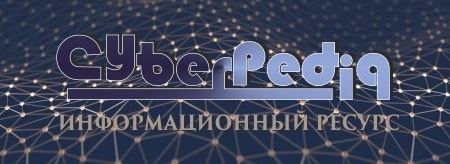
Механическое удерживание земляных масс: Механическое удерживание земляных масс на склоне обеспечивают контрфорсными сооружениями различных конструкций...
Опора деревянной одностоечной и способы укрепление угловых опор: Опоры ВЛ - конструкции, предназначенные для поддерживания проводов на необходимой высоте над землей, водой...
Топ:
Выпускная квалификационная работа: Основная часть ВКР, как правило, состоит из двух-трех глав, каждая из которых, в свою очередь...
Устройство и оснащение процедурного кабинета: Решающая роль в обеспечении правильного лечения пациентов отводится процедурной медсестре...
Теоретическая значимость работы: Описание теоретической значимости (ценности) результатов исследования должно присутствовать во введении...
Интересное:
Отражение на счетах бухгалтерского учета процесса приобретения: Процесс заготовления представляет систему экономических событий, включающих приобретение организацией у поставщиков сырья...
Наиболее распространенные виды рака: Раковая опухоль — это самостоятельное новообразование, которое может возникнуть и от повышенного давления...
Распространение рака на другие отдаленные от желудка органы: Характерных симптомов рака желудка не существует. Выраженные симптомы появляются, когда опухоль...
Дисциплины:
![]() |
![]() |
5.00
из
|
Заказать работу |
|
|
Все жиры, поступающие на варку мыла, должны быть свободны от воды и механических примесей. В связи с этим компоновка баков должна обеспечить возможность подогрева, фильтрации жиров и слива отстоявшейся влаги. Смеси жиров согласно рецептуре мыла готовят в композиционном баке с мешалкой, обеспечивающей интенсивное и равномерное перемешивание, и греющими змеевиками.
Растворы кальцинированной и каустической соды готовят в стальных баках, оборудованных мешалкой и паровым барботером.
В зависимости от применяемого сырья, вида и сорта мыла, а также требований к его качеству варку ведут различными способами, среди них различают два основных: прямой и кос венный [1].
Прямой способ заключается в том, что путем нейтрализации жировой смеси растворами соответствующих содопродуктов получают мыльный клей, который по концентрации жирных кислот и содержанию электролитов соответствует пределам, установленным техническими условиями. Сваренное таким образом мыло направляют на дальнейшую обработку без дополнительных операций. Прямой метод широко применяют при варке мыла из хорошо очищенного жирового сырья.
Косвенный способ заключается в том, что сваренный прямым методом мыльный клей обрабатывают растворами электролитов, под действием которых происходит разделение мыльной массы на две фазы (ядро и подмыльный щелок или ядро и подмыльный клей) или на три фазы (ядро, подмыльный клей и подмыльный щелок).
Полученное в результате высаливания мыльное ядро с содержанием 60…63% жирных кислот в виде мыла подвергают затем охлаждению, сушке и механической обработке, как и мыло, сваренное прямым методом.
Косвенный способ применяют при варке хозяйственных мыл из жирового сырья, содержащего различные примеси, при использовании соапстоков, темных сортов технических животных жиров и пр.; при варке мыла из нейтральных жиров, что дает возможность утилизировать глицерин, переходящий в подмыльный щелок; при выработке всех видов туалетных мыл из жирных кислот и нейтральных жиров.
|
Приготовление основы туалетного мыла из жирных кислот косвенным периодическим способом слагается из следующих технологическихопераций: карбонатное омыление и последующее каустическое доомыление жировой смеси; высаливание мыльного клея; шлифование, отстаивание, слив туалетной основы.
Карбонатное омыление проводят как в чистом котле, так и на клеевом остатке. В котел загружают расчетное количество раствора соды концентрацией 28…30% и постепенно при энергичном кипячении острым паром подают жирные кислоты. Для предотвращения свертывания мыльной массы в процессе нейтрализации и снижения ее вязкости в котел добавляют 1…2% поваренной соли в виде 20%-ного раствора. После загрузки всей смеси кипячение продолжают в течение 1,5…2 ч [2].
По окончании карбонатного омыления содержание углекислой соды в мыльной массе не должно превышать 0,5%; поверхность мыла темнеет, на ней не видно лопающихся пузырьков газа.
Каустическое доомыление карбонатной массы осуществляют раствором каустической соды с целью нейтрализации оставшихся жирных кислот и омыления нейтрального жира. Раствор едкой щелочи концентрацией 40…44% вводят в котел порциями при непрерывном кипячении мыльной массы острым паром. Омыление проводят при постоянном наличии избытки свободной щелочи для предотвращения образования кислого мыла. Каустическое омыление считается законченным, когда содержание свободной едкой щелочи в мыльной массе после контрольного кипячения (в течение 30 мин) не изменяется.
В зависимости от отношения мыла к действию электролитов жиры и жирозаменители, применяемые в мыловарении, подразделяют на ядровые и клеевые.
|
Высаливание мыл может быть полным и неполным:
полное высаливание - когда в мыльный клей вводят электролиты в количестве, обеспечивающем достижение предельной концентрации, с последующим разделением системы на ядро и подмыльный щелок;
частичное высаливание - когда концентрация электролитов ниже предельной, при этом в зависимости от концентрации электролитов в мыльной массе система разделяется на две или три фазы (ядро и подмыльный клей или ядро, подмыльный клей и подмыльный щелок).
После полного высаливания мыльного клея практически все мыло переходит в ядровую фазу. При этом концентрация жирных кислот в мыле (ядре) увеличивается от 48 до 63%. В подмыльный щелок уходит основная часть электролитов (строгих закономерностей соотношения электролита между ядром и под мыльным щелоком нет), а также различные сопутствующие вещества и примеси. Подмыльный щелок содержит 0,5… 1% растворенного мыла (преимущественно низкомолекулярных кислот) [15].
При шлифовании достигается дальнейшая очистка мыла от примесей, снижение содержания электролитов в ядре, полученном при полном высаливании, и улучшение структуры мыла. До шлифования ядро состоит из отдельных зерен, представляет собой неоднородную массу, после шлифования превращается в гладкую гомогенную массу с несколько большим содержанием воды и меньшим содержанием электролитов.
Шлифование производят горячей водой или растворами щелочи и поваренной соли, которые дают отдельными порциями при кипячении массы острым паром. Содержание свободной едкой щелочи поддерживают в пределах 0,5…0,8%, содержание хлористого натрия - от 0,7 до 1% (применение раствора соли для шлифования менее желательно, так как способствует повышению содержания ее в готовом мыле, повышая его хрупкость) [1].
Шлифование заканчивается через час интенсивного кипячения после загрузки в котел последней порции воды или раствора электролитов. По окончании шлифования в мыльном клее должно содержаться 50…54% жирных кислот [30].
Отстаивание мыльной массы после шлифования производится длительно, с разделением на две фазы - ядро (мыльная основа) и подмыльный клей.
Пилирование - очень важный этап производства туалетного мыла. Осуществляют его путем тщательного и многократного перетирания высушенной мыльной стружки с целю получения плотной монолитной массы, обогащения мыла β-модификацией и повышения его пластических свойств.
|
Установлено существование четырех полиморфных превращений мыла: α, β, δ и ω. Каждая из этих модификации стабильна в определенной области температур, обладает определенными свойствами, и преимущественное накопление одной из них в мыле существенно вияет на его качество.
Мыла в β-модификации обладают повышенной растворимостью, хорошей пенообразующей способностью. Они более тверды, чем мыла в δ - и ω - модификациях, мало набухают, более экономично расходуются. При высыхании мыло сохраняет свою форму, не образуют трещин и не расслаивается [1].
Сваренная мыльная основа затем подается на механическую обработку (пилирование).
Пилирование в строго определенных условиях (температура мыльного бруска, выходящего из шнековых прессов, давление при спрессовании) способствуют обогащению мыла β-модификацией.
На предприятиях России, выпускающих туалетное мыло, широко распространена линия ЭЛМ производительностью 2 т/ч. Разработана автоматизированная линия марки А1-МЛТ производительностью 4 т/ч, предназначенная для непрерывной выработки туалетного мыла с содержанием жирных кислот в готовом мыле до 78%. Внедрены линии фирмы «Маццони» производительностью 4 т/ч по выработке высококачественного обернутого туалетного мыла массой 100, 150 и 200 г., различной формы с содержанием жирных кислот в готовом мыле до 80%.
Особенностью линий фирмы «Маццони» является их большая производительность, высокий уровень механизации и автоматизации процессов от подачи мыльной основы до транспортировки готовой продукции на склад, высокая единичная производительность отдельных машин, возможность вырабатывать высококонцентрированные туалетные мыла с содержанием 80% жирных кислот.
Несмотря на перечисленные преимущества линии «Маццони» в дипломном проекте для обработки туалетного мыла предусматривается отечественная линия ЭЛМ. Это объясняется дороговизной импортного оборудования линии фирмы «Маццони».
Линия ЭЛМ включает следующие основные узлы: вакуум-сушильная камера для охлаждения и сушки туалетной основы под вакуумом; двойной шнек-пресс для предварительной обработки (шлифования); смесительный шнек-пресс для непрерывного дозирования и смешивания мыла с добавками; двухступенчатый вакуумный шнек-пресс для окончательной механической обработки и формования туалетного мыла; автомат для резки и штамповки мыла.
|
Одно из основного оборудование - вакуум-сушильная камера, предназначенная для превращения жидкой основы в твердое мыло. В ней происходит сушка, кристаллизация и охлаждения жидкого мыла. Все процессы совмещен и протекают под разрежением без соприкосновения продукта с воздухом. В вакуум-сушильной камере горячее мыло распыляется с помощью форсунок. При этом мыло быстро теряет часть влаги, охлаждается и подсушивается. Оседающие на стенках камеры в виде тонкой пленки мыло снимается укрепленными на валу скребками (ножами) и в форме стружки подается шнек-пресс.
Производительность камеры по стружке 2 т/ч, остаточное давление 2…5,3 кПа [2].
Двойной шнек-пресс предназначен для предварительной механической обработки (пилирования) мыльной стружки, выходящей из вакуум-сушильной камеры, ее уплотнения, частичного подсушивания и получения однородных гранул, удобных для транспортировки.
Производительность двойного шнек-пресса составляет 2 т/ч.
Смесительный шнек-пресс предназначен для непрерывного дозирования и смешивания мыла с красителями, отдушкой и другими добавками (ингредиентами).
Производительность смесительного шнек-пресса - 1 т/ч мыла.
Двухступенчатый вакуумный шнек-пресс служит для окончательной механической обработки мыла.
Из вакуум-камеры мыльная масса в виде гранул подается на нижний шнек-пресс, имеющий такой же диаметр, что и верхний шнек-пресс. В нижнем шнек-прессе мыло спрессовывается под давлением, превращается в монолитную пластичную массу и выходит из отверстия в виде бесконечного бруска заданного поперечного сечения. Производительность двухступенчатого вакуумного шнек-пресса 1 т/ч мыла.
Автомат для резки мыла предназначен для непрерывной резки бруска мыла на куски определенной длины.
Принцип действия автомата заключается в следующем. Брусок мыла попадает на подстилающий транспортери по мере продвижения сверху в брусок начинают врезаться пластинчатые ножи. Одновременно в работеучаствуют 3 или 4 ножа, которые режут мыльный брусок на куски. Отрезанные куски направляются на транспортер, подающий их на штамп-пресс. Производительность автомата 1 т/ч мыла.
Таким образом, в дипломном проекте предусмотрена варка мыльной основы в котлах косвенным способом, затем отстаивание в мылосборниках, а затем механическая обработка мыльной основы на отечественной линии ЭЛМ.
|
|
Таксономические единицы (категории) растений: Каждая система классификации состоит из определённых соподчиненных друг другу...
Типы оградительных сооружений в морском порту: По расположению оградительных сооружений в плане различают волноломы, обе оконечности...
Своеобразие русской архитектуры: Основной материал – дерево – быстрота постройки, но недолговечность и необходимость деления...
Наброски и зарисовки растений, плодов, цветов: Освоить конструктивное построение структуры дерева через зарисовки отдельных деревьев, группы деревьев...
© cyberpedia.su 2017-2024 - Не является автором материалов. Исключительное право сохранено за автором текста.
Если вы не хотите, чтобы данный материал был у нас на сайте, перейдите по ссылке: Нарушение авторских прав. Мы поможем в написании вашей работы!