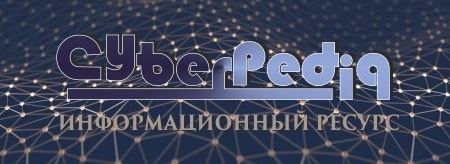
Общие условия выбора системы дренажа: Система дренажа выбирается в зависимости от характера защищаемого...
Состав сооружений: решетки и песколовки: Решетки – это первое устройство в схеме очистных сооружений. Они представляют...
Топ:
Характеристика АТП и сварочно-жестяницкого участка: Транспорт в настоящее время является одной из важнейших отраслей народного...
Оценка эффективности инструментов коммуникационной политики: Внешние коммуникации - обмен информацией между организацией и её внешней средой...
Особенности труда и отдыха в условиях низких температур: К работам при низких температурах на открытом воздухе и в не отапливаемых помещениях допускаются лица не моложе 18 лет, прошедшие...
Интересное:
Национальное богатство страны и его составляющие: для оценки элементов национального богатства используются...
Средства для ингаляционного наркоза: Наркоз наступает в результате вдыхания (ингаляции) средств, которое осуществляют или с помощью маски...
Наиболее распространенные виды рака: Раковая опухоль — это самостоятельное новообразование, которое может возникнуть и от повышенного давления...
Дисциплины:
![]() |
![]() |
5.00
из
|
Заказать работу |
|
|
Прокаливаемость. Прокаливаемостью называется способность стали закаливаться на определенную глубину. Прокаливаемость стали зависит от критической скорости закалки. Чем меньше критическая скорость закалки, тем глубже прокаливаемость.
Прокаливаемость (глубина закалки) определяется расстоянием от поверхности до слоя с полумартенситной структурой, т.е. слоя состоящего из 50 % мартенсита и 50 % троостита.
Прокаливаемость стали зависит от ее химического состава, величины природного зерна, метода выплавки и других факторов. Например, такие легирующие элементы, как марганец, хром, молибден, оказывают большое влияние на прокаливаемость (увеличивают), а кремний, никель - незначительное. С увеличением природного зерна прокаливаемость увеличивается и наоборот. Прокаливаемость увеличивается также с повышением температуры нагрева и ско-рости охлаждения. Способность стали прокаливаться является важным критерием, опреде-ляющим ее свойства и применение. Прокаливаемость определяется разными способами. Наиболее простой способ - торцевая закалка.
Основные методы закалки стали. Различают следующие способы закалки стали:
1. Закалка в одном охладителе. Нагретое изделие охлаждают до температуры
100-150 °С в одном охладителе. Этот основной вид закалки легированных сталей при охлаждении в масле и цементированных углеродистых при охлаждении в воде применяется также для закалки изделий из средне- и высокоуглеродистых сталей самой несложной формы. Изделия из углеродистой стали диаметром до 6 -7мм закаливаются в масле.
2. Закалка в двух охладителях (прерывистая). Нагретое изделие охлаждается в воде до температуры 200-250 °С, после чего быстро переносится в масло для дальнейшего охлаж-дения. Ориентировочное время охлаждения в воде до переноса в масло равно 1-1,5 сек. На каждые 5-6 мм диаметра или толщины изделий. Это основной способ закалки углеродистых инструментальных сталей.
|
3. Струйная закалка. Охлаждение производится струей воды или водяным душем; применяется для закалки изделий со сквозными и глухими отверстиями.
4. Изотермическая закалка. Нагретое изделие охлаждается в горячем масле, расплаве соли или металла (свинец, олово) при температуре на 20-30 °С выше начала мартенситного превращения для стали данной марки. После окончания превращения аустенита, изделия охлаждают на воздухе. В результате изотермической закалки образуется игольчатый троостит (нижний бейнит). Отпуск после изотермической закалки не обязателен. Применяется для изделий сложной формы во избежание образования трещин и коробления.
5. Ступенчатая закалка. Нагретое изделие охлаждают в горячей среде при температуре среды на 20-30 °С выше температуры мартенситного превращения до выравнивания температуры по всему сечению, после чего охлаждают на воздухе. После выемки изделий из горячей среды до окончания превращения аустенита изделие можно править. Применяется для закалки из углеродистых инструментальных сталей диаметром до 8-10 мм сложной конфигурации. Или нагретое изделие охлаждают в горячей среде при температуре 150-180 °С до выравнивания температуры, а затем - на воздух.
6. Закалка сомоотпуском. Рабочая часть нагретого изделия охлаждается в воде, после чего вынимается и отпускается на требуемый цвет побежалости. Применяется в основном для ударного инструмента из углеродистой стали.
7. Закалка подстуживанием. Изделие, нагретое выше требуемой температуры, подстуживается на воздухе до нормальной закалочной температуры, поле чего закаливается. Применяется для цементованных изделий при закалке непосредственно с цементационного нагрева, для штампов из стали 5ХНТ и др.
|
8. Закалка при температурах ниже нуля (обработка холодом). В структуре закаленных и легированных сталей всегда присутствует некоторое количество аустенита. В изделиях, отпускаемых при температурах выше 200-250 °С, этот аустенит под влиянием нагрева превра-щается в отпущенный мартенсит. В изделиях, проходящих отпуск при температурах ниже 200 °С, аустенит фиксируется и остается в стали.
В некоторых высоколегированных сталях аустенит весьма устойчив и при отпуске не превращается в мартенсит. Наиболее полное превращение можно достичь путем дополни-тельного, после закалки, охлаждения до температур ниже нуля. Обработку холодом нужно производить сразу после остывания изделия до комнатной температуры, так как после выле-живания при комнатной температуре аустенит становиться весьма устойчивым. Время от момента закалки до обработки холодом не должно превышать 1-3 часа, а для углеродистых инструментальных деталей и того меньше. Обработка холодом производится до отпуска. В качестве охладителей применяют жидкий азот, жидкий кислород, фреон и т.д.
Дефекты, возникающие при закалке. В процессе закалки при охлаждении стали в результате структурных превращений и изменения объема металла появляются внутренние напряжения. Кроме вышеуказанных дефектов: закалочных трещин, деформации, коробления, недогрева, низкой твёрдости, мягких пятен (см. разряд 1-2), при закалке возможны дефекты – окисление, обезуглероживание, перегрев, пережог.
Окисление. При нагреве в печах поверхность взаимодействует с печными газами. В результате металл окисляется и на поверхности образуется окалина. С повышением температуры и времени выдержки окалина резко возрастает. Образование окалины вызывает угар (потерю) металла, а также искажает геометрическую форму деталей. Поверхность сталей под окалиной получается разъеденной и неровной, что затрудняет обработку режущим инструментом. Окалину с поверхности деталей удаляют травлением в кислотах (серной), или очисткой в дробеструйных установках.
Обезуглероживание -выгорание углерода с поверхности деталей происходит всегда при окислении стали. Обезуглероживание снижает резко прочностные свойства конструкционной стали. Кроме того, детали с обезуглероженной поверхностью склонны к закалочным трещинам и короблению. Особенно большое обезуглероживание наблюдается при нагреве в электропечах. Для исключения обезуглероживания и окисления поверхности деталей в процессе отжига, нормализации и закалки применяют неокисляющие (контролируемые) атмосферы.
|
Перегрев. Сталь перегревается при очень высокой температуре закалки (завышенной), а также при большой выдержке. При перегреве зерна в стали укрупняются, что ведет к сниже-нию прочности, вязкости и образованию закалочных трещин. Такой дефект стали устраняют повторным правильным отжигом или нормализацией.
Пережог. Пережог стали получается при нагреве до высоких температур, выражающийся в оплавлении поверхности деталей и окислении зерен. При высокой температуре нагрева кислород из окружающей печной атмосферы проникает внутрь нагретой стали, при этом границы зерен сильно окисляются. Сталь теряет пластические свойства, прочность и становится настолько хрупкой, что при малейших ударах разрушается. Пережженную сталь исправить термической обработкой невозможно, поэтому она идет на переплавку.
2.Азотирование - процесс насыщения поверхности стальных и чугунных деталей азотом. Этот процесс является одним из эффективных методов повышения износостойкости деталей.
Различают два вида азотирования:
1) прочностное – с целью повышения твердости, износостойкости усталостной прочности; 2) антикоррозионное - с целью повышения сопротивлению коррозии в воде (несоленой) и влажной атмосфере.
Прочностное азотирование ведется в шахтных печах в атмосфере распадающегося аммиака при температуре 525 – 570 °С. Полученный таким образом слой обладает высокой твердостью и способностью сохранять прочность при температуре 600°С, в то время как цементованные детали при такой температуре быстро размягчаются. Перед азотированием детали подвергаются термической обработке - улучшению, т.е. закалке при 930 – 960 °С в воде и от-пуску при температуре 600 °С до твердости 28 -32 НRС, а чугунные – закалке и отпуску при 600 – 650 °С. Обычно глубина азотированного слоя находится в пределах 0,2 - 0,3 мм. Для азотирования применяют специальные стали, содержащие алюминий (35ХЮА и 38ХМЮА). Кроме них, азотируют также инструментальные легированные и нержавеющие стали. Поверхностная твердость на специальных сталях достигает (1000-1150 НV).
|
Чугуны, подвергаемые азотированию должны содержать алюминий и хром. Твердость чугунов после азотирования достигает 1000 НV.
Азотирование более длительный процесс, чем цианирование или цементация, и требует более точной обработки. Азотированию подвергаются шпиндели металлорежущих станков, гильзы, копиры, плунжеры, клапаны и др., изготавливаемые из стали 38ХМЮА, 35ХЮА.
Антикоррозионное азотирование применяется для изделий из углеродистой и легированной стали и чугуна. Перед азотированием детали тщательно обезжириваются.
3. Термическая обработка алюминиевых сплавов. Различают два типа алюминиевых сплавов: деформируемые и литейные.
Деформируемые литейные сплавы разделяются на две группы:
1) сплавы, термически не упрочняемые; 2) сплавы, термически упрочняемые.
Хорошую пластичность сплавы алюминия приобретают в результате отжига в селитровых ваннах в течение 20-30 мин. или электропечах в течение 1- 2 час. от 340- 460 °С в зависимости от марки сплава. Наибольшие пластические свойства и наименьшая твердость достигается в алюминиевых сплавах после отжига в течение 30 мин. при 420 °С с последующим остыванием с печью со скоростью 30 °С в час до 280 °С, а затем на воздухе.
|
|
Биохимия спиртового брожения: Основу технологии получения пива составляет спиртовое брожение, - при котором сахар превращается...
Особенности сооружения опор в сложных условиях: Сооружение ВЛ в районах с суровыми климатическими и тяжелыми геологическими условиями...
Индивидуальные и групповые автопоилки: для животных. Схемы и конструкции...
Состав сооружений: решетки и песколовки: Решетки – это первое устройство в схеме очистных сооружений. Они представляют...
© cyberpedia.su 2017-2024 - Не является автором материалов. Исключительное право сохранено за автором текста.
Если вы не хотите, чтобы данный материал был у нас на сайте, перейдите по ссылке: Нарушение авторских прав. Мы поможем в написании вашей работы!