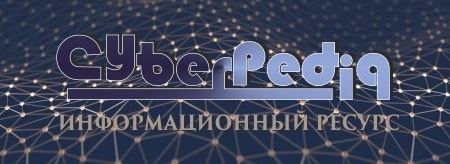
Механическое удерживание земляных масс: Механическое удерживание земляных масс на склоне обеспечивают контрфорсными сооружениями различных конструкций...
Двойное оплодотворение у цветковых растений: Оплодотворение - это процесс слияния мужской и женской половых клеток с образованием зиготы...
Топ:
Устройство и оснащение процедурного кабинета: Решающая роль в обеспечении правильного лечения пациентов отводится процедурной медсестре...
Основы обеспечения единства измерений: Обеспечение единства измерений - деятельность метрологических служб, направленная на достижение...
Методика измерений сопротивления растеканию тока анодного заземления: Анодный заземлитель (анод) – проводник, погруженный в электролитическую среду (грунт, раствор электролита) и подключенный к положительному...
Интересное:
Принципы управления денежными потоками: одним из методов контроля за состоянием денежной наличности является...
Распространение рака на другие отдаленные от желудка органы: Характерных симптомов рака желудка не существует. Выраженные симптомы появляются, когда опухоль...
Средства для ингаляционного наркоза: Наркоз наступает в результате вдыхания (ингаляции) средств, которое осуществляют или с помощью маски...
Дисциплины:
![]() |
![]() |
5.00
из
|
Заказать работу |
|
|
Соединения перлитных сталей с высокохромистыми мартенситно-ферритными сталями. Для сварки перлитных сталей с высокохромистыми сталями на базе 12 % хрома не существует единого мнения о преимуществе использования того или иного легирования металла шва. Отмечается возможность применения как мартенситных, так и высокохромистых сварочных материалов. Отдельные исследователи рекомендуют использовать для этой цели электроды с 5 % хрома.
Применение для рассматриваемых сварных соединений перлитных и высокохромистых сварочных материалов приводит в обоих случаях по условию перемешивания к получению в переходных слоях структур мартенситного класса. При использовании перлитных сварочных материалов переходные составы шва могут содержать до 4 - 5 % хрома; в случае применения высокохромистых сварочных материалов содержание хрома в переходных составах будет меняться в пределах 7 - 11 %.
Для определения свойств металла швов переходных составов в зависимости от содержания в них хрома были изготовлены электроды, обеспечивающие переменное содержание хрома в наплавке от 1 до 11 % за счет введения его через покрытие. Образцы, вырезанные из швов такого переменного состава, были испытаны на растяжение и ударный изгиб при комнатной температуре. С повышением содержания хрома прочность шва в исходном состоянии после сварки возрастает, достигая при 10 % хрома 1100 МПа для предела текучести и 1300 МПа - для предела прочности.
После отпуска изменение содержания хрома меньше сказывается на уровне прочности шва. Минимальная пластичность металла шва в исходном состоянии после сварки соответствует содержанию в нем 8,5 % хрома. При этом количестве хрома наблюдается и минимальная ударная вязкость металла шва, подвергнутого отпуску. Исходя из полученных результатов, можно рекомендовать для сварки перлитных сталей с 12 % -ными хромистыми сварочные материалы, близкие к менее легированному основному металлу (табл. 25.).
|
Если комбинированные стыки данного сочетания сталей используются в крупногабаритных конструкциях повышенной надежности и выполняются методом электрошлаковой сварки, то необходимо принимать меры к обеспечению повышенного запаса вязкости металла шва в целях устранения опасности образования трещин.
По условию снижения до минимума диффузионных прослоек перлитный наплавленный металл должен легироваться определенным количеством карбидообразующих элементов. Так, при сварке углеродистых или низколегированных сталей с 12 % -ными хромистыми сталями следует применять электроды типа Э - ХМ или соответствующую проволоку при механизированных способах сварки. При больших калибрах швов в этом случае указанными сварочными материалами можно производить лишь облицовку кромок со стороны высоколегированной стали, а заварку шва выполнять электродами типа Э - 42А или Э - 50А в зависимости от требований к прочности перлитной стали.
В связи со значительной разницей содержания энергичных карбидообразующих элементов в основном металле рассматриваемых сварных соединений предельная температура их эксплуатации должна быть снижена против рекомендуемой для перлитной стали. Значения этих температур может быть повышены введением переходников из стали промежуточного легирования или облицовок из перлитной стабилизированной стали. Так, сварные соединения низкоуглеродистой стали с 12 % -ной хромистой сталью могут длительно работать при Т = 450 0С если ввести:
1. переходник (при сварке труб) из хромомолибденовой стали марки 15ХМ (20ХМ); сварку патрубка с трубой из высокохромистой стали следует выполнять электродами типа Э-ХМФ, а с трубой из углеродистой стали - типа Э-42А.
|
2. облицовку кромок 12 % -ной хромистой стали электродами типа Э-ХМФ и затем сварка электродами типа Э-42А с последующим отпуском при Т =700-720 0С.
В сварных соединениях перлитных сталей с 12 % -ной хромистой корневые слои в связи с обогащением их хромом имеют повышенную твердость. Проведение отпуска выравнивает ее по сечению многослойного шва, однако, и в этом состоянии твердость корневых слоев на 10 - 15 HV превышает значения для верхних слоев шва. Исходя из неизбежности значительной подкалки корневых слоев шва и ОШЗ 12 % -ной хромистой стали режим подогрева при сварке таких комбинированных узлов следует выбирать по высоколегированной составляющей.
Выбор режима термообработки также должен производиться в соответствии с требованиями к сварным соединениям 12 % -ной хромистой стали. Если имеется опасность развития диффузионных прослоек, то температура отпуска должна быть снижена. При изготовлении крупногабаритных сварных конструкций из этих сталей можно в отдельных случаях рекомендовать замену отпуска нормализацией. Так как перлитная и высокохромистая стали имеют разные коэффициенты линейного расширения, то остаточные сварочные напряжения термообработкой не снимаются. В связи с этим необходимо учитывать возможные деформации конструкции после отпуска. В комбинированных сварных конструкциях из перлитной стали с высокохромистой влияние остаточных сварочных напряжений на прочность может не учитываться.
При сварке перлитных сталей с высокохромистыми ферритно-аустенитными сталями (с содержанием 17 - 28 % Cr) применение сварочных материалов перлитного класса нежелательно вследствие чрезмерного легирования переходных участков хромом и опасности образования трещин. Наиболее целесообразно в данном случае использование сварочных материалов аустенитно-ферритного класса. Может быть допущено также применение аустенитных электродов, однако при этом необходимо учитывать структурную неоднородность соединения и значительную разницу термического расширения шва и основного металла.
Соединения перлитных и мартенситных сталей с аустенитными и ферритно-аустенитными. Из наиболее широко распространенных в промышленности аустенитных сварочных материалов основное применение для сварки мартенситных сталей с аустенитными сталями нашли электроды типов ЭА-2, ЭА-2Г6 и ЭА-1М2Ф и соответствующие им по легированию проволоки композиций Х25Н13, Х20Н10Г6 и 04Х19Н11М3 (табл. 26). Эти сварочные материалы следует использовать в комбинированных сварных конструкциях, высоколегированная составляющая которых выполнена из наиболее распространенной аустенитной стали с указанным содержанием никеля.
|
Таблица 25
Рекомендации по выбору сварочных материалов для соединений из разнородных сталей перлитного класса с высокохромистыми
Предельная температура, 0С | Марки свариваемых сталей | Метод сварки | Сварочные материалы | Отпуск при температуре, 0С | ||
300- 350 | Низкоуглеродистые (20, 30, Ст3) и низколегированные конструкционные |
12 % -ные хромистые 08Х13, 12Х13, 20Х13, 15Х11В2МФ | Ручная дуговая Покрытыми Электродами | Электроды типа Э-ХМ |
650- 680 | |
Под флюсом | Проволока Св-10ХМ | |||||
в СО2 | Св-08ХГСМА | |||||
400-450 | Хромомолибденовые 15ХМ, 12МХ, 30ХМ | Ручная дуговая Покрытыми Электродами | Электроды типа Э-ХМФ | |||
Под флюсом | Св-08ХМФА, |
650 -700
| ||||
в СО2 | Св-08ХГСМФА | |||||
500-520 | Хромомолибденованадиевые 12Х1МФ, 15Х1М1Ф | Ручная дуговая Покрытыми Электродами | Электроды типа Э-ХМФ |
| ||
в СО2 | Св-08ХГСМФА | |||||
580 | Хромомолибденованадиевые Х5М, Х5МФ | 12 % -ные хромистые 08Х13 и др., | Ручная дуговая Покрытыми Электродами | Электроды типа Э-Х5М | 700- 750 | |
300-350 | Низкоуглеродистые (20, 30, Ст3) и низколегированные конструкционные | Высокохромистые Х17Т, 15Х25Т, Х28АН, Х25Н5ТМФ | Ручная дуговая Покрытыми Электродами | Электроды типов: ЭАФ-1МФ, ЭА-2 | Без отпуска или отпуск 700-750 |
Подобными сварочными материалами производится обычно сварка сталей мартенситного класса (35ХН3М, Х5МФ, 2Х13), а также полуферритного и ферритного классов (0Х13, Х17Н2, Х25Т). Используемые в зарубежной практике для подобного назначения электроды композиции Х25Н20 не обеспечивают устойчивых результатов по стабильности свойств металла шва в связи со склонностью отдельных плавок сварочной проволоки такого состава к горячим трещинам при сварке. Можно полагать, что переход к более технологичному наплавленному металлу Х25Н17Г7 позволит заметно улучшить свойства металла швов в комбинированных соединениях. Допустимая степень проплавления перлитной стали при использовании электродов такого легирования может быть повышена на 40 - 50%.
|
При выборе сварочных материалов необходимо учитывать также проплавление основного металла и со стороны аустенитной стали. По этому условию сварочные материалы аустенитно-ферритного класса могут применяться лишь в сварных соединениях перлитных сталей с аустенитными сталями 1-ой группы, у которых содержание хрома превышает содержание никеля или близко к нему. При сварке глубокоаустенитных сталей с перлитными должны использоваться лишь сварочные материалы, обеспечивающие однофазную аустенитную или аустенитно-карбидную структуру металла шва стойкого против трещин в условиях возможного перемешивания с аустенитной и перлитной сталями.
Если в качестве высоколегированного основного металла применяются ферритно-аустенитные стали марок Х25Н5ТМФ, Х21Н5Т и им подобные, сварку комбинированных узлов также желательно выполнять электродами с повышенным запасом аустенитности типа ЭА-3М6. Ферритно-аустенитные сварочные материалы могут допускаться в данном случае, если режимы сварки и разделки кромок обеспечивают проплавление со стороны основного металла не более 20%. Для ручной дуговой сварки крупногабаритных конструкций из стали 10Х18Н3Ф2Л со сталью 20ГСЛ рекомендуется применение аустенитно-ферритных электродов марки ЦЛ-33.
При изготовлении жестких узлов с большой толщиной деталей в процессе отпуска или эксплуатации конструкции возможны хрупкие разрушения в зоне сплавления перлитной стали с аустенитным швом. Опасность этих разрушений можно исключить при использовании сварочных материалов с повышенным содержанием никеля. К их числу относятся электроды ЭА-3М6 и ЭА-4В3Б2 и соответствующие им по легированию проволоки марок Х15Н25М6 и 2Х15Н35В3Б2. Возможность появления трещин в зоне сплавления при сварке жестких узлов резко уменьшается также при введении облицовки свариваемых кромок аустенитными электродами с повышенным содержанием никеля, а также при использовании разделок с развитой границей сплавления.
Исходя из выше изложенного, при выборе сварочных материалов и назначении технологии сварки целесообразно разделить комбинированные сварные конструкции по степени их жесткости. Можно считать, что при
Таблица 26
Рекомендации по выбору сварочных материалов для разнородных сварных соединений перлитных и мартенситных сталей с аустенитными и ферритно-аустенитными
Предельная температура, 0С | Марки свариваемых сталей
| Метод сварки | Сварочные материалы | |||
350 | Низкоуглеродистые и низколегированные конструкционные |
Аустенитные I группы: 12Х18Н9Т, 12Х18Н12Т, 12Х18Н12Б, 10Х17Н13М2Т, Х16Н13М2Б, 20Х23Н18, Х25Н13Т, Х17Н15В2Б | Ручная дуговая Покрытыми Электродами | Электроды типов: ЭА-2, ЭА-1М2Ф, ЭА-2Г6, ЭА-3МФ, ЭА-4В3Б2 | ||
400 | Хромомолибденовые 15ХМ, 12МХ, 30ХМ |
Под флюсом и аргонодуговая |
Проволока Св-07Х25Н13, Св-Х20Н9Г7Т, Св-07Х25Н12Г2Т, Св-06Х25Н12ТЮ, Св-06Х20Н11М3ТБ | |||
520 | Хромомолибденованадиевые 12Х1МФ, 15Х1М1Ф | |||||
580 | Хромомолибденованадиевые Х5М, Х5МФ | |||||
Предельные температуры и марки сталей те же, что и для соединений с аустенитными сталями I группы | Аустенитные II группы: Х14Н18В2БР, Х15Н35В3Т, Х16Н25М6 | Ручная дуговая Покрытыми Электродами | Электроды типов: ЭА-3М6, ЭА-3М9, ЭА-4ВЗБ2 | |||
350 | Низкоуглеродистые и низколегированные конструкционные | Ферритно-аустенитные | Ручная дуговая Покрытыми Электродами | Электроды типов: ЭА-3М6, ЭАФ-1МФ |
толщине свариваемых элементов до 20 мм узел обладает относительно небольшой жесткостью, а при большей толщине соединяемых деталей - повышенной жесткостью. Такое деление является, естественно, условным и может использоваться лишь для предварительного выбора сварочных материалов и технологии сварки. При изготовлении узлов сравнительно небольшой жесткости без дополнительных ограничений по технологии сварки могут применяться следующие сварочные материалы (табл. 26).
Температура подогрева при сварке может быть на 150-200 0С ниже обычно требуемой в однородных узлах из перлитной и мартенситной стали, свариваемых электродами близкими по составу к основному металлу. Эта рекомендация режима подогрева сохраняется и при сварке аустенитными электродами закаливающихся сталей мартенситного класса.
Если сваривается узел повышенной жесткости, то во избежание появления трещин в зоне сплавления перлитной и мартенситной стали с аустенитным швом следует вводить предварительную облицовку ее кромок. Целесообразность этой операции тем больше, чем более высокопрочная и закаливающаяся сталь применяется в данном узле. При выполнении основного соединительного шва электродами типа ЭА-3М6 и ЭА-4В3Б2 облицовку следует выполнять этими электродами. Часто, однако, предпочитают вести сварку основного шва наиболее технологичными аустенитно-ферритными электродными материалами (ЭА-2, ЭА-2Г6, ЭА-1М2Ф). В этих случаях для повышения прочности зоны сплавления следует 1-й слой облицовки выполнять электродами ЭА-3М6, а последующие слои – соответственно электродами, применяемыми для заполнения основного шва. Общую толщину облицовочного слоя, как и при использовании электродов одного легирования, следует выполнять около 9 мм.
Общие положения по технологии сварки двухслойных сталей
Основной принцип, которым руководствуются в данном случае, т.е. выполнение швов основного и облицовочного слоев сварочными материалами близкого с ним состава, обеспечивают минимальную неоднородность сварных соединений двухслойных сталей и облегчают выбор режима их термообработки.
Типовая технология ручной дуговой и автоматической сварки под флюсом предусматривает вначале заполнение разделки основного слоя низкоуглеродистыми или низколегированными перлитными сварочными материалами. Далее, заваривается разделка со стороны облицовки в два слоя аустенитными сварочными материалами. При этом слой 2, при заполнении которого проплавляется как нержавеющий, так и основной низколегированный слой, обычно заваривается электродами типа ЭА-2. Соответственно для верхнего слоя 3, к которому предъявляются требования по МКК, используются сварочные материалы, близкие по составу к облицовочному слою.
При отсутствии доступа к облицовочному слою (сварные трубы малого диаметра) 1-й слой выполняется аргонодуговой сваркой вольфрамовым электродом. Последние слои завариваются электродами типа ЭА-2.
Основного принципа сварки двухслойных сталей следует придерживаться и при изготовлении более сложных конструкционных узлов. Так при вварке штуцера из двухслойной стали в корпус сосуда вначале заполняется разделка с наружной стороны электродами перлитного класса, а затем - с внутренней стороны по облицовочному слою уже аустенитными электродами. Если штуцер изготовлен целиком из аустенитной стали, то вся разделка заваривается электродами типа ЭА-2.
Выбор материала конструкции и условий ее работы должен также производится с учетом снижения до минимума диффузионных прослоек в зоне сплавления аустенитного шва с перлитной сталью. Это требование является наиболее актуальным для узлов, работающих при высоких температурах и в коррозионных средах, а также крупногабаритных изделий, подвергающихся отпуску после сварки. В ряде случаев предельная температура эксплуатации должна быть ниже допускаемой для перлитной стали. Для повышения предельной температуры эксплуатации следует использовать мероприятия, рекомендуемые для сварных соединений перлитных сталей с высокохромистыми сталями. Марки сталей для переходников и типы электродов для защитных оболочек могут быть приняты теми же.
Последовательность выполнения облицовочных работ в этих случаях следующая. Вначале на кромку основного перлитного металла производится наплавка в три слоя перлитного облицовочного слоя на высоту 6 мм, а затем облицовочного слоя высотой 9 мм аустенитными электродами. Заметное подавление процесса миграции углерода в зоне сплавления может быть достигнуто переходом к швам на никелевой основе. Сварочные материалы подобного легирования заслуживают предпочтения также и в связи с близостью коэффициента линейного расширения шва к перлитной стали, что уменьшает дополнительные напряжения в зоне сплавления.
Литература
1. Акулов А.И., Бельчук Г.А., Демянцевич В.П. Технология и оборудование сварки плавлением. - М.: Машиностроение, 1977. - 432 с.
2. Арикава Масаясу, Канаино Мотоки, Ватанабэ Тосихико. Япон. пат., кл. 12В1 (В23К 35/368), № 51-30020, заявл. 29.03.71. № 46-18642. опубл. 28.08.76.
3. Гривняк И. Свариваемость сталей.-М.: Машиностроение, 1984.-216 с.
4. Егорова С.В.. Стеренбоген Ю.А., Юрчишин А.В. и др. Возможность и перспективы использования межкритической нормализации для упрочнения низколегированных сталей и сварных конструкций.//Автоматическая сварка. 1983. № 12, С. 7 – 13.
5. Икэда Мицухико, Иосиити Дзюндзи, Япон. пат., кл. 12 В 1 (В23К 25/00), № 51-26384. заявл. 6.10.73. № 4-112670, опубл. 6.08.76.
6. Исидэаки Кэйдзо. Япон. пат.. кл. 12В11 (В23К 25/00). № 50-20023, заявл. 12.05.64, опубл. 11.07.75.
7. Касаткин Б.С., Мусияченко В.Ф. Низколегированные стали высокой прочности для сварных конструкций. - Киев.: Техника, 1970. - 188 с.
8. Кузмак Е.М., Кошелев Н.Н., Ю Хакимов А.Н. и др. Авт. свид. СССР. кл. В23К 25/00. № 554974.заявл. 14.01.75. № 2089804. опубл. 26.05.77.
9. Макаров Э.Л. Холодные трещины при сварке легированных сталей. - М.: Машиностроение, 1981. - 248 с.
10. Макара А.М., Мосендз Н.А. Сварка высокопрочных сталей.- Киев.: Техника. 1971, - 140 с.
11. Никифоров Г.Д., Бобров Р.В., Никитин В.М, Дьяченко В.В. Технология и оборудование сварки плавлением. М.: Машиностроение, 1978.- 327 с.
12. Технология электрической сварки металлов и сплавов плавлением / Под ред. Б.Е. Патона. - М.: Машиностроение, 1974. - 768 с.
13.Сварка в машиностроении: Справочник в 4-х т. / Под ред. Г.А. Николаева и др. М.: Машиностроение, 1978.-Т.2. 462 с.
14. Шварцер А.Я, Авт. свид. СССР. кл. В23К 25/00, В23р 3/10, № 460146. заявл. 16.03.73, опубл. 15.05.75.
Размещено на Allbest.ru
|
|
Биохимия спиртового брожения: Основу технологии получения пива составляет спиртовое брожение, - при котором сахар превращается...
Опора деревянной одностоечной и способы укрепление угловых опор: Опоры ВЛ - конструкции, предназначенные для поддерживания проводов на необходимой высоте над землей, водой...
Механическое удерживание земляных масс: Механическое удерживание земляных масс на склоне обеспечивают контрфорсными сооружениями различных конструкций...
Адаптации растений и животных к жизни в горах: Большое значение для жизни организмов в горах имеют степень расчленения, крутизна и экспозиционные различия склонов...
© cyberpedia.su 2017-2024 - Не является автором материалов. Исключительное право сохранено за автором текста.
Если вы не хотите, чтобы данный материал был у нас на сайте, перейдите по ссылке: Нарушение авторских прав. Мы поможем в написании вашей работы!