка; v — направление вращения инструмента; S — направление подачи заготовки2
Криволинейные поверхности, как гладкие, так и профильные, фрезеруют с помощью упорного кольца, установленного на рабочий шпиндель непосредственно под фрезой, и шаблона (рис. 5.15). Упорное кольцо 1, диаметр которого выбирают около 70—75 мм, вращается вместе со шпинделем. Шаблон для фрезерования 3 представляет собой щит толщиной 25—50 мм, направляющая кромка которого имеет ту конфигурацию, которую необходимо придать обрабатываемой заготовке.
Рис. 5.15. Схема фрезерования криволинейных поверхностей но кольцу и шаблону:
а — фрезерование криволинейных деталей; б — установка инструмента для фрезерования с нижним расположением кольца и шаблона; в — установка инструмента для фрезерования с верхним расположением кольца и шаблона; 1 — упорное кольцо; 2 — фреза; 3 — шаблон; 4 — обрабатываемая заготовка; 5 — линейка шаблона; 6 — прижим; 7 — упор;
8 — направляющая кромка шаблона[3]
Заготовку, предварительно опиленную на ленточнопильном станке в соответствии с кривизной кромки и с припуском на фрезерование, укладывают на шаблон (см. рис. 5.15, б) или на рабочий стол станка (см. рис. 5.15, в). На шаблоне или рабочем столе для фиксации заготовки установлены упоры 7 и одно или несколько прижимных устройств 6.
Заготовку, прижатую к шаблону, подают на вращающуюся фрезу 2 и плотно прижимают кромку шаблона 8 к упорному кольцу 1. Шаблон в процессе фрезерования перемещают относительно инструмента со скоростью 4—8 м/мин. Вращаясь, упорное кольцо повторяет кривизну кромки шаблона, передавая движение на фрезу. Соответственно кромка обрабатываемой заготовки детали приобретает форму кромки шаблона.
Фрезеруемая кромка может иметь любую кривизну, ограничением служит лишь радиус закруглений, который не может быть меньше радиуса упорного кольца.
Описанным способом выполняют обработку как гладких, так и профильных кромок (см. рис. 5.15, б, в).
Фрезерование сложных рельефов выполняют посредством оборудования с программно-числовым управлением (станки ЧПУ). Фрезерные станки с ЧПУ представляют собой высокотехнологичное современное оборудование, позволяющее получать изделия высокого качества.
Станки с ЧПУ управляются электронной системой, имеющей прямую связь, посредством специального программного обеспечения, с компьютером. Программное обеспечение разрабатывается специально для станков и поставляется производителем вместе с основными рабочими системами. Программное обеспечение принимает с компьютера векторное изображение, разработанное в графических пакетах программ, и переводит его в специализированный G-код, отвечающий за координацию перемещений управляющих режущим инструментом микрошаговых двигателей.
Инструментами для работы на станках с ЧПУ служат цилиндрические твердосплавные или алмазные концевые фрезы.
Алгоритм построения детали со сложным профилем включает в себя: построение конфигурации в графическом редакторе (AutoCad, CorelDraw и др.); выставление необходимых для работы режимов и параметров работы станка; запуск программы; работу станка в автоматическом режиме. Функции оператора станка в процессе работы сводятся к визуальному контролю процесса.
Гнездообразование
Операции выборки гнезд (глухих пазов) и высверливания отверстий в заготовке чаще всего завершают стадию окончательной обработки чистовой заготовки перед подготовкой ее поверхности к отделке.
Для выборки гнезд применяют различные типы оборудования.
Выборка гнезд концевыми фрезами на фрезерных станках является наиболее распространенной схемой гнездообразования. Пазы, полученные способом фрезерования, имеют скругления боковых поверхностей (см. рис. 5.9).
Для установки петлей, замков, щеколд и других элементов, форма которых не может быть изменена и подогнана под форму скругленных пазов, применяют операции выборки пазов на специальном цепнодолбежном оборудовании (рис. 5.16).
Режущим инструментом в цепнодолбежных станках является фрезерная цепь (см. рис. 5.16, б), натянутая на ролик 1 и звездочку 3. В процессе работы цепь скользит по направляющей линейке 2. Цепь 4 состоит из отдельных звеньев, которые шарнирно соединены между собой (см. рис. 5.16, в).
Рис. 5. 16. Цепнодолбежный станок:
а — внешний вид; 6 — устройство цепно-фрезерной головки: 1 — направляющий ролик; 2 — направляющая линейка; 3 — ведущая звездочка; 4 — фрезерная цепь; 5 — ползун; 6 — болты; в — звенья фрезерной цепи: 1 — среднее звено; 2 — крайние звенья; 3 — оси- заклепки; г — конфигурация гнезда1
При вращении звездочки цепь приводится в движение и, соприкасаясь с заготовкой, выбирает объем материала в форме прямоугольного гнезда со скругленным дном (см. рис. 5.16, г).
Для обеспечения плотности соединения с шипом необходимо выбирать гнездо в глубину с запасом, не меньшим, чем величина радиуса концевого ролика плюс толщина фрезерной цени.
Ценнодолбежные станки производительны и обеспечивают требуемую точность для изготовления столярных изделий. Недостатком их работы является наличие сколов в зоне выхода фрезерной цени из материала, поэтому их не используют при выборке гнезд малых размеров в облицованных деталях. Для этой цели используют сверлильно-пазовальные станки.
Для выборки пазов (гнезд) на сверлильно-пазовальных станках используют сверло соответствующего диаметра. Режущий инструмент, кроме вращательного движения, имеет осевую и боковую подачи относительно заготовки.
Принцип выборки пазов на сверлильно-пазовальном станке заключается в том, что сначала с помощью спирального сверла высверливают два отверстия на концах будущего паза, ограничивая тем самым его размер. Затем, не вынимая сверла, включают поперечную подачу и соединяют оба отверстия, расчищая тем самым весь паз.
Сверление отверстий
Сверление круглых отверстий выполняют на универсальных одно- или многошпиндельных вертикально-сверлильных станках, а также на много- шпиндельном специализированном оборудовании. Инструментом для сверления круглых отверстий являются спиральные сверла различных видов.
На рис. 5.17 приведены конфигурации и принципиальные схемы формирования пазов и отверстий на различном оборудовании. [1]
Рис. 5.17. Отверстия, полученные на станках:
а — в — сверлильных; г — сверлильно-пазовальных; д, е — цепнодолбежных; ж — схема формирования круглого гнезда сверлением; з — выборка паза пазовым фрезерованием; и — формирование гнезд на станках с возвратно-поступательным боковым движением фрезы; к — формирование гнезд на станках с колебательным боковым движением фрезы1
Подготовка поверхности деталей к отделке
После выполнения операций окончательной обработки чистовой заготовки получают готовую деталь. Однако требования к качеству поверхности готовой детали обычно бывают выше, чем могут обеспечить технические возможности процессов обработки фрезерованием. Поэтому после окончательной обработки в технологический процесс вводят дополнительную технологическую операцию зачистки поверхности готовых деталей для подготовки их к отделке.
Детали изделий, поступающих на стадию отделки полиэфирными лаками и эмалями, должны иметь поверхности с шероховатостью Rm = 32 мкм. Покрытия нитроцеллюлозными и полиуретановыми лаками и эмалями требует еще более гладкой поверхности, с шероховатостью Rm =16 мкм. Кроме соблюдения степени шероховатости поверхности важно соблюдать условие отсутствия на поверхности таких дефектов механической обработки, как волнистость, сколы, заусенцы, ворсистость.
Для обеспечения этих требований механическая обработка готовых деталей завершается операциями циклевания и шлифования. При проведении этих процессов с поверхности детали снимается минимальный слой материала, что нс влияет на точность размеров детали. Основной целью операций зачистки является достижение требуемых параметров шероховатости поверхности.
Циклеванием называют процесс соскабливания неровностей с поверхности заготовки специальным ножом — циклей. Шлифование выполняют с применением многорезцовых абразивных инструментов — наждачной шкурки (рис. 5.18).
Рис. 5.18. Строение абразивной шкурки:
1 — зерна абразива; 2 — связка; 3 — основа'
Основой для шкурок служат бумага, хлопчатобумажные ткани либо композитные и армированные основы, которые обеспечивают повышенную износостойкость шкурки. Связкой служит мездровый или синтетический клей на основе смол; соответственно шлифовальные шкурки делят на неводоупорные и водоупорные. Зерна абразива выполнены из электрокорунда, карбида кремния или других твердых абразивных материалов.
Шлифуют пиломатериалы и древесные материалы на шлифовальных станках абразивной лентой. Шлифовальные станки отличаются взаимным расположением и сочетанием рабочих органов, размерами, принципом подачи. Абразивная шкурка может надеваться на барабан (барабанный шлифовальный станок), на вальцы (вальцовый шлифовальный станок), крепиться на диск (дисковый шлифовальный станок) или охватывает два шкива бесконечной лентой (ленточный шлифовальный станок). Соответственно в зависимости от вида шлифовального оборудования различают цилиндровое, дисковое и ленточное шлифование.
Само шлифование является сложным н трудоемким процессом, в котором необходимо сочетать п взаимосвязывать многие факторы, влияющие на конечный результат. Шероховатость поверхности после шлифования зависит от скорости обработки, физических свойств материала, номера шкурки, исходного состояния поверхности шероховатости, скорости подачи, усилия прижима инструмента к поверхности, продолжительности обработки и др.
Раскрой плитных и листовых древесных материалов
При производстве изделий широко используют различные материалы на основе древесины (ДВП, ДСП, МДФ, фанера). На предприятиях эти материалы изготавливают в виде листов или плит, форматные характеристики которых регламентируются стандартами. Стандартные форматы листов и плит раскраивают на заготовки.
Раскрой плитных и листовых материалов проводить проще, чем раскрой пиломатериалов, поскольку они имеют заданные стандартом показатели качества и нет необходимости в процессе раскроя отслеживать наличие скрытых дефектов, изменение цвета и формы.
Основными критериями, в соответствии с которыми проводят процесс раскроя плитных и листовых материалов, являются количество и размеры заготовок.
Раскрой плитных и листовых материалов в зависимости от типа производства и по назначению получаемых заготовок делят на три вида: индивидуальный, комбинированный и смешанный. При индивидуальном раскрое каждый формат материала раскраивают на одинаковые но типу и размеру заготовки. При комбинированном раскрое из одного формата можно выкраивать различные заготовки. Смешанный раскрой предполагает комбинацию индивидуального и комбинированного типов раскроя для отдельных случаев.
Эффективность раскроя оценивают показателем выхода заготовок в зависимости от рациональности использования материала. Выход заготовок зависит от технологии раскроя материалов и используемого для раскроя оборудования.
Для рационального раскроя плит и листов на предприятиях разрабатывают карты раскроя. Карта раскроя представляет собой графический эскиз расположения заготовок на стандартном формате раскраиваемого материала. При составлении карт раскроя учитывают размеры заготовок, формат материала, ширину пропилов и технологические возможности применяемого оборудования. На формате раскраиваемого материала располагают все выкраиваемые из него заготовки (чаще всего в масштабе).
Раскрой листовых и плитных материалов осуществляют на форматно- раскроечном оборудовании, технологические особенности которого зависят от мощностей предприятия, вида раскроя, сложности карты раскроя. Раскраивают материалы дисковыми пилами диаметром 300—400 мм с твердосплавными пластинами. Скорость резания и подачи зависит от типа раскраиваемого материала.
|
|
Адаптации растений и животных к жизни в горах: Большое значение для жизни организмов в горах имеют степень расчленения, крутизна и экспозиционные различия склонов...
Таксономические единицы (категории) растений: Каждая система классификации состоит из определённых соподчиненных друг другу...
Археология об основании Рима: Новые раскопки проясняют и такой острый дискуссионный вопрос, как дата самого возникновения Рима...
Наброски и зарисовки растений, плодов, цветов: Освоить конструктивное построение структуры дерева через зарисовки отдельных деревьев, группы деревьев...
© cyberpedia.su 2017-2024 - Не является автором материалов. Исключительное право сохранено за автором текста.
Если вы не хотите, чтобы данный материал был у нас на сайте, перейдите по ссылке: Нарушение авторских прав. Мы поможем в написании вашей работы!