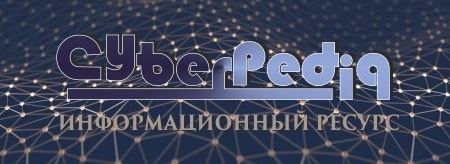
История развития хранилищ для нефти: Первые склады нефти появились в XVII веке. Они представляли собой землянные ямы-амбара глубиной 4…5 м...
Археология об основании Рима: Новые раскопки проясняют и такой острый дискуссионный вопрос, как дата самого возникновения Рима...
Топ:
Основы обеспечения единства измерений: Обеспечение единства измерений - деятельность метрологических служб, направленная на достижение...
Эволюция кровеносной системы позвоночных животных: Биологическая эволюция – необратимый процесс исторического развития живой природы...
Характеристика АТП и сварочно-жестяницкого участка: Транспорт в настоящее время является одной из важнейших отраслей народного хозяйства...
Интересное:
Берегоукрепление оползневых склонов: На прибрежных склонах основной причиной развития оползневых процессов является подмыв водами рек естественных склонов...
Что нужно делать при лейкемии: Прежде всего, необходимо выяснить, не страдаете ли вы каким-либо душевным недугом...
Аура как энергетическое поле: многослойную ауру человека можно представить себе подобным...
Дисциплины:
![]() |
![]() |
5.00
из
|
Заказать работу |
|
|
Содержание
Введение………………………………………………………………………………….3
1. Расчетно-технологическая часть ………………………………….………………….6
1.1. Организация работы производственного участка ТО и ремонта двигателей......6
1.2. Исходные данные для планирования…………………………………………......28
1.3. Расчет количества воздействий и дней простоя за цикл при ТО, ТР, КР………28
1.4. Расчет годовой и суточной производственной программы……………………..31
1.5. Распределение трудоемкости работ ТО и ТР……………………………………..33
1.6. Расчет общей годовой трудоемкости работ по всем видам ТО и ТР……………35
1.7. Расчет трудоемкости отдельных видов работ…………………………………….35
1.8. Расчет зон ТО и ТР………………………………………………………………….36
1.9. Расчет технологического оборудования…………………………………………..40
1.10. Расчет площадей производственных помещений………………………………43
2. Экономическая часть…………………………………………………………………45
2.1. Расчет стоимости 1 нормо-часа производственных рабочих……………………45
2.2. Расчет амортизационных отчислений…………………………………………….46
3. Охрана труда и окружающей среды…………………………………………………49
3.1. Техника безопасности при проведении ТО и ремонтном производстве………..49
3.2. Экологическая безопасность при эксплуатации, ТО и ремонте автомобилей….53
3.3. Пожарная безопасность……………………………………………………………..54
Заключение……………………………………………………………………………….56
Список используемой литературы………………………………………………….......58
НКП и ИТ 23.02.03.11732
Изм.
Лист
№ докум.
|
Подп.
Дата
Разраб.
Никишин Н.В
Организация работы производственного участка ТО и ремонта двигателей
Лит.
Листов
Пров.
Салин Ю.А.
58
НКП и ИТ гр. 1443
Н.контр.
Утв.
Введение
В настоящее время сравнительно мощная инфраструктура автотранспорта с разветвленной системой планирования организации перевозок и службой эксплуатации оснащена достаточно современной технологической базой для ТО и ремонта автомобилей. Однако существенного повышения эффективности перевозочного процесса при одновременном снижении себестоимости перевозок оказалось недостаточно – требуются поиски новых оптимальных решений, тем более в условиях перехода всей экономики на рыночные отношения. Приватизация и акционирование бывших АТП с полной или частичной передачей в частную собственность, в том числе и ПС, потребовало внести существенные изменения, как в организацию перевозочного процесса, так и в организацию ремонтной службы. Подверглось значительным изменениям, как в количественном, так и в качественном отношении, сама структура управления АТ. Следует отметить, что ранее наработанные и отлаженные основные положения эксплуатации, обслуживания и ремонта ПС АТ остались фактически без изменений, не считая отдельных “косметических” нововведений. По-прежнему, мощным рычагом повышения эффективности работы автотранспорта в целом является механизация и автоматизация производственных процессов ремонтной службы в АТП с внедрением в производство новейших технологий, гаражного оборудования (в том числе и зарубежных фирм). Существенную роль в повышении производительности труда ремонтных рабочих, а, следовательно, в снижении себестоимости работ по ТО поточного метода, а в зонах ТР специализированных постов (помимо универсальных), внедрение в производство агрегатного метода ремонта, когда вместо неисправных узлов и агрегатов на а/м сразу же ставят заранее отремонтированные из оборотного фонда – это позволяет резко сократить простой а/м в ремонте.
|
С этой целью необходимо выполнить проектные расчеты для построения нового АТП, которое четко будет выполнять свой производственный процесс по поддержания автопарка в работоспособном состоянии. Создание ремонтной базы и внедрение планово-предупредительной системы технического обслуживания и ремонта автомобилей значительно повышает коэффициент использования парка и производительность подвижного состава автомобильного транспорта, обеспечивает его хорошее техническое состояние, сокращает простои в работе по техническим причинам.
Автотранспортное предприятие применяет агрегатно-узловой и поточный методы организации производственного процесса, постепенно механизирует технологические процессы, морально и материально стимулирует внедрение в практику своей работы новейшие достижения науки, техники и передового опыта по техническому обслуживанию и
НКП и ИТ 23.02.03.11732
3
Изм.
Лист
№ докум.
Подп.
Дата
ремонту подвижного состава автомобильного транспорта.
Актуальность данной проблемы определила выбор темы нашего исследования: «Организация работы производственного участка ТО и ремонта двигателей».
Гипотеза исследования заключается в предположении о том, что для эффективного ремонта автомобилей и уменьшения времени простоя в ремонте, необходимо применить агрегатный метод ремонта автомобилей.
Создание соответствующих цехов и участков по ремонту, оборудованных современным автоматизированным оборудованием, необходимо для обеспечения работоспособности подвижного состава и сокращения затрат предприятий на приобретение новых единиц.
Объектом исследования является технологический процесс капитального ремонта двигателей КамАЗ.
Предметом исследования является участок капитального ремонта двигателей грузовых автомобилей.
Целью данного исследования является теоретическое обоснование и практическое подтверждение необходимости внедрения специализированных участков и технологии капитального ремонта двигателей КамАЗ.
Для достижения поставленной цели были сформулированы следующие задачи:
|
- выстроить последовательность технологического процесса капитального ремонта двигателей КамАЗ;
- выполнить расчеты годовой производственной программы работ по ТО и ТР;
- выполнить расчеты технологического процесса ТО и ТР автомобилей;
- спроектировать участок капитального ремонта двигателей грузовых автомобилей, подобрать технологическое оборудование в соответствии с требованиями нормативных документов;
- обозначить требования безопасности при выполнении разборочно-сборочных и регулировочных работ.
Для решения поставленных задач и проверки гипотезы использовались следующие методы исследования:
- критический анализ и синтез технической литературы по проблеме исследования;
- изучение и обобщение положительного опыта современных автотранспортных предприятий;
- наблюдение за процессом ремонтных работ;
- изучение технологий и документации по организации капитального ремонта двигателей КамАЗ;
НКП и ИТ 23.02.03.11732
4
Изм.
Лист
№ докум.
Подп.
Дата
- беседы с инженерно-техническими работниками автотранспортных предприятий по вопросу капитального ремонта двигателей КамАЗ;
- расчёты годовой производственной программы работ по ТО и ТР, технологического процесса ТО и ТР автомобилей.
Теоретической базой данного исследования являются законодательные и нормативно акты Российской Федерации по вопросу эксплуатации и ремонта автомобильного транспорта.
Исследование проводилось на базе Газпромдобыча Ноябрьск УТТиСТ.
Практическая значимость нашего исследования заключается в следующем:
- применение накопленного материала на практике технологии и документации при организации капитального ремонта двигателей КамАЗ;
- детальное знакомство с проблемой уменьшения времени простоя автомобиля в ремонте;
- изучение технической документации капитального ремонта двигателей КамАЗ;
- приобретение практического опыта технологии капитального ремонта двигателей КамАЗ в соответствии с требованиями ФГОС по специальности 23.02.03. Техническое обслуживание и ремонт автомобильного транспорта.
|
- разработка проекта участок капитального ремонта двигателей грузовых автомобилей.
Дипломная работа структурно представлена введением, тремя частями, заключением, списком литературы и других информационных источников.
Во введении даётся обоснование актуальности работы, проблемы исследования, гипотезы, определены объект, предмет, цели и задачи исследования, методы исследования, теоретическая база исследования и база практики.
В первой части раскрываются: организация работы производственного участка ТО и ремонта двигателей, технология капитального ремонта двигателей КамАЗ, схема технологического процесса ремонта двигателей; расчеты годовой производственной программы работ по ТО и ТР; расчеты технологического процесса ТО и ТР автомобилей; проектирование участка капитального ремонта двигателей грузовых автомобилей с подбором необходимого оборудования.
Во второй части представлен: расчёт стоимости 1 нормо-часа производственных рабочих, расчет амортизационных отчислений.
В третьей части раскрываются вопросы техники безопасности при проведении ТО и ремонта на производстве, требования экологической безопасности при эксплуатации, ТО и ремонте автомобилей и пожарной безопасности.
В заключении содержатся краткие выводы по результатам исследования.
НКП и ИТ 23.02.03.11732
5
Изм.
Лист
№ докум.
Подп.
Дата
НКП и ИТ 23.02.03.11732
6
Изм.
Лист
№ докум.
Подп.
Дата
- замена трубок высокого давления;
- замена всех фильтрующих элементов;
- ремонт топливного насоса и форсунок.
Готовые двигатели обкатываются. После обкатки производится покраска, установка на поддон, обвязка.
Различают два метода сборки:
- поточный метод сборки. При движении по конвейеру на блок цилиндров устанавливают поочередно все детали и агрегаты, при этом каждый рабочий выполняет одно операцию.
- тупиковый метод сборки. Блок цилиндров устанавливают на стенд Р-770, после чего производится сборка. Сборку производит слесарь четвертого разряда. Трудоемкость сборки - 640 чел. мин
НКП и ИТ 23.02.03.11732
7
Изм.
Лист
№ докум.
Подп.
Дата
11. Смазать опорные шейки распределительного вала маслом М10Г2 и установить распределительный вал в сборе в блок цилиндров (емкость, кисть).
Установить на вал корпус подшипника, затянуть болты крепления с запорными шайбами корпуса подшипника распределительного вала и отогнуть усы запорных шайб на грани головок болтов. Болты крепления затянуть усилием 25 Н.м. (2,5 кгс.м.) (головка сменная 17 мм ключ с п.к. рукоятка динамометрическая модель 131М, зубило, молоток).
|
Подобрать вкладыши коренных подшипников коленчатого вала, проверить вкладыши, постели блока, крышки крепления, установить последовательно верхние вкладыши в постель блока цилиндров и нижние вкладыши коренных подшипников в крышки. При установке вкладышей необходимо совместить выточки во вкладыше с выточками в блоке цилиндров и крышках.
14. Смазать вкладыши коренных подшипников маслом М10Г2К (емкость, кисть).
15. Установить в блок цилиндров коленчатый вал в сборе (кран-балка, подвеска).
Установить верхние и нижние полукольца упорного подшипника коленчатого вала. Проверить осевой зазор в упорном подшипнике. Нижнее полукольцо устанавливают одновременно с крышкой заднего коренного подшипника.
Установить крышки коренных подшипников с вкладышами, совместив крышки с перегородками блока по порядковым номерам, выбитым на нижней поверхности крышек (отчет перегородок блока начинать вести спереди двигателя).
18. Завернуть и затянуть болты крепления крышек в два приёма: первый с величиной момента затяжки 96-120 Н.м (9,6-12,0 кгс.м), второй 210-235 Н.м(21-23 кгс.м). Болты заворачивают сначала со стороны правого ряда цилиндров, а затем со стороны левого ряда цилиндров. (Головка сменная 24 мм, удлинитель, ключ с присоединительным квадратом, ключ динамометрический ПИМ-1754)
Замерить осевой зазор коленчатого вала. Он должен быть в пределах 0,100-0,195 мм. При необходимости осевой зазор отрегулировать установки полуколец упорного подшипника другой толщины. (Набор щупов №2)
Установить, завернуть и затянуть стяжные болты с шайбами блока цилиндров. Болты затягивать с величиной момента затяжки 82-92 Н.м (8.2-9.2 кгс.м). (Головка сменная 19 мм, ключ с присоединительным квадратом, рукоять динамометрическая модель 131М).
НКП и ИТ 23.02.03.11732
8
Изм.
Лист
№ докум.
Подп.
Дата
Установить на ось, ведущую шестерню привода распределительного вала в сборе с промежуточной шестерней привода распределительного вала. Шестерню установить так, чтобы метки «0» на промежуточной шестерне привода распределительного вала и на распределение шестерне коленчатого вала совпала. Также должны совпасть риски на ведущей шестерне привода распределительного вала и на шестерне распределительного вала.
НКП и ИТ 23.02.03.11732
9
Изм.
Лист
№ докум.
Подп.
Дата
Дефектация, восстановление коленчатых валов и контроль их после восстановления осуществляются на основании технических условий. Технические условия на контроль, сортировку и восстановление коленчатого вала представлены в табл. 1, а противовесов — в табл. 2.
Таблица 1. Технические условия на контроль, сортировку и восстановление коленчатого вала
Номер позиции на рисунке | Возможные дефекты | Способ установления дефекта и средства контроля | Размер, мм | Рекомендации по устранению дефектов | |
по рабочему чертежу | допустимый без ремонта | ||||
— | Обломы и трещины | Дефектоскоп | Браковать | ||
1 | Изгиб вала | Стенд контроля прогиба | Биение средней коренной шейки не более 0,03 мм | Править при биении более 0,03 мм | |
2 | Увеличение длины шатунных шеек | Калибр 67,5 | 67+0,12 | 67,5 | Браковать при увеличении длины более 67,5 мм |
3 | Износ шатунных шеек dш | Скобы | — | — | Шлифовать шатунные шейки под ремонтный размер |
Уменьшение диаметров шеек меньше номинального | Скоба 79,98 | 30-0,013 | 79,98 | ||
4, (1, 5, 16, 17) | Износ коренных шеек dк | — | — | — | Шлифовать коренные шейки под ремонтный размер |
Уменьшение диаметров шеек меньше номинального | 94,98 | 95-0,015 | 94,98 | — |
НКП и ИТ 23.02.03.11732
10
Изм.
Лист
№ докум.
Подп.
Дата
Продолжение таблицы 1.
6 | Износ шейки под противовес передней шестерни привода масляного насоса | Скоба 125,07 | 125 | — | — | |||||
7 | Вмятины и забоины на направляющем штифте | Осмотр | — | — | Заменить штифт | |||||
Ослабление посадки направляющего штифта | Проверить посадку легкими ударами медного молотка | — | — | То же | ||||||
Износ отверстия под направляющий штифт | Пробка 11,99 | 12 | 11,99 | Обработать под ремонтный размер | ||||||
8 | Износ шпоночного паза под противовес и шестерню привода масляного насоса | Калибр 6,00 | 6 | 6,0 | Обработать под ремонтный размер 6 | |||||
9 | Нарушение взаимного углового расположения относительно 1-й шатунной шейки: | Приспособление для проверки углового расположения шатунных шеек | — | — | Браковать при угловом расположении более +25° | |||||
2-й шатунной шейки |
| 90° ± 10° | — | — | ||||||
3-й шатунной шейки |
| 180° ± 10° | — | — | ||||||
10 | Изменение радиуса кривошипа г | Приспособление для замера радиуса | 60^+0,05 | — | Браковать при радиусе меньше 60,2 мм | |||||
11 | Риски, задиры или износ шейки под манжету | Скоба 104,7 | 105^-0,14 | 125,07 | Шлифовать до устранения рисок и задиров | |||||
| — | 104,70 | ||||||||
12 | Износ шпоночного паза под противовес задний и шестерню распределительную | Калибр 8,00 | 8 | 8,00 | Обработать под ремонтный размер 8,5 | |||||
13 | Износ отверстия под подшипник первичного вала коробки передач | Пробка 52,01 | 52 | 52,01 | Поставить втулку | |||||
14 | Биение заднего торца коленчатого вала | Индикаторное приспособление | — | — | Шлифовать поверхность шейки 15 до устранения биения | |||||
15 | Увеличение длины задней коренной шейки, риски и задиры на упорной поверхности | Калибр 36,55 | 36,2^+0,05 | 36,55 | Отработать до выведения следов износа; при сборке ставить упорные кольца ремонтного размера | |||||
противовесов; изъятие заглушек и втулок центробежной очистки масла и внутренних полостей масляных каналов коленчатого вала. Правка коленчатого вала производится на
НКП и ИТ 23.02.03.11732
11
Изм.
Лист
№ докум.
Подп.
Дата
прессе при наличии изгиба вала более 0,05 мм. Для правки вал устанавливается на призмы крайними коренными шейками, средняя шейка устанавливается под штоком гидравлического пресса таким образом, чтобы прогиб вала находился в верхней части (под штоком пресса). Контроль осуществляется с помощью индикаторного приспособления. На среднюю шейку устанавливается призма со сферическим углублением для предохранения от повреждения шейки вала, и усилием пресса вал прогибается на величину, превышающую изгиб вала в 10 раз.
Таблица 2. Технические условия на контроль, сортировку и восстановление противовесов
номер позиции на рисунке | Возможные дефекты | Способ установления дефекта и средства контроля | Размер, мм | Рекомендации по устранению дефектов | |
по рабочему чертежу | допустимый без ремонта | ||||
— | Обломы или трещины | Магнитный дефектоскоп, осмотр | — | — | Браковать |
1 | Износ отверстия под шейку коленчатого вала | Пробка 125,03 | 125^0,01 | 125,03 | Осталивание |
2 | Износ шпоночного паза b | Калибр 6,0 | 6 | 6,10 | Заварить электродуговым способом; фрезеровать шпоночный паз |
Шейки коленчатого вала шлифуются на круглошлифовальных станках ЗА432. Режимы шлифовки коренных и шатунных шеек коленчатого вала приведены в табл. 3.
Порядок шлифования, следующий. В первую очередь шлифуются коренные шейки после установки коленчатого вала в центрах станка. Во вторую очередь шлифуются шатунные шейки.
Для шлифования шатунных шеек коленчатый вал на станке устанавливается в центросместителях, обеспечивающих смещение оси вала на величину радиуса кривошипа, который имеет размер (604+-0,5) мм, и совмещение осей шатунных шеек с осью шпинделя станка. Шлифование начинается с первой шатунной шейки, для шлифования следующей шейки вал поворачивается на угол 90°.
В процессе шлифования шеек производится контроль их размеров и радиуса кривошипа.
Все коренные и шатунные шейки шлифуются под один ремонтный размер.
После шлифования шейки подвергаются полировке в течение 1 мин на полировальных станках полировальной лентой ЭБ220 или пастой ГОИ № 10.
Восстановленные коленчатые валы поступают на сборку.
НКП и ИТ 23.02.03.11732
12
Изм.
Лист
№ докум.
Подп.
Дата
Шестерни привода масляного насоса из-за ненадежного его крепления могут иметь следующие дефекты: обрыв шестерни, накрен на зубьях, выкрашивание зубьев. Шестерни, имеющие указанные выше дефекты, заменяются новыми.
Противовесы подвергаются осмотру на магнитном дефектоскопе и контролю жестким мерительным инструментом.
Противовесы, имеющие обломы или трещины, выбраковываются; имеющие износ отверстий под шейки вала восстанавливаются осталиванием (железнением). Изношенные пазы под шпонку завариваются электродуговой сваркой и фрезеруются новые.
Таблица 3. Режимы шлифования коренных и шатунных шеек коленчатого вала.
Обрабатываемые шейки | Операция | Характеристика шлифовального круга | Размер круга |
Коренные | Предварительная | Э 5 40 Ст27К5 | ПП 900Х 350Х 63 |
Окончательная | Э 9А 25 Ст15К5 | ПП 900X350X63 | |
Шатунные | Предварительная | Э 5 40 Ст25К5 | ПП 900X305X36 |
Окончательная | Э 9А 25 Ст15К5 | ПП 900X305X36 |
Вкладыши подшипников коленчатого вала и нижней головки шатуна сменные, тонкостенные, трехслойные, с рабочим слоем из свинцовистой бронзы. Верхний и нижний вкладыши коренного подшипника коленчатого вала невзаимозаменяемые. В верхнем вкладыше имеются отверстие для подвода масла и канавка для его распределения.
Камское объединение выпускает десять ремонтных размеров вкладышей. Это позволяет восстанавливать шейки коленчатого вала шлифованием под ремонтный размер. Обозначение вкладышей соответствующей шейки, диаметр вала и диаметр постели в блоке цилиндров и шатуне нанесены на тыльной стороне вкладыша.
Размеры шатунных и коренных шеек коленчатого вала представлены в табл. 4 и 5
Размеры шеек коленчатого вала и гнезда в блоке цилиндров должны соответствовать ремонтным размерам вкладышей. Перед установкой коленчатого вала в блок цилиндров рабочая поверхность вкладышей коренных подшипников и коренные шейки коленчатого вала смазываются чистым дизельным маслом, упорные полукольца коленчатого вала устанавливаются в выточках задней коренной опоры так, чтобы стороны с канавками прилегали к упорным торцам вала. При правильной сборке подшипников вал должен свободно проворачиваться от усилия руки, а осевой зазор в упорном подшипнике должен быть 0,050—0,215 мм. Увеличение длины задней коренной шейки компенсируется подбором полуколец ремонтного размера.
НКП и ИТ 23.02.03.11732
13
Изм.
Лист
№ докум.
Подп.
Дата
Таблица 4. Ремонтные размеры шеек коленчатого вала и вкладышей двигателей КамАЗ-740
Шатунный подшипник | Коренной подшипник | ||||
Диаметр, мм | Маркировка вкладыша | Диаметр, мм | Маркировка вкладыша | ||
шейки коленчатого вала | постели шатуна | шейки коленчатого вала | постели блока | ||
79,50 | 85,0 | 740.1004058 | 94,5 | 100,0 | 740.1005170 |
Р1 79,50—85,0 | (1005171) | ||||
Р1 94,50—100,0 | |||||
79,00 | 85,0 | 740.1004058 | 94,0 | 100,0 | 740.1005170 |
Р2 79,00—85,00 | (1005171) | ||||
Р2 94,00—100,0 | |||||
80,00 | 85,5 | 740.1004058 | 95,0 | 100,5 | 740.1005170 |
Р3 80,00—35,00 | (1005171) | ||||
РЗ 95,00—100,5 | |||||
79,50 | 85,5 | 740.1004058 | 94,5 | 100,5 | 740.1005170 |
Р4 79,50—85,5 | (1005171) | ||||
Р4 94,50—100,5 | |||||
79,00 | 85,5 | 740.1004058 | 94,0 | 100,5 | 740.1005170 |
Р5 79,00—85,0 | (1005171) | ||||
Р5 94,00—100,5 | |||||
78,50 | 85,0 | 740.1004058 | 93,50 | 100,0 | 740.1005170 |
Р6 78,50—85,00 | (1005171) | ||||
Р6 93,50—100,0 | |||||
78,00 | 85,0 | 740.1004058 | 93,0 | 100,0 | 740.1005170 |
Р7 78,00—85,0 | (1005171) | ||||
Р7 93,00—100,0 |
Коленчатые валы двигателей КАМАЗ изготовлены из высококачественной легированной стали 42ХМФА ТУ 14-1-5520-2005 и имеют пять коренных и четыре шатунных шейки, связанные щеками и сопряженные переходными галтелями.
Для равномерного чередования рабочих ходов шатунные шейки коленчатого вала расположены под углом 90°. Упрочнение коленчатых валов производится с использованием следующих технологий:
НКП и ИТ 23.02.03.11732
14
Изм.
Лист
№ докум.
Подп.
Дата
Таблица 5. Ремонтные размеры шеек коленчатого вала и вкладышей двигателей КамАЗ-740
Шатунный подшипник | Коренной подшипник | ||||
Диаметр, мм | Маркировка вкладыша | Диаметр, мм | Маркировка вкладыша | ||
шейки коленчатого вала | постели шатуна | шейки коленчатого вала | постели блока | ||
79,95 | 85,0 | 740.1004058 Р1 79.95 | 94,95 | 100,0 | 740.1005170 Р1 94,95 |
740.1005171 Р1 94,95 | |||||
79,75 | 85,0 | 740.1004058 Р2 79,75 | 94,75 | 100,0 | 740.1005171 Р2 94,75 |
740.1005171 Р2 94,75 | |||||
79,50 | 85,0 | 740.1004058 РЗ 79,50 | 94,50 | 100,0 | 740.1005170 Р3 94,50 |
740.1005171 Р3 94,50 |
азотирование на глубину 0,25...0,3 мм, твердость упрочненного слоя не менее 600 HV;
закалка токами высокой частоты (ТВЧ) коренных и шатунных шеек, включая переходные галтели, на глубину 2,5...5,5 мм, твердость упрочненного слоя 52...62 HRC.
НКП и ИТ 23.02.03.11732
15
Изм.
Лист
№ докум.
Подп.
Дата
Рис. 2. Сборочный чертеж коленчатого вала 7408.1005008-10,
собранного на базе вала 740.13-1005020
Установить нижние и верхние полукольца упорного подшипника коленчатого вала в выточках на пятой опоре, таким образом, чтобы сторона с канавками прилегала к упорным торцам вала. После установки необходимо проверить наличие осевого зазора в упорном подшипнике.
6. Тщательно очистить и смазать моторным маслом резьбу в отверстиях блока и на болтах, избыток масла удалить.
8. Плотно и без перекосов установить крышки коренных опор по посадочным поверхностям. При установке крышек соблюдать совпадение порядкового номера крышки (выбитым на нижней поверхности) с порядковым номером опор по посадочным поверхностям. При установке крышек, соблюдать совпадение порядкового номера крышки (выбитым на нижней поверхности) с порядковым номером опор блока. Нумерация опор на блоке начинается от переднего торца блока (со стороны вентилятора).
Унифицированные размеры диаметров коренных и шатунных шеек коленчатых валов различного конструктивного исполнения, диаметры постелей в шатуне и блоке цилиндров позволяют применять вкладыши одного типоразмера при восстановлении двигателей ОАО «КАМАЗ» различной мощности и экологического класса. Особенности применения заключаются в технологии изготовления вкладышей, имеющейся в распоряжении различных производителей, в связи с чем, одновременная установка на двигатель вкладышей от различных производителей не рекомендуется, а для сопряженных вкладышей (устанавливаемых на одну шейку вала) недопустима.
НКП и ИТ 23.02.03.11732
16
Изм.
Лист
№ докум.
Подп.
Дата
Рис. 3. Сборка опорной шейки коленчатого вала
Ремонт коленчатых валов следует производить согласно ремонтной документации (ремонтных чертежей, карт дефектации, руководящих документов) разработанной НТЦ ОАО «КАМАЗ».
Основные моменты, касающиеся восстановления и ремонта коленчатых валов, на которые необходимо обратить внимание, следующие:
форма галтелей после перешлифовки шеек (переход от шейки вала к щеке выполненный в виде радиуса) должна быть плавной, кромки, подрезы, ступени и риски не допускаются;
ремонтопригодность шеек коленчатого вала определяется видом его упрочнения. Применяемость вкладышей, в зависимости от ремонтного размера шеек коленчатого вала. В комплекте с азотированным коленчатым валом с ремонтными размерами шеек (уменьшение диаметров на 0,25 мм) необходимо применять специальные вкладыши с увеличенной на 0,125 мм толщиной, освоенные на ОАО «ЗПС»;
при замене коленчатого вала с использованием противовесов, спрессованных с вала, вышедшего из строя, повторная балансировка не требуется, так как при изготовлении все детали двигателя (коленчатые валы, противовесы, маховики, шкивы) балансируются раздельно;
установка на двигатель противовесов и маховиков от двигателей других моделей не допускается;
правка коленчатого вала не допускается. Устранять прогиб коленчатого вала следует только перешлифовкой шеек в ремонтный размер;
сборку коленчатого вала с шестернями и противовесами по прессовой посадке следует
НКП и ИТ 23.02.03.11732
17
Изм.
|
|
Своеобразие русской архитектуры: Основной материал – дерево – быстрота постройки, но недолговечность и необходимость деления...
Наброски и зарисовки растений, плодов, цветов: Освоить конструктивное построение структуры дерева через зарисовки отдельных деревьев, группы деревьев...
Поперечные профили набережных и береговой полосы: На городских территориях берегоукрепление проектируют с учетом технических и экономических требований, но особое значение придают эстетическим...
Двойное оплодотворение у цветковых растений: Оплодотворение - это процесс слияния мужской и женской половых клеток с образованием зиготы...
© cyberpedia.su 2017-2024 - Не является автором материалов. Исключительное право сохранено за автором текста.
Если вы не хотите, чтобы данный материал был у нас на сайте, перейдите по ссылке: Нарушение авторских прав. Мы поможем в написании вашей работы!