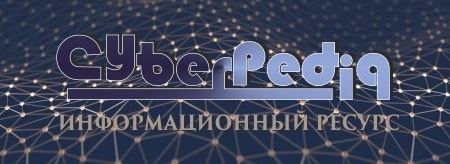
Кормораздатчик мобильный электрифицированный: схема и процесс работы устройства...
Наброски и зарисовки растений, плодов, цветов: Освоить конструктивное построение структуры дерева через зарисовки отдельных деревьев, группы деревьев...
Топ:
Процедура выполнения команд. Рабочий цикл процессора: Функционирование процессора в основном состоит из повторяющихся рабочих циклов, каждый из которых соответствует...
Оснащения врачебно-сестринской бригады.
Устройство и оснащение процедурного кабинета: Решающая роль в обеспечении правильного лечения пациентов отводится процедурной медсестре...
Интересное:
Уполаживание и террасирование склонов: Если глубина оврага более 5 м необходимо устройство берм. Варианты использования оврагов для градостроительных целей...
Национальное богатство страны и его составляющие: для оценки элементов национального богатства используются...
Инженерная защита территорий, зданий и сооружений от опасных геологических процессов: Изучение оползневых явлений, оценка устойчивости склонов и проектирование противооползневых сооружений — актуальнейшие задачи, стоящие перед отечественными...
Дисциплины:
![]() |
![]() |
5.00
из
|
Заказать работу |
|
|
В цикловых системах управление качеством обработки осуществляется при ТПП. Точность обработки зависит от того, насколько при известных входных переменных точно определены условия выполнения операции и все это учтено в задающем воздействии управляющего устройства и наладке технологической системы.
Задачу обеспечения заданной точности решают в два этапа:
1) определяют условия выполнения операции, при которых суммарная погрешность обработки ∆ не превышает поле допуска Т;
2) устанавливают расположение поля погрешности в поле допуска. Последнее обеспечивают размерной наладкой технологической системы, выполняемой в сфере производства, однако способ наладки и условия ее проведения выбирают при технологическом проектировании (в процессе ТПП).
Размерную наладку выполняют на назначенные (рассчитанные) при проектировании наладочные размеры. Рассмотрим соображения, в соответствии с которыми выбирают наладочные размеры в цикловых системах.
Если Т = , то заданная точность будет выдержана только в том случае (рис. 3.5, а), если в процессе наладки будут совмещены нижние и верхние границы заданных
и фактических
размеров:
,
.
Во всех остальных случаях поле погрешности выйдет за пределы поля допуска, а следовательно, возможно получение брака. В данном случае может быть только один наладочный размер, который обеспечивает заданную точность обработки.
Рис. 3.5. Схемы к выбору наладочных размеров в цикловых системах при равенстве допуска и поля суммарной погрешности обработки (а) и при превышении допуском поля суммарной погрешности обработки (б)
При Т > (рис. 3.5, б) поле погрешности
может занимать множество положений относительно поля допуска, обеспечивающих заданную точность обработки. Указанное множество положений поля погрешности относительно поля допуска ограничивается неравенствами
|
;
Значение Т — можно трактовать, например, как допуск на размерный износ инструмента. В рассматриваемом случае может быть множество наладочных размеров, при которых выдерживается заданная точность обработки. Однако эффективность обработки при их использовании различна. В частности, чем больше допуск на износ инструмента Ти, тем меньше требуется подналадок инструмента за период его стойкости, а следовательно, уменьшаются непроизводительные простои станка и трудоемкость обработки. Нетрудно видеть (см. рис. 3.5, б), что допуск Ти будет наибольшим при совмещении нижних предельных и фактически получаемых размеров:
. Исходя из изложенного наладочные размеры следует выбирать таким образом, чтобы фактические размеры первых обработанных деталей были максимально смещены к нижней (для вала) или верхней (для отверстия) границе поля допуска. Это требование обеспечивает минимальное число подналадок технологической системы.
На рис. 3.6 показана точностная диаграмма деталей, обработанных при размерной наладке, выполненной в соответствии с изложенным требованием. Из этой диаграммы можно определить наладочный размер L н.дет для наладки по пробным деталям (случай наружной токарной обработки):
где — погрешность измерения готовых деталей;
— поле рассеяния размеров вследствие действия случайных составляющих погрешности обработки;
— систематическая закономерно изменяющаяся погрешность, обусловленная суммарным действием размерного износа и тепловых деформаций инструмента.
Уменьшение размеров в начальный момент связано с преобладающим влиянием тепловых деформаций. По мере их стабилизации начинается увеличение размеров, вызванное размерным износом инструмента.
Рис. 3.6. Точностная диаграмма деталей, обработанных при постоянной размерной наладке
|
При наладке по эталону силы резания отсутствуют (рис. 3.7, а). После выполнения такой наладки размер обработанных деталей будет больше наладочного размера на значение у средней упругой деформации технологической системы:
где — средние упругие деформации элементов технологической системы, связанных с заготовкой;
— средние упругие деформации элементов технологической системы, связанных с инструментом.
Рис. 3.7. Схема размерной наладки по эталону:
— диаметр заготовки
При наладке по эталону наладочный размер измеряют от формообразующей вершины инструмента (рис. 3.7, б). После обработки измеряемый наладочный размер отличается от наладочного размера по эталону на параметр Rz высоты микронеровностей. Наладочный размер при наладке по эталону определяют по формуле
Изложенный подход и методика определения наладочного размера справедливы не только для цикловых систем, но и для случаев обработки с использованием автоматически подналадочных (наладочных) устройств, когда отсутствует систематический контроль и компенсация размерного износа инструмента (например, статистический контроль). Если износ контролируется и компенсируется при обработке каждой заготовки партии, то в качестве наладочного размера рекомендуется принимать середину поля допуска.
Наладочные размеры как составляющие вектора задающего воздействия непосредственно определяют статическую настройку технологической системы. Если же формой реализации цикловой системы управления является ЧПУ, их вносят в управляющие программы. Наиболее часто обеспечение качества при обработке на станках с ЧПУ связано с компенсацией погрешностей, вызываемых упругими деформациями технологической системы при изменении условий резания. Такие изменения могут происходить, например, при обработке участков заготовок, требующих резкого изменения траектории относительного движения инструмента и заготовки.
При контурном фрезеровании на станке с ЧПУ участка заготовки, показанного на рис. 3.8, радиус R сопряжения плоских участков контура равен радиусу фрезы. Припуск на обработку считается распределенным эквидистантно обработанному контуру. При обработке плоского участка с прямолинейной образующей глубина резания постоянна и равна припуску , а угол контакта
и сила резания
постоянны.
|
Фрезерование участка сопряжения связано с возрастанием глубины резания до . Как следствие, растет сила резания (рис. 3.9). В зависимости от формы сопряжения возможно увеличение окружной силы резания, причем
Рис. 3.8. Схема контурного фрезерования участка заготовки:
1 — заданный контур после обработки; 2 — контур исходной заготовки; 3, 4 — положения концевой фрезы; 5 — заданная (номинальная) траектория центра фрезы
Длина участка LK, на котором наблюдают рост сил резания, зависит от формы и размеров сопряжения. Максимальных значений глубина и сила резания достигают в точке изменения направления движения (точка O '), после чего происходит практически мгновенное изменение силы, действующей на фрезу, до значения, соответствующего плоскому участку. Изменение силы резания вызывает изменение упругих деформаций технологической системы при фрезеровании участка сопряжений.
Фактическая траектория центра фрезы и вид обработанного контура не совпадают с заданными (рис. 3.10). Проявление максимальной погрешности ∆у обработки контура таково, что при встречном фрезеровании возрастает риск появления неисправимого брака. При попутном фрезеровании брак может быть исправлен введением, например, дополнительного рабочего хода по той же управляющей программе, что, однако, резко снижает производительность и увеличивает затраты. К тому же, в связи с некоторыми особенностями процесса применение попутного фрезерования не всегда возможно.
Для обеспечения заданного качества обработки часто прибегают к предварительному искажению (геометрической коррекции) номинальной траектории движения инструмента и заданию ее в управляющей программе.
Рис. 3.9. Изменение окружной силы резания при контурном фрезеровании участка заготовки
Рис. 3.10. Фактические траектории центра фрезы и вид обработанного контура заготовки при встречном (о) и попутном (б) фрезеровании:
1,2 — заданный и фактический контуры после обработки соответственно; 3, 4 — заданная (номинальная) и фактическая траектории центра фрезы соответственно; ∆утах — максимальная погрешность обработки контура
|
При движении центра инструмента по предыскаженной траектории, являющейся зеркальным отображением фактической траектории относительно номинальной, происходит существенная компенсация указанной погрешности. Траектория центра инструмента при этом приближается к номинальной. В отмеченных случаях полного расчета суммарной погрешности обработки контура, как правило, не делают и ограничиваются расчетом отклонений, вызываемых упругими деформациями технологической системы, которые используют для расчетов, связанных с предыскажением траектории.
Расчет предыскажения выполняют в определенной последовательности, которую поясним на примере фрезерования участка заготовки (см. рис. 3.8, 3.9).
1. В зависимости от формы и геометрических параметров сопряжения определяют длину LK участка траектории, на котором ожидается рост силы резания, и в пределах этой длины выбирают 9—12 точек коррекции контура.
2. Для каждой i -й точки определяют угол θ i, контакта фрезы с заготовкой и погрешность контура ∆ i у.
3. Найденное значение ∆ i у ; сравнивают с допуском Т на выдерживаемый размер контура. Если ∆ i у < Т, то предыскажение траектории не делают, а в управляющую программу вводят номинальные координаты центра фрезы. При ∆ i у > Т выполняют расчет предыскажения по соответствующей координате (в рассматриваемом случае по у) (рис. 3.11):
где yKi — скорректированная ордината i -й точки контура. Суммирование осуществляется с учетом изменения знака , на противоположный. Для точек, соответствующих нестационарному участку фактической траектории, промежуточные скорректированные координаты определяют экстраполированием.
Рис. 3.11. Схема формирования предыскажения траектории центра фрезы:
1 — заданная (номинальная) траектория центра фрезы;
2 — фактическая траектория центра фрезы; 3 — предыскаженная траектория центра фрезы
Расчеты предыскажения траектории можно легко формализовать. Как правило, они выполняются автоматически при подготовке управляющих программ с использованием специализированных программно-аппаратных комплексов.
В самонастраивающихся системах контроль условий обработки и управление, обеспечивающее компенсацию влияния возмущающих факторов на качество обработки, возможен до начала автоматического цикла обработки. В этом случае управление качеством сводится к регулированию статической настройки.
|
|
Биохимия спиртового брожения: Основу технологии получения пива составляет спиртовое брожение, - при котором сахар превращается...
Организация стока поверхностных вод: Наибольшее количество влаги на земном шаре испаряется с поверхности морей и океанов (88‰)...
Архитектура электронного правительства: Единая архитектура – это методологический подход при создании системы управления государства, который строится...
Археология об основании Рима: Новые раскопки проясняют и такой острый дискуссионный вопрос, как дата самого возникновения Рима...
© cyberpedia.su 2017-2024 - Не является автором материалов. Исключительное право сохранено за автором текста.
Если вы не хотите, чтобы данный материал был у нас на сайте, перейдите по ссылке: Нарушение авторских прав. Мы поможем в написании вашей работы!