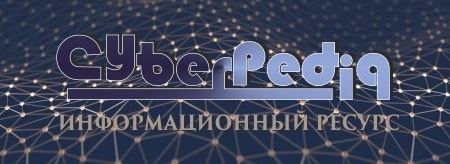
Двойное оплодотворение у цветковых растений: Оплодотворение - это процесс слияния мужской и женской половых клеток с образованием зиготы...
Организация стока поверхностных вод: Наибольшее количество влаги на земном шаре испаряется с поверхности морей и океанов (88‰)...
Топ:
Марксистская теория происхождения государства: По мнению Маркса и Энгельса, в основе развития общества, происходящих в нем изменений лежит...
Теоретическая значимость работы: Описание теоретической значимости (ценности) результатов исследования должно присутствовать во введении...
Методика измерений сопротивления растеканию тока анодного заземления: Анодный заземлитель (анод) – проводник, погруженный в электролитическую среду (грунт, раствор электролита) и подключенный к положительному...
Интересное:
Инженерная защита территорий, зданий и сооружений от опасных геологических процессов: Изучение оползневых явлений, оценка устойчивости склонов и проектирование противооползневых сооружений — актуальнейшие задачи, стоящие перед отечественными...
Отражение на счетах бухгалтерского учета процесса приобретения: Процесс заготовления представляет систему экономических событий, включающих приобретение организацией у поставщиков сырья...
Наиболее распространенные виды рака: Раковая опухоль — это самостоятельное новообразование, которое может возникнуть и от повышенного давления...
Дисциплины:
![]() |
![]() |
5.00
из
|
Заказать работу |
|
|
В настоящее время глицерин и жирные кислоты в нашей стране получают в основном из жиров путем гидролиза.
Количественно полноту гидролиза жира на любой стадии реакции характеризуют величиной глубины гидролиза жира. Глубина гидролиза - это содержание свободных жирных кислот в расщепленном жире. Чем выше глубина гидролиза жира, тем меньше содержится в жирных кислотах неполных глицеридов и, следовательно, тем меньше теряется с ними глицерина.
Параллельно с основным процессом - гидролизом в реакционной системе протекает и обратно направленный процесс - этерификация продуктов реакции (глицерина и жирных кислот) между собой с образованием исходных продуктов.
Постепенно скорость процесса этерификации возрастает и становится равной скорости процесса гидролиза. При этом наступает равновесное состояние системы. Чтобы не допускать существенного замедления процесса гидролиза, последний практически ведется в присутствии значительного избытка воды. Благодаря этому этерификации значительно замедляется. Кроме того, в ходе процесса производится смена воды. Это позволяет достигать глубины расщепления жира в пределах 97-98% [1].
Переработку жиров с целью получения глицерина и жирных кислот (или солей жирных кислот) преимущественно осуществляется двумя способами.
Первый способ - безреактивный гидролиз жиров с получением жирных кислот и глицериновых вод. Последние после очистки от примесей концентрируют, получая сырой глицерин. Для выработки высококачественных сортов глицерина и жирных кислот сырой глицерин и сырые жирные кислоты подвергают дистилляции.
Второй способ - щелочное омыление жиров с получением мыл и подмыльных щелоков и извлечением из последних глицерина.
|
В значительной мере качество получаемой продукции зависит от природы и чистоты исходных жиров, поэтому обязательной является операция рафинации низкокачественных жиров перед расщеплением.
Существуют различные способы рафинации. Одним из таких способов является обработка серной кислотой.
Действие разбавленной серной кислоты объясняется тем, что она коагулирует некоторые коллоидно-растворимые сопутствующие вещества, а также способствует гидролизу белков и слизей с образованием водорастворимых продуктов. Сопутствующие вещества и примеси удаляются этим методом достаточно эффективно, но жир приобретает очень темную окраску.
Также используется другой способ рафинации жиров - отстаивание и центрифугирование. Удаление из жира механических примесей, а также сопутствующих веществ, которые по той или иной причине находятся в жире во взвешенном состоянии, может быть осуществлено путем естественного осаждения. Однако этот метод длителен и требует громоздкой аппаратуры.
Более эффективна обработка жира на сепараторах, позволяющая быстрее и лучше очистить жир от примесей и влаги [1].
Каждый из перечисленных методов имеет свои достоинства и недостатки, однако ни один из них не обеспечивает необходимой степени очистки.
Способы осуществления самого процесса гидролиза весьма разнообразны: ферментативный гидролиз с использованием жирорасщепляющих энзимов (ферментов), в частности липазы; щелочное омыление жиров; кислотный гидролиз; гидролиз с использованием гетерогенных катализаторов - оксидов металлов; безреактивный гидролиз.
На раннем уровне развития гидролизного производства в качестве основного процесса использовался метод сернокислого гидролиза жиров. Полученные глицерин и жирные кислоты имели низкий выход и плохое качество, что требовало дополнительной очистки их, поэтому способ применялся недолго[1].
Более широкое распространение получил метод с использованием в качестве ускорителей оксидов металлов: СаО, МgО, ZnO и пр. Образующиеся металлические мыла труднорастворимы в воде, но хорошо растворяющиеся в жире и жирных кислотах, способствовали ускорению гидролиза. Для выделения жирных кислот из мыл использовали разбавленные растворы серной кислоты. Метод громоздкий и не обеспечивал хорошего качества, как глицерина, так и жирных кислот. В настоящее время он утратил свое значение [1].
|
Перспективным следует считать ферментативный (энзиматический) гидролиз. Метод энзиматического гидролиза технических жиров осуществляется с помощью препаратов липазы, полученных из семян клещевины. Этот метод позволяет получить светлые жирные кислоты при малых затратах теплоты. Однако большие количества препарата фермента и его высокая стоимость, а также большая длительность процесса и неприменимость его для гидролиза высокоплавких жиров препятствуют его распространению.
В настоящее время наиболее распространенным является безреактивный метод гидролиза жиров, осуществляемый в автоклавах при температуре 200-225°С и давлении 2-2,5 МПа без применения катализаторов. Способ обеспечивает получение продуктов гидролиза высокого качества и высокий выход глицерина и жирных кислот [2].
На большинстве предприятий нашей страны, вырабатывающих глицерин и жирные кислоты, гидролиз жиров проводят безреактивным методом, что обусловлено более высоким качеством получаемого глицерина и снижением потерь его в процессе производства по сравнению с методом щелочного омыления жиров.
Таким образом, в дипломном проекте принят безреактивый способ расщепления жиров, т.к. он является экономически и технологически более эффективным.
Процесс гидролиза можно осуществлять как в автоклавах, так и аппаратах колонного типа. Процесс гидролиза в колонном аппарате осуществляется при температуре 255-265ºС и давлении 5,5-6,5 МПа. В этих условиях в результате повышения растворимости воды в жире и повышения степени диссоциации воды в жире скорость реакции омыления жира значительно возрастает по сравнению с реакцией в автоклаве.
Установки колонного типа требуют большое количество однородного сырья, что является недостатком, поэтому более целесообразно использовать автоклавы.
В настоящее время наибольшее распространение в нашей стране получили автоклавы вместимостью 9,5 м³ и 20 м³ [2].
|
В установках автоклавного типа гидролиз может осуществляться как в одном автоклаве, так и в батарее из нескольких автоклавов. При использовании одного автоклава он оборудуется устройствами, улучшающими течение процесса.
В дипломном проекте принят автоклав вместимостью 20 м³, которые позволяют установить меньшее количество оборудования и разгрузить пространство.
Процесс гидролиза жиров в автоклавах осуществляют в два периода с соблюдением замкнутого потока глицериновых вод, при котором основное количество воды после второго периода используют для гидролиза в первом периоде. Во втором периоде используют конденсат.
Глубина гидролиза после первого периода должна быть не менее 85% [1].
После кратковременного отстаивания система разделяется на две фазы: первую глицериновую воду, содержащую 10…14% глицерина, выдавливают из автоклавов под давлением пара в аппарат для понижения давления (понизитель), частично расщепленный жир остается в автоклаве.
Для проведения второго периода гидролиза а автоклав добавляют конденсат, содержимое нагревают до температуры 220…225°С и кипятят в течение 2 ч с последующим расщеплением системы отстаиванием на две фазы: вторую глицериновую воду, содержащую 4…5% глицерина, и жирные кислоты. Последние выгружаются из автоклава под давлением пара и направляются в аппарат для понижения давления.
Глубина гидролиза жира после второго периода 95…96% [15].
Если жирные кислоты и глицериновую воду из автоклава, где они находятся при температуре 220…225°С и давлении до 2,5МПа, направлять в коробку, находящуюся под атмосферным давлением, то произойдет мгновенное испарение воды, а вместе с ней и значительной части глицерина, перегоняемого с водяным паром. Кроме того, жирные кислоты при высокой температуре, соприкасаясь с воздухом, окисляются с образованием темноокрашенных соединений. Чтобы избежать этого по выходе из автоклава с помощью выпускного вентиля давление жирных кислот и глицериновой воды редуцируется до 1,5…1,7 МПа, а затем в понизителе давления оно снижается до атмосферного.
|
Жирные кислоты после разделения фаз содержат некоторое количество растворенного и заэмульгированного глицерина. С целью понижения потерь глицерина их подвергают промывке горячим водным конденсатом в количестве 10% к массе жирных кислот. Жирные кислоты чаще всего промывают в специальных отстойниках-промывниках при температуре 95°С и перемешивании механической мешалкой с последующим разделением системы отстаиванием.
Жирные кислоты после промывки должны содержать не более 0,5% глицерина от общего количества в исходном жире. Промывные воды, содержащие до 2% глицерина, используют вместе со второй глицериновой водой на первый период гидролиза [30].
Перед концентрированием глицериновых растворов последние подвергаются очистке от примесей. Это обусловлено необходимостью, во-первых, получения глицерина, отвечающего требованиям стандартов, во-вторых, обеспечения наиболее благоприятных технологических условий выпаривания (уменьшение образования накипи на трубах подогревателей, предотвращение сильного вспенивания глицерина в вакуум-аппарате и др.), в-третьих, предохранения аппаратуры от коррозии.
Чтобы очистить глицериновые воды после безреактивного гидролиза жиров необходимо осуществить ряд технологических операции: нарушить устойчивость коллоидной системы; разрушить эмульсию липидов с водой; удалить липиды, водорастворимые ионогенные и неионогенные соединения и пр. Известно несколько методов очистки глицериновых вод.
Кислотная обработка глицериновых вод предусматривает удаление поверхностно-активных веществ (ПАВ) путем обработки последних минеральной кислотой. При этом ПАВ разлагаются с образованием свободных кислот и труднорастворимых сульфатов соответствующих металлов.
Существует также ионообменный способ очистки глицериновых вод. Он предназначен для очистки от ионогенных примесей с помощью ионообменных смол (ионитов). Иониты имеют ограниченную обменную емкость, т.е. способность принять из раствора лишь некоторое количество ионов, подлежащих удалению [2].
Одним из недостатков вырабатываемых в настоящее время ионитов является их неустойчивость при температуре выше 40ºС. Поэтому процесс очистки глицериновых вод с помощью ионообменных смол проводят при температуре воды не выше 35ºС. Концентрация глицерина в очищаемых растворах не должна быть больше 30-35%, в ином случае значительно возрастает вязкость раствора и ухудшается фильтрация его через слой ионитов.
Некоторые красящие вещества, содержащиеся в глицериновой воде, необратимо поглощаются анионитами и не отделяются при их регенерации. В результате изменяется цвет смолы от желтого до темно-коричневого и уменьшается ионообменная емкость анионита, что обуславливает необходимость предварительной адсорбционной очистки глицериновых вод перед использованием ионообменных смол.
|
При значительном содержании в исходной глицериновой воде растворимых диссоциирующих минеральных солей удаление их из раствора ионообменным способом сопряжено с определенными трудностями и существенными затратами. В связи с этим ионообменная очистка глицериновых вод, полученных из низкосортных жиров, технического животного жира II и III сорта, содержащих большое количество примесей, экономически нецелесообразна.
Существует очистка глицериновых вод сепарированием. Очистка производится на тарельчатых разделяющих сепараторах. Применяя сепаратор можно снизить содержание липидов в глицериновой воде до 0,04-0,08%, повысить выход глицерина, поскольку потери его с липидами меньше, чем с кальциевыми мылами, создать непрерывность процесса, улучшить условия труда.
Возможно совмещение процесса сепарирования с обработкой глицериновых вод гидроксидом кальция.
Для нейтрализации используют водную суспензию гидроксида кальция (известковое молоко). Процесс нейтрализации производят в нейтрализаторах при перемешивании паром, воздухом или механической мешалкой при температуре около 80°С. Известковое молоко подают в количестве, обеспечивающем достижение слабощелочной реакции среды. Избыток его определяют методом титрования пробы.
По окончании нейтрализации систему отстаивают, удаляют с поверхности всплывшую пену и часть кальциевых мыл, глицериновую воду перемешивают и фильтруют на рамных фильтр-прессах. Кальциевые мыла (шлам) промывают на фильтрах горячей водой для снижения потерь глицерина, затем продувают сжатым воздухом или паром. Допустимые потери глицерина со шламом не должны превышать 0,1% к содержанию глицерина в исходном жире [30].
Для получении глицерина высшего или I сорта дистиллированный глицерин подвергают отбеливанию древесным активированным углем с целью улучшения цвета и запаха, а также незначительного снижения содержания жирных кислот, сложных эфиров, нелетучего органического остатка и минеральных примесей.
Процесс отбеливания проводят при температуре около 80°С и непрерывном перемешивании в течении 2…3 ч с последующим отделением угля на фильтр-прессе. При необходимости в мешалку добавляют расчетное количество конденсата для разбавления глицеринового раствора до 94%-ной концентрации, соответствующей требованиям стандарта на дистиллированный глицерин высшего и I сорта.
Активированный уголь промывают водой, которую направляют на выпаривание. Отработавший активный уголь не должен содержать более 2% глицерина. Повторно уголь можно использовать лишь после регенерации, заключающейся в тщательной промывке его, сушке при 100…110°С и измельчении.
Таким образом, в дипломном проекте принята следующая схема очистки глицериновой воды: сепарирование → фильтрация → обработка известковым молоком → фильтрация → обработка активированным углем →фильтрация.
Для получения сырого глицерина концентрацией 86…88% очищенную глицериновую воду выпаривают (концентрируют). При этом выпаривании глицерин частично перегоняется с водяным паром, и эти потери тем выше, чем выше температура и больше концентрация глицерина. Повышение температуры приводит также к термическим превращениям глицерина, что неблагоприятно влияет на его цвет и уменьшает выход готового продукта.
Глицериновые растворы высокой концентрации являются весьма вязкими, поэтому при проведении процесса выпаривания необходимо обеспечить интенсивную циркуляцию. Чтобы ограничить испарение глицерина и уменьшить его термический распад, глицериновые воды выпаривают под вакуумом и при интенсивной циркуляции жидкости в вакуум-выпарных установках.
На масложировых предприятиях применяют вакуум-аппараты различной конструкции и размеров. Наибольшее распространение получили аппараты с выносными подогревателями, которые могут работать как однокорпусные, так и многокорпусные установки. Последние экономически более эффективны, поскольку работа их ведется непрерывным способом и организована таким образом, что вторичный пар, выходящий из испарителя предыдущего корпуса, может быть использован в качестве греющего в подогревателе следующего корпуса [1].
Установка непрерывного действия «Подъемник» имеет два одинаковых по конструкции и размерам вакуум-выпарных аппарата с выносными подогревателями.
Первый корпус установки состоит из выносного подогревателя и испарителя и рассчитан на работу под давлением 0,1 МПа; второй корпус также состоит из выносного подогревателя и испарителя и работает под вакуумом 86…90 кПа [2].
Установка работает по непрерывной схеме.
Сырой глицерин, полученный при упаривании глицериновых вод, нейтрализованных известковым молоком, фильтруют на рамных фильтр-прессах для отделения кальциевых и других солей жирных кислот, выпадающих в осадок при концентрировании.
К качеству фильтрованного сырого глицерина предъявляют требования в соответствии с ГОСТ 6823-2000. Если глицерин направляется на дистилляцию, то в нем дополнительно проверяют содержание поверхностно-активных веществ (ПАВ).
Очистку сырого глицерина от примесей осуществляют перегонкой его с водяным паром под вакуумом. Снизить температуру перегонки глицерина можно двумя путями: во-первых, проведением процесса дистилляции с водяным паром, во-вторых, созданием пониженных давлений при дистилляции.
При дистилляции сырого глицерина с водяным паром снижается парциальное давление паров глицерина и, как следствие, уменьшается его температура кипения. Поскольку глицерин обладает неограниченной растворимостью в воде, то для дистилляции можно использовать только перегретый пар.
Так, совместное использование перегретого пара и вакуума позволяет проводить процесс дистилляции глицерина при 170…180°С, вследствие чего повышаются его выход и качество.
Состав кубового остатка (гудрона) при дистилляции весьма разнообразен и зависит главным образом от качества сырого глицерина и режима дистилляции. Он содержит глицерин (40…60%), полиглицерины, триметилгликоль, жирные кислоты, азотосодержащие вещества и прочие соединения. Недистиллируемый остаток, называемый гудроном, используют для изготовления мягкой кровли, дорожных покрытий и пр. [1].
На масложировых предприятиях России, выпускающих дистиллированных глицерин, широко распространена дистилляционная установка фирмы «Руймбек»; на некоторых заводах внедрена установка дистилляции, дезодорации и обесцвечивания глицерина фирмы «Маццони». Особенность последней установки заключается в том, что применяют дистиллятор непрерывного действия колонного типа, горячего и холодного конденсаторов для конденсации паров глицерина, дезодоратора для удаления одорирующих веществ дистиллированного глицерина. Для производства дистиллированного глицерина предусмотрена закрытая система его адсорбционной очистки.
Дистиллированный глицерин также можно получить методом ионообменной очистки глицериновых вод. Производство осуществляется по схеме: глубокая очистка ионообменными смолами предварительно обезжиренной глицериновой воды с последующим концентрированием очищенного глицеринового раствора на модернизированной вакуум-выпарной установке «Подъемник».
Этим способом в зависимости от степени очистки глицериновой воды можно получить дистиллированный глицерин, отвечающий требованиям стандарта на глицерин динамитный и высшего сорта.
Ионообменный метод имеет ряд существенных преимуществ по сравнению с дистилляционным. Так значительно сокращаются потери глицерина, качество получаемого глицерина значительно выше. При выпаривании обессоленного глицеринового раствора практически исключается необходимость чистки трубок вакуум-выпарных аппаратов и повышается их производительность. Улучшаются условия труда работающих, т.к. температура в помещении не превышает 20-25ºС, а в воздухе отсутствует акролеин и другие вредные примеси, получаемые при высоких температурах и отрицательно влияющие на здоровье человека.
Однако ионообменный метод является очень дорогим, поэтому в дипломном проекте принят способ получения дистиллированного глицерина на наиболее распространенной и более дешевой установке «Руймбек»
Основной аппарат этой установки - дистилляционный куб, снабженный змеевиками для подогрева глицерина и барометром для острого пара [2].
Образующаяся при дистилляции глицерина паровая смесь, состоящая из паров глицерина и воды, подвергается постепенной или фракционной конденсации с использованием воздушных и водяных поверхностных конденсаторов. При этом в первую очередь конденсируется высококипящий компонент - глицерин, в то время как несконденсировавшиеся пары обогащаются низкокипящим компонентом (водой), что и позволяет получить после воздушных конденсаторов глицерин высокой концентрации 98% и более.
Сырой глицерин засасывается сначала в подогреватель, глухим паром низкого давления 0,2 МПа подогревается до 80…90°С, затем удаляется из подогревателя по переливной трубе и поступает в дистилляционный куб.
В дистилляционным кубе глицерин глухим паром высокого давления 1,4…1,5 МПа нагревается до 175…176°С. Пар поступает из котельной и из куба направляется в пароперегреватель. Перед поступлением в куб этот пар подвергается перегреву до 180°С. Давление впрыскиваемого пара должно быть в пределах 0,02…0,08 МПа [2].
Смесь паров глицерина и воды из дистилляционного куба через ловушку-каплеотделитель поступает в конденсаторную систему, состоящую из двух групп воздушных конденсаторов каждая из которых имеет четыре или пять вертикально расположенных и последовательно соединенных друг с другом конденсаторов. Сконденсировавшийся глицерин стекает в сборники-конденсаторы, где в результате нагрева глухим паром до 117…120°С избыток влаги испаряется с доведением концентрации дистиллята до 98,5…98,7%. Дистиллированный глицерин собирается в сборниках.
Пары глицерина и воды, несконденсировавшие в воздушных конденсаторах, поступают последовательно трубчатые конденсаторы, охлаждаемые водой. Конденсат из первого конденсатора - «первая сладкая вода» - собирается в соответствующий сборник. Затем пары поступают во второй водяной конденсатор, соединенный со сборником для «второй сладкой воды»; «сладкая вода» из двух сборников собирается в бак, откуда направляется на выпаривание. Пары и газы из второго сборника через ловушку-каплеотделитель направляются в третий водяной конденсатор, из которого «третья сладкая вода», содержащая лишь следы глицерина, собирается в третий сборник и используется затем при гидролизе жиров. Незначительная часть несконденсировавшихся паров и газовоздушная смесь из системы откачиваются с помощью насоса и направляются в атмосферу. Остаточное давление в установке поддерживается в пределах 2,2…2,6 кПа.
Температура воды, выходящей их водяных конденсаторов, должна быть равна: в первом 35…45°С, во втором 30…35°С, в третьем 15…20°С.
Система конденсации позволяет получить почти весь глицерин высокой концентрации - выход глицерина составляет 95% к массе пошедшего на дистилляцию, считая на 100%-ный, 2% глицерина получается в виде разбавленных растворов, концентрирование которых неэкономично [1].
Процесс дистилляции по мере накопления недистиллируемого остатка (гудрона) в кубе прерывают для спуска остатка в бак. В случае малой подвижности гудрона перед выгрузкой из аппарата его обрабатывают горячей водой, разваривают, а затем сливают.
Учитывая особенности получения глицерина, дипломном проекте приняты следующие технологические решения по производству дистиллированного глицерина: безреактивный метод расщепления жиров, с последующей очисткой по схеме «сепарирование → фильтрация → обработка известковым молоком → фильтрация → обработка активированным углем →фильтрация», далее получение сырого глицерина с применением двухкорпусной выпарной установки «Подъемник», получение дистиллированного глицерина на установке фирмы «Руймбек».
|
|
Эмиссия газов от очистных сооружений канализации: В последние годы внимание мирового сообщества сосредоточено на экологических проблемах...
Опора деревянной одностоечной и способы укрепление угловых опор: Опоры ВЛ - конструкции, предназначенные для поддерживания проводов на необходимой высоте над землей, водой...
Таксономические единицы (категории) растений: Каждая система классификации состоит из определённых соподчиненных друг другу...
История создания датчика движения: Первый прибор для обнаружения движения был изобретен немецким физиком Генрихом Герцем...
© cyberpedia.su 2017-2024 - Не является автором материалов. Исключительное право сохранено за автором текста.
Если вы не хотите, чтобы данный материал был у нас на сайте, перейдите по ссылке: Нарушение авторских прав. Мы поможем в написании вашей работы!