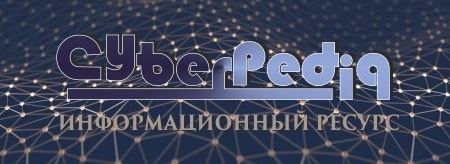
Таксономические единицы (категории) растений: Каждая система классификации состоит из определённых соподчиненных друг другу...
Индивидуальные и групповые автопоилки: для животных. Схемы и конструкции...
Топ:
Марксистская теория происхождения государства: По мнению Маркса и Энгельса, в основе развития общества, происходящих в нем изменений лежит...
Техника безопасности при работе на пароконвектомате: К обслуживанию пароконвектомата допускаются лица, прошедшие технический минимум по эксплуатации оборудования...
Проблема типологии научных революций: Глобальные научные революции и типы научной рациональности...
Интересное:
Распространение рака на другие отдаленные от желудка органы: Характерных симптомов рака желудка не существует. Выраженные симптомы появляются, когда опухоль...
Наиболее распространенные виды рака: Раковая опухоль — это самостоятельное новообразование, которое может возникнуть и от повышенного давления...
Как мы говорим и как мы слушаем: общение можно сравнить с огромным зонтиком, под которым скрыто все...
Дисциплины:
![]() |
![]() |
5.00
из
|
Заказать работу |
|
|
Слесарные работы относятся к процессам обработки металлов резанием. Их осуществляют как вручную, так и с помощью механизированного инструмента. Цель слесарных работ -обработать поверхность заготовки согласно заданным рабочим чертежом размеров, форм и шероховатости.
Слесарь должен уметь выполнять следующие работы:
- рубку и разрубку зубилом вручную;
- опиловку и зачистку заусенцев, облоя и сварных швов;
- нарезку заготовок из прутка и листа ручными ножницами и ножовками;
- разметку простых деталей по шаблону, очистку и промывку деталей;
- сверление отверстий по разметке, кондуктору на сверлильном станке и дрелью;
- снятие фасок и нарезание резьбы.
Слесарь должен знать наименование и название простого рабочего инструмента, устройство слесарных тисков, правила работы с ручными ножницами и ножовками, пневматическими и электрическими машинками, на настольном сверлильном станке, крепежные детали, маркировку и наименование обрабатываемых материалов.
Технология слесарной обработки содержит ряд операций:
- плоскостная и пространственная разметка;
- рубка, правка и гибка металла;
- разрезка листового и пруткового металла;
- опиливание, шабрение, притирка, доводка, пригонка и припасовка поверхностей;
- обработка отверстий на сверлильных станках и с помощью дрелей;
- пайка, лужение и склеивание.
Рабочий инструмент слесаря подразделяется на ручной и механизированный. Типовой набор ручного инструмента для слесарных работ делится на четыре группы:
1) режущий инструмент - напильники, ножовки, зубила, сверла, метчики, плашки, шаберы, развертки, абразивный инструмент (бруски, шкурки, пасты) и др.;
|
2) вспомогательный инструмент - молотки, керны, бородки, чертилки, циркули, воротки, плашкодержатели и др.;
3) слесарно-монтажный.инструмент - гаечные ключи, отвертки, плоскогубцы, съемники и др.;
4) измерительный и контрольный инструмент - измерительные и лекальные линейки, кронциркули, нутромеры, штангенциркули, микрометры, угольники, угломеры и др.
Подробное описание и способы пользования слесарным инструментом даны при изучении конкретного вида работы.
Разметка
Разметкой называется операция нанесения на обрабатываемую заготовку или на поверхность материала, предназначенного для получения заготовки (лист, пруток, полоса и т. п.) разметочных линий (рисок).
Основное назначение разметки заключается в указании границ, до которых надо обрабатывать заготовку на слесарном участке. Разметку применяют в единичном, опытном, мелкосерийном производстве, она также необходима в инструментальном производстве при изготовлении различных шаблонов, штампов, приспособлений. А также при изготовлении деталей большими сериями и в массовом производстве, когда применяют специальные приспособления, кондуктора, специальные и комбинированные инструменты, например набор фасонных фрез.
Разметка разделяется на плоскостную и пространственную.
Разметка плоскостная
Плоскостная разметка применяется для геометрических построений и очертания границ контура детали, нанесения межосевых расстояний отверстий на плоских поверхностях листового материала или заготовок. В этих случаях ограничиваются нанесением рисок только на одной плоскости. Погрешность размеров при плоскостной разметке, как бы аккуратно ни наносились разметочные риски и как бы тонки они ни были, колеблется от 0,2 до 0,5 мм.
Инструмент и приспособления, применяемые при разметке, делятся на следующие основные группы:
1) инструмент для нанесения и накернивания рисок:
- чертилки круглые (Рис.3.1 а);
|
- с отогнутым концом (Рис.3.1 б);
- пружинные циркули (Рис.3.1 в);
- рейсмасы, разметочные штангенциркули, штангенрейсмасы;
- кернеры (Рис.3.1 г).
2) инструмент для нахождения центров деталей:
- кернер-центроискатель;
- угольник-центроискатель;
- транспортир-центроискатель;
- специальные приспособления для разметки деталей с большими отверстиями;
3) приспособления для установки, выверки и закрепления разметочных заготовок:
- подкладки и домкраты;
- специальные поворотные приспособления;
- вертикальные стойки для измерительных линеек;
- дополнительные плоскости к разметочной плите;
- делительные приспособления и центровые бабки.
а) б) в) г)
Рисунок 3.1. Простейший инструмент для плоскостной разметки
Разметочные плиты, на которых выполняют разметочные работы, отливают из серого чугуна. Они имеют коробчатую форму и снабжены внутри ребрами жесткости. Верхнюю рабочую поверхность и боковые стороны точно обрабатывают и затем шабрят.
Поверхность плиты всегда должна быть сухой и чистой. После работы плиту протирают тряпкой, смазывают маслом и накрывают деревянным щитом-крышкой. По плите нельзя передвигать размечаемые заготовки, в результате чего могут появиться царапины и забоины.
Применяемые при разметке инструменты и приспособления передвигают по плите плавно.
Подготовка заготовки к разметке.
Перед разметкой очистить заготовку от пыли, грязи, окалины, следов коррозии стальной щеткой, шлифовальной шкуркой и т. п. Измерить размеры заготовки и сравнить их с размерами детали по чертежу.
Изучая чертеж размечаемой детали, наметить последовательность разметки (установку заготовки на плите, ее выверку в горизонтальной и вертикальной плоскости). Определить поверхности (базы) заготовки, от которых следует откладывать размеры при разметке (основание детали, отверстие, ось симметрии и т. п.).
Подготовить поверхности заготовки к окрашиванию. Заготовки из листового, полосового и круглого материала обязательно должны быть отрихтованы (выравнены) на специальной плите ударами молотка или под прессом.
Окрашивание поверхностей производят различными составами. Поверхности чисто обработанных заготовок (напильником, шлифовальной шкуркой или иным способом) окрашивают раствором медного купороса, полученным путем растворения двух-трех чайных ложек купороса в стакане воды. После высыхания раствора на поверхности заготовки остается тонкий слой меди, на который хорошо наносятся разметочные риски.
|
Для окрашивания можно применять быстросохнущие лаки и краски. Окрашивание мелких заготовок производят, держа их в левой руке в наклонном положении, а кистью наносят тонкий и равномерный слой краски или раствора (рис.21 а). При разметке черных необработанных заготовок, полученных путем отливки, ковки или штамповки, после очистки от окалины или формовочной земли их покрывают мелом, разведенным в воде до густоты молока. Для большей прочности и быстрого высыхания в раствор добавляют жидкий столярный клей и сиккатив.
Приемы плоскостной разметкипоказаны нарис.3.2 б...ж.
Рисунок 3.2. Приемы плоскостной разметки:
а - нанесение краски на заготовку; 6 - нанесение рисок с помощью линейки; в - нанесение рисок с помощью угольника; г - установка чертилки; д - разметка окружностей и дуг; е - применение чертилки с отогнутым концом; ж - разметка по шаблону; з - накернивание разметочных линий (рисок).
Разметочные линии наносят в следующем порядке:
- сначала проводят все горизонтальные риски;
- затем - все вертикальные;
- после этого - наклонные;
- последними наносят дуги, окружности, закругления и
сопряжения.
Если базой являются центровые риски, то разметку начинают с них, а затем, пользуясь ими, наносят все остальные риски. Вычерчивание дуг в последнюю очередь дает возможность проверить точность расположения прямых линий: если линии нанесены точно, дуга замкнет их и сопряжение получится плавным.
Разметку можно считать законченной, если изображение на плоскости заготовки полностью соответствует чертежу.
Прямые линии наносят чертилкой, которая должна быть наклонена в сторону от линейки и по направлению перемещения чертилки.
|
Линейку или угольник плотно прижимают к заготовке левой рукой, а чертилкой, как карандашом, не прерывая движения, проводят риски необходимой длины.
Риски проводят только один раз, иначе может получиться раздвоенная риска. Если риска нанесена плохо, ее закрашивают и проводят вновь. Разметку параллельных, перпендикулярных и наклонных рисок, деление углов и окружности на равные части, построение сопряжений и овалов выполняют по методам, применяемым в курсе черчения.
При изготовлении партии одинаковых деталей применяют разметку по шаблонам. В этом случае из листовой стали изготовляют шаблон, конфигурация и размеры которого точно соответствуют детали. Затем шаблон накладывают на подготовленную для разметки поверхность заготовки и чертилкой обводят его контур.
Отыскание центров окружностей осуществляют с помощью центроискателей и центронаметчиков.
Керновка разметочных рисок.
Убедившись в правильности выполнения разметки, все линии накернивают для того, чтобы они не стерлись при обработке заготовки и чтобы при последующем сверлении имелось центровое, более глубокое, отверстие для предварительного направления сверла.
Керны (конусные углубления) должны быть неглубокими и разделяться разметочной риской пополам. При работе кернер берут тремя пальцами левой руки, ставят острием точно на разметочную риску так, чтобы острие кернера было строго на середине риски, слегка наклоняя от себя, и прижимают к намеченной точке, затем быстро ставят его перпендикулярно размечаемой плоскости и наносят по головке кернера легкий удар разметочным молотком массой 100...200 г (Рис.3.2 з). В такой же последовательности делают керны по всем разметочным рискам.
Расстояние между двумя соседними углублениями должно быть:
- при накернивании длинных рисок - 25...30 мм;
- при накернивании коротких рисок - 10...15 мм;
- на закруглениях, сопряжениях и других криволинейных участках - 5...10 мм.
Линии малых окружностей накернивают в четырех взаимно перпендикулярных точках; линии больших окружностей - в 6...8 местах (на пересечениях и сопряжениях риски накернивать обязательно).
Разметка пространственная
Пространственная разметка применяется для графических построений, осуществляемых на поверхности объемных заготовок, расположенных в разных плоскостях под различными углами друг к другу.
По своим приемам пространственная разметка существенно отличается от плоскостной. Трудность пространственной разметки заключается в том, что приходится не только размечать отдельные элементы на одной поверхности (стороне) детали, а увязывать разметку этих отдельных поверхностей (плоскостей, осей отверстий, их соосности, углов наклона и т. п.) между собой. Практикант, приступающий к пространственной разметке, должен быть знаком с основами проекционного черчения и чтением рабочих машиностроительных чертежей деталей средней сложности.
|
При разметке нужно выбрать базовую поверхность, от которой можно было бы разметить наибольшее количество осей и плоскостей, установить главные оси заготовок, количество положений заготовки на плите и их последовательность, увязать разметку этих поверхностей и осей между собой.
Пространственную разметку производят на разметочной плите, установив и закрепив заготовку на ней таким образом, чтобы каждая плоскость или ось детали была параллельна или перпендикулярна общей плоскости разметочной плиты. Для установки и выверки на разметочной плите заготовки пользуются различными призмами, опорными прокладками, домкратиками, разметочными кубиками и специальными (часто поворотными) приспособлениями.
Подготовка заготовки к разметке состоит из очистки поверхности металлической щеткой или другими способами, установки деревянных пробок в отверстия (проемы, пазы) с обоих концов заготовки, окраски мест, на которые будут наноситься разметочные риски меловым раствором (на необработанных поверхностях). Окраску заготовки производят около разметочной плиты.
Установка заготовки на плите производится следующим образом. При установке только первое положение заготовки на плите является независимым, а все остальные положения зависят от первого. Его выбирают так, чтобы было удобно начать разметку от выбранной базы, параллельной плоскости разметочной плиты. Заготовку устанавливают в требуемом положении с помощью подкладок, клиньев, домкратиков или непосредственно на плоскость плиты, на угольники, разметочные ящики, призмы. Установка должна быть прочной (без качания)
Приемы пространственной разметки (Рис.3.3 а...г) в основном совпадают с приемами проекционного технического черчения. Принанесении рисок заготовка остается неподвижной, а рейсмас или штангенрейсмас перемещается относительно ее по разметочной плите. Риски проводятся с одного раза.
Разметочные линии наносят в следующем порядке: сначала проводят все горизонтальные риски со всех четырех или двух противоположных сторон заготовки, затем вертикальные и в заключение все окружности, дуги, сопряжения, фасоные и наклонные линии.
Кроме основных разметочных рисок параллельно им на расстоянии 5...7 мм проводят контрольные риски, которые служат для проверки установки заготовки на станке при дальнейшей обработке, атакже для возможности обработки в тех случаях, когда разметочная риска почему-то исчезла.
а) б)
в) г)
Рисунок 3.3. Приемы пространственной разметки:
а - нанесение краски на заготовку, установленную на призму; б - нахождение центра отверстия заготовки; в - нанесение рисок на заготовку; г - разметка заготовки, установленной на разметочном приспособлении (ящике)
Разметка вертикальных рисок может быть выполнена тремя способами:
1) без перекантовки заготовки, когда все вертикальные
разметочные риски можно нанести с помощью угольника;
2) поворотом заготовки на 90° с помощью рейсмаса или
штангенрейсмаса;
3) с применением разметочных ящиков, призм и угольников,
на которые крепят (с помощью скоб, струбцин, прижимов)
размечаемые заготовки.
При разметке отверстий в пустотелых заготовках в них забивают деревянные бруски, а на них - пластины из белой жести, латуни или свинца для нахождения положения центрового отверстия, а затем для опоры ножки циркуля. Дальше разметку ведут обычным способом
Керновку рисок при пространственной разметке производят так же, как и при плоскостной разметке.
Правка
Правка представляет собой первую операцию по подготовке заготовки или металла для нее к последующей технологической обработке. Она предназначается для устранения искажений формы (вмятин, выпучиваний, волнистости, коробления, искривления и т. п.) путем пластического деформирования.
Металл подвергается правке как в холодном, так и в нагретом состоянии. Правку можно выполнять ручным способом на стальной или чугунной плите или на наковальне, машинную правку производят на прессах и правильных вальцах.
Для правки применяют:
- молотки с круглым полировальным бойком, так как молотки с квадратным бойком оставляют следы в виде забоин;
- молотки из мягких материалов – киянки (медные, свинцовые, деревянные);
- гладилки и поддержки (металлические или деревянные бруски) для правки тонкого листового и полосового металла;
- правильные бабки для закаленных деталей с цилиндрической, сферической и прочими фасонными поверхностями.
Кривизну заготовок проверяют на глаз или по зазору между плитой и уложенной на нее заготовкой. Изогнутые места отмечают мелом. Правку производят на правильной плите или наковальне. Простейшей является правка металла, изогнутого по плоскости. В этом случае молотком или кувалдой наносят сильные удары по наиболее выпуклым местам полосы, уменьшая силу удара по мере выпрямления и поворачивая полосу с одной стороны на другую по мере необходимости (Рис.3.4 а, б).
Рисунок 3.4. Приемы правки полосового и круглого сечения
Сложней правка металла, изогнутого по ребру. Если в первом случае правка заключалась в простом выравнивании полосы, то здесь прибегают к деформированию растяжением части металла (Рис.3.4 в).Правку полос, имеющих скрученный (спиральный) изгиб (Рис.3.4 г), рекомендуется производить методом раскручивания, для чего один конец заготовки зажимают в слесарные тиски, а на втором конце закрепляют ручные тисочки. Затем рычагом выпрямляют спиральную кривизну. При необходимости окончательную правку проводят на плите. Результаты правки (прямолинейность заготовки) проверяют на глаз (Рис.3.4 д), а для более точной проверки - на разметочной или контрольной плите по просвету, наложением линейки на полосу или щупом.
Правка листового материала - более сложная операция. Она зависит от вида деформирования, как, например, выпуклости или вмятины в середине листа или заготовки, волнистости краев и кромок заготовки, более сложного деформирования, когда заготовка имеет одновременно выпуклости и волнистость кромок листа (Рис.3.5).
Рисунок 3.5. Приемы правки листового материала
Предварительно обводят мелом или карандашом волнистые участки на заготовке, затем кладут ее на плиту выпуклостью вверх так, чтобы заготовка лежала всей поверхностью на плите. Придерживая лист левой рукой в рукавице, правой наносят молотком удары от края листа по направлению к выпуклости (как показано стрелками на рис.3.5 а), по мере приближения к выпуклости удары наносят слабей и чаще. Во время правки заготовку поворачивают в горизонтальной плоскости так, чтобы удары равномерно распределялись кругом по всей площади заготовки.
Если на листе имеется несколько выпуклостей, то удары наносят в промежутке между выпуклостями. В результате этого лист растягивается и все выпуклости сводятся в одну общую, которую выправляют указанным выше способом.
Если лист имеет волнистость по краям, но ровную середину, то удары молотком наносят от середины листа к краям (Рис.3.5 б). От воздействия этих ударов лист в середине вытягивается и волны по кромкам листа исчезают. После этого лист следует перевернуть и продолжать правку таким же способом до получения требуемых допусков прямолинейности и плоскостности.
Правку тонких листов производят деревянными молотками-киянками (Рис.3.5 в), а очень тонкие листы проглаживают деревянным или металлическим бруском-гладилкой, придерживая их на плите левой рукой (Рис.3.5 г). При правке лист периодически переворачивают.
Правку закаленных заготовок, иногда называемую рихтовкой, вызванную короблением при термической обработке, проводят различными молотками с закаленным бойком или специальным молотком с закругленной узкой стороной бойка.
Рисунок 3.6. Правка закаленных деталей и места нанесения ударов
Удары наносят не по выпуклой, а по вогнутой стороне заготовки. Таким образом достигается растяжение волокон металла на вогнутой стороне заготовки и ее выпрямление. Правку заготовок более сложной формы, например угольника, у которого после закалки изменился угол между измерительными сторонами, производят следующими способами: если угол стал меньше 90°, то удары молотком производят у вершины внутреннего угла (Рис.3.6 а), если угол стал больше 90°, то удары наносят у вершины наружного угла (Рис.3.6 б).
Гибка
Гибка - одна из наиболее распространенных слесарных операций. Ее применяют для придания заготовке изогнутой формы по заданному контуру. В процессе гибки металл подвергается одновременному действию растягивающих и сжимающих сил, поэтому при гибке необходимо учитывать механические свойства металла, его упругость, степень деформирования, толщину, форму и размеры сечения заготовки, углы и радиусы изгиба детали. Радиус изгиба детали не следует принимать близким к минимально допустимому, если это не диктуется конструктивными требованиями.
Целесообразно не допускать радиус изгиба меньше толщины заготовки, так как уменьшение радиуса приводит к появлению трещин и других дефектов. В холодном состоянии рекомендуется изгибать детали из листовой стали толщиной до 5 мм, из полосовой стали толщиной до 7 мм, из круглой стали диаметром до 10 мм.
Рисунок 3.7. Приемы гибки полос
Гибку полосы из листовой стали выполняют в следующем порядке: наносят риску загиба, зажимают заготовку в тисках между угольниками-нагубниками так, чтобы разметочная риска была обращена к неподвижной губке тисков и выступала над ней на 0,5 мм (Рис.3.7 а), и ударами молотка, направленными к неподвижной губке, загибают конец полосы (Рис.3.7 б). Для гибки скобы заготовку зажимают в тисках между угольником и бруском-оправкой, загибают первый конец (Рис.3.7 в), затем, вложив внутрь скобы брусок-оправку требуемого размера, зажимают скобу в тиски на уровне рисок и отгибают вторую лапку (Рис.3.7 г).
Гибка полосы под острым углом с применением специальной оправки показана на рис.3.7 д.
Рисунок 3.8. Приемы гибки хомутика:
1 - оправка; 2 - заготовка; 3 - плоскогубцы; 4 - нагубники; 5 - медная пластина
Гибку хомутика из тонкой полосовой стали выполняют в следующем порядке: зажимают в тисках оправку 1 требуемого диаметра (Рис.3.8 а), загибают заготовку 2 на оправке двумя плоскогубцами 3 и обрабатывают хомутик окончательно с помощью молотка на оправке в тисках (Рис.3.8 б, в).
Рубка
Рубка металла представляет собой операцию обработки металла резанием, при которой с помощью режущего инструмента - зубила, крейцмейселя или канавочника - с заготовки или детали удаляют излишний слой металла или заготовку разрубают на части, вырубают отверстие в листовом материале, прорубают смазочные канавки и т. п.
Рубку производят в тех случаях, когда по условиям производства станочная обработка трудно выполнима или нерациональна и когда не требуется высокая точность обработки. Рубку мелких заготовок производят в тисках, крупные заготовки рубят на плите или наковальне, особо крупные - на том месте, где они находятся.
Для рубки применяются следующие инструменты:
зубило, крейцмейсель, канавочник.
а) б) в)
Рисунок 3.9. Инструменты для рубки
Зубило слесарное (Рис.3.9 а) состоит из трех частей: рабочей 2, средней 3 и ударной (бойка) 4.
Рабочую часть зубила, заканчивающуюся клиновой режущей частью 1, и боек закаливают и отпускают. После термической обработки режущая кромка должна иметь твердость HRC 55...60; боек - HRC 35...40.
Зубила изготовляют длиной 100...200 мм, ширину режущей кромки соответственно выбирают 5...25 мм. Угол заострения зубила в зависимости от обрабатываемого материала затачивают на заточном станке до следующих размеров (град):
Твердые материалы (чугун, твердая сталь, бронза)..... 70
Материалы средней твердости (сталь).......................... 60
Мягкие материалы (медь, латунь)................................. 45
Алюминиевые сплавы и цинк.................................. 35
Чем меньше угол заострения, тем меньшую силу необходимо приложить для резания, однако чем больше твердость и хрупкость обрабатываемого металла и сильней сопротивление проникновению в него клина, тем прочней должны быть режущая кромка и больше угол заострения. Головка зубила - боек делается всегда в виде усеченного конуса с полукруглым верхним основанием, так как в этом случае наносимый молотком удар приходится по центру головки зубила. Конусная головка, кроме того, меньше расклепывается при работе.
Крейцмейсель (Рис.3.9 6) отличается от зубила более узкой режущей кромкой. Применяется для вырубания узких канавок, пазов и т. п. Чтобы крейцмейсель, углубляясь в канавку, не заклинивался, его режущую кромку делают несколько шире рабочей части.
Крейцмейселем также пользуются для срубания поверхностного слоя с широкой чугунной плиты, когда сначала прорубают узкие канавки, а затем оставшийся металл зубилом. Углы заточки, твердость рабочей и ударной части крейцмейселя те же, что и у зубила.
Канавочники (Рис.3.9 в)отличаются от крейцмейселя только изогнутой формой режущей кромки и применяются для вырубания смазочных канавок во вкладышах и втулках подшипников и при других подобных работах.
Рисунок 3.10. Положение слесаря при работе зубилом
Приступая к рубке, необходимо подготовить свое рабочее место. Зубило располагают на верстаке с левой стороны тисков режущей кромкой к себе, а молоток - с правой стороны тисков бойком, направленным к тискам.
Большое значение при рубке имеет правильное положение корпуса слесаря: при рубке надо стоять у тисков устойчиво вполоборота к ним, левей тисков (Рис.3.10 а). Положение ног слесаря показано на рис.3.10 б. Качество и производительность рубки зависят от вида удара молотком.
Различают три вида удара молотком: кистевой, локтевой и плечевой. Перед началом рубки необходимо выполнить тренировочные упражнения по нанесению различных ударов молотком.
При кистевом ударе (Рис.3.11 а)изгибается только кисть правой руки. Таким ударом пользуются при выполнении легкой и точной работы: снятие тонких слоев металла, удаление небольших неровностей, рубке тонкой листовой стали и т. п.
При локтевом ударе (Рис.3.11 б)рука изгибается в локте и удар получается более сильным. Этим ударом пользуются при обычной рубке, снятии слоя металла средней толщины, вырубании пазов и канавок.
При плечевом ударе (Рис.3.11 в)рука движется в плече, при этом получается большой замах и максимальная сила удара.
а) б) в)
Рисунок 3.11. Виды удара молотком
Плечевой удар применяют при рубке толстого металла, удалении большого припуска за один проход, обработке больших плоскостей. или разметочные риски должны выступать над губками тисков на 5...10 мм.
Частота замахов молотком в минуту должна быть 40...60 при кистевом; 30...40 замахов при локтевом и плечевом ударах.
При рубке молоток берут правой рукой за рукоятку на расстоянии 15...30 мм от конца так, чтобы четыре пальца охватывали рукоятку, а большой палец был наложен на указательный. Зубило надо держать левой рукой, не сжимая сильно пальцы, на расстоянии 20...30 мм от его головки.
Рисунок 3.12. Углы наклона зубила по отношению к оси
губок тисков и обрабатываемой поверхности заготовки
При рубке металла большое значение имеет правильная установка оси зубила к обрабатываемой поверхности заготовки. Угол между заготовкой (плоскостями губок тисков) и осью зубила должен быть равен 45°, угол наклона зубила зависит от угла заострения режущей кромки и должен составлять 30...35°. При меньшем угле наклона зубило скользит, а не режет, а при большем - излишне углубляется в металл и дает большую неровность обработанной поверхности (Рис.3.12).
В процессе рубки металла руки должны действовать согласованно. Правой рукой нужно точно ударять молотком по зубилу, левой - в промежутках между ударами перемещать зубило по металлу. При ударе смотреть не на головку, а на режущую кромку зубила.
При рубке полосового и листового металла по уровню губок тисков часть заготовки, уходящая в стружку (срубаемая), должна быть над губками тисков, риска разметки - находиться точно на уровне губок без перекоса, в начале рубки заготовка не должна выступать за правый торец губок, рубку выполнять локтевым ударом (Рис.3.13 а).
Рисунок 3.13. Рубка полосового и листового металла
Если разметочные риски находятся выше уровня губок, чтобы зубило излишне не углублялось в металл, угол между осью зубила и обрабатываемой поверхностью надо периодически уменьшать (Рис.3.13 6).
При срубании слоя металла на широкой плоской поверхности заготовка или разметочные риски должны выступать над губками тисков на 5...10 мм. Сначала следует крейцмейселем прорубить канавки шириной 8...10 мм (Рис.3.14 а).
Рисунок 3.14. Рубка широких поверхностей
Ширина промежутков между канавками должна составлять 0,8 длины режущей кромки применяемого при работе зубила. Затем зубилом срубают образовавшиеся выступы (Рис.3.14 6). Толщина стружки, снимаемая крейцмейселем за один ход, равна 0,5...1 мм, а при срубании выступов зубилом - 1,5...2 мм. Чугун, бронзу и другие хрупкие металлы нельзя рубить, доходя до противоположного края заготовки. Недорубленные места следует рубить с противоположной стороны или предварительно сделать скос под углом 45°.
Вырубание пазов (Рис.3.15 а) и криволинейных смазочных канавок (Рис.3.15 б) производят в такой последовательности: сначала на обрабатываемую поверхность заготовки наносят риски, затем крейцмейселем прорубают канавки глубиной 1,5...2 мм за каждый проход.
Оставшиеся после рубки неровности устраняют канавочником, придавая пазам одинаковую ширину и глубину по всей длине заготовки.
Рисунок 3.15. Вырубание пазов и канавок
При вырубании фигурной заготовки на плите или наковальне работу выполняют в такой последовательности. Отступив от разметочных рисок на 2...3 мм, легкими ударами по зубилу надрубают контур. Затем сильными ударами по зубилу рубят лист по контуру. Если лист достаточно толстый, то, перевернув его, прорубают зубилом по контуру, ясно обозначившемуся на противоположной стороне. Затем вновь переворачивают лист на первую сторону и заканчивают рубку.
Рисунок 3.16. Приемы рубки металла:
а - листового материала; б - полосы; в - вырубание фигурной заготовки из листовой стали; г - перерубание чугунной трубы
При вырубании заготовки с криволинейными контурами необходимо пользоваться зубилом с закругленным лезвием или крейцмейселем. Различные приемы рубки металла показаны на рис.3.16 а... г.
Резка
Резка металла - операция разделения на части круглого, полосового, профильного проката, а также труб ручным и механическим способом.
Ручную резку заготовок в зависимости от профиля и площади сечения производят различными инструментами: ножовками, ножницами (ручными, стуловыми, рычажными), труборезами и газопламенными горелками.
Рисунок 3.17. Ручная ножовка
Ручная ножовка — наиболее распространенный инструмент для разрезки толстых листов, полосового и профильного металла, а также для прорезания пазов, шлицев, обрезки и вырезки заготовок по контуру и т. п. Она состоит из рамки (ножовочного станка), подвижной головки, винта с гайкой для натяжения ножовочного полотна и неподвижной головки с хвостовиком и рукояткой (Рис.3.17 а).
Рамки ножовки бывают цельной и раздвижной конструкции.
Ножовочное полотно представляет собой тонкую и узкую стальную пластину с зубьями на одном ребре. Каждый зуб ножовочного полотна (Рис.3.17 б, в) имеет форму клина (резца), на котором различают задний угол α, угол заострения β, передний угол γ. Для уменьшения трения ножовочного полотна о стенки разрезаемого металла (пропила) зубья его разводят в разные стороны, увеличивая таким образом толщину полотна h до ширины пропила К. Зубья с большим шагом отгибают по одному поочередно вправо и влево (Рис.3.17 д), зубья с малым шагом отгибают по два-три вправо и по два-три влево, при этом образуется волнистая линия (Рис.3.17 г).
При разрезке металла ножовкой корпус слесаря необходимо развернуть вправо под углом 45 ° к оси тисков (Рис.3.18 а). Положение ног показано на рис.3.18 б.
Рисунок 3.18. Положение слесаря при работе ножовкой
Прежде чем приступить к разрезке металла, необходимо выбрать ножовочное полотно с учетом твердости, формы и размеров разрезаемого металла и, вставив его в рамку, затянуть натяжным винтом. Степень натяжения проверяют легким нажатием пальца на полотно сбоку: если полотно не прогибается, то напряжение достаточное (Рис.3.19 а).
Рукоятку ножовки охватить пальцами правой руки, конец рукоятки при этом должен упираться в середину ладони, а большой палец лежать вдоль рукоятки сверху.
Рисунок 3.19. Приемы работы при резании металла ножовкой:
а - натяжка полотна; б - положение (хват) левой руки; в - положение правой руки; г - разрезание прутка круглого сечения; д - разрезание тонкого листа; е - разрезание прутка прямоугольного сечения; ж - прорезка шлица (прорези) специальной ножовкой
Левой рукой взять рамку ножовки так, чтобы большой палец находился внутри рамки, а остальные охватывали натяжной винт подвижной головки. Во время разрезки ножовку держать в горизонтальном положении. Двигать ее надо плавно, без рывков, производя 30...60 двойных ходов в минуту. При движении вперед рамку ножовки нажимать вниз. Длина хода ножовки должна быть такой, чтобы работало не менее 2/3 ее длины, а не только ее средняя часть.
Тонкий материал для разрезки ножовкой зажимают в тиски между двумя деревянными брусками и разрезают вм
|
|
Своеобразие русской архитектуры: Основной материал – дерево – быстрота постройки, но недолговечность и необходимость деления...
Кормораздатчик мобильный электрифицированный: схема и процесс работы устройства...
Общие условия выбора системы дренажа: Система дренажа выбирается в зависимости от характера защищаемого...
Эмиссия газов от очистных сооружений канализации: В последние годы внимание мирового сообщества сосредоточено на экологических проблемах...
© cyberpedia.su 2017-2024 - Не является автором материалов. Исключительное право сохранено за автором текста.
Если вы не хотите, чтобы данный материал был у нас на сайте, перейдите по ссылке: Нарушение авторских прав. Мы поможем в написании вашей работы!