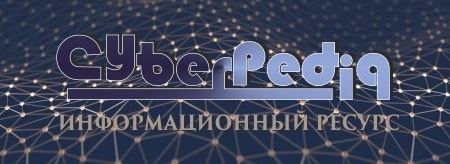
Таксономические единицы (категории) растений: Каждая система классификации состоит из определённых соподчиненных друг другу...
Состав сооружений: решетки и песколовки: Решетки – это первое устройство в схеме очистных сооружений. Они представляют...
Топ:
История развития методов оптимизации: теорема Куна-Таккера, метод Лагранжа, роль выпуклости в оптимизации...
Теоретическая значимость работы: Описание теоретической значимости (ценности) результатов исследования должно присутствовать во введении...
Определение места расположения распределительного центра: Фирма реализует продукцию на рынках сбыта и имеет постоянных поставщиков в разных регионах. Увеличение объема продаж...
Интересное:
Финансовый рынок и его значение в управлении денежными потоками на современном этапе: любому предприятию для расширения производства и увеличения прибыли нужны...
Подходы к решению темы фильма: Существует три основных типа исторического фильма, имеющих между собой много общего...
Аура как энергетическое поле: многослойную ауру человека можно представить себе подобным...
Дисциплины:
![]() |
![]() |
5.00
из
|
Заказать работу |
|
|
Испытание на растяжение
Для этого вида испытания изготовляют стандартные образцы (рис. 3.1, а). В зависимости от площади поперечного сечения различают нормальные и пропорциональные образцы.
Нормальные образцы имеют площадь поперечного сечения 314мм 2 (d 0 = 20мм). Они бывают двух видов: длинные (длина расчетной части l 0 = 200мм, а отношение l 0 ⁄ d 0 = 10) и короткие (l 0 =100 мм и l 0 /d 0 = 5).
Рис. 3.1. Испытание на растяжение:
а — стандартные образцы для испытания на растяжение;
б — диаграмма растяжения пластичного материала
Площадь поперечного сечения пропорциональных образцов может быть произвольная, а расчетную длину определяют по формуле
l0=11,3 или l0=6,65
где F0 — исходная площадь поперечного сечения образцов, мм2. Литые образцы и образцы из
хрупких материалов изготовляют с расчетной длиной l 0 = 2,821 ____
______________При испытаниях образец растягивают до момента его разрыва. При этом вычерчивается диаграмма растяжения образца (рис. 3.1, б). По вертикальной оси диаграммы откладывается нагрузка Р, по горизонтальной — абсолютное удлинение образца ∆ l.
На диаграмме можно отметить характерные участки и точки. На участке ОР удлинение ∆ l образца увеличивается прямо пропорционально нагрузке Рр,называемой нагрузкой предела пропорциональности.
Пределом пропорциональности σрназывают наибольшее напряжение, до которого относительное удлинение образца остается прямо пропорциональным нагрузке Рр.. Его определяют по формуле (в Н/м2 или Па)
σр = Рр / F0
Нагрузка Р, при которой образец получает остаточное удлинение, равное 0,005% расчетной длины, называют нагрузкой предела упругости.
Пределом упругости σ е называют такое напряжение, при котором остаточное удлинение получается равным 0,005% первоначальной расчетной длины образца. Его определяют по формуле
|
σ е = Ре / F0
Выше точки Рт кривая диаграммы растяжения плавно переходит в горизонтальный участок. При этом образец удлиняется без увеличения нагрузки (металл как бы течет).
Нагрузку Рт, при которой начинается течение металла, называют нагрузкой предела текучести, а горизонтальный участок кривой — площадкой текучести.
Пределом текучести σт называют наименьшее напряжение, при котором образец деформируется без заметного увеличения нагрузки. Его определяют по формуле
σт = Рт / F0.
Условным пределом текучести σ0,2 называют напряжение, при котором остаточное удлинение образца равно 0,2% расчетной длины, т.к. у некоторых металлов площадка текучести отсутствует
За площадкой текучести нагрузка снова растет до некоторой максимальной величины Рв, после которой на образце начинается образование местного сужения (шейки). Уменьшение сечения в области шейки вызывает снижение нагрузки, и в точке К принагрузке Рz происходит разрыв образца. Наибольшую нагрузку Рв, при которой начинается образование шейки, называют нагрузкой предела прочности при растяжении.
Пределом прочности прирастяжении называют напряжение σв, соответствующее наибольшей нагрузке Рв.
Определяют его по формуле
σв ═ Pв/ F0
Истинным сопротивлением разрыву σz называют напряжение, определяемое отношением нагрузки в момент разрыва к площади поперечного сечения образца в месте разрыва
σz ═ Pz / F0
Полная деформация образца ∆ lП складывается из остаточной ∆ lост и упругой деформации ∆ lупр Для определения этих деформаций необходимо на диаграмме растяжения из точки К провести прямую, параллельную прямолинейному участку кривой, до пересечения с осью абсцисс.
Относительным удлинением δ называют отношение приращения длины образца после разрыва к его расчетной длине, выраженное в процентах
|
δ ═ l1 – l0 / l0 × 100%
где 11 — длина образца после разрыва, мм; / 0 — расчетная длина образца, мм.
Относительным сужением Ψ называют отношение уменьшения площади поперечного сечения образца после разрыва к начальной площади поперечного сечения, выраженное в процентах:
Ψ ═ F0 – F1 / F0 × 100%
где F0 — начальная площадь поперечного сечения образца, мм2; F1 - конечная площадь поперечного сечения образца, мм2.
Вопросы для повторения и закрепления:
1. Как определяют предел прочности при растяжении?
2. Что называют относительным удлинением?
3. Что называют текучестью металла?
4. Что называют пределом пропорциональности?
Испытание на твёрдость
Под твёрдостью понимают сопротивление испытуемого металла вдавливанию в него металлического или алмазного наконечника. Определение твёрдости является наиболее часто применяемым методом испытания металлов. Для определения твёрдости не требуется изготовления специальных образцов, т.е. испытание может проводиться на реальной детали без её разрушения. Для этой цели применяют несложные по устройству и простые в обращении приборы.
Испытание на твердость по Бринеллю. В поверхность испытуемого металла с определенной силой вдавливают стальной закаленный шарик диаметром 1; 2; 2,5; 5 и 10мм (рис. 3.2, а). В результате на поверхности металла получается отпечаток (лунка). Число твердости по Бринеллю НВ — характеризуется отношением нагрузки, действующей на шарик, к поверхности отпечатка:
НВ ═ F ∕ 9,8 S ═ F ∕ 9,8 π D (D − )
где Р — нагрузка на шарик, Н; S — поверхность отпечатка, мм2; D — диаметр вдавливаемого шарика, мм; d — диаметр отпечатка, мм.
Рис.3.2. Схема определения твердости.
а – по Бринеллю; б – по Роквеллу; в – по Виккерсу
Для того чтобы не вычислять твердость по приведенной выше формуле, на практике пользуются специальной таблицей, в которой диаметру отпечатка соответствует определенное число твердости НВ.
Выбор диаметра шарика D, нагрузки и продолжительности выдержки под нагрузкой зависит от твердости материала и толщины детали. При этом диаметр d отпечатка должен находиться в пределах 0,2D < d< 0,6D.
При измерении твердости шариком D= 10мм под нагрузкой F =29,4 кН в течение 10с твердость обозначается символом НВ, например НВ 200. При других условиях измерения после символа НВ указывают диаметр шарика, значение нагрузки в кгс и продолжительность выдержки под нагрузкой. Например, из обозначения твердости НВ 5/250/30 — 200 следует, что число твердости 200 получено при испытании шариком диаметром D = 5мм под нагрузкой F = 2,45 кН (250 кгс) в течение 30с.
|
Испытание на твердость по Роквеллу. В поверхность испытуемого металла вдавливают алмазный конус с углом 120о или стальной закалённый шарик диаметром 1,59мм
Шарик и конус вдавливают в испытуемый образец, последовательно прилагая предварительную F0 и основную F1 нагрузку. Общая нагрузка (рис. 3.2, б)
F=F0+F1
Предварительная нагрузка. F 0 во всех случаях равна 98 Н, а основная F1 и общая F нагрузки составляют:
при вдавливании стального шарика (шкала В)
F! ═ 882 H; F ═ 980 H
при вдавливании алмазного конуса (шкала С)
F1 =1372 Н; F =1470 Н; при вдавливании алмазного конуса (шкала А)
F1 ═ 490 H; F ═ 588 H (по шкале А измеряют твёрдость очень твердых материалов, а также тонких образцов)
Твердость по Роквеллу выражается в условных единицах; ее обозначают в зависимости от условий испытания - НRА, НRВ, НRС (согласно с наименованием шкалы). Твердость определяют по глубине отпечатка h. За единицу твердости принята величина, соответствующая осевому перемещению наконечника на 0,002мм.
Определение твердости по Роквеллу имеет широкое применение, так как дает возможность испытывать твердые и мягкие материалы; при этом отпечатки от конуса или шарика очень малы, поэтому можно испытывать готовые детали без их порчи; испытание выполняется легко и быстро (30 — 60 с).
Испытание на твёрдость по Виккерсу. В поверхность металла вдавливают четырехгранную алмазную пирамиду с углом при вершине 136о (рис.3.2, в). Число твердости НV определяют по формуле
HV═ 2F ∕ 0,8 d2 sin α ∕ 2 ═ F ∕ d 2
где F —- нагрузка на пирамиду, Н; d — среднее арифметическое длины обеих диагоналей отпечатка после снятия нагрузки, мм; α = 1360 — угол между противоположными гранями пирамиды при вершине.
При испытании применяют нагрузки от 9,8 до 980Н. Возможность применения малых нагрузок позволяет испытывать твердость поверхностных слоев (например, после цианирования, азотирования).
|
Для определения числа твердости НV пользуются специальными таблицами.
Испытание на микротвёрдость применяют при определении твердости микроскопически малых объемов металла, например твердости отдельных структурных составляющих сплавов.
Микротвердость определяют «а специальном приборе (рис. 3.3, а), состоящем из механизма нагружения с алмазным наконечником и металлографического микроскопа. Поверхность образца подготавливают также, как и для микроисследования (шлифование, полирование, травление). Четырехгранная алмазная пирамида (с углом при вершине 136°, как и у пирамиды при испытании по Виккерсу) вдавливается в испытываемый материал под очень небольшой нагрузкой 0,049…4,9 Н.
Число твердости Н определяют по размерам отпечатков (рис. 3.3, б), как и твердость по Виккерсу.
Значение микротвёрдости находят по специальным таблицам.
Рис.3.3. Прибор для испытания на микротвердость и отпечатки на микрошлифе
а – прибор для испытания; б – отпечаток на микрошлифе
1 – образец; 2 – алмазная пирамида; 3 – груз; 4 – окуляр; 5 – объектив.
Вопросы для повторения и закрепления:
1. Что называется твёрдостью металла?
2. С какой целью определяют твердость металла?
3. В каких случаях применяют тот или иной способ определения твёрдости?
4. Почему у прибора Рокквела несколько шкал твёрдости?
Задание:
Составить план ответа по разделу «Методы испытания механических свойств металлов»
3.3 Испытание на ударный изгиб
Динамические испытания на ударный изгиб выявляют склонность металла к хрупкому разрушению. Метод основан на разрушении образца с концентратором посредине одним ударом маятникового копра (рис.3.4.а). Ударная вязкость ан, кгс м/см2, (КС) определяется работой Ан,необходимой для излома образца, отнесенной к площади образца.
Рис.3.4. Схема маятникового копра (а) и образца при испытании (б).
1 – образец; 2 – маятник; 3 – шкала; 4 – стрелка шкалы; 5 – тормоз.
Образец устанавливают на двух опорах, затем наносят удар по его середине (рис.3.4.б) со стороны, противоположной надрезу. Работа, затраченная на разрушение образца (рис.3.4.б)
Ан ═ Рh1 (соs β — соs α)
где Р — масса маятника, кг; h1 — расстояние от оси маятника до его центра
тяжести, м; β — угол подъема маятника после разрушения образца; α – угол подъема маятника перед ударом.
Формула дает возможность подсчитать Ан по измеренным углам α и β (Р и h1 —постоянные для данного копра)
В пластичном состоянии у металлов ан>5…7 кгс-м/см2, а в хрупком состоянии ан < 1…2 кгс • м/см2.
С 1/1 1979 г. введен новый ГОСТ 9454 — 78 «Методы испытания на ударный изгиб при пониженной, комнатной и повышенной температурах».
|
В новом ГОСТе ударную вязкость обозначают буквами КСU, КСV или КСТ.
Первые две буквы КС — обозначают символ ударной вязкости, третья буква U, V или Т—вид концентратора (U– радиус концентратора 1+0,07мм, V—радиус 0,25 + 0,025мм и Т— трещина). Размерность КС - Дж/м2 или кгс-м/см2.
В учебнике сохранено старое обозначение ударной вязкости ан кгс • м/см2, которое принято во всех действующих ГОСТах на стали и другие металлы и сплавы.
Вопросы для повторения и закрепления:
1. Сколько видов образцов применяют при определении ударной вязкости?
2. Как правильно расположить образец относительно маятника?
3. Какие величины копра остаются постоянными при испытании?
3.4 Испытание на усталость
Разрушение металлов под действием многократных (повторно-переменных) нагрузок, изменяющихся по величине и знаку, при напряжениях, меньших предела прочности на растяжение, называют усталостным. Способность металлов выдерживать большое число циклов, называют выносливостью σω, или циклической прочностью. Циклы бывают симметричные, когда наибольшее σmax и наименьшее σmin напряжения равны, но противоположны по знаку, и асимметричные, характеризующиеся различными по величине наибольшими и наименьшими напряжениями.
Рис.3.5. Схема изменения напряжения при испытании на усталость (а) и излом образца (б)
Испытания обычно проводят на цилиндрических образцах путем воздействия на них при вращении изгибающих нагрузок, которые вызывают знакопеременные напряжения (рис.3.5. а) и доводят образец до разрушения. Вследствие усталостного разрушения в сечении образца получается характерный излом (рис.3.5, б), в котором можно заметить две зоны: наружная имеет гладкую поверхность, а внутренняя — шероховатую со следами хрупкого разрушения металла.
Обычно стальные образцы испытывают до 5 млн. переменных циклов.
Задание:
Составить план ответа на темы: «Испытания на ударный изгиб и испытания на усталость»
ПРОИЗВОДСТВО ЧУГУНА
Исходные материалы
Железо в чистом виде редко встречается в поверхностных слоях земной коры: из-за большой склонности к окислению обычно встречаются окислы железа в смеси с соединениями других элементов. Насчитывается около 200 различных минералов, содержащих железо. Ведущие ученые в области геологии академики В.И. Вернадский и А. П. Виноградов считали, что в земной коре (до глубины 16км) содержится примерно 5 % железа в виде окислов, карбонатов, сульфидов и других соединений. В отдельных местах земной коры содержание соединений железа еще выше. Наиболее крупные и богатые окисленными соединениями железа скопления минералов называют месторождениями железных руд. Рудами называют горные породы, которые технически возможно и экономически целесообразно перерабатывать для извлечения содержащихся в них металлов.
К железным рудам относят красный, бурый, магнитный и шпатовый железняки. Эти руды содержат значительное количество рудного вещества или соединений железа, из которого оно извлекается, и относительно небольшое количество пустой породы, легко отделяющейся при переработке.
Пустая порода — это такие минералы, которые не вносят серьезных технологических осложнений в металлургическую переработку и легко отделяются от рудных минералов в процессе обогащения или переходят в шлаки при плавке. Пустой породой в железных рудах чаще всего являются кремнезем, каолин, реже доломит и магнезит. В рудах обычно содержатся и вредные примеси, которые осложняют металлургические переделы и, загрязняя основной металл, снижают его свойства. В железных рудах к вредным примесям обычно относят серу, мышьяк и фосфор.
Красный железняк (гематит) содержит железо главным образом в виде Fе2О3 — безводной окиси железа. Пустой породой в нем обычно бывает кремнезем. Содержание железа в красных железняках по массе составляет 45—65 % при малом содержании вредных примесей. Красный железняк хорошо восстанавливается в доменных печах.
Бурый железняк (лимонит) содержит железо в форме водных окислов nFе2О3 • mН2О. Собственно лимонитом обычно называют минерал желтого цвета, содержащий 57,14 % Fе2О3 и 25,3 % Н2О. Обычно бурый железняк содержит 25—50 % Fе, но кристаллическая вода, легко удаляемая при плавке, делает руду пористой и легко поддающейся восстановлению. Ее пустая порода обычно состоит из глины. Бурые железняки многих месторождений содержат значительные количества серы, фосфора и других вредных примесей.
Магнитный железняк (магнетит) содержит железо главным образом в виде Fе3О4, обладающего хорошо выраженными магнитными свойствами. Пустой породой, сопутствующей ему, бывают кремнеземистые минералы. Магнетиты содержат железа от 40 до 70 % и являются наиболее богатыми железными рудами, но восстанавливать их труднее, так как магнетиты являются плотными горными породами; часть магнетита в результате выветривания бывает иногда окислена до Fе2О3, и такие руды в зависимости от степени окисления иногда называют полумартитом или мартитом. Если они залегают вместе с пиритами, то руда иногда может содержать и до 2 % серы в виде FеS2.
Шпатовый железняк (сидерит) содержит железо в виде карбоната FеСО3. Его пустая порода содержит алюмосиликаты и магнезит, а содержание железа колеблется от 30 до 37 %. Для повышения содержания железа эти руды перед плавкой обжигают, удаляющийся при этом углекислый газ делает руду пористой и легко поддающейся восстановлению.
В природе часто встречаются руды, содержащие несколько полезных металлов. Такие руды принято называть полиметаллическими или комплексными. В некоторых железных рудах кроме железа содержатся марганец, хром, никель, которые при плавке восстанавливаются и растворяются в железе, легируя его.
Для производства чугуна кроме железных руд требуются и другие материалы. К ним в первую очередь следует отнести марганцевую руду, флюсы и кокс.
Марганцевые руды загружаются вместе с железными рудами в доменную печь, если поступающая на плавку железная руда содержит недостаточное количество марганца. Марганцевые руды содержат марганец в виде различных окислов МnО2, Мn3О4, Мn2О3 с содержанием марганца 25—40 %. Их пустая порода в большинстве случаев состоит из глинистых песчаников, которые могут быть частично отделены простой промывкой.
Флюсы вводят в доменную печь для того, чтобы не допустить «зарастания» рабочего пространства печи и обеспечить расплавление пустой породы, руды и золы топлива при необходимой температуре: не слишком высокой, чтобы не тратить много топлива, и не слишком низкой, при которой окислы железа еще не успевают восстановиться. Количество и характер добавляемых флюсов зависят от количества и химического состава пустой породы; их определяют расчетным путём. Так как пустая порода железных руд обычно содержит кремнезём, в качестве флюса в доменных печах часто применяют известняк СаСО 3 содержащий минимальное количество вредных примесей.
Каменноугольный кокс в современном доменном произволе играет двоякую роль. Во-первых, служит топливом и обеспечивает нагрев печного пространства до необходимой температуры и, во-вторых, обеспечивает восстановление окислов железа. Благодаря своей высокой механической прочности, пористости и значительной теплотворной способности он применяется теперь повсеместно и почти вытеснил, применявшийся ранее для этих целей, древесный уголь Каменноугольный кокс содержит 82—88 % твердого углерода, от 5 до10 % золы, однако всегда содержит от 0,5 до 2 % серы.
Вопросы для повторения и закрепления:
1. Что называется рудой?
2. Какие руды наиболее богатые железом?
3. Какое назначение флюсов?
4. Какова роль кокса при выплавки металла?
Подготовка материалов к доменной плавке
Чугун выплавляют в доменных печах. Чтобы печь работала нормально, ее надо загружать кусковым материалом оптимального размера. Крупные куски руды и других материалов не успевают за время их опускания в печи прореагировать на всю глубину. При этом часть, материала расходуется бесполезно. Слишком мелкие куски плотно прилегают друг к другу, не оставляя необходимых проходов для газов. Наиболее удобным материалом для доменной плавки являются куски размером от 30 до 80мм в поперечнике. Поэтому добываемые на рудниках куски руды просеивают через так называемые грохоты, и куски более 100мм в поперечнике подвергают дроблению. При дроблении материалов, как и при добыче руды в рудниках, наряду с крупными кусками образуется и мелочь, не пригодная к плавке в шахтных печах. Возникает необходимость окускования этих материалов до нужных размеров.
Наиболее широко в металлургии применяется агломерация (спекание), которая проводится теперь на больших ленточных агломерационных машинах непрерывного действия (рис. 4.1, а). Исходными материалами для агломерации служат рудная мелочь и колошниковая пыль — отход доменного производства. Эти материалы смешивают с небольшим количеством (8…12 %) мелкого кокса, так называемым коксиком, или каменноугольной мелочью. Часто в шихту добавляют мелкий, недостаточно спекшийся агломерат.
Слегка увлажненную (5…6 % влаги) и хорошо перемешанную шихту, загружают на колосниковую решетку машины слоем толщиной 200…300мм и затем поджигают с поверхности под камерой зажигания, расположенной над лентой. Под колосниковой решеткой имеются камеры, в которых создается небольшой вакуум (остаточное давление 6…12 кПа), обеспечивающий просасывание воздуха через слой агломерационной шихты и перемещение зоны горения коксика с поверхности шихты в ее нижние слои. В зоне горения коксика развивается высокая температура (до 1500°С), вследствие чего образуется небольшое количество жидкой фазы — фаялита Fе2( SiO4) по реакции:
Fе2Оз + SiO2 + C О = Fе2(SiO4) + СО2
Образующийся фаялит склеивает куски руды после перемещения из зоны горения в зону охлаждения материала (рис.4.1, б).
В результате образуется ноздревато-пористый черно-серый продукт спекания — агломерат. Ленточная машина для получения агломерата (рис. 4.1, а) размещается в здании высотой 5…6 производственных этажей и устанавливается на стальном каркасе с транспортными направляющими рельсами, на которых помещают определенное число металлических палет 3 (тележек с днищем в виде колосниковой решетки с бортами и двумя парами роликов по бокам). Приводной механизм 5 (рис. 4.1) захватывает палеты за ролики, поднимает их с нижних направляющих на верхние и передвигает слева направо.
Рис. 4.1. Агломерационная машина: а — общий вид; б — поперечный разрез верхней части; 1 — система бункеров и питателей исходных материалов, 2 — зажигательная камера, 3 — палеты, составляющие агломерационную поверхность машины; 4 — короба для отсоса газов, 5 — приводной механизм
Палеты плотно примыкают друг к другу торцами и образуют в верхней части машины горизонтальный желоб с колосниковым дном, под которым размещены камеры разряжения 4.
В левой части машины находится загрузочное оборудование (система бункеров, транспортеров и питателей), с помощью которого на колосники палет сначала засыпается тонкий слой мелкого агломерата: (постель), предохраняющий колосники от разгара и удерживающий мелкие частицы шихты от проскакивания в зазоры между колосниками, а затем толстый слой шихты. После разравнивания слоя шихты, по мере движения палет, они подходят под камеру зажигания 2, имеющую газовые или мазутные горелки, под которыми зажигается коксик верхних слоев шихты и где расположены камеры разряжения.
Во время перемещения палет по верхнему горизонтальному участку агломерационной машины заканчивается перемещение зоны горения коксика к нижним слоям шихты и завершается процесс агломерации. Попадая на полукруглый участок пути, палеты сбрасывают раскаленный агломерат на колосниковый грохот и, перевертываясь вверх колесами за счет силы тяжести по наклонному нижнему рельсовому участку машины, подкатываются к приводному механизму и вновь поднимаются на верхний ее участок. Производительность крупных агломерационных машин достигает 2,5 тыс.т агломерата в сутки.
В последнее время наряду с обычным агломератом стали производить так называемый офлюсованный агломерат, который получают, добавляя в агломерационную шихту мелкие кусочки флюса (обычно известняка). В процессе агломерации известняк СаСО3 разлагается, выделяя СО2 и участвуя в образовании агломерата.
Офлюсованный агломерат (еще в большей степени, чем обычный) увеличивает производительность доменных печей на 10…25 % и уменьшает расход кокса на доменную плавку на 7…20 %.
Окускование рудной мелочи проводят и другими способами, например брикетированием — простейшим способом окускования порошковых материалов путем прессования их смеси с какими-либо связующими материалами (глиной, жидким стеклом, смолой и т. п.). Вынутые из прессов брикеты в зависимости от характера связующего материала сушат на воздухе или обжигают для придания им необходимой прочности.
С 50-х годов в черной металлургии применяют новый метод окускования — производство окатышей. Суть этого способа заключается в смешивании рудной мелочи и пыли с небольшим количеством дешевого тонкоизмельченного связующего, обычно глины или извести. После небольшого увлажнения до 8…10 % эту смесь помещают в смеситель в виде пустотелого барабана или наклонной неглубокой чаши. Рудная шихта, вращаясь в барабане (чаше), пересыпается с места на место, слипается, образуя круглые окатыши диаметром 25…30мм. Затем окатыши сушат или обжигают, чтобы сделать их достаточно прочными для применения в крупных доменных печах. Обжиг в восстановительной атмосфере позволяет частично восстановить окислы железа и тем самым повысить производительность доменных печей.
Вопросы для повторения и закрепления:
1. Для чего предназначена агломерация?
2. Для чего предназначено производство окатышей?
Задание:
Составить план ответа по темам «Исходные материалы» и «Подготовка материалов к доменной плавке»
|
|
Адаптации растений и животных к жизни в горах: Большое значение для жизни организмов в горах имеют степень расчленения, крутизна и экспозиционные различия склонов...
Индивидуальные и групповые автопоилки: для животных. Схемы и конструкции...
Таксономические единицы (категории) растений: Каждая система классификации состоит из определённых соподчиненных друг другу...
Типы сооружений для обработки осадков: Септиками называются сооружения, в которых одновременно происходят осветление сточной жидкости...
© cyberpedia.su 2017-2024 - Не является автором материалов. Исключительное право сохранено за автором текста.
Если вы не хотите, чтобы данный материал был у нас на сайте, перейдите по ссылке: Нарушение авторских прав. Мы поможем в написании вашей работы!