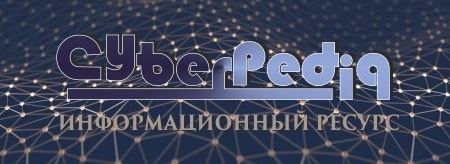
Наброски и зарисовки растений, плодов, цветов: Освоить конструктивное построение структуры дерева через зарисовки отдельных деревьев, группы деревьев...
Биохимия спиртового брожения: Основу технологии получения пива составляет спиртовое брожение, - при котором сахар превращается...
Топ:
Выпускная квалификационная работа: Основная часть ВКР, как правило, состоит из двух-трех глав, каждая из которых, в свою очередь...
Особенности труда и отдыха в условиях низких температур: К работам при низких температурах на открытом воздухе и в не отапливаемых помещениях допускаются лица не моложе 18 лет, прошедшие...
Техника безопасности при работе на пароконвектомате: К обслуживанию пароконвектомата допускаются лица, прошедшие технический минимум по эксплуатации оборудования...
Интересное:
Аура как энергетическое поле: многослойную ауру человека можно представить себе подобным...
Принципы управления денежными потоками: одним из методов контроля за состоянием денежной наличности является...
Как мы говорим и как мы слушаем: общение можно сравнить с огромным зонтиком, под которым скрыто все...
Дисциплины:
![]() |
![]() |
5.00
из
|
Заказать работу |
|
|
1) Опиливание параллельных плоских поверхностей
и поверхностей, расположенных под углом
Опиливание плоскопараллельных плоскостей заготовки начинают с наиболее широкой поверхности, которую принимают за основную измерительную базу. Эту поверхность опиливают окончательно, соблюдая все правила опиливания и проверки плоских поверхностей, выполненные на занятии 5. Затем штангенциркулем предварительно проверяют толщину и параллельность сторон заготовки, замеры производятся в трех-четырех местах. Определив припуск, подлежащий удалению в различных местах второй широкой обрабатываемой поверхности, производят ее опиливание.
Контроль отклонения от прямолинейности, плоскостности и параллельности производят периодически. Отклонение от параллельности сторон в процессе опиливания контролируют кронциркулем (Рис.3.26).
Рисунок 3.26. Определение отклонения от параллельности сторон
кронциркулем
На окончательно обработанной поверхности должны быть наведены продольные штрихи. Отклонение от параллельности, прямолинейности и плоскостности обработанных сторон и их толщина должны быть в пределах допусков, указанных на чертеже.
Если требуется опилить не только широкие, но и узкие стороны плиты (ребра), то опиливание начинают с более длинной боковой стороны. Затем обрабатывают короткие стороны под углом 90 ° с проверкой их от длинной (базовой) стороны. При обработке последней длинной стороны выдерживают параллельность с базовой плоскостью.
На рис.3.27 цифрами 1...6 обозначена последовательность опиливания сторон плоскопараллельной плиты.
Рисунок 3.27. Последовательность опиливания сторон
|
плоскопараллельной плиты
Опиливание сопряженных поверхностей - самый распространенный вид опиливания, так как предназначается для плоскостей, расположенных под углом 90 ° друг к другу или под иным углом, требуемым чертежом. Наружные углы обрабатывают плоскими напильниками, внутренние углы в зависимости от их размера можно обработать плоскими (с одним ребром без насечки), трехгранными, квадратными, ножовочными и ромбическими напильниками.
Обработку заготовки начинают с базовой, наиболее длинной или широкой плоскости. Эту поверхность (или ребро) опиливают окончательно, соблюдая все правила опиливания и проверки плоских поверхностей. Затем угольником предварительно проверяют угол между обработанной (базовой) и необработанной поверхностями. Выступающие места на обрабатываемой поверхности опиливают перекрестным штрихом, периодически проверяя угол угольником, а отклонение от плоскостности и прямолинейности - линейкой.
Если при проверке линейкой и угольником наблюдается равномерный просвет между проверяемой поверхностью и линейкой, проверяемым углом и ребром угольника, то работа по обеспечению точности обработки считается выполненной, после чего на обработанной поверхности необходимо нанести равномерные продольные штрихи.
Последовательность опиливания поверхностей, расположенных под внутренним углом, такая же, как и поверхностей, расположенных под внешним углом, т. е. вначале обрабатывают наиболее длинную или широкую (базовую) поверхность и по ней опиливают другую сопрягаемую поверхность. Особое внимание обращать на тщательность обработки мест сопряжения внутренних плоскостей угла, пользуясь для этого ромбическим или трехгранным напильником.
При закреплении заготовки в тисках для предохранения уже обработанной боковой поверхности от повреждения обязательно пользоваться накладными губками. Размер напильника выбирают с таким расчетом, чтобы он был длинней опиливаемой поверхности не менее чем на 150 мм.
|
Если параметр шероховатости поверхности на чертеже обрабатываемой детали не указан, опиливание производят только напильником с насечкой № 1 или № 2. Если требуется получить поверхность с более низкой шероховатостью, то опиливание заканчивают напильником с насечкой № 3 или № 4.
2) Опиливание криволинейных поверхностей,
пазов и отверстий
Криволинейные поверхности разделяются на выпуклые и вогнутые, они могут находиться как на плоских деталях типа шаблонов, планок, копиров, так и на цилиндрических, многогранных и другой формы стержнях и валиках. Обычно опиливание таких поверхностей связано со снятием больших припусков.
Прежде чем приступить к опиливанию, следует разметить заготовку или получить уже размеченную на предыдущих занятиях, удалить излишний металл путем вырезания ножовкой, срубания зубилом или высверливания с последующим вырубанием.
Выпуклые поверхности опиливают плоскими напильниками вдоль и поперек выпуклости. При движении напильника вперед вдоль выпуклости правая рука должна опускаться вниз, а носок напильника - подниматься вверх. При поперечном опиливании выпуклой поверхности напильнику сообщают кроме прямолинейного движения еще и вращательное.
Основной припуск удаляют напильником с грубой насечкой, не доходя до разметочной риски на 0,8...1,0 мм, после чего напильником с насечкой № 4 окончательно осторожно снимают оставшуюся часть припуска металла до риски или требуемого размера. Контроль опиленной заготовки производят шаблонами, угольником и штангенциркулем.
Приемы опиливания наружных криволинейных и цилиндрических поверхностей показаны на рис.3.28 а... е.
Опиливание вогнутых поверхностей начинают с разметки на заготовке контура детали. Большую часть металла (припуска) можно удалить выпиливанием ножовкой, придав впадине заготовки форму треугольника. Затем полукруглыми или круглыми напильниками спиливают излишний металл до нанесенной разметочной риски. Профиль сечения круглого или полукруглого напильника выбирают таким, чтобы его радиус был меньше, чем радиус опиливаемой поверхности.
Рисунок 3.28. Приемы опиливания наружных криволинейных поверхностей:
|
а - последовательность обработки:
1 - срезание излишнего металла ножовкой; 2 - опиливание черновое на многогранник; 3 - опиливание окончательное по шаблону;
б - опиливание выпуклой поверхности (носка молотка); в - опиливание стержня, закрепленного вертикально; г - опиливание стержня, закрепленного горизонтально; д - опиливание цилиндрического стержня, закрепленного в ручных тисках; е - опиливание стержня на конус, закрепленного в ручных тисках.
При опиливании сочетаются два движения напильника - прямолинейное и вращательное, т. е. каждое движение напильника вперед сопровождается небольшим поворотом его правой рукой на 1/4 оборота вправо или влево. Все приемы опиливания и проверки полученной поверхности аналогичны обработке выпуклых поверхностей.
Приемы опиливания вогнутых криволинейных поверхностей показаны на рис.3.29 а... г.
Рисунок 3.29. Приемы опиливания вогнутых криволинейных поверхностей:
а - последовательность обработки:
1 - срезание излишнего металла ножовкой; 2 - опиливание круглым напильником;
б - опиливание вогнутой поверхности большого радиуса кривизны; в - опиливание вогнутой поверхности малого радиуса кривизны; г - проверка опиленной поверхности шаблоном
3) Распиливание отверстий и пазов
Распиливание отверстий и пазов (Рис.3.30)в целях придания им нужной формы является одной из разновидностей обработки внутренних прямолинейных и криволинейных поверхностей.
Распиливание выполняют напильниками соответствующей формы сечения, например, круглые отверстия обрабатывают круглыми и полукруглыми напильниками; трехгранные отверстия - трехгранными, ножовочными и ромбическими напильниками и т. п.
Подготовка к распиливанию начинается с разметки и накернивания разметочных рисок, сверления по разметочным рискам отверстий и вырубки проймы (удаления излишнего металла из будущего отверстия).
Рисунок 3.30. Приемы распиливания отверстий и пазов:
а - разметка и обсверливание контура; б - сверление, вырубка и распиливание проема;
|
в - распиливание отверстия молотка; г - распиливание квадратных отверстий воротка;
д - распиливание зева гаечного ключа; е - распиливание шестигранного отверстия ключа
Шабровка
Шабровкой называется слесарная отделочная операция, используемая для выравнивания и пригонки плоских и криволинейных (чаще цилиндрических) поверхностей для получения плотного прилегания.
Шабровку применяют для обработки и ремонта трущихся поверхностей сопрягаемых деталей - станин, суппортов, подшипников скольжения и поверхностей проверочных инструментов - плит, угольников, линеек и др. Так же, как и опиливание, шабровка - одна из наиболее распространенных слесарных операций.
В практике слесарных, слесарно-сборочных и ремонтных операций объем шабровочных работ достигает 20...25 %.
Широкое применение шабровки объясняется особыми свойствами полученной поверхности, которые состоят в следующем:
- шабреная поверхность, в отличие от шлифованной или полученной абразивной притиркой, более износостойкая, так как не имеет шаржированных в ее поры (риски, царапины) остатков абразивных зерен, ускоряющих процесс износа трущихся поверхностей;
- шабреная поверхность лучше смазывается и дольше сохраняет смазывающие вещества благодаря наличию так называемой разбивки этой поверхности на пятна (чередование выступающих и углубленных мест), что также повышает ее износостойкость и снижает коэффициент трения;
- шабреная поверхность позволяет применить самый простой и доступный способ оценки ее качества - по числу пятен на единицу площади.
Шабровке предшествует обработка резанием, например опиливание, шлифование, строгание, фрезерование и т. п.
Шабровка дает возможность получить поверхность с низкой шероховатостью (0,003...0,01 мм), так как за один проход шабером снимается слой металла толщиной 0,005...0,07 мм при чистовой обработке и не более 0,01...0,03 мм при предварительной обработке.
Сущность шабровки заключается в том, что с выпуклых (возвышающихся) мест предварительно обработанной поверхности заготовки режущим инструментом - шабером соскабливаются очень тонкие частицы металла.
Шаберы - это металлические стержни различной формы с режущими кромками, изготовленные из углеродистой инструментальной стали марок от У10 до У13 и закаленные до твердости 56...64 HRC.
Иногда шаберы изготовляют оснащенными пластинами из быстрорежущей стали или твердого сплава
Шаберы подразделяют (Рис.3.31):
- по форме режущей части:
плоские, трехгранные, фасонные и специальные;
- по количеству режущих граней:
односторонние и двусторонние;
- по конструкции:
|
цельные и со вставными пластинами.
Форму и геометрические параметры режущих кромок шабера выбирают в зависимости от формы и размеров обрабатываемой поверхности и свойств материала заготовки.
Рисунок 3.31. Шаберы:
а - плоский односторонний;
б - плоский двусторонний;
в - с изогнутым концом;
г - трех- и четырехгранные
Так, для шабровки плоских поверхностей применяют плоские шаберы с прямолинейной или радиусной режущей кромкой, для криволинейных и внутренних (вогнутых) поверхностей - трехгранные и фасонные шаберы.
Шаберы с прямолинейной режущей кромкой удобней применять при обработке краев заготовки, так как при работе он не соскочит с заготовки и не повредит ее поверхности. При обработке остальной части заготовки шабер с прямолинейной режущей кромкой менее удобен, так как боковые углы лезвия могут оставить на поверхности глубокие царапины.
В этом случае удобней применять шаберы с радиусными (дугообразными) режущими кромками, которые обеспечивают более низкую шероховатость шабруемой поверхности, чем при работе шабером с прямолинейной режущей кромкой.
Геометрические параметры шаберов зависят от вида обработки, обрабатываемого материала и угла установки инструмента по отношению к обрабатываемой поверхности.
Торцовую поверхность шабера затачивают под углом 60... 100 ° по отношению к оси инструмента, образуя угол заострения β, который равен: при грубой обработке - 60...75 °, при чистовой - 90°, а для ocoбo чистых работ - 90......100°.
Обрабатываемый материал на выбор угла заострения β плоского шабера влияет следующим образом:
- при обработке чугуна и бронзы β = 90...100°;
- стали - 75...90°;
- мягких металлов — 35...40 °.
Выбор длины режущей кромки и радиуса ее закругления также зависит от твердости обрабатываемого материала и требуемой шероховатости поверхности. Чем тверже материал, тем уже режущая кромка и меньше радиус закругления.
Длина режущей кромки зависит также от заданного числа и размеров пятен на единицу площади. Так, для предварительной (грубой) шабровки выбирают шабер с широким лезвием - 20...30 мм; для точной - 15...20 мм; для самой точной шабровки - 5... 12 мм. Для окончательной (чистовой) шабровки радиус режущего лезвия берется большим, чем для черновой, так как в этом случае получается наименьшее отклонение от плоскости поверхности.
Для обработки криволинейных вогнутых поверхностей применяют трехгранные шаберы, на боковых сторонах которых прорезаны продольные канавки для облегчения заточки. Угол заострения трехгранного шабера β = 60...70°.
Подготовка заготовки к шабровке заключается в опиливании (или в другом виде обработки) нужной поверхности, оставляя как можно меньший припуск, который в зависимости от длины и ширины поверхности равен 0,1...0,4 мм. Перед шабровкой поверхность очищают, промывают, протирают, затем наносят на нее краску.
Окрашивание проверочной плиты проводят шабровочной краской, представляющей собой смесь машинного масла (или автола на керосине) с сажей, лазурью или ультрамарином, которую наносят тампоном на проверочную плиту ровным тонким слоем (Рис.3.32 а). Затем обрабатываемую заготовку плавно опускают на проверочную плиту и медленно передвигают круговыми движениями в разных направлениях, используя всю поверхность плиты, затем заготовку с плиты осторожно снимают (Рис.3.32 б ). При шабровке тяжелых заготовок их оставляют на месте, а на обрабатываемые поверхности накладывают проверочный инструмент для определения выступающих мест (Рис.3.32 г).
-
Рисунок 3.32. Нанесение краски на пришабриваемую поверхность
На предварительно обработанные поверхности краска ложится равномерно, на плохо подготовленные - неравномерно. В небольших углублениях скапливается краска, а в местах более углубленных ее вообще не будет. Так, на подготовленной для шабровки поверхности возникают белые пятна - наиболее углубленные места, не покрытые краской, темные пятна - менее углубленные, в них скопилась краска, серые пятна - наиболее выступающие, на них краска ложится тонким слоем (Рис.3.32 в ).
Процесс шабровки заключается в постепенном удалении металла с окрашенных участков (серые пятна).
При работе шабер следует держать правой рукой, а ладонью левой руки охватить инструмент посередине, поджав книзу четыре пальца (Рис.3.33 а). Принять рабочее положение относительно тисков или обрабатываемой заготовки как при опиливании и установить шабер под углом 30...40 ° к шабруемой поверхности. Рабочим ходом при шабровке является движение вперед, т. е. от себя. При движении назад (холостой ход) шабер приподнимают. Шабрить следует не сгибаясь при свободном положении корпуса.
Шабровка производится за несколько переходов: черновое (предварительное), получистовое (точечное) и чистовое (отделочное). В особых случаях проводят точную и тонкую шабровки.
В начале шабровки перемещение инструмента (длина хода) равно 15...20 мм, а затем по мере выравнивания поверхности оно уменьшается до 2...5 мм.
Направление рабочего хода каждый раз надо изменять так, чтобы полученные штрихи пересекались между собой под углом 45...60° (Рис.3.33 б).
Рисунок 3.33. Шабрение плоской поверхности
Начинать шабровку плоской поверхности надо с наиболее удаленного края, постепенно приближаясь к ближнему краю. После каждого цикла шабровки обрабатываемую поверхность надо насухо протереть, вновь проверить на краску и продолжать шабровку до тех пор, пока вся пришабриваемая поверхность не покроется равномерно чередующимися пятнами краски. Предварительная шабровка считается удачной, если пятна краски равномерно располагаются на всей поверхности.
Окончательная шабровка заключается в расшабривании крупных пятен пополам или на несколько равных по размеру и форме частей, а продолговатых - на более мелкие в поперечном направлении. Чем точнее требуется пришабрить поверхность, тем более тонкий слой краски должен быть наложен на проверочную плиту, взят более узкий шабер (8... 10 мм), а длина рабочего хода не должна быть более 4...5 мм.
Качество шабровки определяют по числу пятен, приходящихся на единицу обработанной поверхности, для чего служит контрольная рама с квадратным окошком 25×25 мм, которую накладывают на пришабренную поверхность и считают число пятен (Рис.3.33 в).
Подсчет числа пятен проводят в 2...4 местах проверяемой поверхности. При черновой шабровке число пятен должно быть не менее 10, при получистовой - 12, при чистовой - 15, при точной - 20, при тонкой - 25.
Притирка
Притиркой называется обработка поверхностей с помощью мелкозернистых шлифовальных порошков или паст, нанесенных на твердую поверхность инструмента - притира, или на сопрягаемую поверхность.
Припуск, оставляемый на притирку, составляет 0,02...0,05 мм, а шероховатость поверхности после притирки достигает 0,001...0,002 мм. Поверхность притирают после окончательной механической обработки - шлифования, точного точения, фрезерования, развертывания, шабрения. Детали могут быть закаленные и термически не обрабатываемые. Детали, подвергающиеся притирке, могут иметь плоскую, цилиндрическую и фасонную поверхности.
В машиностроении притирке подвергают поверхности арматуры, пробки и корпуса кранов, клапаны и седла двигателей и т. п. Особенно широко распространена притирка, а также более точная обработка - доводка, в инструментальном производстве.
Существуют два технологических способа выполнения притирки.
Первый способ состоит в том, что сопрягаемые детали притирают одну по другой. Между притираемыми деталями помещают абразивные материалы в виде порошков или паст. Таким образом притирают, например, клапаны к седлам, пробки к корпусам кранов и др.
Второй способ состоит в притирке каждой из двух сопрягаемых деталей по специальной третьей детали - притиру. Так притирают плиты, крышки и фланцы в плотных соединениях, рабочие поверхности линеек, шаблонов, калибров и т. п.
Притирочные материалы подразделяются на две группы: твердые и мягкие.
К твердым относятся материалы, твердость которых выше твердости закаленной стали. Это шлифпорошки и микропорошки из наждака, корунда, электрокорундов, карбида кремния зеленого, карбида бора и синтетических алмазов.
К мягким относятся материалы, твердость которых ниже твердости закаленной стали. Это абразивные порошки из окиси хрома, окиси железа (крокуса), венской извести и др. Особенностью некоторых мягких абразивных материалов, главным образом окиси хрома, является их способность оказывать на обрабатываемую поверхность помимо механического еще и химическое воздействие.
Входящие в состав многих паст компоненты типа олеиновой и стеариновой кислот энергично разрушают пленки окислов, непрерывно образующихся на поверхности детали, ускоряя процесс притирки. Происходит химико-механический процесс удаления металла. Из мягких абразивных материалов наиболее широко применяют пасты ГОИ (Государственный оптический институт), изготовляемые из окиси хрома (65...80%). Различают пасты ГОИ трех составов: грубую, среднюю и тонкую.
Смазывающие вещества - керосин, машинное масло, скипидар, животные жиры (сало), бензин и т. п. - способствуют ускорению обработки, сохранению остроты зерен, повышению точности и меньшей шероховатости обработанной поверхности.
Притиры - инструменты, которыми производят притирку деталей. В зависимости от формы и размеров обрабатываемых поверхностей притиры могут быть плоскими (плиты, бруски, диски), цилиндричес-кими для притир наружных и внутренних поверхностей; коническими и специальными.
Материал притира должен быть мягче материала обрабатываемой детали, чтобы зерна абразивного порошка вдавливались (шаржировались) в поверхность притира.
Притиры изготовляют из чугуна, бронзы, красной меди, свинца, стекла, фибры и твердых пород дерева. Для твердых абразивно-притирочных материалов чаще применяют чугунные притиры, реже - медные. Для паст ГОИ применяют стеклянные притиры.
Рисунок 3.34. Приемы притирки плоских поверхностей
Существуют два способа покрытия (шаржирования) притиров абразивным материалом: прямой и косвенный.
Прямой способ, когда абразивный порошок вдавливают в притир до работы с помощью стального закаленного валика (Рис.3.34 а). После шаржирования с притира удаляют остаток абразивного порошка и притир слегка смазывают.
Косвенный способ заключается в покрытии притира слоем смазки и посыпании его абразивным порошком. В процессе доводки зерна абразива вдавливаются в притир обрабатываемой деталью.
Притирка подразделяется на предварительную (черновую) и окончательную (чистовую).
Предварительную притирку ведут по плите с канавками (Рис.3.34 б), а окончательную - на гладкой плите (Рис.3.34 в).
Притираемую заготовку передвигают по плите круговыми движениями. Чтобы плита изнашивалась равномерно, притирку ведут по всей поверхности. Узкие стороны заготовок можно притирать пакетом, когда несколько одинаковых заготовок, соединенных винтами, струбциной (Рис.3.34 г)или заклепками (Рис.3.34 д)в пакет, обрабатывают аналогично широким плоскостям.
Притирку тонких и узких заготовок, например шаблонов, угольников, лекальных линеек, можно производить также с помощью чугунных или стальных направляющих кубиков, брусков, призм. Притираемую заготовку прижимают к бруску и вместе перемещают по притирочной плите (Рис.3.34 е).
Для притирки широких плоскостей тонких заготовок (шаблонов, угольников) их закрепляют на деревянном бруске мелкими гвоздями (или иным способом) и вместе с деревянным бруском перемещают по притирочной плите (Рис.3.34 ж).
Клепка
Клепкой называется процесс получения неразъемного соединения двух или нескольких деталей с помощью заклепок
Заклепочные соединения широко применяют при изготовлении различных металлических конструкций, ферм, балок, емкостей, в самолетостроении, судостроении и т. п. Закладная головка создается при изготовлении заклепки, а замыкающая - при расклепывании стержня заклепки (Рис.3.35 а, б).
Рисунок 3.35. Элементы заклепочного соединения:
а - с потайной головкой; б - с полукруглой головкой;
l - длина стержня заклепки; d - диаметр стержня заклепки; s - суммарная толщина склепываемых листов
При изготовлении заклепок между стержнем и головкой делают закругление (галтель), что увеличивает прочность заклепки и герметичность шва.
В соответствии с назначением заклепки имеют различные формы головок (Рис.3.36 а... е).
Рисунок 3.36. Основные типы заклепок:
а - с полукруглой высокой головкой; б - с полукруглой низкой головкой;
в - с плоской головкой; г - с потайной головкой; д - с полупотайной головкой;
е - взрывная заклепка.
В зависимости от материала соединяемых деталей заклепки изготовляют из углеродистой, легированной, нержавеющей стали, цветных металлов и сплавов, алюминия. Заклепки должны быть изготовлены из того же металла, что и соединяемые детали.
Заклепки, расположенные в определенном порядке в один или несколько рядов для получения неразъемного соединения, образуют заклепочный шов.
Заклепочные швы делятся на три типа:
- прочные, от которых требуется только механическая прочность;
- плотно-прочные и плотные, от которых требуется герметичность соединения.
В зависимости от расположения соединяемых деталей различают соединения:
- нахлесточные (Рис.3.37 а), когда один край одного листа накладывается на другой;
- стыковые, когда соединяемые детали своими торцами плотно примыкают друг к другу и соединяются с помощью одной (Рис.3.37 б)илидвух (Рис.3.37 в)накладок.
Рисунок 3.37. Виды заклепочных швов.
а - нахлесточный; б - стыковой с одной накладкой;
в - стыковой с двумя накладками; г - многорядный.
В заклепочном соединении заклепки могут быть расположены в один, два и более рядов, в соответствии с чем швы делят на одно, двух- и многорядные, параллельные и шахматные (Рис.3.37 г).
Инструментами и приспособлениями приручной клепке являются слесарные молотки с квадратным бойком, поддержки, обжимки, натяжки и чеканы.
Молоток выбирают в зависимости от диаметра заклепки:
Диаметр заклепки, мм..... 2...2,5 3...3.5 4...5 6...8
Масса молотка, г ..... 100 200 400 500
Поддержка 1 (Рис.3.38) служит опорой при расклепывании стержня заклепок и должна быть в 3...5 раз массивнее молотка.
Обжимка 2 служит для придания требуемой формы замыкающей головке заклепки после осадки. На рабочем конце обжимки должно быть углубление по форме головки заклепки.
Рисунок 3.38. Применение поддержки и обжимки при клепке
Натяжка представляет собой стержень с отверстием на конце диаметром на 0,2 мм больше диаметра стержня заклепки.
Чекан - слесарное зубило с плоской рабочей частью, применяется для создания герметичности заклепочного шва, достигаемой подчеканкой замыкающей головки и края листов.
Форма рабочей поверхности поддержки зависит от конструкции скрепляемых деталей, диаметра стержня заклепки и от метода клепки.
Различают два метода клепки:
- прямой (Рис.3.38 а)с двусторонним подходом, когда имеется свободный доступ как к закладной, так и к замыкающей головке;
- обратный (Рис.3.38 б) с односторонним подходом, когда доступ к замыкающей головке невозможен.
Прямой метод клепки характеризуется тем, что удары молотком наносят по стержню со стороны вновь образуемой, замыкающей головки.
При этом методе необходимо:
- разметить шов, совместить детали и сжать их вместе ручными тисками или струбцинами;
- просверлить по разметке отверстия под заклепки в обеих деталях одновременно;
- для заклепок с потайными головками зенковать места (гнезда) под головки;
- ввести в отверстие снизу стержень заклепки (Рис.3.39) и под закладную головку подвести массивную поддержку 2;
Рисунок 3.39. Приемы выполнения клепки
1 - натяжка; 2 - поддержка; 3 - обжимка.
- уплотнить детали в месте склепки натяжкой 1 (Рис.3.39 а);
- осадить (расклепать) стержень крайней заклепки бойком молотка (Рис.3.39 б);
- окончательно оформить замыкающую головку с помощью обжимки 3.
Обратный метод клепки характеризуется тем, что удары молотком наносят по закладной головке через оправку 3 с внутренней сферической поверхностью (Рис.3.39 в).
При этом методе стержень заклепки вводят сверху, поддержку 2 с требуемой формой рабочей поверхности подводят под стержень заклепки и формируют замыкающую головку. Этот метод применяют только при затрудненном вводе заклепки снизу и отсутствии доступа к замыкающей головке.
Длина стержня заклепки зависит от толщины скрепляемых листов (пакета) и формы замыкающей головки. Для образования потайной замыкающей головки стержень должен выступать на длину, равную 0,8...1,2 диаметра заклепки, для образования полукруглой замыкающей головки стержень должен выступать на длину, равную 1,2...1,5 диаметра заклепки (см. рис.3.35).
Диаметр заклепки выбирают в зависимости от толщины пакета склепываемых листов по формуле
Диаметр отверстия под заклепку должен быть больше диаметра заклепки на 0,1...0,2 мм при точной сборке и на 0,3...1,0 мм при грубой сборке.
При выборе диаметра сверла для отверстия под заклепку можно пользоваться следующими данными:
Диаметр заклепки, мм... 2,0 2,3 2,6 3,0 3,5 4,0 5,0 6,0 7,0 8,0
Диаметр сверла, мм:
точная сборка.... 2,1 2,4 2,7 3,1 3,6 4,1 5,2 6,2 7,2 8,2
грубая сборка.... 2,3 2,6 3,1 3,5 4,0 4,5 5,7 6,7 7,7 8,7
Качество клепки определяют наружным осмотром, плотность прилегания соединенных деталей проверяют щупом, форму и размеры замыкающих головок, а также расстояние между ними - шаблонами.
Наиболее характерные виды брака при клепке: смещение и изгиб замыкающей головки, прогиб металла, недотяжка металла, неплотное прилегание замыкающей головки, малый размер замыкающей головки, рваные краяголовки и т. п.
Сверлильные работы
При слесарной обработке заготовок часто используют различные способы обработки отверстий на сверлильных станках или с помощью ручных сверлильных машин-дрелей. Наиболее распространенные операции обработки на сверлильных станках показаны на рис.3.40 а... л.
Рисунок 3.40. Работы, выполняемые на сверлильных станках:
а - сверление; б - рассверливание; в - зенкерование; г - растачивание;
д - зенкование; е - развертывание; ж - проглаживание;
з - нарезание внутренней резьбы; и - цекование (подрезка) торцов;
к - вырезание дисков (шайб); л - проточка внутренних канавок
Сверление
Сверлением называется процесс образования отверстия в сплошном материале режущим инструментом - сверлом. Точность обработки не превышает 11... 12-го квалитетов и шероховатость поверхности Rz = 25...80 мкм.
Сверление применяют для получения неответственных отверстий, служащих для облегчения деталей, отверстий под крепежные болты, заклепки, шпильки и т. п., а также отверстий, предназначенных для дальнейшей обработки: рассверливания, зенкерования, развертывания, нарезания резьбы.
Рассверливанием называется операция по увеличению диаметра ранее просверленного отверстия сверлом большего диаметра. Обычно ее выполняют, когда в сплошном металле нужно получить отверстие диаметром более 25 мм. Разница диаметров первого и второго сверла составляет примерно 10...15 мм.
Наибольшее применение в мастерских получили вертикально-сверлильные станки, которые по габаритным размерам и методу установки делятся на две группы: настольно-сверлильные, устанавливаемые на верстаках или специальных столах, и вертикально-сверлильные, устанавливаемые на фундаментах или виброопорах.
Настольно-сверлильные станки моделей НС-12А и 2М112 предназначаются для сверления в небольших заготовках отверстий диаметром не более 12 мм.
Основные узлы и детали настольно-сверлильного станка модели НС-12А показаны на рис.3.41.
Подача инструмента осуществляется вручную, путем вращения штурвала ручкой подачи (рукоятки) 13. Для изменения частоты вращения шпинделя служат ступенчатые шкивы 2, 3 и клиновидный ремень, соединяющий их между собой. Изменение направления вращения шпинделя (реверс) совершает вилка 5 барабанного переключателя электродвигателя.
Вертикально-сверлильные станки моделей 2118А, 2Н125, 2А125, 2Н135и других более современных моделей применяются для более тяжелых сверлильных работ.
Основные узлы и детали вертикально-сверлильного станка модели 2Н135 показаны на рис.3.42.
Рисунок 3.41. Настольно-сверлильный станок НС-12А:
1 - шпиндельная бабка; 2 - шкив шпинделя; 3 - ступенчатый шкив; 4 - электродвигатель;5 - вилка; 6 - плита электродвигателя; 7 - колонна; 8 - кронштейн; 9 - основание (плита); 10 - рукоятка для зажима шпиндельной бабки; 11 - рукоятка для подъема шпиндельной бабки; 12 - шпиндель; 13 - штурвал ручного движения подачи 14 - упор; 15 – стол
Рис.3.42 Вертикально-сверлильный станок 2Н135:
1 - фундаментная плита; 2 - стол; 3 - шпиндель; 4 - коробка скоростей и подач; 5 - крышка кожуха; 6 - электродвигатель; 7 - штурвал ручного движения подачи; 8 - станина; 9 - ручка подъема стола
Осевая подача инструмента осуществляется с помощью коробки подач 4, установленной на станине станка 8. Изменение частоты вращения шпинделя осуществляется коробкой скоростей, расположенной внутри шпиндельной головки, которая передает вращение от электродвигателя 6 на шпиндель 3. Обрабатываемая заготовка устанавливается на столе 2, который в зависимости от ее габаритов (высоты) может подниматься и опускаться при вращении рукоятки стола 9.
В тех случаях, когда заготовку невозможно установить на станке (при ремонте) или когда отверстия расположены в труднодоступных местах, сверление осуществляют с помощью ручных, электрических илипневматических сверлильных машин (дрелей), а также коловоротов, трещоток и прочих устройств.
Ручная сверлильная машина (дрель) применяется для сверления отверстий диаметром до 10 мм и представляет собой зубчатый механизм, передающий вращательное движение рукоятки 5на шпиндель 1 с закрепленным на нем сверлом (Рис.3.43).
Рис.3.43. Ручная сверлильная
машина (дрель):
1 - шпиндель с патроном; 2 - вал;
3, 6, 7, 8 - зубчатые колеса;
4 - упор-нагрудник; 5 - рукоятка
Приемы сверления ручной сверлильной машиной на подставке приведены на рис.3.44 а; а в тис
|
|
Особенности сооружения опор в сложных условиях: Сооружение ВЛ в районах с суровыми климатическими и тяжелыми геологическими условиями...
Типы оградительных сооружений в морском порту: По расположению оградительных сооружений в плане различают волноломы, обе оконечности...
Эмиссия газов от очистных сооружений канализации: В последние годы внимание мирового сообщества сосредоточено на экологических проблемах...
Своеобразие русской архитектуры: Основной материал – дерево – быстрота постройки, но недолговечность и необходимость деления...
© cyberpedia.su 2017-2024 - Не является автором материалов. Исключительное право сохранено за автором текста.
Если вы не хотите, чтобы данный материал был у нас на сайте, перейдите по ссылке: Нарушение авторских прав. Мы поможем в написании вашей работы!