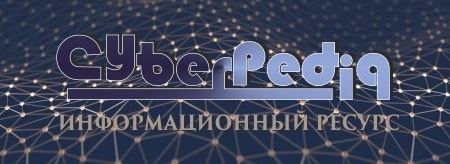
История создания датчика движения: Первый прибор для обнаружения движения был изобретен немецким физиком Генрихом Герцем...
Поперечные профили набережных и береговой полосы: На городских территориях берегоукрепление проектируют с учетом технических и экономических требований, но особое значение придают эстетическим...
Топ:
Отражение на счетах бухгалтерского учета процесса приобретения: Процесс заготовления представляет систему экономических событий, включающих приобретение организацией у поставщиков сырья...
Особенности труда и отдыха в условиях низких температур: К работам при низких температурах на открытом воздухе и в не отапливаемых помещениях допускаются лица не моложе 18 лет, прошедшие...
Интересное:
Что нужно делать при лейкемии: Прежде всего, необходимо выяснить, не страдаете ли вы каким-либо душевным недугом...
Национальное богатство страны и его составляющие: для оценки элементов национального богатства используются...
Мероприятия для защиты от морозного пучения грунтов: Инженерная защита от морозного (криогенного) пучения грунтов необходима для легких малоэтажных зданий и других сооружений...
Дисциплины:
![]() |
![]() |
5.00
из
|
Заказать работу |
|
|
Высокохромистые стали широко применяется в промышленности, и свойства их носят самый разнообразный характер. Поэтому сначала рассмотрим влияние хрома на структуру и свойства хромистых сталей и их классификацию.
Хром (Cr) является основным ферритообразующим элементом. Он упрочняет α – решетку, т.е.решетку кубическую объемно-центрированную. Диаграмма состояния Fe – Cr выглядит следующим образом (рис. 19), т.е. при содержании Cr >12 % имеем уже однофазную структуру, закалка которой уже не возможна, при любой скорости охлаждения. Но эта диаграмма двойная, т.е. диаграмма системы Fe – Cr. В сталях же всегда присутствует некоторое количество углерода, являющегося сильным аустенитизатором. Поэтому при введении в систему Fe – Cr углерода область γ - Fe резко сдвигается вправо (рис. 20).
Рис. 19. Структурная диаграмма системы Fe – Cr
Т, 0С
Рис. 20. Смещение петли γ-растворов в системе Fe – Cr – С в зависимости от содержания хрома и углерода
В связи с этим в зависимости от количества хрома в таких сталях они могут быть весьма чувствительными к закалке при быстром охлаждении, склонны к частичной закалке или являться не закаливающими. Все хромистые стали подразделяются еще на 3 подгруппы по структуре:
1. Высокохромистые (12-13% хрома) мартенситные стали 2Х13, 13Х11Н2ВМФ и др. имеют повышенное содержание углерода, некоторые из них дополнительно легированы никелем. Углерод, никель и др. аустенитообразующие элементы расширяют область g - растворов и способствуют практически полному мартенситному превращению в процессе охлаждения. Применение для закаленной стали отжига при температуре ниже точки АС3 способствует отпуску структур закалки и возможности получения весьма благоприятного сочетания механических свойств – одновременно высоких значений прочности, пластичности и ударной вязкости. Ферритообразующие элементы (Mo, V, Nb, W) вводят для повышения жаропрочности сталей. Если обычные 12 %-ные хромистые стали имеют достаточно высокие механические свойства при температурах до 500 0С, то сложнолегированные на этой основе стали обладают высокими характеристиками до 650 0С и используются для изготовления рабочих и направляющих лопаток, дисков паровых турбин и газотурбинных установок различного назначения.
|
2. Высокохромистые мартенситно – ферритные стали марок 08Х13, 12Х13, 20Х13, 08Х14МФ, 15Х11МФ и др. несмотря на отрицательное влияние d - феррита на пластичность и ударную вязкость находят довольно широкое применение для изготовления химических аппаратов и энергетического оборудования. Сварные детали из стали 08Х13 применяют в основном для изготовления внутренних устройств химических аппаратов и энергетического оборудования, не подлежащих контролю надзорных органов за безопасной эксплуатацией. Сталь 08Х14МФ применяется на предприятиях энергетического машиностроения, в основном в виде труб для изготовления теплообменного оборудования, работающего при температурах до 350 0С. Стали 12Х13 и 20Х13 с повышенным содержанием углерода используются для изготовления деталей различных турбин и насосов с температурой эксплуатации до 500 0С. Сталь марки 14Х17Н2 со значительно большим содержанием хрома, но имеющая мартенситно-ферритную структуру благодаря дополнительному легированию никелем, отличается высокой коррозионной стойкостью, не склонна к межкристаллитной коррозии (МКК) и применяется для внутренних устройств оборудования АЭС.
3. Высокохромистые ферритные стали, содержащие >16% хрома и имеющие структуру феррита (15Х25Т, 15Х28, 08Х17Т и др.) являются перспективными конструкционными материалами. По сопротивляемости коррозии ферритные стали не уступают хромоникелевым аустенитным сталям, значительно превосходят их по стойкости к коррозионному растрескиванию. При дополнительном легировании алюминием и кремнием хромистые ферритные стали 08Х23С2Ю (сихромаль 12) и ЭП904-ВИ могут быть использованы для изготовления оборудования, работающего при температурах до 1200 0С. Широкое применение ферритных сталей позволило бы решить проблему дефицита никеля путем замены ими распространенных в настоящее время аустенитных сталей.
|
Одним из важнейших технологических свойств для высоколегированных сталей является их свариваемость. Хромоникелевые стали при соблюдении соответствующей технологии свариваются без ограничения всеми видами сварки и имеют хорошие свойства сварных соединений в широком диапазоне температур. Высокохромистые стали обладают ограниченной свариваемостью [1-9]. Характерной трудностью при сварке высокохромистых сталей мартенситного и мартенситно - ферритного класса является склонность к образованию холодных трещин. В соответствии с этим технология их сварки базируется на предотвращении холодных трещин: подогрев (общий или местный) перед сваркой; термообработка после сварки; рациональный термический цикл; применение аустенитных и аустенитно-ферритных электродов, когда невозможна термообработка.
Основной проблемой при сварке сталей ферритного класса является охрупчивание сварных соединений, вызванное следующими явлениями:
1. В участке перегрева зоны термического влияния имеет место необратимый рост зерна и связанное с ним резкое падение пластических свойств, особенно ударной вязкости;
2. Охрупчивание, обусловленное дисперсионным упрочнением карбонитридами или s -фазой, а также диффузионным распылением твердого раствора. Резкое охрупчивание при сварочном нагреве сталей ферритного класса с повышенным содержанием углерода и азота обусловлено, прежде всего, выделениями на матрице и границе зерен большого количества дисперсных карбонитридов.
Охрупчивание хромистых ферритных сталей возможно не только при высокотемпературном нагреве, но и в интервалах 550 - 850 и 400-550 0С, способствующих образованию s -фазы и явлению 475 - градусной хрупкости. Охрупчивание, развивающееся в хромистых ферритных сталях в процессе охлаждения от 550 0С или выдержки вблизи 475 0С, относят к одной из разновидностей процесса дисперсионного твердения путем образования когерентно связанных с матрицей комплексов, обогащенных хромом. У сталей ферритного класса возможно проявление и обратимой хрупкости, развивающейся в процессе охлаждения. В интервале 550-850 0С возможно образование карбонитридов. Охрупчивание хромистых ферритных сталей при нагреве в районе 475 0С проявляется в две стадии. Первая стадия процесса охрупчивания, характерная при коротких выдержках, например, для термического цикла сварки, может быть связана с выделением дисперсных карбонитридов. Наряду с влиянием карбонитридов охрупчивание хромистых сталей возможно и в результате собственного явления хрупкости при 475 0С. Однако это явление не характерно для сварочного нагрева, так как начинает проявляться при значительно больших выдержках при эксплуатации.
|
3. Появление хрупкости при снижении температуры ниже Ткр является характерным свойством металлов и сплавов с ОЦК - решеткой. Атомы с ОЦК-решеткой, в отличие от ГЦК-металлов, имеют большой дефицит электронов в подооболочке d, что обуславливает наличие в решетке двух компонентов связи: металлической (взаимодействие коллективизированных электронов с периодическим полем решетки) и гомеполярной (валентные связи в результате спинового расщепления, перекрывание и обменное взаимодействие внешних оболочек ионов).
При легировании железа (3s2p6d64s2) хромом (3s2p6d54s1) наблюдают повышение склонности к хрупкому разрушению, очевидно вследствие возрастания дефицита электронов и количества гомеполярных связей. Молибден, вольфрам, титан, цирконий, ванадий, отличающиеся большим дефицитом электронов в подоболочке d, также отрицательно влияют на вязкость ферритных сталей.
Легирующие металлы с ОЦК - решеткой VI группы периодической системы Д.И. Менделеева: хром, молибден, вольфрам обладают ничтожной растворимостью примесей внедрения (@10-4 %), резко охрупчивающих эти металлы. Поэтому легирование ими сталей в значительных количествах сообщает указанное свойство (чувствительность к примесям внедрения) легируемому металлу. Кроме отмеченных трудностей, все высокохромистые стали склонны к межкристаллической коррозии при нагревах > 950 0С. Высокие технологические свойства и свариваемость хромистых ферритных связей могут быть достигнуты следующими мерами: 1) снижением содержания углерода и азота (в сумме) в основном металле £ 0,04%, в сварочных материалах £ 0,015%; 2) применением технологии сварки, обеспечивающей уменьшение перегрева и роста зерна, в том числе за счет уменьшения погонной энергии; 3) применением подогрева до температур выше температур перехода металла в хрупкое состояние. Такой предварительный подогрев позволяет уменьшить градиент температур отдельных участков, уменьшает влияние остаточных сварочных напряжений.
|
Разработан ряд марок сталей с пониженным содержанием углерода и азота, обладающих высокими технологическими свойствами (01Х25Б, 01Х18Н142Б, 01Х18ЮЗБ).
Изучено влияние термических циклов сварки ферритных сталей, содержащих 15, 20 и 30 % Сг, на критическую температуру хрупкости металла околошовной зоны. Стали, выплавленные вакуумно-индукционным способом и имеющие низкое содержание углерода и азота, могут использоваться для сварных соединений: их критическая температура лежит ниже комнатной.
Сварка высокохромистых мартенситных сталей. Для сварки этих сталей применяются как ферритные хромистые электроды, обеспечивающие в наплавленном металле содержание хрома на уровне основного металла (ЭФ –Х13), так и аустенитные электроды. Так как стали этого типа склонны к резкой закалке в ОШЗ, то сварка их производится с обязательным предварительным подогревом, величина которого рассчитывается по обычной методике. При этом ориентируются на вторую критическую скорость охлаждения V кр2, т.е. идут на частичную закалку. Температуру подогрева повышают с увеличением склонности к закалке (в основном с увеличением содержания углерода в стали) и жесткости изделия. При V охл << V кр1 очень сильно растет зерно в ОШЗ. Поэтому после сварки необходимо провести термообработку для восстановления свойств частично закаленной ОШЗ. Практически величина предварительного подогрева составляет 300-400 0С. После сварки обязательно охлаждение изделия на спокойном воздухе до Т = 120 - 100 0С (так называемое “подстуживание”). Затем осуществляется термообработка по режиму:
- Нагрев в печи до 720-750 0С.
- Выдержка при этой температуре ~5 минут на каждый миллиметр толщины изделия (но не менее 1 час).
- Охлаждение вместе с печью до ~600 0С.
- Охлаждение на спокойном воздухе.
Подстуживание необходимо для прохождения мартенситного превращения с последующим отпуском до получения сорбита. Если же сразу термообрабатывать с температуры предварительного подогрева – шов будет иметь грубую ферритно – карбидную структуру.
|
Такие же результаты могут быть получены, если при температуре 120-100 0С дать металлу в районе сварных соединений «отдых» (изотермическую выдержку) в течение ³ 10 ч. Тогда изделие может быть охлаждено далее до комнатной температуры и вылеживаться до термообработки в течение достаточно длительного времени. Трещин после такого отдыха не наблюдается, а структура и свойства после термообработки – отпуска получаются оптимальными.
С помощью такой сложной технологии получаем равнопрочное сварное соединение и обеспечиваем жаропрочность.
Когда не требуется полная равноценность свойств, а необходимо, например, сохранить коррозионную стойкость, то можно упростить технологию сварки этих сталей путем применения аустенитных хромоникелевых электродов. В этом случае сварку также производят с предварительным подогревом до тех же температур, но последующая термообработка уже не производится, т.к. это может привести к потере коррозионной стойкости металла шва.
Сварка высокохромистых мартенситно – ферритных сталей Так как эти стали также склонны к закалке в ОШЗ, то они тоже свариваются с предварительным подогревом, но уже порядка 200-300 0С. Остальные операции после сварки аналогичны операциям при сварке высокохромистых мартенситных сталей:
- подстуживание 120-100 0С;
- нагрев в печи 750-780 0С;
- выдержка при этой температуре ~5 минут на каждый миллиметр толщины изделия (но не менее 1 час);
- охлаждение на спокойном воздухе.
При этом используют электроды, обеспечивающие легирование, соответствующее основному металлу, например типа ЭФ-Х17. Применение аустенитных хромоникелевых электродов не целесообразно в связи с тем, что они не обеспечивают равноценной коррозионной стойкости и вызывают возникновение электрохимической коррозии на границе «шов – основной металл» при контакте с кислотосодержащими средами.
Сварка высокохромистых ферритных сталей. Как правило, такие стали содержат не менее 25 % Cr (15Х25Т, Х28) и обладают однофазной ферритной структурой, не имеют структурных превращений в твердом состоянии и при сварке не закаливаются. Эти стали жаростойкие, т.е. они обладают окалиностойкостью - минимальным окислением при высоких температурах. На свариваемость этих сталей оказывают влияние следующие ее свойства.
1. Стали этого типа обладают очень малой пластичностью в холодном состоянии.
2. Эти стали весьма склонны к росту зерна при высокотемпературной обработке, в том числе и в результате сварочного нагрева в ЗТВ и металле швов (при их составе, аналогичном ферритным сталям). При крупном зерне такие стали теряют пластичность и вязкость при комнатных и более низких температурах.
Поэтому эти стали свариваются с обязательным подогревом, но величина его относительно не велика - 200-250 0С. Этим самым уменьшается локальность нагрева, увеличивается пластичность (из-за увеличения Т), запаса которой должно хватить при остывании. В тоже время предварительный подогрев может вызвать нежелательный рост зерна. Но все же сварку ведут с подогревом, но “похолоднее” (меньше q п), короткими участками, с большими перерывами, тонкими электродами на малых токах. Наиболее распространены ручная дуговая сварка покрытыми электродами и механизированная в защитном газе. Для малых толщин иногда применяют аргонодуговую сварку неплавящимся электродом.
Для сварки используются электроды типа ЭФ-Х25 и др., а также сварочные материалы, позволяющие получить металл шва, по составу подобный основному. Для увеличения степени пластичности металла шва при сохранении окалиностойкости применяют аустенитные сварочные материалы. В этом случае шов имеет аустенитно – ферритную структуру, иногда с большим содержанием ферритной составляющей.
После сварки производят термообработку при 700-800 0С для снятия остаточных сварочных напряжений и некоторого повышения пластичности.
Если по условиям эксплуатации не требуется обеспечение высокой окалиностойкости и пластичности, применяют низконикелевые электроды типа ЭФ-Х17АН3.
Мы рассмотрели много марок сталей – одни из них свариваются с подогревом, другие без. Чтобы привести это в систему, можно использовать простое правило:
1. Если сталь закаливающаяся, то ее сваривают с подогревом;
2. Если сталь не закаливающаяся, то, как правило, без подогрева.
Из этого правила есть два исключения:
- Среднелегированные броневые стали – закаливающиеся - однако свариваются без подогрева (он все равно бесполезен).
- Высоколегированные хромистые ферритные – не закаливающиеся – однако свариваются с предварительным подогревом для увеличения запаса пластичности.
|
|
Общие условия выбора системы дренажа: Система дренажа выбирается в зависимости от характера защищаемого...
Семя – орган полового размножения и расселения растений: наружи у семян имеется плотный покров – кожура...
Археология об основании Рима: Новые раскопки проясняют и такой острый дискуссионный вопрос, как дата самого возникновения Рима...
Типы сооружений для обработки осадков: Септиками называются сооружения, в которых одновременно происходят осветление сточной жидкости...
© cyberpedia.su 2017-2024 - Не является автором материалов. Исключительное право сохранено за автором текста.
Если вы не хотите, чтобы данный материал был у нас на сайте, перейдите по ссылке: Нарушение авторских прав. Мы поможем в написании вашей работы!