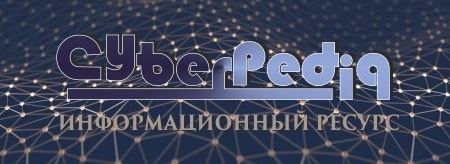
Биохимия спиртового брожения: Основу технологии получения пива составляет спиртовое брожение, - при котором сахар превращается...
Механическое удерживание земляных масс: Механическое удерживание земляных масс на склоне обеспечивают контрфорсными сооружениями различных конструкций...
Топ:
Теоретическая значимость работы: Описание теоретической значимости (ценности) результатов исследования должно присутствовать во введении...
Отражение на счетах бухгалтерского учета процесса приобретения: Процесс заготовления представляет систему экономических событий, включающих приобретение организацией у поставщиков сырья...
Комплексной системы оценки состояния охраны труда на производственном объекте (КСОТ-П): Цели и задачи Комплексной системы оценки состояния охраны труда и определению факторов рисков по охране труда...
Интересное:
Наиболее распространенные виды рака: Раковая опухоль — это самостоятельное новообразование, которое может возникнуть и от повышенного давления...
Средства для ингаляционного наркоза: Наркоз наступает в результате вдыхания (ингаляции) средств, которое осуществляют или с помощью маски...
Аура как энергетическое поле: многослойную ауру человека можно представить себе подобным...
Дисциплины:
![]() |
![]() |
5.00
из
|
Заказать работу |
|
|
Введение
Газогенерирующие топлива (ГГТ) - источники газов и энергии для устройств газогенерации различного назначения, широко используемых в ракетно- космической и другой военной технике, а также в народном хозяйстве. Газогенераторы вырабатывают сжатый газ либо со свободный истечением, либо в замкнутый объем. Технические задачи, решаемые газогенераторами, определяют конкретные требования к ним и соответственно к топливам. Это прежде всего мощность и ее изменение во времени, время работы, температура, химический состав продуктов сгорания и содержание в них конденсированной фазы, максимальное и минимальное давление в газогенераторе и др. Требования по температуре продуктов сгорания определяются жаропрочностью материалов газогенератора и потребителей газов, а также временем работы газогенератора. Так, для некоторых систем с временем работы несколько минут температура должна быть менее 1000К. Наряду с этим требуется, чтобы продукты сгорания содержали минимальное количество твердых частиц (менее I%) и агрессивных по отношению к конструкционным материалам и окружающей среде веществ, а также продуктов неполного окисления и растворяющихся в вытеснительной среде или реагирующих с ней. В некоторых газогенераторах (вдува, стендовых) допускается температура газов, близкая к температуре сгорания основного ракетного топлива. В ракетно-космической технике применяют газогенераторы на основе топлив различного агрегатного состояния: жидких, твердых и смешанных (гибридных). Жидкие ГГТ могут быть однокомпонентные (например, перекись водорода H2O2, гидразин N2H4, изопропил-нитрат C3H7ONO2 и др.), а также двухкомпонентные (компоненты основного топлива ЖРД), в том числе металлсодержащие (гелеобразные). Наиболее компактным источником рабочего тела газогенератора являются твердое топлива, отличающиеся высокой энерговооруженностью. Специфичность состава газогенерирующих твердых топлив (ГГТТ) в отличие от ракетных определяется прежде всего требованиями к уровню их как термодинамических (температура, состав продуктов сгорания), так и баллистических характеристик (скорость горения, ее зависимость от давления и температуры, пределы устойчивого горения). В общем случае уровень температуры продуктов сгорания составляет 1000…2000К, а время работы - от нескольких секунд до нескольких минут. Большая продолжительность работы обусловливает низкую скорость горения топлива (1…2 мм/с и менее) и особую форму заряда (торцевого горения с большим удлинением, например спиральный). Для минимизации разброса выходных параметров твердотопливных газогенераторов, работающих со свободным истечением газов, требуется возможно меньшая зависимость скорости горения топлива от давления (v ≈ 0,1…0,2) и температуры заряда. В системах с малым временем запаздывания при регулировании расхода газов наиболее эффективны топлива с отрицательным показателем степени в законе скорости горения (v = -I…-2). Для газогенераторов, работающих в замкнутый объем, например пороховых аккумуляторов давления, обеспечивающих минометный старт ракет, требуется высокая прогрессивность расходной характеристики (отношения максимального расхода в конце работы к начальному расходу mmax/m = 10…30). Это требование обеспечивается высокой зависимостью скорости горения топлива от давления (v = 0,7…0,8) и высокопрогрессивным характером изменения площади поверхности горения заряда (например, многоканальный моноблок). Твердые топлива для газогенераторов в основе своей близки к ракетным и могут быть баллиститными (гомогенными) и смесевыми (гетерогенными). Принципиальные составы их практически аналогичны ракетным. В отдельных случаях возможно применение сублимирующих топлив. Необходимый уровень термодинамических и баллистических характеристик ГГТТ обеспечивается подбором основных компонентов и введением небольших количеств специальных 16 добавок (модификаторов скорости горения, стабилизаторов горения, антипиренов и др.). Для обеспечения низкой температуры продуктов сгорания и скорости горения в составе баллиститов основной пластификатор ракетных топлив - нитроглицерин, частично или полностью заменяют на менее энергоемкий, но с большим удельным газообразованием, например динитрат диэтиленгликоля, триацетин и др. С этой же целью увеличивают содержание "охлаждающих" добавок, например динитротолуола, полиоксиметилена, а также вводят специальные добавки - антипирены, ингибиторы горения и др. Примерный состав баллиститного ГГТТ: нитраты целлюлозы (коллоксилин) – 50…60%, пластификатор – 30…40%, стабилизатор химической стойкости (централит и др.) и специальные добавки – 10…20%. Температура продуктов сгорания таких топлив при PК = 4 МПа не превышает 2000К, скорость, горения - менее 4 мм/с, удельное газообразование ~ 1 м3/кг, плотность – 1550…1600 кг/м3. Для уменьшения температуры продуктов сгорания и скорости горения смесевых твердых топлив в качестве окислителя используют нитрат аммония, циклические нитрамины - гексоген и октоген и их смеси с перхлоратом аммония, а в качестве горючих-связующих - синтетические каучуки, полиэфиры, полистирол, ацетилцеллюлозу и др. Уменьшение скорости горения достигается также с помощью ингибиторов горения (соединений щелочных и щелочно-эемельных металлов) и теплопоглощающих добавок. Примерный состав смесевого ГГТТ: окислитель – 65…75%, горючее-связующее – 10…30%; специальные добавки – 5…10%. Температура продуктов сгорания при PK = 4 МПа не превышает 2000К, скорость горения составляет 1…5 мм/с, удельное газообразование - 1,0…1,2 м3/кг, плотность – 1600…1700 кг/м3. Сублимирующие топлива представляют собой вещества, способные интенсивно генерировать газообразное рабочее тело путем прямой возгонки (сублимации), минуя жидкую фазу и процесс горения. Эти вещества характеризуются теплотой сублимации, молекулярной массой газовой фазы, коэффициентом испарения и равновесным давлением паров при определенной температуре. Сублимирующее топливо может быть одно- и двухкомпонентным. Сублимация может происходить под воздействием тепла, выделяющегося при работе бортовой аппаратуры или специального нагревателя. Практический интерес представляют такие вещества, как камфора, нафталин, ацетамид и различные аммонийные соли: хлорид, бисульфид, бикарбонат, карбамат. Большая плотность этих топлив по сравнению со сжатым газом и возможность их длительного хранения при низких температурах обусловливают их применение в системах управления космических летательных аппаратов. Наряду с жидкими и твердыми ГГТТ используют композиции смешанного агрегатного состояния, а также пастообразное и порошкообразные псевдоожиженные. Лазерные топлива. Лазерное излучение представляет собой когерентный (узконаправленный) поток электромагнитной энергии, излучаемой оптическим квантовым генератором - прибором с вынужденным излучением и положительной обратной связью. Топливо как источник энергии и газов используют в газодинамических лазерах (ГДЛ) - разновидности молекулярных лазеров, в частности на углекислом газе. В ГДЛ применяют тепловое возбуждение газа, которое может быть реализовано различными нагревателями, в том числе энергией горения как жидкого, так и твердого топлива. Рабочим телом в СO2 - лазерах является смесь газов CО2,N2 и паров Н20. При нагреве рабочего тела газовая среда еще не способна излучать. Происходит лишь возбуждение молекул; завершающееся чаще всего новым состоянием равновесия, но с повышенной температурой. Для создания активной среды, способной генерировать лазерное излучение, необходимо обеспечить так называемую инверсию заселенностей энергетических уровней, создаваемую при истечении газа через сопло со сверхзвуковой скоростью и быстром охлаждении при расширении. Оптимальное соотношение компонентов газовой среды ГДЛ на CO2 зависит от условий ее использования и составляет до 90% N2, 5…10% CO2 и I…2% Н20. Состав продуктов сгорания обычных баллиститных и смесевых твердых топлив далек от оптимального. В них имеется недостаточное количество азота (примерно 15%), значительный избыток Н20 и Н2 (до 40%), а также конденсированные продукты, содержание которых недопустимо. Для обеспечения требуемого соотношения газов в активной среде ГДЛ в состав унитарных лазерных твердых теплив баллиститного типа, кроме нитратов 17 целлюлозы, необходимо вводить высокоазотистые маловодородные пластификаторы и наполнители. В топливах смесевого типа целесообразно использовать безводородные и безгалоидные окислители, а в качестве горючих - гетероциклические полиазотистые соединения с минимальным содержанием водорода. Газодинамические лазеры на твердом топливе открывают широкие перспективы создания компактных мобильных установок с высокой мощностью в непрерывном режиме излучения для мирных и военных целей. Плазменные топлива. Принцип работы МГДГ ТТ основан на прямом преобразовании энергии, выделяющейся при горении твердотопливного заряда, в электрическую. Идея использования в этих целях ТТ основана на замене твердого электрического проводника потоком высокопроводящего газа - низкотемпературной плазмы, образующейся в результате сгорания топлива. Продукты сгорания топлива из генератора плазмы поступают в канал МГДГ, пересекают магнитное поле, электроны устремляются к электродам, и в результате возникает электрический ток. Таким образом, заряд МГДГ ТТ должен обеспечить высокий уровень электропроводности и кинетической энергии продуктов сгорания. Мощность, генерируемая установкой, зависит от величины электрофизического комплекса σW2, где σ - удельная электрическая проводимость продуктов сгорания; W - скорость движений продуктов сгорания. Обычные ТРТ по большинству характеристик удовлетворяют требованиям, предъявляемым к плазменным топливам. При этом требования по кинетической энергии потока согласуется с требованиями по энергетике к РТТ. Однако значение удельной электропроводимости лучших РТТ находится в пределах 0,005…0,010 См/м, а требуемый уровень, обеспечивающий функционирование МГДГ, должен быть в 104 раз больше. Эта задача решается введением в состав топлив веществ, включающих элементы с низким потенциалом ионизации Сs, Rb, К, Na. Наряду с этим состав плазменного топлива должен обеспечивать высокую (приблизительно 4000 К) температуру продуктов сгорания. К настоящему времени разработаны плазменные топлива баллиститного и смесевого типов. В состав баллиститов, кроме основы (нитратов целлюлозы и нитроглицерина), входят металлическое горючее - сплав Al и Mg (20…27%), соединения щелочных и щелочно-земельных металлов, например нитраты калия, цезия и другие вещества в количестве 10…15%. Эти топлива обеспечивают температуру продуктов сгорания: ТК = 3700…3800К; σ = 50…150 См/м; σW2 = 200…390 См/м·(кг/с)2. Особенность составов плазменных СТТ заключается в отсутствии галогенсодержащих компонентов, что обусловлено высоким сродством галогенов к электрону. По этой причине вместо перхлоратов в качестве окислителей применяют нитраты и нитросоединения щелочных и щелочно-земельных металлов. В состав горючих-связующих веществ входят компоненты, содержащие энергоемкие группировки и окислительные элементы. В качестве металлического горючего используют алюминий. Смесевые плазменные твердые топлива в общем случае обеспечивают более высокий, по сравнению с баллиститными, уровень рабочих характеристик, в частности σW2 до 950 См/м·(кг/с)2. Импульсные МГДГ ТТ могут быть использованы в военных целях для питания мощных оптико-квантовых генераторов, сверхдальней связи, создания высокоскоростного оружия. Они широко применяются в народном хозяйстве для геофизических исследований земной коры и верхней мантии в целях поиска полезных ископаемых, долговременного прогноза сильных землетрясений и изучения глубинного строения Земли. Высокометаллизированные плазменные топлива с температурой горения до 4500К применяют также для создания помех (ложных целей) в средствах защиты головных частей МБР и авиации от снарядов и ракет противника с различными системами наведения.
|
|
|
|
|
ВВЕДЕНИЕ
Смесевые энергетические конденсированные системы (ЭКС), реализу-
ющие самоподдерживающееся горение, находят широкое применение в качестве источников рабочего тела газогенераторов различного назначения: ракетные двигатели на твердом топливе, источники низкотемпературной плазмы, устройства пожаротушения, автомобильные мешки безопасности, системы управления газопроводами и реанимации нефтяных скважин и многие другие.
В качестве основных окисляющих компонентов высокоэффективных
ЭКС применяют перхлорат аммония (ПХА) и мощные вторичные взрывчатые вещества типа октогена и гексогена, что выдвигает задачи обеспечения экологической взрывобезопасности при производстве и эксплуатации таких составов [1]. Одним из основных продуктов сгорания ЭКС на основе ПХА является HCl, массовое содержание которого может достигать сотен тонн при работе, например, твердотопливных ускорителей космического корабля многоразового использования типа Шаттл [2]. Введение в ЭКС на основе ПХА нитраминов позволяет снизить массовое содержание HCl в выхлопе двигателей, но одновременно растет опасность таких ЭКС, так как увеличивается возможность детонации и уменьшается стойкость топлив к факторам внешних воздействий.
Поиски перспективных компонентов ЭКС, удовлетворяющих требованиям экологической и взрывобезопасности, ограничены сравнительно узким классом органических и неорганических кислородсодержащих веществ, поэтому наиболее перспективным с этой точки зрения можно считать дешевый, имеющий практически неограниченные сырьевую и промышленную базу, экологически чистый окислитель − нитрат аммония (НА). Одним из преимуществ топлив на его основе можно считать низкую (по сравнению с топливами на основе перхлората аммония) температуру горения, и, соответственно, низкую температуру продуктов сгорания.
1 НИТРАТ АММОНИЯ КАК ОКИСЛИТЕЛЬ
ЭНЕРГЕТИЧЕСКИХ КОНДЕНСИРОВАННЫХ СИСТЕМ
К твердотопливным газогенерирующим составам как гражданского, так
и военного назначения в настоящее время предъявляют жесткие требования
по стоимости, эксплуатационной безопасности, экологической чистоте про-
дуктов сгорания, надёжности и высоким энергетическим характеристикам
горения, поэтому при создании новых компонентов таких составов необхо-
димо соблюдать эти условия.
1.2 Физико-химические свойства нитрата аммония
Нитрат аммония (НА) – кристаллическое вещество, которое применя-
ется не только как удобрение, но и в качестве основного компонента в соста-
ве промышленных взрывчатых веществ (ВВ) а также в твердых газогенери-
рующих составах, продукты разложения которых не содержат конденсиро-
ванной фазы [21, 23].
НА выпускают в виде гранул, чешуек или кристаллов – формула
NH4NO3, молекулярная масса − 80. В чистом виде НА ранее применялся как
малочувствительное ВВ при массовых взрывах; теплота взрывчатого превра-
щения 1600 кДж/кг, работоспособность в свинцовой бомбе 165-230 см3, теп-
лота образования — 355 кДж/моль.
НА обладает полиморфизмом и в зависимости от температуры может
существовать в нескольких модификациях (табл. 1.1): кубической, тетраго-
нальной, ромбической, ромбической бипирамидальной, гексагональной [22].
Это сильно гигроскопичное соединение, хорошо адсорбирующее окру-
жающую влагу с образованием на поверхности насыщенного раствора, а при
испарении влаги (в случае уменьшения относительной влажности воздуха) из
этого раствора будут выделяться кристаллы, которые скрепляют соприкаса-
ющиеся частицы НА. В результате многократного увлажнения и высыхания
кристаллы все прочнее связываются, теряют сыпучесть и материал самопро-
извольно уплотняется до монолита или крупных кусков. Процесс самопроиз-
вольного уплотнения (слеживания) НА является следствием гигроскопично-
сти и полиморфизма [24].
В зависимости от формы и размеров частиц насыпная плотность НА
составляет 0,8-0,9 г/см3. В процессе хранения в условиях частого и резкого
перепада температур происходит значительное увеличение объема кристалла
НА, особенно при высокой влажности, а сухой кристалл НА даже при резких
колебаниях температуры сохраняет свой первоначальный объем.
НА хорошо растворим в воде, причем растворимость находится в силь-
ной зависимости от температуры, растворение в воде сопровождается погло-
щением тепла и понижением температуры замерзания раствора. При раство-
рении 6 частей НА в 10 частях воды температура понижается примерно на 27
°C, а раствор, содержащий 50 г НА в 100 г воды, замерзает при температуре
около минус 13 °С.
НА хорошо растворим в этиловом и метиловом спирте, пиридине, аце-
тоне и в жидком аммиаке, а с повышением температуры растворимость воз-
растает [36].
Безводный НА плавится при температуре 169,4 °C, при увлажнении
температура плавления значительно снижается, согласно выражения tKp =
169,4 − 13,2 • Х, где X — содержание влаги, % [25, стр.145].
СПИСОК ИСПОЛЬЗУЕМОЙ ЛИТЕРАТУРЫ
1. Тимнат И. Ракетные двигатели на химическом топливе [Текст]: Пер.
с англ. / Тимнат И.; перевод с англ. В.А. Вебера и С.М. Фролова с предисло-
вием автора. − М.: Мир, 1990. − 294 с.
2. De Luca, L. T. Ballistic properties of solid rocket propellants based on
dual-oxidizer (ammonium perchlorate and ammonium nitrate) mixtures [Текст] /
L. T. De Luca, L. Galfetti, F. Severini, P. Taiariol, V. A. Babuk, B. N. Kondrikov,
A. B. Vorozhtsov, G. Klyakin // Progress in Combustion and Detonation: Proceed-
ings of the International Conference on Combustion and Detonation. Moscow. Au-
gust 30 – September 3. – 2004. – P. 151-152.
3. Пат. 6811626 Соединённые Штаты Америки, МПК C06B23/006,
C06D5/06. Газогенерирующий состав [Текст] / Kazuya Serizawa, Katsuhiko
Takahashi; заявитель и патентообладатель NOF Corporation. - № 09/952840;
заявл. 14.09.01; опубл. 02.10.04.
4. Пат 6623574 Соединённые Штаты Америки, МПК C06D5/06,
C06B31/30. Газогенерирующий состав [Текст] / Jianzhou Wu; заявитель и па-
тентообладатель Daicel Chemical Industries, Ltd. – № US 09/530185; заявл.
28.09.99; опубл. 23.09.03.
5. Mauno, E.E. Harju. Transition path selection between ammonium nitrate
solid phases IV, III and II [Текст] / Mauno E.E. Harju // Annales Academiae Sci-
entiarum Fennicae. Series A. Chemica. – Helsinki. – 1994. – P. 40.
6. Nakamura Hidetsugu. Nitrate ammonium reaction with carbon powder
[Текст] / Nakamura Hidets, Saeki Kohzi, Akiyoshi Miyako, Takahasi Katsuhiko //
Journal Japan Explosive Societies. – 2002. – № 3 (63). – P. 87-93.
7. Yoshida Saeko. Характеристики горения композитных ракетных топ-
лив на основе нитрата аммония и перхлората аммония, приготовленных с
мелкими и крупными частицами перхлората аммония [Текст] / Yoshida Saeko,
Kohga Makoto // Sci. and Technol. Energ. Mater. – 2006. – №4 (67), – C. 117-
8. Айзеле, З. Твердые ракетные топлива: примеры целенаправленных
разработок [Текст] = Raketenfesttreibstoffe: Beispiele fur aufgabenspezifische
Entwicklungen / З. Айзеле, В. Клён = Elsele S., Klohn. V // FhG-Berichte. –
1984. – №3-4. – C. 8-13.
9. Бабук, В.А. Особенности агломерационного процесса при горении
топлив на основе нитрата аммония [Текст] / А. А. Глебов, И. Н. Долотказин //
Сб. трудов Четвертой Международной школы конференции «Внутрикамер-
ные процессы, горение и газовая динамика дисперсных систем». Санкт Пе-
тербург. – 2004. – С. 23.
10. Popok, V. N. Combustion of high energy compositions on base nitrate
ammonium and active binders / V. N. Popok, L. A. Savelyeva // The 10th Interna-
tional Scientific Conference «Reshetnev’s Readings». November 5–10. Krasno-
yarsk. Russia. – 2007. – P. 153.
11. Пат. 7147830 Соединённые Штаты Америки, МПК 7 C 01 C 1/18.
Стабилизированные гранулы нитрата аммония [Текст] = Stabilized ammonium
nitrate granules / Kemira Growhow Oyj, Hero Heikki, Poukari Juhani. Jianzhou
Wu; заявитель и патентообладатель Kemira Growhow Oyj (Finland). – №
11/206875; заявл. 19.08.05; опубл. 12.12.06.
12. Zhou Long-Mei. Композиционный материал наночастицы Y2O3. Уг-
леродные нанотрубки: получение и каталитическое действие в разложении
перхлората аммония [Текст] / Zhou Long-Mei, Liu Hong-Ying, Li Feng-Sheng //
Acta phys.-chem. science. – 2006. – №5 (22). – С. 627-630.
13. Клякин, Г. Ф. Разработка концепции и основные направления фа-
зовой стабилизации нитрата аммония как окислителя экологически чистых
высокоэнергетических конденсированных систем [Текст] / Г. Ф. Клякин //
HEMs-2004: Материалы конференции. Белокуриха. – 2004. – С. 14-16.
14. Лемперт, Д. Б. Новое поколение газогенерирующих составов для
автомобильных мешков безопасности [Текст] / Д. Б. Лемперт, Г. Б. Манелис /
Химия в интересах устойчив. развития. – 2005. – № 6 (13). – С. 855-858.
15. Милехин, Ю. М. Энергобаллистические характеристики экологи-
чески безопасных ТРТ для РКК на основе нитрата аммония, перхлората ка-
лия и гексогена [Текст] / Ю. М. Милехин, Н. Н. Парфенов, В. М. Меркулов,
Б. И. Ларионов, Ю. Б. Банзула // Ракетные двигатели и проблемы освоения
космического пространства: Сб. статей. – 2005. – Т. 1. – C. 231-232.
16. Никифоров, А. Е. Пути фазовой стабилизации нитрата аммония
[Текст] / А. Е Никифоров // Современные проблемы технической химии: Ма-
териалы докладов Международной научно-технической и методической
конференции. Казань. 22-24 декабря. – Казань, 2004. – С. 442-443.
17. Пат. 6872265 Соединённые Штаты Америки, МПК 7 D 03 D
23/00. Фазостабилизированный нитрата аммония [Текст] = Phase-stabilized
ammonium nitrate / Hamilton Brian K.; заявитель и патентообладатель Autoliv
ASP, Inc. – № 10/354278; заявл. 30.01.03; опубл. 29.03.05.
18. Нечипоренко, Г.Н. Получение сокристаллизатов нитрата аммония
как способ устранения фазовых переходов в кристаллической решетке нитра-
та аммония [Текст] / Г. Н. Нечипоренко, Н. И. Головина, Г. В. Шилов, Д. Б.
Лемперт, Г. П. Долганова, Г. Г. Немцев // HEMs – 2004. – 2005. – С. 218-221.
19. Пат. 2240283 Российская Федерация, МПК 7 C 01 C 1/18, C 06 B
31/28. Фазостабилизированный нитрат аммония [Текст] / Таранушич В. А.,
Клякин Г. Ф., Вязенова И. А., Павловец Г. Я., Салько А. Е.; заявитель и па-
тентообладатель Государственное образовательное учреждение высшего
профессионального образования "Южно-Российский государственный тех-
нический университет (Новочеркасский политехнический институт)". –
№ 2003125154/15; заявл. 11.08.03; опубл. 20.11.04.
20. Никифоров, А. Е. О механизме стабилизирующего действия аммо-
нийных комплексов переходных металлов в составах на основе нитрата ам-
мония [Текст] / А. Е. Никифоров, С. Н. Киселев, О. А. Седова // Воспламене-
ние и горение конденсированных систем, излучение их пламен: Материалы
Всеросссийской научно-технической и учебно-методической конференции.
Казань. Сентябрь. 1999. – Казань, 2001. – С. 104-105.
21. Beckman Charles. Чистые ракетные топлива для запуска космиче-
ских ракет [Текст] = Clean propellants for space launch boosters / Beckman 126
Charles // Pap. Propuls. and Energ. Panel (PEP) 84th Symp. "Environ. Aspects
Rocket and Gun Propuls.". Aalesund. 29 August - 2 September 1994. – 1995. –
№ 559. – С. 6/1-6/9.
22. Технология аммиачной селитры [Текст] / Под ред. доктора
технических наук профессора В. М. Олевского. – М.: Химия, 1978. –311 с.
23. Киселев, С. Н. Фазовая стабилизация нитрата аммония - экологи-
чески чистого окислителя для взрывчатых составов и твердых топлив [Текст]
/ С. Н. Киселев, А. Е. Никифоров, В. Я. Базотов, О. А.Седова // Современные
проблемы технической химии: Материалы докладов Всероссийской научно-
технической конференции. Казань. 26-28 сент. 2002. – Казань, 2002. – Ч. 1. –
C. 257-259.
24. Хамский, Е.В. Кристаллизация в химической промышленности
[Текст] / Е. В. Хамский – М.: Химия, 1979. – 344 с.
25. Справочник азотчика [Текст] / Под ред. Е.Я. Мельникова. – 2-е изд.
перераб. – М.: Химия, 1987 – 464 с.
ВВЕДЕНИЕ
Смесевые энергетические конденсированные системы (ЭКС), реализующие самоподдерживающееся горение, находят широкое применение в качестве источников рабочего тела газогенераторов различного назначения: ракетные двигатели на твердом топливе, источники низкотемпературной плазмы, устройства пожаротушения, автомобильные мешки безопасности, системы управления газопроводами и реанимации нефтяных скважин и многие другие. В качестве основных окисляющих компонентов высокоэффективных ЭКС применяют перхлорат аммония (ПХА) и мощные вторичные взрывчатые вещества типа октогена и гексогена, что выдвигает задачи обеспечения экологической и взрывобезопасности при производстве и эксплуатации таких составов [1]. Одним из основных продуктов сгорания ЭКС на основе ПХА является HCl, массовое содержание которого может достигать сотен тонн при работе, например, твердотопливных ускорителей космического корабля многоразового использования типа Шаттл [2]. Введение в ЭКС на основе ПХА нитраминов позволяет снизить массовое содержание HCl в выхлопе двигателей, но одновременно растет опасность таких ЭКС, так как увеличивается возможность детонации и уменьшается стойкость топлив к факторам внешних воздействий. Поиски перспективных компонентов ЭКС, удовлетворяющих требованиям экологической и взрывобезопасности, ограничены сравнительно узким классом органических и неорганических кислородсодержащих веществ, поэтому наиболее перспективным с этой точки зрения можно считать дешевый, имеющий практически неограниченные сырьевую и промышленную базу, экологически чистый окислитель − нитрат аммония (НА). Одним из преимуществ топлив на его основе можно считать низкую (по сравнению с топливами на основе перхлората аммония) температуру горения, и, соответственно, низкую температуру продуктов сгорания.
КОНВЕЙЕРЫ ВИБРАЦИОННЫЕ ОДНОТРУБНЫЕ КВ1Т
Предназначены для пылеплотного транспортирования в горизонтальном направлении сыпучих, кусковых, пылящих и абразивных материалов, не склонных к налипанию, крупностью до 1/3 диаметра рабочего органа с температурой не выше +100°С. Возможно создание транспортной системы из нескольких последовательно установленных конвейеров. Вибрационные конвейера типа КВ1Т применяются в пищевой, строительной, стекольной, металлургической, литейной и других отраслях промышленности.
Состав виброконвейера:
1 - грузонесущий орган (труба); 2 - вибратор; 3- упругая подвеска (пружины или резиновые виброизоляторы); 4 - опора; 5 - герметизатор.
Конвейер представляет собой одномассную свободноколеблющуюся зарезонансную систему. Под действием усилий, создаваемых вращающимися дебалансами вибраторов, грузонесущий орган конвейера совершает вынужденные гармонические колебания с заданной частотой, амплитудой и углом вибрации. При этом материал, поступающий в грузонесущий орган конвейера, подбрасываясь, перемещается от патрубка загрузки к патрубку разгрузки.
Конвейеры изготавливаются с рабочим органом из углеродистой или нержавеющей стали.
На рисунке 2 приведена схема комбинированной сушилки с псевдоожиженным слоем
сыпучего материала для сушки порошкообразных компонентов смесевых составов в периодическом и непрерывном режимах.
Рисунок 2. Схема сушилки порошкообразных
компонентов: 1 – корпус; 2 – газораспредели-
тельная камера; 3 – крышка; 4 – мембрана; 5
– прерыватель потока теплоносителя; 6 –
Электродвигатель
Сушилка содержит корпус 1, газорас-
пределительную камеру 2 с газораспредели-
тельной решѐткой, крышку 3 с патрубками и
штуцерами. На крышке установлена предо-
хранительная мембрана 4. В нижней части
камеры 2 установлен прерыватель 5 газового
потока с приводом. Регулирование скорости
вращения вала электродвигателя 6 осущест-
вляется автотрансформатором по показани-
ям тахометра. Порошкообразный материал
загружается в корпус сушилки через штуцер
расположенный в верхней его части. Нагре-
тый в калорифере воздух подаѐтся через
прерыватель в газораспределительную ка-
меру и далее в слой влажного материала.
Высушенный продукт выгружается из корпуса
сушилки порционно через штуцер, располо-
женный на уровне газораспределительной
решѐтки, а отработанный теплоноситель по-
ступает в систему очистки воздуха от пыли.
Вибромельница МВ-400
Помол в вибромельнице.
Процесс помола в вибрационных мельницах, как правило, происходит в непрерывном режиме. В загрузочное отверстие мельницы расположенное сверху корпуса подается сырье – материал с влажностью не более 2% и размером частиц до 2 мм. Далее материал проходит через рабочую камеру мельницы, заполненную движущимися шарами, и измельчается за время пути. После этого материал самотеком выгружается с другой стороны мельницы, через выгрузочные отверстия. В выгрузочном отверстии монтируется решетка, предотвращающая выпадение шаров из рабочей камеры, но не мешающая движению тонкого порошка.
![]() |
Рис. 8. Процесс помола в вибрационной мельнице – показана подача сырья в верхнее загрузочное отверстие и выгрузка из нижнего выгрузочного отверстия. |
Производительность мельницы определяется производительностью питателей (чаще всего это шнековый питатель, иногда ленточный), подающих сырье. Производительность питателей проще всего регулировать частотными преобразователями-инверторами. Подача сырья ведется через гибкие герметичные соединения на загрузке и выгрузке – это полностью исключает пыление при работе оборудования.
Дезинтегратор ТКМ -1А (2)
ООО "Авимед" г. Новосибирск
Дезинтегратор ТКМ -1А (2) предназначен для измельчения свободным многократным ударом до состояния порошка сухих сыпучих и зернистых материалов
Технические характеристики ТКМ-1А (2):
«Техноком»г. Екатеринбург
Шкаф сушильный "ШСП-0,25-500"
Сушильный шкаф ШСП-0,25-500 предназначен для сушки и испытания материалов при температуре в атмосфере воздуха. Сушильный шкаф рассчитан для работы при температуре окружающего воздуха от 10°С до 35°С и относительной влажности до 80% при температуре 25°С.
Шкафы типа ШСП имеют:
камеру из оцинкованной стали;
цифровой термоконтроллер для управления нагревом;
программное ведение режима нагрева (по отдельному заказу)
точность задания температуры ± 2 °С;
Технические характеристики ШСП-0,25-500:
Диапазон рабочих температур 50 - 250 °С
Размер рабочего пространства (шир/выс/глуб) 560x1350x645 мм
Габаритные размеры (шир/выс/глуб) 1030x1970x900 мм
Питание переменным током: напряжением 380±38 В частотой 50±1 Гц
Потребляемая мощность 7 кВт
Масса шкафа 325 кг
Нагреватель ТЭН 12 шт
Завод «ТЕХПРИБОР» г. Щекино
ВК-ГШ-50-AISI
Спиральный конвейер (гибкий шнек) из нержавеющей стали «ВК-ГШ-50-AISI» ТУ 3167-001-92992044-2012 предназначен для транспортирования сыпучих, порошкообразных, мелкозернистых, гранулированных материалов с производительностью до 0,5 м куб./ч. В спиральном конвейере «ВК-ГШ-50-AISI» узлы, контактирующие с перемещаемым материалом (загрузочная емкость, разгрузочный модуль) изготовлены из нержавеющей стали - 08Х18Н10Т (AISI-304).
Общие сведения
Винтовой конвейерный транспорт является одним из наиболее эффективных механизмов для перемещения сыпучих материалов. Простота конструкции, надежность, низкая себестоимость транспортирования обуславливают широкое применение данного вида оборудования в самых различных технологических процессах. Однако, винтовым конвейерам присущи и определенные недостатки, ограничивающие области их использования. С помощью «жестких» шнеков, можно собрать горизонтальную, наклонную или даже вертикальную конвейерную трассу, но каждый ее элемент будет состоять из прямого участка. Отсюда излишняя громоздкость, металлоемкость, а значит и высокая стоимость пространственных трасс на основе «жестких» шнеков.
Гибкие шнеки или как их еще называют спиральные конвейеры, не имеют подобных недостатков. Спираль позволяет создавать сложные пространственные трассы, где перемещаемый материал движется по наиболее короткому пути, без перегрузок из одного конвейера в другой. К несомненным достоинствам гибких шнеков можно отнести, низкое энергопотребление, герметичность, возможность подачи материала по наклонам и поворотам трассы без образования «пробок». Гибкий корпус повышает «технологическую мобильность» конвейера, делая его идеальным вариантом транспортирования сыпучих материалов в условиях плотной компоновки технологического оборудования.
Устройство
Спиральный конвейер из нержавеющей стали «ВК-ГШ-50-AISI» (Рис.1) (Рис.1) состоит из загрузочной емкости (1), с одной стороны которого расположен патрубок выхода материала, а с другой – приводной узел (2) подающей спирали (3) и мотор - редуктор (4). Гибкий корпус (5) заканчивается разгрузочным модулем (6) с установленной подшипниковой опорой (7). Патрубок разгрузочного модуля (6) оснащен фланцем (8) служащим для присоединения гибкого шнека «ВК-ГШ-50» к другому технологическому оборудованию.
Верхняя часть загрузочной емкости (1) имеет отбортовку (9), нижняя – площадки (10) с отверстиями (11), предназначенными для установки гибкого шнека «ВК-ГШ-50» на площадке или фундаменте.
Рис. 1
Москва, Россия
Дозатор сыпучих продуктов
ООО «Геа-Пак» г.Ростов-на-Дону
Назначение: Дозатор предназначен для весового дозирования сыпучих продуктов с высокой степенью точности. Расфасовка производится в готовые пакеты, мешки, коробки и т. д. Рабочий диапазон весов от 0,1 до 12 кг. Дозирующее оборудование дает возможность упаковывать такие продукты как крупы, коротко-резанные макаронные изделия, орехи, семечки, сахар и т. д.
Описание: | |||||
С электронного блока задаются параметры для работы дозатора, на дисплее высвечивается текущее значение веса. Нажатием на педаль подается команда на набор очередной дозы продукта. Набранная доза опускается по лотку в стоящий на весовой платформе готовый пакет. | |||||
Технические характеристики: | |||||
Пределы дозирования, гр. | 100-12 000 | ||||
Производительность, уп./мин | До 10 | ||||
Вместимость бункера, л | |||||
Электропитание, В | |||||
Потребляемая мощность, кВт, не более | |||||
Габариты, мм | 600х600х1500 | ||||
Масса, кг | |||||
Завод компании «ВИБРОТЕХНИК» г. Санкт-Петербург.
Истиратель дисковый ИД 250
Арактеристики и описание
Истиратель дисковый ИД 250 предназначен для измельчения хрупких материалов различной прочности до мелкодисперсного состояния.
Истиратели дисковые – оборудование лабораторного класса, которое применяется в различных отраслях промышленности, в том числе: горнодобывающей, металлургической, строительной, фармацевтической и химической.
|
|
Архитектура электронного правительства: Единая архитектура – это методологический подход при создании системы управления государства, который строится...
Таксономические единицы (категории) растений: Каждая система классификации состоит из определённых соподчиненных друг другу...
Автоматическое растормаживание колес: Тормозные устройства колес предназначены для уменьшения длины пробега и улучшения маневрирования ВС при...
Механическое удерживание земляных масс: Механическое удерживание земляных масс на склоне обеспечивают контрфорсными сооружениями различных конструкций...
© cyberpedia.su 2017-2024 - Не является автором материалов. Исключительное право сохранено за автором текста.
Если вы не хотите, чтобы данный материал был у нас на сайте, перейдите по ссылке: Нарушение авторских прав. Мы поможем в написании вашей работы!