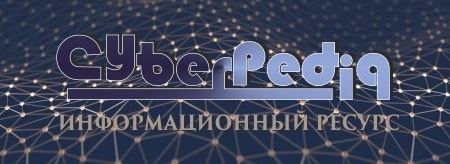
Эмиссия газов от очистных сооружений канализации: В последние годы внимание мирового сообщества сосредоточено на экологических проблемах...
Организация стока поверхностных вод: Наибольшее количество влаги на земном шаре испаряется с поверхности морей и океанов (88‰)...
Топ:
Характеристика АТП и сварочно-жестяницкого участка: Транспорт в настоящее время является одной из важнейших отраслей народного...
Когда производится ограждение поезда, остановившегося на перегоне: Во всех случаях немедленно должно быть ограждено место препятствия для движения поездов на смежном пути двухпутного...
Проблема типологии научных революций: Глобальные научные революции и типы научной рациональности...
Интересное:
Отражение на счетах бухгалтерского учета процесса приобретения: Процесс заготовления представляет систему экономических событий, включающих приобретение организацией у поставщиков сырья...
Финансовый рынок и его значение в управлении денежными потоками на современном этапе: любому предприятию для расширения производства и увеличения прибыли нужны...
Подходы к решению темы фильма: Существует три основных типа исторического фильма, имеющих между собой много общего...
Дисциплины:
![]() |
![]() |
5.00
из
|
Заказать работу |
|
|
Нагрев термически упрочняемых алюминиевых сплавов для упрочнения производится в тех же печах. Температура закалки колеблется от 490-540 °С в зависимости от марки сплава, охлаждающей средой является вода. Повышение верхнего предела закалочной температуры может привести к пережогу, характерными признаками которого являются резкое потемне-ние поверхности, появление пузырей и трещин. Это неисправимый брак. Температура воды при закалке не менее 30 °С. С увеличением объема деталей и их сложности рекомендуется повышать температуру воды до 70 – 80 °С. Повышение температуры воды уменьшает трещи-нообразование и коробление. Промежуток времени между выемкой из печи и погружением в воду должен быть не более 20-30 сек.
После закалки алюминиевые сплавы несколько упрочняются, но все же остаются настолько пластичными, что допускают возможность деформирования изделий. Через некоторый проме-жуток времени от 1,5 – 3(6) часов в зависимости от марки сплава, сплав начинает стареть. Естественное старение при 15 – 20 °С у многих сплавов осуществляется в течение 4 суток. Старение ускоряется путем отпуска при 150 - 170 °С в течение 6-12 часов - искусственное старение.
Свежезакаленное состояние изделий можно сохранить, выдерживая их после закалки при температуре от 0 до – 20 °С.
Закаленный и состаренный дуралюмин можно привести в свежезакаленное состояние путем кратковременного нагрева (0,5-1 мин.) при температуре 240 - 260 °С. После произведен-ной операции (штамповка и пр.) сплав вновь стареет.
Термообработка литейных сплавов (АЛ1, АЛ2, АЛ3, АЛ4, АЛ5, АЛ6, АЛ7, АЛ8, АЛ9, АЛ10В, АЛ11, АЛ12, АЛ14В, АЛ15В, АЛ16В, АЛ17В). Многие отливки из алюминиевых сплавов подвергают термической обработке. В зависимости от характера отливки и условий ее работы используют один из следующих видов термообработки:
|
1. Искусственное старение (условное обозначение Т1), чаще при (175 ±5) °С в течение 5-10 ч.
Повышает прочность, улучшает обработку резанием.
2. Отжиг (Т2) при 300 °С в течение 5 -10 ч. Охлаждение при отжиге проводят на воздухе. Отжиг применяют для снятия литейных и остаточных напряжений, вызванных механической обработкой. Этот отжиг несколько повышает пластичность.
3. Закалка и естественное старение (Т3, Т4). Температура закалки 510 – 520 °С для сплавов АЛ1, АЛ7 и 535 – 545 °С для сплавов АЛ4, АЛ9, АЛ19, и др. Закалку производят в горячей воде (40 -100°С). Так как после закалки отливки выдерживают достаточно длительное время при комнатной температуре, режим (Т1) практически соответствует закалке и естественному старению.
4. Закалка и кратковременное (2-3 ч.) искусственное старение обычно при 175 °С (Т5). Приданной температуре и продолжительности процесс старения полностью не заканчивает-ся. Поэтому после такой обработки отливки приобретают высокую прочность при сохране-нии повышенной пластичности.
5. Закалка и полное искусственное старение (Т6), которое чаще всего проводят при 200 °С,
3 – 5 ч. Старение при повышенной температуре и более длительной выдержке по сравнению с режимом (Т5) придает наибольшую прочность, но пластичность снижается.
6. Закалка и стабилизирующий отпуск (Т7) при 230 °С (для сплавов АЛ9, АЛ1, АЛ20) и при 250°С сплава АЛ19) в течение 3 – 10 ч. Этот вид обработки используют для стабилизации структуры и объемных изменений отливки, при сохранении достаточной прочности.
7. Закалка и смягчающий отпуск (Т8) обычно происходят при 240 – 260 °С в течение 3 -5 ч. Высокая температура отпуска заметно снижает прочность, но повышает пластичность и ста-бильность размеров.
При термообработке литых сплавов, вследствие весьма грубой структуры, применяют длительные нагревы. Нагревая при закалке в соляных ваннах детали сложной формы, их предварительно подогревают в электропечах до 300 – 350 °С. При обработке алюминиевых сплавов в воздушных печах для обеспечения равномерности нагрева следует применять печи с принудительным перемешиванием атмосферы печи (типа ПН-31 и др.).
|
Алюминиевые литейные сплавы с высоким содержанием магния (АЛ8) из-за опасности возгорания следует нагревать под закалку в воздушных печах, а не в селитровых ваннах. Период между выемкой из печи и охлаждением должен быть наименьшим. Чем сложнее деталь, тем выше следует применять температуру охлаждающей среды.
Й разряд.
1. Отпуск стали. Отпуск применяют для уменьшения или полного снятия напряжений, уменьшения твердости закаленной стали и увеличения пластичности.
Отпуском стали называют операцию термической обработки, при которой закаленную сталь нагревают до температуры ниже критической точки Ас1, выдерживают и затем охлаждают. Обычно охлаждение после отпуска производится на воздухе.
Нагрев при отпуске производят в масляных, селитровых или щелочных ваннах, а также в печах с воздушной атмосферой. Общее время пребывания изделия в печи при отпуске составляет примерно 2-3 мин. на 1 мм наименьшего сечения, но не менее 30-40 мин.
В любой закаленной на мартенсит стали появляются не только высокая твердость и прочность, но и большие внутренние напряжения. Поэтому закаленная сталь очень хрупка и легко разрушается от ударных и изгибающих нагрузок. Для снятия внутренних напряжений и повышения вязкости закаленную сталь подвергают отпуску.
Структура закаленной стали - мартенсит, представляет собой твердый раствор углерода в решетке α-железа т.е. в объемно- центрированной тетрагональной кристаллической решетке, с такой же концентрацией, как у исходного аустенита. Углерод находится в центре грани. Микроструктура мартенсита характеризуется игольчатостью и высокой твердостью (64-65 НRС), высоким пределом прочности, большой хрупкостью и магнитными свойствами. Мартенсит закаленной стали является неустойчивой структурой, поэтому при отпуске из него выделяется углерод и образуются зерна цементита.
При низких температурах (низкий отпуск) тетрагональный мартенсит переходит в отпу-щенный, при более высоких (средний и высокий отпуск) – в троостит отпуска и затем в сорбит, и структура из неустойчивого состояния переходит в более равновесное, в резуль-тате чего внутренние напряжения уменьшаются. Такие изменения в структуре закаленной стали приводят к изменению ее физико - механических свойств.
|
В зависимости от требуемых свойств стали различают три вида отпуска: низкий - при температуре 150 – 250 °С, средний - при температуре 350 – 500 °С и высокий - при температуре 500 – 680 °С.
Низкотемпературный (низкий) отпуск проводят с нагревом до 250 °С. При этом снижаются внутренние напряжения, мартенсит закалки переходит в отпущенный мартенсит, повышается прочность и немного улучшается вязкость без заметного снижения твердости. Закаленная сталь (0,6-1,3 %С) после низкотемпературного отпуска сохраняет твердость в пределах 58 - 63 НRС, а, следовательно, высокую износостойкость. Но такие изделия, если они не имеют вязкой сердцевины, не выдерживают значительных динамических нагрузок.
Низкотемпературному отпуску подвергают режущий и измерительный инструмент, а также детали, после поверхностной закалки, цементации, цианирования или нитроцементации. Продолжительность отпуска 1 - 2,5 часа, а для изделий больших сечений и измерительного инструмента назначают более длительный отпуск.
Среднетемпературный (средний) отпуск выполняют при 350 – 500 °С и применяют для пружин и рессор, а также штампов и ударного режущего инструмента. Такой отпуск обеспечивает высокий предел упругости, предел выносливости и релаксационную стойкость. Структура стали после среднего отпуска - троостит отпуска или троостомартенсит и твердость стали 40 - 50 НRС, твердость троостита отпуска 300 - 400 НВ. Температуру отпуска выбирают так, чтобы не вызвать необратимой отпускной хрупкости.
Охлаждение после отпуска при 400-450 °С следует проводить в воде, что способствует образованию на поверхности сжимающих остаточных напряжений, которые увеличивают предел выносливости пружин.
Высокотемпературный (высокий) отпуск. Температура отпуска 500 – 600 (680) °С.
Процесс термической обработки, заключающийся в закалке с последующим высоким отпуском при 500°С и выше, называют у лучшением. Улучшение применяют для измельче-ния структуры, а также для получения наилучшего сочетания прочности и вязкости конструкционной стали, главным образом, легированной. Структура стали после высокого отпуска – сорбит отпуска. Твердость сорбита отпуска 250 - 300 НВ.
|
Улучшению подвергают среднеуглеродистые (0,3-0,5 %С) конструкционные стали, к кото-рым предъявляются высокие требования к пределу выносливости и ударной вязкости. Одна-ко износостойкость улучшенной стали вследствие ее пониженной твердости не является вы-сокой. Улучшение значительно повышает конструктивную прочность стали, уменьшая чувст-вительность к концентраторам напряжений, увеличивая работу развития трещины и снижая температуру верхнего и нижнего порога хладноломкости.
Дефекты отпуска.
Переотпуск. Снижение твердости и прочности стали при завышении заданной температуры отпуска. Исправляется повторным отжигом или нормализацией, а затем производят повторную закалку и отпуск по нормальному режиму.
Недоотпуск. Возрастание твердости и прочности в результате температуры отпуска ниже заданной. Исправление брака - повторный отпуск при нормальном режиме.
Отпускная хрупкость стали (снижение величины ударной вязкости) наблюдается при отпуске углеродистых доэвтектоидных и некоторых легированных сталей в интервале температур 250 – 400 °С – хрупкость I рода и 500 – 600 °С - хрупкость II рода и медленного охлаждения.
Предупреждение брака:
1) охлаждение в воде или масле после отпуска при 400 – 600 °С;
2) применение стали, содержащей молибден, титан и ниобий.
Исправление брака: повторный отпуск с охлаждением в масле при повышении температуры отпуска на 20-30 °С выше первого.
Дефекты закалки и методы их устранения смотри в ответах по 4-му разряду.
2. Цианирование -насыщение поверхности стальных деталей углеродом и азотом.Существуют два вида цианирования:
1) высокотемпературное - с целью повышения твердости, износостойкости и усталостной прочности деталей из конструкционных сталей;
2) низкотемпературное - с целью повышения твердости и красностойкости инструмента из быстрорежущей стали.
Высокотемпературное жидкое цианирование. Цианированию подвергают детали из конструкционных малоуглеродистых сталей, которые содержат углерода 0,1-0,4 %. Оно производится в ваннах с расплавленными нейтральными солями такими, как NaCl, BaCl2, Na2CO3 и т.д. В качестве карбюризатора используют цианистые соли NaCN и KCN, основ-ной компонент (циан), который способствует насыщению деталей углеродом и азотом. В цианированном слое образуются карбиды и нитриды железа. При цианировании глубина слоя не превышает 0,15- 0,35 мм.
Рабочая температура обычного жидкого цианирования 830 – 860 °С, а глубокого – 900 – 950 °С. Закалку производят непосредственно в цианистой ванне с подстуживанием на возду-хе до 780 – 800 °С. Отпуск осуществляется при температуре 160 – 180 °С. Твердость слоя 65-67 НRС.
|
Высокотемпературное цианирование в газовой среде. Газовое цианирование производят в смеси аммиака с углеродосодержащими газами, применяемыми при газовой цементации, в шахтных печах. Цианирующая смесь содержит: аммиака 20-30 %, науглероживающего газа 70-80 %. Рабочая температура газового цианирования 840 – 860 °С. Для деталей простой формы можно повысить температуру до 900 °С. Закалку деталей, прошедших жидкое и газовое цианирование следует производить непосредственно из печи по окончании цианирования. При высокой температуре цианирования производится подстуживание детали на воздухе. После закалки детали проходят отпуск при 160 – 200 °С. Мелкие, неответственные детали из малоуглеродистой стали отпуску не подвергаются.
Глубина цианированного слоя на деталях в зависимости от температуры и времени выдерж-ки составляет 0,15- 1,4 мм.
Низкотемпературное цианирование в жидкой среде применяют для повышения твердости (на 2-4 единицы выше по сравнению с обычной закалкой), износостойкости и красностойкости режущего инструмента. Низкотемпературное цианирование производят при 550 – 570 °С для быстрорежущих сталей Р18 и Р9 и при 510 – 520 °С для высокохромистых сталей. Цианирование осуществляется в соляных ваннах, которые содержат 50 % NaCN и 50 % KCN. Глубина цианированного слоя составляет 0,02- 0,035 мм.
Низкотемпературное цианирование в газовой среде. Состав цианирующей газовой среды такой же, и соотношение такие же, как и при высоко температурном цианировании. После окончания выдержки при 540 – 560 °С инструмент охлаждают на воздухе или с печью до 200 °С. В последнем случае он приобретает серебристый цвет.
Цианистые соли ядовиты, поэтому ванны с такими солями изолируются защитными колпаками с отсасывающей вентиляцией. Процесс требует тщательной подготовки инструмента и соблюдения точности геометрических размеров после обработки.
Й разряд.
1. Поверхностная закалка. Многие ответственные детали работают на истирание и одновременно подвергаются ударным нагрузкам. Такие детали должны иметь высокую поверхностную твердость, хорошую износостойкость и в то же время не быть хрупкими, т.е. не разрушаться под действием ударов. Высокая твердость поверхности деталей при сохранении вязкой и прочной сердцевины достигается методом поверхностной закалки, т.к. детали закаливаются только с поверхности на некоторую (заданную) глубину, тогда как сердцевина остается незакаленной и воспринимает ударные нагрузки.
Из современных методов поверхностной закалки наибольшее распространение находят следующие: закалка при нагреве токами высокой частоты (ТВЧ); пламенная закалка и закал-ка в электролите. Выбор того или иного метода поверхностной закалки обуславливается технологической и экономической целесообразностью.
Особенностью нагрева ТВЧ является то, что индуктируемые в стали вихревые токи распределяются по сечению детали неравномерно, а оттесняются к поверхности. Неравномерное распределение вихревых токов приводит к неравномерному ее нагреву: поверхностные слой очень быстро нагреваются до высоких температур, а сердцевина или совсем не нагревается или нагревается незначительно благодаря теплопроводности стали. Толщина слоя, по которому проходит ток, называется глубиной проникновения и обозначается буквой d. Толщина слоя зависит от частоты переменного тока, удельного электросопротивления металла и магнитной проницаемости. Эту зависимость определяют по формуле
d = 5,03*104 Ö ρ/ μ* ν мм, (10)
где ρ – удельное электросопротивление, Ом* мм²/м;
μ - магнитная проницаемость, гс/э;
ν - частота, гц.
Микроструктура поверхностного слоя представляет собой мелкоигольчатый мартенсит, твердость поверхностного слоя деталей при нагреве ТВЧ, получается на 3-4 единицы выше, чем твердость при обычной объемной закалке.
Для повышения прочности сердцевины детали перед закалкой на ТВЧ подвергают улучшению или нормализации.
Применение ТВЧ дает возможность изготавливать для закалки деталей механизированные и автоматизированные линии (агрегаты), которые устанавливаются в общем потоке механообрабатывающих цехов.
Пламенная поверхностная закалка. Этот метод заключается в нагреве поверхности стальных деталей ацетилено- кислородным пламенем до температуры, превышающей на 50-60 °С верхнюю критическую точку Ас3, с последующим быстрым охлаждением водяным душем.
Сущность процесса - тепло, подводимое газовым пламенем от горелки к закаливаемой детали, концентрируется на ее поверхности и значительно превышает количество тепла, распространяемого вглубь металла. В результате такого температурного поля поверхность детали сначала быстро нагревается до температуры закалки, затем охлаждается, а сердцевина детали практически остается незакаленной и после охлаждения не изменяет свою структуру и твердость.
Пламенную закалку применяют для упрочнения и повышения износостойкости крупных и тяжелых стальных изделий: коленчатых валов механических прессов, ковшей экскаваторов и т.д. Кроме стальных деталей пламенной закалке подвергают детали, изготовленные из серо-го и перлитного чугуна, например направляющие станин металлорежущих станков.
В зависимости от назначения детали глубина закаленного слоя обычно берется равной 2,5 - 4,5 мм.
Основными факторами, влияющими на глубину закалки и структуру закаливаемой стали, являются скорость передвижения закалочной горелки относительно детали; скорость выхода газов и температуры пламени. В качестве горючих газов применяют ацетилен и кислород.
После пламенной закалки закаленный поверхностный слой получает высокую твердость и остается чистым, без следов окисления и обезуглероживания. Переход структуры от поверхности детали к сердцевине происходит плавно, что имеет большое значение для повышения эксплуатационной стойкости деталей и полностью устраняет вредные явления – растрескивание и отслоение закаленных слоев металла. На поверхности детали твердость равна 56-57 НRС, а потом понижается до твердости, которую имела деталь до поверхностной закалки.
|
|
Состав сооружений: решетки и песколовки: Решетки – это первое устройство в схеме очистных сооружений. Они представляют...
Адаптации растений и животных к жизни в горах: Большое значение для жизни организмов в горах имеют степень расчленения, крутизна и экспозиционные различия склонов...
Таксономические единицы (категории) растений: Каждая система классификации состоит из определённых соподчиненных друг другу...
Механическое удерживание земляных масс: Механическое удерживание земляных масс на склоне обеспечивают контрфорсными сооружениями различных конструкций...
© cyberpedia.su 2017-2024 - Не является автором материалов. Исключительное право сохранено за автором текста.
Если вы не хотите, чтобы данный материал был у нас на сайте, перейдите по ссылке: Нарушение авторских прав. Мы поможем в написании вашей работы!