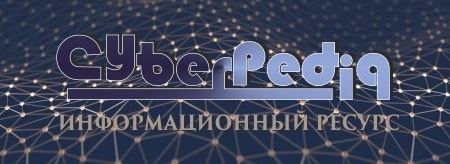
Папиллярные узоры пальцев рук - маркер спортивных способностей: дерматоглифические признаки формируются на 3-5 месяце беременности, не изменяются в течение жизни...
Кормораздатчик мобильный электрифицированный: схема и процесс работы устройства...
Топ:
Процедура выполнения команд. Рабочий цикл процессора: Функционирование процессора в основном состоит из повторяющихся рабочих циклов, каждый из которых соответствует...
Характеристика АТП и сварочно-жестяницкого участка: Транспорт в настоящее время является одной из важнейших отраслей народного хозяйства...
Эволюция кровеносной системы позвоночных животных: Биологическая эволюция – необратимый процесс исторического развития живой природы...
Интересное:
Аура как энергетическое поле: многослойную ауру человека можно представить себе подобным...
Инженерная защита территорий, зданий и сооружений от опасных геологических процессов: Изучение оползневых явлений, оценка устойчивости склонов и проектирование противооползневых сооружений — актуальнейшие задачи, стоящие перед отечественными...
Мероприятия для защиты от морозного пучения грунтов: Инженерная защита от морозного (криогенного) пучения грунтов необходима для легких малоэтажных зданий и других сооружений...
Дисциплины:
![]() |
![]() |
5.00
из
|
Заказать работу |
|
Рис. 5.3. Мартеновская печь:
1 – под печи; 2 – бетонные опоры; 3 – вертикальные каналы; 4 – газовый канал; 5 – воздушный канал головки; 6 – откос; 7 – свод; 8 – загрузочные окна; 9 – крепление воздушного и газового каналов; 10 – крепление пода печи; 11 – передняя стенка; 12 – задняя стенка
Современные мартеновские печи (рис. 5.3) отапливают обычно смесью доменного и коксовального (иногда природного) газа и оборудуют четырьмя регенераторами (по два с каждой стороны печи), с насадками (кирпичной решетчатой кладкой), для раздельного подогрева газообразного топлива и воздуха, подаваемых в печь. Продукты горения из рабочего пространства печи направляются в одну пару регенераторов, например в правую, и нагревают их насадку, а затем выпускаются в дымовую трубу. В это время газовое топливо и воздух подают в печь через вторую пару регенераторов, насадка которых была нагрета раньше. Через некоторое время с помощью автоматически переключающихся клапанов меняется направление выхода печных газов и подачи топлива.
Мартеновские печи строят разной вместимости (10…500 т). На некоторых заводах работают печи, отапливаемые мазутом или природным газом, в которых подогревается только воздух, подающийся в. печь.
В первых печах, предложенных П. Мартеном, под, стены и свод выкладывали из динасового огнеупорного кирпича. В 1880г. в России была построена первая мартеновская печь с подом и стенками из доломитового кирпича. Затем такие печи получили широкое распространение. В современном сталеплавильном производстве для кладки стен и пода печей применяют как кислые, так и основные огнеупоры, этим отличается устройство основных и кислых мартеновских печей. Ванна печи, удерживающая расплавленные материалы, имеет форму чаши, и ее длину и ширину обычно определяют на уровне порогов садочных окон, через которые и загружают в печь твердые материалы. Современная 500-тонная печь имеет ванну 16,4м длины, 5,9м ширины и более 1м глубины. Произведение длины на ширину принято считать условной площадью пода мартеновской печи. Глубиной ванны считают расстояние от самой глубокой ее части, которая расположена около выпускного отверстия (т. е. от подины), до уровня порогов садочных окон.
Боковую кладку и под укрепляют снаружи прочными стальными балками. До недавнего времени своды мартеновских печей делали арочными и выкладывали динасовым кирпичом. Такие своды не допускали их нагрев выше 1700°С, что тормозило производительность печей; эти своды обычно выдерживали 200…250 плавок. Теперь, своды делают из термостойкого хромомагнезитового кирпича. Изменилась и конструкция свода. Отдельные блоки свода подвешивают на тягах к поперечным балкам каркаса печи, и свод получается подвесным.
Теперь свод выдерживает нагрев до 1800°С. Подвесные хромомагнезитовые своды выдерживают 500 плавок. Газ подают в печь по центральному каналу, воздух — по двум боковым. Сходясь в рабочем пространстве печи, эти каналы образуют так называемую головку печи, формирующую газовое пламя. Внутрь стенок головки обычно вставляют кессоны, в которых циркулирует вода для сохранения огнеупоров головки от быстрого разгара.
Перед регенераторами в мартеновской печи устанавливают шлаковики для сбора пыли и капель шлака, выносимых из печи с отходящими газами, и предохранения регенераторов от быстрого загрязнения. Твердую шихту в печь загружают через окна с помощью завалочных машин. Выпуск стали и шлака из мартеновской печи после завершения плавки проводят через летку (выпускное отверстие) в задней продольной стенке печи. Некоторое количество шлака выпускают иногда через так называемые ложные пороги загрузочных окон на лицевую сторону печи. На время плавки летку заделывают магнезитовым порошком и огнеупорной глиной.
Для переработки чугунов, содержащих много фосфора, иногда применяют качающиеся мартеновские печи, рабочее пространство которых располагают на катках. Это облегчает и ускоряет удаление (скачивание) в процессе передела фосфористых шлаков и тем самым повышает производительность печи.
Мартеновский способ получил широкое применение благодаря возможности использования различного сырья и разнообразного топлива. В настоящее время различают следующие разновидности мартеновского процесса в зависимости от.используемого сырья: скрап-процесс — шихта состоит из 60…70 % стального лома и 30…40 % твердого чушкового чугуна (эта разновидность процесса применяется на заводах, не имеющих доменного производства); скрап-рудный процесс — шихта состоит из 20…50 % скрапа и 50…80 % жидкого чугуна, который после выпуска из доменных печей хранится в миксерах. Скрап-рудным процесс называют потому, что для ускорения окисления примесей чугуна в печь загружают, кроме того, гематитовую железную руду в количестве 15…30 % от массы металлической части шихты.
.Процесс в кислой и основной мартеновских печах проходит различно (меняется состав флюсов и некоторых других шихтовых материалов, по-разному идет окисление примесей). Поэтому различают кислый и основной мартеновские процессы.
Рассмотрим кратко сущность широко применяемого на наших заводах основного скрап-рудного процесса. Мартеновские печи работают циклами, но нагрев печи ведется непрерывно, поэтому подготовка новой плавки стали начинается с осмотра печи и устранения изъянов в подине и боковых откосах печи путем их заварки новым слоем доломита или магнезита еще во время выпуска предыдущей плавки. После выпуска металла выпускное отверстие заделывают и загружают шихту для новой плавки. Сыпучие шихтовые материалы (руда, известняк, скрап) загружают обычно первыми и отдельные их слои хорошо прогревают. На подину, принято сначала засыпать железную руду, потом известняк, и сверху стальной лом. Все эти материалы подвозят к печам на железнодорожных платформах в так называемых мульдах (металлические коробки с приспособлением для захвата их хоботом завалочной машины).
Завалочная машина — это самоходная тележка, перемещающаяся по рельсам вдоль продольных лицевых стенок нескольких мартеновских печей, обычно расположенных в одну линию. На самоходной тележке установлена кабина машиниста с пультом управления и загрузочный механизм с длинным штоком (хоботом). Хобот завалочной машины поднимает с платформы мульду с шихтой, вносит ее в печь и, поворачивая, высыпает содержимое, затем выносит пустую мульду из печи, и ставит ее на платформу.
Во время загрузки твердых материалов в печь расходуется максимальное количество топлива для обеспечения быстрого прогрева и расплавления шихтовых материалов. Жидкий чугун загружают в печь через окно с помощью вставляемого в него стального желоба, футерованного изнутри огнеупором. Жидкий чугун подают к печи в чугуновозном ковше с помощью мостового крана. Чугун заливают в печь через желоб, вставляемый в одно из загрузочных окон, когда твердая шихта прогрета и начинает оплавляться. После заливки жидкого чугуна резко ускоряется плавление металлической части шихты. Одновременно с прогревом шихты начинается окисление примесей. К моменту расплавления шихты почти полностью окисляется кремний, более половины марганца, третья часть фосфора и частично углерод. Во время плавления образуется значительное количество FеО, так как количество воздуха, подаваемого в мартеновскую печь, обычно больше, чем необходимо для сжигания топлива, и пламя в мартеновской печи бывает окислительным. Образующаяся закись железа, растворяясь в шлаке, окисляет примеси.
[Si] + 2(FеО) = [2Fе] + (SiO2); 2 [Р] + 8 (FеО) = [5Fе] + (ЗFеО • РаО5); [Мn] + (FеО) = Fе + (МпО); [С] + (FеО) = [Fе] + СО
Окисление углерода в еще не прогретой ванне вызывает вспенивание шлака. Этим пользуются для удаления из печи самотеком через пороги загрузочных окон (в некоторых печах есть и отдельные летки) части первичного шлака, содержащего значительное количество фосфора в виде ЗFеО• Р2О5 и кремнезем. Скачивание шлака продолжается в крупных печах в течение 1…2 ч; оно сокращает потребность в известняке и уменьшает слой шлака в печи, что в свою очередь улучшает прогрев металла. К концу плавления шихты известняк, прогревшись, переходит в известь
СаСО3 → СаО + СО2 и, всплывая, растворяется в шлаке.
После расплавления шихты начинается период доводки стали. В печи образуется ванна металла, покрытая сверху слоем шлака, содержащего значительное количество окислов железа. Они взаимодействуют с жидким металлом
(Fе203) + [Fе] = 3(FеО)
Образующаяся закись железа растворяется в шлаке и благодаря интенсивному перемешиванию ванны попадает в металл, диссоциирует в нем на ионы и активно окисляет примеси, в том числе и углерод;
(FеО) + [С] = [Fе]+ CO
Образующаяся окись углерода в виде газовых пузырьков хорошо перемешивает ванну и способствует выделению из металла газовых и других включений.
Этот процесс выделения угарного газа называют кипением ванны. В это время для интенсификации процесса кипения, в печь добавляют железную руду. Увеличение окислов железа в шлаке ускоряет процесс. При перемешивании шлака образовавшаяся в нем закись железа, соприкасаясь с окислительными газами печи, переходит в окись, которая в свою очередь окисляет металл. Таким образом, шлак в ванне мартеновской печи, интенсивно перемешиваемый тепловыми потоками и выделяющимся из металла газом, передает металлу теплоту и кислород.
В этот же период из шихтовых материалов удаляют фосфор периодическим скачиванием шлака. Важную роль для связывания окислов фосфора в этот период играет известь, так как соединения типа ЗFеО • Р2О5 при высоких температурах нестойки. Фосфор связывают в этих условиях известью по уравнению
ЗFеО • Р2О5 + 4СаО = 4СаО • Р2О3 + ЗFеО
Для успешного удаления фосфора необходимо иметь в шлаке максимальное количество извести, не связанное кислотными окислами (главным образом SiO2). Однако большой избыток извести делает шлаки более тугоплавкими, что затрудняет мартеновскую плавку. Наличие свободной окиси кальция способствует также и переводу в шлак соединений серы, присутствующих в металле, по уже известной нам реакции
[Fе] + [S] + (СаО) ↔ (FеО) + (СаS)
Но в условиях мартеновской плавки обратимость этой реакции не.позволяет полностью удалить серу, поэтому ее присутствие в компонентах шихты крайне нежелательно.
Процесс доводки металла до нужного химического состава производится в так называемый период чистого кипения металла, начинающегося после прекращения добавок в неё железной руды. Чистое кипение ванны протекает не менее одного часа. Готовность заданной плавки стали определяют взятием пробы и экспресс-анализом в цеховой лаборатории.
После этого проводится раскисление и выпуск стали в ковши, из которых ее разливают в слитки. Раскисление стали в ванне мартеновской печи проводят сначала доменным ферромарганцем, а затем доменным ферросилицием. Кремний ферросилиция отнимает кислород от закиси железа и образует сложные силикаты железа и марганца, которые обладают низкой температурой плавления и малой плотностью. Они всплывают в ванне и переходят в шлак. После этого сталь начинают выпускать из печи и завершают раскисление в ковше (или на желобе, по которому она вытекает в ковш), богатым ферросилицием (45 % или 75 % Si), и вводят небольшое количество более сильного восстановителя — обычно алюминия или силикоалюминия.
Алюминий является активным раскислителем стали, но образующаяся окись алюминия тугоплавка и в виде тонкой взвеси остается в стали. Принято считать, что эти частички окиси алюминия являются центрами кристаллизации при формировании слитка, и с увеличением количества алюминия, вводимого для раскисления, можно получить более мелкую структуру слитка или отливки. Обычно для раскисления берут 100…400 г алюминия на 1 т выплавляемой стали в зависимости от ее марки. Шлакосновных мартеновских печей, получаемый при завершении процесса, обычно содержит 10…15% FeO, 9…15% MnO, 18…25% SiO2, 40…47% CaO, 1% P2O5,, а также MgO, Al2O3 и другие окислы.
Вопросы для повторения и закрепления:
1. Каково устройство мартеновской печи?
2. Какое назначение имеют регенераторы при мартеновской плавки стали?
3. Что является шихтой, применяемой при мартеновской плавке?
История развития пистолетов-пулеметов: Предпосылкой для возникновения пистолетов-пулеметов послужила давняя тенденция тяготения винтовок...
Автоматическое растормаживание колес: Тормозные устройства колес предназначены для уменьшения длины пробега и улучшения маневрирования ВС при...
Архитектура электронного правительства: Единая архитектура – это методологический подход при создании системы управления государства, который строится...
Особенности сооружения опор в сложных условиях: Сооружение ВЛ в районах с суровыми климатическими и тяжелыми геологическими условиями...
© cyberpedia.su 2017-2024 - Не является автором материалов. Исключительное право сохранено за автором текста.
Если вы не хотите, чтобы данный материал был у нас на сайте, перейдите по ссылке: Нарушение авторских прав. Мы поможем в написании вашей работы!