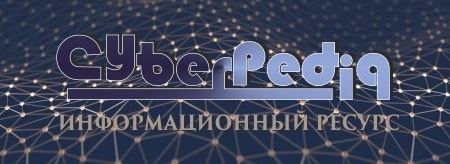
Адаптации растений и животных к жизни в горах: Большое значение для жизни организмов в горах имеют степень расчленения, крутизна и экспозиционные различия склонов...
Механическое удерживание земляных масс: Механическое удерживание земляных масс на склоне обеспечивают контрфорсными сооружениями различных конструкций...
Топ:
Определение места расположения распределительного центра: Фирма реализует продукцию на рынках сбыта и имеет постоянных поставщиков в разных регионах. Увеличение объема продаж...
Техника безопасности при работе на пароконвектомате: К обслуживанию пароконвектомата допускаются лица, прошедшие технический минимум по эксплуатации оборудования...
Интересное:
Как мы говорим и как мы слушаем: общение можно сравнить с огромным зонтиком, под которым скрыто все...
Наиболее распространенные виды рака: Раковая опухоль — это самостоятельное новообразование, которое может возникнуть и от повышенного давления...
Лечение прогрессирующих форм рака: Одним из наиболее важных достижений экспериментальной химиотерапии опухолей, начатой в 60-х и реализованной в 70-х годах, является...
Дисциплины:
![]() |
![]() |
5.00
из
|
Заказать работу |
|
|
В курсовом проекте расчет на прочность производится только для основных деталей в соответствии с заданием на курсовой проект. Прежде чем приступить к расчету деталей на прочность, необходимо: выбрать или установить материал и термообработку данной детали; выяснить, какие силы и в каких сечениях создают опасные напряжения; установить, все ли силы определены в динамическом расчете или необходимо дополнительно произвести расчеты по их определению. К расчету каждой детали должен прилагаться эскиз с указанием опасных сечений и необходимых для расчета размеров. Кроме того, в расчетах на прочность должны быть указаны допустимые напряжения и запасы прочности для оценки прочностных характеристик проектируемой детали или узла.
Предпосылки к расчету и расчетные режимы
Расчет деталей с целью определения напряжений и деформаций, возникающих при работе двигателя, производится по формулам сопротивления материалов и деталей машин. До настоящего времени большинство из используемых расчетных выражений дают лишь приближенные значения напряжений.
Несоответствие расчетных и фактических данных объясняется различными причинами, основными из которых являются:
Отсутствие действительной картины распределения напряжений в материале рассчитываемой детали; использование приближенных расчетных схем действия сил и места их приложения; наличие трудно учитываемых знакопеременных нагрузок и невозможность определения их действительных значений; трудность определения условии работы многих деталей двигателя и их термических напряжений; влияние не поддающихся точному расчету упругих колебаний; невозможность точного определения влияния состояния поверхности, качества обработки (механической и термической), размеров детали и т. д. на величину возникающих напряжений.
|
В связи с этим применяемые методы расчета позволяют получить напряжения и деформации, являющиеся лишь условными величинами и характеризующие только сравнительную напряженность рассчитываемой детали.
Основными нагрузками, действующими на детали двигателя, являются силы давления газов в цилиндре и инерции поступательно и вращательно движущихся масс, а также усилия от упругих колебаний и тепловых нагрузок.
Нагрузка от давления газов непрерывно изменяется в течение рабочего цикла и имеет максимальное значение лишь на сравнительно небольшом участке хода поршня. Нагрузка от инерционных сил имеет периодический характер изменения и в быстроходных двигателях иногда достигает значений, превышающих нагрузку от давления газов. Указанные нагрузки являются источниками различных упругих колебаний, представляющих опасность при явлениях резонанса.
Усилия от температурных нагрузок, возникающие в результате выделения тепла при сгорании рабочей смеси и трения, снижают механическую прочность материалов и вызывают дополнительные напряжения в сопряженных деталях при их различном нагревании и различном линейном (или объемном) расширении.
Расчетные режимы
Величина и характер изменения основных нагрузок, воздействующих на детали двигателя, зависят от эксплуатационного режима работы двигателя. Обычно рассчитывают детали для режимов, на которых они работают в наиболее тяжелых условиях.
Для карбюраторных двигателей (рисунок 27, а) за основные расчетные принимают режимы:
1 Максимального крутящего момента Меmах при частоте вращения nM = (0,4÷0,6)nN, когда давление газов достигает наибольшего значения рz max, а силы инерции сравнительно малы;
2 Номинальной мощности NeN при частоте nN, когда все расчеты деталей производятся от совместного действия газовых и инерционных нагрузок;
|
3Максимальной частоты вращения при холостом ходе nx.xmax=(1,05÷1,20)nN. Когда силы инерции достигают наибольших значений, а давление газов незначительно или даже равно нулю (при работе двигателя с ограничителем частоты вращения или с упорным винтом регулировки
частоты вращения на холостом ходу).
Для быстроходных дизелей (рисунок 27, б) принимают расчетные режимы:
1 Номинальной мощности NeN при частоте вращения nN, когда давление достигает максимального значения рzmax, а детали рассчитывают от совместного действия газовых и инерционных нагрузок;
2 Максимальной частоты вращения при холостом ходе nx.xmax =(1,04÷1,07)nN, при котором силы инерции достигают наибольших значений (при работе двигателя с регулятором).
При расчетах деталей карбюраторных двигателей максимальное давление газов рzmax определяют или по тепловому расчету, проведенному для режима максимального крутящего момента, или приближенно принимают равным расчетному (без учета скругления индикаторной диаграммы) максимальному давлению рz сгорания, полученному по тепловому расчету для режима номинальной мощности. Инерционными силами при расчетах на режиме максимального крутящего момента пренебрегают.
а — карбюраторный двигатель; б — дизель с наддувом
Рисунок 27 – К выбору расчетных режимов работы двигателя
При расчетах на режиме номинальной мощности условно принимают, что максимальная газовая сила Рz действует совместно с максимальной инерционной силой в в. м. т. Величину максимальной газовой силы определяют по тепловому расчету для режима номинальной мощности с учетом скругления индикаторной диаграммы.
При расчетах на режиме максимальной частоты вращения при холостом ходе давлением газов пренебрегают.
|
|
Археология об основании Рима: Новые раскопки проясняют и такой острый дискуссионный вопрос, как дата самого возникновения Рима...
Биохимия спиртового брожения: Основу технологии получения пива составляет спиртовое брожение, - при котором сахар превращается...
Индивидуальные и групповые автопоилки: для животных. Схемы и конструкции...
История развития хранилищ для нефти: Первые склады нефти появились в XVII веке. Они представляли собой землянные ямы-амбара глубиной 4…5 м...
© cyberpedia.su 2017-2024 - Не является автором материалов. Исключительное право сохранено за автором текста.
Если вы не хотите, чтобы данный материал был у нас на сайте, перейдите по ссылке: Нарушение авторских прав. Мы поможем в написании вашей работы!