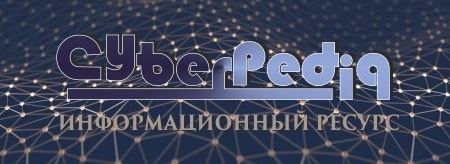
Семя – орган полового размножения и расселения растений: наружи у семян имеется плотный покров – кожура...
Типы оградительных сооружений в морском порту: По расположению оградительных сооружений в плане различают волноломы, обе оконечности...
Топ:
Техника безопасности при работе на пароконвектомате: К обслуживанию пароконвектомата допускаются лица, прошедшие технический минимум по эксплуатации оборудования...
Определение места расположения распределительного центра: Фирма реализует продукцию на рынках сбыта и имеет постоянных поставщиков в разных регионах. Увеличение объема продаж...
Методика измерений сопротивления растеканию тока анодного заземления: Анодный заземлитель (анод) – проводник, погруженный в электролитическую среду (грунт, раствор электролита) и подключенный к положительному...
Интересное:
Отражение на счетах бухгалтерского учета процесса приобретения: Процесс заготовления представляет систему экономических событий, включающих приобретение организацией у поставщиков сырья...
Искусственное повышение поверхности территории: Варианты искусственного повышения поверхности территории необходимо выбирать на основе анализа следующих характеристик защищаемой территории...
Распространение рака на другие отдаленные от желудка органы: Характерных симптомов рака желудка не существует. Выраженные симптомы появляются, когда опухоль...
Дисциплины:
![]() |
![]() |
5.00
из
|
Заказать работу |
|
|
Выделяют четыре базовые модели:
1. Модель с запасами на входе и выходе. Для нее характерно следующее:
• Это самая распространенная модель.
• Поставки товарно-материальных ценностей для организации запаса на входе должны быть гарантированы.
• Модель может использоваться только при устойчивом спросе на определенный ассортимент продукции.
• Такая организация работы позволяет достичь максимальной эффективности операционной деятельности в связи с тем, что запас обеспечивает бесперебойное снабжение потребности.
2.Модель с запасами на выходе. Для нее характерно следующее:
• Операционная деятельность в модели с запасом на выходе предприятия находится в критической зависимости от надежности поставщика товарно-материальных ценностей на входе организации.
• Фактически запас со входа предприятия передается поставщику, который несет и затраты, связанные с созданием и поддержанием запаса на выходе своего предприятия.
• Модель работы с запасами на выходе экономически эффективна при переработке скоропортящихся материалов.
3. Модель с запасами на входе. Для нее характерно следующее:
• Модель с запасом на входе предприятия можно применять экономически эффективно только при определенной ситуации покупатель готов ждать поставки товара.
• Модель с запасом на входе используют в позаказном производстве, где отсутствие запаса на входе не является признаком точно-срочных отношений.
4. Модель без запасов. Для нее характерно следующее:
• Модель работы без запаса является реализацией философии точно в срок в полном объеме в отличие от предыдущих двух моделей.
• При традиционной организации бизнеса модель работы без запасов можно эффективно использовать в позаказном производстве, если не требуется запас на входе предприятия, а также в посылочной торговле и электронной коммерции.
|
37. Системы планирования и организации деятельности по управлению запасами
1.Система пополнения запасов минимаксная система контроля.
Ее отличие состоит в том, что здесь вместо переменного размера заказа используют определенный заданный размер заказапоставки. При этом система ограничивает нижний предел переменного размера заказа. В результате уровень запасов поддерживается в интервале между верхним и нижним пределами. Верхний предел устанавливает максимальный уровень запасов, а нижний гарантирует, что размер заказа будет не меньше, чем разность.
В системе в качестве базовых единиц измерения можно использовать запас продукции в натуральном выражении штуки, единицы, срок снабжения в днях либо комбинацию
этих единиц измерения.
2. Система расшивки узких мест
Эта система может быть достигнуто путем акцентирования внимания лишь на очень немногих аспектах ее функционирования, а именно — на ограничениях, мешающих получению и увеличению прибыли. Любое предприятие рассматривается как система, состоящая из ресурсов, причем эти ресурсы связаны между собой процессами, в которых они участвуют. Все эти ресурсы работают на достижение цели организации. Любая организация может рассматриваться как цепь или несколько последовательных, параллельных цепей. Большинство организаций имеют ограниченные ресурсы и в то же время множество задач, которые должны быть выполнены. Если в силу неправильного акцентирования внимания ограничение не расшивается, то вряд ли можно рассчитывать на реальный успех в продвижении по направлению к цели. Более того, все действия, не направленные на расшивку узких мест, не добавляют стоимости, а лишь увеличивают затраты.
3. Толкающая система
Представляет собой систему организации производства, в которой предметы труда, поступающие на производственный участок, непосредственно этим участком у предыдущего технологического звена не заказываются. Материальный поток выталкивается получателю по команде, поступающей на передающее звено из центральной системы управления производством. Эта система, способна с помощью микроэлектроники увязать сложный производственный механизм в единое целое.
|
4. Тянущая система
Представляет собой систему организации производства, в которой детали и полуфабрикаты подаются на последующую технологическую операцию с предыдущей по мере необходимости.
Здесь центральная система управления не вмешивается в обмен материальными потоками между различными участками предприятия, не устанавливает для них текущих производственных заданий. Производственная программа отдельного технологического звена определяется размером заказа последующего звена. Центральная система управления ставит задачу лишь перед конечным звеном производственной технологической цепи.
АВС — классификация
АВС — анализ является одним из методов рационализации, который может использоваться во всех функциональных сферах деятельности предприятия.
При дифференцированном подходе к организации закупок и управлению складскими запасами ABC-анализ позволяет добиться существенного снижения затрат.
В зависимости от затрат материальные запасы подразделяются на три класса: А, В и С. Материальные запасы распределяются на отдельные классы по их удельному весу в общих издержках на материалы. Полученная кривая распределения названа кривая Лоренца.
ABC — анализ показывает значение каждой группы материалов и помогает обратить внимание на основные.
Материалы класса А — это немногочисленные, но важнейшие материалы, на которые приходится большая часть денежных средств около 75%, вложенных в запасы.
Материалы класса В относятся к второстепенным и требуют меньшего внимания, чем материалы класса А. С приобретением материалов класса В связано примерно 20% денежных средств.
Материалы класса С составляют значительную часть в номенклатуре используемых материалов, но недороги, на них приходится наименьшая часть вложений в запасы — 5%.
Для проведения ABC-анализа необходимо:
1. Установить стоимость каждого наименования материала для покупных деталей принимаются цены поставщика;
|
2. Расположить материалы по мере убывания издержек;
3. Суммировать данные о количестве и издержках на материалы и нанести их на схему;
4. Разбить материалы на группы в зависимости от их удельного веса в общих издержках.
Контроль и регулирование запасов осуществляются в зависимости от класса материала.
Материалы класса А. Тщательно определяются размеры и моменты выдачи заказов. Устанавливается строгий контроль и регулирование запасов.
Материалы класса В. Определяются экономичные размеры и момент выдачи повторного заказа. Осуществляется контроль и сбор информации о запасах.
Материалы класса С. Никаких расчетов не производится. Размер повторного заказа устанавливается так, чтобы поставки осуществлять в течение 1-2 лет. Пополнение запасов регистрируется, но текущий учет уровня запасов не ведется. Проверка наличных запасов проводится периодически один раз в год.
Управление группами XYZ
XYZ — анализ материалов предполагает оценку их значимости в зависимости от частоты потребления. В их числе есть материалы, имеющие постоянный и стабильный спрос; материалы, расход которых подвержен определенным, например сезонным, колебаниям, и, наконец, материалы, расход которых носит случайный характер. Поэтому в пределах каждого из классов А, В и С материалы могут быть распределены еще и по степени прогнозируемости их расхода. Для такой классификации используются символы X, Y, Z.
К классу X относятся материалы, спрос на которые имеет постоянный характер или подвержен случайным незначительным колебаниям, поэтому поддается прогнозированию с высокой точностью. Удельный вес таких материалов в общей номенклатуре, как правило, не превышает 50-55%.
К классу У относятся материалы, потребление которых осуществляется периодически либо имеет характер падающей или восходящей тенденции. Их прогнозирование возможно со средней степенью точности. Их удельный вес в общей номенклатуре составляет около 30%.
К классу Z относятся материалы, для которых нельзя выявить какой-либо закономерности потребления. По этой причине прогнозирование их расхода невозможно они составляют 15% общей номенклатуры.
|
Для проведения XYZ-анализа необходимо:
1. Установить средний расход каждого вида материала с учетом колебания потребности в них по периодам, это могут быть, например, сезонные колебания;
2. Рассчитать коэффициент вариации по каждой номенклатурной позиции;
3. Расположить материалы по мере убывания коэффициентов вариации;
4. Суммировать данные о количестве материалов в соответствии с возрастанием коэффициентов вариации, нанести их на схему;
5. Разбить материалы на группы в зависимости от вариации спроса.
Результатом XYZ-анализа является построение кривой Лоренца.
XYZ-анализ служит вспомогательным средством при подготовке решений по совершенствованию планирования материального обеспечения производства.
Если такой анализ проводится самостоятельно, то для материалов класса X можно рекомендовать закупки в соответствии с плановой потребностью синхронному их расходу в производстве, для класса Y — создание запасов, а для класса Z — приобретение по мере возникновения потребности.
№ 40, методы DRP планирование ресурсов сети распределения
DRP — планирование ресурсов дистрибуции — это система управления, обеспечивающая автоматизацию управления распределением запасов в сети.
Общие сведения.
DRP-система представляют собой график расписание, который координирует весь процесс поставки и пополнение запасов в дистрибьютивной сети. Для этого формируются расписания для каждого звена сети, связанного с формированием запасов, которые затем интегрируются в общее требование для пополнения запасов на складах предприятия или оптовых посредников.
Функционирование DRP-систем базируется на потребительском спросе, который не может контролироваться предприятием, поэтому неопределенная внешняя среда накладывает дополнительные требования и ограничения в политике управления запасами, DRP-системы планируют и регулируют уровни запасов на базах и складах предприятия в собственной товаропроводящей сети сбыта или у оптовых торговых посредников.
Цели внедрения.
улучшить уровень сервиса за счет уменьшения времени доставки запасов и удовлетворения ожиданий потребителей
улучшить продвижение новых товаров на рынок
сократить общий объем запасов в сети
сократить уровня издержек на распределительную логистику предприятия
Методы достижения целей.
Методы достижения целей можно разделить на организационные и программные. С нашей точки зрения, эффективная дистрибуция базируется в первую очередь на правильных управленческих показателях. Для системы распределения — основными показателями при этом являются:
1 Общий уровень товароматериальных ценностей в сети в целом
2 Процент неудовлетворенного спроса, либо же сумма задержки исполнения заказа в деньго-днях.
|
Методики управлени продуктах.
Имеется 2 методики програмной реализации DRP-систем
1-я методика базируется на принципе — чем больше в системе информации по поставках, тем лучший уровень управления поставками в сети. 2-я методика базируется на принципе — управляй реальным спросом в реальном режиме времени.
Преимущества метода:
уменьшение логистических издержек, связанных с хранением и управлением запасами готовой продукции
уменьшение уровней запасов за счет точного определения величины и места поставок
сокращение потребности в складских площадях за счет уменьшения запасов
уменьшение транспортной составляющей издержек за счет эффективной обратной связи по заказам
улучшение координации между дистрибьюцией и производством.
№41. Определение оптимального размера заказа на восполнение запаса.
Экономичный размер заказа формула Уилсона, EOQ-модель — модель, определяющая оптимальный объём заказываемого товара, который позволяет минимизировать общие переменные издержки, связанные с заказом и хранением запасов.
Основные предположения
1. Спрос на продукт известен.
2. Время реализации заказа поставки известно и постоянно.
3. Получение товара происходит мгновенно.
4. В модели не учитываются оптовые скидки.
5. Дефицит не допускается.
№42 Модель управления запасами с фиксированным интервалом времени.
Заказы делаются в строго определенные моменты времени, которые отстоят друг от друга не равные интервалы.
Исходные данные для расчета параметров системы следующие:
-потребность в заказываемом продукте, шт.,
-интервал времени между заказами, дни,
-время поставки, дни,
-возможная задержка поставки, дни.
Расчётные параметры системы:
1) Определить интервал времени между заказами можно с учетом оптимального размера заказа (ЕОQ = √(2∙А∙S)/I, где А–з-ты на постав 1 парт; S–год-ая потреб-ть; I – ср.год-ые з-ты на хр-ие 1 шт.). Оптимальный размер заказа позволяет минимизировать совокупные затраты на хранение запаса и повторение заказа, а также достичь наилучшего сочетания взаимодействующих факторов, таких, как используемая площадь складских помещений, издержки на хранение запасов и стоимость заказа.
Интервал врем м/у заказами: Т=N/(S/EOQ),где N–кол-во раб дней в году.
2)Гарантийный (страховой) запас предназначен для непрерывного снабжения потребителя в случае непредвиденных обстоятельств, т.е при максимально возможной задержке Восполнение ГЗ производится в ходе последующих постав ч/з использование ПУ запаса. ГЗ = tзп×λ, где tзп – возможная задержка поставки, λ – ожидаемое дневное потребление = S / кол-во раб дней.
3) МЖЗ определяет уровень запаса, экономически целесообразный в данной системе управления запасами: МЖЗ=ГЗ+Т∙λ. В этой системе величина ПУ не рассчитывается.
4) Т.к в данной системе момент заказа заранее определен и не меняется ни при каких обстоятельствах, постепенно пересчитываемым параметром являет размер заказа. Его вычисление осн-ся на прогнозируемом уровне потребления до момента поступления заказа на склад организации. РЗ = МЖЗ – ТЗ + ОП, где ОП – обязательное потребление, ТЗ – текущий запас = МЖЗ – (Т - tп)∙λ, где tп – время поставки, (Т- tп) – период расходования запаса до ПУ. Т.е. РЗ рассчитывается т.образом, что при условии точного соответствия фактического потребления за время поставки ожидаемому, поставка пополняет запас на складе до МЖЗ. Система допускает возникновение дефицита. Это означает, что система применима, когда возможные потери от дефицита для предприятия несущественны
№43 Модель управления запасами «min-max».
Система содержит в себе эл-ты основных сис-м упр-я запасами. В ней используется постоянный интервал времени м/у заказами. Система используется, когда затраты на учет запасов и издержки на оформление заказа настолько значительны, что становятся соизмеримы с потерями от дефицита запасов. Поэтому в рассматриваемой системе заказы, производятся не через каждый заданный интервал времени, а только при условии, что запасы на складе в этот момент оказались равными или меньше установленного минимального уровня. В случае выдачи размер рассчитывается так, чтобы поставка пополнила запасы до максимального желательного уровня. Таким образом, данная система работает лишь с двумя уровнями запасов – минимальным и максимальным, чему она и обязана своим названием.
Исходные данные для расчета параметров системы таковы:
-потребность в заказываемом продукте, шт.,
-интервал времени между заказами, дни,
-время поставки, дни,
-возможная задержка поставки, дни.
Гарантийный (страховой) запас позволяет обеспечивать потребителя в случае предполагаемой задержки поставки. Как и система с установленной периодичностью пополнения запасов до постоянного уровня, гарантийный запас используется для расчета порогового уровня запаса.
Пороговый уровень запаса в системе «Минимум—максимум» выполняет роль «минимального» уровня. Если в установленный момент времени этот уровень пройден, т. е. наличный запас равен пороговому уровню, или не достигает его, то заказ оформляется. В противном случае заказ не выдается, и отслеживание порогового уровня, а также выдача заказа будут произведены только через заданный интервал времени.
Максимальный желательный запас в системе «Минимум—максимум» выполняет роль «максимального» уровня. Его размер учитывается при определении размера заказа. Он косвенно (через интервал времени между заказами) связан с наиболее рациональной загрузкой площадей склада при учете возможных сбоев поставки и необходимости бесперебойного снабжения потребления.
Система «Минимум—максимум» ориентирована на ситуацию, когда затраты на учет запасов на складе и издержки на оформление заказа настолько значительны, что становятся соизмеримы с потерями от дефицита запасов. Это единственная из рассмотренных ранее систем, допускающая дефицит запасов по экономическим соображениям. Тем не менее и система «Минимум—максимум» учитывает возможность задержки поставки через параметр гарантийного запаса
№44. современные направления в развитии информационного обеспечения логистики.
Понятие и сущность логистических информационных систем
качественного информационного обеспечения логистических процессов возникают проблемы:
Ш отсутствие сбора информации на предприятиях. В основном информация носит не точный, не оперативный и не преемственный характер. Зачастую компании терпят крах по причине несвоевременной, либо недостоверной полученной информации
Ш слабое развитие коммуникационных сетей по структуре и техническому уровню для информационных систем обслуживающих ЭВМ и отсутствие информационного взаимодействия между поставщиками-производителями и покупателями-потребителями
Ш отсутствие технических средств информационного обеспечения на предприятиях
Ш отсутствие единой межнациональной коммуникационной информационной системы, которая была бы способна передавать информацию о материальных потоках и осуществлять контроль за их движением.
Логистические информационные системы представляют собой соответствующие информационные сети, начинающиеся с отслеживания оперативных требований заказчиков представляющих чисто стохастическую величину, распространяющиеся через распределение и производство до поставщиков. Эти системы обычно разделяются на три группы.
1.Информационные системы для принятия долгосрочных решений структурах и стратегиях
2.Информационные системы для принятия решений на среднесрочную и краткосрочную перспективу так называемые диапозитивные или диспетчерские системы. 3.Информационные системы для исполнения повседневных дел так называемые исполнительные системы.
Виды и принципы построения современных информационных систем
Логистические информационные системы подразделяются на три группы:
Ш плановые
Ш диапозитивные или диспетчерские
Ш исполнительные или оперативные.
Логистические информационные системы, входящие в разные группы, отличаются как своими функциональными, так и обеспечивающими подсистемами. Функциональные подсистемы отличаются составом решаемых задач. Обеспечивающие подсистемы могут отличаться всеми своими элементами, т.е. техническим, информационным и математическим обеспечением. Остановимся подробнее на специфике отдельных информационных систем.
Плановые информационные системы. Эти системы создаются на административном уровне управления и служат для принятия долгосрочных решений стратегического характера. Среди решаемых задач могут быть следующие:
Ш создание и оптимизация звеньев логистической цепи
Ш управление условно-постоянными, т.е. мало изменяющимися данными
Ш планирование производства
Ш общее управление запасами
Ш управление резервами и другие задачи.
Диспозитивные информационные системы. Эти системы создаются на уровне управления складом или цехом и служат для обеспечения отлаженной работы логистических систем. Здесь могут решаться следующие задачи:
Ш детальное управление запасами местами складирования
Ш распоряжение внутрискладским или внутризаводским транспортом
Ш отбор грузов по заказам и их комплектование, учет отправляемых грузов и другие задачи.
Исполнительные информационные системы. Создаются на уровне административного или оперативного управления. Обработка информации в этих системах производится в темпе, определяемом скоростью ее поступления в ЭВМ. Это так называемый режим работы в реальном масштабе времени, который позволяет получать необходимую информацию о движении грузов в текущий момент времени и своевременно выдавать соответствующие административные и управляющие воздействия на объект управления. Этими системами могут решаться разнообразные задачи, связанные с контролем материальных потоков, оперативным управлением обслуживания производства, управлением перемещениями и т.п.
В соответствии с принципами системного подхода любая система сначала должна исследоваться во взаимоотношении с внешней средой, а уж затем внутри своей структуры. Этот принцип последовательного продвижения по этапам создания системы, должен соблюдаться и при проектировании логистических информационных систем.
С позиций системного подхода в процессах логистики выделяют три уровня:
Первый уровень — рабочее место, на котором осуществляется логистическая операция с материальным потоком, т.е. передвигается, разгружается, упаковывается и т.п. грузовая единица, деталь или любой другой элемент материального потока.
Второй уровень — участок, цех, склад, где происходят процессы транспортировки грузов, размещаются рабочие места.
Третий уровень — система транспортирования и перемещения в целом, охватывающая цепь событий, за начало которой можно принять момент отгрузки сырья поставщиком. Оканчивается эта цепь при поступлении готовых изделий в конечное потребление.
В плановых информационных системах решаются задачи, связывающие логистическую систему с совокупным материальным потоком. При этом осуществляется сквозное планирование в цепи сбыт — производство -снабжение, что позволяет создать эффективную систему организации производства, построенную на требованиях рынка, с выдачей необходимых требований в систему материально-технического обеспечения предприятия. Этим плановые системы как бы ввязывают логистическую систему во внешнюю среду, в совокупный материальный поток.
Диспозитивные и исполнительные системы детализируют намеченные планы и обеспечивают их выполнение на отдельных производственных участках, в
складах, а также на конкретных рабочих местах.
В соответствии с концепцией логистики информационные системы, относящиеся к различным группам, интегрируются в единую информационную систему. Различают вертикальную и горизонтальную интеграцию.
Вертикальной интеграцией считается связь между плановой, диспозитивной и исполнительной системами посредством вертикальных информационных потоков.
Горизонтальной интеграцией считается связь между отдельными комплексами задач в диспозитивных и исполнительных системах посредством горизонтальных информационных потоков.
В целом преимущества интегрированных информационных систем заключается в следующем:
Ш возрастает скорость обмена информацией
Ш уменьшается количество ошибок в учете
Ш уменьшается объем непроизводительной, бумажной работы:
Ш совмещаются разрозненные информационные блоки.
№45. формирование организационной структуры управления логистическорй компании
Основные задачи отдела логистики:
1.Развитие, формирование, реорганизация ЛС.
2.Разработка и реализация логистической стратегии предприятия.
3.Внутренняя и внешняя логистическая интеграция:
1формирование взаимодействий, гармоничных и продуктивных рабочих отношений между сотрудниками различных функциональных подразделений, которые обеспечивали бы достижение цели ЛС, организация их совместной работы
2координация деятельности в функциональных областях логистики на предприятии и в ЛЦ.
4.Управление МП и сопутствующими потоками, начиная от формирования договорных отношений с поставщиком и заканчивая доставкой покупателю ГП.
5.Логистический реинжиниринг.
Стадии эволюции логистических структур
По аналогии с историческими этапами развития логистики по уровню охвата логистическим управлением различных сфер деятельности предприятий, эволюциялогистических структур на предприятиях проходит также следующие три стадии.
На первой стадии основная функции логистики — доставка продукции предприятия в розничную сеть. На этой стадии логистические функции распылены между различными подразделениями, но появляются тенденции к объединению ЛФ в организационные подсистемы.
На второй стадии к доставке продукции в розничную сеть добавляются и другие: организация хранения на складах, оптимизация запасов, обслуживание клиентуры и т.д. ЛФ не только расширяются, но и объединяются большинство ЛО, и создаются системы доставки товаров по заказам клиента.
На третьей стадии происходит полное объединение всех ЛО на предприятии. В набор логистических задач включаются построение ЛС, участие в планировании производства и прогнозировании продаж; организация закупок МР для предприятия, организация поставок товаров за рубеж и др.
|
|
Двойное оплодотворение у цветковых растений: Оплодотворение - это процесс слияния мужской и женской половых клеток с образованием зиготы...
Историки об Елизавете Петровне: Елизавета попала между двумя встречными культурными течениями, воспитывалась среди новых европейских веяний и преданий...
Биохимия спиртового брожения: Основу технологии получения пива составляет спиртовое брожение, - при котором сахар превращается...
История развития пистолетов-пулеметов: Предпосылкой для возникновения пистолетов-пулеметов послужила давняя тенденция тяготения винтовок...
© cyberpedia.su 2017-2024 - Не является автором материалов. Исключительное право сохранено за автором текста.
Если вы не хотите, чтобы данный материал был у нас на сайте, перейдите по ссылке: Нарушение авторских прав. Мы поможем в написании вашей работы!