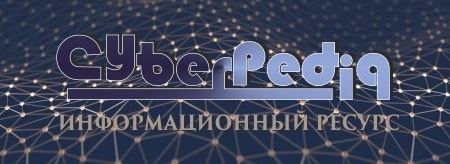
Семя – орган полового размножения и расселения растений: наружи у семян имеется плотный покров – кожура...
Археология об основании Рима: Новые раскопки проясняют и такой острый дискуссионный вопрос, как дата самого возникновения Рима...
Топ:
Характеристика АТП и сварочно-жестяницкого участка: Транспорт в настоящее время является одной из важнейших отраслей народного хозяйства...
Генеалогическое древо Султанов Османской империи: Османские правители, вначале, будучи еще бейлербеями Анатолии, женились на дочерях византийских императоров...
Основы обеспечения единства измерений: Обеспечение единства измерений - деятельность метрологических служб, направленная на достижение...
Интересное:
Лечение прогрессирующих форм рака: Одним из наиболее важных достижений экспериментальной химиотерапии опухолей, начатой в 60-х и реализованной в 70-х годах, является...
Аура как энергетическое поле: многослойную ауру человека можно представить себе подобным...
Наиболее распространенные виды рака: Раковая опухоль — это самостоятельное новообразование, которое может возникнуть и от повышенного давления...
Дисциплины:
![]() |
![]() |
5.00
из
|
Заказать работу |
|
|
Определение станочного приспособления. Области применения приспособлений.
Приспособление – это технологическая оснастка, предназначенная для установки или направления предмета труда и инструмента при выполнении технологических операций.
Станочное приспособление - устройство для базирования и закрепления заготовки или инструмента при обработке на металлорежущем станке. Являются основным видом технологической оснастки.
Станочное приспособление - это не имеющее формообразующих средств вспомогательное орудие производства, предназначенное для установки в нем заготовок с целью изготовления изделий на механообрабатывающем оборудовании.
Приспособления применяют во всех типах производства.
Приспособления применяют при выполнении различных производственных процессов (при транспортировке, контроле, сборке к г. п.).
Универсальные приспособления предназначены для обработки разнообразных деталей. Такие приспособления применяют в единичном и мелкосерийном производствах.
Применение специальных приспособлений является одним из основных путей повышения производительности труда в условиях серийного и массового производства, позволяет производить обработку заготовок без предварительной разметки и выверки.
Кроме того, обработка заготовок в специальных приспособлениях обеспечивает надежное их закрепление, повышенную точность размеров, позволяет производить одновременную обработку нескольких заготовок.
Для массового и крупносерийного производства в большинстве случаев применяют специальные станочные приспособления (НСП).
В условиях среднесерийного и мелкосерийного производства выгодны системы УСП, СРП, УНП, СНП и другие СП многократного применения.
|
В мелкосерийном производстве применяют немеханизированные наладочные приспособления, а в серийном и крупносерийном - пневматические или гидравлические. СНП имеют специализированные базовые агрегаты и могут быть использованы для установки геометрически подобных заготовок, а УНП - универсальные базовые агрегаты и применяются для установки различных заготовок.
2. Преимущества применения приспособлений. Направления совершенствования приспособлений.
Применение станочных приспособлений позволяет:
Устранить разметку заготовок перед обработкой и исключить их выверку на станке по разметке;
Значительно повысить производительность труда в результате сокращения вспомогательного времени, увеличения числа одновременно обрабатываемых заготовок и числа одновременно работающих режущих инструментов, а также повышения режимов резания;
Обеспечить условия для многостаночного обслуживания нескольких станков одним рабочим;
Значительно облегчить труд рабочих-станочников и использовать рабочих с более низкой квалификацией;
Повысить точность изготовления деталей;
Расширить технологические возможности станков;
Создать условия для механизации или автоматизации станков;
Снизить себестоимость изготовления деталей.
Направления совершенствования:
1) использование быстродействующих устройств ДЛЯ зажима деталей, в том числе пневматических, гидравлических, пневмогидравлических;
2) использование поворотных, маятниковых, конвейерных устройств, дающих возможность снимать обработанные детали и устанавливать новые в то время, когда обрабатываются другие детали;
3) применение многоместных и других высокопроизводительных приспособлений;
4) применение устройств для автоматизации загрузки и удаления со станков и машин деталей;
5) применение быстрозажимных резцедержателей, быстросменяемых и быстрозажимных патронов для сверл и других инструментов;
6) использование сменных многошпиндельных головок для сверлильных станков и револьверных настроечных головок для токарно-револьверных станков;
7) разработка и использование быстро переналаживаемых принадлежностей к станкам (тисков, патронов, оправок и др.), технологической оснастки (в том числе универсально-сборной УСП), инструментов (регулируемых и др.) с целью обеспечения возможности групповой обработки деталей;
|
8) Сокращение вспомогательного времени за счет совершенствования конструкций зажимных устройств.
Расчеты при проектировании приспособления. Требования, предъявляемые к приспособлениям.
В расчетной части выполняются следующие этапы:
1. Сбор исходных данных в которые входят операционный эскиз на выполняемую операцию со схемой базирования, данные о материале заготовки, режущем инструменте, режимах резания, сведения о рабочем органе станка, на который монтируется проектируемое приспособление. В задании указывается также тип приспособления согласно принятой классификации.
2. Расчет сил резания.
3. Выбор схемы закрепления заготовки и расчет усилия зажима.
4. Выбор конструкции и расчет зажимного механизма.
5. Выбор конструкции и расчет силового привода.
6. Разработка конструкции корпуса.
7. Разработка вспомогательных элементов.
8. Расчет погрешности установки заготовки в приспособление (выполняется после разработки рабочего чертежа заготовки).
Конструкция приспособления должна отвечать ряду требований, которые необходимо учесть как при выборе составных элементов и устройств, так и при разработке его общей компоновки.
Приспособление должно:
а) обеспечить получение заданной точности обработки.
б) обеспечить заданную производительность операции, быть быстродействующим
в) быть экономически целесообразным.
г) обладать хорошей ремонтоспособностью, быть доступным для ремонта и замены изношенных элементов
д) быть удобным в эксплуатации
е) облегчать труд рабочего.
ж) обеспечивать безопасность работы
з) иметь высокий уровень использования нормализованных и стандартизованных элементов и узлов.
При конструировании и изготовлении приспособлений необходимо обеспечивать их безотказность, долговечность, ремонтопригодность. Приспособления должны быть эргономичными, их обслуживание должно быть удобным и лёгким.
|
6 Экономический анализ приспособления
Порядок проведения технико-экономического анализа применения станочных приспособлений 1. Описание конструкции и принципа работы сравниваемых вариантов приспособлений с указанием их преимуществ и недостатков. 2. Подготовка исходных данных для расчета технико-экономических показателей. 3. Расчет штучного времени с указанием схемы обработки для расчета основного (машинного) времени (см. Приложение 1). 4. Расчет себестоимостей обработки в сравниваемых приспособлениях одной заготовки. 5. Расчет экономического эффекта от применения более совершенного приспособления. 6. Расчет программы выпуска, при которой сравниваемые варианты приспособлений равноценны. 7. Расчет срока окупаемости. 8. Выводы и предложения.
7 Типовые схемы установки заготовок и конструкции установочных элементов приспособлений. Общие требования к установочным элементам
Требования, предъявляемые к установочным элементам:
1. Количество и расположение установочных элементов должно обеспечить необходимую ориентацию заготовки в пространстве, устойчивость и жесткость.
2. Рабочие поверхности установочных элементов должны обладать высокой износостойкостью.
3. Конструкция установочных элементов должна предусматривать быструю их замену при износе или повреждении.
4. Установочные элементы должны быть жесткими и обеспечивать жесткость их сопряжения с корпусом приспособления.
5. Установочные элементы не должны портить базовые поверхности при установке на обрабатываемую поверхность.
6. Рабочие поверхности установочных элементов должны быть по возможности небольших размеров, чтобы исключить влияние макрогеометрии базовой поверхности на точность установки.
Материал установочных элементов: инструментальная углеродистая сталь У10А, У8А, У7А с последующей закалкой до HRC 50-55
Все типовые схемы установки заготовок в приспособлениях разделены на две группы:
· установка заготовок типа «тела вращения»;
· установка заготовок не тел вращения.
Рис. 4.12. Схема базирования в длинную призму:
|
опорные точки 1, 2, 3, 4 – двойная направляющая скрытая база; точка 5 – явная опорная база; точка 6 – опорная скрытая база
Рис. 4.13. Схема базирования заготовки в короткую призму:
точки 1,2,3 – явная установочная база; точки 4, 5 – двойная опорная скрытая база; точка 6 – опорная скрытая база
Рис. 4.18. Базирование в центрах с передним жестким центром
Рис. 4.22. Схема базирования в «координатный угол»
Вспомогательные опоры
Правило 6 точек
Рассмотренная схема обеспечивает полное базирование детали с лишением ее всех степеней свободы, при этом используются три базирующие поверхности, несущие шесть опорных точек.
Установка с помощью шести опор называется установкой по правилу шести точек. Правило это весьма существенно. Почти во всех установках при разных способах базирования соблюдается правило шести точек.
Виды баз
Установочная база – база, используемая для наложения на заготовку или изделие связей, лишающих их трех степеней свободы – перемещения вдоль одной координатной оси и поворотов вокруг двух других осей.
Направляющая база - база, используемая для наложения на заготовку изделие связей, лишающих их двух степеней свободы – перемещения вдоль одной координатной оси и поворота вокруг другой оси.
Опорная база – база, используемая для наложения на заготовку или изделие связей, лишающих их одной степени свободы – перемещения вдоль одной координатной оси или поворота вокруг оси
Погрешность базирования
Погрешность базирования εБ возникает в результате базирования заготовки в приспособлении по технологическим базам, не связанным с измерительными базами. При базировании по конструкторской основной базе, являющейся и технологической базой, погрешность базирования не возникает. Погрешности базирования можно определять расчетом геометрических связей принятой схемы базирования. Погрешности εБ возникают и при зажатии под действием сил зажатия, контактных деформаций заготовки и упругих деформаций приспособления.
Погрешность закрепления
Погрешность закрепления εЗ образуется из погрешностей, возникающих до приложения силы зажатия и при зажатии. При работе на предварительно настроенных станках режущий инструмент, а также упоры и копиры устанавливают на размер от установочных поверхностей приспособления до приложения нагрузки, поэтому сдвиг установочных баз приводит к погрешностям закрепления. Погрешности закрепления определяют расчетным и опытным путем для каждого конкретного способа закрепления заготовок (значения их приводят в справочных таблицах).
|
Погрешность положения
Погрешность положения заготовки, вызванная неточностью приспособления, включает в себя три элемента:
где – погрешность изготовления и сборки приспособления;
– погрешность, вызванная износом установочных элементов приспособления;
– погрешность установки и фиксации приспособления на станке.
Составляющая характеризует неточность положения установочных элементов приспособления. При использовании одного приспособления она представляет собой систематическую постоянную погрешность; ее нередко можно частично или полностью устранить соответствующей настройкой станка. При использовании нескольких одинаковых приспособлений (приспособлений-дублеров и приспособлений-спутников) эта величина не компенсируется настройкой станка и входит полностью в состав
.
Технологические возможности изготовления приспособлений в современных инструментальных цехах обеспечивают выдерживание составляющей в пределах 0,01 – 0,005 мм (для прецизионных приспособлений еще точнее).
Составляющая характеризует изменение положения контактных поверхностей установочных элементов в результате их износа в процессе эксплуатации приспособлений. Интенсивность износа установочных элементов зависит:
· от конструкции и размеров установочных элементов;
· от материала и веса заготовки;
· от состояния базовых поверхностей заготовок;
· от условий установки заготовки в приспособлении и снятия ее (с ударом, скольжением).
Базирование заготовок для цилиндрических деталей Примеры
Любая цилиндрическая деталь имеет две плоскости симметрии, которые, пересекаясь, образуют ось. Эта особенность и позволяет использовать при базировании цилиндрической детали в качестве базы ось. Базирование цилиндрической детали с использованием двусторонних связей представлено на рисунке 1. Базирование цилиндрической детали
Рис. 1
При базировании цилиндрической детали в качестве баз используются ось и две плоские поверхности, которые образуют комплект баз, включающий в себя двойную направляющую и две опорные базы.
Двойной направляющей базой называется база, которая накладывает 4 двусторонние связи и лишает, тем самым, деталь 4-х перемещений. На практических схемах двойная направляющая база отображается 4 опорными точками. Например, на рисунке 1 первая двусторонняя связь лишает деталь перемещения вдоль оси OZ, вторая – вращения вокруг оси OY, третья — перемещения в вдоль оси OY, четвертая — вращения вокруг оси OZ.
Из двух опорных баз у цилиндрической детали одна лишает деталь перемещения, а другая вращения. На рисунке 1 пятая опорная точка лишает деталь перемещения вдоль оси OX, а шестая – вращения вокруг оси OX.
Теория базирования. Базирование и базы. Базирование призматической детали.
Деталь типа «диск», как правило, имеет две плоскости симметрии, которые, пересекаясь, образуют ось, и хорошо развитые торцовые поверхности. Базирование детали типа «диск» с использованием двусторонних связей приведено на рисунке 2.
Схема базирования диска
Рис. 2
При базировании детали типа «диск» в качестве баз используются ось и две плоскости, которые образуют комплект, включающий в себя установочную, двойную опорную и опорную базы.
Базирование на призмах
Рис. 1. Установка цилиндрической заготовки в призме. Комплект баз: двойная направляющая (точки 1, 2, 3, 4); опорные (точки 5, 6); а – теоретическая схема базирования; б - схема установки
При базировании цилиндрической детали на призме, деталь лишается четырёх степеней свободы четырьмя неподвижными одностоечными опорами. Оставшихся двух степеней свободы – перемещение детали вдоль оси у (вдоль призмы) и вращение детали вокруг оси – она лишается с помощью двух одноточечных опор.
Ступенчатые валы нельзя устанавливать на две неподвижные призмы. При установке ступенчатых валов следует применять одну призму, неподвижную по высоте, а другую – регулируемую.
Оправки
Оправки по конструктивным особенностям разделяют на жесткие и разжимные.
Жесткие оправки бывают трех видов:
- конические;
- цилиндрические с установкой заготовки с зазором;
- цилиндрические с установкой заготовки с натягом.
Коническую оправку выполняют с конусностью 1:2000-1:4000 Заготовка имеет цилиндрическое отверстие, обработанное с точностью Н6-Н7. Заготовка заклинивается на оправке, и удерживается силами трения от проворота при обработке. Точность центрирования 0,005...0,01 мм. Применяют в единичном и мелкосерийном производстве.
На цилиндрическую оправку с натягом заготовка напрессовывается. Используя подкладные кольца при запрессовке, заготовку точно ориентируют по длине оправки. Точность центрирования 0,005...0,01 мм. Оправки применяют в крупносерийном производстве при обработке на токарных многорезцовых п/а и др.
Цилиндрическая оправка с зазором. Положение заготовки по длине определяется буртом оправки. От проворачивания заготовка удерживается трением на торцах от затяжки гайкой или шпонкой (шлицами при наличии таковых). Отверстие заготовки обрабатывают с точностью Н7. Точность центрирования 0,02...0,03 мм.
Все жесткие оправки, как правило, центровые.
Разжимные оправки отличаются от жестких тем, что имеют подвижные элементы, перемещающиеся в радиальном направлении. Заготовка устанавливается на оправку свободно с зазором. Разжимающиеся элементы оправки фиксируют заготовку на ней, выбирая зазор между оправкой и заготовкой. Типы разжимных оправок:- цанговые; - кулачковые; - гидропластные; - с гофрированными втулками; - с тарельчатыми пружинами.
Кулачковые оправки допускают установку заготовок с необработанным или грубо обработанным базовым отверстием. Используется для закрепления толстостенных заготовок. Точность центрирования 0,05...0,1 мм.
Оправка с гирдопластом. Базовое отверстие заготовки обрабатывают с точностью Н7-Н8. Точность центрирования 0,005...0,01 мм.
Оправка с гофрированными втулками. Обеспечивает точность центрирования 0,002-0,003 мм при обработке базового отверстия заготовки с точностью Н6-Н7. При приложении осевой силы цилиндрическая часть втулок выпучивается, и прочно закрепляет заготовку. Втулки выполняют из стали 38Х, У10А или 65Г с термообработкой HRC45-50.
Оправка с тарельчатыми пружинами. Обеспечивает надежное закрепление заготовки при точности базового отверстия не ниже Н11. Точность центрирования 0,01...0,02 мм. Пружины выполняют из стали 60С2А с термообработкой HRC40-45.
По способу установки на станке, независимо от вида оправки, оправки бывают: - консольные; - цанговые.
Консольные устанавливаются в шпиндель станка и присоединяются к нему либо конусным хвостовиком, либо посадочным пояском и винтами.
Цанговые оправки для установки заготовок с точностью базового отверстия Н8-Н12 обеспечивают точность центрирования 0,02-0,04 мм.
Установочные пальцы
Установочные пальцы применяются для установки деталей по плоскостям и отверстиям. Установочные пальцы бывают постоянные и сменные. Постоянные пальцы запрессовываются в корпус приспособления по посадке в натяг , а диаметры их установочных поверхностей выполняется по посадке g 6 или f 9 в зависимости от требуемой точности базирования.
Сменные пальцы применяются при интенсивной эксплуатации приспособления, когда они сравнительно быстро изнашивается и заменяются. Пальцы монтируются во втулке по посадке .
Независимо от того, применяются ли установочные пальцы постоянные или сменные, они подразделяются на цилиндрические и срезанные. Цилиндрические пальцы лишают двух степеней свободы (двух перемещений перпендикулярному направлению оси пальца). Срезанные пальцы лишают одной степени свободы (вращения вокруг оси параллельной оси пальца). При этом постоянные опоры бывают нормальные и высокие.
Пальцы могут закрепляться винтами или гайками. При базировании детали по плоскости и двум отверстиям пальцы обычно применяют в сочетании с опорными пластинами. При этом один палец выполняют цилиндрическим, а другой срезанным (ромбическим). Опорные пластины могут быть выполнены заодно с пальцем, а в случае большого их износа – раздельно. В этом случае для предотвращения от поворота пальцев иногда применяют штыри или шпонки.
Установку заготовок базовыми отверстиями в стационарные приспособления производят на консольные цилиндрические пальцы. В зависимости от технических условий на обработку применяют длинные и короткие пальцы. Длинным считается палец, у которого отношение L/d>l. Длинные пальцы применяют, когда необходимо обеспечить условие перпендикулярности базового отверстия относительно обрабатываемого торца. Если требуется выдержать условие параллельности обрабатываемого и базового торцов, заготовку устанавливают на короткий палец.
21. Погрешность базирования при установке на один палец
При установке обрабатываемых заготовок на оправку или палец возникают погрешности базирования из-за зазора
При посадке без зазора (разжимной палец) погрешность базирования для размера = 0, т.к. конструкторская и технологическая база совмещены, а для размера А равна половине допуска на диаметр D заготовки т.е.
При наличии зазора (жесткий палец) погрешность базирования для этого же размера возрастает на величину диаметрального зазора D
22.Установка заготовок по двум отверстиям и плоскости
Установка по двум отверстиям и плоскости, перпендикулярной осям отверстий, используется очень широко при обработке деталей малых и средних размеров типа корпусов, плит и др. Базирование приспособлений – спутников на позициях автоматических линий осуществляется по этой схеме. Теоретическая схема базирования дана на рисунке 2.22 – теоретическая схема базирования по плоскости и двум отверстиям. На плоскости расположены три опорные точки (1, 2, 3) она является установочной базой.
Рисунок 2.22 - Теоретическая схема базирования по плоскости и двум отверстиям.
В качестве направляющей базы могут использоваться либо ось двух цилиндрических поверхностей (точки 4,5) либо образующие этих отверстий (точки 41, 51). В качестве опорной базы используют либо ось одного из отверстий (точка 6) либо образующую этого отверстия (точка 61). Таким образом, в качестве двойной опорной базы (рисунок 2.22) используется либо ось отверстия, либо образующая этого отверстия.
Общие положения о зажимных элементах(механизмах).Требование, предьявляемые к зажимным механизмам.
Назначение зажимных приспособлений – это обеспечение надежного контакта заготовки с установочными элементами и предотвращение смещения и вибрации ее в процессе обработки. Требования к зажимным элементам:
- надежность в работе;
- простота конструкции;
- удобство обслуживания;
- не должны вызывать деформацию заготовок и порчу их поверхностей;
- не должны сдвигать заготовку в процессе ее закрепления с установочных элементов;
- закрепление и открепление заготовок должно производиться с минимальной затратой труда и времени;
- зажимные элементы должны быть износостойкими и по возможности сменными.
Зажимными называются механизмы, устраняющие возможность вибрации или смещения заготовки относительно установочных элементов под действием собственного веса и сил, возникающих в процессе обработки.
Зажимные механизмы не нужны:
1 Когда обрабатывают тяжёлую, устойчивую заготовку, по сравнению с весом которой силы обработки малы;
2 Когда силы резания приложены так, что они не могут нарушить положение заготовки, достигнутое базированием.
Требования к зажимным механизмам:
1 При зажиме не должно нарушаться положение заготовки достигнутое базированием. Это достигается рациональным выбором направления и точки приложения силы зажима;
2 Зажимы не должны вызывать деформации заготовок или порчи их поверхностей;
3 Сила зажима рассчитывается как минимально необходимая для обеспечения неподвижности заготовки;
4 Зажим и открепление заготовок необходимо производить с минимальной затратой сил и времени рабочего;
5 Зажимные устройства не должны воспринимать силы резания;
6 Зажимной механизм должен быть простым по конструкции, удобным и безопасным;
7 При выборе направления зажимной силы должны соблюдаться правила:
· сила зажима должна быть перпендикулярна поверхности установочного элемента;
· сила зажима должна быть направлена на тот элемент, с которым заготовка имеет наибольшую площадь контакта;
· направление Q должно совпадать с направлением веса заготовки.
Винтовые зажимы
Винтовые зажимы применяются в приспособлениях с ручным и механизированным закреплением заготовок, а также на автоматических линиях при использовании приспособлений–спутников. Эти зажимные устройства просты, компактны и надежны в работе. При проектировании винтовых зажимов выполняются расчеты номинального диаметра винта и момента на рукоятке.
Винтовые механизмы используют как для непосредственного зажима, так и в сочетании с другими механизмами. Непосредственный зажим осуществляется либо винтом при неподвижной резьбовой втулке, либо гайкой при неподвижной шпильке
34. клиновые механизмы
Клин очень широко используют в зажимных механизмах приспособлений, этим обеспечивается простота и компактность конструкции, надежность в работе. Клин может быть как простым зажимным элементом, действующим непосредственно на заготовку, так и входить в сочетание с любым другим простым при создании комбинированных механизмов.
Назначение клиновых механизмов: увеличение исходной силы привода, перемену направления исходной силы, самоторможение механизма (способность сохранять силу зажима Q при прекращении действия силы W, создаваемой приводом). Если клиновой механизм применяют для перемены направления силы зажима, то угол клина обычно равен 45º, а если для увеличения силы зажима или повышения надежности, то угол клина принимают равным 6 – 15º (углы самоторможения).
35. клино- плунжерные механизмы
Клиноплунжерные механизмы применяются с одним, двумя и большим числом плунжеров. Одно- и двухплунжерные обычно используются в качестве усилителей привода; многоплунжерные — в качестве центрирующих механизмов патронов и оправок.
Плунжер представляет собой промежуточную деталь нажимного действия (обычно цилиндрический валик), служащую для передачи усилия от одного элемента механизма к другому или воздействующею непосредственно на зажимаемую заготовку. Конструкция и размеры плунжеров стандартизованы.
36 Эксцентриковый зажим является зажимным элементом усовершенствованных конструкции. Эксцентриковые зажимы (ЭЗМ) используются для непосредственного зажима заготовок и в сложных зажимных системах.
Эксцентриковый зажим хотя и отличается быстродействием, но не обеспечивает большой силы зажима детали, поэтому его применяют лишь при сравнительно небольших силах резания.
Преимущества:
-простота и компактность конструкции;
-широкое использование в конструкции стандартизованных деталей;
-удобство в наладке;
-способность к самоторможению;
-быстродействие (время срабатывания привода около 0.04 мин).
Недостатки:
-сосредоточенный характер сил, что не позволяет применять эксцентриковые механизмы для закрепления нежестких заготовок;
-силы закрепления круглыми эксцентриковыми кулачками нестабильны и существенно зависят от размеров заготовок;
-пониженная надежность в связи с интенсивным изнашиванием эксцентриковых кулачков.
Рис. 113. Эксцентриковый зажим: а - деталь не зажата; б - положение при зажатой детали
Круглый эксцентрик 1, представляющий собой диск со смещенным относительно его центра отверстием, показан на рис. 113, а. Эксцентрик свободно устанавливается на оси 2 и может вращаться вокруг нее. Расстояние е между центром С диска 1 и центром О оси называется эксцентриситетом.
37 Рычажный механизм механизм, состоящий из звеньев, соединённых между собой в низшие кинематические пары (См. Кинематическая пара). Р. м. бывают плоские и пространственные. В плоских Р. м. звенья соприкасаются по окружности (шарниры, вращательные пары) и по линии (поступательные пары). В пространственном Р. м. звенья соединяются по цилиндрическим или сферическим поверхностям (вращательные пары) и по плоскости (поступательные пары). Часто в технической литературе Р. м. называют стержневыми шарнирными механизмами. К ним относят также кулисные и кривошипно-ползунные механизмы. Р. м. проще в изготовлении, прочнее и более износостойки, чем кулачковые и зубчатые механизмы, поэтому Р. м. применяют для передачи больших усилий в прессах, ковочных машинах, двигателях внутреннего сгорания, погрузчиках и т. п.
38 пружинный зажим - это современная конструкция для замены системы.
Прост в использовании и универсален.
Предназначен для использования с арматурой или проволокой диаметром 6-10 мм.
Бывает обычный и усиленный.
Обычный выдерживает 2 тонны,усиленный 3.
39 Многократные зажимы приводятся в действие от одного силового источника и зажимают одновременно несколько или одну деталь в нескольких точках одновременно. Применение многократных зажимов позволяет сократить вспомогательное время на операции. Основным требованием, предъявляемым к многократным зажимам, является равенство зажимных сил. Для того, чтобы обеспечить равенство сил зажима, ведомые звенья механизма должны составлять сблокированную «плавающую» систему, развивающую силу зажима независимо от колебаний размеров заготовок.
Известно много конструкций многократных зажимов приспособлений, которые можно распределить на группы, приняв за классификационный признак направление сил зажима. Можно выделить следующие группы: последовательного действия, передающие силу зажима в одном направлении от заготовки к заготовке (закрепление пакета заготовок); параллельного действия, зажимающие детали в нескольких параллельных направлениях; со встречными силами зажима; с пересекающимся направлением сил; комбинированные механизмы, представляющие собой соединение механизмов первых групп.
40. Принципы положенные в основу самоцентрирующихся механизмов
Самоцентрирующие механизмы различаются между собой формой рабочей поверхности подвижных элементов и конструкцией механизма, обеспечивающего взаимосвязанное их движение. По первому признаку различают призматические и кулачковые механизмы, а по второму признаку – винтовые, реечно-зубчатые, спирально-реечные, клиновые (клиноплунжерные и клиношариковые), с упругодеформируемыми элементами (цанговые, мембранные, гидропластовые). Границы применимости различных по конструкции механизмов определяются двумя их характеристиками – величиной присущей им погрешности центрирования и величиной создаваемой силы зажима.
Принципиальная схема винтового самоцентрирующего механизма приведена на рис. 2.48. Такие механизмы имеют большую погрешность центрирования (0,3-0,5 мм). В то же время с помощью этого механизма можно создать большую силу зажима, легко скомпоновать с механизированным приводом, поэтому их широко применяют на черновых и получистовых операциях.
![]() |
Мембранные механизмы
Основным рабочим элементом в этих механизмах являются мембраны, упругие свойства которых используется для центрирования и закрепления заготовок. В машиностроении мембранные механизмы для установки заготовок применяются с плоскими и кольцевыми мембранами. Первые выполняются в виде потронов, вторые в виде оправок. Плоские мембраны изготавливают из сталей 65Г и 30ХГС с термообработкой.
Гидравлически механизмы
Гидравлические механизмы — аппараты и инструменты, использующие в своей работе кинетическую или потенциальную энергию жидкости. К гидравлическим механизмам относят гидравлические машины.
В таких механизмах сила высокого давления гидравлической жидкости преобразуется механизмами различных гидравлических моторов и цилиндров. Потоком жидкости можно управлять напрямую или автоматически — посредством управляющих клапанов. Распределение потока происходит по специальным гидравлическим шлангам и трубкам.
Гидравлические механизмы имеют большую популярность в машиностроении благодаря тому, что возможно передавать огромную энергию через тонкие трубки и гибкие шланги.
Пневматические приводы
Исходной энергией в пневматических приводах является энергия сжатого воздуха. Пневмопривод широко используют в приспособлениях благодаря его быстродействию (скорость срабатывания – доли секунды), простоте конструкции, легкости и простоте управления, надежности и стабильности в работе. Вместе с тем пневмопривод имеет недостатки – неплавное перемещение штока, низкое давление воздуха и шум при выпуске отработанного воздуха.
Пневмопривод включает в себя следующие части: источник сжатого воздуха – обычно цеховая или заводская компрессорная установка; силовой агрегат – пневмодвигатель, преобразующий энергию сжатого воздуха в силу W на штоке; пневмоаппаратура – контролирующие приборы, распределительные, предохранительные устройства и т. д.; воздухопроводы.
46 Классификация по компоновке приводов.
Силовой агрегат привода представляет собой преобразователь какого-
либо вида энергии в механическую, необходимую для работы зажимного
механизма.
В приспособлении используют следующие приводы: пневма-тический, гидравлический, магнитный, вакуумный.
Определение станочного приспособления. Области применения приспособлений.
Приспособление – это технологическая оснастка, предназначенная для установки или направления предмета труда и инструмента при выполнении технологических операций.
Станочное приспособление - устройство для базирования и закрепления заготовки или инструмента при обработке на металлорежущем станке. Являются основным видом технологической оснастки.
Станочное приспособление - это не имеющее формообразующих средств вспомогательное орудие производства, предназначенное для установки в нем заготовок с целью изготовления изделий на механообрабатывающем оборудовании.
Приспособления применяют во всех типах производства.
Приспособления применяют при выполнении различных производственных процессов (при транспортировке, контроле, сборке к г. п.).
Универсальные приспособления предназначены для обработки разнообразных деталей. Такие приспособления применяют в единичном и мелкосерийном производствах.
Применение специальных приспособлений является одним из основных путей повышения производительности труда в условиях серийного и массового производства, позволяет производить обработку заготовок без предварительной разметки и выверки.
Кроме того, обработка заготовок в специальных приспособлениях обеспечивает надежное их закрепление, повышенную точность р
|
|
Семя – орган полового размножения и расселения растений: наружи у семян имеется плотный покров – кожура...
История создания датчика движения: Первый прибор для обнаружения движения был изобретен немецким физиком Генрихом Герцем...
Типы сооружений для обработки осадков: Септиками называются сооружения, в которых одновременно происходят осветление сточной жидкости...
История развития пистолетов-пулеметов: Предпосылкой для возникновения пистолетов-пулеметов послужила давняя тенденция тяготения винтовок...
© cyberpedia.su 2017-2024 - Не является автором материалов. Исключительное право сохранено за автором текста.
Если вы не хотите, чтобы данный материал был у нас на сайте, перейдите по ссылке: Нарушение авторских прав. Мы поможем в написании вашей работы!