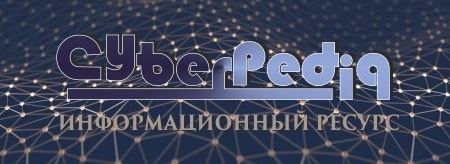
Биохимия спиртового брожения: Основу технологии получения пива составляет спиртовое брожение, - при котором сахар превращается...
Механическое удерживание земляных масс: Механическое удерживание земляных масс на склоне обеспечивают контрфорсными сооружениями различных конструкций...
Топ:
Марксистская теория происхождения государства: По мнению Маркса и Энгельса, в основе развития общества, происходящих в нем изменений лежит...
Устройство и оснащение процедурного кабинета: Решающая роль в обеспечении правильного лечения пациентов отводится процедурной медсестре...
Выпускная квалификационная работа: Основная часть ВКР, как правило, состоит из двух-трех глав, каждая из которых, в свою очередь...
Интересное:
Аура как энергетическое поле: многослойную ауру человека можно представить себе подобным...
Влияние предпринимательской среды на эффективное функционирование предприятия: Предпринимательская среда – это совокупность внешних и внутренних факторов, оказывающих влияние на функционирование фирмы...
Лечение прогрессирующих форм рака: Одним из наиболее важных достижений экспериментальной химиотерапии опухолей, начатой в 60-х и реализованной в 70-х годах, является...
Дисциплины:
![]() |
![]() |
5.00
из
|
Заказать работу |
Предел прочности на изгиб и твёрдость порошкового твёрдого сплава зависят от содержания в нём кобальта (Со). Чем больше его в твёрдом сплаве и чем крупнее зёрна карбидов, тем выше предел прочности на изгиб, но тем ниже твёрдость. Однако повышение содержания Со ≥ 15 % нарушает сплошной каркас из зёрен карбида и резко снижает предел прочности на изгиб. В случае уменьшения содержания Со и применения мелкозернистых карбидов, которые лучше растворяются в кобальте, вязкость и предел прочности на изгиб снижаются, но твёрдость и износостойкость увеличиваются. Удельный вес характеризует степень пористости. Высокая теплопроводность способствует отводу тепла от режущей кромки и увеличивает стойкость инструмента.
Красностойкость твёрдых сплавов, т.е. способность сохранять структуру и режущие свойства при высоких температурах, значительно выше красностойкости быстрорежущих сталей. При этом чем меньше Со в сплаве и чем он мелкозернистее, тем выше красностойкость.
Слипаемость или сцепление твёрдого сплава с обрабатываемым материалом резко ухудшает обрабатываемость, особенно стальных деталей. Титановольфрамовые твёрдые сплавы группы ТК отличаются меньшей слипаемостью, которая начинается у них при более высоких температурах, чем у вольфрамовых ВК. Кроме того, чем меньше в твёрдом сплаве Со, тем меньше слипаемость.
Разряд.
1. Антифрикционные сплавы. Пористые, пропитанные маслом подшипники очень удобны в труднодоступных узлах трения и обеспечивают высокую износостойкость при малом коэффициенте трения. Они могут заменять бронзу и позволяют более экономно расходовать цветные металлы. В связи с наличием пор для тяжёлонагруженных подшипников не применимы.
Пористые бронзовые подшипники изготавливают из смеси порошков 88 %Cu, 10 %Sn, 2 % графита, после прессования и спекания они отжигаются при Т=740 0С.
Фрикционные материалы. К ним предъявляются требования: высокий коэффициент трения, обеспечивающий плавность торможения и минимальную пробуксовку, износостойкость, прирабатываемость, высокая теплопроводность. Ф. материалы изготавливаются из порошков Cu, Sn, Fe с добавками Si, SiO2, асбеста. В автомобильной промышленности для работы в масле применяется сплав: 60 % Cu, 10 % Sn, 4 % Fe, 7 % Pb, 4 % графита, 8 % пульвер-бакелита и 7 % асбеста. Так как ф. сплавы обладают высокой прочностью, они применяются в виде тонкого слоя на стальном диске или на стальной ленте.
Пористые фильтры. Из шарообразных порошков бронзы или сплава никеля с медью изготавливаю металлические фильтры с объёмом пор, достигающим 80 % от общего объёма изделия. Их применяют в химической промышленности, а также в качестве топливных фильтров в двигателях.
Электротехнические сплавы. Постоянные магниты небольшого размера, полученные из порошков Fe-Al-Ni сплавов (альни) или Fe-Al-Ni-Co (альнико), отличаются мелкозернистостью, в отличие от литых магнитов из этих сплавов. Допуски в размерах гораздо уже, что сводит до минимума механическую обработку. Порошковые сплавы позволяют соединить жаро - и износостойкость W, Mo, Ni и графита с высокой электропроводностью Cu и Ag. Из них изготавливают электрические контакты.
Тема № 9.
Защита металлов от коррозии
Разряд.
Коррозией называют разрушение материалов под влиянием окружающей среды в результате её химического или электрохимического воздействия (коррозия происходит от латинского слова «corrodere» - разъедать, разрушать).
Обычно рассматривают коррозию металлических материалов. В зависимости от свойств окружающей среды и характера её физико-химического воздействия на материал различают:
1) Химическую коррозию, обусловленную воздействием сухих газов, а так же жидкостей, не являющихся электролитами (нефть, бензин, фенол).
2) Электрохимическую коррозию, обусловленную воздействием жидких электролитов: водных растворов солей, кислот, щелочей, влажного воздуха, грунтовых вод, т.е. растворов, содержащих ионы и являющихся проводниками электричества.
Химическая коррозия. Наиболее распространённым видом является газовая коррозия (особенно усиливающаяся при высоких температурах), т.е. процесс взаимодействия с кислородом или активными газовыми средами (сернистый газ, сероводород, пары серы и т.д.). При газовой коррозии разрушаются такие ответственные узлы и детали, как лопатки газовых турбин, сопла реактивных двигателей, арматура печей.
В производственных условиях чаще всего сталкиваются с окислением металлов, в случае сплавов на основе железа – с образованием окалины. Защитные свойства металлов от окисления обусловлены образованием сплошных оксидных плёнок на их поверхности. Только сплошная оксидная плёнка способна эффективно защитить металл от коррозии. Помимо сплошности, оксидные плёнки должны обладать высокими механическими свойствами, хорошо сцепляться с металлом и иметь достаточную толщину, обеспечивающую высокие защитные характеристики. Этим требованиям удовлетворяет плёнка оксида хрома Cr2O3, что обусловливает высокую устойчивость против коррозии сталей и жаростойких сплавов с высоким содержанием хрома.
2. Электрохимическая коррозия – наиболее распространённый вид коррозии металлов.
При электрическом контакте двух металлов, обладающих разными электродными (электрохимическими) потенциалами и находящихся в электролите, образуется гальванический элемент. Поведение металлов зависит от значения их электродного потенциала. Металл, имеющий более отрицательный электродный потенциал (анод), отдаёт положительно заряженные ионы в раствор и растворяется. Избыточные электроны перетекают по внешней цепи в металл, имеющий более высокий электродный потенциал (катод). Катод при этом не разрушается, а электроны из него удаляются во внешнюю среду. Чем ниже электродный потенциал металла по отношению к стандартному водородному потенциалу, принятому за нулевой уровень, тем легче металл отдаёт ионы в раствор, тем ниже его коррозионная стойкость.
Многообразие процессов электрохимической коррозии и условий её проявления обусловили широкий диапазон способов защиты от этого явления.
Методы защиты от коррозии можно объединить в следующие группы:
1) Нанесение защитных покрытий и плёнок;
2) Изменение электрохимического потенциала защищаемого материала по отношению к среде на границе фаз;
3) Модификация коррозионной среды.
1. Применение защитных покрытий и плёнок.
Борьба с коррозией с применением защитных покрытий является наиболее распространённым способом. Его эффективность зависит не только от выбора подходящего покрытия, но и от соответствующей обработки (подготовки) поверхности материала. Подготовка поверхности состоит в мытье, обезжиривании, механической очистке шлифованием, полированием, очистке щётками или дробеструйной обработке. Чистую поверхность получают также химическим или электролитическим травлением в растворах кислот.
В качестве защитных покрытий применяют металлические (гальванические) и неметаллические (лакокрасочные) покрытия.
В зависимости от применяемых материалов, характера воздействия деталей механизма, окружающую среду, прибегают к выбору того или другого вида защитного антикоррозионного покрытия, которое должно отвечать следующим требованиям:
- надёжно и прочно покрывать основной металл;
- иметь мелкокристаллическое строение;
- обеспечивать гладкую поверхность деталей;
- равномерно распределяться по всей поверхности деталей;
- быть плотным, иметь минимальное количество пор;
- не снижать механические характеристики готовой детали;
- не вызывать хрупкость, трещин и поломок;
- не увеличивать остаточную деформацию.
А. Металлические покрытия – получают нанесением различными способами на поверхность одного металла пленок другого металла различной толщины. К покрытиям относятся меднение, цинкование, кадмирование, никелирование, хромирование, лужение (покрытие оловом), серебрение. Основное требование: защищающий металл должен иметь более электроотрицательный потенциал, чем защищаемый. Тем самым он в первую очередь подвержен разрушению в условиях коррозионной среды.
Металлические покрытия в свою очередь делятся на две группы: катодные и анодные.
Катодные покрытия имеют более положительный электродный потенциал, чем защищаемый металл, и поэтому при наличии пор или повреждений в покрытии будет коррозировать основной металл. Таковы покрытия из меди (Cu), хрома (Cr), свинца (Pb), никеля (Ni) на углеродистой или низколегированной стали.
Анодные покрытия имеют более отрицательный электродный потенциал, чем защищаемый металл, и поэтому при нарушении его сплошности анодное покрытие играет протекторную роль, разрушаясь само и тем самым защищая металл от разрушения. Покрытия из цинка (Zn), кадмия (Cd) на углеродистой стали являются анодными.
Основными методами нанесения металлических покрытий являются
1) погружение в расплавленный металл (горячее покрытие);
2) термодиффузионный (диффузионная металлизация);
3) напыление (металлизация);
4) механотермический (плакирование);
5) гальванический.
Горячие покрытия наносят на изделия или заготовки погружением их в расплавленный металл на короткое время. Этот метод применяется для нанесения покрытий из легкоплавких металлов (олова, свинца, алюминия).
Металлизация заключается в нанесении расплавленного металла на поверхность изделия. Аппараты для нанесения (металлизаторы) бывают газовые и электродуговые. Металл, поступающий в металлизатор в виде проволоки или порошка, расплавляется в зависимости от типа металлизатора в газовом пламени или в электрической дуге и распыляется сжатым воздухом или газом. Этим способом можно наносить покрытия на крупногабаритные детали и готовые конструкции, а так же на неметаллические материалы (стекло, дерево, цемент).
Плакированием получают биметаллические листы, ленты, проволоку. Для получения листового биметалла заготовка основного металла совместно с тонкими листами защитного металла подвергается горячей прокатке, при которой в результате диффузионного взаимодействия основного и защитного металлов создаётся их прочное соединение.
Гальванический способ нанесения покрытий является самым распространённым в машиностроении благодаря целому ряду преимуществ: экономичности, лёгкой управляемости процессом, чистоте и равномерности покрытий, хорошему сцеплению покрытия с основным металлом, отсутствию нагрева, а, следовательно, и структурных превращений в металле и коробления.
При нанесении гальванических покрытий детали погружают в ванну с раствором электролита, содержащего ионы осаждаемого металла. Катодом служит деталь, которую подключают к отрицательному полюсу источника постоянного тока. Аноды могут быть растворимые (пластины из наносимого металла) и нерастворимые (графитные пластины).
Для электролитического процесса цинкования деталей применяют цианистые, щелочные (цинкатные), сернокислые, аммиакатные и другие электролиты. Суть процесса заключается в осаждении Zn на поверхность детали под действием электрического тока. Вследствие избытка электронов на катоде на нём происходит разряд положительно заряженных ионов защищающего металла, находящихся в растворе и их осаждение на защищаемый металл. Гальваническим методом на сталь наносят Zn, Cd, Sn, Pb, Cu, Ni, Cr.
Для повышения коррозионной стойкости самих цинковых покрытий применяют химическую обработку деталей в хромовых растворах с добавкой азотной кислоты и сернокислого натрия. В результате на поверхности образуется тонкая хроматная пленка. Процесс называется пассивирование.
Многие гальванические покрытия имеют существенный недостаток – это водородная хрупкость металла, особенно губительная для мелких деталей и пружин из тонкой проволоки. На катоде выделяется атомарный водород, который частично диффундирует в материал катода, (т.е. покрываемый материал) и приводит к появлению водородной хрупкости. Подобное явление встречается при кислотном и электролитическом травлении. Количество диффундирующего водорода Н, так же как и глубина его проникновения, зависят от состава стали. Чем больше в ней углерода, тем более она подвержена водородной хрупкости.
А так же в результате подготовки поверхности перед покрытием происходит насыщении поверхности детали водородом, который необходимо удалять нагревом до Т=180-220 0С. Эта операция называется - обезводороживание.
Б. Покрытия, получаемые химической обработкой поверхности – это плёнки, образующиеся в результате химической реакции между металлом и химическими реагентами. К таким покрытиям относятся образующиеся плёнки фосфатов, окислов при процессах фосфатирование, оксидирование (воронение).
При фосфатировании – на поверхности металла образуется защитная пленка, состоящая из фосфатов железа и марганца. Обрабатываемая пружина погружается в раствор соли Мажефа. Пленка приобретает мелкокристаллическую структуру, толщина её не превышает 0,005 мм. Пленка должна быть «закреплена» минеральным маслом, лаком или краской. Фосфатирование применяют для защиты стали от атмосферной коррозии.
Оксидирование (воронение) – заключается в образовании на поверхности металла окислов того же металла (окиси железа Fe3O4) химическим или химико-термическим способом. Воронение после «закрепления» оксидной плёнки вазелином или лаком приобретает темный глянцевый вид. Оксидная пленка обладает повышенной пористостью, и поэтому недолго предохраняет металл от коррозии при нормальных атмосферных условиях, постепенно разрушается при воздействии повышенной влажности и агрессивных сред.
В. Неметаллические покрытия – это наносимые на металл плёнки органического или минерального (неорганического) происхождения. К органическим покрытиям относятся смолы, эмали, лаки, полимеры, краски, резина и т.п. К неорганическим - цементные и бетонные покрытия, стеклоэмали, керамические материалы.
Лакокрасочные покрытия – имеют наиболее широкое применение. Лакокрасочные покрытия также применяют совместно с оксидными, фосфатными и гальваническими. При добавлении в лаки пигментов получают эмалевые краски. Кроме эмалевых, существуют следующие виды красок: клеевые, гуашевые (на основе декстрина), масляные (на олифе), силикатные (на жидком стекле).
Широко распространены эфироцеллюлозные и алкидные материалы. К эфироцеллюлозным относятся нитролаки и нитроэмали. Они отличаются бензо - и маслостойкостью, эластичностью и быстро высыхают при комнатных температурах. К алкидным относятся глифталевые и пентафталевые лакокрасочные материалы, применяемые для окраски автомобилей и всевозможных аппаратов и приборов.
Покрытие смолами, в том числе и синтетическими, производится кистью, окунанием или распылением. Плёнки из капрона и нейлона обладают широким сцеплением с металлом, прочностью, химической стойкостью и высокими электроизоляционными свойствами. Для нанесения покрытий применяют также фторопласты, полиэтилен, эпоксидные смолы и т.д.
Покрытие резиной (гуммирование) осуществляют облицовкой листами резиновой смеси с последующей вулканизацией, напылением, а также нанесением жидких каучуковых композиций (латекса и лаков на основе каучука). Резиновые покрытия эластичны, стойки к истиранию, обладают хорошей химической стойкостью, водо- и газонепроницаемы.
Покрытия стеклоэмалями получают нанесением расплавленных стёкол специального состава, образующих после остывания фарфоровидный слой. Эти покрытия устойчивы в органических и минеральных кислотах и в слабых растворах щелочей; отличаются высокой твёрдостью, прочностью на истирание и хрупкостью.
Керамические покрытия (футеровка) выполняют из диабазовых, керамиковых, метлахских и других плиток, цементируя их кислотоупорными замазками. Применяют эти покрытия для защиты от действия высоких температур (выше 1200 С0). Керамические и металлокерамические покрытия наносят также напылением; наиболее часто применяют напыление окиси алюминия и двуокиси циркония.
Тема № 10.
Неметаллические материалы
I. Пластические массы
Производство полимеров с высокими физико-химическими, механическими и технологическими свойствами способствует широкому внедрению этих перспективных материалов во многие отрасли техники, способствует совершенствованию конструкций, снижению себестоимости продукции, повышению производительности труда.
Пластические массы (пластмассы) – это материалы на основе природных или синтетических высокомолекулярных соединений, пригодные для переработки в изделия в результате пластической деформации под влиянием нагревания и давления и способные затем сохранять закреплённую в результате охлаждения или отверждения форму.
Химическое строение, молекулярный вес, структура цепи и взаимное расположение молекул определяют свойства высокомолекулярных соединений полимеров.
При выборе пластмасс методом аналогий используют классификацию по эксплуатационному назначению, сведения о характерных особенностях различных пластмасс, их преимуществах, ограничениях и рекомендациях по применению и способам переработки.
Пластмассы включают широкий перечень термопластичных и термореактивных материалов, которые используют для изготовления различных деталей машин, механизмов, приборов, а также плёнок, листов, труб, заготовок и пр. В этих изделиях пластмассы характеризуются параметрами механических свойств и теплостойкости, которые должны быть не ниже определённого уровня: σт.р ≥ 2 Мпа; Ер ≥ 10 Мпа; Тв ≥ 55 0С; Нб ≥ 2 Мпа. Такие пластмассы принято называть конструкционными, в отличие от полимерных материалов (в основном это синтетические смолы), у которых значение хотя бы одного из параметров ниже приведённых.
Пластмассы конструкционного назначения можно условно разделить на три группы: пластмассы низкой прочности, средней прочности и высокопрочные. К пластмассам низкой прочности относятся фенопласты, фенолиты и аминопласты. К пластмассам средней прочности относятся слоистые пластики, изготовленные из бумаги, хлопчатобумажной ткани или древесного шпона, пропитанных фенолоформальдегидной смолой, а также пластики полимеризационного типа, обладающие повышенной механической прочностью. К группе высокопрочных пластических масс относятся стеклопластики, состоящие из полимера, армированного стекловолокном. Наиболее распространённые: фенолформальдегидные, эпоксидные и полиэфирные смолы.
Основная классификация пластмасс осуществляется по эксплуатационным свойствам:
1) По направлениям применения пластмассы различают:
- для работы при действии кратковременной или длительной постоянной нагрузки: пентапласт ПТ, полиамид 66, фенопласт, аминопласт, текстолит, полиформальдегид ПФ, стеклотекстолит и т.п.;
- для получения эластичных изделий: полиэтилен ПЭ, полипропилен ПП, полифинилхрорид пластифицированный ПВХП, фторопласт ФТ, полиуретан ПУР, полиамид 12, сополимер этилена СЭП;
- для работы при низких температурах: полипропилен морозостойкий, фторопласт ФТ, полиэтилен ПЭ, поликарбонат ПК, сополимеры формальдегида СФ;
- антифрикционного назначения: фторопласт ФТ, полиамид ПА, полиформальдегид ПФ, полиимид ПИ, фенопласт, текстолит;
- электро- и радиотехнического назначения: полиэтилен ПЭ, полипропилен ПП, полистирол ПС, фторопласт ФТ;
- для получения прозрачных изделий: полистирол ПС, прозрачный фторопласт ФТ;
- тепло- и звукоизоляционного назначения: газонаполненные материалы на основе полиэтилена ПЭ, полистирола ПС, поливинилхлорида ПВХ, полиуретана ПУР;
- для пищевых продуктов и питьевой воды: полиэтилен ПЭ, полиуретан ПУР, пентапласт ПТ, полистирол ПС;
- для работы в агрессивных средах: полиэтилен ПЭ, полипропилен ПП, полиимид ПИ.
2) По совокупности параметров эксплуатационных свойств: общетехнического и инженерно-технического назначения с более высокими параметрами механических свойств и теплостойкости.
3) По назначению отдельных параметров эксплуатационных свойств: для различных параметров эксплуатационных свойств (температура размягчения, температура длительной эксплуатации, температура хрупкости и т.д.).
В зависимости от условий отверждения пластмассы подразделяют на термореактивные и термопластичные.
1. Термореактивные (полимеры) – при отверждении образуютпространственную структуру макромолекул, претерпевают необратимые изменения и переходят в твёрдое, неплавкое и нерастворимое состояние. Наиболее распространённые полимеры: фенолоформальдегидные, эпоксидные, кремнийорганические, полиэфирные.
Слоистые материалы – материалы, армированные параллельно расположенными слоями листового наполнителя: бумаги, ткани и т.п. Наибольшую прочность имеют стеклотекстолиты, наиболее высокую теплостойкость – асботекстолиты. Наиболее распространённые и дешёвые фенолоформальдегидные смолы. Они имеют хорошую адгезию к большинству наполнителей, термостойки, но требуют сравнительно высоких давлений при формировании изделий. Кремнийорганические смолы имеют хорошую водостойкость, термостойкость, обеспечивают повышенные диэлектрические свойства; их высокий коэффициент линейного расширения снижает механические свойства материала.
Слоистые пластмассы применяют как конструкционные, электротехнические и поделочные материалы. Конструкционные пластмассы содержат меньше полимерного связующего, т.к. с увеличением его содержания механические свойства материалов снижаются. Наиболее распространёнными слоистыми пластмассами являются гетинакс, текстолит, стеклотекстолит, асботекстолит, древеснослоистые пластики (ДСП).
Гетинакс – наполнитель из параллельно уложенных слоёв бумаги, связующее – фенолоформальдегидные смолы. Обладает хорошими электроизоляционными свойствами и имеет высокую механическую прочность. Применяется в электро- и радиотехнике для изготовления панелей, щитков, печатных схем, для корпусов приборов и других малонагруженных изделий.
Текстолит – в качестве наполнителя используется бязь, связующее – фенолоформальдегидная или другие термореактивные смолы. В паре со сталью текстолит имеет низкий коэффициент трения и высокую износоустойчивость. Его применяют для бесшумных зубчатых и червячных колёс, подшипников скольжения. Специальный графитизированный текстолит применяют для вкладышей подшипников прокатных станов, центробежных насосов.
Древеснослоистые (ДСП) – получают в виде листов и плит горячим прессованием тонких листов древесного шпона, пропитанных феноло- или крезольноформальдегидными смолами. Так как они имеют высокую механическую прочность, то применяются как конструкционные материалы для изготовления частей автомобилей, вагонов, лодок, деталей машин, шкивов. Так же применяют в качестве электроизоляционного материала для различных панелей электрических приборов. Недостаток – чувствительность к воздействию влаги.
Асботекстолит – слоистый пластик, состоящий из асбестовой ткани и различных термореактивных смол. Обладает высокой термостойкостью и применяется в качестве теплозащитного и теплоизоляционного материала. Благодаря фрикционным свойствам его широко используют для изготовления тормозных колодок, фрикционных дисков.
Стеклотекстолит – в качестве наполнителя используется стеклоткань, в качестве связующего - термореактивные фенолоформальдегидные, кремнийорганические и другие смолы. Анизотропные материалы (различные прочностные свойства вдоль и поперёк нитей). Обладают высокой прочностью, химической стойкостью, негорючестью, незагниваемостью. Стеклотекстолит конструкционного назначения используют для высокопрочных изделий (труб, ёмкостей, кабин автомобиля), панелей, щитков, корпусов приборов.
Стекловолокнистые – в качестве наполнителя стеклянные волокна. СВАМ имеет наиболее высокую удельную прочность. Применяются для сильно нагруженных изделий.
Порошковые материалы (пресспорошки) – композиционные пластмассы с порошкообразными органическими или минеральными наполнителями (древесная мука, порошок кварца и т.д.). Прессматериалы – пластмассы с волокнистыми наполнителями (хлопковые очёсы, асбестовые волокна. Минеральные наполнители придают пластмассам химическую стойкость, водостойкость, повышенные электроизолирующие свойства. В качестве связующих применяют полимеры на основе фенолоформальдегидных, фенолоальдегидных, карбамидных, кремнийорганических, эпоксидных и других смол с различными наполнителями.
В зависимости от области применения делятся на материалы:
- общетехнического назначения;
- электроизоляционные;
- электроустановочные (жаростойкие);
- влагохимстойкие;
- специального назначения (фрикционные, антифрикционные, рентгеностойкие).
Полуфабрикаты термореактивных пластмасс выпускают в виде твёрдосыпучих прессматериалов (пресспорошков, волокнистых и крошкообразных материалов, гранулированных смесей). При изготовлении деталей методом литья применяют полуфабрикаты в виде различных вязко-текучих композиций, заливочных и формовочных масс.
Из композиционных термореактивных пластмасс изготавливают корпуса приборов, панели, рукоятки, детали зажигания автотракторного электрооборудования, платы печатных схем, электроизоляционные детали, резьбовые соединения, технические детали с повышенными водостойкостью и химической стойкостью, подшипники скольжения, тормозные колодки и диски, аппаратуру теплообменников, детали насосов, краны, трубы, зубчатые колёса, изделия бытового назначения.
2. Термопластинчатые (полимеры) – термопласты, при нагреве переходят в пластичное или вязкотекучее состояние. Эти пластмассы отверждаются при охлаждении. При повторном нагреве они снова размягчаются и т.д., допуская возможность многократного повторного формования изделий. Важнейшие термопласты: полиэтилен, поливинилхлорид, фторопласты, полистирол, полиамиды, органическое стекло.
Полиэтилен – является полимером аморфнокристаллического строения. Он имеет невысокую прочность, его морозостойкость до – 60 0С. Обладает отличными диэлектрическими свойствами и широко применяется как высокочастотный диэлектрик. Из полиэтилена изготавливают катушки и другие электро- и радиотехнические детали, изоляцию кабелей, химически стойкие ёмкости, трубы для химической промышленности, защитные от коррозии плёнки и покрытия.
Пполивинилхлорид – относится к группе аморфных полимеров (пластикаты, винипласты). Он является хорошим низкочастотным диэлектриком, стоек к щелочам, кислотам, смазкам и бензину. Диапазон рабочих температур от – 40 до + 60 0С. Пластикаты применяют для изоляции и оболочек проводов и кабелей, в строительной промышленности. Винипласты применяют для изготовления труб, деталей химического оборудования, фланцев, муфт, деталей насосов, вентиляторов.
Фторопласты – фторсодержащие полимеры винильного типа (фторопласт-3, фторопласт-4). Они устойчивы почти во всех агрессивных средах, имеют хорошие антифрикционные свойства. Диапазон используемых температур от -269 до +250 0С. Недостатки – склонность к хладнотекучести.
Используются в авиастроении, электротехнической промышленности, в радиотехнике.
Полистирол – обладает высокими диэлектрическими свойствами, высоким коэффициентом лучепреломления, отсутствием хладотекучести, водостоек, химически стоек. Его используют для изготовления деталей в электро- и радиотехнической промышленности, в авто- и самолётостроении.
Полиамиды нейлон, капрон и др. являются продуктом поликонденсации аминокислот. Обладают высокой прочностью, низким коэффициентом трения, хорошему сопротивлению износу. Применяют для изготовления подшипников, зубчатых колёс, кулачков.
Органическое стекло – термопласт на основе сложных эфиров акриловой и метакриловой кислот. Оно прозрачно, является атмосферостойким. Недостаток – низкая твёрдость. Широко применяется для остекления зданий, в светотехнических устройствах, предохранительных щитках приборов и машин.
Газонаполненные пластмассы.
Это лёгкий материал, имеющий пористую структуру, напоминающую застывшую пену. Различают пенопласты с замкнутыми или изолированными ячейками (порами) и поропласты с открыто-пористой структурой. Основные свойства: очень небольшая плотность, высокие звукопоглощающие и теплоизолирующие. Некоторые пенопласты обладают высокими демпфирующими и амортизационными свойствами. Высокой удельной прочностью и жёсткостью обладают армированные пенопласты – конструкционные материалы, состоящие из чередующихся слоёв пенопласта и листовой металлической, стеклопластиковой или другой армировки.
Пенопласты использую как тепло- и звукоизоляционные материалы, для амортизационных прокладок, изготовления плавучих и труднозатопляемых средств, предметов обихода. Заполнение пенопластами полых деталей и конструкций увеличивает их устойчивость и жёсткость, повышает вибрационную и усталостную прочность.
II. Резина
В современном машиностроении используют большое количество резиновых изделий. Резина как конструкционный материал обладает рядом важных технических свойств: высокой эластичностью, высоким сопротивлением разрыву, износу, газо- и водонепроницаемостью, химической стойкостью, ценными электротехническими свойствами, малой плотностью.
Резина – является сложной смесью различных компонентов (ингредиентов). К ним относятся каучук, вулканизирующие вещества, ускорители вулканизации, активаторы ускорителя, наполнители, противостарители, смягчители, красители.
Основной резиновой смесью является натуральный или искусственный каучук. Для уменьшения расхода каучука и придания необходимых физико-механических свойств резиновым изделиям, в композицию вводят наполнители.
Резиновые технические изделия применяют для:
1) оснащения движущихся устройств (приводные ремни, транспортёрные ленты);
2) подачи воды, жидкого топлива, кислот, масел, пара, воздуха;
3) уплотнения неподвижных и подвижных контактов (сальники, манжеты);
4) амортизации (резиновые подвески, опоры, подшипники, буфера);
5) электроизоляции (детали слаботочной и высокочастотной аппаратуры, изоляционные трубки, изоляционная лента);
6) защиты химической аппаратуры, изготовления воздухо - и водоплавательных средств.
В зависимости от назначения и требуемых эксплуатационных свойств резины делят на две большие группы: общего назначения – резины, используемые в производстве шин, ремней, рукавов, амортизаторов; специальные – резины морозо - и теплостойкие, маслостойкие, газонепроницаемые, электротехнические, стойкие к радиации.
Резины также подразделяют на мягкие (для изготовления шин, прокладок), жёсткие или эбонитовые (для электротехнических деталей и химически стойких элементов), пористые или губчатые (для амортизаторов, сидений и т.д.), пастообразные (для герметизации и уплотнения). Резиновые материалы классифицируют по виду сырья, по технологическим методам переработки.
Резиновые смеси на основе силиконовых каучуков (ТУ 38-103104-72) – предназначены для термоморозостойких резиновых изделий, для работы в интервале температур от -50 до +250 0С, в любых климатических условиях.
Выпускают резиновые смеси следующих специализированных марок:
ИРП-1341 – для изготовления деталей, работающих в неподвижных соединениях в среде воздуха, озона, а также электрическом поле;
ИРП-1399 – для элементов рукавов, к которым предъявляют повышенные требования по прочности, и изделий, которые могут кратковременно работать при +300 0С;
ИРП-1401 – для изделий высокой твёрдости, работающих в среде воздуха, озона, а также в электрическом поле. Шланги с повышенной теплостойкостью.
26-7058 – резиновая смесь для изготовления шлангов, работающих в контакте с охлаждающей автожидкостью и тормозной жидкостью.
7-57-5011 -резиновая смесь для изготовления шлангов, работающих в контакте с бензином.
5Э-292 - резиновая смесь (ТУ 38.1051651-85) предназначенная для обрезинивания манжетки золотника вентилей пневматических камер и шин, а также для изготовления резиновых пластин.
5Э-293 – р езиновая смесь (ТУ 38.105.1652-85) предназначенная для изготовления прокладок, колпачков-ключиков и резиновых колец золотников вентилей пневматических шин.
III. Лакокрасочные материалы
Лакокрасочные материалы (л.к.м.) и их композиции (л.к.к.) предназначены для образования лакокрасочных покрытий (л.к.п.), служащих для защиты машин от воздействия среды (защитные покрытия), придания им внешнего вида, отвечающего требованиям технической эстетики (декоративные покрытия), и при объединении этих свойств л.к.п. носят название «защитно-декоративные покрытия» - наиболее распространённые. Отдельную категорию составляют л.к.п. с особыми свойствами (антиадгезионные, электроизоляционные, токопроводящие, антисептические, теплостойкие, термочувствительные, светящиеся и др.).
Повышение качества и долговечности л.к.п. обеспечивается внедрением новых л.к.м. на основе полимерных материалов, которые обладают не только требуемыми конструкционными (эксплуатационными) свойствами, но и лучшими технологическими данными, ускоряющими и удешевляющими процессы окрашивания.
Создание качественного л.к.п. начинается с тщательной подготовки укрываемой поверхности (выравнивание, очистка, обезжиривание, оксидирование, фосфатирование).
Основой л.к.п. являются плёнкообразующие, т.е. полимерные вещества, способные образовывать тонкие прочные непрерывные плёнки, определяющие качество декоративно-защитного покрытия. Плёнкообразующими служат растительные масла, естественные и синтетические смолы и эфиры целлюлозы. Плёнкообразующие растворяют в растворителях, такие растворы называют лаками. Привведении в лак-основу пигмента образуется эмалевая краска – эмаль. Растительные масла, загущенные пигментами, называют масляными красками.
Для повышения качества л.к.п. в лакокрасочную композицию вводят легирующие добавки (или присадки) – пластификаторы (мягчители) – для повышения пластичности плёнки, сиккативы – для ускорения высыхания, разбавители – дляпридания малярной консистенции краскам, наполнители (улучшители) – для улучшения и придания покрытию твёрдости, химической стойкости, светостойкости, теплостойкости и т.д.
Условное обозначение: Эмаль ФЛ – 2 5 голубая ГОСТ 9825-73
ФЛ – плёнкообразующие; 2 – назначение л.к.м. (стойкие внутри помещений); 5 – порядковый номер.
IV. Технические, смазочные и охлаждающие жидкости
Жидкие и пластичные материалы (технические жидкости), применяемые в машиностроении, по назначению подразделяют на группы:
Конструкционные – смазочные масла и жидкости, пластичные смазки, жидкости, применяемые в качестве рабочих тел гидроприводов, амортизаторов, теплообменных аппаратов и др.
Технологические – смазочно – охлаждающие, моющие, раство
Археология об основании Рима: Новые раскопки проясняют и такой острый дискуссионный вопрос, как дата самого возникновения Рима...
Организация стока поверхностных вод: Наибольшее количество влаги на земном шаре испаряется с поверхности морей и океанов (88‰)...
Биохимия спиртового брожения: Основу технологии получения пива составляет спиртовое брожение, - при котором сахар превращается...
Архитектура электронного правительства: Единая архитектура – это методологический подход при создании системы управления государства, который строится...
© cyberpedia.su 2017-2024 - Не является автором материалов. Исключительное право сохранено за автором текста.
Если вы не хотите, чтобы данный материал был у нас на сайте, перейдите по ссылке: Нарушение авторских прав. Мы поможем в написании вашей работы!