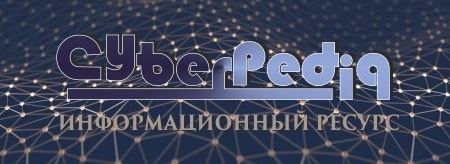
История развития хранилищ для нефти: Первые склады нефти появились в XVII веке. Они представляли собой землянные ямы-амбара глубиной 4…5 м...
Поперечные профили набережных и береговой полосы: На городских территориях берегоукрепление проектируют с учетом технических и экономических требований, но особое значение придают эстетическим...
Топ:
Особенности труда и отдыха в условиях низких температур: К работам при низких температурах на открытом воздухе и в не отапливаемых помещениях допускаются лица не моложе 18 лет, прошедшие...
Выпускная квалификационная работа: Основная часть ВКР, как правило, состоит из двух-трех глав, каждая из которых, в свою очередь...
Марксистская теория происхождения государства: По мнению Маркса и Энгельса, в основе развития общества, происходящих в нем изменений лежит...
Интересное:
Мероприятия для защиты от морозного пучения грунтов: Инженерная защита от морозного (криогенного) пучения грунтов необходима для легких малоэтажных зданий и других сооружений...
Принципы управления денежными потоками: одним из методов контроля за состоянием денежной наличности является...
Уполаживание и террасирование склонов: Если глубина оврага более 5 м необходимо устройство берм. Варианты использования оврагов для градостроительных целей...
Дисциплины:
![]() |
![]() |
5.00
из
|
Заказать работу |
|
|
Решения, формируемые (принимаемые) при контроле и управлении ТП, являются основой для разработки конкретных технологических мероприятий, направленных на стабильное обеспечение качества продукции при выполнении конкретного ТП или его элемента. Эти ТР должны быть конструктивными, т. е. представлять собой конкретные ответы на вопрос, что необходимо сделать для стабильного обеспечения заданного качества продукции. По своей сути указанные ТР относят к синтезирующим (проектным) решениям, принимаемым на основе ранее принятых аналитических решений.
Различают формирование ТР в неавтоматизированном производстве (при изготовлении опытных, установочных контрольных партий; при установившемся серийном изготовлении продукции и в автоматизированном (автоматическом) производстве, в котором полностью или частично реализован «безлюдный» режим работы. В первом случае ТР принимают по результатам выполнения соответствующей задачи и функции ТПП, во втором — выделяют первичные решения о выборе схемы (метода) управления и соответствующих технических средств, принимаемые при ТПП, и решения, формирующиеся автоматически управляющими устройствами в процессе работы.
Любую производственную систему, в которой реализован конкретный ТП, можно рассматривать как упорядоченную совокупность отдельных технологических систем, объединенную общей транспортной системой. В производственной системе различают подсистемы, состояние которых оценивается одним параметром бинарного вида («норма» или «отказ»), и подсистемы, состояние которых оценивается несколькими параметрами, находящимися в пределах нескольких зон.
|
К первым относятся, например, все подсистемы автоматики, элементы транспортной системы и другие, не являющиеся предметом рассмотрения настоящей книги, хотя ситуации, возникающие вследствие изменения их параметров, могут потребовать принятия соответствующего решения по управлению ТП; ко вторым — все технологические системы. В качестве изменяемых (выходных) параметров в последних могут выступать размеры или отклонения размеров обработанных поверхностей, элементарные погрешности размеров и т. п.
На рис. 3.2 схематично показано расположение зон изменения параметра технологической системы. Если фактическое значение параметра П е {nHmin, Пнтах}, то система функционирует нормально, обеспечивая заданное качество продукции. Если
Рис. 3.2. Схема расположения зон изменения параметра технологической системы
Пp min< П < Пн min или Пн max < п < Пр тах, то система функционирует в зоне риска, обеспечивая заданное качество продукции. При этом, однако, существует реальная возможность такого смещения параметра П, которое приведет к потере качества продукции, что равносильно отказу системы. Ситуация принятия решения возникает при смещении параметра П к границам зон риска Пр min, Пн min или Пн max, Пр max.
Возможны следующие задачи, требующие формирования различных по характеру ТР, а при их реализации и различных стратегий управления.
1. Гарантированное обеспечение заданного качества продукции, что соответствует условию
2. Обеспечение возврата к нормальной работе при и
3. Предотвращение неисправимого брака продукции и возникновения аварийных ситуаций при П < Пр min или П > Пр mаx-
4. Ликвидация последствий отказа и восстановления нормальной работы после предотвращения аварийных ситуаций.
Исходными данными для формирования решений при контроле и управлении ТП являются:
модель объекта управления;
параметры текущего состояния объекта управления, определяющие нахождение самого объекта в одной из выделенных зон;
|
цель управления (задача принятия решения);
критерии оптимальности управления.
Параметры текущего состояния могут быть определены с помощью наиболее соответствующего ситуации метода анализа ТП. Самыми распространенными критериями оптимальности управления для ТП механосборочного производства являются критерии максимальной (заданной) производительности и минимальных затрат. Критерий оптимальности задает ограничение на осуществление выбора той или иной стратегии управления и может определяться, например, ценой потерь вследствие того, что заданное качество продукции не обеспечивается (потери от неисправимого брака; потери на исправление брака; потери, связанные с частотой появления брака, и т. д.). Иногда, если отклонения возникают по ряду составляющих вектора выходных переменных, целесообразно определение наиболее желаемого (приоритетного) порядка стабилизации параметров качества.
Формирование ТР при управлении ТП машиностроения начинается с генерирования множества альтернативных ТР. Практически для любого дестабилизирующего фактора можно априорно определить набор стандартных для данной ситуации ТР. В большинстве случаев искомое оптимальное ТР находится среди них. Так, если установлено, что выходной параметр качества зависит в основном от погрешности закрепления заготовки в данной технологической операции, то возможными ТР, в той или иной степени устраняющими действие этого фактора, можно считать:
стабилизацию параметров качества исходных заготовок (прежде всего качества поверхностного слоя поверхностей, используемых как установочные базы);
неизменность условий закрепления заготовок (постоянство силы зажима заготовок, выбор рациональной формы установочных элементов приспособления);
изменение схемы закрепления заготовки (обеспечение перпендикулярности силы закрепления выдерживаемому размеру); принципиальное изменение схемы установки заготовки. Многие из этих ТР могут быть конкретизированы и сведены до элементарного уровня. Например, стабилизация силы зажима заготовки может быть достигнута применением автоматизированного зажимного устройства (пневматического, гидравлического и т. д.) либо использованием специальных динамометрических устройств при ручном приводе. В любом случае желательной является генерация на первом этапе формирования множества ТР, пусть даже и с различной степенью детализации. Такие множества создают для каждого параметра качества, стабилизация которого необходима.
|
Сформированное таким образом множество ТР просматривают с учетом ограничений, накладываемых условиями реализации ТП в конкретной производственной системе. В силу этих ограничений многие из предложенных ТР не могут быть реализованы. Вместе с тем ограничения должны быть ранжированы по приоритету их «строгости». Строгое ограничение — это ограничение, которое не может быть снято ни при каких условиях. Некоторые же из ограничений в силу необходимости могут быть сняты. Обычно это происходит в случаях, если в множестве предлагаемых ТР не остается ни одного элемента. Так, ТР об изменениях схем закрепления и установки могут быть отвергнутыпри наличии уже изготовленного приспособления. Однако в случае необходимости уже изготовленное приспособление может быть заменено другим, сконструированным на основе принятого ТР.
Множество возможных ТР, пройдя через фильтр ограничений, становится множеством допустимых ТР. Указанные множества могут совпадать. Множество допустимых ТР должно иметь хотя бы один элемент, в противном случае может быть вновь создано новое множество возможных ТР.
Альтернативные ТР из множества возможных ТР ранжируют по предполагаемой эффективности. Просматривают множества возможных ТР, ориентированные на обеспечение разных параметров качества. Решение, выполнение которого обеспечивает качество по ряду параметров, имеет максимальный приоритет.
Для каждого ТР с использованием модели объекта определяют ожидаемый результат (по выходным переменным), дают комплексную оценку качества ТР, выполняют тщательный анализ воздействия реализации принятого ТР на другие составляющие вектора выходных переменных.
При наличии множества альтернатив ТР оптимизируют с учетом принятых критериев и формируют множество равноэффективных ТР (в частном случае это множество может состоять из одного ТР). Окончательный выбор ТР из множества равноэффективных осуществляет лицо, принимающее решение.
|
При необходимости стабилизации нескольких параметров качества возможен вариант, когда для стабилизации каждого из параметров необходима реализация самостоятельного ТР. В этом случае выполняют процедуру синтеза отдельных ТР в комплексные, желательно меньшего числа или даже единственные. Успех выполнения этой процедуры зависит от опыта и знаний ее исполнителей. Если принятое ТР связано с применением нового СТО, то выдают задание на разработку необходимого информационно-технического обеспечения.
В ряде случаев принятие ТР не требует строгого соблюдения описанной последовательности действий. Это происходит при достаточной очевидности причин отклонений качества и устраняющих их действие ТР.
Автоматические управляющие устройства формируют и реализуют управляющие решения, соответствующие конкретной ситуации, с использованием функциональных подсистем, показанных на рис. 3.3. Информация о состоянии объекта управления (ОУ) от датчиков (Д) поступает на вход подсистемы контроля (ПК). Результаты контроля в соответствии с принятой стратегией контроля, поступают в подсистемы диагностики (ПД) и принятия решений (ППР). Принятое ТР в форме корректирующих воздействий передается в устройство с числовым программным управлением (УЧПУ) и далее в формате сигналов ЧПУ — к объекту управления. Сообщения о принятых и отработанных ТР, а также данные об изменениях контролируемых параметров как сигналы обратной связи поступают от устройства с ЧПУ к подсистемам принятия решений и контроля.
Рис. 3.3. Структура автоматизированного управляющего устройства
Целью рассмотренного устройства является обеспечение качества продукции при автоматической работе оборудования. Параметры качества можно измерять непосредственно на станке, в процессе обработки заготовки либо в специально выделенной контрольной позиции.
Подсистема диагностики предназначена для определения причины и места возможного отказа в технологической системе и выдачи информации для подсистемы принятия решений.
Необходимость диагностики при принятии обоснованных ТР рассмотрим на примере контроля сил резания при точении. Измеряемый силовой параметр может находиться в зоне риска по следующим причинам:
1) затупление инструмента;
2) увеличенный припуск на обработку;
3) изменение твердости материала заготовки;
4) ошибка в управляющей программе.
В зависимости от причины подсистема принятия решения может принять одно из следующих ТР:
1) сменить инструмент;
2) уменьшить глубину резания;
|
3) уменьшить подачу;
4) скорректировать управляющую программу, например путем генерации и введения исправленного кадра.
Подсистема диагностики, по возможности, должна обеспечивать выдачу единственной причины. В противном случае определяется набор (меню) возможных причин, ранжированных по вероятности их появления. В развитых подсистемах диагностики для этого используют специализированное программное обеспечение.
Подсистема принятия решений предназначена для обеспечения стабильного качества выпускаемой продукции при действии дестабилизирующих факторов, а также автоматического продолжения работы после случайного отказа или других нарушений функционирования объекта управления.
Условиями восстановления работоспособности в автоматизированных производственных системах являются:
наличие резервного механизма (подсистемы);
возможность восстановления отказавшего механизма (подсистемы);
возможность организации «обходного пути».
В производственных системах металлообработки, как правило, резервных механизмов нет. Определенный резерв имеется в инструментальном обеспечении при условии установки инструментов-дублеров. Можно резервировать заготовки в накопителях транспортных систем. При поломках или предельном износе инструмента, а также при невозможности продолжения начатой обработки подсистема принятия решений может выбрать следующие ТР:
1) сменить инструмент и продолжить обработку той же заготовки;
2) забраковать обрабатываемую заготовку и заказать новую;
3) отложить начатую заготовку до появления нового инструмента;
4) рискнуть и завершить обработку несмотря на сигналы о предельном износе. Решение принимается исходя из конкретных условий обработки: степени автоматизации системы, стоимости инструмента и заготовки, стоимости простоев оборудования, времени появления нарушений в работе объекта, состояния производственного плана и т. д. Правильность принятого ТР определяется степенью «интеллектуальности» программного обеспечения подсистемы.
Возможность восстановления нормальной работы после отказа характерна для большинства вспомогательных механизмов, в которых движущиеся части имеют склонности к заеданию или «непопаданию». Часто достаточно повторить движения, чтобы восстановить нормальную работу. Во всяком случае необходимо предусмотреть неоднократное повторение подобной попытки. Восстановление возможно и тогда, когда контроль детали зафиксировал неисправимый брак. В этом случае подсистема принятия решений должна обеспечить проведение необходимой соответствующей коррекции для того, чтобы качество изготовления следующих деталей было обеспечено.
Возможность организации «обходного пути» является сложной задачей ситуационного управления ТП, связанной с адаптацией к изменению производственной ситуации. Суть принимаемых при этом решений сводится к определению наиболее рационального в данных условиях продолжения ТП, в общем случае не совпадающего с заданным.
В более простых ситуациях возможности подсистемы принятия решений вполне достаточны для обеспечения нормальной работы объекта управления и производственной системы в целом.
|
|
Индивидуальные очистные сооружения: К классу индивидуальных очистных сооружений относят сооружения, пропускная способность которых...
Поперечные профили набережных и береговой полосы: На городских территориях берегоукрепление проектируют с учетом технических и экономических требований, но особое значение придают эстетическим...
Типы сооружений для обработки осадков: Септиками называются сооружения, в которых одновременно происходят осветление сточной жидкости...
Состав сооружений: решетки и песколовки: Решетки – это первое устройство в схеме очистных сооружений. Они представляют...
© cyberpedia.su 2017-2024 - Не является автором материалов. Исключительное право сохранено за автором текста.
Если вы не хотите, чтобы данный материал был у нас на сайте, перейдите по ссылке: Нарушение авторских прав. Мы поможем в написании вашей работы!