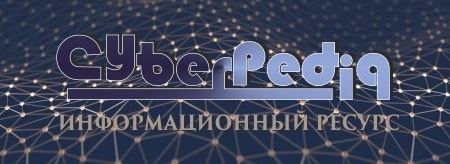
Архитектура электронного правительства: Единая архитектура – это методологический подход при создании системы управления государства, который строится...
Двойное оплодотворение у цветковых растений: Оплодотворение - это процесс слияния мужской и женской половых клеток с образованием зиготы...
Топ:
Марксистская теория происхождения государства: По мнению Маркса и Энгельса, в основе развития общества, происходящих в нем изменений лежит...
Характеристика АТП и сварочно-жестяницкого участка: Транспорт в настоящее время является одной из важнейших отраслей народного...
История развития методов оптимизации: теорема Куна-Таккера, метод Лагранжа, роль выпуклости в оптимизации...
Интересное:
Лечение прогрессирующих форм рака: Одним из наиболее важных достижений экспериментальной химиотерапии опухолей, начатой в 60-х и реализованной в 70-х годах, является...
Подходы к решению темы фильма: Существует три основных типа исторического фильма, имеющих между собой много общего...
Финансовый рынок и его значение в управлении денежными потоками на современном этапе: любому предприятию для расширения производства и увеличения прибыли нужны...
Дисциплины:
![]() |
![]() |
5.00
из
|
Заказать работу |
Компоновочные структуры автоматических ПС зависят от типа производства и принципа межоперационного транспортирования. В AЛ массового производства реализован принцип меж- операционной передачи станок — станок. По этому принципу строят и ГАЛ в крупно- и среднесерийном производстве (см. рис. 7.7, б). Компоновочные структуры ГПС мелкосерийного производства строят по принципу межоперационного транспортирования станок — склад — станок и, как правило, предусматривают централизованный межоперационный склад-накопитель (см. рис. 7.7, а, в), обслуживаемый одним или несколькими оперативными транспортными устройствами. Емкость склада обеспечивает работу ГПС на период оперативного планирования от 6 до 10 рабочих смен.
AЛ являются сложными техническими системами с большим количеством инструментов, исполнительных механизмов и контрольных устройств. Для уменьшения снижения производительности вследствие отказов отдельных элементов технических систем AЛ разбивают на участки, предусматривая между ними накопительные подсистемы. Их число устанавливают на основе расчета фактической производительности AЛ в зависимости от надежности технологических систем, определяющих внецикловые потери.
Оптимальное число последовательных позиций AЛ жесткого типа на одном участке
где — такт работы AЛ или поточной линии жесткого типа;
— внецикловые потери по оборудованию, которые являются комплексным показателем надежности технологических систем, характеризующим безотказность работы оборудования, устойчивость и стабильность ТП,
— параметр потока отказов, характеризующий их интенсивность (среднее число отказов в минуту);
— среднее время обнаружения и устранения отказов, мин.
Между участками АЛ или поточных линий предусматривают накопители, емкости которых должны быть достаточными для работы смежного участка на период времени устранения отказа, вызванного отказом станка, системы управления, внезапной поломкой инструмента, его преждевременным износом и т. п. Емкость накопителя определяют по формуле
где =1,3…1,5.
Типичными для AЛ жесткого типа будут структуры, показанные на рис. 7.14. Короткие AЛ состоят из одного участка (см. рис. 7.14, а), линии с числом станков (позиций) более 10, как правило, разбивают на два или несколько участков с накопителями между ними (см. рис. 7.14, б, в).
Рис. 7.14. Структура AЛ массового и крупносерийного производства:
а — без разделения на участки; б, в — с разделением на участки последовательного и последовательно-параллельного действия соответственно; 1 — станки (позиции) линии; 2 — накопитель
ГПС на предприятиях внедряют поэтапно, поэтому следует определить очередность их использования для групп деталей. Это очень важно в связи с большими капитальными затратами на их проектирование и создание. Поэтому для обеспечения наибольшей эффективности первой очереди ГПС необходимо сосредоточить в ГПС максимальную концентрацию обработки наиболее предпочтительной группы деталей или их станкоемкостей. Если в изготавливаемых изделиях не выявляются однозначные подобные предпочтительные группы деталей, коэффициент значимости k -й группы можно определить по формуле
где — параметр, характеризующий долю деталей k -й группы в общем объеме деталей,
— число наименований деталей в k -й группе;
— годовой объем выпуска j -й детали k -й группы; т — общее число наименований обрабатываемых в цехе деталей;
— годовой объем выпуска j -й детали.
Ранжированием групп по убыванию определяют в первом приближении очередность внедрения ГПС для соответствующих групп деталей. Может оказаться так, что в наиболее предпочтительную группу будут включены детали, равномерно входящие во все изделия, и их влияние на каждое изделие окажется незначительным. Поэтому на первых этапах внедрения ГПС необходимо рассчитывать коэффициент значимости групп деталей для каждого изделия:
Здесь
-соответственно число разных деталей изделия в £-й группе и в изделии в целом.
По значению оценивают значимость групп деталей для конкретных изделий и судят о целесообразности и наибольшей эффективности первоочередного внедрения ГПС.
Одной из составляющих ГПС является автоматизированная транспортно-складская система (АТСС), которая является организационной основой ГПС, обеспечивающей возможность планирования производства и реагирования на возникшие в ходе производства ситуации. Она материализует действия АСУП и обеспечивает взаимодействие различного оборудования ГПС. Поэтому при выборе компоновочной схемы ГПС в первую очередь необходимо увязать расположение ГПМ и АТСС.
Относительно транспортной магистрали станочные модули размещают вдоль, поперек, под углом, а также кустами с использованием кольцевых структур при загрузке станков роботами (рис. 7.15). Выбор варианта определяется видом транспорта, способом загрузки заготовок на станок, направлением и способом удаления стружки, а также другими факторами. Например, при использовании безрельсовых транспортных роботов для доставки заготовок и деталей в кассетах и наличии в станке стружкоуборочного транспортера с тыльной стороны эффективным является размещение станочных модулей под углом (см. рис. 7.15, в). При такой планировке транспортный робот используется не только для передачи кассет с заготовками и деталями, но и для транспортирования емкости со стружкой на участок сборки.
При использовании стружкоуборочных конвейеров применяют размещение станочных модулей вдоль или поперек транспортной магистрали. Продольное расположение характерно при обработке заготовок в ГПС на приспособлениях-спутниках. В этом варианте наиболее просто осуществляется стыковка загрузочных устройств станка с рельсовыми или безрельсовыми транспортными роботами и транспортерами спутников.
Опыт проектирования показывает, что в пролете шириной 18 м удается разместить до трех рядов оборудования ГПС обработки тел вращения и один или два ряда оборудования при обработке корпусных деталей. В пролете шириной 24 м размещают до четырех рядов станков при обработке тел вращения и мелких корпусных деталей и два или три ряда оборудования при обработке корпусных деталей.
На компоновку ГПС наряду со структурой и схемой АТСС влияют и другие системы обеспечения функционирования производства. Важнейшим компонентом ГПС является система обеспечения инструментом, которая включает участок инструментальной подготовки и технические средства для доставки и замены инструментов в магазинах станочных модулей.
Рис. 7.15. Схемы размещения станочных модулей относительно трассы движения транспортного робота: а — вдоль; б — поперек; в — под углом; г — в виде кольцевой структуры; 1 — ГПМ; 2 — стружкоуборочный конвейер; 3 — транспортный робот; 4 — емкость для стружки; 5 — загрузочный робот
Как правило, участок инструментальной подготовки входит в состав ГПС, однако возможно инструментальное обслуживание цеховым отделением. Доставку и замену инструментов в магазинах и револьверных головках станочных модулей в более простых ГПС осуществляют вручную.
В более совершенных системах, рассчитанных на продолжительную работу в безлюдном режиме, предусматривают автоматическую доставку и замену инструментов. Для этой цели используют транспортные роботы АТСС и пристаночные манипуляторы или предусматривают отдельную транспортную систему.
На рис. 7.16 показана схема ГПС, в которой для автоматической замены инструментов в многоцелевых станках 6 предусмотрена автоматизированная система инструментообеспечения, включающая склад-накопитель инструментов 5, робот на тележке 3 для подачи инструментов в магазины станков и в склад-накопитель, а также станцию 1 для предварительной настройки инструментов. Для транспортирования заготовок в ГПС применена рельсовая тележка 9, вдоль трассы которой размещены накопители палет 8. Запаса палет достаточно для работы без обслуживания в третью смену. В начале ГПС предусмотрена зона 10 загрузки и выгрузки заготовок и деталей и моечная машина 12. На участке ГПС расположен управляющий вычислительный комплекс 2 и пульт управления 11. Для удаления стружки от станков предусмотрены конвейеры 7, с помощью которых стружку транспортируют к емкостям 4, расположенным в зоне, удобной для обслуживания внутрицеховым транспортом. ГПС предназначена для обработки корпусных деталей двухсот наименований массой до 500 кг.
Рис. 7.16. ГПС для изготовления корпусных деталей с автоматизированной системой обеспечения инструментом и уборки стружки
Для малых ГПС, содержащих 6—8 станочных модулей, отделение инструментальной подготовки не предусматривают, размещая одно рабочее место (станцию) по настройке инструментов с приборами настройки и терминалом у станков.
При изготовлении корпусных и плоскостных деталей на многоцелевых станках в ГПС возможны два варианта установки заготовок для обработки. В условиях среднесерийного производства заготовки устанавливают непосредственно в приспособления-спутники, расположенные на сменном столе (модуль ИР500ПМФ4) или в магазине (модуль ИР500ПМ1Ф4). Доставляют заготовки к рабочему месту транспортным роботом в таре, таким же способом их возвращают на склад или передают на следующую станцию.
При частых переналадках в условиях мелкосерийного производства более предпочтительным является вариант автоматизации с обработкой в приспособлениях-спутниках. В этом случае заготовки в приспособления-спутники размещают в отделении установки заготовок, полуфабрикатов и съема обработанных деталей. Рядом обычно располагают агрегат мойки универсальносборной оснастки и приспособлений-спутников, а также позиции сборки и разборки оснастки.
На рис. 7.17 приведена планировка ГПС модели АСК-20, предназначенная для обработки корпусов, столов, звеньев звездочек и других деталей станков в условиях мелкосерийного производства. В ГПС предусмотрены четыре ГПМ 1 модели ИР500ПМ1Ф4 с шестипозиционными накопителями и моечный агрегат 7. Система обеспечения функционирования включает в себя транспортно-накопительную систему на базе транспортного робота 5, перемещающегося по рельсовому пути 6; участок загрузки и разгрузки приспособлений-спутников с рабочими позициями 2, приемными столами 12, устройствами ориентации 14 и уравновешенными манипуляторами 1 5; участок сборки универсально-сборной переналаживаемой оснастки на приспособления-спутники со стеллажами 3 для хранения элементов оснастки, слесарным верстаком 13 и шкафами 11; участок инструментальной подготовки, оборудованный прибором 9 для настройки инструментов вне станка, рабочими местами 4, инструментальным стеллажом 8 и ручной тележкой 10. Некоторые современные ГПС оборудуют системами полуавтоматической настройки инструментов непосредственно на станке. Рядом с участком инструментальной подготовки расположен диспетчерский пульт 16, а на антресольном этаже — управляющий вычислительный комплекс. Емкость станочного магазина приспособлений-спутников обеспечивает непрерывную работу модуля в течение смены и более.
Рис.7.17. Планировка ГПС для изготовления корпусных деталей в условиях мелкосерийного производства
Число позиций загрузки и разгрузки приспособлений- спутников зависит от количества СГпс многоцелевых станков ГПС, работающих с приспособлениями-спутниками, проходящими через участок загрузки и разгрузки, и продолжительности t обработки заготовок в приспособлении-спутнике при одном закреплении и среднем времени
снятия деталей со спутника и установки заготовок. Однако поскольку в ГПС обрабатывают заготовки разных деталей, удобнее использовать среднюю продолжительность
их обработки на станке. Тогда
где К3 = 0,85; — эффективный фонд времени позиции в соответствии с режимом работы участка (одна или две смены).
В задачу рабочих по загрузке приспособлений-спутников входит также укладка обработанных полуфабрикатов или деталей в унифицированную тару для последующей отправки на автоматизированный склад. Численность рабочих , обслуживающих позиции загрузки и разгрузки приспособлений-спутников, определяют по формуле
где — эффективный годовой фонд времени рабочего, равный
1 720 ч.
Количество собираемых в течение года приспособлений на участке сборки универсально-сборной оснастки вычисляют по формуле
где — среднее количество приспособлений-дублеров, используемых при обработке партии заготовок;
— средний размер партии изготавливаемых деталей.
Численность рабочих, занятых на участке сборки универсально-сборной оснастки, определяют исходя из того, что один слесарь-сборщик собирает до 1000 компоновок средней сложности в год. Площадь участка сборки универсально-сборной оснастки можно определить по следующим данным:
Численность слесарей на участке сборки..... 1 2,3 4
Норма площади на человека, м2............ 20 15 12
Двойное оплодотворение у цветковых растений: Оплодотворение - это процесс слияния мужской и женской половых клеток с образованием зиготы...
Своеобразие русской архитектуры: Основной материал – дерево – быстрота постройки, но недолговечность и необходимость деления...
Состав сооружений: решетки и песколовки: Решетки – это первое устройство в схеме очистных сооружений. Они представляют...
Поперечные профили набережных и береговой полосы: На городских территориях берегоукрепление проектируют с учетом технических и экономических требований, но особое значение придают эстетическим...
© cyberpedia.su 2017-2024 - Не является автором материалов. Исключительное право сохранено за автором текста.
Если вы не хотите, чтобы данный материал был у нас на сайте, перейдите по ссылке: Нарушение авторских прав. Мы поможем в написании вашей работы!