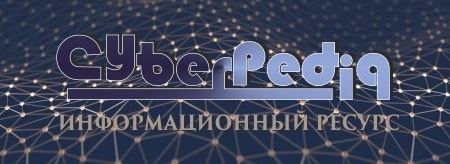
Общие условия выбора системы дренажа: Система дренажа выбирается в зависимости от характера защищаемого...
Опора деревянной одностоечной и способы укрепление угловых опор: Опоры ВЛ - конструкции, предназначенные для поддерживания проводов на необходимой высоте над землей, водой...
Топ:
Проблема типологии научных революций: Глобальные научные революции и типы научной рациональности...
Техника безопасности при работе на пароконвектомате: К обслуживанию пароконвектомата допускаются лица, прошедшие технический минимум по эксплуатации оборудования...
Интересное:
Средства для ингаляционного наркоза: Наркоз наступает в результате вдыхания (ингаляции) средств, которое осуществляют или с помощью маски...
Уполаживание и террасирование склонов: Если глубина оврага более 5 м необходимо устройство берм. Варианты использования оврагов для градостроительных целей...
Подходы к решению темы фильма: Существует три основных типа исторического фильма, имеющих между собой много общего...
Дисциплины:
![]() |
![]() |
5.00
из
|
Заказать работу |
|
|
Горение топлива – это химический процесс соединения горючих компонентов с кислородом воздуха, сопровождающийся выделением теплоты.
По реакции горения топлива рассчитывается количество воздуха, необходимое для полного сгорания топлива, а также объём получаемых продуктов сгорания. Расчёты выполняются для определения потерь теплоты с уходящими продуктами сгорания, КПД тепловых аппаратов, геометрических параметров газоходов.
Теплогенерирующие устройства, преобразующие химическую энергию сгорания топлива, имеют аналогичные конструкции, отличающиеся отдельными конструктивными элементами, которые изменяются в зависимости от вида топлива и способа его сжигания.
Все виды теплогенерирующих устройств этого типа имеют топку, трубопроводы для подачи жидкого и газообразного топлива, газоходы для удаления продуктов сгорания. Вид топлива (твёрдое, жидкое или газообразное) определяющим образом влияет на конструктивные особенности топок и их классификацию.
Топки подразделяются на слоевые и камерные. Слоевые предназначены для сжигания твёрдого топлива на колосниковой решётке, камерные – для сжигания жидкого и газообразного топлива.
Газовыми горелками называются устройства, предназначенные для образования газовоздушной смеси, подачи её или подачи только газа (при диффузионном сгорании) в камеру сгорания (топку) и сжигания. Рациональное сжигание горючего газа зависит в первую очередь от правильного выбора типа и конструкции газовых горелок. Газовая горелка должна обеспечивать возможность зажигания газовоздушной смеси, регулирования подачи газа и воздуха, а также гарантировать при правильной её эксплуатации тщательное перемешивание горючего газа с воздухом, устойчивое горение и полное сгорание горючего газа.
|
Работа горелки считается устойчивой, если длительное горение газа происходит без отрыва и проскока пламени. Отрыв пламени происходит при увеличении давления газа в сети и при избытке воздуха. Проскок пламени имеет место при резком понижении давления газа в сети. В этом случае пламя проскакивает внутрь смесительной трубки и горит у сопла. Скорость процесса горения, высота и форма пламени зависят от способа и скорости перемешивания горючего газа с воздухом: диффузионный (внешнее смешение), диффузионно-кинетический (частичное предварительное смешение) и кинетический (полное предварительное смешение).
Наивысшая температура пламени (до 1500 °С) и наименьшая длина его достигаются при полном предварительном смешении горючего газа с воздухом.
Газовые горелки классифицируются по следующим признакам: способу подачи воздуха, номинальному давлению газа и воздуха, теплоте сгорания газа, номинальной тепловой мощности, длине факела (калибру) и методу стабилизации (созданию устойчивости) факела.
По способу подачи воздуха различают горелки внешнего смешения – горелки с подачей воздуха из окружающей среды и смешения газа с воздухом в камере сгорания за счёт разрежения в ней и конвекции. Такие горелки называются диффузионными. Длина факела пламени и его свечение в диффузионных горелках достигают наибольшей величины.
По номинальному давлению газа различают горелки низкого (до 5 кПа), среднего (от 5 до 100 кПа) и высокого (свыше 100 кПа) давления, соответственно номинальное давление воздуха подразделяют на низкое (до 1 кПа), среднее (от 1 до 3 кПа) и высокое (свыше 3 кПа).
В аппаратах, применяемых на предприятиях общественного питания, используются в основном инжекционные газовые горелки низкого давления с частичным предварительным смешением газа с воздухом.
|
Горючие газы токсичны и в определённых концентрациях в воздухе взрывоопасны. Токсическое воздействие на организм человека возможно как за счёт действия собственно газа, так и продуктов его сгорания, поэтому необходимо строго соблюдать правила эксплуатации газовых горелок.
Перед началом работы газовых горелок проветривают помещение. Если в воздухе ощущается запах газа, необходимо отключить подачу газа и вызвать специальную службу. Для розжига горелок следует использовать только, переносной или стационарный запальник. При правильной эксплуатации горение происходит устойчиво без явлений отрыва и проскока пламени. При нормальной работе горелки пламя должно быть почти прозрачным с отчётливо выраженным голубовато-зеленоватым ядром в середине факела.
В случае значительного избытка воздуха пламя резко укорачивается, становится почти бесцветным, имеет расплывчатое ядро, горение происходит с потрескиванием. При недостатке воздуха пламя удлиняется, появляются жёлтые коптящие языки, свидетельствующие о неполном сгорании газа.
У горелок большой производительности перед включением следует закрыть регулятор воздуха, в противном случае произойдёт хлопок (взрыв смеси внутри горелки). Хлопок может нарушить герметичность соединений.
В процессе работы аппарата следует через смотровое окно периодически проверять работу горелки. При выключении аппарата вначале закрывают кран перед горелкой, а затем на спуске газопровода к аппарату.
Категорически запрещается искать утечку газа с помощью огня, так как это может вызвать взрыв. Искать утечку газа можно только путём нанесения на предполагаемые места утечки мыльной воды. К работе с газовыми аппаратами допускаются только лица, обученные безопасным методам работы и имеющие удостоверения о сдаче техминимума в соответствии с существующим законоположением.
9.4. Теплогенерирующие устройства для преобразования электрической энергии в тепловую
Основными элементами электротепловых аппаратов являются электронагреватели, преобразующие электрическую энергию в тепловую. При этом используется свойство проводников нагреваться при прохождении через них электрического тока.
Классификация электронагревателей. Электронагреватели можно разделить на три группы – преобразующие электрическую, энергию в тепловую, преобразующие электрическую энергию в электромагнитные колебания, которые непосредственно в пищевых продуктах превращаются в тепловую (СВЧ- и ИК-нагрев), и электронагреватели, преобразующие электрическую энергию в электромагнитные колебания металлических поверхностей (индукционный нагрев).
|
По виду проводника электронагреватели подразделяются на проводники с металлическим сопротивлением, с неметаллическим сопротивлением и жидкостные.
· К проводникам с неметаллическим сопротивлением относятся уголь, графит, карборунд и др.
· К жидкостным проводникам относятся электролиты (водный раствор соды), в том числе вода (практически не применяется в настоящее время).
· Электронагреватели с металлическим сопротивлением по конструктивному оформлению делятся на открытые, закрытые (с доступом воздуха) и герметически закрытые (без доступа воздуха).
Деление электронагревателей на три группы условное и зависит от среды, в которую они помещены. Так, электронагреватели с металлическим сопротивлением при работе в воздушной среде излучают электромагнитные колебания и поэтому одновременно являются и ИК-генераторами. В жидкой среде и при контактном нагреве теплота в основном передаётся конвекцией и теплопроводностью, поэтому в данном случае электронагреватели с металлическим сопротивлением относятся к первой группе.
Электронагреватели с металлическим сопротивлением. В электротепловых аппаратах, используемых на предприятиях общественного питания, наибольшее распространение получили электронагреватели с металлическим сопротивлением.
Электронагреватели с металлическим сопротивлением должны обладать большим удельным сопротивлением (более 10-6 Ом∙м), быть термостойкими, т. е. не окисляться при высоких температурах, жаропрочными (не изменять механических свойств при t = 1000...1200 °С), иметь низкий коэффициент удлинения. Для изготовления электрических проводников используют сплавы никеля с жаропрочными присадками: хромоникелевые (нихром), железохромоникелевые (фехраль, хромаль) (см. таблицу 5). Продолжительность работы при высоких температурах должна быть более 10000 ч.
|
Таблица 5 – Основные показатели нихрома и фехраля
Марка сплава | Удельное электрическое сопротивление при 20 ºС, 10-6 Ом∙м | Максимальная рабочая температура, ºС | Рекомендуемая рабочая температура, ºС (не выше) |
X15H60 | 1,06 – 1,16 | 1000 | 950 |
X20H80 | 1,07 – 1,09 | 1100 | 950 |
X13Ю4 | 1,18 – 1,34 | 1000 | 900 |
X23Ю5 | 1,37 | 1150 | 900 |
X23Ю | 1,4 | 1200 | 900 |
Для безопасности работы и увеличения срока службы спирали укладывают в изоляционный материал, обладающий высоким электрическим сопротивлением, хорошей теплопроводностью и незначительной влагопоглощающей способностью. В качестве электроизоляционных материалов используются специальные материалы: периклаз (окись магния с температурой плавления 1700°С и измельчённая в шаровых мельницах), шамот (прокаленная и измельчённая огнеупорная глина), кардиерит (керамика), фарфор, слюда, кварцевый песок и др. (см. таблицу 6).
Таблица 6 – Техническая характеристика изоляционных материалов, применяемых при производстве электронагревателей
Материал | Плотность, кг/м3 | Максимальная рабочая температура, ºС |
Периклаз | 2850—3200 | 1400—1700 |
Шамот | 1800—2000 | 1400—1500 |
Фарфор | 2200—2500 | 500—600 |
Слюда | 2700—2900 | 500—800 |
Кварцевый песок | 600—1400 | 1400—1500 |
Открытые нагревательные элементы представляют собой спираль, помещённую в керамические бусы, или подвешенную на фарфоровых изоляторах, или уложенную в пазы керамических панелей. Передача теплоты в них осуществляется преимущественно излучением (распространены в тепловых аппаратах незначительно).
Достоинствами нагревателей являются простота изготовления, удобство замены спирали; хорошие условия теплопередачи. К недостаткам относятся меньший срок службы по сравнению с закрытыми и герметически закрытыми нагревателями, так как они не защищены от механических повреждений и от коррозийного воздействия влажного атмосферного воздуха и агрессивных жидких сред; повышенная электро- и пожароопасность.
Закрытые нагревательные элементы представляют собой спираль, запрессованную в электроизоляционную, хорошо проводящую теплоту массу и помещённую в корпус, который предохраняет её от механических повреждений, но не защищает от доступа воздуха. В качестве изоляционного материала в конфорках обычно используется периклаз (окись магния) и шамотная глина. Нагревательная спираль изготавливается из нихрома марки Х20Н80 или фехрали марки Х23Ю5.
В конфорках обычно помещается спираль, состоящая из четырёх секций, соединённых попарно. Это позволяет осуществлять трёхступенчатое регулирование мощности (сильный, средний, слабый нагрев) в соотношении 4:2:1. Регулирование мощности осуществляется четырёхпозиционным трёхступенчатым пакетным переключателем.
|
В зависимости от технологического процесса и температуры на поверхности конфорок они выпускаются нескольких типов: с максимальной рабочей температурой на поверхности 450 °С – для ведения основных процессов варки и жарки в наплитной посуде, с максимальной рабочей температурой на поверхности 300 °С – для жарки изделий непосредственно на поверхности конфорки и с максимальной рабочей температурой на поверхности 250 °С – для поддержания в горячем состоянии готовой кулинарной продукции.
К достоинствам закрытых нагревательных элементов относятся их более высокие надёжность и долговечность по сравнению с открытыми нагревательными элементами. Недостатком являются чувствительность к длительным перегревам, поэтому их нельзя эксплуатировать без наплитной посуды. При нарушении этого требования на поверхности появляются трещины, что приводит к неравномерности температурного поля на поверхности конфорки, ухудшению процесса теплопередачи и перегоранию спирали. К недостаткам также следует отнести и то, что спираль соприкасается с воздухом и быстро окисляется.
Герметически закрытые трубчатые электронагреватели (тэн, рэн) получили наиболее широкое применение в тепловых аппаратах, используемых на предприятиях общественного питания.
Трубчатый электронагреватель (тэн) представляет собой цельнотянутую трубку, выполненную из углеродистой или нержавеющей стали, внутри которой расположена запрессованная в периклаз нихромовая спираль. Концы спирали соединяются со стальными контактными стержнями, свободные концы которых выводятся наружу и присоединяются к электросети. Стержни с помощью фарфоровых изоляторов изолируются от трубки. Перед установкой изоляторов концы трубки заливают термостойким лаком (герметиком) дли защиты периклаза от влаги.
Для увеличения поверхности теплообмена иногда трубку тэна оребряют, и такой ребристый электронагреватель носит название рэн.
Тэны изготавливают различной длины, диаметров и конфигурации Тэны должны использоваться только в той среде, для которой они предназначены.
Температура поверхности трубки тэна зависит от удельной мощности на поверхности и условий теплоотдачи к нагреваемой среде.
В соответствии с ГОСТом на тэны срок их службы должен составлять от 6000 до 10 000 ч, однако на практике срок их службы колеблется в более значительных пределах. Это свидетельствует о том, что в существующих конструкциях тэнов, технологии их изготовления, реальных условиях эксплуатации имеются факторы, существенно влияющие на срок службы тэнов. К таким факторам относятся следующие: неравномерная плотность периклаза в различных частях тэна (на изгибах и у контактных стержней), неравномерность шага намотки спирали, смещение спирали относительно оси трубки, контактирование витков спирали и тэнов сложной конфигурации, образование накипи на поверхности тэнов, коррозия оболочки тэнов.
В зависимости от условий теплообмена между поверхностью тэна и окружающей средой их выпускают в следующих исполнениях: воздушные — для подогрева воздуха в тепловых, жарочных, пекарных шкафах и аппаратах с принудительной циркуляцией воздуха; водяные — для нагревания воды в пищеварочных котлах, автоклавах, пароварочных аппаратах, кипятильниках, водонагревателях; масляные — для нагревания масла и пищевых жиров в жаровнях и фритюрницах. Выпускают также тэны для заливки в металлические отливки (конфорки, утюги, вафельницы).
Тэны, выпускаемые для тепловых аппаратов предприятий общественного питания, в основном рассчитаны на напряжение 220 В. Они выпускаются мощностью от 0,2 до 4 кВт. Устанавливаются тэны в аппаратах индивидуально или блоками.
Одной из разновидностей трубчатых нагревательных элементов являются сэны – силитовые электронагреватели. Они изготавливаются из полупроводниковых материалов, обладающих повышенным удельным сопротивлением. Силит представляет собой спёк карбида кремния с добавлением кристаллического кремния и углерода. Силит обладает высокой теплостойкостью. Изготавливают сэны в форме цилиндрического стержня постоянного или переменного сечения. Сэны постоянного сечения изготовляют из крупнозернистого карбида кремния, переменного сечения – из мелкозернистого. Концы нагревателей покрывают окисью кремния с алюминием для понижения электрического сопротивления и обеспечения надёжного контакта между стержнем и токопроводом. Сэны обладают рядом преимуществ по сравнению с другими электронагревателями, а именно: сравнительно низкая стоимость, быстрый выход их на рабочий режим (не более 30 с), возможность получения температуры в пределах от 1073 до 1773 К, длительный срок службы, простота изготовления и обслуживания. Недостатками сэнов являются окисление материала в среде водяного пара и снижение срока службы вследствие этого на 25...30 %. Кроме того, повышение допустимой рабочей температуры силитового излучателя приводит к разложению карбида кремния и увеличению электрического сопротивления нагревателя.
Для увеличения срока службы сэнов их помещают в трубки из кварцевого стекла при удельной мощности на поверхности трубки Wт=12,5 Вт/см2 и при групповом расположении Wт = 2,5 Вт/см2.
Энергия излучения силитового излучателя на 90 % генерируется в пределах 1,05...5,0 мкм.
Трубчатые кварцевые генераторы ИК-излучения представляют собой спираль, помещённую в трубку из кварцевого стекла. Кварцевые генераторы с хромоникелевой спиралью работают в диапазоне температур спирали 1350... 1570 К. Спираль выполняется из сплава Х20Н80Т или ОХ27Ю5А и помещается в негерметизированную кварцевую трубку диаметром 18...20 мм. Стеклянная трубка препятствует провисанию спирали и защищает обслуживающий персонал от поражения электрическим током. Кварцевые генераторы выпускают длиной от 0,4 до 2,0 м, мощностью 0,5...7,5 кВт.
Преимуществами кварцевых генераторов являются простота конструкции и технологичность в изготовлении. Недостатками – невозможность установки в вертикальном положении из-за провисания спирали.
Кварцевые генераторы с вольфрамовой спиралью работают в диапазоне температур спирали 2400...2800 К. Вольфрамовая спираль помещается в кварцевую трубку диаметром 10,75 мм. Трубка вакуумируется и заполняется аргоном до давления 80 кПа с добавкой паров йода в количестве 1...2 мг. Это обеспечивает удаление налёта вольфрама с внутренней поверхности трубки. Срок службы генератора 5000 ч. Концы спирали крепятся к молибденовым выводам.
Температура в активной зоне поверхности трубки составляет 723...773 К, в пассивной – 423 К. Основная доля энергии излучения (95 %) генерируется в пределах 0,8...2,4 мкм. Инерционный период 0,6 с.
Преимуществами кварцевых генераторов являются значительная удельная мощность и безынерционность. Недостатком – незначительная механическая прочность.
Магнетроны. Основным элементом СВЧ-установки является СВЧ- генератор – прибор, в котором электрическая энергия постоянного или переменного тока преобразуется в энергию электромагнитного поля сверхвысоких частот. Широкое применение в электротермических установках СВЧ в качестве генераторной лампы нашли магнетроны непрерывного генерирования, которые характеризуются относительно простой конструкцией, достаточно высокой мощностью и КПД. Геометрические параметры магнетрона, параметры электрического и магнитного полей выбирают с таким расчётом, чтобы электроны, взаимодействуя с переменным электрическим полем, наведённым в зазорах резонатора, отдавали этому высокочастотному электрическому полю резонатора часть своей энергии, приобретённой при их ускорении постоянным электрическим полем, приложенным между катодом и анодом. Энергия, возникающая в системе резонаторов, с помощью индуктивной петли связи и коаксиальной линии подаётся к внешней нагрузке.
Магнетроны непрерывного генерирования для электротермических СВЧ-аппаратов имеют выходную мощность от 0,5 до нескольких десятков киловатт, КПД их может достигать 70 % и выше.
|
|
Поперечные профили набережных и береговой полосы: На городских территориях берегоукрепление проектируют с учетом технических и экономических требований, но особое значение придают эстетическим...
Механическое удерживание земляных масс: Механическое удерживание земляных масс на склоне обеспечивают контрфорсными сооружениями различных конструкций...
История создания датчика движения: Первый прибор для обнаружения движения был изобретен немецким физиком Генрихом Герцем...
Археология об основании Рима: Новые раскопки проясняют и такой острый дискуссионный вопрос, как дата самого возникновения Рима...
© cyberpedia.su 2017-2024 - Не является автором материалов. Исключительное право сохранено за автором текста.
Если вы не хотите, чтобы данный материал был у нас на сайте, перейдите по ссылке: Нарушение авторских прав. Мы поможем в написании вашей работы!