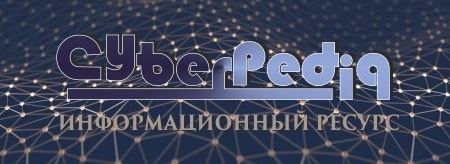
Двойное оплодотворение у цветковых растений: Оплодотворение - это процесс слияния мужской и женской половых клеток с образованием зиготы...
Наброски и зарисовки растений, плодов, цветов: Освоить конструктивное построение структуры дерева через зарисовки отдельных деревьев, группы деревьев...
Топ:
Методика измерений сопротивления растеканию тока анодного заземления: Анодный заземлитель (анод) – проводник, погруженный в электролитическую среду (грунт, раствор электролита) и подключенный к положительному...
Основы обеспечения единства измерений: Обеспечение единства измерений - деятельность метрологических служб, направленная на достижение...
Интересное:
Финансовый рынок и его значение в управлении денежными потоками на современном этапе: любому предприятию для расширения производства и увеличения прибыли нужны...
Берегоукрепление оползневых склонов: На прибрежных склонах основной причиной развития оползневых процессов является подмыв водами рек естественных склонов...
Аура как энергетическое поле: многослойную ауру человека можно представить себе подобным...
Дисциплины:
![]() |
![]() |
5.00
из
|
Заказать работу |
|
|
Общие сведения
Создание машин и механизмов – процесс длительный и трудоемкий, особенно в области производства авиационной и ракетно-космической техники. Начинается он с проработки конструкции будущего изделия и инженерного анализа соответствия конструкции требованиям технического задания, расчетов на прочность, износоустойчивость, долговечность и т.д. В результате возникает необходимость внесения изменений в элементы конструкции: изменять форму и положение отдельных деталей и частей изделия.
Для ускорения процесса проектирования часто изготавливают эскизы.
Эскизы – чертежи деталей, выполненные от руки без применения чертежных инст- рументов и без точного соблюдения масштаба, но с соблюдением всех правил ЕСКД и ГОСТов.
К эскизированию прибегают при ремонте оборудования. В этом случае эскизы выполняют самостоятельную роль, так как по ним изготавливают детали взамен изношенных, непригодных для дальнейшей эксплуатации деталей.
Следует помнить о том, что эскиз это не черновик чертежа, а полноценный конструкторский документ, который должен быть выполнен так, чтобы в нем мог разобраться не только автор, но и другие участвующие в производстве лица. Чем больше эскиз по внешнему виду похож на чертеж, изготовленный с помощью чертежных инструментов, тем выше его ценность.
При составлении эскизов рекомендуется:
1. Выполнять на клетчатой бумаге мягким карандашом без нажима.
2. Изображать деталь в приблизительном (глазомерном) масштабе, но по возможности ближе к действительным размерам элементов эскизируемой детали.
3. Выдерживать пропорциональность конструктивных элементов детали на эскизе на глаз, не прибегая к обмеру.
|
4. Выбирать масштаб таким образом, чтобы на изображениях были понятны все конструктивные элементы детали.
Изучение правил и приобретение практических навыков в составлении чертежей деталей в учебном процессе осуществляют в три этапа:
1. Эскизирование деталей по заданным образцам.
2. Выполнение чертежей деталей по составленным предварительно эскизам в том числе и компьютерных чертежей.
3. Выполнение эскизов и чертежей деталей по чертежу общего вида изделия.
Выбор изображений
Количество изображений детали на чертеже должно быть минимальным, но достаточным для полного представления о форме детали и всех её составляющих геометрических элементов (ГОСТ 2.103-68).
Изображаемую деталь располагают относительно плоскостей проекций так, чтобы изображение на фронтальной плоскости проекций давало наиболее полное представление о форме и размерах детали, что облегчает чтение эскиза. Изображение на фронтальной плоскости проекций принимается на чертеже в качестве главного вида.
На главном виде деталей, ограниченных поверхностями вращения (валы, втулки, гильзы, зубчатые колеса, шкивы, маховики и т.п.), – ось вращения располагается горизонтально (параллельно основной надписи). Такое расположение главного вида cоответствует положению детали на станке, при котором выполняется наибольшее количество операций, и поэтому облегчает пользование чертежом при изготовлении деталей.
Главное изображение в зависимости от формы детали может быть представлено как видом спереди, так и фронтальным разрезом. Главным видом детали, изображенной на рис. 1, является изображение, представленное на рис. 3.
![]() | |||||||||||||||||
![]() | ![]() | ![]() | ![]() | ![]() | ![]() | ![]() | ![]() | ||||||||||
![]() | |||||||||||||
![]() | ![]() | ![]() | |||||||||||
![]() | ![]() | ![]() | |||||||||||
Рис. 3
Кроме главного вида необходимо выполнить три вынесенных сечения плоскостями, перпендикулярными оси вала, для уточнения его конструкции. Вид слева на торец 1 помогает уточнить форму паза 2.
|
Теперь рассмотрим выполнение эскиза и чертежа корпусной детали (корпуса) простой формы, которая состоит из элементов, изображенных на рис. 4.
В качестве главного изображения выберем вид спереди. Одного этого вида недоста- точно для полного отображения всей конструкции корпуса. Необходимо дополнить вид спереди видом сверху, чтобы показать форму основания, и разрезом вдоль оси отверстия для вала в качестве вида слева.
Все эти изображения необходимо расположить в проекционной связи, при этом следует применить местный разрез отверстия для болта для того, чтобы избежать линий невидимого контура, которые снижают наглядность чертежа.
Детали более сложной формы требуют большего количества изображений. Вопрос о количестве необходимых изображений решается индивидуально для каждой конкретной детали.
Рис. 4
Оформление видов, разрезов и сечений
При оформлении выбранных видов уточняют дополнительные подробности (скругления, фаски, проточки, канавки и т.п.), при необходимости выполняют выносные элементы и удаляют вспомогательные линии черновых построений (рис. 8).
![]() | |||
![]() | |||
Рис. 8 Рис. 9
Затем оформляют разрезы и сечения (рис. 9) в соответствии с ГОСТ 2.305-68, выполняют штриховку в одном направлении с одинаковым расстоянием на всех изображениях по ГОСТ 2.306-68 и окончательно обводят изображения линиями соответствующего типа по ГОСТ 2.303-68.
Нанесение размерных чисел
При помощи измерительных инструментов следует определить размеры поверхностей, входящих в состав данной детали, и размеры, характеризующие их положение относительно выбранных баз, и проставить размерные числа на эскизе.
![]() |
Рис. 10
1.9 Окончательное оформление эскиза
При окончательном оформлении выполняют необходимые обозначения местных и дополнительных (или других) видов, разрезов, сечений и выносных элементов в указанной последовательности, начиная с прописной буквы А русского алфавита (для каждого отдельного эскиза или чертежа). В случае необходимости указывают технические требования и выполняют пояснительные надписи. Для зубчатых колес составляют таблицу геометрических параметров зацепления. Затем окончательно проверяют выполненный эскиз, и вносят необходимые уточнения и исправления. Заполняют основную надпись.
|
При составлении эскизов по готовой детали следует критически проанализировать форму и расположение отдельных ее элементов. Необходимо иметь в виду следующее:
1. Эскизы не должны передавать дефекты детали от её износа или неправильной обработки.
2. Не должны отражаться на эскизе дефекты литья, происходящие от неточности формовки заготовок: неравномерность толщин стенок, асимметрия частей детали относительно оси, неровные края, необоснованные приливы и т. п.
3. Всякая плоскость, в которой имеется отверстие под болт, должна быть перпендикулярна оси этого отверстия и иметь опорную площадь, достаточную для размещения гайки.
4. Не допускается упрощение изображений детали, игнорирование отдельных элементов детали (литейные уклоны, конусности, фаски, галтели и т.п.).
Измерительные инструменты
Простейшими измерительными инструментами являются штанген- циркуль, кронциркуль, нутромер, сталь- ная линейка, угломер, радиусомер и другие.
Стальная линейка. Изготавли- вается длиной от 100 до 500 мм и применяется, если не требуется высокая точность измерения.
Штангенциркуль применяется для более точных измерений диаметров поверхностей вращения, линейных размеров. Точность измерения достига- ет 0,05–0.1 мм (рис. 11).
Рис. 11
Кронциркуль и нутромер являются вспомогательными мерительными инструментами, применяются для измерения наружных и внутренних размеров детали посредством переноса отдельных размеров с детали на стальную линейку. Точность измерения не высокая, не более 0,5–1мм (рис. 12).
|
Резьбомер применяется для измерения шага резьбы или числа ниток резьбы на определенной длине. Измерение производится с помощью набора стальных шаблонов (гребенок), заключенных в колодку. Каждая гребенка является точной копией профиля резьбы определенной стандартной резьбы.
Радиусомер применяется при замере закруглений небольшого радиуса величиной 0,5…1,5 мм, представляет собой набор шаблонов различных радиусов, скрепленных в колодку. Пользуются им так же, как и резьбомером.
Обмер деталей
Рис. 12
При обмере деталей различных конструкций приходится измерять диаметраль- ные и линейные размеры, толщины стенок, рас- стояния между центрами отверстий и некото- рые другие.
Измерение диаметральных размеров детали (наружных и внутренних) осуществляет- ся с помощью кронциркуля и нутромера.
На рис. 12 показаны варианты измерения этими инструментами наружного и внутреннего диаметров цилиндра D и d.
Измерение линейных размеров детали можно выполнить стальной линейкой, штанген- циркулем, глубиномером и другими инструмен- тами.
На рис. 12 показано также определение некоторых линейных размеров. Определить толщину дна пустотелого цилиндра можно по формуле b0 = H - h. Стальной линейкой измеряется высота цилиндра H и его глубина h. Зная эти размеры, можно определить b0.
Расстояние от центра отверстия до опорной поверхности определяется при помощи стальной линейки. Её прикладывают к поверхности цилиндра, как указано на рис.12, и определяют размеры h1 и h3. Зная диаметр отверстия d1, можно легко определить искомый размер по формулам:
h2 = h1 + d1/2, или h2 = h3 - d1/2.
Измерение толщины стенки b полых деталей производится кронциркулем (см. рис.12).
Толщина стенки может быть определена по формуле b = (D – d)/2.
В том случае, если измерить толщину стенки кронциркулем не представляется возможным, так как при его выемке необходимо раскрыть его ножки, пользуются стальной линейкой.
Толщина стенки b1 (рис. 13) в этом случае определяется как разность размеров S и S1, т. е.
b1 = S - S1.
Рис. 13
Обмер зубчатых колес
Деталями зубчатых передач являются зубчатые колеса, зубчатые рейки, червячные колеса и валы. При эскизировании зубчатых колес необходимо определять основные параметры.
Коническое зубчатое колесо
Характерной особенностью конических зубчатых колес (рис.18) является переменность значения модуля, шага и высоты зуба по длине зуба. Их значения увеличиваются в направлении от вершины к основанию делительного конуса.
Форму и размеры зуба конического колеса определяют следующие соосные конические поверхности (рис. 19):
1. Делительный конус с углом между контурными образующими и осью колеса δ.
|
2. Конус вершин зубьев с углом конуса вершин зубьев и осью колеса δa.
3. Конус впадин зубьев с углом конуса вершин зубьев и осью колеса δf.
4. Дополнительный конус, у которого контурные образующие перпендикулярны к образующим делительного конуса, и с углом между контурными образующими и осью колеса ε.
5. Плоскость общего основания - это плоскость пересечения конуса вершин зубьев с дополнительным конусом.
![]() |
Рис. 18 Рис. 19
Дополнительный конус пресекает соосные конические поверхности зубчатого колеса по трем окружностям:
1. Внешний диаметр делительной окружности – de.
2. Внешний диаметр вершин зубьев – dae.
3. Внешний диаметр впадин зубьев – dfe.
Конические зубчатые колеса характеризуются рядом специфических терминов и обозначений, как например:
Длина образующей делительного конуса Re – внешнее конусное расстояние. Расстояние от базовой плоскости до плоскости общего основания С. Ширина зубчатого венца b.
Величину диаметра делительной окружности de принимают в качестве расчетной.
На чертежах указывается наибольший модуль me, определяемый по высоте зуба he, которая измеряется по поверхности внешнего дополнительного конуса.
Для конических зубчатых колес эвольвентного профиля, согласно ГОСТ 13754-81 на исходный контур конических зубчатых колес, hae = me, а hfe = 1.2 me, тогда: he = 2.2 me. Отсюда
me = he / 2,2.
Найденный модуль сопоставляется со стандартными модулями, приведенными в табл. 1, и принимается его ближайшее значение. После этого определяется диаметр делительной окружности эскизируемого зубчатого конического колеса de и уточняется внешний диаметр вершин зубьев dae:
de= me. z; dae = m (z + 2 cos d).
Если угол между образующими делительного и внешнего дополнительного конусов равен
900,то модуль me можно определить по формуле
me = dae / (z + 2 cos d).
Поэтому надо измерить диаметр вершин зубьев daе .
Величина угла δ может быть определена приближенно по формуле
cos d =(dae -- de) / 2 me.
Угол вершин зубьев δa = δ + b a , а угол впадин зубьев δf = δ - b f. При этом b a = b f.
Угол головки зуба b a определяется приближенно расчетом по формуле
tg b a = hae / Re = 2,4 sin d / z.
Длина образующей делительного конуса R определяется по формуле
Re = de / 2 sin d.
Кроме найденных величин на чертежах конических зубчатых колес указывают размеры: А, С и угол ε.
Расстояние С от базовой плоскости зубчатого колеса до плоскости внешней окружности вершин зубьев определяется замером.
Базовое расстояние (монтажный размер) А можно определить по формуле
А = Re cos d + hae sin d.
Величина угла дополнительного конуса ε равна 900- d.
Примечание:
Если известно число зубьев двух конических зубчатых колес z1 и z2, находящихся в зацеплении друг с другом, то угол d может быть определен точно по формуле
tg d = z1 / z2.
Расчетные параметры зубчатых колес m, z и ГОСТ заносят в таблицу, показанную на рис. 20, а – для одного зубчатого венца, на рис.20, б – для блока зубчатых колес. Форма таблиц имеет учебное назначение.
![]() | ![]() | ||
а) б)
Рис. 20
Пример условного обозначения соединения, втулки, вала
с числом зубьев z, внутренним диаметром d, наружным диаметром D, шириной зуба b при центрировании:
по внутреннему диаметру d – z × d × D × b, по наружному диаметру D – z × d × D × b, по боковым сторонам: b – z × d × D × b.
Размеры прямобочных шлицевых соединений приведены в Приложении 14.
Эвольвентные шлицевые соединения ГОСТ 6033-80.
Обладают рядом преимуществ по сравнению с прямобочными: повышенная прочность зуба вследствие утолщения его к основанию (рис. 22); повышенная точность изготовления в результате применения в качестве режущих инструментов червячных фрез и возможности шлифования.
Основные параметры: номинальный диаметр D, модуль m и число зубьев z.
Модуль m = 0,5; (0,6); 0,8; (1,0); 1,25; (1,5); 2; (2,5); 3; (3,5);
(4); 5; (6); 8; (10).
Число зубьев z = 6 и более.
Размеры эвольвентных шлицевых соединений приведены в Приложении 15.
Рис. 22 Пример условного обозначения соединения, втулки, вала
с модулем m и номинальным D:
D × m ГОСТ 6033-80.
Рис. 23
Треугольные шлицевые соединения (рис. 23) применяют в неподвижных соединениях для передачи небольших крутящих моментов при наличии тонкостенных шлицевых втулок. Основные параметры: число зубьев z от 20 до 70;угол впадин зубьев на валу β – 600, 720, 900.
Условное обозначение:
Тр. Dа × z,
где Dа – номинальный диаметр;
z - число зубьев.
Нестандартизованные шлицевые соединения, например, валы с торцевыми шлицами треугольного профиля и муфты с V-образным мелким (мышиным) зубом (рис. 24), помещают изображение профиля зуба с двумя впадинами (шлицами) со всеми необходимыми сведениями (см. таблицу).
D | d | γ | z | a | h | β |
40 | 28 | 120 | 30 | 30 45 | 3,07 1,80 | 5011'30″ 2059'30″ |
50 | 32 | 100 | 36 | 30 45 | 3,22 1,89 | 4019' 2028'30″ |
60 | 40 | 8060' | 40 | 30 45 | 3,53 2,06 | 3053' 2015' |
70 | 46 | 8012' | 44 | 30 45 | 3,77 2,21 | 3032' 2002'30″ |
80 | 50 | 6072' | 50 | 30 45 | 3,80 2,22 | 3006'30″ 1048' |
90 | 56 | 8060' | 50 | 30 45 | 4,34 2,53 | 3006'30″ 1048' |
Рис. 24
Примечание: при эскизировании деталей с прямобочными и эвольвентными шлицами (не находящихся в соединении) в учебных целях рекомендуется применять центрирование по наружному диаметру.
ЧЕРТЕЖИ ДЕТАЛЕЙ МАШИН
На иллюстрациях представлены типовые детали:
корпус (рис. 33),
фланец (2 вида) (рис. 34),
блок зубчатых колес (2 вида) (рис.35),
Рис. 34
![]() | ![]() | ||
Рис. 35
вал (рис. 36)
Рис. 36
Приложения
Нормальные линейные размеры
Приложение 1
Ряд | Размеры |
Первый ряд | 1,0; 1,6; 2,5; 4,0; 6,3; 10,0; 16; 25; 40; 63; 100; 160; 250…. |
Второй ряд | 1,2; 2,0; 3,2; 5,0; 8,0; 12; 20; 32; 50; 80; 125; 200; 320….. |
Третий ряд | 1,1; 1,4; 1,8; 2,2; 2,8; 3,6; 4,5; 5,6; 7,1; 9,0; 11; 14; 18; 22; 28; 36; 45; 65; 71; 90; 110; 140; 180; 220…. |
Четвёртый ряд | 1,05; 1,15; 1,3; 1,7; 1,9; 2,1; 2,4; 2,6; 3,0; 3,4; 3,8; 4,2; 4,8; 5,3; 6,0; 6,7; 7,5; 8,5; 9,5; 10,5; 11,5; 13; 15; 17; 19; 21; 24; 26; 30; 34; 38; 42; 48; 53; 60; 67; 75; 85; 95 … |
Приложение 2
ГОСТ 8724-81
Диаметр d резьбы для ряда | Шаг P | |||
1 ряд | 2 ряд | 3 ряд | крупный | мелкий |
3 | - | - | 0,5 | |
4 | - | - | 0,7 | |
5 | - | - | 0,8 | |
6 | - | - | 1 | 0,75; 0,5 |
8 | - | 9 | 1,25 | 1; 0,75; 0,5 |
10 | - | 11 | 1,5 | 1,25; 1; 0,75; 0,5 |
12 | - | - | 1,75 | 1,5; 1,25; 1; 0,75; 0,5 |
- | 14 | 15 | 2 | 1.5; 1,25; 1; 0,75; 0,5 |
16 | - | 17 | 2 | 1,5; 1; 0,75; 0,5 |
- | 18 | - | 2,5 | 2; 1,5; 1; 0,75; 0,5 |
20 | - | - | 2,5 | 2; 1,5; 1; 0,75; 0,5 |
- | 22 | - | 2,5 | 2; 1,5; 1; 0,75; 0,5 |
24 | - | 25 | 3 | 2; 1,5; 1; 0,75 |
- | - | 26 | - | 2; 1,5; 1 |
- | 27 | 28 | 3 | 2; 1,5; 1; 0,75 |
30 | - | 32 | 3,5 | 3; 2; 1,5; 1; 0,75 |
- | 33 | 35 | 3,5 | 3; 2; 1,5; 1; 0,75 |
36 | - | 38 | 4 | 3; 2; 1,5; 1 |
- | 39 | 40 | 4 | 3; 2; 1,5; 1 |
42 | - | - | 4,5 | 4; 3; 2; 1,5; 1 |
- | 45 | - | 4,5 | 4; 3; 2; 1,5; 1 |
48 | - | 50 | 5 | 4; 3; 2; 1,5; 1 |
- | 52 | 55 | 5 | 4; 3; 2; 1,5; 1 |
56 | - | 58 | 5,5 | 4; 3; 2; 1,5; 1 |
- | 60 | 62 | 5,5 | 4; 3; 2; 1,5; 1 |
64 | - | 65 | 6 | 4; 3; 2; 1,5; 1 |
- | 68 | 70 | 6 | 4; 3; 2; 1.5; 1 |
72 | - | 75 | - | 6; 4; 3; 2; 1,5; 1 |
- | 76 | 73 | - | 6; 4; 3; 2; 1,5; 1 |
80 | - | 82 | - | 6; 4; 3; 2; 1,5; 1 |
- | 85 | - | - | 6; 4; 3; 2; 1,5 |
90 | - | - | - | 6; 4; 3; 2; 1,5 |
- | 95 | - | - | 6; 4; 3; 2; 1,5 |
100 | - | - | - | 6; 4; 3; 2; 1,5 |
Приложение 6
Проточки для выхода метрической резьбы ГОСТ 10549-80
Наружная резьба | Внутренняя резьба | ||||||||||||||||
|
|
|
| ||||||||||||||
| |||||||||||||||||
Шаг резьбы | Тип 1 | Тип 2 |
d f |
|
Шаг резьбы |
| Тип 1 | Тип 2 |
d f | ||||||||
f | R | R1 | f | R2 | f | R | R1 | f | R2 | ||||||||
0,5 | 1,6 | 0,5 | 0,3 | - | - | d -0,8 | 0,5 | 2,0 | 0,5 | 0,3 | - | - | d +0,3 | ||||
0,7 | 2,0 | 0,5 | 0,3 | - | - | d -1,0 | 0,75 | 3,0 | 1,0 | 0,5 | - | - | d +0,4 | ||||
0,75 | 2,0 | 0,5 | 0,3 | - | - | d -1,2 | 1 | 4,0 | 1,0 | 0,5 | 3,6 | 2,0 | d +0,5 | ||||
0,8 | 3,0 | 1,0 | 0,5 | - | - | d -1,2 | 1,25 | 5,0 | 1,6 | 0,5 | 4,5 | 2,5 | d +0,5 | ||||
1 | 3,0 | 1,0 | 0,5 | 3,6 | 2,0 | d -1,5 | 1,5 | 6,0 | 1,6 | 1,0 | 5,4 | 3,0 | d +0,7 | ||||
1,25 | 4,0 | 1,0 | 0,5 | 4,4 | 2,5 | d -1,8 | 1,75 | 7,0 | 1,6 | 1,0 | 6,2 | 3,5 | d +0,7 | ||||
1,5 | 4,0 | 1,0 | 0,5 | 4,6 | 2,5 | d -2,2 | 2 | 8,0 | 2,0 | 1,0 | 6,5 | 3,5 | d +1,0 | ||||
1,75 | 4,0 | 1,0 | 0,5 | 5,4 | 3,0 | d -2,5 | 2,5 | 10,0 | 3,0 | 1,0 | 8,9 | 5,0 | d +1.0 | ||||
2 | 5,0 | 1,6 | 0.5 | 5,6 | 3,0 | d -3,0 | 3 | 10,0 | 3,0 | 1,0 | 11,4 | 6,5 | d +1,2 | ||||
2,5 | 6,0 | 1,6 | 1,0 | 7,3 | 4,0 | d -3,5 | 3,5 | 10,0 | 3,0 | 1,0 | 13,1 | 7,5 | d +1,2 | ||||
3 | 6,0 | 1,6 | 1,0 | 7,6 | 4,0 | d -4,5 | 4 | 12,0 | 3,0 | 1,0 | 14,3 | 8,0 | d +1,5 | ||||
3,5 | 8,0 | 2,0 | 1,0 | 10,2 | 5,5 | d -5 | 4,5 | 14,0 | 3,0 | 1,0 | 16,6 | 9,5 | d +1,5 | ||||
4 | 8,0 | 2,0 | 1,0 | 10,3 | 5,5 | d -6 | 5 | 16,0 | 3,0 | 1,0 | 18,4 | 10,5 | d +1,8 | ||||
4,5 | 10 | 3,0 | 1,0 | 12,9 | 7,0 | d -6,5 | 5,5 | 16,0 | 3,0 | 1,0 | 18,7 | 10,5 | d +1,8 | ||||
5 | 10 | 3,0 | 1,0 | 13,1 | 7,0 | d -7 | 6 | 16,0 | 3,0 | 1,0 | 18,9 | 10,5 | d +2,0 | ||||
Примечание: d – наружный диаметр метрической резьбы
Приложение 7
Размеры фасок для метрической резьбы ГОСТ 10549-80*
Шаг | 0,75 | 1,0 | 1,25 | 1,5 | 1,75 | 2,0 | 2,5 | 3,0 | 3,5 | 4,0 | 4,5 | 5,0 | 5,5 | 6,0 |
Фаска Сҳ450 | 1,0 | 1,0 | 1,6 | 1,6 | 1,6 | 2,0 | 2,5 | 2,5 | 2,5 | 3,0 | 3,0 | 4,0 | 4,0 | 4,0 |
Приложение 8
Тип 1
Тип 2
Шпонки призматические ГОСТ 23360-78
Приложение12
Диаметр вала, d | Сечение шпонки b ´ h | Глубина шпоночного паза | Длина шпонки, A | |||
вал t 1 | втулка t 2 | от | до | ряд длин | ||
Св.10 до 12 | 4 ´ 4 5 ´ 5 6 ´ 6 8 ´ 7 10 ´ 8 12 ´ 8 14 ´ 9 16 ´ 10 18 ´ 11 20 ´ 12 | 2,5 | 1,8 | 8 | 45 | 6, 8, 10, 12, 14, 16, 18, 20, 22, 25, 28, 32, 36, 40, 45, 50, 56, 63, 70, 80, 90, 100, 110, 125, 140, 160, 180, 200, 220… |
12…17 | 3,0 | 2,3 | 10 | 56 | ||
17…22 | 3,5 | 2,8 | 14 | 70 | ||
22…30 | 4,0 | 3,3 | 18 | 90 | ||
30…38 | 5,0 | 3,3 | 22 | 110 | ||
38…44 | 5,0 | 3,3 | 28 | 140 | ||
44…50 | 5,0 | 3,3 | 36 | 160 | ||
50…58 | 6,0 | 4,3 | 45 | 180 | ||
58…65 | 7,0 | 4,4 | 50 | 200 | ||
65…75 | 7,5 | 4,9 | 56 | 220 |
Шпонки сегментные ГОСТ 24071-80
Приложение 13
Диаметр вала, D |
Размеры шпонки b ´ h ´ d | Глубина шпоночного паза | ||
Назначение шпонки | ||||
передача крутящих моментов | фиксация элементов | вал t 1 | втулка t 2 | |
Св. 6 до 7 | Св. 8 до 10 | 2 ´ 3,7 ´ 10 2,5 ´ 3,7 ´ 10 3 ´ 5 ´ 13 3 ´ 6,5 ´ 16 4 ´ 6,5 ´ 16 4 ´ 7,5 ´ 19 5 ´ 6,5 ´ 16 5 ´ 7,5 ´ 19 5 ´ 9 ´ 22 6 ´ 9 ´ 22 | 2,9 | 1,0 |
7…8 | 10…12 | 2,7 | 1,2 | |
8…10 | 12…15 | 3,8 | 1,4 | |
10…12 | 15…18 | 5,3 | 1,4 | |
12…14 | 18…20 | 5,0 | 1,8 | |
14…16 | 20…22 | 6,0 | 1,8 | |
16…18 | 22…25 | 4,5 | 2,3 | |
18…20 | 25…28 | 5,5 | 2,3 | |
20…22 | 28…32 | 7,0 | 2,3 | |
22…25 | 32…36 | 6,5 | 2,8 |
Рифления
Приложение 14
Рифления предотвращают проскальзывания пальцев руки при завинчивании детали. На чертеже указывают, согласно ГОСТ 21474-75, тип рифления (прямое или сетчатое) и его шаг P. Угол рифления, отличный от 450, указывается на изображении. Шаг зависит от ширины и диаметра накатываемой поверхности и (для сетчатого рифления) материала детали.
1. Форма и основные размеры рифлений должны соответствовать указанным на чертеже.
![]() |
2. Фаска - по ГОСТ 10948-64 (см. приложение 3).
3. Шаги рифлений P следует выбирать из рядов: прямых - 0,5; 0,6; 0,8; 1,0; 1,2; 1,6;
сетчатых - 0,5; 0,6; 0,8; 1,0; 1,2; 1,6; 2,0.
Пример условного обозначения:
прямого рифления с шагом P =0,8 мм: сетчатого рифления с шагом P =1,0 мм:
Рифление прямое 0,8 ГОСТ 21474-75 Рифление сетчатое 1,0 ГОСТ 21474-75
4. Высота рифления h: для стали 0,25 0,7 P;
для цветных металлов и сплавов 0,25 0,5P.
5. α =70° для рифлений по стали, α =90° для цветных металлов и сплавов.
6. Зависимость шага P от диаметра и ширины накатываемой поверхности указана в табл. П1 и П2.
Таблица П1. Рифления прямые для всех материалов
Ширина накатываемой поверхности, B | Диаметр накатываемой поверхности, D 1 | |||||
до 8 | св.8 до 16 | св.16 до 32 | св.32до 63 | св.63 до 125 | св.125 | |
Шаг рифлений, P | ||||||
До 4 | 0,5 | 0,5 | 0,6 | 0,6 | 0,8 | 1,0 |
св.8 до 16 |
| 0,8 | 0,8 | |||
св.16 до 32 | 1,0 | 1,0 | 1,2 | |||
св.32 | 1,2 | 1,6 |
Таблица П2. Рифления сетчатые
Материал заготовки |
Шири
![]() Организация стока поверхностных вод: Наибольшее количество влаги на земном шаре испаряется с поверхности морей и океанов (88‰)... ![]() Историки об Елизавете Петровне: Елизавета попала между двумя встречными культурными течениями, воспитывалась среди новых европейских веяний и преданий... ![]() Своеобразие русской архитектуры: Основной материал – дерево – быстрота постройки, но недолговечность и необходимость деления... ![]() Индивидуальные очистные сооружения: К классу индивидуальных очистных сооружений относят сооружения, пропускная способность которых... © cyberpedia.su 2017-2024 - Не является автором материалов. Исключительное право сохранено за автором текста. |