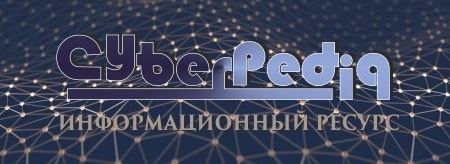
Историки об Елизавете Петровне: Елизавета попала между двумя встречными культурными течениями, воспитывалась среди новых европейских веяний и преданий...
Биохимия спиртового брожения: Основу технологии получения пива составляет спиртовое брожение, - при котором сахар превращается...
Топ:
История развития методов оптимизации: теорема Куна-Таккера, метод Лагранжа, роль выпуклости в оптимизации...
Особенности труда и отдыха в условиях низких температур: К работам при низких температурах на открытом воздухе и в не отапливаемых помещениях допускаются лица не моложе 18 лет, прошедшие...
Методика измерений сопротивления растеканию тока анодного заземления: Анодный заземлитель (анод) – проводник, погруженный в электролитическую среду (грунт, раствор электролита) и подключенный к положительному...
Интересное:
Подходы к решению темы фильма: Существует три основных типа исторического фильма, имеющих между собой много общего...
Наиболее распространенные виды рака: Раковая опухоль — это самостоятельное новообразование, которое может возникнуть и от повышенного давления...
Инженерная защита территорий, зданий и сооружений от опасных геологических процессов: Изучение оползневых явлений, оценка устойчивости склонов и проектирование противооползневых сооружений — актуальнейшие задачи, стоящие перед отечественными...
Дисциплины:
![]() |
![]() |
5.00
из
|
Заказать работу |
|
|
В процессе изготовления сварных конструкций в них возникают сварочные напряжения и деформации. Сварочные напряжения, превышающие предел текучести металла, вызывают пластическую деформацию его. Это приводит к изменению размеров и формы изделия, т.е. к его короблению. Если сварочные напряжения превышают предел прочности, то происходит разрушение сварного шва или соединения, т.е. образуются трещины. Причинами возникновения сварочных напряжений и деформаций являются: неравномерное нагревание металла при сварке, литейная усадка расплавленного металла и структурные превращения в металле в процессе его охлаждения.
4.1.Неравномерное нагревание металла
Как известно, все металлы при нагревании расширяются, а при охлаждении сжимаются. При наличии жестких связей между нагретыми и холодными участками металла это приводит к образованию сжимающих или растягивающих внутренних сварочных напряжений. Рассмотрим несколько примеров.
При местном нагреве пластины длиной l свободно лежащей на сварочном столе, размеры ее по длине увеличатся на величину Δ l. Это увеличение будет зависеть от коэффициента линейного расширения данного металла, длины нагретой зоны, а также температуры ее нагрева. В процессе охлаждения, по мере уменьшения температуры, удлинение будет уменьшаться и при начальной температуре оно станет равным нулю. После охлаждения пластина приобретает свои первоначальные размеры и в ней не будет ни внутренних напряжений, ни остаточных деформаций. При местном нагреве этой же пластины, но жестко закрепленной с обоих концов, она не может свободно удлиняться, поэтому в ней возникнут сжимающие внутренние напряжения. При высоком нагреве (более 600° С) сжимающие напряжения превзойдут предел текучести нагретого участка, в нем произойдет пластическая деформация сжатия и на длине l ' он станет несколько толще. Напряжения сжатия частично исчезнут. При охлаждении пластина должна бы укоротиться, но этому препятствует жесткое закрепление, в результате чего в ней возникнут растягивающие напряжения.
|
Аналогичным образом возникают внутренние напряжения и деформации при наплавке валика на кромку полосы. Наплавленный валик и нагретая часть полосы будут расширяться и растягивать холодную часть полосы, вызывая в ней растяжение с изгибом. Сам же валик и нагретая часть полосы будут сжаты, поскольку их тепловому расширению препятствует холодная часть полосы. Растягивающие напряжения принято обозначать знаком плюс (+), а сжимающие – знаком минус (–). В результате такого распределения напряжений полоса прогнется выпуклостью вверх. В процессе остывания наплавленный валик и нагретая часть полосы, претерпев пластические деформации, будут укорачиваться. Этому укорочению снова будут препятствовать верхние слои холодного металла полосы. Теперь уже наплавленный валик и нагретая часть полосы будут стягивать верхние холодные волокна ее. Они сожмутся и полоса прогнется выпуклостью вниз.
В реальных условиях изменение температур от нагретой к холодной зоне полосы происходит плавно, поэтому на графиках распределения температур переход от растягивающих напряжений к сжимающим также будет более плавным.
4.2.Литейная усадка расплавленного металла
В результате остывания и затвердевания жидкого металла сварного шва происходит его усадка. Явление усадки объясняется тем, что при затвердевании металл становится более плотным, в результате чего объем его уменьшается. Ввиду того, что металл шва жестко связан с основным металлом, остающимся в неизменном объеме, который противодействует этой усадке, то в сварном соединении возникают внутренние напряжения.
|
При сварке происходит продольная и поперечная усадка расплавленного металла, в результате чего образуются продольные и поперечные внутренние напряжения, вызывающие деформации сварных изделий.
В результате продольной усадки возникает коробление изделии в продольном направлении.
Поперечная усадка, как правило, приводит к угловым деформациям, т.е. к короблениям листов в сторону большего объема расплавленного металла.
4.3.Структурные превращения в металле
При сварке легированных и высокоуглеродистых сталей наряду с тепловыми напряжениями сжатия возникают объемные структурные напряжения.
Объясняется это тем, что при охлаждении изменяется структура металла. Это приводит к изменению размеров и взаимному расположению его зерен, сопровождающемуся изменением объема металла, что и вызывает внутренние напряжения. При сварке низкоуглеродистых и низколегированных не закаливающихся сталей структурные напряжения почти не возникают.
4.4.Методы борьбы с деформациями
Методы борьбы с деформациями включают в себя мероприятия, выполняемые до сварки, в процессе сварки и после сварки.
4.4.1.Мероприятия, выполняемые досварки
Рациональное конструирование сварных изделий. В процессе конструирования необходимо ограничивать количество наплавленного металла путем уменьшения угла скоса кромок или уменьшения катетов швов, не допускать пересечения швов, не располагать сварные швы там, где действуют максимальные напряжения от внешних нагрузок, размещать их симметрично, применять преимущественно стыковые швы и т. п.
4.4.1.1.Правильная сборка деталей с учетом возможных деформаций
При этом наиболее часто применяются обратные деформации. Зная, что шов после охлаждения всегда сокращается в размерах, можно заранее предугадать характер возможных напряжений и деформаций и произвести предварительный выгиб свариваемых деталей в противоположную сторону. Величина обратного выгиба определяется расчетным или опытным путем. При сборке деталей следует избегать прихваток, которые создают жесткое закрепление деталей и способствуют возникновению значительных остаточных напряжений. Лучше применять сборочные приспособления, допускающие некоторое перемещение деталей при усадке металла.
|
4.4.2.Мероприятия, выполняемые в процессе сварки
Конструкции следует сваривать так, чтобы замыкающие швы, создающие жесткий контур, заваривались в последнюю очередь. Сварку нужно вести от середины конструкции к ее краям, как бы сгоняя при этом внутренние напряжения наружу. Каждый последующий шов при многослойной сварке рекомендуется накладывать в направлении, обратном наложению предыдущего шва.
Если сваривают полотнища из отдельных листов, то в первую очередь нужно выполнять поперечные швы отдельных поясов, что обеспечит их свободную усадку, а затем сваривать пояса между собой продольными швами. В противном случае возможно образование трещин в местах пересечения поперечных и продольных швов. При сварке двутавровых балок в первую очередь сваривают стыковые соединения стенок и полок, а затем производят сварку угловых поясных швов. При сварке цилиндрических сосудов из нескольких обечаек сначала выполняют продольные швы обечаек, а затем сваривают обечайки между собой кольцевыми швами. При ручной и полуавтоматической сварке швов большой протяженности рекомендуется применение обратноступенчатого порядка наложения сварных швов.
4.4.2.1.Уравновешивание деформаций
В этом случае назначают такую последовательность выполнения швов, при которой последующий шов должен вызывать деформации обратного направления по сравнению с деформациями от предыдущего шва. Этот способ может быть использован при симметричном расположении швов.
4.4.2.2.Жесткое закрепление деталей при сварке
В этом случае детали закрепляют в сборочно-сварочных приспособлениях, обладающих значительной жесткостью. После сварки в таких приспособлениях короблений деталей почти не будет, но в сварных швах возрастут внутренние напряжения.
4.4.3.Мероприятия, выполняемые после сварки
В тех случаях, когда деформации все таки произошли и величина их выходит за пределы допустимых, применяется правка сварных изделий различными способами.
4.4.3.1.Механическая правка
В этом случае при помощи молотов, домкратов, винтовых прессов или других устройств создается ударная или статическая нагрузка, которая обычно прилагается со стороны наибольшего выгиба изделия.
|
Это мероприятие довольно трудоемкое, а неправильное его выполнение может привести к образованию трещин и надрывов. Изделия из тонколистового металла можно править прокатыванием их между валками. При этом на сварные швы предварительно устанавливаются накладки. В результате такой прокатки сварной шов растягивается, в нем происходят пластические деформации, снижающие напряжения и вызванные ими коробления.
4.4.3.2.Термическая правка
Это мероприятие состоит в местном нагреве небольших участков металла деформированной конструкции. Нагрев, как правило, производят сварочными горелками большой мощности. Он ведется быстро и только до пластического состояния верхних волокон на выпуклой стороне изделия. При охлаждении нагретых участков последние сжимаются и выпрямляют изделие. Исправление деформации сварной тавровой балки производится нагревом выпуклой части вертикальной стенки. Ширина полос нагрева 20—30 мм. Полосы нагрева сходятся под углом 30°. При правке сварных швеллеров помимо треугольных участков нагрева, располагаемых на обеих полках, производится нагрев нескольких полос на его стенке. Нагревать нужно ту поверхность, сжатие которой придает изделию правильную форму. Температура нагрева поверхности зависит от толщины металла и может быть выбрана по табл.3.
Таблица 3
Температуры нагрева стали при термической правке
Толщина металла, мм | до 6 | 7—12 | 13—20 | свыше 20 |
Температура нагрева, °С | 300—500 | 500—650 | 650— 800 | 800-850 |
Для определения температуры нагрева можно пользоваться таблицами температур, соответствующих различным цветам нагрева стали и появлению цветов побежалости. Особенно внимательно следует выполнять нагрев при правке на улице в солнечные дни, так как наличие яркого освещения искажает цвет нагреваемого участка. Более точно контроль температуры нагрева может осуществляться оптическими или радиационными пирометрами.
4.4.3.3.Термомеханическая правка
Данный способ состоит в сочетании местного нагрева с приложением статической нагрузки, изгибающей исправляемый элемент конструкции в нужном направлении.
Эта нагрузка может создаваться домкратами, прессами и другими устройствами. Применение дополнительного усилия способствует более интенсивному воздействию нагрева. Такой способ обычно применяется для правки жестких сварных узлов.
|
Все способы правки желательно вести в приспособлениях, позволяющих контролировать размеры выпрямляемых элементов и его прогибы.
Существует несколько методов уменьшения внутренних напряжений. Наиболее часто применяется предварительный или сопутствующий подогрев при сварке, проковка или прокатка сварных швов, статическое нагружение сварной конструкции, отпуск после сварки и др.
Предварительный или сопутствующий подогрев применяется при сварке сталей, склонных к закалке и образованию трещин. Температуру подогрева выбирают в зависимости от марки стали и жесткости конструкции. Обычно она лежит в пределах 100—600° С. Подогрев производится многопламенными горёлками, индукторами или в печах.
Подогрев уменьшает пластические деформации сжатия, что значительно снижает остаточные напряжения. Кроме того, в ряде случаев он благоприятно влияет на структуру металла шва и околошовной зоны.
Послойная проковка швов выполняется пневматическим зубилом с закругленным бойком непосредственно после сварки по горячему металлу (горячая проковка) или после полного остывания его (холодная проковка). Благодаря осадке металла в направлении удара происходит его раздача в разные стороны, что снижает растягивающие напряжения. Проковка рекомендуется при многослойной сварке металла большой толщины, причем во избежание трещин и надрывов первый и последний слои многослойного шва не проковывают. Швы на металле, склонном к закалке, проковывать нельзя. Преимущество проковки состоит в ее простоте и маневренности.
Прокатка шва выполняется при сварке тонколистового металла. В процессе прокатки растягивающие напряжения уменьшаются. Преимущество ее перед проковкой состоит в статическом характере приложения давления и возможности плавном регулировки его.
Статическое нагружение элементов сварной конструкции возможно в процессе сварки или чаще всего после полного остывания шва. В качестве такого нагружения применяется растяжение или изгиб с образованием растягивающих напряжений в зонах, где остаточные напряжения максимальны. Это приводит к пластическим деформациям и значительному уменьшению остаточных напряжений.
Отпуск после сварки, обычно применяемый для выравнивания структуры шва и околошовной зоны, также снижает внутренние напряжения. Отпуск может быть общий, когда нагревается все изделие, и местный, когда нагревается лишь часть его в зоне сварного соединения. Преимущество общего отпуска состоит в том, что снижение напряжений происходит во всей сварной конструкции, независимо от ее сложности. Наиболее часто применяется высокий отпуск при температуре нагрева 550—680° С. Операция отпуска состоит из четырех стадий: нагрев, выравнивание температуры по длине и сечению изделия, выдержка при температуре отпуска и охлаждение. Выдержка независимо от толщины металла обычно составляет около трех часов, после чего происходит естественное охлаждение. По применению отпуск сварных конструкций значительно превосходит все методы снятия внутренних напряжений.
БАЛКИ
Типы поперечных сечений и размеры сварных балок весьма разнообразны. Если нагрузка приложена в вертикальной плоскости, чаще всего используют балки двутаврового сечения. При приложении нагрузки в вертикальной и горизонтальной плоскостях, а также при действии крутящего момента более целесообразно использование балок коробчатого сечения.
5.1. Сборка и сварка двутавровых балок
Обычно сварной двутавр состоит из трех основных листовых элементов: стенки и двух полок. Сборка балки должна обеспечить симметрию и взаимную перпендикулярность полок и стенки, прижатие их друг к другу и закрепление прихватками. При использовании сборочных кондукторов это достигается соответствующим расположением баз и прижимов по всей длине балки с последующей постановкой прихваток. На рис.15 показан универсальный сборочный кондуктор для сборки балок.
Рис.15. Универсальный сборочный кондуктор с пневматическими прижимами
В некоторых случаях для сварки балок удобны кантователи с кольцами (рис.16). Собранная балка укладывается на нижнюю часть 1 кольца, откидная часть 2 замыкается с помощью откидных болтов 3, и балка закрепляется системой зажимов 4, В том случае, если длина балки велика и необходимо предотвратить ее прогиб, можно между опорами расположить опорные разъемные кольца.
Рис.16. Кантователь с кольцами
При сварке двутавровых балок значительной высоты иногда используют простейшие приспособления, являющиеся составной частью сборочного стеллажа. Более целесообразны полуповоротные кондукторы (рис.17) с перекатными порталами для поджатия горизонтальных листов, обеспечивающие после сборки сварку двух поясных швов. При этом рама 7 кондуктора наклоняется на 45° в ту или иную сторону с помощью гидравлических цилиндров 2. Однако применение таких кондукторов требует дополнительных приспособлений и транспортных операций для сварки «в лодочку» второй пары поясных швов. Поэтому при изготовлении балок мостов нашли применение поворотные кондукторы для сборки и сварки балок длиной до 34,2м и высотой от 1,6 до 3,8м при ширине поясов до 1м.
Рис.17. Схема полуповоротного специализированного кондуктора для сборки двутавровых балок
5.2.Непрерывное производство сварных балок
Для высокопроизводительного изготовления сварных балок в непрерывных автоматических линиях большое значение приобретает применение сварки токами высокой частоты, обеспечивающей скорость сварки 10-60 м/мин, т.е. на порядок выше, чем при сварке под флюсом.
В 60-х годах в США были выпущены агрегаты для производства сварных двутавров из рулонного проката или обычных полос и листов с использованием сварки ТВЧ. Рулонные заготовки для стенки и полок двутавра подают к сварочному агрегату из трех разматывателей 1 (рис.18). Гибочное устройство 4 обеспечивает подачу полок в зону сварки под углом 4-7° к кромкам стенки. Скользящие контакты подводят ток к одной из полок и отводят от другой, что обеспечивает протекание сварочного тока вдоль поверхности стыкуемых элементов и через место их контакта под обжимными роликами. При непосредственной приварке полки к стенке сварное соединение приобретает неблагоприятную форму. Холодная высадка кромки стенки с увеличением ее толщины с зачисткой соединения после сварки в горячем состоянии позволяет обеспечить плавный переход от стенки к полке. В соответствии с этим в рассматриваемом агрегате (рис.4), кромки проходят предварительную осадку в машине 3 и свариваются с полками в сварочной установке 5. Затем балка проходит огневую зачистку 6, зону охлаждения 7, правку 8, дефектоскопию 9 и на отводящем роликовом конвейере разрезается летучей пилой 10. В случае значительной толщины полок их жесткие заготовки подают не из рулонов, а из питателей 2 поштучно. В процессе сварки эти заготовки проходят сварочный агрегат плотно прижатые торцами друг к другу.
Рис.18. Схема агрегата для изготовления двутавровых профилей сваркой ТВЧ
5.3.Элементы промышленных зданий
Широкополочные прокатные двутавры и тавры рекомендуется широко использовать при изготовлении подкрановых балок, колонн и других элементов строительных конструкций (рис. 19). Между собой подкрановые балки соединяют болтами, пропущенными через торцовые ребра жесткости, выступы этих ребер опирают на колонны.
Рис.19. Каркас несущего здания
Колонны могут быть постоянного и переменного сечения, сплошные и решетчатые. Их сечения обычно выполняют составными с использованием широкополочных прокатных профилей (рис.20). К изготовлению колонн условия монтажа предъявляют следующие требования: перпендикулярность оси колонны к опорной плоскости плиты башмака и соблюдение расстояния между колоннами, правильность расположения монтажных отверстий.
Рис.20. Основные типы стальных колонн:
а-постоянного сечения; б…д-переменного сечения; е-раздельного типа
5.4.Мостовые краны
Для конструкций крановых мостов малой и средней грузоподъемности характерны два типа. Мосты первого типа состоят из двух коробчатых пространственно-жестких балок объединенных по концам концевыми балками, в которых устанавливают ходовые колеса. В мостах второго типа каждая половина несущей конструкции представляет собой пространственную систему, составленную из двух вертикальных и двух горизонтальных ферм. Вертикальная ферма является главной, на ее верхнем поясе располагают рельс. Вспомогательная ферма соединяется с главной горизонтальными фермами. Все элементы половины моста приводятся к пространственно-жесткой системе при помощи раскосов. Схема движений мостового крана и тележки показана на рис.21.
Рис.21. Схема движений мостового крана
В настоящее время основной конструктивной формой главных балок считают коробчатое сечение с симметрично расположенным рельсом (рис.22). По сравнению с ферменной конструкцией она несколько тяжелее, но более технологична.
Рис.22. Рабочий чертеж главной балки кранового моста. Q=50/10т, L=22,5м
СТРОПИЛЬНЫЕ ФЕРМЫ
Стропильные фермы изготовляют трех основных типов: с параллельными поясами (рис. 23,а, б), полигональные (рис.23, в) и треугольные (рис.23, г).
Рис.23. Схемы ферм
Крепление ферм к колоннам показано на рис. 24, а,б,в. Такие фермы можно применять для перекрытия любых пролетов. Унифицированные фермы имеют пролеты 18, 24, 30 и 36м.
Рис.24. Крепление ферм к колоннам
Работают стропильные фермы при статической нагрузке. В качестве стержней используют главным образом прокатные и в меньшей степени гнутые замкнутые сварные профили и трубы. В общем объеме производства около 90% составляют фермы из парных прокатных уголков. Стержни в узлах соединяют или непосредственно, или с помощью вспомогательных элементов главным образом дуговой сваркой. Перспективным является применение точечной контактной сварки.
При сборке ферм особое внимание уделяют правильному центрированию стержней в узлах (рис.25), предотвращающему появление изгибающих моментов, не учтенных расчетом. В случае составных элементов их совместная работа обеспечивается постановкой прокладок (рис.26) на расстоянии ℓ, равном 40 радиусам инерции сечения для сжатых стержней или 80 радиусам инерции для растянутых.
Конструкции стропильных ферм с поясами из широкополочных тавров по сравнению с типовыми фермами из уголков получаются легче при меньшей трудоемкости и стоимости. Снижение массы фермы достигается в основном благодаря существенному уменьшению размеров узловых косынок, а также из-за отсутствия косынок в узлах крепления стоек к верхним поясам и исключения прокладок в поясах ферм (рис.27, а). Иногда удается крепить решетку непосредственно к поясу без косынок (рис. 27, б). Вэтом узле элементы прикреплены к верхнему поясу эксцентрично. Такая расцентровка в данном случае допустима благодаря малым усилиям в примыкающих раскосах и недонапряжения мощного верхнего пояса этой панели. Трудоемкость при изготовАн фермы с поясами из тавров снижается вследствие уменьшения числа деталей и сокращения длины сварных швов.
Целесообразно, чтобы конструкция узлов стропильных ферм с поясами из тавров и решеткой из парных уголков позволяла полностью расчленить операции: сначала сборка, затем сварка. Концы уголков раскоса рекомендуется смещать для этой цели вдоль оси раскоса на расстояния а1, а2, а3 (рис.27, а) относительно парных им уголков, располагаемых с другой стороны косынки так, чтобы разделка стыкового шва, приваривающего узловую косынку к стенке поясного тавра, оказалась доступной для сварки после сборки. При этом подварку корня стыкового шва с противоположной стороны выполняют только на участках, свободных от уголков раскоса.
Уменьшить массу фермы позволяет использование трубчатых профилей. Однако для труб круглого сечения непосредственное соединение в узле получается весьма трудоемким (рис.28). Иногда концы труб относительно небольших диаметров сплющивают, что упрощает их соединение в узлах дуговой сваркой. Значительно проще оказывается соединение в узлах труб прямоугольного или квадратного сечения.
6.1.Изготовление ферм
На рис. 29 показана схема кондуктора, смонтированного на базе сборочной плиты. По разметке геометрической схемы фермы в соответствии с чертежом настройки кондуктора устанавливают и прихватывают фиксаторы 1, 7 опорного узла, опоры 2, 4 уголков, фиксаторы 3 поясов, фиксаторы 5, б косынок.
Рис.29. Сборка фермы в кондукторе
При использовании универсальных сборных сборочных приспособлений (УССП) кондуктор собирают на базе плиты с Т-образными пазами (рис.30), набранной из отдельных секций. Номера на схеме фермы соответствуют номерам под рисунками узлов приспособлений. Регулируемые опоры обеспечивают фиксацию деталей в горизонтальной плоскости; регулировка по высоте осуществляется при помощи резьбы, фиксация – через отверстия в детали при помощи пробки. Детали, не имеющие отверстий, устанавливают по упорам, уголки закрепляют зажимами. Сборка заключается в последовательной установке деталей фермы в кондуктор и соединении их прихватками. Поджимают детали перед прихваткой с помощью инвентарных сборочных приспособлений: эксцентриковых зажимов, струбцин, вилок или переносной пневмогидравлической струбциной.
Рис.30. Кондуктор для ферм с применением универсально-сборочных приспособлений
Использованию механизированных поточных методов при изготовлении ферм препятствует не только разнообразие типоразмеров и ограниченное число изделий в серии, но и малая технологичность типовых конструктивных решений. Большое число деталей, составляющих ферму, усложняет сборочную операцию, приводит к необходимости выполнения множества дуговых швов, различным образом ориентированных в пространстве, и требует кантовки собранного изделия при сварке.
Эффективным способом, облегчающим создание автоматизированного производства по изготовлению решетчатых конструкций, является контактно-дуговая точечная сварка. Сквозное проплавление элементов суммарной толщиной 20-40мм без образования отверстия при этом способе обеспечивается предварительным их нагревом между электродами контактной машины. Это позволяет визуально контролировать качество выполненных соединений. Достоинством метода является также возможность резкого сокращения числа деталей путем выполнения бескосыночных соединений и исключение кантовки фермы, поскольку сварку производят с одной стороны.
6.2.Конструкции пролетных строений
Простейшее пролетное строение железнодорожного моста при езде поверху состоит из двух главных балок, связанных системой связей. Непосредственно на пояса балок укладывают мостовые брусья, на которых располагают рельсы. Главные балки обычно имеют двутавровое сечение. Такие пролетные строения с расчетными пролетами 18,2; 23,0 и 33,6 м изготовляют, как правило, цельносварными на заводе и доставляют на строительную площадку в готовом виде одним блоком (рис.31, а).
При езде понизу расстояние между главными балками значительно увеличивается, и возникает необходимость устройства балочной клети из продольных 2 и поперечных 1 балок. По такой схеме выполняют железнодорожные мосты больших пролетов со сквозными болтосварными фермами (рис.31, б).
Рис.31,а. Главные балки и связи пролётного строения; 31,б. Пролетное строение (езда понизу)
|
|
Особенности сооружения опор в сложных условиях: Сооружение ВЛ в районах с суровыми климатическими и тяжелыми геологическими условиями...
Таксономические единицы (категории) растений: Каждая система классификации состоит из определённых соподчиненных друг другу...
Автоматическое растормаживание колес: Тормозные устройства колес предназначены для уменьшения длины пробега и улучшения маневрирования ВС при...
Папиллярные узоры пальцев рук - маркер спортивных способностей: дерматоглифические признаки формируются на 3-5 месяце беременности, не изменяются в течение жизни...
© cyberpedia.su 2017-2024 - Не является автором материалов. Исключительное право сохранено за автором текста.
Если вы не хотите, чтобы данный материал был у нас на сайте, перейдите по ссылке: Нарушение авторских прав. Мы поможем в написании вашей работы!