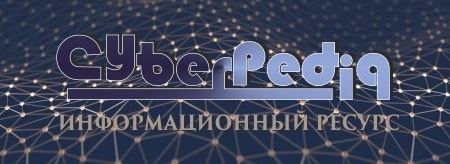
Кормораздатчик мобильный электрифицированный: схема и процесс работы устройства...
Организация стока поверхностных вод: Наибольшее количество влаги на земном шаре испаряется с поверхности морей и океанов (88‰)...
Топ:
Особенности труда и отдыха в условиях низких температур: К работам при низких температурах на открытом воздухе и в не отапливаемых помещениях допускаются лица не моложе 18 лет, прошедшие...
Проблема типологии научных революций: Глобальные научные революции и типы научной рациональности...
Интересное:
Национальное богатство страны и его составляющие: для оценки элементов национального богатства используются...
Финансовый рынок и его значение в управлении денежными потоками на современном этапе: любому предприятию для расширения производства и увеличения прибыли нужны...
Инженерная защита территорий, зданий и сооружений от опасных геологических процессов: Изучение оползневых явлений, оценка устойчивости склонов и проектирование противооползневых сооружений — актуальнейшие задачи, стоящие перед отечественными...
Дисциплины:
![]() |
![]() |
5.00
из
|
Заказать работу |
|
|
Эти сплавы получают методами порошковой металлургии в виде пластин или коронок. Основными компонентами таких сплавов являются карбиды вольфрама WC, титана TiC, тантала ТаС и ниобия NbС, мельчайшие частицы которых соединены посредством сравнительно мягких и менее тугоплавких кобальта или никеля
в смеси с молибденом (табл. 8). Твердые сплавы имеют высокую твердость – 88...92 HRA (72...76 HRC) и теплостойкость до 850...1000 °С, широко применяются для изготовления различного режущего инструмента.
С появлением твердых сплавов произошел резкий скачок в металлообработке. Скорости резания возросли в 5…10 раз по сравнению с обработкой инструментами из быстрорежущих сталей.
В настоящее время нашей промышленностью выпускаются
однокарбидные, двухкарбидные и трехкарбидные твердые сплавы –вольфрамовые (ВК), титановольфрамовые (ТК) и танталотитано-вольфрамовые (ТТК). Твердые сплавы подразделяются на марки,
отличающиеся одна от другой физико-механическими свойствами и процентным содержанием входящих в них элементов. Твердость НRА: ВК – 91…86; ТК – 92…87; ТТК – 87…89. Химический состав твердых сплавов легко расшифровывается по обозначению
марок.
Так, в сплаве ВК2 содержится 98 % WС и 2 % Со; в сплаве ВК8 содержится 92 % WС и 8 % Со; в сплаве Т15К6 содержится 79 % WС, 15 % ТiС и 6 %Со; в сплаве ТТ7К12 содержится 81 % WС,
Таблица 8
Содержание легирующих элементов в быстрорежущих сталях, %
Марка стали | С | W | Cr | V | Мо | Со |
Стали нормальной теплостойкости | ||||||
Р18 | 0,70…0,8 | 17,0…18,5 | 3,8…4,4 | 1,0…1,4 | До 1,0 | – |
Р12 | 0,8…0,9 | 12,0…13,0 | 3,8…4,4 | 1,5…1,0 | До 1,0 | – |
Р9 | 0,85…0,95 | 8,5…10,0 | 3,8…4,4 | 2,0…2,6 | До 1,0 | – |
Р6М5 | 0,8…0,9 | 5,5…6,5 | 3,8…4,4 | 1,7…2,1 | 5,0…5,5 | – |
Р6М3 | 0,85…0,95 | 5,5…6,5 | 3,0…3,5 | 2,0…2,5 | 3,0…3,6 | – |
Р8М3 | 0,8…0,9 | 7,6…8,4 | 3,6…4,0 | 1,6…1,9 | 3,0…3,5 | – |
Р2М5 | 0,95…1,05 | 1,7…2,3 | 3,8…4,3 | 0,9…1,3 | 4,8…5,3 | – |
11М5Ф | 1,0 | – | 3,8 | 1,2 | 5,1 | – |
Стали повышенной теплостойкости | ||||||
10Р8М3 | 0,96…1,05 | 7,5…8,5 | 3,3…3,9 | 1,7…2,1 | 3,0…3,6 | – |
10Р6М5 | 1,05 | 6,0 | 4,0 | 2,4 | 5,0 | – |
Р12Ф3 | 0,94…1,04 | 12,0…13,5 | 3,5…4,0 | 2,5…3,3 | До 1,0 | – |
Р2М3Ф8 | 0,90…1,05 | 2,0…2,5 | 4,0…4,8 | 7,5…8,5 | 2,5…3,0 | – |
|
Окончание табл. 8
Марка стали | С | W | Cr | V | Мо | Со |
Р9Ф5 | 1,4…1,5 | 9,0…10,5 | 3,8…4,4 | 4,3…5,1 | До 1,0 | – |
Р18Ф2К5 | 0,85…0,95 | 17,0…18,5 | 3,8…4,4 | 1,8…2,4 | До 1,0 | 5,0…6,0 |
Р6М5К5 | 0,8…0,9 | 6,0…7,0 | 3,8…4,3 | 1,7…2,2 | 4,8…5,8 | 4,8…5,3 |
Р9К5 | 0,9…1,0 | 9,0…10,5 | 3,8…4,4 | 2,0…2,6 | До 1,0 | 5,0…6,0 |
Р9К10 | 0,9…1,0 | 9,0…10,5 | 3,8…4,4 | 2,0…2,6 | До 1,0 | 9,5…10,5 |
Р9М4К8Ф | 1,0…1,1 | 8,5…9,6 | 3,0…3,6 | 2,1…2,5 | 3,8…4,3 | 7,5…8,5 |
10Р6М5Ф2К8 | 1,0 | 5,75 | 4,1 | 2,1 | 6,0 | 8,0 |
Р3М3Ф4К5 | 1,0 | 3,0 | 4,0 | 4,0 | 3,0 | 5,0 |
А11Р3М3Ф2 | 1,02…1,12 | 2,5…3,3 | 3,8…4,4 | 2,2…2,7 | 2,5…3,0 | – |
Стали высокой теплостойкости | ||||||
В11М7К23 | 0,1 | – | 0,5 | |||
В14М7К25 | 0,1 | – | 0,5 | |||
3В20К20Х4Ф | 0,25 | 4,0 | 1,0 | – |
4 %ТiС и 3 % ТаС, 12 % Со; в сплаве ТT20К9 содержится 71 % WС,8 % ТiС, 12% ТаС, 9 % Со.
Карбиды вольфрама, титана и тантала являются как бы режущими составляющими. В качестве связки выступает Со. Чем меньше Со
в сплаве, тем он более твердый, но более хрупкий, и прочность
его ниже.
Теплостойкость их – 800...950 °С; износостойкость выше быстрорежущих ~ в 50 раз.
Вольфрамовые сплавы менее износоустойчивы, чем титано-вольфрамовые, поэтому их лучше применять для обработки хрупких материалов. Сплавы ВК с меньшим содержанием Со используются для чистовой обработки, сплавы с большим содержанием Со – для черновых операций. Кроме того, сплавы группы ВК рекомендуется применять при обработке закаленных, жаропрочных, коррозионно-стойких и других труднообрабатываемых сталей и сплавов.
Применяемые в настоящее время твердые сплавы делятся на:
1) вольфрамовые сплавы группы ВК: ВК3, ВК3-М, ВК4, ВК6, ВК6-М, ВК6-ОМ, ВК8 и др. (табл. 9). Буква М означает, что сплав мелкозернистый (величина зерна до 1 мкм), а В – высокопрочный, крупнозернистый, в которых размер зерен 3…5 мкм. У других марок сплавов этой группы размеры зерен 1…2 мкм. В условном обозначении цифра показывает процентное содержание кобальта. Например, обозначение ВК8 показывает, что в нем 8 % кобальта
и 92 % карбидов вольфрама. Буквами ОМ обозначается особо мелкозернистая структура;
|
2) титановольфрамовые сплавы группы ТК: Т15К6, Т5К10, Т30К4, Т14К8, Т5К12, Т60К6 и др. В условном обозначении цифра, стоящая после буквы Т, показывает процентное содержание карбидов титана, после буквы К – кобальта, остальное – карбиды вольфрама;
3) титанотанталовольфрамовые сплавы группы ТТК: ТТ7К12, ТТ10К8, ТТ20К9, ТТ8К6 и др. В условном обозначении цифры, стоящие после букв Т, показывают процентное содержание карбидов титана и тантала, после буквы К – кобальта, остальное – карбиды вольфрама;
Таблица 9
Марки, химический состав и свойства вольфрамосодержащих
твердых сплавов
Группы сплавов | Марки сплавов | Состав сплавов, % | Физико-механические свойства | ||||
Карбид вольфрама | Карбид титана | Карбид тантала | Кобальт | Предел прочности при изгибе, МПа, не менее | Твердость HRA, не менее | ||
ВК | ВК3 | – | – | 89,5 | |||
ВК3-М | – | – | 91,0 | ||||
ВК4 | – | – | 89,5 | ||||
ВК4-В | – | – | 88,0 | ||||
ВК6 | – | – | 88,5 | ||||
ВК6-М | – | – | 90,0 | ||||
ВК6-ОМ | – | 90,5 | |||||
ВК6-В | – | – | 87,5 | ||||
ВК8 | – | – | 87,5 | ||||
ВК8-В | – | – | 86,5 | ||||
ТК | Т5К10 | – | 88,5 | ||||
Т15К6 | – | 90,0 | |||||
Т14К8 | – | 89,5 | |||||
Т30К4 | – | 92,0 | |||||
ТТК | ТТ7К12 | 87,0 | |||||
ТТ8К6 | 90,5 | ||||||
ТТ10К8-Б | 7* | 89,0 | |||||
ТТ20К9 | 89,0 |
* В смеси с карбидами ниобия.
4) безвольфрамовые твердые сплавы. В связи с дефицитом вольфрама появились так называемые безвольфрамовые твердые сплавы. Основой их является ТiС и (ТiМo)С, т.е. карбиды или карбонитриды ТiNiС; а связкой – Co или Мо.
Эти сплавы имеют высокую теплостойкость, низкую теплопроводность, высокую твердость (НRА 89…90). Они применяются для чистовой и получистовой обработки. Стойкость инструментов из этих сплавов в 1,5 раза выше, чем из Т15К6.
На никельмолибденовой связке выпускают следующие марки безвольфрамовых твердых сплавов: ТМ-3, ТН-20, КНТ-16; например ДНТ-16 состоит из 74 % карбонитридов титана ТiNiC и 16 % Мо.
|
Состав сплавов ТМ-1, ТМ-3, ТН-20, КНТ-16, ТС20ХН приведен в табл. 10. Обозначения этой группы твердых сплавов условные.
Во ВНИИинструмент проведены исследования более 30 сплавов, показавшие, что наиболее перспективными с точки зрения практического применения являются твердые сплавы ТН-20 и КНТ-16.
Таблица 10
Марки, химический состав и свойства безвольфрамовых
твердых сплавов
Марки сплавов | Состав сплавов, % | Физико-механические свойства | |||||
Карбиды титана и ниобия | Карбонитриды титана | Карбиды титана | Никель | Молибден | Предел прочности при изгибе, МПа, не менее | Твердость НRА, не менее | |
Тм-1 | – | – | 5,0 | 5,0 | |||
ТМ-3 | – | – | 21,0 | 15,0 | |||
ТН-20 | – | – | 15,0 | 6,0 | |||
КНТ-10 | – | – | 19,5 | 6,5 |
На инструментальных заводах Минстанкопрома освоено промышленное производство резцов, оснащенных пластинами из этих сплавов.
Сплав КНТ-16 состоит из 84 % карбонитрида и 16 % молибдено-никелевой связи. Прочность на изгиб s b – 1200 МПа, НRА 89...90.
ТН-20 состоит из 80 % карбида Тi и 20 % молибденоникелевой связки; s b ~ 1100 МПа; НRА – 91.
Разрабатываются новые составы безвольфрамовых твердых сплавов и методы их изготовления. Один из них – метод высокотемпературного самораспространяющегося синтеза (ССВС).
Рекомендации по применению твердых сплавов
Сплавы группы ТК более износостойки и имеют повышенную теплостойкость по сравнению с ВК. Сплавы группы ТТК предпочтительно применять для обработки труднообрабатываемых сталей
и сплавов. Тантал придает сплаву большую вязкость и прочность. Твердые сплавы с особомелким (субмикронным) зерном имеют повышенную прочность и стойкость. Выпускаются сплавы на основе карбида вольфрама: ВК6-ХОМ, ВК10-ХОМ, ВК15-ХОМ. Они рекомендуются для обработки труднообрабатываемых материалов.
Нанесение тонкого износостойкого покрытия (толщиной
5…10 мкм) на твердые сплавы является весьма перспективным способом упрочнения поверхностного слоя и повышения режущих свойств инструмента. Для этого применяют карбиды и нитриды титана (ТiС и ТiN) или их сочетание – карбонитриды.
Твердые сплавы выпускаются в виде стандартизованных пластин, которые припаиваются, приклеиваются или крепятся механически к державкам из конструкционной стали. Выпускаются также инструменты, рабочая часть которых целиком выполнена из твердого сплава (монолитные).
|
Правильным выбором марки твердого сплава обеспечивается эффективная эксплуатация режущих инструментов. Для конкретного случая обработки сплав выбирают исходя из оптимального сочетания его теплостойкости и прочности. Например, сплавы группы ТК имеют более высокую теплостойкость, чем сплавы ВК. Инструменты, изготовленные из этих сплавов, могут использоваться при высоких скоростях резания, поэтому их широко применяют при обработке сталей.
Инструменты из твердых сплавов группы ВК применяют при обработке деталей из конструкционных сталей в условиях низкой жесткости системы станок–приспособление–инструмент–деталь, при прерывистом резании, при работе с ударами, а также при обработке хрупких материалов типа чугуна, что обусловлено повышенной прочностью этой группы твердых сплавов и невысокими температурами в зоне резания.
Такие сплавы используются также при обработке деталей из высокопрочных, жаропрочных и нержавеющих сталей, титановых сплавов. Это объясняется тем, что наличие в большинстве этих материалов титана вызывает повышенную адгезию со сплавами группы ТК, также содержащими титан. Кроме того, сплавы группы ТК имеют значительно худшую теплопроводность и более низкую прочность, по сравнению со сплавами ВК.
Введение в твердый сплав карбидов тантала или карбидов тантала и ниобия (ТТ10К8-Б) повышает его прочность. Поэтому трех-
и четырехкарбидные твердые сплавы применяются для оснащения инструментов, работающих с ударами и по загрязненной корке. Однако температура теплостойкости этих сплавов ниже, чем у двухкарбидных. Из твердых сплавов с существенно улучшенной структурой следует отметить особомелкозернистые, применяемые для обработки материалов с большой истирающей способностью. Сплавы ОМ обладают плотной, особомелкозернистой структурой, а также имеют малый (до 0,5 мкм) размер зерен карбидов вольфрама. Последнее обстоятельство позволяет затачивать и доводить инструмент, изготовленный из них, с наименьшими радиусами режущих кромок. Инструменты из сплавов этой группы применяются для чистовой и получистовой обработки деталей из высокопрочных вязких сталей
с повышенной склонностью к наклепу.
Незначительное добавление в состав сплавов группы ОМ карбида тантала и кобальта способствует повышению их теплостойкости, что позволяет использовать эти сплавы при изготовлении инструментов, предназначенных для черновой обработки деталей из различных сталей. Весьма эффективна замена карбидов тантала карбидами хрома. Это обеспечивает получение сплавов с мелкозернистой однородной структурой и высокой износостойкостью. Представителем таких материалов является сплав ВК10-XOM.
|
Сплавы с низким процентным содержанием кобальта (Т30К4, ВК3, ВК4) обладают меньшей вязкостью и применяются для изготовления инструментов, срезающих тонкие стружки на чистовых операциях. Наоборот, сплавы с большим содержанием кобальта (ВК8, Т14К8, Т5К10) являются более вязкими и применяются при снятии стружек большого сечения на черновых операциях.
Работоспособность твердых сплавов значительно возрастает при нанесении на них износостойких покрытий.
Минералокерамика
Из современных инструментальных материалов заслуживает внимания минералокерамика, которая не содержит дорогостоящих
и дефицитных элементов. В основе минералокерамики лежит окись алюминия Аl2О3. Она дешевле других инструментальных материалов. оксидная минералокерамика ЦМ-332 имеет более высокую твердость (на 2…5 единиц), а теплостойкость 1200 °С, а также повышенную износостойкость по сравнению с твердыми сплавами. Однако этот материал хрупок и малопрочен. вследствие ее малой прочности (s b ~300 МПа) используемая до настоящего времени оксидная минералокерамика ЦМ-332 не нашла широкого применения
в качестве режущего материала.
Всесоюзный научно-исследовательский институт абразивов
и шлифования (ВНИИАШ) создал оксидную керамику марки ВШ-75. ее рекомендуется применять при чистовой и получистовой обработке сталей и чугунов. Минералокерамика допускает скорость резания
в 1,5…2 раза выше, чем твердые сплавы.
Всесоюзный научно-исследовательский институт тугоплавких металлов и твердых сплавов (ВНИИТС) разработал минералокерамку оксидно-карбидного типа, полученную методом горячего прессования марок В-3, ВОК-60 и ВОК-63 и методом холодного прессования ВО-13, ВО-15, ВО-16. В основе ее лежат окись алюминия и добавки карбидов тугоплавких металлов – вольфрама, титана. Режущие свойства их выше керамики ВШ; стойкость в 3…5 раз выше, чем стойкость сплавов Т3ОК4.
Минералокерамика В-3, ВОК-60, ВОК-63 применяется для получистовой и чистовой обработки сталей и высокопрочных чугунов. Основу ее составляют оксиды алюминия Аl2O3 с небольшой добавкой оксида магния MgO (0,5...1 %). Высокая твердость минералокерамики, теплостойкость до 1200 °С, химическая инертность к металлам, сопротивление окислению во многом превосходят эти же параметры твердых сплавов. Однако минералокерамика уступает этим сплавам по теплопроводности, имеет более низкий предел прочности на изгиб. Современная минералокерамика, созданная в нашей стране и за рубежом, по прочности приближается к наиболее износостойким твердым сплавам. Минералокерамику на основе оксида алюминия можно разделить на три группы:
1) чисто оксидная керамика (белая), основу которой составляет оксид алюминия с незначительными примесями (АlО3 – до 99,7 %);
2) керамика, представляющая собой оксид алюминия с добавлением металлов (титан, ниобий и др.);
3) оксидно-карбидная (черная) керамика оксид алюминия с добавлением карбидов тугоплавких металлов (титана, вольфрама, молибдена) для повышения ее прочностных свойств и твердости.
Отечественная промышленность в настоящее время выпускает оксидную керамику ЦМ-332, ВО-13 и оксидно-карбидную В-3,
ВОК-60, ВОК-63, в состав которой входит до 40 % карбидов титана, вольфрама и молибдена. Наряду с материалами на основе оксида алюминия выпускается материал на основе нитрида кремния – силинит-Р и кортинит ОНТ-20 (с добавками оксидов алюминия и некоторых других веществ). Физико-механические свойства режущей минералокерамики приведены в табл. 11.
Таблица 11
Физико-механические свойства режущей минералокерамики
Марка | Плотность, г/см3, не менее | Твердость НRА | Предел прочности при изгибе, МПа, не менее |
ЦМ-332 | 3,85 | 90…92 | 295…350 |
ВО-13 | 3,95 | 90…92 | 450…500 |
ОНТ-20 | 4,30 | 92…94 | 500…650 |
В-3 | 4,50 | 92…94 | 560…600 |
ВОК-60 | 4,20 | 92…94 | 560…600 |
ВОК-63 | 4,20 | 92…93 | 635…700 |
Силинит-Р | – | 94…96 | 500…700 |
Высокие режущие свойства инструментов из минералокерамики проявляются при скоростной обработке сталей и высокопрочных чугунов, причем чистовое и получистовое точение и фрезерование повышает производительность обработки деталей до 2 раз при одновременном возрастании периодов стойкости инструментов до 5 раз по сравнению с обработкой инструментами из твердого сплава.
Минералокерамика выпускается в виде неперетачиваемых пластин, что существенно облегчает условия ее эксплуатации.
Инструмент, оснащенный пластинами из керамики, прошел промышленные испытания. На ВАЗе режущую керамику применяют на семи позициях чистовой обработки деталей из серого чугуна. На
КамАЗе режущую керамику широко используют при обработке тормозных барабанов, гильз деталей. На заводе «Красный пролетарий» при чистовой обработке деталей из серого чугуна резцы ВК3-М были заменены керамикой ВОК-60. Машинное время сократилось за счет увеличения скорости резания почти в 6 раз при одновременном увеличении стойкости в 5…6 раз.
Разработанные отечественные марки керамики не уступают по своим свойствам физико-механическим свойствам керамики зарубежных фирм. Применение режущих пластин из керамики позволило повысить скорость резания в 2…4 раза при одновременном повышении стойкости до двух раз.
Абразивные материалы
Абразивные материалы – это вещества природного или синтетического происхождения, содержащие минералы высокой твердости и прочности, зерна и порошки которых способны обрабатывать поверхности других тел путем царапания, скобления или истирания. Их применяют для изготовления шлифовальных и заточных кругов, головок, брусков, хонов, доводочных порошков и паст.
Абразивные материалы разделяют на естественные и искусственные.
К первым относятся кварц, наждак и корунд. Все они имеют сравнительно низкие режущие свойства и поэтому мало применяются в абразивной промышленности. Кроме того, залежи корунда
в природе ограничены.
Для абразивных инструментов в основном применяют искусственные абразивные материалы: электрокорунд, карбид кремния, карбид бора, силикокарбид бора.
Электрокорунд получают методом электрической плавки в дуговых печах при температуре 2000…2500 °С из материалов, богатых окисью алюминия (бокситы, глинозем). В зависимости от процентного содержания А12О3 электрокорунд бывает нормальный, белый, легированный и монокорунд.
Карбид кремния SiC получают в печах при температуре 1800…1850 °С из нефтяного кокса, антрацита, т.е. из материалов, богатых кремнеземом и высоким содержанием углерода. Карбид кремния разделяется на черный 5С и зеленый 6С. Лучше из них зеленый: он имеет большую твердость и лучшие режущие кромки.
Карбид бора В4С получают при плавке борной кислоты В2О3
и нефтяного кокса в электропечах. Применяется в виде порошков или паст для доводки твердоплавкого инструмента.
|
|
Организация стока поверхностных вод: Наибольшее количество влаги на земном шаре испаряется с поверхности морей и океанов (88‰)...
Автоматическое растормаживание колес: Тормозные устройства колес предназначены для уменьшения длины пробега и улучшения маневрирования ВС при...
Общие условия выбора системы дренажа: Система дренажа выбирается в зависимости от характера защищаемого...
Археология об основании Рима: Новые раскопки проясняют и такой острый дискуссионный вопрос, как дата самого возникновения Рима...
© cyberpedia.su 2017-2024 - Не является автором материалов. Исключительное право сохранено за автором текста.
Если вы не хотите, чтобы данный материал был у нас на сайте, перейдите по ссылке: Нарушение авторских прав. Мы поможем в написании вашей работы!