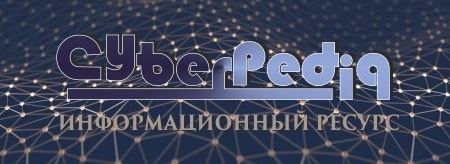
Особенности сооружения опор в сложных условиях: Сооружение ВЛ в районах с суровыми климатическими и тяжелыми геологическими условиями...
Состав сооружений: решетки и песколовки: Решетки – это первое устройство в схеме очистных сооружений. Они представляют...
Топ:
Оснащения врачебно-сестринской бригады.
Проблема типологии научных революций: Глобальные научные революции и типы научной рациональности...
Интересное:
Средства для ингаляционного наркоза: Наркоз наступает в результате вдыхания (ингаляции) средств, которое осуществляют или с помощью маски...
Распространение рака на другие отдаленные от желудка органы: Характерных симптомов рака желудка не существует. Выраженные симптомы появляются, когда опухоль...
Национальное богатство страны и его составляющие: для оценки элементов национального богатства используются...
Дисциплины:
![]() |
![]() |
5.00
из
|
Заказать работу |
|
|
Объекты производства
К объектам производства относятся:
- изделие;
- полуфабрикат;
- заготовка;
- исходная заготовка;
- основной материал (материал);
- вспомогательный материал;
- комплектующее изделие; - производственная партия;
- операционная партия; - сборочный комплект;
- задел;
- типовое изделие.
Дадим определения перечисленным объектам производства:
Изделием по ГОСТ 2.10*-68 ЕСКД называется любой предмет
или набор предметов производства, подлежащих изготовлению на предприятии. Изделия, в зависимости от их назначения, делят на из- делия основного и вспомогательного производства. К изделиям ос- новного производства следует относить изделия, предназначенные для поставки (реализации), а к изделиям вспомогательного производ- ства относят изделия, предназначенные только для собственных нужд предприятия, изготовляющего их. Причем, устанавливаются следую- щие виды изделий: а) детали; б) сборочные единицы; в) комплексы; г) комплекты.
Изделия, в зависимости от наличия или отсутствия в них состав- ных частей, делят на: а) неспецифицированные (детали) - не имею- щие составных частей; б) специфицированные (сборочные единицы, комплексы, комплекты) - состоящие из двух и более составных час- тей.
Причем, понятие «составная часть» следует применять только в отношении конкретного изделия, в состав которого она входит, а составной частью может быть любое изделие (деталь, сборочные еди- ницы комплекс, комплект).
Различают еще покупные изделия, к которым относятся изделия, не изготовляемые на данном предприятии, а получаемые им в гото- вом виде, кроме получаемых в порядке кооперирования.
Дадим определения составным частям изделия:
|
Деталь - изделие, изготовленное из однородного по наименова-
нию и марке материала, без применения сборочных операций. На- пример: болт, винт, литой корпус, пластина из биметаллического лис- та и т.д. или эти же изделия, подвергнутые покрытиям (защитным или декоративным) или изготовленные с применением местной пайки, сварки, сшивки и т.п., например: винт подвергнутый хромированию, трубка спаянная или сваренная из одного куска листового материала. Сборочная единица - изделие, составные части которого подле-
жат соединению между собой на предприятии изготовителе сбороч- ными операциями, например: автомобиль, редуктор, сварной корпус; электрооборудование станка, готовальня и т.д.
Комплекс - два и более специфицированных изделия, не соеди- ненных на предприятии изготовителе сборочными операциями, но предназначенных для выполнения взаимосвязанных эксплуатацион- ных функций, например: цех-автомат, автоматическая телефонная станция, корабль, большие краны и т.д. В комплекс кроме изделий, выполняющих основные функции, могут входить детали, сборочные единицы и комплекты, предназначенные для выполнения вспомога- тельных функций, например: детали и сборочные единицы, предна- значенные для монтажа комплекса на месте его эксплуатации, ком- плект запасных частей и т.д.
Комплект - два и более изделия, не соединенных на предпри- ятии изготовителе сборочными операциями и представляющих набор изделий, имеющих общее эксплуатационное назначение вспомога- тельного характера, например: комплекты запчастей, инструментов, упаковочной тары и т.п.
Виды изделий и их структура Следующим объектом производства является полуфабрикат (ГОСТ 3.1109-82) - предмет труда, подлежащий дальнейшей обра- ботке на предприятии-потребителе.
Заготовка - предмет труда, из которого изменением формы,
размеров, свойств поверхности и (или) материала изготавливают де- таль.
Исходная заготовка - заготовка перед первой технологической операцией.
|
Основной материал - это материал исходной заготовки.
Вспомогательный материал - материал, расходуемый при вы-
полнении технологического процесса дополнительно к основному ма- териалу, например, материал, расходуемый при нанесении покрытия, сварке, пайке, закалке и т.д.
Комплектующее изделие - изделие предприятия-поставщика, применяемое как составная часть изделия, выпускаемого предприяти- ем-изготовителем. Составными частями изделия могут быть детали и сборочные единицы.
Производственная партия - группа заготовок одного наимено- вания и типоразмера, запускаемых в обработку одновременно или не- прерывно в течение определенного интервала времени.
Операционная партия - производственная партия или ее часть, поступающая на рабочее место для выполнения технологической операции.
Сборочный комплект - группа составных частей изделия, кото- рые необходимо подать на рабочее место для сборки изделия или его составной части.
Задел - производственный запас заготовок или составных час- тей изделия для обеспечения бесперебойного выполнения технологи- ческого процесса.
Типовое изделие - изделие, принадлежащее к группе изделий близкой конструкции, обладающее наибольшим количеством конст- руктивных и технологических признаков этой группы.
Элементы технологических операций
Различают следующие элементы технологических операций:
Установ - часть технологической операции, выполняемая при
неизменном закреплении обрабатываемой заготовки или собираемой сборочной единицы.
Технологический переход (переход) - законченная часть технологи- ческой операции, характеризуемая постоянством применяемого инстру- мента и поверхностей, образуемых обработкой или соединяемых при сборке.
Вспомогательный переход - законченная часть технологической
операции, состоящая из действий человека и (или) оборудования, ко- торые не сопровождаются изменением формы, размеров и шероховато- сти поверхностей, но необходимы для выполнения технологического перехода (установка заготовки, смена инструмента и т.п.).
Рабочий ход - законченная часть технологического перехода, состоящая из однократного перемещения инструмента относительно заготовки, сопровождаемого изменением формы, размеров, шерохова- тости поверхности или свойств заготовки.
|
Вспомогательный ход - законченная часть технологического перехода, состоящая из однократного перемещения инструмента от- носительно заготовки, не сопровождаемого изменением формы, разме- ров, шероховатости поверхности или свойств заготовки, но необходи- мого для выполнения рабочего хода.
Позиция - фиксированное положение, занимаемое неизменно за- крепленной обрабатываемой заготовкой или собираемой сборочной единицей совместно с приспособлением относительно инструмента или неподвижной части оборудования для выполнения определенной части операции.
Ностроения
Основными направлениями развития технологии машинострое-
ния являются:
*) Создание новых методов обработки.
2) Совершенствование существующих методов обработки (по-
вышение уровня механизации и автоматизации производственных процессов, ускорение производственных процессов на основе внедре- ния поточного производства).
Первое направление включает создание и внедрение следующих
методов обработки:
- электромеханическая и электроэрозионная обработка,
- электрогидравлическая, электрохимическая, электроабразив-
ная и ультразвуковая обработка,
- обработка электронным лучом и плазменной струей, с при-
менением квантовых генераторов (лазеров),
- электро-ферромагнитная обработку и др.
Перечисленные методы обработки наряду с такими мероприя-
тиями как использование в качестве инструментов атомов воды и их частиц, а также естественных и искусственных алмазов, развитие об- работки давлением с высокими скоростями, индукционного метода прессования являются одним из основных направлений совершенст- вования технологии в машиностроении.
Второе направление включает:
1) унификацию машин и механизмов;
2) приближение формы заготовки к форме готового изделия;
*) специализацию и совершенствование металлорежущего обо-
рудования;
4) совершенствование обрабатывающего инструмента и повы-
шение съема металла при резании;
5) комплексную технологию в машиностроении;
6) механизацию, автоматизацию и создание автоматических ли-
ний и заводов;
7) использование вычислительной техники для решения техно- логических и организационных задач.
|
Хозяйственное значение
В природе существует ничтожно малое количество предметов,
которые может использовать человек непосредственно без преобразо- вания. Поэтому человеку приходиться приспосабливать предметы природы для удовлетворения своих потребностей.
Современный человек стремиться преобразования предметов природы выполнять с помощью машин.
Человеческое общество постоянно испытывает потребности в новых видах продукции, либо в сокращении затрат труда при изго- товлении освоенной продукции. Эти потребности могут быть удовле- творены с помощью новых технологических процессов и новых ма- шин. Таким образом, стимулом к созданию новой машины всегда яв- ляется новый технологический процесс.
Машина полезна лишь, если она обладает требуемым качеством
и, таким образом, способна удовлетворять потребность людей.
Ресурсы труда в жизни человеческого общества представляют собой наивысшую ценность.
Создавая машину, человек ставит перед собой две задачи:
1) создать машину качественной;
2) затратить меньшее количество труда при создании маши-
ны.
Замысел новой машины возникает при разработке технологиче- ского процесса изготовления продукции, в производстве которой воз- никла потребность. Этот замысел выражается в формулировке слу- жебного назначения, которая является исходным документом для проектируемой машины.
Процесс создания машины состоит из двух этапов:
1) проектирование;
2) изготовление.
В результате проектирования появляются чертежи машины. В результате изготовления с помощью производственного процесса по- является машина.
Второй этап и составляет основную задачу технологии машино- строения. Создание машины можно представить в виде схемы, предcтавленной на рис. 2.1. Изготовление машины связано с использованием различных способов обработки металлов.
- в то же время повышение уровня надежности машины, сокращает затраты на устранение отказов, технического обслуживания и ремонт.
Показатели качества отражают степень пригодности, полезности, те блага, которые извлекает человек, используя машину.
Экономичность - цена этих благ, их стоимость. Она зависит от технического совершенства конструкции машины и технологии ее из- готовления.
Стоимость машины зависит от качества, количества и стоимости материалов, выбранных конструктором в процессе проектирования. Конечные затраты на материалы, входящие в себестоимость, можно определить лишь после осуществления технологического процесса ее изготовления.
Уровень унификации и технологичности машины определяет конструктор. Влияние этих факторов на себестоимость машины про- является не прямым путем, а через технологию ее изготовления. Эти же факторы оказывают влияние на затраты по техническому обслу- живанию и ремонту.
|
Экономическими показателями являются потребление машиной энергии, потребление машиной топлива, потребление машиной мате- риалов в процессе эксплуатации.
Теория размерных цепей. Основные понятия и опреде-
Ления
Размерные цепи отражают объективные размерные связи в кон-
струкции машины, в технологических процессах изготовления ее де- талей и сборки, при измерении, возникающие в соответствии с усло- виями решаемых задач.
Размерная цепь - совокупность размеров, непосредственно уча- ствующих в решении поставленной задачи и образующих замкнутый контур. Обозначаются размерные цепи прописными буквами русско- го алфавита (А, Б, В, ¼, Я), если они образованы линейными разме-
рами, и строчными буквами греческого алфавита (b, g, ¼, кроме букв
a, d, x, l, w), если их составляют угловые размеры.
Размерные цепи, связывающие исполнительные поверхности
машины, называются сборочными размерными цепями. Размерные цепи, при помощи которых проводят измерения, - измерительными размерными цепями. Технологическая размерная цепь - это размерная цепь, связывающая межпереходные размеры поверхностей обрабаты- ваемой детали, так же как и размерные цепи станков, при помощи ко- торых они образованны.
Звено размерной цепи - это размер, определяющий относитель-
ное расстояние или поворот поверхностей детали или их осей. Исход- ное звено - это размер, с которого начинается построение размерной цепи. Замыкающим называют звено размерной цепи, получающееся последним в результате построения. Составляющие звенья - это зве- нья, изменение величины которых приводит к изменению исходного или замыкающего звена. Уменьшающее звено - это звено, с увеличе- нием которого уменьшается исходное или замыкающее звено. Увели- чивающим называют звено, с увеличением которого возрастает ис- ходное или замыкающие звено. Компенсирующие звено - это звено, изменением величины которого поглощается, против допустимой, ве- личина отклонения замыкающего звена. Плоская размерная цепь - это цепь, все звенья которой находятся в одной плоскости или нескольких параллельных плоскостях. Пространственной называют размерную цепь в том случае, если хотя бы одно, входящее в нее звено не удов- летворяет условиям, установленным для плоской размерной цепи.
10.Погрешность замыкающего звена размерной цепи
При определении погрешности замыкающего звена размерной
цепи следует различать два вида задач:
1) определение погрешности у одной детали или изделия;
*) определение погрешности у партии деталей или изделий.
При решении задач первого вида следует принимать во внима-
ние тот факт, что при выполнении любого технологического процесса происходит непрерывное изменение величин всех действующих фак- торов. Поэтому определение погрешности замыкающего звена раз- мерной цепи у одного экземпляра детали или изделия рассматривает- ся как изменение погрешности в выбранный момент времени. При этом считается, что величины всех составляющих звеньев размерной цепи в течение этого момента времени остаются постоянными. Прак- тически это условие реализуется тем, что измерение происходит в регламентированном месте и при строго регламентированных усло- виях. Поэтому погрешность замыкающего звена будет равна алгеб- раической сумме погрешностей составляющих звеньев размерной це- пи, т.е. с учетом их влияния на замыкающее звено в данный момент времени для данной детали или изделия.
При решении задач второго вида, а именно, определении по- грешности замыкающего звена размерной цепи при изготовлении партии деталей или сборке партии изделий правильнее и строже го- ворить не о погрешности, а о рассеивании размера замыкающего звена, т.к. приходится иметь дело с полями рассеивания всех состав-
ляющих звеньев. В этом случае погрешность замыкающего звена бу- дет равна арифметической сумме полей рассеивания всех состав- ляющих звеньев данной размерной цепи.
22-24Методы достижения точности замыкающего звена раз мерной цепи
Обеспечение точности создаваемой машины сводится к дости-
жению требуемой точности замыкающих звеньев размерных цепей, заложенных в ее конструкцию, и размерных цепей, возникающих в процессе изготовления машины. Задача обеспечения требуемой точ- ности замыкающего звена в зависимости от предъявляемых к нему требований, типа и условий производства может быть решена эконо- мично одним из пяти методов: полной, неполной, групповой взаимоза- меняемости, пригонки или регулирования.
Метод полной взаимозаменяемости предусматривает сборку машин без какой-либо дополнительной обработки деталей с установ- кой и заменой любой детали без пригонки. При сборке по этому ме- тоду требуется более высокая точность изготовления деталей, специ- альное оборудование и оснастка.
Простейшим примером использования данного метода является достижение требуемой точности зазора при соединении электроламп и патронов, в которые они ввертываются при эксплуатации.
Преимуществами метода полной взаимозаменяемости являют-
ся:
- наибольшая простота достижения требуемой точности замы- кающего звена, так как построение размерной цепи сводится к про-
стому соединению всех составляющих ее звеньев;
- простота нормирования процессов во времени;
- возможность широкого использования основных преимуществ
кооперирования различных цехов и отдельных заводов для изготов-
ления деталей или сборочных единиц машин;
- возможность выполнения технологических процессов сборки рабочими, не обладающими высокой квалификацией, поскольку про- цесс сводится к простому соединению деталей.
Решение о применении сборки с полной взаимозаменяемостью должно базироваться на анализе работы механизмов и на технико- экономических расчетах. При этом основными факторами, ограничи- вающими использование этого метода сборки, являются требования применения точных методов обработки большого количества деталей,
сложных и точных приспособлений и контрольно-измерительных
приборов, что нерентабельно при небольшом объеме производства. Использование метода полной взаимозаменяемости целесообразно в массовом и крупносерийном производствах, в этом случае капиталь- ные затраты на оснащение производства окупаются большим количе- ством изготовляемых машин.
Границы применения метода полной взаимозаменяемости опре- деляют экономикой производства. В этом легко убедится, если рас- смотреть график (рис.2.5.), показывающий зависимость величины возможного брака в партии деталей в зависимости от установленной величины допуска на один из размеров детали.
Рассматривая кривую 1, можно видеть, что по мере уменьшения величины допуска количество выходящих за пределы поля допуска деталей увеличивается. Вначале этот процесс идет медленно (участок а-б), затем темп роста брака увеличивается (участок б-в), наконец при малых величинах допусков брак возрастает настолько резко (участок в-г), что обработка деталей становится неэкономичной и возможно появление сплошного брака.
В таких случаях для достижения высокой точности необходимо перейти на новый технологический процесс (кривая 2), а следова- тельно, большей частью и на новый вид оборудования. Однако изме- нение технологического процесса и особенно переход на новый вид оборудования, дающего более высокую точность, обычно связаны с
увеличением затрат и, следовательно, себестоимости изготовления детали (изделия).
Относительная себестоимость возрастает с уменьшением допус- ка по гиперболической кривой, т.к. новое дополнительное оборудова- ние обычно более дорогое и зачастую менее производительное.
Использование метода полной взаимозаменяемости является экономичным в условиях достижения высокой точности при помощи малозвенных размерных цепей. При этом решающее значение имеет также и количество изделий, подлежащих изготовлению. С увеличе- нием количества изделий возрастают возможности экономичного ис- пользования более дорогого, но и более производительного и точного оборудования, инструмента и другой технологической оснастки. Если величина допуска в производственных условиях, соответствующих этапу развития техники, оказывается не экономичной, то от использо- вания метода полной взаимозаменяемости приходится отказываться и переходить на другие методы.
Сущность метода неполной (частичной) взаимозаменяемости заключается в том, что требуемая точность замыкающего звена раз- мерной цепи достигается с некоторым, заранее обусловленным рис- ком путем включения в нее составляющих звеньев без выбора, подбо- ра или изменения их значений.
Преднамеренный риск выхода значений замыкающего звена за пределы допуска, определяемого условиями задачи, обычно незначи- телен. Однако этот риск позволяет расширить допуски составляющих звеньев в сравнении с их значениями, установленными при достиже- нии точности замыкающего звена методом полной взаимозаменяемо- сти. Эта возможность создается малой вероятностью возникновения крайних отклонений составляющих звеньев и попаданий таких откло- нений в одно изделие. Таким образом, метод основан на учете веро- ятностей отклонений размеров, составляющих размерную цепь.
Отличие рассматриваемого метода от предыдущего заключается в установлении больших по величине допусков на составляющие зве- нья, что делает изготовление деталей более экономичным. При этом идут на риск получения небольшого процента случаев выхода по- грешности замыкающего эвена размерной цепи за пределы установ- ленного допуска. В основе рассматриваемого метода лежит одно из известных положений теории вероятностей, по которому возможные сочетания крайних значений погрешностей всех составляющих размерную цепь звеньев встречаются несравненно реже, чем средних
значений, вследствие чего возможный процент изделий, имеющих выход погрешностей замыкающего звена за пределы требуемого до- пуска, обычно крайне мал.
Дополнительные затраты труда и средств на исправление не- большого количества изделий, вышедших за пределы допуска, в по- давляющем большинстве случаев малы, по сравнению с экономией труда и средств, получаемой за счет изготовления составляющих звеньев с большими величинами допусков.
Преимущества данного метода по сравнению с предыдущим возрастают по мере повышения требований к точности замыкающего звена и увеличения количества звеньев в размерной цепи.
Сущность метода групповой взаимозаменяемости (селектив- ной сборки), заключается в том, что требуемая точность исходного (замыкающего) звена достигается путем включения в размерную цепь составляющих звеньев, принадлежащих к одной из групп, на которые они предварительно разбиты.
Добавочные расходы, связанные с необходимостью измерения всех деталей точным измерительным инструментом вручную или ав- томатически с *opтировкой, хранением и доставкой деталей отдель- ными группами на сборку, должны окупаться за счет экономии, полу- чаемой от обработки деталей по широким, экономически достижи- мым допускам.
Обычно данный метод используется для достижения более вы- сокой точности замыкающих звеньев малозвенных размерных цепей в шарикоподшипниковой промышленности, в соединениях поршней и пальцев авиационных и автомобильных двигателей и т.д.
Сущность метода пригонки заключается в том, что требуемая точность замыкающего звена достигается в результате изменения ве- личины одного из заранее намеченных составляющих звеньев (ком- пенсатора) путем снятия с него необходимого слоя металла.
При этом на все составляющие звенья размерной цепи устанав- ливаются экономичные в данных производственных условиях допус- ки, что и является основным преимуществом этого метода.
Существенным недостатком метода является необходимость до- полнительных работ, связанных с пригонкой компенсаторов по «мес- ту», причем в подавляющем большинстве случаев эти работы выпол- няются вручную и требуют высокой квалификации рабочего.
Данный метод применим при изготовлении единичных изделий,
у которых при большом количестве звеньев в размерных цепях требу- ется обеспечить высокую точность замыкающего звена.
Сущность метода регулировки заключается в том, что требуе- мая точность замыкающего звена достигается путем изменения вели- чины заранее забранного компенсирующего звена 6eз снятия с него слоя материала.
Метод регулировки может осуществляться двумя путями:
- изменением положения одной из деталей (метод подвижных
компенсаторов);
- введением в размерную цепь специальной детали требуемого размера (метод неподвижного компенсатора, в том числе и метод шайб).
Метод регулировки имеет следующие преимущества:
- возможность достижения любой степени требуемой точности
замыкающего звена при экономичных допусках на все составляющие
звенья;
- отсутствие пригоночных работ;
- возможность периодически, а в ряде случаев - непрерывно и
автоматически сохранять требуемую точность замыкающего звена.
Данный метод эффективен при решении задач достижения вы- сокой точности замыкающего звена в многозвенных размерных це- пях, а также в таких размерных цепях, где имеются звенья, изменяю- щиеся по величине вследствие износа, колебаний температуры и т.д.
Недостатком метода регулировки является увеличение в некото- рых случаях количества деталей в машине.
11.Расчет прямой и обратной задачи методом полной взаимозаме няемости
При решении размерной цепи приходится иметь дело с двумя
видами задач:
1) Прямая - когда при известных величинах допуска и коор-
динаты его середины для замыкающего звена размерной цепи требу- ется определить величины допусков и координат их середин всех со- ставляющих звеньев размерной цепи.
2) Обратная задача - когда при известных величинах допус-
ков и координат их середин всех составляющих звеньев размерной цепи требуется определить допуск и координату его середины для за- мыкающего звена.
Если обратная задача имеет математически однозначное реше-
ние, то прямая задача имеет математически неоднозначное решение, т.к. уравнений для расчета, всегда меньше, чем неизвестных величин. Поэтому решение прямой задачи может быть однозначным только при совместном решении уравнения с другими техноэкономическими закономерностями.
Рассмотрим методики решения этих двух задач.
Обратная задача. Для ее решения Ивановым В.В. предложена
следующая методика. Построив схему размерной цепи, подсчитывают допуск замыкающего звена, для чего допуски увеличивающих и уменьшающих звеньев сводят в расчетную таблицу (+,-) руководству- ясь следующими правилами записи: для увеличивающих звеньев верхняя граница допуска записывается в колонку «+», а нижняя - в колонку «-», а для уменьшающих звеньев наоборот - нижняя граница допуска - в колонку «+», а верхняя - в колонку «-».
Причем, если при занесении в таблицу (+,-) значения верхних и нижних границ допусков увеличивающих звеньев берутся с теми же знаками, что и на чертеже, то для уменьшающих звеньев знак меняет- ся на обратный.
Затем производится алгебраическое суммирование величин по колонкам и в результате получаем для замыкающего звена верхнюю границу допуска (в колонке +) и нижнюю (в колонке -), причем уже со знаком границ допусков.
то есть, получен тот же результат, что и методом Иванова.
При решении прямой задачи, когда по замыкающему звену оп- ределяются составляющие звенья, на практике используются три спо-
соба распределения допусков:
1) Равномерное распределение допуска Т ∆ между составляю-
щими звеньями - способ равных допусков или принцип равных влия- ний, т.е. полагается, что все звенья в равной степени влияют на обра- зование погрешности замыкающего звена, и, следовательно, величи- ны их допусков могут быть равны. При этом условии средняя величи-
на допуска Тср определяется из формулы
Т ср Т ∆
* -1
где m - количество звеньев в размерной цепи.
Если эта средняя величина допуска оказывается экономически приемлемой в производственных условиях, то ее корректируют, учи- тывая трудности и экономику получения требуемой точности для ка- ждого из составляющих звеньев размерной цепи.
2) Способ назначения допусков на составляющие звенья, соот- ветствующие одному и тому же квалитету точности обработки - способ равной точности, т.е. в его основу положен принцип одинаковой
сложности изготовления всех размеров звеньев.
Сложность изготовления звеньев зависит от их номинальных размеров. Так при механической обработке проще получить размер
40-0,** , чем размер 400-0,05. Это видно из таблиц допусков. Поэтому в
основу построения таблиц допусков и посадок положена единица до-
пусков (ЕД), которая выражается следующей формулой
ЕД 0,53 d
где d - средний размер в мм той группы размеров, в которую входит
данный номинальный размер.
4.Основные положения по получению и выбору заготовок
Выбор заготовки тесно связан с последующей ее обработкой.
Поэтому в современном производстве одним из основных направле- ний развития технологии механообработки является использование заготовок с экономичными конструктивными формами, обеспечи- вающими возможность применения наиболее рациональных и эконо- мичных способов их обработки на металлорежущих станках. Это на- правление особенно важно для условий поточного и автоматизиро- ванного производства.
В практике возможны следующие варианты выбора заготовок:
1) когда при проектировании детали конструктор указывает
только марку материала и, если нужно, то термообработку и твер-
дость. В этом случае технолог сам выбирает вид заготовки;
2) когда заготовка имеет довольно сложную конструкцию (на- пример: корпус коробки передач, коленчатый вал и др.). В этом слу- чае конструктор согласовывает вид заготовки с технологами загото- вительных и механических цехов.
Изводстве заготовок
Основными видами заготовок в зависимости от назначения и
марки материала деталей является:
*) отливки из черных и цветных металлов;
2) кованые и штампованные заготовки;
3) заготовки из проката;
4) заготовки, полученные комбинированным способом (ли-
тейно-сварные и штампосварные);
5) заготовки из металлокерамики (порошковая металлургия);
6) пластмассовые заготовки.
Основные тенденции в производстве заготовок:
а) Для производства корпусных деталей (блоки и головки ци-
линдров, корпусы коробок скоростей, насосов, редукторов; передние и задние бабки, фартуки станков и др.) в настоящее время все чаще стали применять вместо чугуна алюминий. Этому способствует появление высокопроизводительных машин для отливки заготовок под
давлением, а также резкий рост выработки алюминия и снижение его стоимости. При этом сокращается вес заготовок и деталей, увеличи- вается точность отливок и сокращается общая трудоемкость изготов- ления деталей.
Для изготовления заготовок корпусных деталей, к которым предъявляются требования высокой прочности, все чаще применяют литье в оболочковые формы.
б) Для производства стальных деталей средних размеров (зубча- тые колеса, валы, рычаги, шатуны и др.) вместо горячей штамповки на штамповочных молотах заготовки получают штамповкой на вер- тикальных штамповочных прессах. Это обеспечивает большую про- изводительность в 1,5¼2 раза и снижение веса заготовки на 15% за счет меньших припусков и приближения конфигурации заготовки к конфигурации готовой детали. Эта тенденция особенно заметна в массовом производстве, но эффективна и при серийном производстве.
В мелкосерийном и серийном производствах имеется тенденция к переходу от ковки к штамповке на ковочных молотах в подкладных штампах, к ковке на штамповочных молотах и на прессах. Многие коленчатые и распределительные валы, шпиндели станков вместо штамповки из стали изготовляют отливкой из высокопрочного чугу- на. Все большее количество малонагруженных деталей средних и мелких размеров изготавливают из пластмасс.
в) Мелкие стальные детали, как и прежде, обрабатываются на револьверных станках и автоматах из горячекатаной или калиброван- ной прутковой стали, т.е. проката.
При выборе заготовок должен учитываться следующий ком-
плекс факторов:
1) назначение детали (материал и технические условия) для чего изучается работа детали в машине, устанавливаются требования по
прочности, и выясняется точность ее изготовления;
*) объем и серийность выпуска детали, которые влияют на эко-
номичность выбора заготовки;
3) тип и конструкция детали;
4) размеры деталей и имеющееся на заводе оборудование для
получения заготовок и их обработки;
5) экономичность изготовления заготовки, т.е. зачастую необхо- димо провести технико-экономическое сравнение двух и более вари- антов получения заготовок.
5.Припуски на обработку: основные понятия и опреде ления
Путем механической обработки заготовки за ряд переходов и
операций достигается требуемая геометрическая форма, размеры и качество поверхностей детали, заданные рабочим чертежом. При этом на каждом переходе с обрабатываемой поверхности снимается слой металла, в результате чего изменяется размер заготовки. Слой мате- риала, необходимый для выполнения технологического перехода, т.е. снимаемый за один переход называется промежуточным припуском. Слой материала, снимаемый с обрабатываемой поверхности за одну операцию, называется операционным припуском. Слой материала, снимаемый с обрабатываемой поверхности заготовки, в процессе всей ее механической обработки, называется припуском на обработку. Припуск измеряется в направлении перпендикулярном к обрабаты- ваемой поверхности. Для тел вращения он задается на диаметр, а для плоскостей (линейных размеров) он может задаваться на сторону, но с обязательной оговоркой этого. Неоправданно большие припуски ве- дут к перерасходу материала, что вызывает необходимость введения дополнительных переходов. Увеличивается трудоемкость процесса обработки, затраты энергии, инструмента, себестоимость детали и снижается производительность труда. В некоторых случаях, увели- ченные припуски приводят к удалению при обработке с рабочих по- верхностей наиболее износостойкого слоя металла. Следовательно, необходимо назначать меньшие значения припусков. Однако недоста- точные припуски не обеспечивают возможность удаления дефектных поверхностных слоев металла и получение требуемой точности и ше- роховатости обработанных поверхностей, а в ряде случаев, создают неприемлемые технические требования для работы режущего инст- румента. Поэтому в результате недостаточных припусков возрастает брак, что приводит к повышению себестоимости продукции. Большое значение имеет правильный выбор величины припуска и правильное назначение допуска на него, т.к. слишком узкие допуски приводят к удорожанию заготовок, а слишком широкие - снижают точность об- работки заготовок в приспособлениях на настроенных станках, ус- ложняя настройку и наладку станков. Поэтому установление опти- мальных величин припусков на обработку и технологических допус- ков на размер заготовки по всем переходам и операциям является од- ной из основных технологических задач.
Аналитическим методом
В связи с тем, что расчетно-аналитический метод находит наи-
большее применение в серийном и массовом производстве, где работа ведется в основном на настроенных станках, поэтому рассмотрим бо- лее подробно порядок расчета припусков на обработку и предельных размеров заготовки по технологическим переходам для случая одно- проходной обработки.
Расчет выполняется в следующей последовательности:
1) для обрабатываемой заготовки намечаются установочные ба-
зы и технологический маршрут обработки;
2) записываются в расчетную карту (табл. 3.1) обрабатываемые элементарные поверхности и последовательный порядок технологи-
ческих переходов обработки по ка<
|
|
Поперечные профили набережных и береговой полосы: На городских территориях берегоукрепление проектируют с учетом технических и экономических требований, но особое значение придают эстетическим...
Механическое удерживание земляных масс: Механическое удерживание земляных масс на склоне обеспечивают контрфорсными сооружениями различных конструкций...
Особенности сооружения опор в сложных условиях: Сооружение ВЛ в районах с суровыми климатическими и тяжелыми геологическими условиями...
Организация стока поверхностных вод: Наибольшее количество влаги на земном шаре испаряется с поверхности морей и океанов (88‰)...
© cyberpedia.su 2017-2024 - Не является автором материалов. Исключительное право сохранено за автором текста.
Если вы не хотите, чтобы данный материал был у нас на сайте, перейдите по ссылке: Нарушение авторских прав. Мы поможем в написании вашей работы!