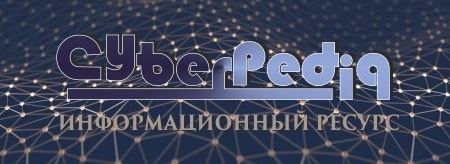
Опора деревянной одностоечной и способы укрепление угловых опор: Опоры ВЛ - конструкции, предназначенные для поддерживания проводов на необходимой высоте над землей, водой...
Семя – орган полового размножения и расселения растений: наружи у семян имеется плотный покров – кожура...
Топ:
Комплексной системы оценки состояния охраны труда на производственном объекте (КСОТ-П): Цели и задачи Комплексной системы оценки состояния охраны труда и определению факторов рисков по охране труда...
Устройство и оснащение процедурного кабинета: Решающая роль в обеспечении правильного лечения пациентов отводится процедурной медсестре...
Оценка эффективности инструментов коммуникационной политики: Внешние коммуникации - обмен информацией между организацией и её внешней средой...
Интересное:
Мероприятия для защиты от морозного пучения грунтов: Инженерная защита от морозного (криогенного) пучения грунтов необходима для легких малоэтажных зданий и других сооружений...
Принципы управления денежными потоками: одним из методов контроля за состоянием денежной наличности является...
Искусственное повышение поверхности территории: Варианты искусственного повышения поверхности территории необходимо выбирать на основе анализа следующих характеристик защищаемой территории...
Дисциплины:
![]() |
![]() |
5.00
из
|
Заказать работу |
|
|
Качество стали определяется содержанием в ней вредных примесей – серы, фосфора, газов (О2, N2 , Н2)
По качеству стали могут быть: обыкновенного качества,
качественные, высококачественные, особо высокого качества
Удаление вредных примесей происходит в процессе :
- шлакообразования и газообразования при плавке чугуна и стали;
- раскисления стали, т.е. уменьшения количества FeO, в процессе плавки путем введения Si, Mn, Al;
- рафинирования и дегазации при разливке стали;
- переплава стали в электропечах (вакуумный переплав в ЭДП и ЭИП, электрошлаковый, электронно-лучевой и плазменно-дуговой переплав)
Лекция № 4
Основы порошковой металлургии
Порошковая металлургия – это область науки техники, охватывающая совокупность методов производства порошков химических элементов (металлов и неметаллов) и соединений, полуфабрикатов и изделий из них или их смесей в том числе с волокнистыми материалами (без расплавления основных компонентов).
Типовая технология изготовления изделий методом порошковой металлургии предусматривает следующие этапы:
1) получение порошков;
2) формование (прессованием и прокатной заготовок из порошка с использованием связей или без нее);
3) спекание /заготовки;
4) дополнительная обработки спеченных изделий (механическая, пропитка и т.д.).
Достоинство порошковой металлургии
-возможность получения материалов и изделий из них с комплексом свойств и структурой, которые невозможно получить другими методами (литьем, обработкой давлением и т.д.)
Основные материалы, получаемые методами порошковой металлургии представляют собой композиционные материалы, состоящие из разнородных компонентов, например, спеченные стали (Fe + графит + легирующие элементы)
|
- цветные металлы и сплавы (пористый титан, спеченные алюминиевые сплавы)
- тугоплавкие металлы (вольфрам, молибден, ниобий, тантал и др.)
- керметы (керамико-металлические материалы керамическая фаза (бериды карбиды оксиды нитриды) и металлическая фаза (сталь, никель, кобальт, тугоплавкие металлы)
P азливка стали
После завершения плавки металл из плавильной печи выпускают в разливочный ковш и транспортируют к месту разливки.
Для выравнивания химического состава металла и очистки его от газов и неметаллических включений сталь определенное время выдерживают в ковше.
В зависимости от степени раскисления сталь делят на кипящую, спокойную, полуспокойную.
Спокойная сталь раскисляют марганцем, кремнием и алюминием. Кислород при этом не проявляет активности и реакция окисления углерода FeO + C FeC + CO прекращают. Разливка и кристаллизация спокойной стали протекают почти без газового выделения, при разливке кипящей происходит окисление угерода и активное выделение пузырьков газа СО.
Разливка стали в изложницы.
Изложницы – это толстостенная, в основном чугунная форма, используемая при литье стальных слитков. Масса слитка колеблется от 1 до 12т.
Существуют два способа разливки стали в изложницы: сверху и снизу (сифоном).
Преимущества разливки сверху:
1) использование более простого оборудования;
2) отсутствие отходов металла на литниковую систему.
Недостатки:
1) более низкое качество поверхности слитков;
2) значительная продолжительность процесса.
Преимущества способа ифонной разливки:
1) получение более чистой поверхности слитка;
2) высокая производительность процессов.
Недостатки:
1) более сложная технология сборки поддонов и центровых литников;
2) дополнительные расходы металла на литники;
3) возможность загрязнения стали неметаллическими включениями в процессе перемещения расплава по литниковой системе.
|
Непрерывная разливка стали
Непрерывная разливка стали состоит в том, что жидкую сталь из ковша 1 через промежуточное разливочное устройство 2 непрерывно подают в водоохлаждаемую изложницу без дна – кристаллизатор 3, из нижней части которого вытягивается затвердевающий слиток 5. Перед заливкой металла в кристаллизатор вводят затравку – стальную штангу со сменной головкой, имеющей паз в виде ласточкиного хвоста, которая в начале заливки служит дном кристаллизатора. Вследствие интенсивного охлаждения жидкий металл у стенок кристаллизатора и на затравке затвердевает, образуется корка, соединяющая металл с затравкой. Затравка движется вниз при помощи тяговых роликов 6, постепенно вытягивая затвердевающий слиток из кристаллизатора. После прохождения тяговых роликов 6, затравку отделяют. Скорость вытягивания составляет в среднем 1 м/мин. Окончательное затвердевание в сердцевине происходит в результате вторичного охлаждения водой из брызгал 4. Затем затвердевший слиток попадает в зону резки, где его разрезают газовым резаком 7, на куски заданной длины. Слитки имеют плотное строение и мелкозернистую структуру, отсутствуют усадочные раковины.
Вакуумная обработка стали
Позволяет значительно уменьшить количество газов, растворенных в расплаве и неметаллических включений, что повышает качество слитка.
|
|
История создания датчика движения: Первый прибор для обнаружения движения был изобретен немецким физиком Генрихом Герцем...
Поперечные профили набережных и береговой полосы: На городских территориях берегоукрепление проектируют с учетом технических и экономических требований, но особое значение придают эстетическим...
Кормораздатчик мобильный электрифицированный: схема и процесс работы устройства...
Археология об основании Рима: Новые раскопки проясняют и такой острый дискуссионный вопрос, как дата самого возникновения Рима...
© cyberpedia.su 2017-2024 - Не является автором материалов. Исключительное право сохранено за автором текста.
Если вы не хотите, чтобы данный материал был у нас на сайте, перейдите по ссылке: Нарушение авторских прав. Мы поможем в написании вашей работы!